酸性光亮铜镀层不亮因素有哪些?
如何维护酸性光亮连续镀铜电镀液?

如何维护酸性光亮连续镀铜电镀液?酸性光亮连续镀铜液在维护上应注意如下几点。
(1)严格控制工艺规范是维护电镀液的重要手段。
镀液中硫酸铜的含量虽然可以在比较宽的范围内变动,但浓度差异太大也将影响镀液性能;当硫酸铜含量过低时,会使镀层光亮度下降;浓度过高时,铜盐则容易在阳极表面形成结晶析出,造成阳极钝化。
另外,操作中应根据镀液温度的变化和搅拌的强度及时调整阳极电流密度。
在较高的槽液温度和强烈的搅拌情况下,可采用较大的电流密度;反之,电流就应开小一些。
不然,将会造成镀层粗糙疵病。
(2)正确地使用添加剂是保证工艺稳定的重要因素。
实践证明,添加剂的消耗与很多因素有关:如温度,电流密度,阳极状态,通过的电量及镀液中硫酸含量等。
其中,影响较大的是镀液的温度高低和通电量的多少。
添加剂的消耗量与通过电镀槽的电量成正比。
电流大,时间长,添加剂消耗量大。
反之,添加剂消耗量就少。
温度高,添加剂消耗快;温度低,消耗就慢一些。
在正常情况下操作,每升溶液通电4A·h后约需补加lmL添加剂。
由于添加剂中各组分的电极行为不一样,相对稳定的含量不能用均一的添加来维持,要采用经验的方法来判断添加剂的消耗情况。
在生产过程中,由于添加剂各组分含量甚微,镀液中添加剂含量高低无法用一般的分析方法得知。
最简单可行的方法是采用变换阴极移动速度时观察镀层光亮度来加以判断;当加快阴极移动的速度后,所获得的镀层较未加速之前更亮,则表明光亮剂不足,需要补加;当减慢阴极移动速度或停止移动时,所得到的镀层反而显得更光亮,则表明添加剂已经过量了。
(3)应避免有害杂质进入槽内。
硝酸银、氯根和铬酸根等阴离子对镀液性能会产生不良的影响。
连续镀铜的酸铜液对氯离子是比较敏感的,当缺少氯离子时,即使添加剂含量在正常范围内,也难以得到整平性良好的全光亮镀层。
氯离子含量在20~40mL/L时,镀层光泽型最为理想;超过80mL/L,光亮将会下降,因此在配制镀液时应事先了解自来水中氯离子的含量,若超过工艺规范,则应采用蒸馏水或去离子水进行配制,而后再补充适量的氯离子。
常见酸铜缸产品故障原因分析与解决方法
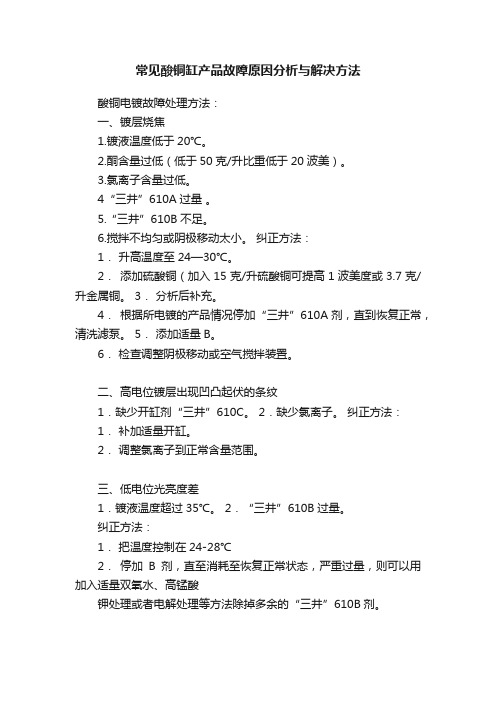
常见酸铜缸产品故障原因分析与解决方法酸铜电镀故障处理方法:一、镀层烧焦1.镀液温度低于20℃。
2.酮含量过低(低于50克/升比重低于20波美)。
3.氯离子含量过低。
4“三井”610A过量。
5.“三井”610B不足。
6.搅拌不均匀或阴极移动太小。
纠正方法:1.升高温度至24—30℃。
2.添加硫酸铜(加入15克/升硫酸铜可提高1波美度或3.7克/升金属铜。
3.分析后补充。
4.根据所电镀的产品情况停加“三井”610A剂,直到恢复正常,清洗滤泵。
5.添加适量B。
6.检查调整阴极移动或空气搅拌装置。
二、高电位镀层出现凹凸起伏的条纹1.缺少开缸剂“三井”610C。
2.缺少氯离子。
纠正方法:1.补加适量开缸。
2.调整氯离子到正常含量范围。
