模具零部件尺寸确定
模具相关尺寸的计算:

模腔尺寸的计算: (1)、型腔的径向尺寸确定:按平均值计算,塑件的平均收缩率S为0.6% 7级精度模具最大磨损量取塑件公差的1/6;模具的制造公差£z=△/3取x=0.75。
LM1 5.98O+0.48 →6.26O-0.48 (LM1)o+£z=〔(1+s)Ls1-X△〕o+£z =〔(1+0.006)×0.26-0.75×0.48〕0+0.18=5.930+0.16 ②LM2 48O+0.48 →5.28O-0.48 (LM2)o+£z=〔(1+S) ×5.28-0.75×0.48〕o+£z =4.950+0.16 ③LM3 5.15O+0.48 →5.63O-0.48 (LM3)o+£z=〔(1+S) ×5.63-0.75×0.48〕o+£z =5.300+0.16 ④LM4 1O+0.48→1.38O-0.38 (LM4)o+£z=〔(1+S) ×1.38-0.75×0.38〕o+£z=1.100+0.12 ⑤LM5 18.89O+0.88→19.77O-0.88 (LM5)o+£z=〔(1+S)×19.77-0.75×0.88〕o+£z =19.230+0.29 ⑥LM60.96O+0.38→1.34O-0.38 (LM6)o+£z=〔(1+S) ×1.34-0.75×0.38〕o+£z =1.060+0.12 ⑦LM7∮2O+0.38 →∮2.38O-0.38 (LM7)o+£z=〔(1+S) ×2.38-0.75×0.38〕o+£z =2.100+0.12 ⑧LM8 ∮6.1O+0.58 →∮6.68O-0.38 (LM7)o+£z=〔(1+S) ×6.68-0.75×0.38〕o+£z =6.290+0.19 ⑨LM9 ∮0.77→1.05 (LM9) =〔(1+S)*1.05-0.75*0.38〕=0.86 o+0.13 ⑩LM10 10.5 →11.18 (LM10) =〔(1+S)*11.18-0.75*0.68〕 =10.74 (2)、型芯高度尺寸① H 4.7 →5.18 HM1 =〔(1+S)*5.18-0.75*0.48] =[(1+0.006)*4.7+0.5*0.48]=4.97 ② H 8.9 →9.48 HM2 =〔(1+S)*9.48-0.75*0.58〕 =[(1+0.006)*8.9+0.5*0.58] = 9.25 (3)、型芯的径向尺寸:① LM1=5.98 →5.98 LM1 =[(1+s)*Ls+x△] =[(1+0.006)*5.98+0.75*0.48]= 6.37 ②LM2=2.12 →2.12 LM2 =[(1+s)*Ls+X△] =[(1+0.006)*2.12+0.75*0.38] =2.42 (4)、型腔的深度尺寸① H m1 0.77 →1.15 Hm1 =〔(1+s)Hs1-x 〕 =〔(1+0.006)*1.15-0.5*0.38〕=0.97 Hm2 10.5 →11.18 Hm1 =〔(1+s)Hs2-x 〕 =〔(1+0.006)*11.18-0.5*0.68〕 =10.9 (5)斜导柱侧抽芯机构的设计与计算①:抽芯距(S) S=S1+(2→3)㎜ = +(2→3)㎜= +(2→3)㎜ =2.93+2.5㎜ =5.43㎜②:抽芯力(Fc) Fc=chp( cos -sin ) =[2*3.14*(3.1+1)∕2*10 ]*3.5*10 *1*10 *(0.15*cos30-sin30) =60.38N ③: 斜导柱倾斜角()斜导柱倾角是侧抽心机构的主要技术数据之一,它与塑件成型后能否顺利取出以及推出力、推出距离有直接关系。
