Deep desulfurization of diesel fuel by extraction with ionic liquids
SBA-15负载磷钼钒杂多酸催化柴油氧化脱硫

SBA-15负载磷钼钒杂多酸催化柴油氧化脱硫李金磊;胡兵;杨玉皖;彭贝根【摘要】Oxidative desulfurization was studied using H2C>2 as oxidant,and PMoV/SBA-15(supported mo-lybdovanadophosphoric heteropoly acids) prepared by wet-impregnation method as catalyst. The influences of loading amount of H5PMo10 V2O40 ,reaction temperature,reaction time, volume ratio of oxidant to diesel on the desulfurization efficiency were investigated. The optimum conditions were obtained as follows: the loading a-mount of H5PMo10 V2O40 was 60%,catalyst dosage was 0.2 g,reaction time was 90 min, reaction temperature was 80 °C and volume ratio of oxidant to diesel was 1 : 5. Under above conditions, the desulfurization rate reached 98. 1%.%以浸渍法制备的SBA-15负载磷钼钒杂多酸(PMoV/SBA- 15)为催化剂、H2O2为氧化剂,对模拟柴油进行催化氧化脱硫,考察了H5PMo10VzO40的负载量、反应温度、反应时间、氧化剂和模拟柴油体积比对脱硫效果的影响.确定最优反应条件为:H5PMo10V2O40(负载量60%)/SBA-15催化剂用量0.2g、反应温度80℃、反应时间90 min、氧化剂和模拟柴油体积比1∶5,在此条件下,脱硫率可达98.1%.【期刊名称】《化学与生物工程》【年(卷),期】2012(029)003【总页数】3页(P27-29)【关键词】磷钼钒杂多酸;SBA-15;漫渍法;氧化脱硫【作者】李金磊;胡兵;杨玉皖;彭贝根【作者单位】湖北工业大学化学与环境工程学院,湖北武汉430068;湖北工业大学化学与环境工程学院,湖北武汉430068;湖北工业大学化学与环境工程学院,湖北武汉430068;湖北工业大学化学与环境工程学院,湖北武汉430068【正文语种】中文【中图分类】TE624燃料油中有机硫化物燃烧后生成的SOx是汽车尾气的主要污染物之一。
几篇石化文章的汉译英
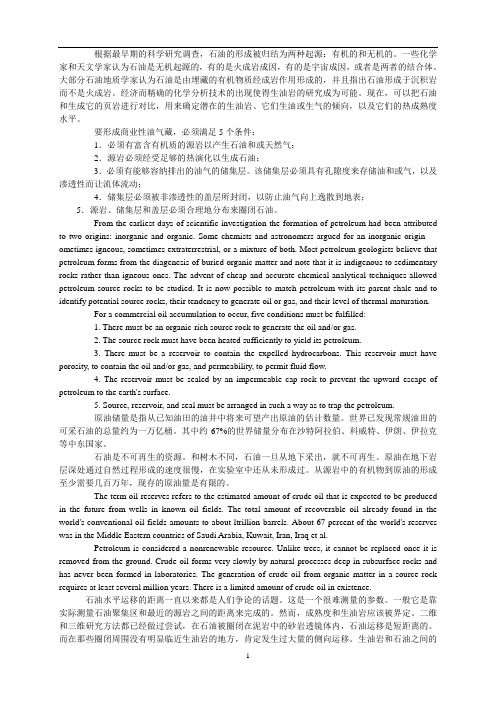
根据最早期的科学研究调查,石油的形成被归结为两种起源:有机的和无机的。
一些化学家和天文学家认为石油是无机起源的,有的是火成岩成因,有的是宇宙成因,或者是两者的结合体。
大部分石油地质学家认为石油是由埋藏的有机物质经成岩作用形成的,并且指出石油形成于沉积岩而不是火成岩。
经济而精确的化学分析技术的出现使得生油岩的研究成为可能。
现在,可以把石油和生成它的页岩进行对比,用来确定潜在的生油岩、它们生油或生气的倾向,以及它们的热成熟度水平。
要形成商业性油气藏,必须满足5个条件:1.必须有富含有机质的源岩以产生石油和或天然气;2.源岩必须经受足够的热演化以生成石油;3.必须有能够容纳排出的油气的储集层。
该储集层必须具有孔隙度来存储油和或气,以及渗透性而让流体流动;4.储集层必须被非渗透性的盖层所封闭,以防止油气向上逸散到地表;5.源岩、储集层和盖层必须合理地分布来圈闭石油。
From the earliest days of scientific investigation the formation of petroleum had been attributed to two origins: inorganic and organic. Some chemists and astronomers argued for an inorganic origin --- ometimes igneous, sometimes extraterrestrial, or a mixture of both. Most petroleum geologists believe that petroleum forms from the diagenesis of buried organic matter and note that it is indigenous to sedimentary rocks rather than igneous ones. The advent of cheap and accurate chemical analytical techniques allowed petroleum source rocks to be studied. It is now possible to match petroleum with its parent shale and to identify potential source rocks, their tendency to generate oil or gas, and their level of thermal maturation.For a commercial oil accumulation to occur, five conditions must be fulfilled:1. There must be an organic-rich source rock to generate the oil and/or gas.2. The source rock must have been heated sufficiently to yield its petroleum.3. There must be a reservoir to contain the expelled hydrocarbons. This reservoir must have porosity, to contain the oil and/or gas, and permeability, to permit fluid flow.4. The reservoir must be sealed by an impermeable cap rock to prevent the upward escape of petroleum to the earth's surface.5. Source, reservoir, and seal must be arranged in such a way as to trap the petroleum.原油储量是指从已知油田的油井中将来可望产出原油的估计数量。
脱除油品中噻吩类硫化物的研究进展

脱除油品中噻吩类硫化物的研究进展赵阳;张君涛;申智兵;默云娟;陈英敦【摘要】简单介绍了噻吩类硫化物的必要性以及传统加氢脱硫技术并提出传统脱除方法在脱除噻吩类硫化物方面的局限性,氧化脱硫技术成为脱除油品中噻吩类硫化物的新方法,主要介绍了双氧水/有机酸和双氧水/杂多酸两种体系在氧化脱硫方面的研究进展.【期刊名称】《当代化工》【年(卷),期】2015(044)012【总页数】4页(P2811-2813,2817)【关键词】噻吩类硫化物;氧化脱硫;双氧水【作者】赵阳;张君涛;申智兵;默云娟;陈英敦【作者单位】西安石油大学石油炼化工程技术研究中心,陕西西安710065;西安石油大学石油炼化工程技术研究中心,陕西西安710065;西安石油大学石油炼化工程技术研究中心,陕西西安710065;西安石油大学石油炼化工程技术研究中心,陕西西安710065;中国石油塔里木油田分公司,新疆维吾尔自治区巴音郭楞蒙古自治州库尔勒市841000【正文语种】中文【中图分类】TE624近年来,随着环保要求的不断提高,汽油和柴油的标准也在不断提高,不同国家的经济发展水平不同,汽油和柴油的生产过程各不相同,但对于汽柴油硫含量的控制都是日趋严格[1]。
有国家通过立法将含硫量控制在10~15×10-6。
因此,改善油品性质、严格控制含硫量成为油品发展的必然趋势。
汽油组成性质对汽车尾气组成的影响如表1。
由表1可以看出降低汽油中的硫含量可以最大程度地改善尾气的排放,因此低硫甚至无硫化成为升级油品质量的关键因素。
根据原油来源及其加工方法的不同,原油中的硫可以分为元素硫、二硫化物、硫化氢、硫醇类、硫醚类、噻吩及其同系物等,其中后两者之和占总硫量的85 %以上。
国内部分炼油厂的有机硫含量如表2。
从表2中可以看出,硫醚硫和噻吩硫是脱硫的主要对象。
其中硫醚硫可以通过加氢脱硫技术除去,而噻吩类硫化物是五元杂环化合物,杂原子的未共用电子对参与了芳香性的6π电子体系的形成[2],化学性质类似芳香烃,很难发生裂化脱硫,这就导致噻吩类硫化物在加氢脱硫条件下难以脱除。
开题报告最终版

[4] Brunet S,Mey D,Appl Catal A,perot G,et al. On the Hydrodesulfurization of FCC Gasoline:a Review[J].Appl Catal A,2005,278 (2):143-172 [5] Shan H,Li C,Yang C,et al.Mechanistic Studies on Thiophene Species Cracking over USY Zeolite.Catal Today[J],2002,77(1-2):117-126 [6] Yu S,Waku T,Iglesia E.Catalytic Desulfurization of Thiophene on HZSM-5 Using Alkanes as Coreactants.Appl Catal A[J],2003,242(1):111一121
掺杂不同价态Ce的MCM-41得脱硫效果
[9] 崔榕.Ce-MCM-41分子筛吸附剂的制备及其在模拟汽油脱硫中的性能[J].天然气与化 工.2008,33(2):11-16
14
3.研究思路
可以看到,适量的引入稀土离子对分子筛改性,对 选择性脱硫有帮助。另一方面,利用分子筛的酸性 可以增加异构化的产物,使辛烷值得到恢复。
所以为了提高催化剂对汽油中硫化物的吸附选择性,应尽可能使金属离子的
π络合作用减少,和噻吩类化合物只形成S-M直接作用。
New design approaches to ultra-clean diesel fuels by deep desulfurization and deep dearomatization

Applied Catalysis B:Environmental41(2003)207–238New design approaches to ultra-clean diesel fuels by deepdesulfurization and deep dearomatizationChunshan Song∗,Xiaoliang MaClean Fuels and Catalysis Program,Department of Energy and Geo-Environmental Engineering,The Energy Institute, The Pennsylvania State University,209Academic Projects Building,University Park,PA16802,USAReceived17January2002;accepted27January2002AbstractThis paper is a selective review on design approaches and associated catalysis and chemistry for deep desulfurization and deep dearomatization(hydrogenation)of hydrocarbon fuels,particularly diesel fuels.The challenge for deep desulfurization of diesel fuels is the difficulty of removing the refractory sulfur compounds,particularly4,6-dimethyldibenzothiophene, with conventional hydrodesulfurization processes.The problem is exacerbated by the inhibiting effect of polyaromatics and nitrogen compounds,which exist in some diesel blend stocks on deep HDS.With the new Environmental Protection Agency (EPA)Tier II regulations to cut the diesel sulfur from current500ppmw down to15ppmw by June2006,refineries are facing major challenges to meet the fuel sulfur specification along with the required reduction of aromatics contents.The principles and problems for the existing hydrodesulfurization processes,and the concepts,advantages and disadvantages of various new approaches will be discussed.Specifically,the following new design approaches for sulfur removal will be discussed:(1) novel catalysts for ultra-deep hydrodesulfurization under conventional HDS process conditions;(2)new design concept for sulfur-tolerant noble metal catalysts for low-temperature hydrogenation;(3)new desulfurization process by sulfur adsorption and capture under H2;(4)new desulfurization process by selective adsorption at ambient temperature without H2and a related integrated process concept;(5)oxidative desulfurization in liquid-phase;and(6)biodesulfurization.