单嘴精炼炉冶炼超洁净钢工艺
洁净钢生产工艺及技术概述

1.9L/min,滑板系统 最大6L/min。
– 定期在SEN后方卡门漩涡区产生的下排流。
– 从SEN出口到表面的大的氩气泡。
– SEN出口布流不均匀引起
– 在较高钢通量的情况下,钢水和保护渣之间聚集的泡 沫。
16
炉渣乳化
• 影响卷渣的参数
– Kelvin-Helmholtz不稳定性标准(不同层流之间相对运动波动性)
图12.渣脱氧后ULC钢板表面指数降低
图13.渣脱氧后表面缺陷率降低
25
二次氧化
• 减少中间包覆盖剂引起的二次氧化
B C
产生的液态炉渣会增加对中间包耐火材料的侵蚀
19
炉渣乳化
• 漩涡卷渣
漩涡下排(漩涡型漏斗)和汇流下排(非漩涡型漏斗) 稳态漩涡和非稳态漩涡 表面微凹、表面漩涡、全面发展卷吸空气的漩涡
低流速下,漩涡随着流出速度的增加而达到最大 稳定的高流速下,随着流出速率的增加,熔池临界深度
减小
20
• 漩涡卷渣
炉渣乳化
K-流动能量损失 随着渣钢比率的增加,临界熔池深度增大
• 炼钢过程中,由于钢液或渣对耐火材料的化学或热侵 蚀作用以及固态耐火材料颗粒脱落进入钢液。
• 卷渣产生的夹杂物,渣钢界面上钢水流速较大以及渣 的乳化使液态渣滴卷入钢液。
6
钢中的夹杂物---控制/去除
• 避免生产过程中夹杂物的生成。 • 促使夹杂物向渣/气、钢/渣或钢液/耐火材料界面移
动,使其进一步脱离钢液进入界面并从界面分离。
图8.表面缺陷与结晶器中T[O]之间的 关系
图9.宏观夹杂物数量与T[O]之间的 关系
23
二次氧化
• 渣中FeO含量和厚度的检测
EA4T钢纯净化冶炼工艺研究

EA4T钢纯净化冶炼工艺研究EA4T钢是一种高强度、高耐腐蚀性能的钢材,在军工、化工等领域有着广泛的应用。
然而,EA4T钢的生产工艺比较复杂,其中的净化冶炼环节对产品质量的影响较大。
本文针对EA4T钢的净化冶炼工艺进行研究,旨在提高产品质量和生产效率。
1. 净化冶炼原理EA4T钢是一种低合金高强度钢,其中的杂质元素会对钢材的强度和耐腐蚀性能产生不良影响。
因此,在钢铁生产过程中,需要采用净化冶炼技术,将其中的杂质元素去除,以提高产品质量。
净化冶炼的原理是通过氧化还原反应和化学反应使杂质元素还原成氧化物或硫化物等高熔点物质,并从钢水中剥离出来。
2. 净化冶炼工艺(1)操作流程EA4T钢的净化冶炼工艺分为两道工序,即精炼和真空处理。
首先,在精炼炉中加入氧化剂和脱硫剂,使其中的杂质元素发生氧化还原反应和化学反应,并与氧化剂和脱硫剂生成气体,从而剥离出钢水中的杂质元素。
然后,将经过精炼后的钢水在真空下进行处理,进一步去除其中的氧化物和气体,最终得到高纯度的EA4T钢。
(2)工艺参数EA4T钢的精炼过程中,需要根据钢水中杂质元素的情况,确定适当的操作参数。
一般来说,氧化剂的加入量应根据钢铁冶炼过程中产生的氧化物量来确定;脱硫剂的加入量则应根据钢水中硫含量来确定。
同时,在真空处理的过程中,需要控制真空度和温度,以使钢水中的气体被完全去除。
(3)工艺改进为提高EA4T钢的净化冶炼效果,可以采取一些工艺改进措施。
例如,可以适当增加氧化剂和脱硫剂的加入量,提高净化冶炼的效率。