汽车模具设计标准与要求
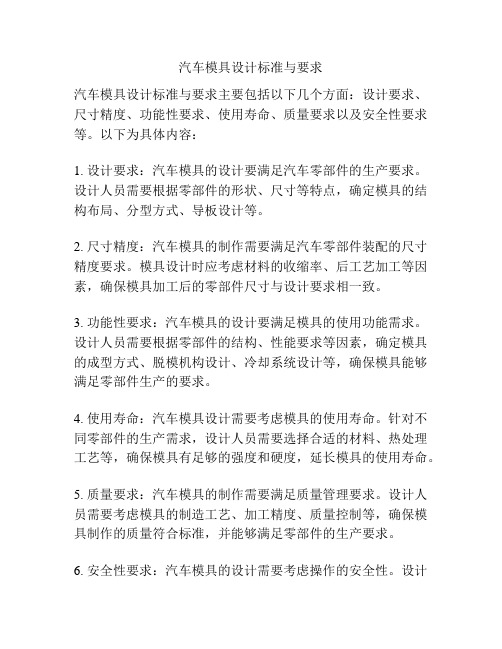
汽车模具设计标准与要求
汽车模具设计标准与要求主要包括以下几个方面:设计要求、尺寸精度、功能性要求、使用寿命、质量要求以及安全性要求等。
以下为具体内容:
1. 设计要求:汽车模具的设计要满足汽车零部件的生产要求。
设计人员需要根据零部件的形状、尺寸等特点,确定模具的结构布局、分型方式、导板设计等。
2. 尺寸精度:汽车模具的制作需要满足汽车零部件装配的尺寸精度要求。
模具设计时应考虑材料的收缩率、后工艺加工等因素,确保模具加工后的零部件尺寸与设计要求相一致。
3. 功能性要求:汽车模具的设计要满足模具的使用功能需求。
设计人员需要根据零部件的结构、性能要求等因素,确定模具的成型方式、脱模机构设计、冷却系统设计等,确保模具能够满足零部件生产的要求。
4. 使用寿命:汽车模具设计需要考虑模具的使用寿命。
针对不同零部件的生产需求,设计人员需要选择合适的材料、热处理工艺等,确保模具有足够的强度和硬度,延长模具的使用寿命。
5. 质量要求:汽车模具的制作需要满足质量管理要求。
设计人员需要考虑模具的制造工艺、加工精度、质量控制等,确保模具制作的质量符合标准,并能够满足零部件的生产要求。
6. 安全性要求:汽车模具的设计需要考虑操作的安全性。
设计
人员需要合理设置模具的安全装置、警示标识等,确保操作人员的人身安全。
总之,汽车模具设计标准与要求是为了保证模具能够满足汽车生产的需求,并达到高质量、高效率的生产目标。
模具设计人员应严格按照标准要求进行设计,确保模具的质量和安全性。
导套导柱标准尺寸
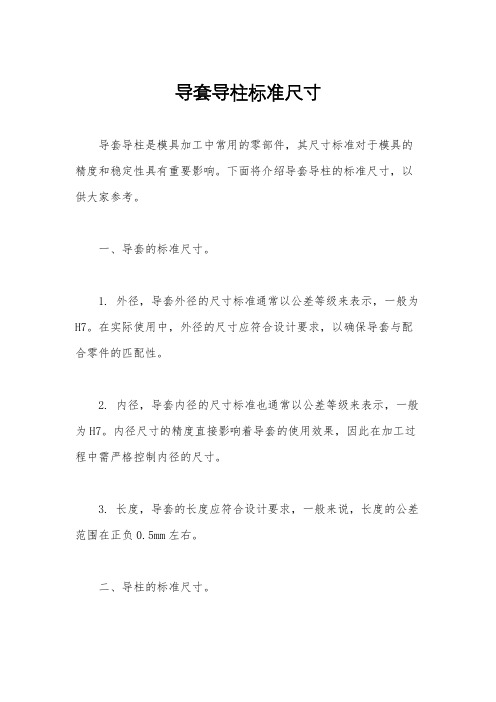
导套导柱标准尺寸导套导柱是模具加工中常用的零部件,其尺寸标准对于模具的精度和稳定性具有重要影响。
下面将介绍导套导柱的标准尺寸,以供大家参考。
一、导套的标准尺寸。
1. 外径,导套外径的尺寸标准通常以公差等级来表示,一般为H7。
在实际使用中,外径的尺寸应符合设计要求,以确保导套与配合零件的匹配性。
2. 内径,导套内径的尺寸标准也通常以公差等级来表示,一般为H7。
内径尺寸的精度直接影响着导套的使用效果,因此在加工过程中需严格控制内径的尺寸。
3. 长度,导套的长度应符合设计要求,一般来说,长度的公差范围在正负0.5mm左右。
二、导柱的标准尺寸。
1. 直径,导柱的直径尺寸标准通常以公差等级来表示,一般为h6。
导柱的直径尺寸直接影响着模具的定位和导向效果,因此在加工过程中需严格控制直径的尺寸。
2. 长度,导柱的长度应符合设计要求,一般来说,长度的公差范围在正负0.5mm左右。
导柱的长度对于模具的结构稳定性和使用效果具有重要影响。