三、低电位光亮度差1.镀液温度超过35℃。
2.“三井”610B过量。
纠正方法:1.把温度控制在24-28℃2.停加B剂,直至消耗至恢复正常状态,严重过量,则可以用加入适量双氧水、高锰酸钾处理或者电解处理等方法除掉多余的“三井”610B剂。
四、填平度低1.光剂不足。
2.氯离子过量,镀液主盐低,磷铜阳极少等。
纠正方法:1. 按照添加方法添加光剂。
2. 杜绝带入氯离子,让氯离子带出、消耗降低;严重时采用稀释、沉锌、硝酸银除氯等方法来降低氯离子的含量;另外注意主盐和磷铜阳极的补充。
五、镀层有微细针孔 1.滤泵吸入空气;2.不适当之空气搅拌;3.缺少开缸剂 C。
纠正方法:1. 滤泵入水口要远离打气孔,防止吸入空气。
2.打气孔不可过小(直径不小于3毫米),适当调节打气强度。
3.添加适量开缸剂C。
六、镀层布满细小的微粒1.镀液内有悬浮的微小颗粒(例如活性炭粉)2.搅拌用之空气被污染。
3.田家硫酸铜时,过滤不充分。
4.使用不适当的阳极。
纠正方法:1. 连续过滤镀液,建议使用助滤剂。
2. 检查隔尘纲、隔油纲,最好使用无油气泵打气。
3. 加强过滤,彻底滤清镀液。
4. 使用合格的磷铜阳极。
浅谈光亮酸性镀铜光亮剂及典型故障处理
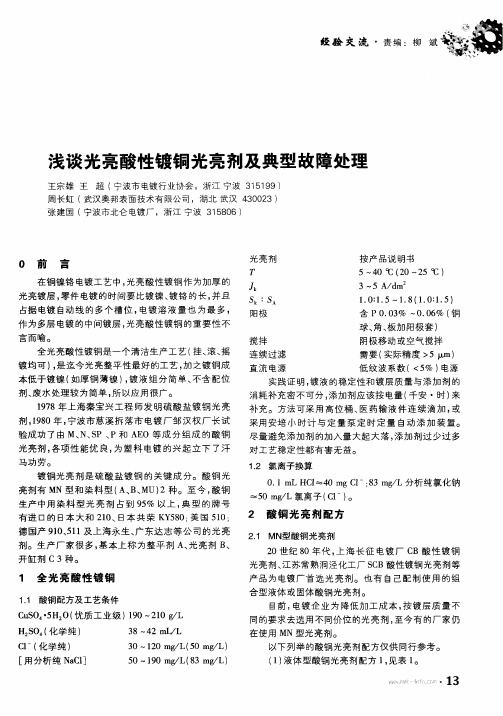
浅谈 光亮酸性镀 铜光亮剂及典型 故障处理
王宗雄 王 超 ( 宁波市 电镀行业协 会 ,浙 江 宁波 3 1 5 1 9 9) 周长虹 ( 武汉奥邦表面技术有 限公司 ,湖北 武汉 4 3 0 0 2 3) 张建国 ( 宁波市北仑 电镀 厂 ,浙江 宁波 3 1 5 8 0 6)
1 全光 亮 酸性 镀 铜
1 . 1 酸铜配方及工艺条件 C u S O 4 ・ 5 H 2 O( 优 质工 业级 ) 1 9 0— 2 1 0 g / L
H 2 S O 4 ( 化 学纯 ) C l 一 ( 化学 纯 ) 3 8— 4 2 m L / L 3 O一1 2 0 m g / L( 5 0 mg / L )
实践 证 明 , 镀 液 的稳定 性和 镀 层质 量 与添 加 剂 的 消耗 补充 密 不可 分 , 添 加剂 应该按 电量 ( 千安 ・ 时) 来
1 9 7 8年上 海秦 宝兴 工 程 师发 明硫 酸 盐镀 铜 光 亮
剂, 1 9 8 0年 , 宁波市 慈 溪拆 落 市 电镀 厂 邹 汉权 厂长 试 验成 功 了由 M、 N、 S P、 P和 A E O 等成 分 组 成 的酸 铜
开缸 剂 C 3种 。
2 0世纪 8 0年 代 , 上 海 长 征 电镀 厂 C B酸 性 镀 铜 光 亮剂 、 江苏 常熟 洞泾 化工 厂 S C B酸性 镀铜 光 亮剂等 产 品为 电镀厂 首 选 光 亮剂 。也 有 自己配 制 使 用 的组 合型 液体 或 固体 酸 铜 光亮剂 。 目前 , 电镀企 业 为 降低 加 工成 本 , 按 镀层 质 量不
光 亮剂 , 各项 性 能 优 良 , 为塑 料 电镀 的兴 起 立 下 了汗
酸铜常见故障及解决方法