©2002Elsevier Science B.V.All rights reserved.Keywords:Ultra-clean diesel;Deep desulfurization;Deep dearomatization;Catalyst;Adsorption;SulfurAbbreviations:4,6-DMDBT,4,6-dimethyldibenzothiophene; 4,6-DEDBT,4,6-diethyldibenzothiophene;DBT,dibenzothio-phene;EIA,Energy Information Administration;EPA,Environ-mental Protection Agency;FCC,fluid catalytic cracking;GO,gas oil,a middle distillate fraction from;HDS,hydrodesulfurization; LCO,light cycle oil,derived from FCC;MBPD,million barrels per day;RIA,regulatory impact analysis;PASH,polycyclic aro-matic sulfur heterocycles;SRGO,straight-run gas oil∗Corresponding author.Tel.:+1-814-863-4466;fax:+1-814-865-3248.E-mail address:csong@(C.Song).1.IntroductionClean fuels research including desulfurization and dearomatization has become an important subject of environmental catalysis studies worldwide.The US Clean Air Act Amendments of1990and the new reg-ulations by the US Environmental Protection Agency (EPA),and government regulations in many countries call for the production and use of more environmen-tally friendly transportation fuels with lower contents of sulfur and aromatics[1–4].In the mean time,the demand for transportation fuels has been increasing in most countries for the past two decades.Essentially,0926-3373/02/$–see front matter©2002Elsevier Science B.V.All rights reserved. PII:S0926-3373(02)00212-6208 C.Song,X.Ma/Applied Catalysis B:Environmental41(2003)207–238all of these liquid fuels are produced from petroleum except in South Africa(where a coal-based gasifica-tion system produces the synthesis gas which is then converted to liquid fuels).The total US consumption of petroleum products reached18.68million barrels per day(MBPD)in1998.Of the petroleum con-sumed,8.20MBPD was used as motor gasoline,3.44 MBPD as distillate fuels(including diesel fuels and industrial fuels),1.57MBPD as jet fuels,0.82MBPD as residual fuel oil,and 1.93MBPD as liquefied petroleum gas(LPG),and2.72MBPD for other uses [5].Currently,about2.2million barrels of diesel fuel is consumed everyday in the US road transportation mar-ket[6].Increasing attention worldwide is being paid to chemistry of diesel fuel processing.This height-ened interest is related to both the thermal efficiency and the environmental aspects,which include both the pollutants and greenhouse gas emissions.Accord-ing to a recent analysis,diesel fuel demand is ex-pected to increase significantly in the early part of the 21st century and both the US and Europe will be in-creasingly short of this product[7].Sulfur content in diesel fuel is an environmental concern because upon combustion,sulfur is converted to SO x during com-bustion,which not only contributes to acid rain,but also poisons the catalytic converter for exhaust emis-sion treatment.Sulfur content is usually expressed as the weight percent(wt.%)of sulfur in the fuel,since there are many different sulfur-containing compounds in petroleum-derived fuels.Dramatic changes occurred in many countries con-cerning diesel sulfur regulations in the past decade [8,9].The maximum sulfur content of highway diesel fuel in the US was reduced by regulations,from about 0.20–0.50wt.%in the late1980s[10,11]to0.05wt.% on1October1993for all highway(on-road)diesels [3].The sulfur content of diesel fuel in western Eu-rope was limited to0.3wt.%in1989to0.2wt.%in 1994,and further reduced to0.05wt.%from1Octo-ber1996.The diesel sulfur content in Japan was re-duced by regulation from0.4to≤0.2wt.%in1993, and further to≤0.05wt.%in1997.Canadian govern-ment regulations required that all diesel fuels sold must contain no more than0.05wt.%sulfur since January 1998.Currently,the fuel specifications for all highway diesel fuels in the US,Japan,and western Europe limit the sulfur content of the diesel fuels to be less than0.05wt.%or500parts per million by weight (ppmw).The new government regulations in many countries will further lower the contents of sulfur and aromatics in the year2004–2007[12].In January 2001,US EPA announced new rules that will require a97%reduction in sulfur content of highway diesel fuel to15ppmw from current500ppmw,starting from June2006[13].New gasoline sulfur regula-tions will require most refiners to meet a30ppmw sulfur average with an80ppmw cap for both conven-tional and reformulated gasoline by1January2006 [14,15].The problem of deep removal of sulfur has be-come more serious due to the lower and lower limit of sulfur content infinished fuel products by regula-tory specifications,and the higher and higher sulfur contents in the crude oils.A survey of the data on crude oil sulfur content and API gravity for the past two decades reveals a trend that US refining crude slates continue towards higher sulfur contents and heavier feeds[16,17].The average sulfur contents of all the crude oils refined in thefive regions of the US known asfive Petroleum Administration for Defense Districts(PADDs)increased from0.89wt.%in1981 to1.25wt.%in1997,while the corresponding API gravity decreased from33.74◦in1981to31.07◦in 1997.The heightened interests in ultra-clean fuels are also due to the need for using new emission con-trol technologies for IC engines(especially those for diesel fuels),and for using on-board or on-site reforming of hydrocarbon fuels for new fuel cell ve-hicles.Our studies on clean fuels have focused on deep desulfurization and dearomatization of diesel and jet fuels as well as gasoline([18–22]Turaga and Song,2001).One new application area which presents great challenge to ultra-deep desulfurization of liq-uid hydrocarbon fuels is hydrocarbon fuel processor for proton-exchange membrane fuel cells,which es-sentially require zero-sulfur fuels,such as gasoline and diesel fuels[23].The general chemistry of diesel fuels is covered by a recent book[8,9].This paper is a selective overview on new design approaches and associated catalysis and chemistry as well as processes for deep desulfurization and deep hydro-genation of hydrocarbon fuels,particularly diesel fuels.C.Song,X.Ma /Applied Catalysis B:Environmental 41(2003)207–238209Table 1V olume fraction of US highway diesel pool from each feedstock component Diesel blendstockPercentage of US highway diesel fuel pool per blendstock boiling fraction NaphthaLight distillate Heavy distillate Light gas oil All boiling fractions combined Straight-run0.1 6.4 4.9 1.012.4Hydrotreated straight-run 0.38.141.2 2.351.9Cracked stock–0.10.8 2.2 3.1Hydrotreated cracked stock – 2.115.6 1.719.4Coker gas oil–– 1.0– 1.0Hydrotreated coker gas oil 0.1 2.1 3.7 2.38.2Hydrocrackate–1.32.7–4.0Source:EPA,EPA420-R-00-026,2000.2.Sulfur compounds in transportation fuels There are three major types of transportation fuels,gasoline,diesel and jet fuels that differ in composition and properties [140–143].The common types of sulfur compounds in liquid fuels are listed below.•Gasoline range:naphtha,fluid catalytic cracking (FCC)–naphtha,◦mercaptanes (RSH);sulfides (R2S);and disul-fides (RSSR);◦thiophene and its alkylated derivatives;◦benzothiophene.•Jet fuel range:heavy naphtha,middle distillate,◦benzothiophene (BT)and its alkylated deriva-tives.•Diesel fuel range:middle distillate,light cycle oil (LCO),◦alkylated benzothiophenes;Table 2Sulfur levels of US highway diesel blendstocks (CA excluded)Diesel blendstockSulfur content (ppmw)by boiling fraction NaphthaLight distillate Heavy distillate Light gas oil All boiling fractions combined Straight-run8271770226949802218Hydrotreated straight-run 362119394548358Cracked stock–221928926347a 5322Hydrotreated cracked stock 183********a874Coker gas oil54018003419–3419Hydrotreated coker gas oil 825310400258Hydrocrackate –12120–85Source:EPA,EPA420-R-00-026,2000.a Indicating properties that were not reported in the refiner survey.These values were calculated by EPA using the reported sulfur contents of like boiling fractions in other diesel blendstocks by assuming the same relative sulfur levels between boiling fractions.◦dibenzothiophene (DBT)and its alkylated deriva-tives.