Investigation on the corrosion process of carbon steel coated by HVOF WC-Co cermets neutral
科技英语写作(2)—Title

Importance of the Title In preparing a title for a paper, the author would do well to remember one salient fact: That title will be read by thousands of people. Perhaps few people, if any, will read the entire paper, but many people will read the title, either in the original journal or in one of the secondary (abstracting and indexing) publications. Therefore, all words in the title should be chosen with great care, and their association with one another must be carefully managed. Perhaps the most common error in defective titles, and certainly the most damaging in terms of comprehension, is 5 faulty syntax (word order).
2
题名撰写的基本要求 在设计题名时,作者应思考一下“我如何检索 在设计题名时,作者应思考一下“ 这类信息” 这类信息” 为了方便二次检索,题名中应避免使用化学式、 上下角标、特殊符号(数字符号、希腊字母 等)、公式、不常用的专业术语和非英语词汇 (包括拉丁语)等。部分文体指南和作者须知 中还特别规定题名中不得使用专利名、化工产 品、药品、材料或仪器的公司名、特殊商业标 记或商标。
异氰酸酯改性竹材表面及其抗蚀性能研究

第39卷第1期2019年2月林㊀产㊀化㊀学㊀与㊀工㊀业ChemistryandIndustryofForestProductsVol.39No.1Feb.2019doi:10.3969/j.issn.0253 ̄2417.2019.01.007异氰酸酯改性竹材表面及其抗蚀性能研究㊀㊀收稿日期:2018 ̄10 ̄14㊀㊀基金项目:国家自然科学基金资助项目(21776234)ꎻ中国石油天然气集团有限公司创新基金(2018D ̄5007 ̄0503)㊀㊀作者简介:高和(1994 ㊀)ꎬ男ꎬ江西九江人ꎬ硕士生ꎬ研究方向为能源化工㊀∗通讯作者:孙勇ꎬ副教授ꎬ硕士生导师ꎬ研究领域为生物能源化学和生物基材料ꎻE ̄mail:sunyong@xmu.edu.cnꎮGAOHe㊀㊀高和ꎬ孙勇∗ꎬ唐兴ꎬ曾宪海ꎬ林鹿(厦门大学能源学院ꎻ福建省生物质清洁高值化技术工程研究中心ꎻ厦门市生物质清洁高值化利用重点实验室ꎬ福建厦门361102)摘㊀要:㊀以异氰酸酯对竹材表面进行接枝改性ꎬ大幅提升了天然竹材的抗蚀性能ꎮ研究中分别以热水预处理竹材(H ̄bam)和碱预处理竹材(A ̄bam)为原料ꎬ采用二环己甲烷4ꎬ4ᶄ ̄二异氰酸酯(HMDI)为改性剂ꎬ得到改性竹材样品H ̄HMDI ̄bam和A ̄HMDI ̄bamꎮ抗蚀机制研究表明:改性后竹材表面的羟基数量明显减少ꎬ羰基㊁酰胺官能团增加ꎬHMDI成功接枝到纤维表面并成絮状包裹状ꎬA ̄HMDI ̄bam和H ̄HMDI ̄bam的负载量分别为6.342和4.080mmol/cm2ꎮ改性样品疏水性明显增强ꎬ其中H ̄HMDI ̄bam表现优异ꎬ吸水率由原料的68.7%下降到35.5%ꎬ孔径和孔体积大幅下降到33.48nm和0.0390cm3/gꎮSEM观察表明H ̄HMDI ̄bam样品无明显被腐蚀的痕迹ꎬ腐蚀等级为0~1级ꎬ与工业传统炭化抗腐处理工艺水平相当ꎮ关键词:㊀竹材ꎻ改性ꎻ异氰酸酯ꎻ耐蚀性中图分类号:TQ35㊀㊀㊀㊀㊀㊀㊀㊀㊀㊀㊀文献标识码:A㊀㊀㊀㊀㊀㊀㊀㊀㊀文章编号:0253 ̄2417(2019)01 ̄0046 ̄07引文格式:高和ꎬ孙勇ꎬ唐兴ꎬ等.异氰酸酯改性竹材表面及其抗蚀性能研究[J].林产化学与工业ꎬ2019ꎬ39(1):46-52.IsocyanateModifiedBambooSurfaceandItsCorrosionResistancePropertyGAOHeꎬSUNYongꎬTANGXingꎬZENGXianhaiꎬLINLu(FujianEngineeringandResearchCenterofCleanandHigh ̄valuedTechnologiesforBiomassꎻXiamenKeyLaboratoryofCleanandHigh ̄valuedUtilizationforBiomassꎻCollegeofEnergyꎬXiamenUniversityꎬXiamen361102ꎬChina)Abstract:Theprocessofenhancingthecorrosionresistanceofnaturalbamboobymodifyingitssurfacewithisocyanatewasdeveloped.Thebambootreatedwithhotwateroralkaliwasmodifiedwithdicyclohexylmethane4ꎬ4ᶄ ̄diisocyanate(HMDI)andachievedthebamboosamplesH ̄HMDI ̄bamandA ̄HMDI ̄bamꎬrespectively.Theinvestigationoncorrosionresistancemechanismindicatedthatthenumberofhydroxylgroupsonthesurfaceofthemodifiedbamboowassignificantlyreducedaftermodificationꎬwhilethenumbersofthecarbonylandamidegroupsincreased.HMDIwassuccessfullygraftedontothefibersurfaceandformedtheflocculentencapsulation.Theloadingswere6.342mmol/cm2forA ̄HMDI ̄bamand4.080mmol/cm2forH ̄HMDI ̄bamꎬrespectively.ThehydrophobicityofthemodifiedsamplewassignificantlyenhancedꎬespeciallyforH ̄HMDI ̄bamꎬwhosewaterabsorptiondecreasedfrom68.7%(rawmaterial)to35.5%ꎬandtheporesizeandporevolumedecreasedsignificantlyto33.48nmand0.0390cm3/gꎬrespectively.TheSEMimagesshowedthatthesamplecoatedwithHMDIwashardlycorrodedꎬcorrespondingtothegradeof0-1ꎬwhichwassimilartothatofthesampletreatedbythetraditionalcarbonizationprocessinindustry.Keyword:bambooꎻmodificationꎻisocyanateꎻcorrosionresistance竹子是重要的森林资源ꎬ生长周期短ꎬ可再生能力强ꎬ有超过1500种传统用途ꎬ是理想的木材替代品[1-2]ꎮ由于天然竹材原料容易发生霉变ꎬ对竹产品加工㊁储存步骤和使用过程会带来一定程度的影响ꎬ故需对竹材加工来提高其防蚀性能ꎮ目前ꎬ工业上常用的增强竹材抗蚀性的方法有低温炭化法和热第1期高和ꎬ等:异氰酸酯改性竹材表面及其抗蚀性能研究47㊀水处理法ꎮ低温炭化主要是通过热分解耐热性差的半纤维素ꎬ缩合部分纤维素中游离羟基ꎬ从而降低了竹材原料的吸湿性ꎬ提高竹材的耐腐蚀性ꎮ然而低温炭化存在竹材颜色加深㊁处理时间长㊁能耗高等缺点ꎮ高温热水抽提也被工业应用作为竹材防腐的处理手段之一ꎬ通过抽提出竹材中的易水解糖和控制材料的吸湿性ꎬ从而提高材料的抗腐蚀性ꎮLiu等[3]研究了热水处理竹材能溶解出少量的单糖和低聚糖等导致竹材霉变的物质ꎬ然而同样有费时㊁材料颜色加深等缺点ꎮ化学改性防腐处理具有反应时间短㊁能耗低的优点ꎬ因此渐渐受到重视ꎮ异氰酸酯由于其含有高度不饱和的基团ꎬ在常温下能迅速与多羟基化合物反应生成氨基甲酸酯[4-5]ꎬ常用于做交联剂或表面改性剂使材料获得疏水性㊁耐磨性㊁隔热性等性质[6-7]ꎮGao等[8]利用液化竹材与聚芳基聚亚甲基异氰酸酯(PAPI)反应ꎬ合成了新型可控机械性能的半刚性聚氨酯(PU)泡沫ꎮ近些年来ꎬ利用异氰酸酯对高分子材料表面改性的研究得到了广泛关注ꎮ本研究中选用二环己甲烷4ꎬ4ᶄ ̄二异氰酸酯(HMDI)作为毛竹的改性剂ꎬ配合热水和碱处理两种不同的预处理方案ꎬ制备了异氰酸酯改性竹材ꎬ探讨了异氰酸酯改性竹材对里氏木霉的抗蚀性能ꎬ并从孔径结构㊁接触角㊁吸水率及材料形貌结构几个方面的变化来分析改性竹材的耐蚀机制ꎮ1㊀实验1.1㊀原料、试剂及仪器毛竹ꎬ购自江门市木江伟华香料厂ꎬ处理成相同尺寸(28.0mmˑ7.5mmˑ2.0mm)备用ꎮ二环己甲烷4ꎬ4ᶄ ̄二异氰酸酯(HMDI)(纯度98.0%)㊁无水硫酸镁㊁CoCl2㊁ZnSO4 7H2O㊁FeSO4 5H2O㊁MnSO4 H2O㊁无水氯化钙㊁四氢呋喃(THF)㊁丙酮㊁氢氧化钠㊁硫酸铵㊁磷酸二氢钾㊁二正丁基二乙酸锡(纯度95%)均为市售分析纯ꎮ里氏木霉(Trichodermareesei)购买自中国海洋微生物菌种保藏管理中心ꎮ基本培养基(无碳源):取5.0g硫酸铵㊁15.0g磷酸二氢钾㊁0.6g无水硫酸镁㊁0.6g无水氯化钙以及10mL微量元素储备液体溶于适量去离子水中ꎬ再定容到1Lꎬ用1mol/L的NaOH溶液将pH值调节至5.5ꎮ其中微量元素储备液为CoCl2(0.20g/mL)㊁ZnSO4 7H2O(0.14g/mL)㊁FeSO4 5H2O(0.50g/mL)和MnSO4 H2O(0.16g/mL)的混合溶液ꎮ在混合溶液中加入20.0g琼脂粉ꎬ混合均匀放入压力蒸汽灭菌锅中ꎬ在0.1MPa㊁121ħ的条件下灭菌1hꎬ灭菌结束趁热倒入培养皿中ꎬ待其自然冷却固化后封口备用ꎮParr100mL恒温搅拌反应釜ꎬUSAꎻElementarAnalysenSyetemGmbH元素分析仪ꎬ德国Elementar公司ꎻNicolet系列傅里叶变换红外光谱(FT ̄IR)仪ꎬ美国ThermoFisher公司ꎻDSA20型接触角测量仪ꎬ德国克吕氏公司ꎻSUPRA55型场发射扫描电子显微镜(FE ̄SEM)ꎬCarlZeiss公司ꎻMicromeriticsASAP2020物理吸附仪ꎬ美国Micromeritics有限公司ꎮ1.2㊀竹材预处理1.2.1㊀碱预处理㊀将竹材加入质量分数100g/L的NaOH中ꎬ并于恒温搅拌反应釜中60ħ保温30minꎬ反应完毕后用去离子水冲洗样品ꎬ用pH计测量洗液pH值ꎬ直至洗液呈中性ꎬ60ħ真空干燥备用ꎬ即得碱预处理样品(A ̄bam)ꎮ1.2.2㊀热水预处理㊀将竹材加入一定量去离子水中ꎬ并于恒温搅拌反应釜中160ħ保温1hꎬ反应完毕后用大量去离子水冲洗样品ꎬ60ħ真空干燥备用ꎬ即得热水预处理样品(H ̄bam)ꎮ1.3㊀竹材改性样品的制备1.3.1㊀HMDI改性竹材㊀称取0.5gHMDI溶于5mL四氢呋喃ꎬ将预处理后的样品A ̄bam/H ̄bam分别浸泡在溶液中ꎬ滴加少量二乙酸二正丁基锡作为催化剂ꎬ常温下充分搅拌5minꎬ将样品取出用水喷淋5sꎬ待其在表面皿中自由发泡30minꎬ得到碱预处理的HMDI改性竹材(A ̄HMDI ̄bam)和热水预处理的HMDI改性竹材(H ̄HMDI ̄bam)ꎮ再用丙酮抽提样品8h洗去表面杂质ꎬ在60ħ真空干燥ꎬ备用ꎮ1.3.2㊀炭化竹材㊀将竹材在管式炉中采用氮气氛围(流速1.0L/min)加热至260ħ(升温速率10K/minꎬ初始温度为室温)ꎬ保温10hꎬ得炭化竹材(C ̄bam)ꎮ1.4㊀分析表征1.4.1㊀HMDI负载量测定㊀竹材主要由三大组分(纤维素㊁半纤维素和木质素)组成ꎬ因竹材本身氮元素48㊀林㊀产㊀化㊀学㊀与㊀工㊀业第39卷含量很低ꎬ研究中利用测定氮元素含量来确定样品表面的HMDI接枝含量ꎮ将原料和不同样品经反复粉碎过筛ꎬ以确保所得粉末的最终粒径小于450μmꎬ取10mg粉末进行元素分析测试ꎮHMDI负载量按下式计算ꎬ其中wN和wᶄN分别为改性前后样品中的N元素(%)ꎬmd为样品干质量ꎬMN为N的相对分子质量ꎬS为样品表面积(S=5.62cm3)ꎮLHMDI=(wᶄN-wN)ˑmd2ˑMNˑS1.4.2㊀FT ̄IR㊀将各个样品粉碎后ꎬ在Nicolet系列傅里叶变换红外光谱仪上采用KBr压片法测试ꎬ光谱分辨率为4cm-1ꎮ1.4.3㊀水接触角测定㊀利用DSA20型接触角测量仪ꎬ采用高速科学用CCD成像ꎬ测量原料和不同样品的纵向接触角ꎮ每次测量取5s时的读数ꎬ测定环境温度为24ħꎮ1.4.4㊀吸水率的测定㊀将各样品浸泡在去离子水中48h后ꎬ分别测量试件充分吸水后的质量(mw)ꎬ再将其置于烘箱中烘至绝干(110ħ)ꎬ最后称取绝干后样品的质量(m)ꎬ吸水率(W)的计算公式如下[9]:W=(mw-m)/mˑ100%1.4.5㊀FE ̄SEM分析㊀样品形态结构采用场发射扫描电子显微镜进行分析ꎬ加速电压为5kVꎬ样品在Bal ̄TecMD020仪器中进行炭和金溅射涂层ꎮ1.4.6㊀BET分析㊀将不同预处理及其改性样品裁剪至5.0mmˑ5.0mmˑ2.0mmꎬ使用物理吸附仪分析样品的比表面积及孔径分布ꎮ在氮气吸附测试前ꎬ将待测物置于分析管中ꎬ在90ħ下真空脱气4hꎮ1.5㊀抗腐蚀性能测试将处理后的6组样品(C ̄bam㊁bam㊁H ̄bam㊁A ̄bam㊁H ̄HMDI ̄bam和A ̄HMDI ̄bam)采用紫外灭菌法灭菌12h后备用ꎮ取里氏木霉孢子50μL加入磷酸缓冲液中ꎬ再将6组样品分别浸入混合液中ꎬ浸泡10min后取出依次放入不同固体培养基中ꎬ封口后再将培养基放入30ħ培养箱培养ꎬ定期观察腐蚀情况ꎮ培养10日后ꎬ按国家标准GBT1741 2007«漆膜耐霉菌性测定法»对样品被腐蚀情况进行分级ꎮ2㊀结果与分析2.1㊀HMDI改性竹材的结构分析2.1.1㊀HMDI的负载量㊀竹材中N元素含量较低ꎬ可以通过N元素的变化来反应异氰酸酯的接枝量[10]ꎬ各样品具体元素分析结果以及HMDI负载量见表1ꎮ表1㊀不同样品元素含量以及HMDI负载量Table1㊀TheHMDIloadingandtheelementscontentofbamboosamples样品编号1)㊀samplescode㊀N/%C/%HMDI/%HMDI负载量/(mmol cm-2)HMDIloadingbam0.12243.788A ̄bam0.13044.472H ̄bam0.11745.671C ̄bam0.04361.074A ̄HMDI ̄bam0.90444.4737.2526.342H ̄HMDI ̄bam0.71745.7945.6224.0801)bam:原料竹材bamboorawmaterialsꎻA ̄bam:碱预处理竹材alkalipretreatedbambooꎻH ̄bam:热水预处理竹材hotwaterpretreatmentbambooꎻC ̄bam:炭化竹材carbonizedbambooꎻA ̄HMDI ̄bam:碱预处理 ̄HMDI改性竹材alkalipretreatment ̄HMDImodifiedbambooꎻH ̄HMDI ̄bam:热水预处理 ̄HMDI改性竹材hotwaterpretreatment ̄HMDImodifiedbambooꎬ下同sameasinfollowing由表1可知ꎬ竹材经过热水处理后ꎬC元素从43.788%升至45.671%ꎬ但N元素由0.122%变为0.117%ꎬ几乎没什么变化ꎮ改性后ꎬ样品H ̄HMDI ̄bam和A ̄HMDI ̄bam中的N的质量分数分别增加至0.717%和0.904%ꎬ说明HMDI成功接枝到样品表面ꎮ并且样品A ̄HMDI ̄bam的HMDI负载量(6.342mmol/cm2)高于样品H ̄HMDI ̄bam(4.080mmol/cm2)ꎬ说明样品碱预处理后A ̄bam表面与HMDI反应的羟基数量更多ꎬ有利于接枝反应ꎮ第1期高和ꎬ等:异氰酸酯改性竹材表面及其抗蚀性能研究49㊀2.1.2㊀FT ̄IR分析㊀以水作为引发剂ꎬHMDI能迅速与竹材表面游离羟基反应ꎬ生成氨基甲酸酯ꎬ在竹材表面形成网状结构ꎬ使竹材表面覆盖一层疏水性基团ꎬ同时减少竹材表面游离羟基的数量[11]ꎮ图1为样品的红外光谱图ꎬ由图可见所有样品在3400cm-1都有较大的 OH吸收峰ꎬ2800~3000cm-1附近为亚甲基吸收峰ꎬ且接枝HMDI后的样品(H ̄HMDI ̄bam和A ̄HMDI ̄bam)在3400cm-1处的羟基峰明显减小ꎬ表明纤维表面的自由羟基数量减少ꎮ样品H ̄bam和A ̄bam在1720cm-1处的羰基峰明显减小ꎬ说明两种预处理的方法都能有效脱除一定量的半纤维素和木质素ꎻ而接枝HMDI后的样品在1720cm-1附近的羰基峰又重新出现ꎬ是因为反应生成了氨基甲酸酯重新引入了羰基[12]ꎮ样品H ̄HMDI ̄bam和A ̄HMDI ̄bam在3337.7cm-1处出现N H的伸缩振动峰ꎬ且在1621和1258cm-1处出现酰胺键峰和醚键(酯类)峰进一步证明了氨基甲酸酯的生成[13]ꎬ说明HMDI已成功连接到竹材的表面ꎮ2.1.3㊀BET分析㊀图2中为H ̄HMDI ̄bam和A ̄HMDI ̄bam这两种具有代表性样品的吸附 ̄脱附曲线图ꎮ吸附与脱附曲线基本重合ꎬ并且在相对压力低于0.4的时吸附量很低ꎬ而接近饱和压力ꎬ吸附量明显上升ꎬ属于BDDT分类法的Ⅲ型等温线[14]ꎮ这说明样品颗粒内部孔隙很少ꎬ而外表面有一些能够引起毛细管凝聚的大孔ꎮ固体表面由于各种原因呈现凹凸不平的状态ꎬ而当凹坑深度大于凹坑直径时就会变成孔结构ꎬ孔的吸附水分行为因孔径而异ꎬ样品的主要孔隙结构参数见表2ꎮ㊀㊀㊀㊀㊀㊀㊀图1㊀多种改性竹材的红外图谱㊀㊀㊀㊀㊀㊀㊀㊀㊀㊀图2㊀样品的N2吸附 ̄脱附等温线㊀㊀㊀㊀㊀Fig.1㊀FT ̄IRspectraofmodifiedbamboos㊀㊀㊀㊀㊀Fig.2㊀N2adsorption ̄desorptionisotherms相对于原料竹材来说ꎬA ̄bam的孔体积和平均孔径分别减小至0.0603cm3/g和50.32nmꎬ主要是由于碱预处理过程中部分半纤维素和木质素被抽提出来ꎻH ̄bam经热水处理后部分半纤维素分解成小分子的糖类溶解出来ꎬ同样导致了样品孔体积和孔径的降低ꎬ分别减小至0.0572cm3/g和37.84nmꎻ炭化过程中ꎬC ̄bam样品的孔隙结构呈现出相似的变化趋势ꎬ这主要归结于样品中半纤维素和木质素的部分分解以及纤维素的软化ꎮ表2㊀各样品的物理结构特征Table2㊀Texturalpropertiesofbamboosamples样品㊀㊀samples㊀㊀比表面积/(m2 g-1)surfacearea孔体积/(cm3 g-1)porevolume孔径/nmporesizebam1.5920.063665.98A ̄bam2.1630.060350.32H ̄bam2.4230.057237.84A ̄HMDI ̄bam5.7100.042642.71H ̄HMDI ̄bam4.2270.039033.48C ̄bam2.3240.053617.16这3个过程都会破坏三组分的镶嵌结构ꎬ造成结构坍塌ꎬ结构坍塌对于孔体积大小的变化起主导作用[15]ꎮ而半纤维素和木质素析出ꎬ使得原有样品中有大量的小孔形成ꎬ从而使得样品颗粒内部的孔隙结构更为发达ꎬ造成样品A ̄bam和H ̄bam的比表面积增大ꎬ分别增加至2.163和2.423m2/gꎮ由于改性剂本身的发泡性会形成微细孔系层负载在改性材料表面ꎬ并对材料表面原孔道产生一定的填充作用ꎬ使50㊀林㊀产㊀化㊀学㊀与㊀工㊀业第39卷得改性后的样品A ̄HMDI ̄bam和H ̄HMDI ̄bam的平均孔径相比于预处理之后的样品分别降低了7.61和4.36nmꎬ而比表面积增大了3.547和1.804m2/gꎮ从上述分析可知ꎬ由于坍塌㊁改性和填充的多重作用ꎬ使得两种HMDI改性后的竹材比表面积增大ꎬ孔体积和孔径减小ꎬ孔的吸附水分的能力因孔径缩小而下降ꎬ这在一定程度上增强了材料疏水性能ꎮ2.1.4㊀FE ̄SEM分析㊀从图3中可以看出ꎬ相比于经过热水预处理(图3(a))和碱预处理(图3(b))的样品ꎬ经过异氰酸酯改性后ꎬ竹片能明显观察到HMDI接枝在竹纤维表面(图3(c)和(d)的表面)ꎬ在纤维表面形成局部无规则的絮状包裹ꎬ有效地减少了霉菌与竹材的接触几率ꎮ图3㊀各样品表面形态的SEM图(ˑ2000)Fig.3㊀SEMimagesofsamples2.2㊀吸湿性分析2.2.1㊀表面润湿性㊀各个样品在5s时的纵向接触角为:bam74.3ʎ㊁H ̄bam88.0ʎ㊁A ̄bam69.7ʎ㊁C ̄bam96.5ʎ㊁H ̄HMDI ̄bam100.3ʎ和A ̄HMDI ̄bam91.2ʎꎮ由此可见ꎬ改性后的H ̄HMDI ̄bam和A ̄HMDI ̄bam接触角相比预处理竹材分别提高了12.3ʎ和21.5ʎꎬ表面的疏水性增强ꎮ而A ̄bam接触角从74.3ʎ降低至69.7ʎꎬ是因为碱处理打断了部分半纤维素和木质素与纤维素之间的化学与物理连接ꎬ样品表面吸水性基团裸露ꎬ造成样品的表面润湿性增大ꎮ2.2.2㊀吸水率㊀表3为各个样品的吸水率ꎮ可以看出对照样品bam的吸水率为68.7%ꎬ而改性后的H ̄HMDI ̄bam和A ̄HMDI ̄bam分别为35.5%和41.9%ꎬ均在50.0%以下ꎮ说明改性之后竹材的整体的疏水性有一定程度的提升ꎮ综合来看ꎬH ̄HMDI ̄bam相对于其它样品来说有较低的表面润湿性和吸水率ꎮ竹材表面纤维本身含有大量的亲水性的羟基ꎬ改性之后大部分羟基基团被封闭ꎬ虽然会重新出现有一定亲水性的酰氨基结构ꎬ但由于HMDI中的环己烷的疏水结构存在ꎬ竹材的表面润湿性总体上会大幅度降低ꎬ使得改性竹材整体亲水性降低[16]ꎮ由于HMDI在纤维表面呈均匀的分布ꎬ其疏水性阻碍了水向深层纤维通道的渗透ꎬ因此吸水率也会明显降低ꎮ2.3㊀抗蚀性试验结果2.3.1㊀腐蚀等级分析㊀通过观察样品表面菌落的分布情况随时间的变化可以反映出样品的抗蚀性能ꎬ样品被腐蚀情况分级见表3ꎮ各样品的抗蚀实验结果如图4所示ꎮ表3㊀不同样品的吸水率及腐蚀情况Table3㊀Waterabsorptionandcorrosionlevelofsamples样品samples干质量/gdryweight湿质量/gwetweight吸水率/%waterabsorption腐蚀等级1)corrosiondegree表面霉菌斑点程度moldareaonsurfacebam1.472.4868.74>60%H ̄bam1.221.9660.6330%~60%A ̄bam1.192.0975.64>60%H ̄HMDI ̄bam1.071.4535.50~1~0A ̄HMDI ̄bam1.291.8341.91~10%C ̄bam1.161.4625.9001)抗菌实验第十天的表面霉菌分布情况surfacemolddistributionofantibacterialexperimenton10thday相比于其它样品ꎬ样品A ̄bam表面菌落生长速度最快ꎬ表面霉菌斑点超过60%ꎬ腐蚀程度为4级ꎮ可能是由于经过碱预处理后竹材表面中的一部分半纤维素和木质素脱离ꎬ而木质素本身具有一定的抗菌性ꎻ其次ꎬ低温碱性处理难以充分溶解出表面深层的糖低聚物㊁蛋白等霉菌营养成分ꎬ使得表面环境有第1期高和ꎬ等:异氰酸酯改性竹材表面及其抗蚀性能研究51㊀利于纤维素降解霉菌的生殖ꎬ从而使样品A ̄bam的腐蚀程度与速度比其它样品更大ꎮ对比A ̄bam与A ̄HMDI ̄bamꎬ可以看出改性之后的A ̄HMDI ̄bam表面菌落面积明显减小ꎬ霉菌斑点程度约10%左右ꎬ腐蚀等级为1级ꎬ可知HMDI的接枝阻碍了霉菌在竹材表面的生长ꎮ而热水预处理过程能够除去为霉菌提供营养的单糖㊁低聚糖和无机盐等组分[17]ꎬ抑制了霉菌的生长ꎬ从而提高了H ̄bam的抗腐蚀性ꎮ在此基础上ꎬ接枝HMDI后的H ̄HMDI ̄bam抗蚀性进一步提升ꎬ表面几乎观察不到里氏木霉的菌落ꎬ腐蚀等级为0~1级ꎬ与传统工业所用的炭化方法制得的竹材抗蚀性相当ꎮ炭化样品C ̄bam的水接触角只有96.5ʎꎬ低于H ̄HMDI ̄bamꎬ但其被腐蚀等级为0级ꎬ可能是因为炭化过程中竹材中的低聚糖㊁蛋白等营养物质会分解或蒸发逸出ꎬ从而表现出对真菌的生长繁殖的抑制ꎬ因此ꎬ竹材样品的表面亲水性和低聚糖等营养成分的含量共同决定了样品的耐腐蚀性ꎮ图4㊀不同样品腐蚀情况图Fig.4㊀Photographsofsamplesbeforeandaftercorrosionresistancetest2.3.2㊀FE ̄SEM分析㊀从SEM图(图5)中可以观察到抗蚀测试之后样品表面的微观变化ꎮ经过10天的培养ꎬ样品A ̄bam和bam的表面最为粗糙ꎬ纤维纹理被破坏严重ꎬ能明显看到霉菌腐蚀后留下的不规则痕迹ꎮ与A ̄bam和H ̄bam比较ꎬA ̄HMDI ̄bam和H ̄HMDI ̄bam基本保持了竹材的本征结构ꎬ未见明显霉菌腐蚀痕迹ꎬ这也与宏观状态下观察到的结果一致ꎮC ̄bam表面结构出现明显的孔隙和裂缝ꎬ主要是由于炭化过程中半纤维素的分解ꎬ以及挥发分的析出所造成的[10]ꎮ图5㊀抗腐蚀测试后各样品表面SEM图(ˑ500)Fig.5㊀SEMimagesofsamplesaftercorrosionresistancetest从宏观结果与扫描电镜观察到的情况中可以得知ꎬHMDI接枝到竹材表面确实可以影响霉菌在竹材上的生长ꎬ增加竹材的抗腐蚀性ꎬ减缓霉菌腐蚀速度ꎮ52㊀林㊀产㊀化㊀学㊀与㊀工㊀业第39卷3㊀结论3.1㊀以二环己甲烷4ꎬ4ᶄ ̄二异氰酸酯(HMDI)为改性剂ꎬ分别对热水预处理竹材(H ̄bam)和碱预处理竹材(A ̄bam)表面进行接枝改性得到改性竹材样品ꎮ由于HMDI的填充作用ꎬ使得H ̄HMDI ̄bam平均孔径和孔容积分别减小至0.0572cm3/g和37.84nmꎬ而孔的吸附水分能力因孔径下降而降低ꎻ同时氨基甲酸酯的形成使竹材表面亲水性羟基减少ꎬ环己烷疏水结构使竹材的表面润湿性降低ꎬ从而改性之后竹材的整体亲水性下降ꎮ其中样品H ̄HMDI ̄bam的纵向水接触角由74.3ʎ提升到100.3ʎꎬ吸水率从68.7%降低到35.5%ꎮ3.2㊀由于HMDI使竹材整体亲水性降低ꎬ破坏了里氏木霉生长所需的环境ꎮ同时HMDI的局部包裹也减小了竹材纤维与霉菌的接触ꎬ使得改性竹材在抗蚀效果中呈现优异的抗蚀性ꎮH ̄HMDI ̄bam表面几乎看不到菌落ꎬ被腐蚀等级为0~1级ꎬ与工业传统炭化防腐处理制备的竹材相当ꎮ该方法具有传统工业方法不具有的能耗低ꎬ加工时间短的优点ꎬ具有良好的应用前景ꎮ参考文献:[1]CHONGTHAMNꎬBISHTMSꎬHAORONGBAMS.Nutritionalpropertiesofbambooshoots:Potentialandprospectsforutilizationasahealthfood[J].ComprehensiveReviewsinFoodScience&FoodSafetyꎬ2011ꎬ10(3):153-169.[2]SHRESTHAK.DistributionandstatusofbamboosinNepal[R/OL].Xishuangbanna:BambooTrainingCourse/Workshop(1998 ̄05 ̄17) [2018 ̄03 ̄30].https:ʊwww.bioversityinternational.org/fileadmin/bioversity/publications/Web_version/572/ch29.htm.[3]LIUBBꎬZHANGSYꎬZHOUYYꎬetal.Mildewinbambooflourtreatedwithdifferentsolvents[J].JournalofZhejiangA&FUniversityꎬ2015ꎬ32(1):11-17.[4]MURRAYLJꎬDINCÂMꎬLONGJR.Hydrogenstorageinmetal ̄organicframeworks[J].ChemicalSocietyReviewsꎬ2009ꎬ38(5):1294-1314. [5]CHATTOPADHYAYDKꎬWEBSTERDC.Thermalstabilityandflameretardancyofpolyurethanes[J].ProgressinPolymerScienceꎬ2009ꎬ34(10):1068-1133.[6]BLATTMANNHꎬFLEISCHERMꎬBHRMꎬetal.Isocyanate ̄andphosgene ̄freeroutestopolyfunctionalcycliccarbonatesandgreenpolyurethanesbyfixationofcarbondioxide[J].MacromolRapidCommunicationꎬ2014ꎬ35(14)ꎬ1238-1254.[7]XUEFꎬJIADꎬLIYꎬetal.Facilepreparationofamechanicallyrobustsuperhydrophobicacrylicpolyurethanecoating[J].JournalofMaterialsChemistryAꎬ2015ꎬ3ꎬ13856-13863.[8]GAOLLꎬLIUYHꎬLEIHꎬetal.Preparationofsemirigidpolyurethanefoamwithliquefiedbambooresidues[J].JournalofAppliedPolymerScienceꎬ2010ꎬ116(3):1694-1699.[9]王相君.酯化改性木材的过程和性能研究[D].呼和浩特:内蒙古农业大学ꎬ2010:17-18.WANGXJ.Esterificationprocessandtheperformanceofesterifiedwood[D].Hohhot:InnerMongoliaAgriculturalUniversityꎬ2010:17-18. [10]GONGCꎬHUANGJꎬFENGCꎬetal.Effectsandmechanismofballmillingontorrefactionofpinesawdust[J].BioresourceTechnologyꎬ2016ꎬ214:242-247.[11]STANKOVICHSꎬPINERRDꎬNGUYENSBTꎬetal.Synthesisandexfoliationofisocyanate ̄treatedgrapheneoxidenanoplatelets[J].Carbonꎬ2006ꎬ44(15):3342-3347.[12]CHENJꎬKONGZWꎬJIAOJꎬetal.Preparationandcharacterizationofgraftmodifiedpoplarwoodpowderbu4ꎬ4  ̄methylenebis(phenylisocyanate)/γ ̄aminopropyltriethoxysilane[J].ChemistryandIndustryofForestProductsꎬ2013ꎬ33(1):1-7.[13]TANGQꎬHEJꎬYANGRꎬetal.Studyofthesynthesisandbondingpropertiesofreactivehot ̄meltpolyurethaneadhesive[J].JournalofAppliedPolymerScienceꎬ2013ꎬ128(3):2152-2161.[14]BRUNAUERSꎬDEMINGLSꎬDEMINGWEꎬetal.OnatheoryofthevanderWaalsadsorptionofgases[J].JournaloftheAmericanChemicalSocietyꎬ1940ꎬ62(7):1723-1732.[15]郝宏蒙.烘焙生物质疏水性能及热解特性研究[D].武汉:华中科技大学ꎬ2013:20-21.HAOMH.Thestudyonbiomasshydrophobicpropertyandpurolysischaracterictics[D].Wuhan:HuazhongUniversityofScienceandTechnologyꎬ2013:20-21.[16]李贤军ꎬ刘元ꎬ苏洪泽ꎬ等.高温炭化处理对木材平衡含水率的影响规律[J].林业实用技术ꎬ2008ꎬ2008(10):50-51.LIXJꎬLIUYꎬSUHZꎬetal.Effectofhightemperaturecarbonizationontheequilibriummoisturecontentofwood[J].PracticalForestryTecgnologyꎬ2008ꎬ2008(10):50-51.[17]徐干君ꎬ彭万喜ꎬ吴海刚ꎬ等.水抽提对尾巨桉木材表界面性质的影响[J].科技创新导报ꎬ2009(10):124-126.XUGJꎬPENGWXꎬWUHGꎬetal.Effectofwaterextractionontheinterfacepropertiesofthewoodtable[J].ScienceandTechnologyInnovationHeraldꎬ2009(10):124-126.。
医学英语写作与翻译
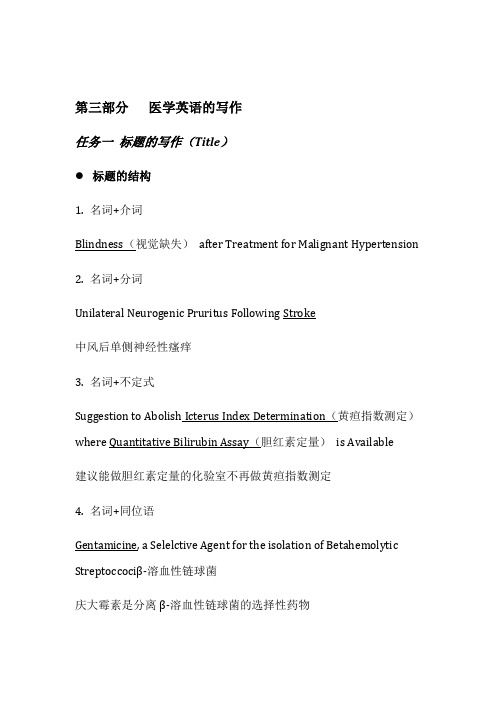
第三部分医学英语的写作任务一标题的写作(Title)标题的结构1. 名词+介词Blindness(视觉缺失)after Treatment for Malignant Hypertension 2. 名词+分词Unilateral Neurogenic Pruritus Following Stroke中风后单侧神经性瘙痒3. 名词+不定式Suggestion to Abolish Icterus Index Determination(黄疸指数测定)where Quantitative Bilirubin Assay(胆红素定量)is Available建议能做胆红素定量的化验室不再做黄疸指数测定4. 名词+同位语Gentamicine, a Selelctive Agent for the isolation of Betahemolytic Streptocc ociβ-溶血性链球菌庆大霉素是分离β-溶血性链球菌的选择性药物5. 名词+从句Evidence that the V-sis Gene Product Transforms by Interaction with the Receptor for Platelet-derived Growth Factor血小板源性生长因子.V-sis 基因产物由血小板生成因子受体相互作用而转化的依据6. 动名词短语Preventing Stroke in patients with Atrial Fibrillation心房纤维性颤动心旁纤颤患者中风预防Detecting Acute Myocardial Infarction(急性心肌梗死)byRadio-immunoassay for Creative Kinase(酐激酶)用放射免疫法测定酐激酶诊断急性心肌梗死7. 介词短语On Controlling Rectal Cancer8. 陈述句Dietary Cholesterol is Co-carcinogenic协同致癌因素for Human Colon Cancer9. 疑问句Home or Hospital BirthsIs Treatment of Borderline Hypertension Good or Bad?注意副标题的作用1.数目:Endoluminal Stent-graft 带支架腔内搭桥for Aortic Aneurysms动脉瘤: A report of 6 cases带支架腔内搭桥治疗动脉瘤的六例报告2.重点:Aorto-arteritis 大动脉炎Chest X-ray Appearance and Its Clinical Significance大动脉炎胸部X线表现及临床意义3.方法:Gallstone Ileus(胆结石梗阻): A Retrospective Study 4.作用:Carcinoembryonic Antigen in Breast-cancer Tissue: A useful prognostic indictor乳腺癌组织中癌胚抗原——一种有用的预后指示5.疑问:Unresolved—Do drinkers have less coronary heart disease? 6.连载顺序:Physical and Chemical Studies of Human Blood Serum: II. A study of miscellaneous Disease conditions人类血清的理论研究:II. 多种病例的研究7.时间:A Collaborative 综合Study of Burn Nursing in China: 1995-1999常见标题句式举例1. 讨论型:Discussion of/ on; An approach to; A probe into; Investigation of; Evaluation of / on汉语中的“初步体会”、“试论”、“浅析”之类的谦辞可以不译。
2195铝锂合金在N2O4中的浸泡腐蚀研究

第50卷第1期2021年1月应用化工Appeoed ChemocaeIndusioyVoe.50No.1Jan.20212195铝锂合金在N2O4中的浸泡腐蚀研究郭一,黄智勇,金国锋,田干(火箭军工程大学导弹工程学院,陕西西安710000)摘要:针对液体推进剂在长期贮存中对贮箱材料的腐蚀问题,研究NO*、含6%水的NO*以及30%HNO3三种介质与2195铝锂合金的相容性。
结果表明,三者的腐蚀速率依次增大,其中在NO*中相容性良好,在前期几乎不发生腐蚀,浸泡90d后,可以在试件的表面发现点蚀坑&在含6%水的NO*中,腐蚀由点蚀引起,腐蚀坑逐渐变大,扩展成面;在30%HNO3中,由点蚀逐步扩展形成剥落腐蚀。
三种介质的腐蚀产物均为ACH2O)6(NO3)3(H2O)3;随着腐蚀的加剧,2195铝锂合金的力学性能逐渐下降&关键词:2195铝锂合金;NO*;HNO3;点蚀;剥落腐蚀中图分类号:TQ050.4d1;TG172.2文献标识码:A文章编号:1671-3206(2021)01-0056-05 Stiidy on immersion corrosion of2195Al-Lt alloy in N2O4GUO Y-,HUANG Zhi-goog,JIN Guo-geeg,TIAN Gan(Missile Engineering Colleye,Rocket Force University of Engineering,Xi*an710000,China)Abstract:Aiming vt tha cooosion of liquid pmp/lant to tank materials in long-term storaga.Tha cooosion dfects of NO*,N2O4containing6%watar and30%HNO3on tha2195Al-Pi dlvy were studied.Tha m-sults show th/t there is almost no cooosion in tha exOy stagy,and after immersion for90d,pitting pits can ba found on tha suOzco of tha test piece which mexns NO*h/s good compdib/ity with NO*.In NO* containing6%wdag cooosion is caused by pitting cofosion,and cooosion pits becoma largar and widvr; in30%HNO3,cooosion A stably and spd/ng corrosion formed-Tha cooosion products of tha threa medio are At(H q O)6(NO3)3(H q O)3-With tha increase of cooosion,tha mechanical pmpeOies of2195Al-Pi dlvy decrexso gmdudty-Key wop!s:2195Al-Pi dlvy;NO*;HNO3;p/ting;exfoliation coo osion2195铝锂合金在空气动力学领域被广泛认为是一种理想的轻质高强度结构材料[1]&在铝合金中,每添加1%的锂,可使铝合金密度降低3%,弹性模量提高6%[2]&由于NO*的蒸汽压大、沸点低(21.13C)、极易挥发,并具有强烈的刺激性、毒性和腐蚀性,给材料的腐蚀研究工作带来了困难⑺句。
砂沉积模拟工况下深水油气管道腐蚀行为及缓蚀剂评价研究

0引言
随着油气工业不断发展,海底管道已经成为油气
田开发中海上油气集输的“生命线”% X65管线钢具
有良好的抗拉强度,低温冲击韧性也相对较高,同时 具有良好的焊接性能,已在我国海底油气管道的建设
基金项目:国家科技重大专项(No. 2016ZX05028-004) 作者简介:王赟(1991—),女,硕士,主要从事缓蚀剂评价方面的研究%
工况的缓蚀效率达83.52% ;而试样被表面砂覆盖后,缓蚀剂有效作用浓度下降,缓蚀效率降低%缓蚀剂ZDE加入
后,其作用于碳钢表面,形成一层保护膜,使得金属/溶液界面处的电荷转移电阻增加,腐蚀反应的发生需要克服较