3. 表面处理,导柱的表面通常需要进行镀铬处理,以提高其耐磨性和使用寿命。
表面处理的质量直接关系着导柱的使用效果,因此在加工过程中需严格控制表面处理的质量。
三、导套导柱的配合尺寸。
1. 间隙配合,导套和导柱的配合尺寸应符合设计要求,一般来说,配合间隙的公差范围在0.01mm左右。
配合间隙的大小直接关系着模具的精度和稳定性。
2. 表面配合,导套和导柱的表面配合应保持良好的接触状态,以确保其在使用过程中的稳定性和精度。
表面配合的质量直接关系着模具的使用效果,因此在加工过程中需严格控制表面配合的质量。
综上所述,导套导柱的标准尺寸对于模具的精度和稳定性具有重要影响,因此在加工过程中需严格控制其尺寸和配合质量,以确保模具的使用效果。
希望以上内容能够对大家有所帮助,谢谢阅读!。
汽车模具结构设计标准规范

汽车模具结构设计标准规范
汽车模具结构设计需要遵循一定的标准规范,以确保其质量和安全,具体要求如下:
1. 尺寸标准:模具尺寸应符合汽车零部件的尺寸要求。
参考汽车零部件的图纸和技术要求,确保模具的尺寸精度满足设计标准。
2. 材料要求:模具材料应选择高强度、高硬度和耐磨损的材料,如合金钢、硬质合金等。
材料的选择应满足使用寿命和使用环境的要求。
3. 结构设计:模具的结构设计应合理,确保其刚度和稳定性。
模具应易于加工和组装,并且便于维护和维修。
模具的零件要求尽量简化,以降低生产成本。
4. 冷却系统:模具应设计合理的冷却系统,以确保汽车零部件在注塑过程中能够快速冷却并保持一定的温度控制。
5. 注塑工艺要求:模具设计应考虑汽车零部件的注塑工艺要求,如射胶系统、射胶口的设置、充模比例等。
确保汽车零部件的质量和表面质量满足设计要求。
6. 模具的标准件选用:模具应尽量选用标准件进行设计和组装,并确保标准件的质量和可靠性。
7. 强度和刚度计算:模具结构应进行强度和刚度计算,确保其
能够承受正常工作状态下的载荷和应力,并防止变形。
8. 表面处理:模具的表面处理应根据汽车零部件的要求进行选择,如电镀、喷涂等。
确保汽车零部件的表面质量和外观满足设计要求。
总之,汽车模具结构设计应符合汽车零部件的要求,并满足强度、刚度、耐磨性和可维护性等方面的要求,以确保模具在使用过程中的安全和稳定性。
同时,还需要考虑到生产工艺和成本等因素,综合各个方面进行设计,以提高汽车零部件的生产效率和质量。
凸凹模刃口尺寸计算方法
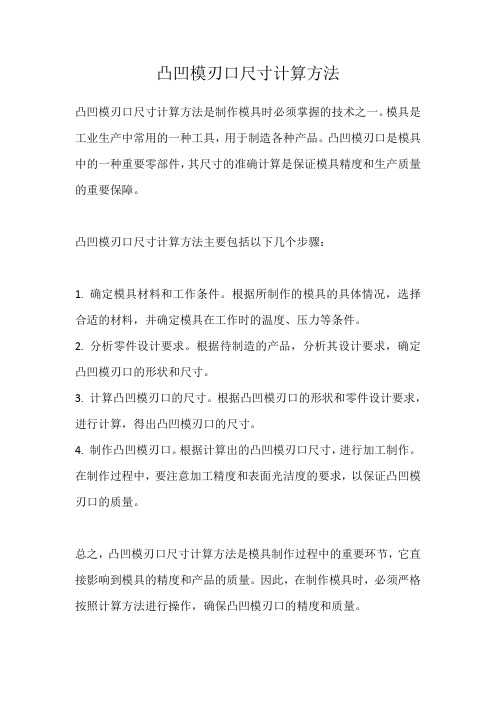
凸凹模刃口尺寸计算方法
凸凹模刃口尺寸计算方法是制作模具时必须掌握的技术之一。
模具是工业生产中常用的一种工具,用于制造各种产品。
凸凹模刃口是模具中的一种重要零部件,其尺寸的准确计算是保证模具精度和生产质量的重要保障。
凸凹模刃口尺寸计算方法主要包括以下几个步骤:
1. 确定模具材料和工作条件。
根据所制作的模具的具体情况,选择合适的材料,并确定模具在工作时的温度、压力等条件。
2. 分析零件设计要求。
根据待制造的产品,分析其设计要求,确定凸凹模刃口的形状和尺寸。
3. 计算凸凹模刃口的尺寸。
根据凸凹模刃口的形状和零件设计要求,进行计算,得出凸凹模刃口的尺寸。
4. 制作凸凹模刃口。
根据计算出的凸凹模刃口尺寸,进行加工制作。