•Boiler fuels feeds:heavy oils and distillation re-sides,◦≥3-ring polycyclic sulfur compounds,including DBT,benzonaphthothiophene (BNT);◦phenanthro[4,5-b ,c ,d ]thiophene (PT),and their alkylated derivatives.Table 1shows the volume fraction of US high-way diesel pool and Table 2shows the corresponding sulfur levels of US highway diesel blendstocks [12].Among the diesel blendstocks,the light cycle oil from fluid catalytic cracking contains highest amount of sulfur and aromatics,and the LCO also tends to have the highest contents of refractory sulfur compo-unds,especially 4-methyldibenzothiophene (4-MDBT)and 4,6-dimentyldibenzothiophene (4,6-DMDBT)[12].210 C.Song,X.Ma /Applied Catalysis B:Environmental 41(2003)207–238There are various 2-and 3-ring sulfur compounds in middle distillates from various refinery streams that can be used to make middle distillate fuels-diesel fu-els and jet fuels.Kabe and co-workers have analyzed the sulfur compounds in a light gas oil (LGO)and hydrotreated gas oils using gas chromatography with atomic emission detector (GC–AED)and GC–mass spectrometer (GC–MS)[24,25].They found that there were 42alkylated benzothiophene compounds and 29alkylated dibenzothiophene compounds in the oil.Among them,the 4,6-DMDBT was found to remain even after deep hydrodesulfurization [24,26].Ma et al.have analyzed the sulfur compounds in a gas oil and a non-polar fraction of vacuum gas oil [27–31].They found that the major sulfur compounds are alkyl ben-zothiophenes and alkyl PBT in the gas oil,and alkyl thiophenes,alkyl benzothiophenes,alkyl DBT,alkyl BNT and alkyl PT in the vacuum gas oil.The diben-zothiophenes with two alkyl substituents at 4-and 6-positions,respectively,were found to be the sulfur compounds that are the most difficult to beremoved Fig.1.GC–FPD chromatograms of commercial gasoline,jet fuel and diesel.from the oils.Hsu and co-workers have performed mass spectrometric analysis of many diesel fuels and petroleum fractions [32,33].They have identified not only the major compounds in all classes,but also trace amounts of heteroatom-containing compounds.Trace amounts of nitrogen compounds in diesel fuels include indoles,carbazoles,quinolines,acridines,and phenanthridines.The oxygen compounds are alky-lated phenols and dibenzofurans.Formulated diesel fuels also contain trace amounts of additives.Recently,we have conducted a detailed analysis to identify the type of sulfur compounds and their alky-lated isomers in a commercial gasoline sample and a commercial diesel fuel sample which were purchased in 2001from local fuel station in State College,Pennsylvania,and a JP-8type jet fuel sample from Wright Laboratory of US Air Force.Fig.1shows the GC–FPD chromatograms of the three transportation fuel samples analyzed in our laboratory [18].The identification of different alkylated polycyclic sulfur compounds and their isomers is complicated,sinceC.Song,X.Ma/Applied Catalysis B:Environmental41(2003)207–238211there are a few commercially available standards and their mass spectra(e.g.fragmentation patterns)are often similar for most isomers of alkyl thiophenic compounds.In our group,we did the identification of the sulfur components in the gasoline,jet fuel and diesel fuel based on a combination of various techniques,standard sample,HPLC separation[31], sulfur-selective ligand exchange chromatography [31],GC–MS[27,31],retention time comparison with the literature data[34,35],reactivities of various sul-fur compounds in HDS[27,30]and an understanding of the elution order of the isomers[36].As shown in Fig.1,the major sulfur compounds existing in the commercial gasoline are thiophene, 2-methylthiophene,3-methylthiophene,2,4-dimethyl-thiophene and benzothiophenes,indicating that most sulfur compounds with higher HDS reactivity,includ-ing thiols(mercaptans),disulfides and sulfides,have been removed from the commercial gasoline in cur-rent processes.The major sulfur compounds in the JP-8are dimethylbenzothiophenes and trimethylben-zothiophenes with two methyl groups at the2-and 3-positions,respectively,implying that these alkyl benzothiophenes are more difficult to be removed than their isomers.No dibenzothiophenes was detected in the JP-8.The sulfur compounds in the commercial diesel fuel include alkyl benzothiophenes and alkyl dibenzothiophenes,but the major sulfur compounds are the alkyl dibenzothiophenes with alkyl groups at the4-or/and6-positions,indicating that the major sulfur compounds remaining in the commercial diesel fuel are the refractory sulfur compounds,which are difficult to be removed by the conventional HDS process.Fig.1also clearly demonstrates that sulfur com-pounds tend to become larger in ring size and higher in number of substitutes as the fuel becomes higher in boiling point ranges from gasoline to jet fuels to diesel fuels.The current sulfur contents in highway (on-road automotive)diesel fuel and gasoline are lim-ited to500ppm and350ppmw,respectively,by reg-ulations in the US.The jet fuel sulfur is limited to 3000ppmw.Sulfur level in typical jet fuel was re-ported to be490ppmw[37].The real sulfur contents in commercially available gasoline and diesel fuel sam-ples are typically lower than the regulatory upper lim-its.This statement applies to commercial and military jet fuels as well.3.Challenges of ultra-deep desulfurization of diesel fuels3.1.Reactivities of sulfur compoundsFig.2shows the qualitative relationship between re-activities of sulfur compounds and their ring size and substitution.The organic sulfur compounds present in petroleum vary widely in their reactivities in catalytic hydrodesulfurization.Deeper hydrodesulfurization (HDS)is not a simple increase in conversion of to-tal sulfur compounds by a pseudofirst order.There are many different sulfur compounds in diesel fuels. Earlier research has shown that certain sulfur com-pounds are easier to convert.The reactivities of the1-to3-ring sulfur compounds decrease in the order of thiophenes>benzothiophenes>dibenzothiophenes [38–42].In naphtha,thiophene is so much less reac-tive than the thiols,sulfides,and disulfides that the latter can be considered to be virtually infinitely reac-tive in practical high-conversion processes[43,44]. Similarly,in gas oils,the reactivities of(alkyl-substi-tuted)4-methyldibenzothiophene and4,6-dimethyldi-benzothiophene are much less than those of other sulfur-containing compounds[24,27,44,45].Conse-quently,in deep HDS,the conversion of these key substituted dibenzothiophenes largely determines the required conditions.Gates and Topsoe[44]pointed out in1997that4-methyldibenzothiophene and4,6-dimethyldibenzothiophene are the most appropriate compounds for investigations of candidate catalysts and reaction mechanisms.While the new regulation will further reduce the environmental impact of diesel emissions,it cre-ates a major technical challenge for fuel processing [46,47].It is the most refractory sulfur species that remains in the diesel fuel after sulfur reduction to 500ppmw level by conventional hydrodesulfurization [24,27,30,44,45,48–51].For desulfurization of sulfur species in gasoline,it is not difficult to remove the sul-fur compounds in naphtha range by current catalytic HDS processes.For the US refineries,most sulfur in gasoline pool is found in FCC naphtha.The challenge in deep desulfurization of FCC naphtha is selective conversion of sulfur compounds without saturation of olefinic compounds,which contribute to octane number enhancement.For straight-run kerosene that is used for making jet fuels,the sulfur removal by212 C.Song,X.Ma /Applied Catalysis B:Environmental 41(2003)207–238Fig.2.HDS Reactivities of various sulfur compounds in gas oil,GC–FPD chromatograms.HDS is more difficult than that from naphtha but less difficult compared to that from gas oil.Recently,investigations have demonstrated that sul-fur compounds remaining in diesel fuels at sulfur level lower than 500ppm are the dibenzothiophenes with alkyl substituents at the 4-and/or 6-position,and are lower in HDS reactivity [24,27,30,44,48,52].These species are termed refractory sulfur compounds.Both steric hindrance and electronic factor are responsible for the observed low reactivity of 4-and 6-substituted DBTs [53,54].Based on recent studies on gas oil HDS [27,45],the sulfur compounds can be classified into four groups according to their HDS reactivities that were described by the pseudo-first-order rate constants.The first group is dominantly alkyl BTs;the second,DBT and alkyl DBTs without alkyl substituents at the 4-and 6-positions;the third,alkyl DBTs with only one alkyl substituent at either the 4-or 6-position;the fourth,alkyl substituents at the 4-and 6-positions (as shown in Scheme 1).The sulfur distribution in the four groups in the gas oil is 39,20,26and 15wt.