另外,可以通过增加搅拌时间或采用电磁搅拌等方式,提高钢水的混匀性,加速杂质元素的还原和剥离。
3. 结论EA4T钢的净化冶炼工艺对产品质量的影响非常重要。
为提高EA4T钢的质量和生产效率,需要对净化冶炼的操作流程和工艺参数进行优化和改进。
在实际生产中,应根据生产要求和杂质元素的含量确定合适的操作参数,以最大程度地提高净化冶炼的效率和钢材的质量。
为了更好地研究EA4T钢的净化冶炼工艺,我们需要收集和分析一些相关的数据。
洁净钢生产工艺技术

洁净钢生产工艺技术1. 简介洁净钢是一种具有高纯度、低气体含量和低不纯物含量的钢材。
洁净钢的生产工艺技术在钢铁行业中起着重要的作用。
本文将介绍洁净钢的生产工艺技术、工艺流程和相关设备。
2. 洁净钢生产工艺技术的意义洁净钢的生产工艺技术可以有效降低钢材中的气体含量和不纯物含量,提高钢材的纯度和质量。
洁净钢广泛应用于汽车制造、航空航天、电子设备等高端领域,对提高产品的品质和性能具有重要意义。
3. 洁净钢生产工艺技术的主要方法洁净钢的生产工艺技术主要包括如下几种方法:3.1 精炼精炼是洁净钢生产的关键步骤之一。
通过在高温条件下对炼钢液进行溶解和脱气处理,可以将钢液中的气体含量和不纯物含量大大降低,提高钢材的纯度。
3.2 熔盐浸渍熔盐浸渍是一种将钢材浸入熔盐中,通过离子交换和溶解作用去除钢材表面的氧化物和其他杂质的方法。
这种方法可以显著降低钢材中的含氧量和含杂质量,提高钢材的纯度。
3.3 真空处理真空处理是将钢材放入真空设备中进行处理的方法。
利用真空环境可以有效去除钢材中的气体,减少钢材中的含气量和含杂质量,提高钢材的纯度。
3.4 气体透平气体透平是通过气体的透平作用去除钢材中的气体的方法。
通过将高速气体喷射到钢材中,可以将钢材中的气体冲出,降低钢材中的气体含量。
3.5 再结晶控制再结晶控制是通过控制钢材的热处理过程中的再结晶过程,来提高钢材的晶粒度和纯度的方法。
通过精确控制再结晶过程中的温度和时间,可以得到具有更好性能和纯度的洁净钢材。
4. 洁净钢生产工艺技术的工艺流程洁净钢的生产工艺技术一般包括以下几个主要步骤:1.原料准备:将适量的生铁、废钢和合金等原料按照一定比例混合。
2.熔炼:通过高炉冶炼或电炉冶炼,将原料熔化成钢水。
3.精炼:在精炼炉中对钢水进行溶解和脱气,去除其中的气体和不纯物。
4.过滤:通过过滤器将钢水中残余的杂质和固体颗粒去除。
5.熔盐浸渍:将钢材浸入熔盐中,去除表面氧化物和其他杂质。
如何冶炼洁净钢

冶炼洁净钢应根据品种和用途要求,铁水预处理-炼钢-精炼-连铸的操作都应处于严格的控制之下,主要控制技术对策如下:(1)铁水预处理。
对铁水脱硫或三脱工艺(脱Si、脱P、脱S),入炉铁水硫含量应小于0.005%甚至小于0.002%。
(2)转炉复合吹炼和炼钢终点控制。
改善脱磷条件,提高终点成分和温度一次命中率,降低钢中溶解氧含量,减少钢中非金属夹杂物数量。
(3)挡渣出钢。
采用挡渣锥或气动挡渣器,钢包内渣层厚度控制在50mm以下,转炉内流出的氧化性炉渣会增加氧化物夹杂。
防止出钢下渣可避免回磷和提高合金吸收率。
为保证钢包渣百分之百合格,在钢水接收跨设置钢渣扒渣机是有利的。