在制作过程中,要注意加工精度和表面光洁度的要求,以保证凸凹模刃口的质量。
总之,凸凹模刃口尺寸计算方法是模具制作过程中的重要环节,它直接影响到模具的精度和产品的质量。
因此,在制作模具时,必须严格按照计算方法进行操作,确保凸凹模刃口的精度和质量。
塑料模具成型零部件尺寸影响因素及计算方法研究

,
. :
L ) r 『 七 一 式2 ‘ 叶J ( 1 + △ ( )
0
结果
结 果
5 。 0
,
∞ .3 。 1 :。
奶 l ” 2 型 芯 径 向 尺 寸
<2 7 l 9 2 a
中 25 6
0 3 I o
0 2582 D .
。
-
:
L k ,寻r 『+) 一△ 式3 H J ( 1 ( )
0
4 . 02 径向 a'7 28 0 i3 0 M : 尺寸
-
 ̄3 I 70  ̄
34 0 6
’
’
中3a ; s 。
1 91 5
do ∞ 8
兰
:! 兰
高 新 技 术
Chn w T c n lge n r d c i oNe e h oo isa d P o u t s
塑料模具成型零部件尺寸影响因素及计算方法研究
吕野 楠 丁 韧 许 光 君
(辽 宁省交通高等专科 学校机 电系, 宁 沈 阳 10 2 ) 辽 1 12
引言 : 成型零部件是直接与塑料熔 体接触 、 构成 塑料模 具模 腔的零部件 。成 型零 部件工作 尺寸是 直接 构成塑件型面 的尺寸 , 其对 塑件精 度有 直接的影 响 ,研究表明成型零部件 尺寸的 影响 因素很 多 , 尺寸的计算方法是保证 塑料 其 产 品合格的关节因素 。 1影响塑件精度 的因素及解决方法 . 1 塑料 的收缩率 . 1 塑料 的主要成分 ——合成树脂是通 过聚合 反应生产 的一 种高分子化合物 ( 亦称 聚合物 ) , 研究表 明聚合 物的分子链结构分 为线 型 、 型 体 和带有支链 的线型 , 分子排列是杂乱无 章的 。 其 由于 塑料品种 、 塑件结构 、 成型 工艺等 因素 , 导 致熔融塑料在模具 内冷却 凝固所产生 的实际收 缩率不 同, 塑料收缩率在 一定范围 内波动 , 收缩 率波动误差为 0 k ( -… m () 1 式中& —— 塑料收缩率波动误差 ,i h m k, m——塑料 最大收缩率 k, m—— 塑料最小收缩率
模具设计标准

Subject :一、(一).排位1.根据产品大小、结构等因素确定模穴,如1X1、1X2、1X3、1X4、1X8、1X16 等。
2.当几个产品出在同一套模具中时,考虑进胶的均匀性。
应将大的产品排在中间位置,小的产品置于两边。
3.当几个分型面不规则的产品在同一模具中时,排位必须充分考虑其分型面连接的顺畅。
4.一模多穴模具中,当有镶拼、行位等结构时,不得使其发生干涉。
5.排位时应综合模具每一方面,对流道,是否镶拼、行位、顶出、运水等结构要有一个全局性思考。
6.排位时以产品零线为定位基准。
当一模出一件时,可以考虑以产品对称方向外形分中。
(二)、模具系统设计【模具系统设计程序】浇注系统内模结构行位系统顶出系统冷却系统导向定位系统排气系统模胚结构件。
说明﹕在具体的模具设计过程中﹐不一定会严格遵守此程序﹐通常我们要返回上一步甚至上几步﹐修改部分数值﹐直至最后确认。