%,respectively,and the relative rate constant of HDS for each of the four groups is 36,8,3,and 1,respectively [27,45].Fig.3shows the relative reactor volume re-quirements for various degrees of sulfur removal byC.Song,X.Ma /Applied Catalysis B:Environmental 41(2003)207–238213Scheme 1.Structures of related polycyclic sulfur compounds found in diesel fuels.conventional single-stage HDS of diesel fuels.The estimation of volume requirements is based on the results from HDS kinetics studies using a commercial CoMo/Al 2O 3catalyst [27–29],assuming 1.0wt.%S in feed.When the total sulfur content is reduced to 500ppmw,the sulfur compounds remaining in the hydrotreated oil are the third and fourth group sulfur compounds.When the total sulfur content is reduced to 30ppmw,the sulfur compounds remaining in the hydrotreated oil are only the fourth group sulfur com-pounds,indicating that the less the sulfur content,the lower the HDS reactivity is,which has been discussed by Whitehurst et al.in their review paper [55].More recent studies using various straight-run gas oils from different crude oils confirmed the differences in reac-tivity between different sulfur compounds [56,57].Fig.3.Simulated HDS of diesel to meet 15and 0.1ppm level on the basis of a conventional single-stage reactor,assuming 1.0wt.%S in feed;HDS kinetic model:C S ,total =C S1o e −k 1t +C S2o e −k 2t +C S3o e −k 3t +C S4o e −k 4t .To put these problems into perspective based on conventional approaches for HDS of diesel fuels if reducing the sulfur level from current 500to 15ppmw (the regulation in 2006)by conventional HDS pro-cessing,the volume of catalyst bed will have to be increased 3.2times as that of the current HDS catalyst bed.If reducing the sulfur level to 0.1ppm by con-ventional HDS processing for fuel cell application,the volume of catalyst bed will have to be increased by about seven times.As it is well known,increasing high temperature and high-pressure reactor volume is very expensive.In another scenario,with current commercial HDS processes without changing the reactor volume the catalyst activity will have to be increased by a factor of 3.2and 7to meet the new regulation and fuel cell applications,respectively.It might be hard to meet such a demand by making small incremental improvements in the existing hydrotreat-ing catalysts that have been developed during the last 50years.Therefore,the petroleum refining industry is facing a major challenge to meet the new stricter sulfur spec-ifications in the early 21st century when the quality of the crude oils continue to decline in terms of increased sulfur content and decreased API gravity.214 C.Song,X.Ma /Applied Catalysis B:Environmental 41(2003)207–2383.2.Mechanistic pathwaysSubstantial progress has been made in fundamen-tal understanding and practical applications of hy-drotreating catalysis and metal sulfide-based catalysts for HDS,as discussed in several excellent reviews [26,49,51,54,58,59].The following discussion fo-cuses on deep desulfurization of polycyclic sulfur compounds shown in Scheme 1.HDS of thiophenic compounds proceeds through two pathways:hydrogenation pathway (hydrogena-tion followed by hydrogenolysis)and the direct hy-drogenolysis pathway (direct elimination of S atom via C–S bond cleavage)[21,22,52,60–64,144].Hy-drogenation and hydrogenolysis occur at different ac-tive sites.Polyaromatic compounds have been found to be the main inhibitors towards the hydrogenation pathway [65–68].Girgis and Gates published an ex-cellent review on reactivities of various compounds and their reaction networks as well as kinetics of high-pressure catalytic hydroprocessing [41].Kabe et al.[69]compared the reactivities of DBT,4-MDBT and 4,6-DMDBT under deep hydrodesulfurization conditions (sulfur concentration <0.05wt.%)using CoMo/Al 2O 3.The conversion of DBTs into cyclo-hexylbenzenes (CHBs)was nearly the same while that of DBTs into biphenyls (BPs)decreased inorder Fig.4.Adsorption conformations of 4,6-DMDBT at the hydrogenation active site and the hydrogenolysis active site.There is a strong steric hindrance in the plug-in adsorption.DBT >4MDBT >4,6-DMDBT.Data for DBTs could be arranged by the Langmuir–Hinshelwood rate equation.Activation energies of DBT,4-MDBT and 4,6-DMDBT were 24,31and 40kcal/mol,respec-tively [69].Heats of adsorption for DBT,4-MDBT and 4,6-DMDBT were 12,20and 21kcal/mol,re-spectively [69].Kabe et al.proposed that 4-MDBT or 4,6-DMDBT can be adsorbed on the catalyst through a -electron in the aromatic rings more strongly than that of DBT and that the C–S bond cleavage of adsorbed DBTs is disturbed by steric hindrance of the methyl group [69].Previous studies by the Mochida’s group [29,52,70,71]have demonstrated that over the industrial HDS catalysts,the refrac-tory sulfur compounds,particularly 4,6-DMDBT are desulfurized dominantly by the hydrogenation path-way as the alkyls at the 4-and/or 6-position of DBT strongly block the hydrogenolysis pathway.The rate constant of DBT and 4,6-DMDBT for hydrogena-tion pathway is similar,being 0.015and 0.010min −1over a commercial CoMo catalyst,while the rate constant of 4,6-DMDBT for hydrogenolysis pathway is 0.004min −1,less than that of DBT (0.048)by 12times.Quantum chemical calculation on the confor-mation and electron property of the various sulfur compounds and their HDS intermediates by Ma et al.[45,48,53]shows that the hydrogenation pathwayC.Song,X.Ma/Applied Catalysis B:Environmental41(2003)207–238215favors desulfurization of the refractory sulfur com-pounds by both decreasing the steric hindrance of the methyl groups and increasing the electron density on the sulfur atom in the sulfur compounds.As desul-furization of the refractory sulfur compounds occurs dominantly through the hydrogenation pathway,the inhibition of the coexistent aromatics towards HDS of the refractory sulfur compounds by competitive ad-sorption on the hydrogenation active sites becomes stronger in deep HDS[68].H2S produced from reac-tive sulfur compounds in the early stage of the reaction is one of the main inhibitors for HDS of the unreactive species[27,72].Computer modeling and simulation in the active sites on the catalyst surface and their interaction with sulfur compounds have also been applied to understand the reaction pathways and mechanism [73–76].Fig.4shows two types of chemisorption patterns of4,6-DMDBT on MoS2,theflat adsorp-tion and S-3type adsorption.Semi-empirical cal-culations have been carried out to illustrate the difference in chemisorption patterns between DBT and4,6-DMDBT.Both DBT and4,6-DMDBT can interact well with the30¯30edge of MoS2cata-lyst byflat chemisorption.The chemisorption of 4,6-dialkyldibenothiophenes,different from that of the DBTs without any alkyl group at both4-and 6-positions,is difficult by the S-3type coordination due to the steric hindrance of the alkyl groups.This steric hindrance is expected to increase with increas-ing size of the alkyl groups(from methyl to ethyl to propyl).Milenkovic et al.