(4)钢包渣改质。
出钢过程向钢流加入炉渣改质剂,还原FeO并调整钢包渣成分。
(5)炉外精炼。
根据钢种质量要求选择一种或多种精炼组合方式完成钢水精炼任务,达到脱氢、极低C化、极低S化、脱氮、减少夹杂物和夹杂物形态控制等。
1)LF炉。
包盖密封,造还原渣,可扩散脱氧、脱硫、防止渣中FeO和MnO对钢水再氧化。
调整和精确控制钢水成分、温度,排除夹杂物并进行夹杂物形态控制。
2)真空处理。
冶炼超低碳钢的脱碳和脱氧、脱氢、脱氮,排除脱氧产物。
(6)保护浇注。
在浇注过程中采用保护浇注技术对生产洁净钢尤为重要。
1)钢包→中间包注流用长水口+吹氩保护,控制钢水吸氮量小于1.5ppm(1.5×10-4%),甚至为零。
2)中间包→结晶器用浸入式水口+保护渣的保护浇注,钢水吸氮小于2.5ppm(2.5×10-4%)。
3)浇注小方坯时,中间包→结晶器采用氩气保护浇注,气氛中Φ02<1%。
4)在第一炉开浇前中间包内充满空气,为防止钢水中生成大量的Al203和吸氮,在中间包内充入氩气,并用耐火纤维密封中间包体与包盖间的缝隙。
(7)中间包冶金。
在中间包内组织钢水的合理流动,延长钢水停留时间,促进夹杂物上浮。
1)采用碱性包衬的大容量深熔池中间包;2)中间包加砌挡墙+坝、多孔挡墙、过滤器,采用吹氩搅拌、阻流器;3)中间包覆盖剂可保温、隔绝空气,吸附夹杂物;生产洁净钢中间包采用碱性覆盖剂为宜;4)滑动水口高的自开率,自开率应大于95%;5)开浇、换包、浇注即将结束时防止卷渣;6)应用中间包热态循环使用技术;7)应用中间包真空浇注技术。
炉外精炼与洁净钢技术

1、炉外精炼的内容脱氧、脱硫;去气、去除夹杂;调整钢液成分及温度。
2、炉外精炼的手段渣洗:最简单的精炼手段;真空:目前应用的高质量钢的精炼手段;搅拌:最基本的精炼手段;喷吹:将反应剂直接加入熔体的手段;调温:加热是调节温度的一项常用手段。
3、主要的精炼工艺LF(Ladle Furnace process);AOD(Argon-oxygen decaburizition process );VOD (Vacuum oxygen decrease process) ;RH (Ruhrstahl Heraeus process);CAS-OB( Composition adjustments by sealed argon -oxygen blowing process) ;喂线(Insert thread) ;钢包吹氩搅拌(Ladle argon stirring);喷粉( powder injection )。
LF炉LF炉指一种利用钢包对钢水进行炉外精炼的设备!!!LF炉(LADLE FURNACE)即钢包精炼炉,是钢铁生产中主要的炉外精炼设备。
它的主要任务是:①脱硫②温度调节③精确的成分微调④改善钢水纯净度⑤造渣在LF炉生产中建立过程控制计算机系统,主要用来解决以下问题:①实时接收生产计划,按照计划动态组织生产。
②按照炉次对LF炉生产进行实时的数据跟踪。
③通过冶金模型的计算,实现作业过程的优化,同时并向操作人员提供操作指导。
④向下工序提供LF炉作业数据。