1﹑浇注系统浇注系统由主流道﹑分流道﹑冷料井和浇口等部分组成。
在设计浇注系统时,要考虑: 制品最主要的要求是什么?外观还是强度或是尺寸精度,找出最主要的矛盾,设计时,立足主要矛盾,同时,在不与主要矛盾发生冲突的前提下,改善其它次要矛盾,要做到进浇的均匀与顺畅。
1.1.主流道主流道一般为圆锥形,角度2~4o1.2.分流道1.2.1 .分流道的形状有圆形﹑梯形等几种,从减少压力和热量损失的角度来看, 圆形流道是最优越的流道形状。
当分型面是平面或者曲面时,一般采用圆形流道;细水口模,选用梯形流道,当流道只开在前模或者后模时,则选用梯形流道。
1.2.2.布置一模多腔的流道时,应充分考虑进浇的均匀性,尽可能做到平衡进浇。
1.2.3.设计分流道大小时,应充分考虑制品大小,、壁厚、材料流动性等因素,流动性不好的材料如PC料其流道应相应加大,并且分流道的截面尺寸一定要大于制品壁厚,同时应选适合成形品形状的流道长度。
流道长则温度降低明显,流道过短则剩余应力大,容易产生“喷池”,顶出也较困难。
din 1530标准

din 1530标准DIN 1530标准是指德国标准化协会(DIN)制定的一项关于模具零部件的标准。
该标准涵盖了模具零部件的尺寸、材料、加工工艺等方面,对于模具制造行业具有重要的指导意义。
本文将对DIN 1530标准进行详细介绍,以便更好地了解和应用这一标准。
首先,DIN 1530标准主要适用于注塑模具、压铸模具、冲压模具等各类模具的零部件。
它规定了模具零部件的尺寸公差、表面粗糙度、材料硬度等技术要求,旨在保证模具零部件的质量和可靠性。
遵循DIN 1530标准可以有效提高模具的加工精度和使用寿命,降低模具制造成本,提高生产效率。
其次,DIN 1530标准对于模具零部件的材料选择提出了明确的要求。
根据不同的工作环境和工艺要求,标准规定了模具零部件应选用的材料种类和硬度等级。
这些要求旨在确保模具零部件具有足够的强度、耐磨性和耐腐蚀性,以满足模具在生产过程中的各种工况要求。
此外,DIN 1530标准还对模具零部件的加工工艺和检测方法进行了规范。
标准要求模具零部件的加工应符合一定的工艺要求,包括精密加工、热处理工艺、表面处理等。
同时,标准还规定了模具零部件的检测方法和标准,以确保模具零部件的质量符合设计要求。
总的来说,DIN 1530标准是模具制造行业的重要标准之一,它对模具零部件的设计、制造、加工和检测提出了一系列具体要求。
遵循DIN 1530标准可以帮助模具制造企业提高产品质量、降低成本、提高竞争力。
因此,熟练掌握和准确应用DIN 1530标准对于模具制造企业来说至关重要。
综上所述,DIN 1530标准对模具制造行业具有重要的指导作用,它规定了模具零部件的尺寸、材料、加工工艺等方面的具体要求。
遵循DIN 1530标准可以帮助模具制造企业提高产品质量、降低成本、提高竞争力。
因此,我们应该充分认识和理解DIN 1530标准的重要性,切实做好标准的贯彻执行工作,以推动模具制造行业的健康发展。
- 1、下载文档前请自行甄别文档内容的完整性,平台不提供额外的编辑、内容补充、找答案等附加服务。