酸铜常见故障及解决方法光亮酸铜工艺中常见故障及处理方案---镀层易氧化、变色1、光剂过高----双氧水至正常、消耗至正常或碳粉至正常2、有机杂质过多----依据杂质程度和性质决定处理方案光亮酸铜工艺中常见故障及处理方案---发脆1、杂质污染----依据杂质程度和性质决定处理方案2、光剂比例失调----依据失调情况调整光亮酸铜工艺中常见故障及处理方案---镀液混浊、毛刺1、阳极不正常(阳极质量差)----换质量好的阳极2、材料不纯----换质量好的材料3、车间沙尘、尘埃太重----控制车间沙尘光亮酸铜工艺中常见故障及处理方案---光剂消耗量大1、镀液温度太高----调整温度至正常;2、硫酸含量相对过高----分析调整;3、阳极不足或阳极钝化----调整阳极至正常;4、光剂比例失调----根据失调情况调整光剂比例。
光亮酸铜工艺中常见故障及处理方案---填平差1、硫酸铜含量过低----分析调整;2、光剂比例失调----依据实际情况调整;3、氯离子不足或过高----分析调整。
光亮酸铜工艺中常见故障及处理方案---走位差1、硫酸铜过高或硫酸过低----分析调整;2、温度过高----调整温度至正常;3、A剂不足或过多----调整A剂至正常;4、B剂过高----调整B剂至正常;5、有机杂质过多----依据其严重情况和性质决定处理方案。
光亮酸铜工艺中常见故障及处理方案---出光慢1、成份不正常,例如:硫酸铜过高或过低----调整成份至正常;2、温度相对过高或过低----调整温度至正常范围;3、搅拌不均匀----调整搅拌均匀;4、阳极太少、阴极质量差、阳极钝化等----根据实际情况调整处理;5、电流密度相对较低----调整电流密度正常;6、工件挂的太多、太密、阴极屏蔽----调整工件均匀,避免阴极屏蔽;7、光剂比例失调----调整光剂比例至正常;8、有机杂质方面(如引起高电位发哑)----依据有机杂质严重程度和性质决定处理方案。
光亮酸性镀铜常见故障分析和排除

光亮酸性镀铜常见故障分析和排除一.杂质的影响和去除1.有机杂质的处理对镀铜液中的光亮剂,通常是采取勤加、少加的原则,避免一次性加入过多的光亮剂。
如果光亮剂加入量过多,或者在镀铜液温度高时光亮剂足量,但在镀铜液冷下来后则光亮剂就显得过量了,这时的光亮剂就起到了有机杂质的影响。
在电镀零件的低电流密度区出现亮与不亮的明显分界,复杂零件的深凹处镀铜层发花,甚至镀层上有铜粉末状析出物等故障。
镀液中的光亮剂(有机杂质)如果稍多可以通过电解的方法消耗,也可以通过加入少量双氧水破坏部分光亮剂,再行调整。
但一次双氧水加入量不宜大于0.ImL/L,且应在强烈搅拌下稀释10倍以上加入。
需要注意的是双氧水对镀液中M、N光亮剂的破坏,可能会造成镀液中整体光亮剂比例的失调。
如果有机杂质过多,这时只能采取停产大处理的方法来除去镀铜液中的有机杂质。
在大处理时应注意:(1)能不加氧化剂只加活性炭吸附即可时,则尽量避免在镀铜液中加氧化剂。
因为加入的氧化剂稍不慎可能未除尽有机杂质,甚至会使后加入的光亮剂再度被破坏,短时间很难调至正常。