⑤向工艺人员提供生产数据的历史追溯.LF炉一般指钢铁行业中的精炼炉。
实际就是电弧炉的一种特殊形式。
最常用的精炼方法;取代电炉还原期;解决了转炉冶炼优钢问题;具有加热及搅拌功能;脱氧、脱硫、合金化LF 精炼炉LF钢包精炼炉可供初炼炉(电炉、中频炉、AOD炉、转炉)钢水精炼、保温之用。
是满足优钢、特钢生产和连铸、连轧的重要冶金设备。
具有常压电弧加热、脱氧去气、吹氩搅拌、加料调整成分、测温、取样、脱磷脱硫等功能。
精炼炉工艺操作规程
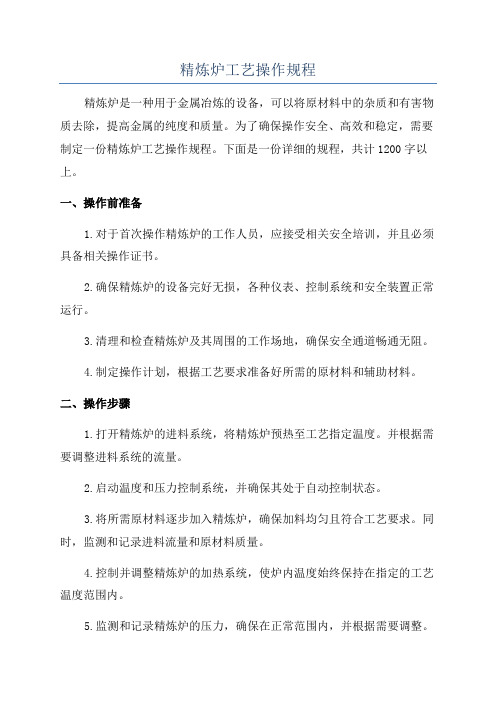
精炼炉工艺操作规程精炼炉是一种用于金属冶炼的设备,可以将原材料中的杂质和有害物质去除,提高金属的纯度和质量。
为了确保操作安全、高效和稳定,需要制定一份精炼炉工艺操作规程。
下面是一份详细的规程,共计1200字以上。
一、操作前准备1.对于首次操作精炼炉的工作人员,应接受相关安全培训,并且必须具备相关操作证书。
2.确保精炼炉的设备完好无损,各种仪表、控制系统和安全装置正常运行。
3.清理和检查精炼炉及其周围的工作场地,确保安全通道畅通无阻。
4.制定操作计划,根据工艺要求准备好所需的原材料和辅助材料。
二、操作步骤1.打开精炼炉的进料系统,将精炼炉预热至工艺指定温度。
并根据需要调整进料系统的流量。
2.启动温度和压力控制系统,并确保其处于自动控制状态。
3.将所需原材料逐步加入精炼炉,确保加料均匀且符合工艺要求。
同时,监测和记录进料流量和原材料质量。
4.控制并调整精炼炉的加热系统,使炉内温度始终保持在指定的工艺温度范围内。
5.监测和记录精炼炉的压力,确保在正常范围内,并根据需要调整。
6.在精炼过程中,根据需要向精炼炉添加辅助材料,如脱硫剂、脱氧剂等。
添加时应小心谨慎,并注意控制时间和加量。
7.定期抽取炉内样品进行化验分析,以确保精炼炉中金属的纯度和质量达到工艺要求。
8.在精炼过程中,监测和记录炉内的操作参数,如温度、压力、流量等,并进行实时调整,确保工艺参数符合要求。
9.精炼炉操作结束后,关闭进料系统,并将残余的金属材料转移至指定地点进行处理。
10.关闭加热系统和压力控制系统,并确保精炼炉内温度和压力降至安全范围。
11.清理和维护精炼炉及其周围环境,确保操作场地整洁和安全。
三、安全注意事项1.操作人员必须穿戴好个人防护装备,包括耐高温手套、防护镜、工作鞋等。
2.确保精炼炉周围通风良好,防止有害气体积聚。
3.严禁在操作过程中任意修改设备或绕过安全装置,如有需要必须由有资质的工作人员进行。
4.操作人员必须熟悉应急处理措施,如精炼炉故障、泄漏、火灾等情况的应对方法。
洁净钢生产工艺技术(PDF 79页)

外来夹杂物的产生原因
• 外来夹杂物大多为复合氧化物夹杂,一般 多来自钢渣界面湍流形成的卷渣。在炼钢 温度下,外来夹杂物多为液态球形夹杂物 尺寸在10-300μm。钢渣界面的湍流是由浇 铸、强烈搅动、涡流或液面控制不稳定等 原因造成的。另一种为钢水或炉渣与耐火 材料反应生成,固态夹杂物经常来自于耐 火材料的破损。
冷却和凝固过程生成的的氧化物。一般与 钢液处于平衡状态,它们是自然生成,因 此只能减少而不能被完全去除。 • 2、外来夹杂物:炉渣卷入或耐火材料侵蚀 卷入钢水。一般是与冶炼过程相关,因此 采用合适冶炼工艺可以避免外来夹杂物的 产生。