- 2、"仅部分预览"的文档,不可在线预览部分如存在完整性等问题,可反馈申请退款(可完整预览的文档不适用该条件!)。
- 3、如文档侵犯您的权益,请联系客服反馈,我们会尽快为您处理(人工客服工作时间:9:00-18:30)。
模具零、部件的尺寸确定
所以在已颁布的国家标准中在一定的尺寸范围内给出了孔和轴配合公差的尺寸。
但我们发现:在模具零、部件制造时很难实施和得以应用,也就是说我们在制作一个模具零、部件时无法按国家标准所制定的孔和轴配合公差尺寸给定模具零、部件尺寸和公差。
假设我们要制作一个尺寸为200mm×200mm×85mm这样一个镶块。
原则上这样一个镶块应视作为轴;参照现行的国家标准我们选取了G6的配合。
其公差值为?-0.015。
那么这个镶块的上限尺寸为:200mm×200mm×85mm,下限为:199.985 mm×199.985 mm×84.988 mm。
假如我们做到了以上所要求的尺寸,200 mm×200 mm×85mm的下限即:199.985mm×199.985mm×84.988mm,按照标准,这个零件是合格的。
而与其相匹配的孔我们取G6的公差。
其公差值为0.044。
则这个孔的上限为:200.044mm×200.044mm×85.034mm。
下限为:200mm×200mm×85mm。
如果我们将这个孔的尺寸做到它的上限200.044mm×200.044mm×85.034mm。
按照选定的标准,这个尺寸也是合格的。
现在我们先不去考虑它的几何形状是否符合要求,但我们发现;当“轴”的尺寸在下限时,“孔”的尺寸在上限时,以上二个几何体之间存在着0.059的间隙(其平均值为单边0.03),假设我们使用的成型材料为PP,而PP 料的溢边值是0.02,那么这个间隙就可能会产生“飞边”,从而满足不了要求;何况受到各种困素的影响,而这个理论上的单边0.03的间隙在实际上是无法均衡取得的,这就使得我们在实际操作上带来一系列问题;首先我们如何给定名义尺寸;如果我们给这个镶块和与其配合的孔都给定为200×200×85,这就是我们通常所说的“零配零”,但我们大家都知道;实际上这是很难做到的,即使做到了也不一定能适用。
这是因为零、部件除了名义尺寸的准确外,还有一个几何形状的问题。
我所通常看到的零件图或者是3D造型所提供的数据,多数是“零配零”的尺寸。
实际上这是不正确、不合理的。
我们都知道,采用不同的加工手段和采用不同类型加工机,其结果是不一样的。
这个镶块和与其配合的孔可以用CNC.EDM.W/C.普通铣床等加工机床来完成,而不同类型、不同加工手段和不同类型的加工机会产生不同等级的表面粗糙度,所以必须根据不同类型加工机和不同的加工手段来考虑加工后应预留精细加工的余量,而这个余留量是很难确定的。
不同类型加工机,加工工艺,操机人员的技术能力,甚至工件的装、夹是否正确、合理都会对尺寸产生很大的影响;这些问题要想在给定名义尺寸时都考虑的十分周到是非常困难的,何况在我们很多模具制造企业没有工艺部门来制订加工工艺,设计部门或设计人员无法确定到底用哪种设备来加工这个零、部件,所以我们通常都采用加大余留量的办法来解决它,这实际上是一个无可奈何之举;但是,这个无可奈何之举也给后续加工带来了很大的工作量。