大的阻力,进而抑制了阴阳极腐蚀反应的进行%
关键词 X65管线钢;缓蚀剂;砂沉积;电化学阻抗谱
摘要 采用腐蚀浸泡和电化学方法研究了砂在腐蚀模拟介质中对X65管线钢的腐蚀行为影响及缓蚀剂ZDE的缓
蚀性能%实验结果表明,砂沉积使得X65钢在腐蚀模拟介质中的腐蚀速率增加,腐蚀加重% ZDE属于一种混合型
缓蚀剂,在模拟盐溶液中对X65钢的腐蚀表现出了一定的阻碍作用%在60l ,ZDE加注浓度为0.15 g/L时,无砂
第6卷第4期
2019年8月
海洋工程装备与技术
OCEAN ENGINEERING EQUIPMENT AND TECHNOLOGY
Vol. 6 , No. 4 Aug. , 2019
砂沉积模拟工况下深水油气管道 腐蚀行为及缓蚀剂评价研究
王赟1向婉倩1王贝1,张雷1李清平2姚海元2路民旭1
(1.北京科技大学新材料技术研究院,北京100083; 2.中海油研究总院,北京100028)
中图分类号:TG174
文献标志码:A
文章编号:2095-7297(2019)04-0625-07
螺纹钢表面锈蚀的实验研究

螺纹钢广泛使用在各类建筑 中,建筑工地上 随处可见 生 了锈 的螺 纹 钢筋 .生 了锈 的钢 筋 会 削 弱它与混凝土的结合程度 ,严重时可影 响到钢筋 强 度 ,甚 至 影 响建 筑 物 寿 命 … .为 了提 高 我 国 建 筑安全标准 , 纹钢 .与 微合金 强 化钢筋 相 比 , 采 用轧后 水 冷强 化 成 本低 ,很 多 钢铁 企 业 采 用 轧 后穿水冷却工艺 j.但穿水冷却 后的钢筋更容易 生 锈 J,影 响外 观 和强 度 ,导 致 销 售 困难 ,成 为 加 速 冷却钢 筋 的一个 瓶颈 问题 .本 文针对 这一 问题 , 结 合现 场生 产工艺 ,在 避免 大 幅度增 加成本 、不 增 加专门工序环节 的前提下 ,找到一种提高螺纹钢 防锈 性能 的方 法 .
1 实 验研 究
1.1 实验材 料 选 取钢 种为 400 MPa级 的 O16 mm螺 纹钢 筋
(成 分 见 表 1),削 去 表 面 氧 化 皮 ,切 割 成 四 组 100 mm 长 的 试 样 ;选 取 体 积 分 数 为 3% 的 H 0 水 溶液 作为 氧化 剂. 1.2 实验 过程
An Experim ental investigation on rust—-eaten of rebar surface
Gu Zhengman ,Li Yanjie ,Deng Qian。,Chen Yi ,Liu Xianghua。
1Cr18Ni9Ti与1Cr13不锈钢的焊接试验[1]
![1Cr18Ni9Ti与1Cr13不锈钢的焊接试验[1]](https://img.taocdn.com/s3/m/1e02552eb4daa58da0114a27.png)
为 1Cr13 马氏体不锈钢母材拉伸断口微观组织形 貌 ,断口中韧窝小且多 , 属于韧性断 裂. 图 2c 为 1Cr18Ni9Ti 奥氏体不锈钢和 1Cr13 马氏体不锈钢焊 接接头拉伸断口微观组织形貌 ,韧窝和撕裂棱混合 共存 ,但撕裂棱在断口中所占的比例较小 ,仍属于韧 性断裂. 断口中 ,韧窝的大小和深度各不相同 ,韧窝 的大小和深度相差悬殊 ,这与焊接 HAZ 晶粒大小不 均匀以及析出第二相粒子的数量 、形状和分布有 关[4] . 2. 2 焊接接头力学性能 2. 2. 1 焊接接头的显微硬度
86
焊 接 学 报
第 30 卷
从图 1 中可以看出 ,在靠近奥氏体区 ,得到奥氏 体组织. 在马氏体侧形成板条状马氏体[3] ,因为马 氏体不锈钢含铬量高 ,淬透性好 ,在焊缝金属从液态 降温时 ,接近母材 ,冷却速度快 ,空冷时形成了马氏体 组织. 在焊接接头的熔合区得到典型的柱状晶组织. 2. 1. 2 断口 SEM 观察及分析
5
缝区
2. 3. 1 焊接接头的交流阻抗对比分析 图 4 为焊接接头各区域的交流阻抗谱. 从图 4
中可以看出 ,阻抗弧由小到大的试样编号为 2 号 , 5 号 ,4 号 ,3 号 ,1 号 ,阻抗弧越小 ,相对应的低频阻 抗幅值越小 ,所以腐蚀速度越快 ,所以腐蚀率由大到 小的变化顺序为 2 号 ,5 号 ,4 号 ,3 号 ,1 号. 这是由 于在靠近奥氏体 、马氏体母材的热影响区 ,得到单相 的奥氏体 、马氏体组织 ,耐蚀性相对于双相或多相组 织要强 ;在焊缝区 ,马氏体不锈钢和奥氏体不锈钢焊 接熔合的过程中 ,两种不锈钢所含的镍 Ni ,Cr ,Ti 等 元素扩散转移 ,化学成分不均匀性使焊缝区可能得 到双相或多相的混合组织 ,从而使焊缝的耐腐蚀性
Erosion-Corrosion of Stainless Steels

30C ORROSION—JANUARY 2005Submitted for publication July 2003; in revised form, April 2004. ‡ Corresponding author. E-mail: dxhe@. * Institute of Metal Research of Chinese Academy of Sciences, 72Wenhua Road, Shenyang, People’s Republic of China, 110015. Present address: Max Planck Institute for Metals Research, Heisenbergstraße 3, D-70569 Stuttgart, Germany.** Institute of Metal Research of Chinese Academy of Sciences, 72Wenhua Road, Shenyang, People’s Republic of China, 110015. (1)UNS numbers are listed in Metals and Alloys in the Unifi ed Num-bering System , published by the Society of Automotive Engineers (SAE International) and cosponsored by ASTM International.Erosion-Corrosion of Stainless Steelsin Aqueous Slurries—A Quantitative Estimation of Synergistic EffectsD.D. He,‡,* X.X. Jiang,** S.Z. Li,** and H.R. Guan**ABSTRACTThe synergism between erosion and corrosion of stainless steels (SS) in 3.5 wt% sodium chloride (NaCl) + 0.5 N sulfuric acid (H 2SO 4) + 30 wt% aluminum oxide (Al 2O 3) dual-phase fl u-id has been studied by means of a rotating cylinder electrode apparatus. The erosion/erosion-corrosion behavior of several SS, 1Cr13 (ferritic), Type 316L (austenitic [UNS S31603]), 0Cr14Ni5Mo (martensitic), and CD-4MCu (α+γ duplex), were investigated further to illustrate the synergistic mechanism. The experimental results showed that CD-4MCu had a higher erosion-corrosion resistance because of its excellent deforma-tion strengthening capability. By measuring and calculating each component of the synergistic interaction, it could be con-cluded that the removal of material mainly came from the me-chanical damage in the condition of this study. Based on the classifi cation of erosion-corrosion regimes with respect to the ratio of erosion to corrosion rate, the synergistic mechanism of erosion-corrosion of SS in the condition of this study should be an erosion-dominated corrosion process.KEY WORDS: e rosion-corrosion, dual-phase fl uid, stainless steel, synergistic interactionINTRODUCTIONThe synergistic effect of erosion and corrosion on me-tallic degradation,1-8 as well as on metallic or cermetcoatings used in an erosion-corrosion environment,9-10 has been receiving increasing attention in recent years because of the widespread occurrence of such problems in various materials processing industries. In these conditions, with the appearance of botherosion and corrosion, materials selection could be a major problem and, in many cases, was only carried out on the basis of empirical experience. The wastage rates of the material can be signifi cantly higher than the combined effects of erosion and corrosion acting separately. The phenomena of synergistic effect of ero-sion and corrosion in aqueous environments (liquid-solid dual phases or liquid-solid-gas multi-phases) are more common than that at high temperature(gas-solid dual phases). Although some investigations focused on the erosion-corrosion processes and dis-cussed the possible mechanism of damage, the syner-gistic mechanism of erosion and corrosion in aqueous environments is not well understood.Slurry erosion-corrosion usually occurs in tur-bulent fl ow conditions. Commonly used apparatus in studies of erosion-corrosion are the pipe loop, the impinging jet, the slurry pot, and the rotating cylinder electrode.5-6 Usually, the materials used for the blades or turbulent parts are carbon steels, cast steels, and stainless steels (SS). The SS selected in this investiga-tion are 1Cr13 (ferritic), Type 316L (austenitic [UNS S31603](1)), 0Cr14Ni5Mo (martensitic), and CD-4MCu (α+γ duplex). The erosion and erosion-corrosion be-havior of these SS were studied using a rotating cylin-der electrode (RCE) apparatus. Each component of the synergistic interaction, such as weight loss of steels caused by pure erosion or pure steady electrochemical corrosion, and weight loss increment caused by the0010-9312/04/000007/$5.00+$0.50/0© 2005, NACE InternationalC ORROSION—Vol. 61, No. 131synergy of erosion and corrosion, was measured or calculated. The synergistic mechanism of erosion and corrosion was discussed briefl y.EXPERIMENTAL PROCEDURES Experimental MethodsA RCE system, used in this investigation, was based on the experimental setup reported by Zhou,et al.5 Some modifications had been made to increase the area ratio of the reference electrode and working electrode, and the confi guration of three electrodeswas changed slightly.11Polytetrafluoroethylene (PTFE) was used for all electrode components except the out-er cylinder, which was made from nylon. The rotating speed could be changed from 1.02 m/s to 8.75 m/s step by step. An EG&G Princeton 332† system was used for all electrochemical measurements. A satu-rated calomel electrode (SCE) and a piece of platinum wire (1 mm in diameter) were used as the reference electrode and the counter electrode, respectively. The schematic illustration of this apparatus can be found elsewhere.7 The working electrodes were fabricated from cylindrical SS, with compositions and micro-hardness (Hv) values shown in Table 1. The working area of the test specimen was 12.56 cm 2. Microstruc-tural characterization of these materials revealed fer-ritic, austenitic, martensitic, and α+γ duplex phases for 1Cr13, Type 316L, 0Cr14Ni5Mo, and CD-4MCu, respectively. Prior to testing, the specimen surface was polished to 600 grit with silicon carbide (SiC) abrasive paper, degreased with acetone, dried with air, and weighed.The standard corrosion test was carried out in static solution, and the corrosion rate was calculated by electrochemical parameters, e.g., corrosion poten-tial and current. The erosion/erosion-corrosion test was carried out in both benign and aggressive dual-phase slurry, H 2O + 30 wt% aluminum oxide (Al 2O 3) and 3.5 wt% sodium chloride (NaCl) + 30 wt% Al 2O 3 (or 3.5 wt% NaCl + 0.5 N sulfuric acid [H 2SO 4] + 30 wt% Al 2O 3). The reason for introducing H 2SO 4 into the solu-tion was to accelerate the corrosion process and shorten the test time. The slurry was prepared with Analar †-grade chemical regents, distilled water, andcommercial 100-mesh corundum sand (Al 2O 3). The granularity of the corundum particles was laid in the range of 80 mesh to 100 mesh (125 µm to 160 µm) and their properties were described in detail else-where.11 Before each test, the solution was deaerated for more than 6 h by N 2 purging and then introduced into the RCE. Continuous deaeration was maintained during the test by bubbling nitrogen through the solu-tion. All tests were carried out at room temperature (~25°C). Both Al 2O 3 and solution was changed after 63 min at 5.28 m/s and 38 min at 8.75 m/s, which corresponded to a rotation distance of 20 km with respect to a point on the working surface of the sam-ple. Before and after erosion/erosion-corrosion test, the specimen weight was measured using an analyti-cal balance with a sensitivity of 0.1 mg, and the micro-hardness of specimens was measured with a Shimadzu † micro-hardness tester.All erosion or erosion-corrosion testing were re-peated three to fi ve times; three times were chosen if they were quite consistent with each other, or more duplicates were introduced to get a comparable and reliable results. In the meantime, an assumption was made that porously attached corrosive product could be completely removed by the erosion process; there-fore, the sample surface was cleaned after erosion-corrosion testing in the same way as that used before testing, prior to the weight measurement.Experimental ResultsErosion Behavior — The erosion behavior of four SS was tested in a Al 2O 3 + H 2O dual-phase slurry (benign environment) at two particle velocities of 5.28 m/s and 8.75 m/s. The erosion rates of SS are illustrated in Figure 1. The Type 316L SS had the highest weight loss at both velocities, which was ap-proximately twice the value for the others. At a lower velocity, there is no major difference in the weight loss among 1Cr13, 0Cr14Ni5Mo, and CD-4MCu. But at a higher velocity, the duplex phase steel showed good resistance. In ascending order, the sequence of weight loss was CD-4MCu, 1Cr13, 0Cr14Ni5Mo, and Type 316L SS. In the benign environment, the erosion resistance of SS would depend principally on the me-chanical properties of the materials, especially their hardness here, when they were exposed to the benign environment.