非金属夹杂物的三个来源
• 1、加入脱氧剂后生成的脱氧产物、裸露的 钢液被大气氧化和被耐火材料氧化生成的 度,这主要是为 了使用更薄的钢材来减轻重量,并需要钢材在加 工的过程中具有良好的变形性能。
• 降低钢水中的夹杂物的数量可以减少钢材中缺陷 的产生。据日本钢管某厂统计,当结晶器中的全 氧含量低于0.0020%(20ppm)时,冷轧钢板表 面缺陷的数量将显著减少。
• 对钢包中钢水进行搅拌,通常会在钢液表面形成 “裸眼”使钢液直接接触空气从而形成二次氧化, 因此在整个冶炼过程中钢液表面需覆盖合适厚度 的渣层能够防止这种二次氧化。
钢水的二次氧化
• 钢液二次氧化的原因有如下几种形式: 1、被合金中的氧化物污染。例如,锰合金中
主要含有MnO夹杂,当碳含量相对较低 时,影响更为明显。 2、上一炉附着在钢包内壁或者RH浸渍管内 的渣瘤污染钢液。 3、在钢包和中间包中与渣的反应。 4、转炉出钢、二次精炼过程中、浇注过程中 包内,钢水与空气的反应。 5、钢液与耐火材料内衬之间的反应。
洁净钢冶炼先进案例

洁净钢冶炼先进案例洁净钢冶炼是一种环保、高效、先进的钢铁冶炼技术,旨在降低对环境的污染,提高钢铁质量和生产效率。
下面列举了10个洁净钢冶炼先进案例。
1. 湿法洁净钢冶炼技术:该技术采用湿法处理炼钢过程中产生的烟尘和废气,通过湿式电除尘器和湿法脱硫等装置,有效减少了炼钢过程中的大气污染物排放。
2. 高炉煤气洁净利用技术:传统高炉在炼钢过程中产生的煤气含有大量的有毒有害物质,通过引入洁净利用技术,如煤气净化装置和煤气发电技术,可以将煤气中的有害物质净化,实现高效利用。
3. 废渣资源化利用技术:钢铁冶炼过程中会产生大量的废渣,传统上这些废渣往往被视为废弃物处理。
现在,通过洁净钢冶炼技术,可以将废渣进行资源化利用,如生产水泥、建筑材料等。
4. 电弧炉炼钢技术:电弧炉炼钢是一种洁净钢冶炼技术,它利用电弧高温熔化废钢和铁合金,可以有效减少对原材料的需求,降低能源消耗,同时还可以控制冶炼过程中的污染物排放。
5. 气体循环冷却技术:传统高炉冷却系统往往会产生大量废热,通过引入气体循环冷却技术,可以将废热回收利用,提高炼钢过程的能源利用效率。
6. 炉渣处理技术:炉渣是钢铁冶炼过程中产生的一种固体废弃物,传统上往往需要通过填埋或堆放等方式处理。
现在,通过洁净钢冶炼技术,可以对炉渣进行资源化利用,如生产水泥、路基材料等。
7. 无废水排放技术:传统钢铁冶炼过程中会产生大量废水,含有大量的重金属和有机物等污染物。
现在,通过引入洁净钢冶炼技术,可以实现无废水排放,通过废水处理装置将废水进行处理,达到环保要求。
8. 超高炉技术:超高炉是一种高效、环保的炼钢设备,具有高炉煤气洁净利用、炉渣资源化利用等先进技术。
超高炉的应用可以提高钢铁冶炼的效率、减少能源消耗和污染物排放。
9. 先进的炉排系统:炉排系统是钢铁冶炼过程中的关键设备,传统上往往存在能耗高、污染物排放多等问题。
现在,通过引入先进的炉排系统,如高效炉排和低NOx燃烧技术,可以实现钢铁冶炼过程的高效、洁净。