我们可以看到钳工经常使用电磨头、角向砂轮、锉刀等手动工具在修正尺寸;这样做的效果是显而易见的,而这种不规范的加工手段既增加了劳动强度,又消耗了工作时间而效果却十分的差。
综观我们宁海地区的模具在结构的设计方面是做的比较好的,但是在表面、外观上有一部份产品确实令人不敢恭维,有的制品用“惨不忍睹”来形容也丝毫不为过,而造成这种不良现象的一个重要原因也是与设计给定的名义尺寸时不能正确、合理的给定配合尺寸、公差有着很大的关系。
讲到这里,有的人可能会说这是由于我们的加工机的精度、档次不高所造成的;但我想,这虽是一个重要的方面,但也不尽然;即使我们的某些零、部件尺寸精度达到了纳米级,它还会与其相配合的零、部件存在着装配关系;如果我们给不了一个正确、合理的配合尺寸,问题照样会出现;因为我看到有的模具制造企业所拥有的加工设备其精度可以控制到0.01~0.02之间,从理论上说是可以满足一般产品的要求了。
但光是一个零、部件的尺寸达到了要求,而在装配关系上没有得到合理的处置,而是需要用人工修磨的手段来达到装配要求,同样得不到良好的效果。
所以有的模具制造企业尽管拥有高精度的加工设备,但在进行模具组装时仍有人在从事人工修磨的工作。
所以说单凭某个零件尺寸精度达到了要求,还不能完全满足整个模具的功能和产品的要求。
另外还有一个问题就是如何去判定一个零、部件的尺寸是否能满足使用要求?一般的模具制造企业都配置了检测设备如:三座标测量仪。
它可以检测到小数点后的三位值,它可以检测出一个零、部件的尺寸,但很少有人
能判定一个零、部件的尺寸是否能符合和满足使用要求;这是一个普遍存在的问题。
由于上述问题的存在,也给我们的设计人员提出了一个严峻的问题:就是如何给模具零、部件一个合适的尺寸?这就对模具的设计人员和制造者提出了一个非常高的要求;以上面所列的镶块为例:这个镶块我们采用了线切割来成型,其中高度20mm为栽入部份,斜度取为1°。
其余部份为成型面,脱模斜度取1°30′,产品要求表面粗糙度在Ra3.2以上,成型材料为PP,根据要求,达到Ra3.2以上的表面粗糙度手工抛光时用到800#水砂就基本可以满足;现根据以往的綷-验,用线切割成型的零件表面的粗糙度一般在Ra12.5左右,要想达到Ra3.2以上的表面粗糙度,零件表面单面应留出0.06~0.08的(抛光)加工余量。
同时这个镶块在模具上为轴,而在制品上则为孔。
我们取GB/T1804-2000中线性尺寸的极限偏差数值中m级所制定的值200mm+0.50mm=200.50mm。
65mm+0.30mm=65.30mm。
在此我们取收缩率0.16%,则这个镶块的尺寸为200.82mm×200.82mm×65.31mm,再加上抛光所需的单边0.08mm的加工余量,镶块的尺寸应为200.90mm×200.90mm×65.39mm。
同时我们还要考虑到分子流向所产生的尺寸变异,200.90mm×200.90mm这个尺寸未必是合理的。
当然对一般要求的产品而言,问题还不算太大,但对精度要求很高的产品而言,可能就会满足不了要求。
模具零、部件实行标准化是很多模具制造企业在追求的一个目标,但上述问题的存在又是一个非常突出的而又普遍存在的问题,要实行模具零、部件标准化,这是一个必须解决的问题。