† Trade name.TABLE 1Chemical Composition and Micro-Hardness of SS (wt%)CCrNiMo Cu SiMnNFeHvFerritic SS 1Cr130.1 13.5 0.2 — — 0.4 0.1 — Bal. 530Austenitic Type 316L SS 0.03 17.2 13.1 2.1 — 0.8 1.0 — Bal. 200 Martensite SS 0.00 12.8 5.7 1.7 0.2 0.3 0.5 — Bal. 410 0Cr14Ni5MoDuplex SS CD-4MCu 0.06 25.7 5.4 2.0 3.0 1.5 0.7 Trace Bal. α-235γ-280Composition (wt%)32C ORROSION—JANUARY 20053. At lower velocities, the performance of Type 316L SS here was completely different from that in 3.5% NaCl + 30% Al 2O 3. Its erosion-corrosion resistance was much better than 1Cr13 and 0Cr14Ni5Mo steel, and its weight loss approached that of CD-4MCu. The erosion-corrosion resistance of CD-4MCu is the best among all steels at this speed. Correspondingly, at higher velocities, both Type 316L SS and CD-4MCu steels had higher weight loss in the erosion-corrosion process than those at lower velocities. But CD-4MCu still sustained better performance under this condi-tion, especially after a long exposure time, for exam-ple, after 104 min (three cycles).SYNERGISTIC EFFECT AND ITS MECHANISMAnalysis of Experimental ResultsIn all the dual-phase slurries, H 2O + 30% Al 2O 3, 3.5% NaCl + 30% Al 2O 3, and 0.5 N H 2SO 4 + 3.5% NaCl + 30% Al 2O 3, the erosion or erosion-corrosion behavior of four SS could be summarized briefl y. The 1Cr13 and 0Cr14Ni5Mo steels had similar performance in all erosion/corrosion tests. Their weight losses increased with the increase in corrosion of the aggressive media and the velocity of impacting particles.The hardness of Type 316L SS is not very high, but its concentration of Ni + Cr is on the top, in com-parison to the other three alloys. It could be expected that Type 316L SS would be vulnerable to mechanical (erosion) damage and be highly resistant to a corrosive environment. This is verifi ed by the experimental re-sults. At a higher velocity of 8.75 m/s, Type 316L SS had the last place in the ascending sequence of ero-sion (-corrosion) resistance of those four alloys in H 2O+ Al 2O 3, but had the first place in the strong corrosive media of H 2SO 4 + NaCl + Al 2O 3. That means that the stronger the corrosion of the media, the better perfor-mance that the Type 316L SS had in this investiga-tion when compared with others. At a lower velocity of 5.28 m/s, the Type 316L SS had the highest weight(a)(b)FIGURE 1. Weight loss of steels vs exposure time with different velocity in H 2O + Al 2O 3.FIGURE 2. Weight loss of steels with different velocities in NaCl + Al 2O 3 slurry.Erosion-Corrosion Behavior — In Cl –-containing dual-phase slurry (3.5% NaCl + 30% Al 2O 3), the aver-age weight loss of materials was also linearly propor-tional to the exposure time. The average weight loss per 63 min (20 km) of CD-4MCu, 1Cr13, 0Cr14Ni5Mo, and Type 316L SS was 0.42, 0.57, 0.69, and1.54 mg/cm 2-h at a lower velocity; the average weight loss per 38 min (20 km working distance) at a higher velocity was2.27, 2.55,3.28, and 3.47 mg/cm 2-h, respectively (Figure 2). Excluding the duplex phase steel, the average weight loss of the other three SS has the same order as their respective hardness.Among the alloys 1Cr13, 0Cr14Ni5Mo, and Type 316L, the ferritic 1Cr13 had the highest micro-hardness and was found to lose the least weight.Another erosion-corrosion test was carried out in a stronger corrosive dual-phase slurry of H 2SO 4 (3.5% NaCl + 0.5 N H 2SO 4 + 30% Al 2O 3) at two velocities. Theweight-loss curves of the SS are illustrated in FigureC ORROSION—Vol. 61, No. 133loss in both benign (H 2O) and mild (3.5% NaCl + H 2O) corrosive media. It was much better in strong corro-sive media (0.5 N H 2SO 4 + 3.5% NaCl) and got close to the performance of duplex-phase steel, where both of them showed high erosion-corrosion resistance. That means that Type 316L SS is resistant to erosion or erosion-corrosion in strong corrosive media and at low velocity, in which case the damage of materials was not mainly caused by mechanical damage.In general, dual-phase CD-4MCu steel had the best performance at high rotation speed, especially at high rotation speed and in strong corrosive media. In 0.5 N H 2SO 4 + 3.5% NaCl + 30% Al 2O 3, there was no signifi cant difference between CD-4MCu steel and Type 316L SS at low velocity, but the former was bet-ter after a long-term exposure at high velocity. The reason for the superior performance under strong corrosive media and low velocities may have been aresult of the better corrosion resistance (due to the(a)(b)FIGURE 3. Weight loss of steels vs exposure time with different velocities in H 2SO 4 + NaCl + Al 2O 3 slurry.FIGURE 4. Sectional micro-hardness of steels.higher nickel and chromium content in these two steels). Moreover, under more severe conditions, CD-4MCu exhibited the best behavior not just because of its high corrosion resistance, but also its highwork-hardening capability (Figure 4). Micro-hardness testing indicated that the dual-phase has very high work-hardening capability, which was demonstrated in other experiments. CD-4MCu exhibited high work-hardening capability only at high external force, in-cluding long-term exposure to particle impacting. This was consistent with its result of steady-state corrosive wear in 69% phosphoric acid (H 3PO 4).12-13Regime Defi nitions and Calculation of SynergyReferring to the investigation methods and prin-ciples of corrosive wear and the characteristics of the erosion-corrosion itself, erosion-corrosion rate and its components were measured and calculated.7-8,12-15 The erosion-corrosion process of four alloys in a strong corrosive environment (0.5 N H 2SO 4 + 3.5% NaCl + 30% Al 2O 3), at both 5.28 m/s and 8.75 m/s, was con-sidered for the calculation. The total weight loss of erosion-corrosion (W), which is the removal of SS in dual-phase slurry caused by erosion-corrosion pro-cesses, should be composed of the following:—pure mechanical damage (no electrochemical corrosion) or pure erosion W e—pure steady electrochemical corrosion W c—increment/synergy of erosion and corrosion ΔW The increment of the synergistic interaction of erosion and corrosion is composed of two aspects, the increment of corrosion, ΔW c , due to mechanical dam-age, and the increment of erosion, ΔW e , due to electro-chemical corrosion.15 Others, such as the protection or degradation deceleration of material due to electro-chemical corrosion in mechanical damage (e.g., the corrosion products restrain the mechanical damage of materials because of its lubricative effect sometimes) and the increment of local electrochemical corrosion due to the fretting process (e.g., the weight loss comes from crevice corrosion), can be ignored.15-16 So the34C ORROSION—JANUARY 2005total weight loss of materials in the erosion-corrosion process W can be described as Equation (1): W W W W e c =++∆(1)where:∆∆∆W W W e c =+(2)Erosion-corrosion testing was carried out in 30 wt% Al 2O 3 + 3.5 wt% NaCl + 0.5 N H 2SO 4 slurry at two par-ticle velocities, 5.28 m/s and 8.75 m/s. The erosion-corrosion rates of SS at two velocities were obtained. The testing period was four cycles, 4 × 63 min at 5.28 m/s and 4 × 38 min at 8.75 m/s. During the test, the solution, including sand, was replaced for each cycle. The pure erosion rate, W e , was obtained in 30% Al 2O 3 + H 2O. In this case, it was supposed that there was no corrosive media in the slurry of 30% Al 2O 3 + H 2O, and there was no difference after replac-ing H 2O with 3.5% NaCl + 0.5 N H 2SO 4 solution. The pure steady electrochemical corrosion W c was carried out under the standard corrosion test. The corrosionrate due to erosion-corrosion W cʹ was calculated by the corrosion current in Equation (3):′=×W M nFi c (3)where M