[77]synthesized various alkyldibenzothiophenes bearing bulky groups in posi-tions4and6and compared their sensitivity to HDS over a NiMo/Al2O3industrial catalyst in a batch re-actor at573K,and under5MPa H2pressure.It was further demonstrated that their reactivity is correlated to the steric hindrance near the sulfur atom.4.Design approaches to ultra-deep desulfurizationApproaches to ultra-deep desulfurization include: (1)improving catalytic activity by new catalyst for-mulation for HDS of4,6-DMDBT;(2)tailoring reac-tion and process conditions;(3)designing new reactor configurations;(4)developing new processes.One or more approaches may be employed by a refinery to meet the challenges of producing ultra-clean fuels at affordable cost.4.1.Improving catalytic activity by new catalyst formulationDesign approaches for improving catalytic activ-ity for ultra-deep hydrodesulfurization focus on how to remove4,6-DMDBT more effectively,by modify-ing catalyst formulations to:(1)enhance hydrogena-tion of aromatic ring in4,6-DMDBT by increasing hydrogenating ability of the catalyst;(2)incorporate acidic feature in catalyst to induce isomerization of methyl groups away from the4-and6-positions;(3) remove inhibiting substances(such as H2S)and tai-loring the reaction conditions for specific catalytic functions.The catalytic materials formulations may be improved for better activity by using different sup-ports(carbon,TiO2,TiO2-Al2O3,HY,MCM-41,etc.) for conventional alumina-supported CoMo,NiMo and NiW catalysts;by increasing loading level of active metal(Mo,W,etc.);by adding one more base metal (e.g.Ni to CoMo or Co to NiMo);and by incorporat-ing a noble metal(Pt,Pd,Ru,etc.).New and improved catalysts and different process-ing schemes are among the subjects of active research on deep HDS[49,59,51].For example,some recent studies examined carbon-supported CoMo catalysts for deep HDS[78,79,145,146].Binary oxide sup-ports such as TiO2-Al2O3have been examined for making improved HDS catalysts[80–82].In1992, novel mesoporous molecular sieve MCM-41was in-vented by Mobil researchers[83,84].Al-MCM-41 has been synthesized with improved aluminum in-corporation into framework[85–87]and applied to prepare CoMo/MCM-41for deep HDS of diesel fuels [8,9,21,88–90]and for HDS of petroleum resid[91]. Compared to CoMo/Al2O3,higher activity for HDS has been observed for CoMo/MCM-41with a higher metal loading.4.1.1.Mesoporous CoMo/MCM-41for HDSFor existing HDS process,we are exploring the design of new catalysts based on synthesis and appli-cation of novel mesoporous aluminosilicate molecular sieves of MCM-41type[21,22,147].The design ap-proach makes use of high surface area of MCM-41。
海员听力会话 口述题 问答题-new 评估

轮机英语听力与会话第1至7章第一章公共用语一、口述1. How to express apology.We can certainly say that nobody can make no mistakes throughout his life. Doing something wrong is not so terrible, what important is we should confess that we are wrong and learn a lesson from the mistake, this is apology. One should apologize for being late for an appointment, for being late means you have wasted other people’s time and maybe cause a serious result. Once a friend from Shanghai came to Wuhan to visit me, we said I would come to the railway station to receive him because that’s the first time he came to Wuhan, but I remembered a wrong time and I was half a hour’ late, he was a little angry, I apologized to him scenically, he forgave me finally for we have been good friends for many years.Thank you very much for inviting me to the party. Unfortunately I have to attend a lecture at 9 pm. I am looking for the next chance to be with you. I am really sorry for this.2. Self-introductionI come from -------province, my name is-----, now I study in the Wuhan university of technology .my score is good, I’m good at the marine engineering, so I decide devote myself to the marine affairs.3. Your life on boardRelatively, seaman’s life is dull, because the working and living conditions are li mited to such a small space that the work has almost no change and seamen communicate much less with other people. But this is not absolute; a man’s life depends on himself. I, for example, like to read English stories and listen to music during my spare time when at sea, and like to make friends with all kinds of people when ship is in port, this makes my live quite interesting.I have been to several ports of the world. I’ve been on board for six years. so I’ve accumulated so much experience about sea life.4. Say something about your familyThere are 3 persons in my family, my father, my mother and me. They are working so hard to earn some money to support the whole family, especially for my studying in the university.5. How to welcome port state control officer?Welcome the port state control officer to our shipIntroduce myself;Introduce my captain and chief engineer to the port state control officer;Ask the officers what items they want to inspect;Arrange someone operate the items for the officers and politely answer the questions from the officer;Welcome, Mr. Smith. I’m -----, the chief engineer. Well, the master is coming, this is our master, Mr. -----, this is Mr. Smith, PSCO. What items will you inspect on board our ship, Mr. Smith? Ok, now the 3rd engineer will operate the lifeboat, this way please, Mr. Smith.6. How to receive ship chandler?Welcome the ship chandler to our ship,Introduce myself;Introduce my captain and chief engineer to the ship chandler;Give the ship chandler a store order which includes item numbers, descriptions, units, required and remarks of the stores we need;Especially mention the time limitWelcome, Mr. Smith. I’m -----, the 4th engineer. Well, our master and chief engineer are coming, this is our master, Mr.-----, this is our chief engineer, Mr. --------, this is Mr. Smith, chandler. Here is our store order list, you can have a look. How about the price? A little bit too high, you will give us a discount, will not you? That’s ok. Please supply our vessel with the stores before our departure on 10th, Oct.7. Talk about your education background.I am studying in Wuhan University of Technology. After four years’studying, I learn much about marine engineering, including the procedure of operating the marine diesel engine and the generator. also I get some experience about how to deal with some simple troubles about operation of the engine. In addition, our teachers have taught us many international legislations and codes, which are very important to our sea life.8. Your responsibilities on board ship.As a chief engineer, my responsibilities on board ship are (1) to keep all machines both in engine room and on deck in good order, so I must organize the watch-keeping in the engine room, and the maintaince work, therefore ensure the safety of the ship and the seamen. (2) to protect marine pollution from the ship.As an engineer, when on duty I work for 4 hours each watch. During the watch time, I should keep everything in good order, the parameters, such as temperatures, pressures of all machines, and the liquid levels of fuel oil tanks, lub. oil tanks and water tanks, etc. should be kept in normal range. Bridge orders must be promptly carried out. I also should determine the possible hazards in the engine room and try to diminish them. The parameters should logged periodically to provide a maintenance base for the machines. At the completion of the watch, I will hand over to my relief, while I must ensure that the relief is competent to take over and carry out his duties effectively.二、问答1. How long have you been a seaman?2years2. Which company do you serve?In COSCO company3. When did you begin to work on board?In 20024. What do you say when someone has helped you?I would say “THANK YOU”.5. What types of main engine have you ever experienced!Sulzer and B&W.6. How long have you ever worked on board?2 months.7. Have you ever studied SMS? What is SMS?I have studied SMS, SMS is safety management system.8. What is NCR in ISM code?Non-conformity report.9. Which certificate do you have now?I have the CERTIFICAITE OF 4/E.10. Which company are you working?I’m working in COSCO.11. Can you name some foreign ports you have been to?I have been to Sydney, Singapore and Portland.12. How many sailors are there on your ship?24.