(2)双氧水氧化性比高锰酸钾弱,其分解产物为无害的水。
因此,非必要时,仍以加双氧水为好。
若镀铜液中双氧水稍多又急于电镀生产时,可通过加入适量的高锰酸钾来氧化破坏双氧水(此时双氧水成为还原剂),加入量由试验确定。
(3)加入氧化剂破坏镀铜液中有机杂质时,务必加热到55℃~65℃,强烈搅拌0.5h以上,否则一是氧化不彻底,二是残存物除不尽。
因此,必须备有钛质蒸汽管或电加热器用于加热。
(4)一般来讲,大处理要采用优质活性炭,在处理彻底后应补加开缸电镀的光亮剂。
但有时处理并不彻底,则应通过霍耳槽试验来决定添加开缸光亮剂还是加补充剂和加人量的多少。
2.氯离子的处理在光亮硫酸盐镀铜液中,氯离子可以降低镀铜层的应力,提高镀铜层的韧性,同时适量的Cl-离子还能提高镀铜层的光亮度和整平性,使零件的低电流密度区镀层更亮。
但它的含量过高时(≥120mg/L),就会使镀铜层粗糙,产生树枝状条纹并失去光泽等。
酸性镀锡光亮剂控制工艺及常见故障处理方法

LHX-920酸性镀锡光亮剂控制工艺及常见故障处理方法青岛南涯电子有限公司电镀TEAM 徐宽文任常忠薛江1.前言LHX-920酸性镀锡光亮剂是由青岛大学用应技术学院谢洪波教授研制的硫酸盐镀锡光亮剂,其使用量少,工艺范围宽,而且能使镀层结晶细致光亮,镀液长期使用稳定不变色,是一种质优价廉的光亮剂。
其性能完全可以替代国外产品。
我公司主要生产弱电轻触开关镀件为铁基体上镀锡。
2000年的时候我们曾使用一种进口光亮剂,但老是出现质量问题,镀液也不稳定,在2003年的时候经过试验选择了LHX-920光亮剂,一直使用至今效果不错。
我们总结了一套适合LHX-920酸性光亮剂的最佳工艺条件及一些常见故障的处理方法,希望与电镀界同仁一起探讨。
2.工艺流程化学除油—酸洗—镀镍—活化—镀锡—中和—烘干3.配方及操作3.1化学除油目的:将粘附在待镀件表面上的油污去除,提高镀层与基体金属的结合力和保持镀液清洁。
工艺:市售一般除油剂温度:50-60℃时间:5-10分钟操作:把待镀件浸入除油液处理5-10分钟,然后用热水清洗(60-70℃)1分钟,再用流水清洗直水呈中性。
3.2酸洗目的:去除镀件表面氧化膜工艺:H2SO4: 3-5%温度:室温时间: 2-3分钟操作:把镀件浸入酸洗液中2-3分钟,注意把氧化膜完全去除。
否则可延长时间。
3.3镀镍目的:提高镀件盐雾试验工艺:NISO4: 250g/lNICL2: 50g/lH3BO3: 50g/l3.4活化目的:溶解镀件表面钝态膜,以保证镀层与基体结合力。
工艺:H2SO4: 5-7%温度:室温时间: 2分钟操作:把镀件浸入活化液中2分钟。
3.5电镀3.5.1镀液成分及工艺条件SnSO4 25-40g/LH2SO4 80-100ml/LLHX-920开缸剂 30-40ml/LLHX-920辅光剂 1-5ml/L温度 5-30℃(最佳10-25℃)电流密度 0.5-1A/dm2过滤连续阳极99.95%纯锡3.5.2 镀液的配制(1)注入3/4的纯水与洁净的镀槽内。
在酸性亮铜镀液中影响铜镀层光亮度的因素有哪些?