was the equivalent molecular weight, n was the equivalent electrons in reaction, F was Faraday’s constant and equal to 96,500 coulomb per molar electrons, and i was the corrosion current in the ero-sion-corrosion process. The erosion rate in the ero-sion-corrosion process W e ʹ could be calculated by subtracting the corrosion rate W c ʹ from the total ero-sion-corrosion rate W. From the above defi nitions, two more equations could be obtained: ′=×W W W c c c ∆ (4)′=+W W W e e e ∆(5)And then:W W W c e =′+′(6)From the experimental and calculated results and previous analysis in the literature, it is proposed that the most appropriate regimes in terms of the ratio of the corrosion to erosion rate could be classifi ed:14 110./,erosion dominated ′′≥W W e c(7) 2101./,corrosion-assisted erosion >′′≥W W e c(8)3101./.,erosion-assisted corrosio >′′≥W W e e n (9)401./.,corrosion dominated ′′<W W e c(10)It should be pointed out that the steady electrochemi-cal corrosion was preferably recognized as the purecorrosion in this study, although the erosion-corro-sion in single-phase pure water was used in some of the literature. It was found that there was a large dif-ference between the corrosion rates in these two ex-perimental methods. The corrosion rate in the former conditions were 0.08, 0.03, 0.04, and 0.03 mg/cm 2-h for 1Cr13, Type 316L, 0Cr14Ni5Mo, and CD-4MCu SS, respectively. However, in the latter conditions, the corrosion rates increase to 0.34, 0.22, 0.31, and 0.18 mg/cm 2-h. Both groups of those results were obtained at a fl uid velocity of 8.75 m/s. It can be said that the erosion did infl uence the corrosion pro-cess even in single-phase pure water, and this effect should increase with increasing fl uid velocity.Calculated ResultsLow Velocities of 5.28 m/s — At 5.28 m/s, the measured or calculated results of the erosion-corrosion rate and its components for SS are listed in Table 2, and the calculated ratios of each component to the total weight loss are listed in Table 3. As for the pure erosion in H 2O-Al 2O 3 (noncorrosive environment), there was no big difference among the erosion rates W e of four SS, although that of the CD-4MCu SS was a little bit lower. However, in the corrosive environ-ment, the erosion rate of ferritic 1Cr13 SS W e ʹ was much higher than the rate of the other three steels; the erosion increment due to corrosion ΔW e was sig-nifi cant and increased to 50% of the total erosion-corrosion rate. The increment due to the synergistic effect ΔW was 60% of the total weight loss. The ero-sion increment due to electrochemical corrosion W e ʹ and the synergistic interaction ΔW of Type 316L,0Cr14Ni5Mo, and CD-4MCu SS were not as much as that of 1Cr13. This may result from the difference in the corrosion resistance of those steels. In 3.5 wt% NaCl + 0.5 N H 2SO 4 + 30 wt% Al 2O 3, the corrosion re-sistance of Type 316L and CD-4MCu SS were the best and that of the 1Cr13 was the worst (pure corrosion, W c in the Table 2).Both the pure steady corrosion W c and the cor-rosion component in the erosion-corrosion W cʹ were smaller than the corresponding erosion component W e or W e ʹ. Furthermore, in the erosion-corrosion pro-cess, the ratios W e ʹ/W cʹ of erosion (W e ʹ) to corrosion (W cʹ) were 5.4, 11, 4.8, and 4.8 for 1Cr13, Type 316L, 0Cr14Ni5Mo, and CD-4MCu SS, respectively. Accord-ingly, the removal of materials at 5.28 m/s mainly came from the mechanical damage. Referring to the classifi cation of erosion-corrosion regimes based on the ratio of erosion to corrosion rate, the synergistic mechanism of erosion-corrosion of SS under this con-dition could be attributed to corrosion-assisted ero-sion regime (Regime 2, Equation [8]). For instance, thecorrosion component in erosion-corrosion W cʹ of Type 316L SS was just 8.3% of the total weight loss W.High Velocities of 8.75 m/s — At 8.75 m/s,the measured or calculated results of the erosion-corrosion rate and its components of SS are listed in Table 4, and the calculated ratios of each component to the total weight loss are listed in Table 5 as well. When compared to the results at low velocity, theratio of both pure corrosion and corrosion in erosion-corrosion to the total weight loss of materials was smaller. Both the increment of erosion and the total synergistic increment of Type 316L, 0Cr14Ni5Mo, and CD-4MCu increased with increasing velocity. More-over, the synergistic increments of erosion-corrosion for 1Cr13 and 0Cr14Ni5Mo SS were 50% of the total weight losses, respectively.Similarly, the pure steady corrosion Wcor the cor-rosion component in erosion-corrosion Wcʹ was smaller than the pure erosion and the erosion component in synergistic interaction, respectively. In the erosion-corrosion process, the ratios Weʹ/W cʹ of erosion to cor-rosion were 2.6, 11, 4.6, and 8.1 for 1Cr13, Type 316L, 0Cr14Ni5Mo, and CD-4MCu SS, respectively. Accord-ingly, the removal of materials at 8.75 m/s mainly came from the mechanical damage. Referring to the classifi cation of erosion-corrosion regimes based on the ratio of erosion to corrosion rate, the synergistic mechanism of erosion-corrosion of SS at this condi-tion was similar to that at lower fl uid velocities and it was corrosion-assisted erosion regime. For instance, the corrosion in erosion-corrosion Wcʹ of Type 316L SS was just 8.2% of the total weight loss W.Synergistic Mechanism of Erosion and Corrosion In the erosion-corrosion experiments, Type 316L and CD-4MCu exhibited high corrosion resistance in both pure corrosion condition, and erosion and corro-sion acted simultaneously. In particular, the corrosion component in erosion-corrosion of Type 316L SS was approximately 8% at the two velocities. The removal of materials mainly came from the mechanical damage. Interestingly, the weight loss of CD-4MCu was lower at the higher velocity than that at the lower velocityin this study. The erosion-corrosion resistance ofSS at low velocity could be correlated to their micro-hardness. This is consistent with literature data.12 The results obtained in this study showed that erosion and corrosion promoted each other and accel-TABLE 2Erosion-Corrosion Rate of SS at 5.28 m/s (mg/cm2-h) in a Slurry of 3.5 wt% NaCl + 0.5 N H2SO4+ 30 wt% Al2O3Alloys W Wc WeWcʹW eʹΔW cΔW eΔW1Cr13SS 1.54 0.08 0.53 0.24 1.30 0.16 0.77 0.93 Type 316L SS 0.72 0.03 0.57 0.06 0.66 0.03 0.09 0.12 0Cr14Ni5MoSS 0.69 0.04 0.45 0.12 0.57 0.08 0.12 0.20 CD-4MCu 0.52 0.03 0.38 0.09 0.43 0.06 0.05 0.11TABLE 3Ratio of Each Component to the Total Weight Loss (%, 5.28 m/s, 3.5 wt% NaCl + 0.5 N H2SO4+ 30 wt% Al2O3)Alloy Wc /W We/W Wcʹ/W W eʹ/W ΔW c/W ΔW e/W ΔW/W1Cr13SS 5.2 34.4 15.6 84.4 10.3 50.0 60.4 Type 316L SS 4.1 79.1 8.3 91.7 4.1 12.5 16.7 0Cr14Ni5MoSS 5.8 65.2 17.4 82.6 11.6 17.4 29.0 CD-4MCu 5.8 73.1 17.3 82.7 11.5 9.6 21.1TABLE 4Erosion-Corrosion Rate of SS at 8.75 m/s (mg/cm2-h) in a Slurry of 3.5 wt% NaCl + 0.5 N H2SO4+ 30 wt% Al2O3Alloy W Wc WeWcʹW eʹΔW cΔW eΔW1Cr13 SS 3.47 0.08 1.34 0.95 2.52 0.87 1.18 2.05 Type 316L SS 2.55 0.03 1.61 0.21 2.34 0.18 0.73 0.91 0Cr14Ni5Mo SS 3.28 0.04 1.57 0.58 2.70 0.54 1.13 1.67 CD-4MCu 2.27 0.03 0.95 0.25 2.02 0.22 1.07 1.29TABLE 5Ratio of Each Component to the Total Weight Loss (%, 8.75 m/s, 3.5 wt% NaCl + 0.5 N H2SO4+ 30 wt% Al2O3)Alloy Wc /W We/W Wcʹ/W W eʹ/W ΔW c/W ΔW e/W ΔW/W1Cr13SS 2.3 38.6 27.4 72.6 25.1 34.0 59.1 Type 316L SS 1.2 63.1 8.2 91.8 7.0 28.6 35.70Cr14Ni5MoSS 1.2 47.9 17.7 82.3 16.4 34.4 50.9 CD-4MCu 1.3 41.8 11.0 89.0 9.7 47.1 56.8C ORROSION—Vol. 61, No. 13536C ORROSION—JANUARY 2005erated the removal of materials, but it must be men-tioned that the weight loss of Type 316L in 0.5 N H 2SO 4-included slurry was much lower than that in both H 2O and 3.5% NaCl + 30% Al 2O 3 slurry at 5.28 m/s. In this case, the passivation fi lms devel-oped in H 2SO 4-included solution was promoting the erosion resistance of Type 316L SS, although the weight loss increased signifi cantly with the increase of velocity to 8.75 m/s. The corrosion and erosion processes would infl uence each other, and sometimes the synergistic effect might greatly increase the weight loss of materials. Corrosion might promote erosion by dissolving the work-hardened layer on the specimen surface as well as roughening the surface. The erosion might inhibit corrosion by making the fi brous struc-ture on the bottom of craters on which crystal planes of an interior dissolving rate are arranged.12,15A possible explanation 17-18 for the effect of corro-sion on erosion could be, on the one hand, that the adhesion between the corrosion products and sub-strate was not so strong and, consequently, these cor-rosion products were removed easily when impacted by particles and/or fl uid. On the other hand, the corrosion process, even if it is uniform corrosion or localized corrosion such as pitting, would damage the integrity and smoothness of the material surface. The rougher the materials’ surface, the easier the materi-als can be removed by the mechanical process.A possible explanation for the effect of erosion on corrosion could be, on the one hand, that erosion accelerated the corrosion process by damaging the passivation fi lms from the impacting of particles and, consequently, erosion exposed fresh metal to the cor-rosive media. On the other hand, the impact of parti-cles on the materials’ surface might have changed the uniformity of surface stress and electrochemistry due to elastic deformation, for example, leading to the for-mation of active corrosion sites such as impacting pitsFIGURE 5. Polarization curves of Type 316L SS at three fl uid velocities in the dual-phase slurry of 0.5 N H 2SO 4 + 3.5% NaCl + 30 wt% Al 2O 3.and protuberant lips. In the stress-concentrated or low-stress zone, there might be some corrosion cells due to the stress difference from its peripheral zone, which then would accelerate the corrosion process. The representation of this effect on the polarization of materials might be the shortening of the polarization range and the increasing of the polarizing current and polarization maintaining current (Figure 5).CONCLUSIONS❖ In 3.5% NaCl + 30% Al 2O 3 dual-phase slurry, the sequence of the erosion-corrosion resistance for SS could be CD-4MCu>1Cr13>0Cr14Ni5Mo>Type 316L. Their micro-hardness infl uenced the erosion-corrosion behavior.