第二章机舱日常业务(主机系统)一、口述1. Look at the illustration and say something about the removing of a piston.The preparing for lifting out a piston.The procedure of lifting out a piston.The items to be inspected when lifting out a piston.The procedure of removing a piston:1) Stop engine and close all inlet and outlet valves;2) Prepared all tools for overhaul;3) Engaged engine to up dead center;4) Unscrew bolts by means of hydraulic tools;5) Lift out cylinder head by means of engine room crane and put on the wooden mat;6) Lift out piston by means of engine room crane and put on the wooden mat;7) Clean cylinder liner, piston and rod. Check worn-out of cylinder and liner. Check butt clearances and gaps. Renew all gaskets and packing;8) Piston and the rod, cylinder cover and components have been reassembled; the surrounding has been cleaned out by fitters. All tools have been put in place.2. Look at the illustration and say something about the marine diesel engine.This marine diesel engine is a two-stroke type of engine .It height is more than that of a four-stroke type; It’s power can be improved by 60-70% according to the same conditions of the four-stroke type.It’s main moving parts are piston, cross-head, piston rod and crankshaft. The fired parts of the marine engine are cylinder cover by the tie bolts.The necessary systems are lubricating system cooling systems and turbocharger systems and so on.3. Look at the illustration and say something about the exhaust gas turbocharger and supercharging.The main parts are exhaust manifold, turbine, compressor, charge air cooler and manifold.The turbine itself is driven by exhaust and then moves the compressor; air after pass compressor will increase its pressure and then flow to cooler, air receiver.The purpose is to the recover the waste heat and increase the fresh air’s amount and density, so as to develop more power.4.Look at the illustration and say something about the control room.The control room has a lot of buttons, computers, some generator s’ controller.Boxes, telegraph and soon to make sure enough power main.Watch-keeping rules in UMS.Start emergency pump and run generator in parallel, to make sure enough power.5. Look at the illustration and say something about the maneuvering of the main engine.Operation when charging from diesel oil to fuel oil, turn on the heater in the tank, and warm up the fuel the speed also regulate by the governor. Oil regulates the viscosity of the fuel oil, and then shut down the diesel oil valve, turn on the fuel oil valve.6. Look at the illustration and say something about the modern UMS.There are several plates in the UMS room, for example the bus. Some electrical control plates, on the computer, the watching keeper can check the operation situation of all systems, and find them direct from the computer and deal with these troubles.7. Look at the illustration and say something about the oil mist detector and the fan unit.(1) The function of the crankcase oil mist detector is checking for the concentration of oil mist in the crankcase.(2) The function of the fan unit is removing the flammable air in the crankcase(3) Inspect the sensitivity of the detector ad the work condition of the fan frequently.8. Talk something about fuel oil bunking procedure.First selecting a kind of oil, we should take into account the following characteristics: viscosity, setting point, flashing point cetane number, calorific value, sculpture and carbon residues, specific gravity, water content and mechanical impurities. Before bunkering, the E/3 will go down to the oil lighter, where he will sound the oil tanks, logging the tanks’ oil type, sounding number, trim, etc. Bunkering can be started only after all prepare work is finished. After bunkering but before dismantling the pipe, the retained oil in the hose should be blown into oil tank with compressed air, to prevent oil pollution.9. Preparation for the engine department before entering harbor.Change the control handle to maneuveringSupply the engine with diesel oil instead of fuel oilKeep good lubricating and cooling condition of the engineUse the high sea valves instead of the low sea valves.10. Talk about the marine diesel engine shown in the illustration.Cylinder, fuel injector, turbocharger, stuffing box, bedplate, tie bolts, cylinder head, are the main fixed.Exhaust valve, camshaft, crosshead, connecting rod, crankshaft, piston are the moving part.The large two-stroke/cycle low-speed turbocharger main propulsion diesel engines.For the ship provide power, make the ship operate on the sea二、问答1. What’s the function of the purifier used in the fuel oil system?Separate water from oil.2. What’s the function of the clarifier used in the fuel oil system?Separate impurities from oil3. The fuel oil system can be divided into two sub-systems. What are they?The fuel supply and the fuel injection systems.4. How does the fuel oil viscosity regulator control the fuel oil’s viscosity?Control the fuel oil’s temperature.5. When selecting a fuel oil, there are more than ten factors to be considered. Please name at least three of the main factors.Viscosity, ash, residues.6. What’s the advantage of central cooling water system?The corrosion problems are much reduced in this system for less equipment in contact with seawater.7. What’s the function of the head tank used in the cooling water system?Removing the air of the cooling system, making up water, adding additives.8. What’s the usual coolant used in the marine diesel engine?fresh water。
Platinum Doped Hydrotreating Catalysts for Deep Hydrodesulfurization of Diesel

Platinum Doped Hydrotreating Catalysts for Deep Hydrodesulfurization of Diesel FuelsSte´phanie Pessayre,†Christophe Geantet,*,†Robert Bacaud,†Michel Vrinat,†Thanh Son N’Guyen,†Yvonne Soldo,‡Jean Louis Hazemann,§and Miche`le Breysse#Institut de Recherches sur la Catalyse,UPR CNRS5401,2A V enue Albert Einstein,69626Villeurbanne Cedex,France,Laboratoire d’Electrochimie et Physico-chimie des Mate´riaux et des Interfaces,UMR CNRS,INPG-Uni V ersite´Joseph Fourier,38402St Martin d’He`res,France,Laboratoire de Cristallographie,UPRCNRS,BP166,38043Grenoble,France,and Laboratoire de Re´acti V ite´de Surfaces Paris,UMR CNRS,Uni V ersite´Pierre et Marie Curie-Paris6,75252Paris Cedex,FranceTwo-stage processes are possible solutions for reaching10ppm sulfur in gas oil without severe runningconditions.First,most of the sulfur is removed by using a CoMo conventional catalyst.Second,after H2Sremoval,the treated oil,with a remaining S content below500ppm,is again hydrotreated.In this latter case,the use of noble metal catalysts can be envisaged.In the present study dealing with this second stage reactor,we examined a catalytic system based on the addition of a low content of Pt to a commercial sulfide catalyst.An enhancement in catalytic activity can be obtained in the conversion of model molecules(tetralin anddibenzothiophene)as well as a hydrotreated straight run gas oil.The promotion effect strongly depends onthe preparation procedure which requires the impregnation of Pt on a presulfided commercial HDT catalyst.Advanced EXAFS and HRTEM characterizations were used to characterize the active phases.IntroductionThe primary goal of the recently proposed regulations by the European Community,as well as those which have appeared in United States or Japan,is to reduce the sulfur content in transportation fuels in order to minimize air pollution and prevent the poisoning of exhaust treatment catalysts.For instance,present EC or US regulation for the sulfur contents of diesel fuels is50ppm and is expected to be10ppm in2009.1 Thus,sulfur removal is still a major problem to be solved2and several approaches are proposed.3As a result of the tightening of these regulations,there has been a great interest in the research and development