在酸性亮铜镀液中影响铜镀层光亮度的因素有哪些?在酸性亮铜镀液中影响铜镀层光亮度的因素有哪些?造成酸性亮铜不良的原因较多。
生产中可根据经验积累来分析检查产生故障的原因以确定解决的办法。
一般来讲,导致酸性亮铜不亮的原因大体可以归纳如下几点。
(1)电解质及溶液本身不纯所含有害杂质。
在新配溶液时,所采用的工业硫酸铜通常含有一定量的铁和有机杂质,若不进行处理,则新配制的镀液导致镀层不亮。
此时,可在尚未添加硫酸之前的硫酸铜电解液中(pH=4左右)加入l~2mL/L 30%双氧水。
利用三价铁氢氧化物容易沉淀的性质除去杂质。
如果同时加入活性炭吸附,则可同时消除有机杂质的影响。
(2)力争较准确地掌握好添加剂的消耗情况。
长期使用的镀液中,一部分添加剂随着工件的带出和镀层的夹杂而消耗掉;一部分将分解成有机杂质;还有一部分留在溶液中而使添加剂本身的组分发生变化。
这一切都有可能影响镀层的光亮而造成镀层缺陷。
生产中应注意经验的积累和细心观察,采用少加勤加的办法补充添加剂。
(3)注意操作条件的变化,特别是镀液温度的变化。
大多数酸性亮铜体系所采用的添加剂其最佳区域要求镀液温度保持在10~35℃之间,并需根据镀液温度和电解液浓度来适当选择电流密度。
有些新型的酸铜光亮剂可将镀液温度提高40℃左右。
低电流密度区仍可获得全亮镀层,适于较大工件加工,具有宽温度的特点。
与此同时,操作中采用搅拌及阴极移动将有助于获得光亮铜层。
(4)阳极铜粉及一价铜的存在将造成镀层不亮。
阳极铜粉通常是阳极电流密度太大、阳极含磷量不适而使阳极出现不正常溶解。
一价铜离子有时是因为某些还原剂带入而产生。
为了消除一价铜影响,可在每天班前用30%双氧水按0.25mL/L的量稀释后加入槽内;有时可根据阳极溶解的情况,加入适量的硫酸。
(5)在酸性硫酸铜溶液中,微量的氯离子(C1-)会增加电荷传递反应的交换电流密度,加速在酸性镀铜溶液中铜的沉积和溶解反应,故有微量的Cl-存在下,铜电镀过程中可在一个很大的电流密度范围内进行。
酸铜走位不好、凹位镀不亮怎么办

酸铜电镀工艺常见的一个故障现象题是容易出现走位不好、凹位镀不亮。
导致酸铜走位不好、凹位镀不亮的可能因素如下:
1、使用了不合格的酸铜光剂。
因为配方的原因,有些酸铜光剂的走位性能天生就不
好。
2、氯离子含量偏高或不足。
氯离子是影响酸铜电镀质量的关键因素之一。
在酸铜电
镀工艺中,氯离子作为催化剂,使酸铜电镀能镀出平滑、光亮、致密的镜面镀层。
3、光剂比例失调
4、阳极钝化。
5、阳极不足,钛篮袋上部空、或者下面阳极泥淤积都会导致对应部位的产品走位不
良。
6、设备故障,比如个别钛篮不导电,导致产生了双电极现象,或者滞空时间过长导
致表面氧化或者钝化。
当酸铜电镀生产中出现走位不好、凹位镀不亮时,应该通过现场查勘、镀液分析、工艺参数校验、Hell槽试片、数据分析等手段,采用排除法对“人、机、物、环、法、测”六大影响因素进行逐一排查,直至找到真正的原因,然后对症下药予以解决。