❖ In 3.5% NaCl + 0.5 N H 2SO 4 + 30% Al 2O 3 dual-phase slurry, the CD-4MCu and the Type 316L SS had the best erosion-corrosion resistance at low ve-locities. However, at high velocities the performance of the CD-4MCu improves. The sequence of the erosion-corrosion resistance for SS under this condition could be CD-4MCu>Type 316L>0Cr14Ni5Mo>1Cr13.❖ In solid-liquid dual-phase slurry, the superior ero-sion-corrosion performance of α+γ duplex-phase SS may be attributed to its high corrosion resistance and high work-hardening capability.❖ Under the experimental conditions of this study, the corrosion component was a small amount of the total erosion-corrosion weight loss, and the removal of materials mainly resulted from mechanical damage. The synergistic mechanism of erosion-corrosion of SS in the condition of this study can thus be termed cor-rosion-assisted erosion behavior.REFERENCES1. C.H. Pitt, Y.M. Chang, Corrosion 42 (1986): p. 312. 2. B.W. Madsen, Wear 123 (1988): p. 1273. Y. Oka, M. Uhkubo, Corrosion 46 (1990): p. 687.4. M.M. Stack, S. Zhou, R.C. Newman, Mater. Sci. Technol. 12(1996): p. 261.5. S. Zhou, M.M. Stack, R.C. Newman, Corros. Sci. 38 (1996): p.1,071.6. Y.G. Yan, “Mechanism of Erosion-Corrosion in Liquid-Solid DualPhase Aqueous Environments” (Ph.D. diss., Institute of Corrosion and Protection of Metals of Chinese Academy of Science, 1998). 7. A. Neville, M. Reyes, H. Xu, Tribol. Int. 35 (2002): p. 643-650. 8. R.J.K. Wood, J.A. Wharton, A.J. Speyer, K.S. Tan, Tribol. Int. 35(2002): p. 631-641.9. V.A. de Souza, A. Neville, Wear 255 (2003): p. 146-156. 10. J.M. Perry, A. Neville, V.A. Wilson, T. Hodgkiess, Surf. Coat.Technol. 137 (2001): p. 43-51. 11. D.X. He, X.X. Jiang, S.Z. Li, H.R. Guan, Corrosion 58 (2002): p.276. 12. X.C. Lu, X.X. Jiang, S.Z. Li, T.C. Zhang, J. Chin. Soc. Corros.Prot. 14 (1994): p. 201. 13. T.C. Zhang, X.X. Jiang, S.Z. Li, C.X. Shi, Acta Metall. Sin. 29(1993): p. PB217. 14. M. Bjordal, E. Bardal, T. Rogne, T.G. Eggen, Wear 2 (1995): p. 186. 15. X.X. Jiang, S.Z. Li, Mech. Chem. Eng. 18 (1991): p. 150. 16. R.J.K. Wood, S. Phutton, Wear 140 (1990): p. 150. 17. Y.G. Zheng, Z.M. Yao, Li He, W. Ke, Mater. Sci. Eng. 12 (1994): p.27. 18. Y.G. Zheng, Z.M. Yao, X.Y. Wei, W. Ke, Wear 186-187 (1995): p.556.。
- 1、下载文档前请自行甄别文档内容的完整性,平台不提供额外的编辑、内容补充、找答案等附加服务。
- 2、"仅部分预览"的文档,不可在线预览部分如存在完整性等问题,可反馈申请退款(可完整预览的文档不适用该条件!)。
- 3、如文档侵犯您的权益,请联系客服反馈,我们会尽快为您处理(人工客服工作时间:9:00-18:30)。
Investigation on the corrosion process ofcarbon steel coated by HVOF WC/Cocermets in neutral solutionC.Monticelli *,A.Frignani,F.ZucchiDepartment of Chemistry,Corrosion Study Centre ‘‘A.Dacc o ’’,University of Ferrara,Via L.Borsari,46-44100Ferrara,ItalyReceived 5June 2003;accepted 26September 2003AbstractThe corrosion protection afforded to a carbon steel substrate by two cermet coatings (WC/12wt.%Co and WC/17wt.%Co;0.05,0.01and 0.2mm coating thickness),applied by highvelocity oxygen fuel (HVOF)technique,has been studied in 3.5%NaCl solutions.Potentio-dynamic polarization curves of cermet constituents,substrate and coated samples,iron andcobalt dissolution kinetics under potentiostatic conditions and galvanic coupling tests havebeen carried out.Cermet layer hinders the anodic process and WC/17%Co is more protective than WC/12%Co,particularly at high coating thickness.I t is likely that the increase in the matrix cobaltcontent changes the pore morphology,from interconnected to isolated pores,with enhancedprotective efficiency.Ó2003Elsevier Ltd.All rights reserved.Keywords:A.Cermet coatings;A.Cobalt;C.Corrosion;C.Sodium chloride;A.WC1.IntroductionCermet coatings on metals are useful when high surface hardness and resistance towear are required.Higher densities and improved quality of the coating can be*Corresponding author.Tel.:+39-532-291136;fax:+39-532-240709.E-mail address:mtc@unife.it (C.Monticelli).0010-938X/$-see front matter Ó2003Elsevier Ltd.All rights reserved.doi:10.1016/j.corsci.2003.09.013/locate/corsciCorrosion Science 46(2004)1225–12371226 C.Monticelli et al./Corrosion Science46(2004)1225–1237achieved by high velocity oxygen fuel(HVOF)technique,that is a thermal spray process characterized by increased sprayed particle velocity and lower temperatures than those employed by other techniques,such as plasma spraying[1,2].The corrosion process of cermet coated metallic substrates is a very complex phenomenon.In WC base cermets both the corrosion protection efficiency afforded to the substrate(which is usually anodic to the carbide)and the corrosion of the coating constituents themselves have been investigated[3–8].It has been found that the corrosion process on the matrix depends on the type of metal alloy.For instance, in sea water86WC–10Co–4Cr undergoes a general attack which dissolves the matrix near the hard particles due to micro-galvanic effects,while50WC–50Ni–Cr–B–Si is subjected to crevice and pitting[3–5].The dissolution of the metallic substrate strictly depends on the presence of in-terconnected porosity in the coating[1,2,9],which is very difficult to reduce to very low or zero levels.Then the development of microgalvanic effects between the sub-strate and the coating can become important[3,4].I n the case of WC–Co cermets,it is found that the cobalt matrix corrodes just at the WC/Co interface[3,6]and in erosion–corrosion tests this cermet presents a very high corrosion rate,because of the active behaviour of cobalt[10].This research concerns the study of the corrosion behaviour of WC/12wt.%Co and WC/17wt.%Co coated steel specimens in neutral chloride solutions,at different coating thickness and constant and low porosity values,by both electrochemical and chemical techniques.Polarization curves recorded on the base materials(carbon steel substrate,massive or electrodeposited pure cobalt,pure WC and WC/5%Co)as well as on coated samples,have been carried out.Moreover,iron and cobalt dissolution kinetics in potentiostatic conditions have been determined by solution analysis and the presence of galvanic effects has been investigated by short-circuiting steel or cobalt to the cermets.The influence exerted by the coating thickness and matrix amount in the cermets has been taken into consideration.2.ExperimentalWC/12wt.%Co and WC/17wt.%Co cermet coatings were sprayed on shot-blasted steel cylinders(Uni EN10011steel type;nominal composition:0.37–0.44% C;0.5–0.8%Mn;0.15–0.4%Si;balance Fe)by high velocity oxygen fuel(HVOF) technique.These cylinders(10mm height;15mm diameter;4.7cm2lateral surface area exposed to the aggressive solution)had a central threaded hole for their mounting on a rotating shaft for the corrosion tests.The constancy of the experimental conditions in HVOF technique maintained an almost constant porosity in the coatings(measured by image analysis on polished sections of specimens,Table1),while(1or2or4times)repetition of the coating process produced0.05;0.1or0.2mm coating thickness.This procedure induced a decrease in the surface roughness as measured by a Talysurf Plus Taylor Hobson Profilometer(Table1).C.Monticelli et al./Corrosion Science46(2004)1225–12371227 Table1Porosity and surface roughness for the various WC/12%Co and WC/17%Co coatingsCoating type WC/12%Co WC/17%CoThickness/mm0.050.10.20.050.10.2 Porosity/% 2.4±1.0 2.3±0.9 2.0±0.7 1.8±0.9 1.8±1.0 1.7±0.6 Roughness/l m7.5±0.6 5.4±0.4 5.4±0.5 6.9±0.3 4.8±0.5 3.8±0.2 SEM and EPMA analysis revealed that in WC/12%Co coating the hard phase is partially and uniformly dissolved within the matrix,while in WC/17%Co coating WC dissolution in the matrix is inhomogeneous,as locally the matrix shows different tungsten to cobalt content ratios[11].Beside the steel substrate,also pure WC and WC/5wt.%Co discs,99.995wt.