of refining processes and suitable catalysts.Even if the preparation of conventional hydrotreating catalysts has been improved and their reactivity enhanced by the use of P or organic additives,the severe operating conditions required to meet the objectives drastically reduces the catalyst life time.Thus,two-stage processes have been proposed and developed.4-6The objective of the first step is to reduce the sulfur content of the crude in order to decrease the H2S partial pressure in the second reactor.As a result,only organic compounds difficult to desulfurize(mostly substituted diben-zothiophenes)remain.The conversion of these sterically hindered molecules mainly proceeds via the hydrogenation route instead of the direct desulfurization route which is dominating for molecules like dibenzothiophene.2,7,8Therefore,a way to overcome the low reactivity of4,6-DMDBT would be to favor the hydrogenation pathway.Noble metal supported on silica-alumina or NiW sulfide supported on alumina catalysts were found to be promising systems for the desulfurization of a straight run gas oil containing760ppm of S.9,10Besides,by doping conventional systems with small amounts of Pt,a benefit in catalytic activity could be expected. This has been done for improving the catalytic activities of MoS2 with Pt either as a dopant11-14or as a catalyst mixture(MoS2/ Al2O3+Pt/Al2O3).15Some of these authors pointed out the importance of an impregnation of Pt on already sulfided Mo on alumina catalysts.13,14EXXON patented the preparation of a Pt doped NiMo supported on alumina catalysts,16the Pt being introduced with a S-containing precursor with ligands such as dithiocarbamates.More recently the use of mixed clusters such as[Pt(NH3)4](Mo6S8)S,x(H2O/MeOH)]was also proposed.17A favorable effect of the addition of Pt or Rh on CoMo catalysts was also reported by Vanhaeren.18The objective of the present study was to examine the effect of the addition of Pt on three industrial sulfide catalysts,i.e., CoMo,NiMo,and NiW supported on alumina,in the context of ultra-deep desulfurization,i.e.,in the presence of a low partial pressure of H2S.Hydrogenation properties and hydrodesulfur-ization properties were characterized by means of test reac-tions:tetralin hydrogenation and dibenzothiophene desulfur-ization.Moreover,the conversion of gas oils in a trickle bed reactor was also examined.The catalysts were characterized mainly by X-ray absorption spectroscopy.Experimental Sectionmercial NiMo,CoMo(14wt%MoO3,3wt %NiO or CoO),or NiW(25.7wt%WO3,3.82wt%NiO)on alumina catalysts were used.The Pt catalyst was prepared by impregnation of a250m2/g alumina with H2PtCl6(0.3wt%), then calcined for1h at773K,and reduced under pure H2during 6h at573K.Mixed PtNiW/Al2O3or PtCo(Ni)Mo/Al2O3 catalysts(0.15<Pt wt%<0.7)were obtained by deposition of H2PtCl6precursor either on the oxidic form of the commercial catalyst(so-called Pt/NiW ox,Pt/NiMo ox,or Pt/CoMo ox)or on the sulfided one(so-called Pt/NiW sulf,Pt/NiMo sulf,Pt/ CoMo sulf).In both cases,the impregnated catalysts were dried at393K.Then,the commercial samples and mixed catalysts*To whom correspondence should be addressed.Tel.:(0)47244 5336.Fax:(0)472445390.E-mail:geantet@rs.fr.†Institut de Recherches sur la Catal.‡Laboratoire d’Electrochimie et Physico-chimie des Mate´riaux et des Interfaces.§Laboratoire de Cristallographie.#Laboratoire de Re´activite´de Surfaces Paris.3877Ind.Eng.Chem.Res.2007,46,3877-388310.1021/ie060932x CCC:$37.00©2007American Chemical SocietyPublished on Web12/16/2006were sulfided using gas flows of 5vol %H 2S in H 2at 673K for 4h (heating rate 10K/min).After cooling down to room temperature under the same sulfiding mixture and flushing with nitrogen for 30min,the catalysts were transferred under argon and kept in sealed vessels.Catalytic Activity.The catalysts were tested by means of three reactions:the hydrogenation of tetralin,the hydrode-sulfurization of dibenzothiophene (DBT),and the straight run (SR)gas oil conversion.Experiments on model molecules were carried out in a microreactor running in the dynamic mode,in the vapor phase.The operating conditions were the following for tetralin hydrogenation:reaction temperature,573K;total pressure,43×105Pa;tetralin partial pressure,8886Pa;H 2S partial pressure,550ppm or 0(to check the stability of the catalysts).For DBT conversion,the reaction temperature was kept at 523K with a total pressure of 34×105Pa,a DBT partial pressure of 480Pa,and no H 2S addition.According to the model of the integral reactor,the rate constant k of a reaction can be expressed as follows:x )conversion,m )mass of catalyst (g),F 0)molar flow of reactant (mol/s),C 0)concentration of reactant (mol/L).When the conversion is less than 15%,the above formula can be simplified,giving the following reaction rate:The rates were measured when the steady state of the catalyst was reached after 15h on-stream.The accuracy is within (5%.Catalytic rates were also measured in a trickle bed reactor described in references 19and 20using hydrotreated gas oils as feeds.The reactions were performed at 613K,with a 2<LHSV <10h -1(LHSV:liquid hourly space velocity),and a total pressure of 3Mpa (catalyst weight 0.5<m <1g).The ground catalysts were placed between two layers of alumina in an up-flow tubular reactor (2cm 3).The composition of the starting gas oil feeds is given in Table 1.A periodic sampling of the liquid effluent was performed,and the total sulfur content was determined by X-ray fluores-cence (HORIBA SLFA-1800H analyzer),careful attention being paid on matrix effects.21Kinetic orders n were obtained from the fitting of f (n ))1/LHSV according to the following expression (for n *1):with S i and S o corresponding to S concentration at the entrance and at the exit of the reactor,respectively.Then,rate constants k app were calculated according to the expression above.Catalyst Characterization.Chemical analysis was used to control the metal contents of the catalysts.The dispersion of the catalysts was determined by TEM performed on a JEOLTable position and Physical Properties of Straight Run Hydrotreated Gas Oil Feeds (A and B)gas oil Agas oil B density (288K)g/L 846852sulfur content (ppm)515142aromatics (wt %)3630Table 2.Catalytic Activities in Gas Oil Conversion of Conventional Alumina Supported Sulfides acatalystCoMo NiMo NiW gas oil 515ppm Sk app (103g 1,9mmol -1,9h -1)13.214.614.2gas oil 142ppm Sk app (106g 2,8mmol -2,8h -1)1616.315.4aInitial wt %S content:(a)515ppm S and (b)142ppmS.Figure 1.Stability in the conversion of tetralin of NiMo and NiW sulfide catalysts under reducing conditions.Figure 2.Catalytic activities in tetralin hydrogenation at 45KPa (500ppm H 2S)of (a)NiW,(b)CoMo,and (c)NiMo on alumina,Pt on alumina,and mixed catalysts prepared by impregnation of Pt on the sulfided form (sulf)or oxidic form (ox).1n -1((1S o)(n -1)-(1S i)(n -1)))k app LHSVk )F 0mC 0ln(1-x )(L s -1g -1)r )F 0mx (mol s -1g -1)3878Ind.Eng.Chem.Res.,Vol.46,No.12,20072010-FEG instrument equipped with a Link-Isis EDS detector.Catalyst grains were dispersed in pure ethanol,the suspension stirred in an ultrasonic bath,and one drop deposited on a carbon coated copper grid.X-ray absorption spectroscopy (XAS)measurements were performed using BM32beam line at the ESRF (French Collaborative Research Group).The storage ring operated at 6GeV in the multi-bunch mode (2/3filling)with a 200mA current.Experiments were performed at Pt L III edge in the fluorescence detection mode performed with a 30-element solid-state detector (Canberra).The sulfidation procedure was carried out in a dedicated in situ furnace adapted for fluorescence detection from the cell described in reference 22.This activation process was carried out in a way similar