酸铜光剂哪家好?Unimirror AC-930 镜牌酸铜光亮剂由电镀添加剂专业生产厂家---深圳市汇利龙科技有限公司经多年优化精研而成,已广泛应用于挂镀、滚镀和摇镀等各类酸铜电镀制程。
Unimirror AC-930 镜牌酸铜光亮剂品牌口碑好,技术先进,质量稳定,价格实惠,使用成本低,服务好,可批发。
- 1、下载文档前请自行甄别文档内容的完整性,平台不提供额外的编辑、内容补充、找答案等附加服务。
- 2、"仅部分预览"的文档,不可在线预览部分如存在完整性等问题,可反馈申请退款(可完整预览的文档不适用该条件!)。
- 3、如文档侵犯您的权益,请联系客服反馈,我们会尽快为您处理(人工客服工作时间:9:00-18:30)。
酸性光亮铜镀层不亮因素有哪些?
现代电镀网1月12日讯:
酸性光亮镀铜是以硫酸铜和硫酸作为基本成分,引入适量添加剂或其他光亮剂,使镀液的工艺特性得以改善和提高,并直接获得镜面光亮铜层。
其广泛用于装饰性多层电镀中间层及印刷线路板镀铜层,省去机械抛光。
但是,生产中有时会出现镀层不亮现象。
造成这种情况的因素较多,本文将其归纳为如下几点进行分析。
1.电解质不纯
在新配镀液时所用的普通硫酸铜、硫酸是不纯的,如工业硫酸的质量分数≥92.5%,含有很多的铁和有机杂质,若不进行处理,电镀时会使镀层不亮。
即便是用试剂级硫酸,如果不处理也会出现这种情况,因为硫酸铜或多或少也有杂质。
可在尚未添加硫酸之前,在已溶解的硫酸铜溶液中(pH值为4)加入质量分数为30%的H2O21~2mL/L和活性炭0.5~1.0g/L联合处理。
利用三价铁的氢氧化物容易沉淀的性质除去铁杂质;加入活性炭吸附,可以同时消除有机杂质的影响。
这样开始电镀,就能镀得光亮铜层。
镀液经长期使用所产生的金属杂质和有机杂质将越积越多,显然,该镀液是不纯的。
如果不按工艺要求做定期处理,当铁杂质的质量浓度达到10g/L以上时,电流效率和镀层亮度明显下降。
例如:某厂一镀槽电流开不大,镀层薄而不亮,镀件边角易烧焦,曾一度无法正常生产。
在笔者建议下取样分析,但由于溶液中铁的质量浓度高,对分析硫酸铜、硫酸终点产生干扰而无法显示数据,于是分析铁离子竟高达40g/L。
根据观察,镀液颜色浅,在确认镀液中各成分的质量浓度偏低的情况下,补充40g/L硫酸铜和15g/L硫酸,以降低铁杂质的影响;然后按常规进行处理,使镀槽恢复了正常,镀出了全光亮铜层。
2.光亮剂消耗
酸性光亮镀铜液中光亮剂的消耗情况与很多因素有关,如工件种类、形状、表面状态以及镀液中无机、有机杂质和硫酸铜的质量浓度等。
特别是Cl-不足,即便是光亮剂在正常范围内也难以获得整平性好的光亮镀层;当Cl-的质量浓度过高时,将加快光亮剂的消耗。
长期使用的镀液,一部分光亮剂随着工件的带出和镀层的夹杂作用而消耗掉;一部分将分解成有机杂质;还有一部分留在镀液中而使光亮剂本身的组分发生变化。
这些情况都有可能影响镀层的光亮性,造成镀层缺陷。
在生产中除了按所用光亮剂的使用说明书使用之外,还要力求准确地掌握光亮剂的消耗情况,并注意经验的积累和细心的观察,采用少加勤加的办法及时补充光亮剂,以保持光亮剂在镀液中恒定。