% pure cobalt wire and electrodeposited cobalt were studied as reference materials. Massive WC and WC/5%Co were obtained by powder hot pressing;cobalt wire was purchased from Aldrich Chemical Company,I nc.,while electrodeposited cobalt was prepared according to the procedure described in[12].Electrodeposited cobalt was used as prepared,while the massive materials werefinished by grinding with up to n.600emery paper(average surface roughness¼0.093±0.006l m)and degreased with acetone.Most tests were carried out in3.5%NaCl aqueous solution,at room temperature, but some tests were carried out in the same solution with0.25%suspended silica (Silica Gel60,0.2–0.5mm particle size,Fluka product).Potentiodynamic(1mV sÀ1)polarization curves were recorded on coated and uncoated steel electrodes,after1and4h of immersion in the solution at a rotating speed of3000rpm.Polarization curves were also recorded on reference materials under stagnant conditions,after0.5h of immersion.Potentiostatic tests were carried out on coated specimens at+0.030V with respect to their corrosion potential(E cor), 300s after the immersion in the aggressive solution.Iron and cobalt concentrations in the aggressive solution were analysed at intervals during900s by inductive cou-pling plasma–atomic emission spectrometry(ICP–AES)technique.Galvanic coupling effects were checked by recording the galvanic currents and potentials of equal area short-circuited electrodes.All the potentials quoted in the text are referred to the saturated Ag/AgCl ref-erence electrode.3.Results and discussion3.1.Polarization curves of the reference materials(coating constituents and substrate)The polarization curves recorded on steel,cobalt wire,WC and WC/5%Co under stagnant conditions are reported in Fig.1.The corrosion potential(E cor)of the steel is about–0.52V and its anodic polar-ization curve shows a tafelian behaviour with a slope(b a)of0.068V decadeÀ1,closeto the expected value of 0.060V decade À1for iron active dissolution.Cobalt wire(E cor ¼À0:31V)shows an anodic behaviour similar to that of the steel.On the contrary,the anodic polarization curve of WC (E cor ¼þ0:2V),a nobleelectroconducting compound [13,14]is typical for a quasi-passive electrode,withcurrents lower than 50l A cm À2in the investigated potential range.The cathodic polarization curves of these specimens,which refer to the oxygenreduction process,coincide and reach a common limit current (i l ).In the case ofcobalt this curve shows a current peak at about )0.7V,that may be related to thereduction of Co þþions to the metallic state.WC/5%Co has a more active (E cor ¼À0:34V)corrosion potential than pure WC.I n this case the oxidation of cobalt,instead of WC,occurs.For limited polarizations,the slope of the anodic curve of WC/5%Co is low and close to that exhibited bycobalt wire,suggesting the dissolution of surface cobalt regions in the cermet.On thecontrary,at nobler potentials,increasing anodic overpotentials are found,because ahigh ohmic drop is involved in cobalt dissolution through the micro-channels in theWC skeleton.WC/5%Co shows limit cathodic current densities close to those re-corded on the materials previously described and again the cathodic jump at )0.7Vis found.E cor of WC/5%Co is slightly more active than that of cobalt wire and this suggeststhat cobalt dissolution rate in the cermet is faster than that in the massive state,probably as a consequence of the alloying with the carbide [9,15]and/or a moredisjointed metal structure in the cermet [15].I n fact,the effective anodic polarizationcurrent densities of cobalt in WC/5%Co,which are referred to the effective area ofthe cobalt surface region (calculated by assuming that in the cermet the cobaltvolume fraction,V Co ,is equal to the cobalt surface area fraction,A Co [16,17])aremuch higher than those of the cobalt wire (Fig.2).Similar results are obtained withelectrodeposited cobalt,which is more active than WC/5%Co (E corr ¼À0:46V)andits anodic curve is not far from the effective anodic curve of cobalt inWC/5%Co;Fig.1.Polarization curves of massive materials:steel (1),thick line;cobalt wire (2);WC (3);WC/5%Co(4),in 3.5%NaCl solution under stagnant conditions.1228 C.Monticelli et al./Corrosion Science 46(2004)1225–1237therefore the electrodeposited metal can probably represent more closely the cobaltdissolution behaviour in the cermet,owing to its less inert nature.3.2.Polarization curves on coated and uncoated specimensThe comparison between the polarization curves recorded on quiet and rotatingsteel electrodes shows that rotation stimulates the cathodic reaction by one order ofmagnitude,while it exerts much smaller effects on the anodic one (Fig.3).parison of the anodic polarization curves of:cobalt wire (2);electrodeposited cobalt (5);WC/5%Co,referred to the effective area of the cobalt surface in the cermet (40),in 3.5%NaCl solution understagnantconditions.Fig.3.Polarization curves in 3.5%NaCl solution under flowing (3000rpm)conditions:uncoated (thickline)or WC/12%Co coated steel at increasing coating thickness values (0.05;0.1;0.2mm,thin lines);uncoated steel (thick line)under stagnant conditions (0rpm).C.Monticelli et al./Corrosion Science 46(2004)1225–12371229The anodic and cathodic polarization curves recorded on rotating WC/12%Cocoated specimens are close to those recorded on rotating bare steel specimens (Fig.3).The cermet layer exerts a negligible influence on the oxygen reduction reaction,while it can retard the anodic reaction only at high anodic overvoltages.On WC/17%Co coated steel electrodes the action afforded by the cermet is much more evi-dent,particularly on the anodic process;by increasing the coating thickness,lowerand lower anodic polarization currents (with higher anodic slopes)are recorded,while the cathodic polarization currents are scarcely affected (Fig.4).The comparison between the polarization curves of the two coating types at thesame thickness values (0.05and 0.2mm,Fig.5)clearly shows that WC/17%Co ismore protective than WC/12%Co,particularly at high coating thickness.During anodic polarization,underlying iron dissolution through the coating poresis certainly stimulated and,at increasing anodic polarization,concomitant cobaltdissolution is expected.As already evidenced in the case of cobalt dissolution fromWC/5%Co,high ohmic drops are involved in steel dissolution through the coatingpores and cobalt dissolution through WC skeleton pores in the coating,thus in-ducing the high observed anodic slopes.The pores have an interconnected morphology in WC/12%Co coating,as thegradual formation of red insoluble corrosion products (mainly hydrated ferric hy-droxide)is noticed after only 1h of immersion.The same occurs in the case of WC/17%Co at thickness values of 0.05and 0.1mm,while only at the end of 4h im-mersion red corrosion products form in 0.2mm coating.As both WC/12%Co andWC/17%Co coatings exhibit more or less the same porosity,it is likely that thehigher protectiveness offered by the latter,particularly at the highest thickness,islinked to a different pore morphology,i.e.isolated pores in WC/17%Co replaceinterconnected pores inWC/12%Co.Fig.4.Polarization curves in 3.5%NaCl solution,3000rpm:uncoated (thick line)or WC/17%Co coatedsteel at increasing coating thickness values (0.05;0.1;0.2mm,thin lines).1230 C.Monticelli et al./Corrosion Science 46(2004)1225–1237The polarization curves recorded after 4h immersion of the steel specimen show adecrease in the cathodic currents,with a consequent shift of the corrosion potentialin the negative direction (Fig.6).This is attributable to the growth of the ironcorrosion products on the specimen surface,hindering oxygen diffusion from thesolution to the electrode surface.The polarization curves carried out under the sameconditions,in the presence of suspended silica,are close to those recorded on a baresteel surface after 1h immersion,as the suspended particles remove the corrosionproducts and stimulate the cathodicreaction.parison between the polarization curves of WC/17%Co (thick lines)and WC/12%Co (thinlines)coated steel in 3.5%NaCl solution,3000rpm.Coating thickness:0.2mm or 0.05mm.Fig.6.Polarization curves of uncoated steel in 3.5%NaCl solution,3000rpm:after 1or 4h immersion(thin lines);after 4h immersion in the presence of 0.25%suspended silica (thick line).C.Monticelli et al./Corrosion Science 46(2004)1225–12371231Fig.7shows that suspended silica can markedly stimulate the cathodic reactionalso in the case of coated specimens with a low coating thickness,suggesting thepresence of bulky red iron corrosion products on the specimen surface.On thecontrary,no or limited stimulation is detected on coated specimens at the highestcoating thickness,where the formation of iron corrosion products is confined tosmall regions at the pore mouths.This confirms that these thermal spray coatingsoffer an hindrance to the steel dissolution only at high thickness values as the ag-gressive solution reaches the steel substrate with increasing difficulty.3.3.Potentiostatic tests on coated specimensThe concomitant oxidation of steel (iron)and