此外,镀液温度的高低和通电量的多少对光亮剂的消耗影响较大。
电流大、时间长,光亮剂消耗量就大;反之,光亮剂消耗减少。
大多数酸性镀铜所用的光亮剂,其最佳温度范围为在10~35℃之间,需根据镀液温度和电解液的质量浓度来选择适当的阴极电流密度,否则往往使镀层不亮。
如某种光亮剂,当镀液温度超过38℃时,光亮剂消耗很快,镀层光亮范围变窄。
只有采用宽温酸性镀铜光亮剂,才可以将镀液温度提高到40℃左右,低电流密度区域仍可获得光亮铜镀层。
3.Cl-的质量浓度
在酸性光亮镀铜液中,Cl-是一种不可缺少的阴离子,其质量浓度的高低对镀层的光亮度也有影响。
若镀液中没有Cl-或较少时,则整平能力很低,镀层就会发花、无光泽;当其质量浓度过高,整个镀层亮度降低,并有树枝状条纹出现,且光亮剂消耗量也增大。
新配镀液中Cl -不足时,可加少许盐酸或氯化钠,但不能用一般井水或河水来补充镀槽水位和进行工件镀前的清洗,避免带入过多的Cl-。
当Cl-的质量浓度过高时,可加锌粉,搅拌、过滤。
用锌粉1g/ L能除去15~20mg/L的Cl-。
也可用去氯剂在搅拌下慢慢加入镀液中,继续搅拌30min,静置过滤。
Cl-的质量浓度控制在20~40mg/L最为理想,不要超过80~100mg/L。
4.一价铜存在
酸性光亮镀铜液中只要有一价铜存在将造成镀层不亮。
因为电沉积时,由于一价铜总是比二价铜优先析出,所以很容易使镀层出现粗糙、毛刺,特别是在低电流密度区域镀不亮,整平能力差。
另外,如果镀液中Cl-过量时,一价铜与Cl-还会生成氯化亚铜沉淀,使镀液混浊不
清而恶化镀层质量。
一价铜是因为某些还原剂带入而产生的,有时铜阳极钝化也会产生一价铜。
为了消除一价铜的影响,可在每天班前用H2O2按0.25mL/L的体积分数稀释后加入镀液中;有时可根据阳极溶解的情况加入适量的硫酸,也能消除一价铜的影响。
最好是采用连续过滤生产的办法,使镀液更清洁,保持镀层细致光亮。
5.铜阳极钝化
阳极铜粉及一价铜的存在,通常是由于所用的阳极电流密度太大或铜阳极含磷量不适合,而使阳极钝化,造成镀层不亮。
酸性光亮镀铜阳极中磷的质量分数应在0.02%~0.07%的范围内,电解时有利于阳极表面被一层柔和的黑色膜覆盖,以减少阳极泥渣的生成,避免镀液与阳极金属表面直接接触。
这样,不仅可以防止镀层产生麻点,而且可以避免光亮剂在阳极泥上吸附和氧化分解。
如果阳极中磷的质量分数低于0.02%,电解中所形成的黑色膜就难以阻止一价铜的产生,使镀液中铜粉增加。
若磷的质量分数超过0.1%,将会严重影响阳极的溶解,造成阳极钝化,使镀液中二价铜的质量浓度下降,并生成大量阳极泥,影响镀层光亮性。
因此,最好是使用经过拉毛处理的聚丙烯布料作为阳极袋,以防止阳极泥污染镀液。
6.结语
酸性光亮镀铜液除了上述因素会引起镀层不亮之外,硫酸盐的比例失调、光亮剂本身的质量及整流器损坏缺相也会出现这种情况。
只要通过生产实践,了解和掌握影响镀层光亮性的各种因素,就可以根据实际情况进行分析处理。