coating matrix (cobalt)is expectedduring corrosion of coated specimen.Therefore,an accelerated test was carried outto evaluate the relative amount of metals dissolved.It consisted in a 900s polari-zation of the coated specimens at +0.030V vs E cor ,followed by chemical analysis ofplanned-interval solution aliquots.Table 2collects the iron ion amounts,the dissolved Fe/Co ratio,measured atincreasing polarization times and dissolved from a single coated specimen,withdifferent coating thickness values.Fig.8shows some examples of dissolved iron andcobalt trends as a function of time.The iron ion amounts are usually greater and often much greater than cobalt ionamounts,even at short polarization times.These observations confirm the presenceof bare steel areas in contact with the solution,at the bottom of interconnected poresin the coatings.Smaller areas are present in thicker coatings,particularly in the caseof WC/17%Co coated specimens.Fig.8also shows that dissolved Fe þþions quickly accumulate in the solution atincreasing polarization time.This trend indicates that the bare steel areasincreaseFig.7.Corrosion rates,extrapolated from the cathodic polarization curves of uncoated and 0.05mm and0.2mm WC/12%Co,WC/17%Co coated steel,after 1or 4h immersion in 3.5%NaCl solution or 4himmersion in 3.5%NaCl +0.25%suspended silica,3000rpm.1232 C.Monticelli et al./Corrosion Science 46(2004)1225–1237Table2Average amounts of dissolved iron ions and iron/cobalt ratio of a coated specimen polarized at+0.030V vs E corCoating type WC/12%Co WC/17%CoThickness/mm0.050.10.20.0500.10.2E appl a/V)0.40)0.37)0.32)0.40)0.36)0.32 Polarization time/s Fe/l g Fe/Co Fe/l g Fe/Co Fe/l g Fe/Co Fe/l g Fe/Co Fe/l g Fe/Co Fe/l g Fe/Co 20025410.872037.0221 5.7743013.92133 3.00360.72 40058913.2458611.126919.26138034.41296 4.17580.81 600147028.11112014.25128013.38270056.49662 6.651080.97 800317048.77171016.93200016.26451084.6211609.21182 1.46 900409061.04202018.36243017.365760103.23145010.43258 1.80a The applied potential vs saturated Ag/AgCl reference electrode.C. Monticelli et al. / Corrosion Science 46(2004) 1225–1237 1233with time,as a consequence of the progressive detachment of the coating due to the corrosion attack on steel at the pore bottom.The same probably occurs under free corrosion conditions,because of the acidification of the solution inside the coating pores,due to the hydrolysis of metal ions.The coated specimen E cor values,measured 300s after the immersion,become nobler as the coatings become thicker and are more or less independent from the coating type.As a consequence,also the applied potentials become nobler at in-creasing coating thickness.Notwithstanding,the amount of dissolved iron ions de-creases as thickness increases.This supports the hypothesis of a decrease in the interconnected porosity at increasing coating thickness.At variance with iron,dissolved Co þþamounts always increase linearly as a function of the time (Fig.8)i.e.cobalt has a constant dissolution rate.The cermet with a higher matrix percentage produces higher amounts of dissolved cobalt ions,which also increase as thickness increases,particularly in the case of 12%Co cermet.This last observation could be linked both to the presence of longer channels through thicker coatings and to the quoted increase in the applied potential at increasing coating thicknessvalues.Fig.8.Dissolution kinetics of iron (solid symbols)and cobalt (open symbols)in WC/12%Co or WC/17%Co coated steel,under potentiostatic conditions (+0.030V vs E cor ).Coating thickness:0.05mm (circles);0.2mm (triangles).1234 C.Monticelli et al./Corrosion Science 46(2004)1225–12373.4.Galvanic coupling testsCobalt–tungsten carbide galvanic coupling,simulated by the couple cobalt-WC/5%Co,can always affect the corrosion process,while steel–cermet coupling can be found only when the solution comes in contact with the steel substrate at the pore bottom in the coatings.Table 3shows both the stable potentials (usually reached within 12h of test)and the charge amounts passed in 24h (Q,referred to a unity electrode area),obtained by short circuiting either steel or cobalt to the cermets,which always result cathodic to the metals.Fig.9shows some examples of the evolution of the short-circuit currents (scC)and short-circuit potentials (scP)recorded during these tests.In the case of coupling steel to tungsten carbide (either WC/5%Co or WC/12%Co or WC/17%Co)the scP shifts from about )0.45V towards more negative values,first quickly and then more slowly.The stable potential values are always close to the steel corrosion potential measured 4h after the immersion in the aggressive solution (Fig.6).This suggests that galvanic corrosion is under cathodic control.By coupling cobalt to WC,a rather similar trend is found,but in this latter case nobler potential values are recorded.Table 3Parameters deduced from the galvanic coupling testsGalvanic couple aQ /C cm 2Stable coupling potential/V Steel––WC/17%Co (coating)2.69)0.58Steel––WC/12%Co (coating)3.25)0.57Steel––WC/5%Co1.58)0.58Co––WC/5%Co1.39)0.35a The first element is theanode.Fig.9.Short circuit potentials and short circuit currents of Co-WC/5%Co coupling (thin lines)or Steel-WC/12‚17%Co coupling (thick lines)in 3.5%NaCl,0rpm.C.Monticelli et al./Corrosion Science 46(2004)1225–123712351236 C.Monticelli et al./Corrosion Science46(2004)1225–1237The scCs of steel coupled either to WC–12%Co or WC–17%Co increase at the beginning of the test and reach almost constant and common values(around35 l A cmÀ2after6–8h),while with steel or cobalt coupled to WC/5%Co scCs reach lower values(around15l A cmÀ2).The galvanic currents measure the stimulation of the corrosion process on the anode due to short circuiting.The Q values obtained for steel or cobalt coupled to WC/5%Co are quite close to each other,probably because the galvanic current density corresponds to the limit current density on the cathode,which is the same in both cases.Higher Q values are measured in the case of steel coupled to WC/12%Co or WC/17%Co coatings,as these coatings have a higher surface roughness and higher effective surface areas than WC/5%Co and induce higher galvanic current densities on the anode.4.Conclusions•The corrosion protection afforded by WC/Co coatings to the underlying steel sub-strate depends on the morphology of the cermet layer porosity.In the case of 17%Co cermet,by increasing the layer thickness(from0.05to0.2mm)it is likely that the interconnected porosity turns into the more protective isolated one.Therefore such coating offers the highest hindrance to the anodic oxidation of the steel,as the access of the aggressive solution to the steel surface is more diffi-cult.•The iron oxidation takes place at the bottom of the cermet pores and by increas-ing the testing time an enlargement of the substrate corroding surface area occurs.•Cobalt and iron dissolution is enhanced by WC coupling.A galvanic current is present on steel or cobalt(anodic)coupled to a WC coating(cathodic)and cor-responds to the limit current of oxygen reduction on the coating itself.The couple activity strictly depends on cermet to exposed substrate area ratios and therefore on the amount of interconnected porosity in the coatings. AcknowledgementsThe Authors wish to thank Mr.D.Contri and Mr.A.Volta(PMC s.r.l.,Pieve di Cento,Bologna,I taly)for their valuable assistance in the preparation of the speci-mens.References[1]A.Neville,T.Hodgkiess,Br.Corros.J.34(4)(1999)262–266.[2]P.L.Cabot,J.Fernadez,J.M.Guilemany,Mater.Sci.Forum289–292(2)(1998)679–687.[3]A.Neville,T.Hodgkiess,Surf.Eng.12(4)(1996)303–312.[4]A.Neville,T.Hodgkiess,J.Am.Ceram.Soc.62(8)(1999)2138–2144.C.Monticelli et al./Corrosion Science46(2004)1225–12371237[5]J.M.Perry,A.Neville,V.A.Wilson,T.Hodgkiess,Surf.Coating Technol.137(2001)43–51.[6]J.M.Guilemany,J.M.de Paco,Surf.Eng.14(2)(1998)129–132.[7]J.M.Guilemany,P.L.Cabot,J.Fernandez,J.M.de Paco,J.S a nchez,pos.Mater.7(3)(1998)205–208.[8]A.Collazo,X.R.Novoa,C.P e rez,Electrochim.Acta44(1999)4289–4296.[9]A.M.Human,H.E.Exner,I nt.J.Refr.Metals Hard Mater.15(1997)65–71.[10]E.Bardal,M.Bjordal,T.G.Eggen,T.Rogne,T.Solem,Prevention of erosion and corrosion inslurries using various inorganic coatings,in:J.M.Costa,A.D.Mercer(Eds.),Progress in the Understanding and Prevention of Corrosion,The I nstitute of Materials,The University Press, Cambridge,1993,pp.158–164.[11]C.Monticelli,A.Frignani,F.Zucchi,Corrosion Behaviour of Thermal Spray Coated Carbon Steel ina Saline Environment,in:Proc.15th CC,Granada(Spain),22–27September2002,paper no.222,CD-Rom.[12]P.Pedeferri,Corrosione e Protezione dei Materiali Metallici,CLUP(Milano)1978.[13]J.D.Voorhies,J.Electrochem.Soc.119(1972)219–222.[14]D.zur Megede,E.Heitz,Werkst.Korros.37(1986)207–214.[15]S.P.Pednekar,Corrosion53(10)(1997)813–819.[16]E.Underwood,Quantitative Stereology,Addison Wesley,1970.[17]Annual Book of ASTM Standards,Standard Practice for Determining the I nclusion or Second PhaseConstituents of Metals by Automatic mage Analysis,E1245,04.14,ASTM,Philadelphia,1995.。