to the laboratory procedure under an H 2/H 2S (5%)flow from room temperature up to 673K (rising temperature 4K/min,gas flow 50mL/min).Standard analysis of the EXAFS spectra (normalization,background removal,Fourier transformation,and curve fitting)were carried out usingTable 3.Catalytic Activities in DBT Conversion and Gas Oil Conversion a of NiW on Alumina,Pt on Alumina,and Mixed PtNiW on Alumina CatalystscatalystPt(0.3)/Al 2O 3NiW/Al 2O 3Pt(0.3)NiW sulfPt(0.3)NiW oxDBTk (10-3L g -1s -1)0.8 2.5 3.50.7gas oilk app (106g 2,8mmol -2,8h -1)1310199aInitial wt %S content:142ppm.Figure 3.Effect of Pt loading on the catalytic activities (or conversion)of PtNiW on alumina catalysts in tetralin conversion (HYD)and gas oil conversion.Figure 4.HRTEM image of a Pt(0.3)NiW on alumina catalysts prepared from impregnation of Pt on the sulfided catalyst.Ind.Eng.Chem.Res.,Vol.46,No.12,20073879the SEDEM software 23with FEFF624theoretical phase and amplitude functions.The curve fitting procedure was performed in R -space.Fourier transformation of the normalized k 3-weighted EXAFS signal was performed over the 2.5-15Å-1k -range with Kaiser window functions.Coordination numbers (N ),interatomic distances (R ),Debye -Waller parameters (σ2),and energy shifts(∆E 0)were used as variables in the fitting procedure.Scale factors S 02were fixed at 0.8.ResultsCatalytic Properties of Conventional Catalysts.Conven-tional industrial sulfide catalysts were investigated in the conversion of the two SR gas oil hydrotreated feeds containing,respectively,515and 142ppm of S.By varying the LHSV,we determined for each reacting oil the kinetic order with respect to S and found it respectively equal to 2.9and 3.8.These kinetic orders express the wide reactivity scale of the various refractory S compounds remaining in the desulfurized oil.25It can be seen in Table 2that the three catalysts present almost the same activity.However,the stability of the sulfided catalyst is also an important factor and depends on the partial pressure of H 2S.It is known that CoMo catalysts segregate under reducing condi-tions (pure H 2)26and therefore are less stable than in the presence of H 2S.The stability of the other industrial catalysts,i.e.,NiW and NiMo,was checked in the conversion of tetralin.After stabilization of the activity under 500ppm of H 2S,the addition of this gas was suppressed and the evolution of the conversion was measured as illustrated in Figure 1.It can be seen that the NiW system is the most stable catalyst in the absence or with low partial pressure of H 2S in agreement with previous reported in the literature.27Catalytic Properties of Pt Based Systems.In order to improve the catalytic performance of conventional industrial catalytic systems and favor the hydrogenation pathway of the desulfurization scheme,these catalysts were doped with a small amount of Pt.The activity of Pt on alumina,NiW,NiMo,and CoMo on alumina catalysts alone or doped with 0.3wt %of Pt were measured in tetralin conversion (Figure 2).Among commercial catalysts,NiW is the most active one.In all cases,an improvement in the catalytic hydrogenation activity is observed when Pt is added after the sulfidation of the com-mercial catalyst.In that case,the catalytic properties seem to correspond to the addition of the properties of each component.On the contrary,when Pt is impregnated on the oxidic form of the catalyst a sharp decrease in the activity is observed.The NiW system was then studied in the conversion of DBT (see Table 3).Figure 5.Normalized absorption spectra at Pt L III edge of the catalysts after impregnation of H 2PtCl 6and drying on (a)oxidic CoMo and (b)sulfided CoMo catalysts.Figure 6.Magnitude of the Fourier transformed k 3-weighted data on (a)oxidic CoMo and (b)sulfided CoMo catalysts (top)and after sulfidation with a 5vol %H 2S in H 2gas mixture.3880Ind.Eng.Chem.Res.,Vol.46,No.12,2007A similar trend,i.e.,addition of the properties of each component,is observed when Pt is added on a presulfided NiW on alumina catalysts.Thus,we can expect that the conversion of a real feed can be increased by the use of such a mixed system.Table3gives the rate constants in the conversion of gas oil B.Again,we notice an enhancement of the rate for the mixed catalysts as compared to the unpromoted one.As compared to tetralin hydrogenation,Pt on alumina catalyst exhibits a much higher activity with respect to NiW catalyst. This effect can be ascribed to a weaker inhibiting effect of H2S due to the lower sulfur content of the feed.Under these specific conditions,Pt is less inhibited by H2S and the feed is composed of refractory alkyl DBT which are mainly converted by the hydrogenation route.2The variations of the catalytic properties with the amount of Pt added to the NiW catalyst were studied in both tetralin and gas oil conversion reactions(see Figure3).Although these variations are not exactly similar,it appears that a loading of 0.25-0.3wt%of Pt gives the best improvement in the catalytic activity.Nanoscale Characterization of the Catalysts.Character-ization by HRTEM.Both types of catalysts were characterized after sulfidation by HRTEM.For sulfided Pt(0.3)/NiW sulf, HRTEM pictures show NiW sulfide slabs and small particles with an average size of0.8nm(see Figure4)composed of Pt as revealed by1nm probe analysis with EDS.Due to the background emission of neighboring(Ni)WS2particles and the radiolytic effect of the small electron probe,the presence of S on these particles(and the stoichiometry)cannot be determined. Nevertheless,it can be concluded from these examinations that sulfide NiW slabs and Pt containing particles are separated systems.The sizes of the WS2slabs,i.e.,average length3.1 nm,and average number of layers,i.e.,2,are not very different from those reported previously for NiW catalysts,28,29but a slight decrease in the length can be noticed.The dispersion of the reference catalyst composed by0.3wt%of Pt on alumina was also determined by HRTEM,the average size of the particles being close to1.5nm by comparison to0.8nm for the mixed catalyst.This means that both phases“NiWS”and Pt are highly dispersed.By contrast,Pt cannot be observed by HRTEM in sulfided Pt(0.3)/NiW ox catalyst,which can be due either to the small size of the Pt containing particles(less than the resolution limit of the TEM,i.e.,0.8nm)or to their close vicinity to dense WS2particles.The morphology of this last phase (length and stacking)is similar to that of sulfided Pt(0.3)/ NiW sulf.XAS Characterization of the Precursor and Sulfided States of the Catalysts.Further information on the chemical nature of the noble metal nanoparticles as well as on the role of the preparation procedure was obtained by means of XAS performed before and after sulfidation under in situ conditions (5vol%H2S in H2at673K,for30min,heating rate5K/min). In order to avoid the overlap of adsorption edges(Pt L III:11564 eV and W L II:11544eV),the CoMo sulfide system was chosen instead of the NiW one.The XANES spectra of the Pt(0.3)/ CoMo ox catalyst and Pt(0.3)/CoMo sulf after impregnation by hexachloroplatinic acid and drying at393K are presented in Figure5.For Pt(0.3)/CoMo ox,some Pt-O bonds are formed as already reported for Pt/Al2O3catalysts.30,31The presence of these Pt-O bonds gives rise to a strong white line.By contrast, the Pt(0.3)/CoMo sulf sample presents a different electronic configuration indicating another nature of the Pt-neighboring atoms bonds as compared to the previous sample.The XANES spectra is similar to the one obtained on the sulfided catalyst (either Pt(0.3)/CoMo ox or sulf)suggesting that the electronic configuration of Pt is close the one obtained after in-situ sulfidation.The Fourier transforms at Pt L III edge are presented in Figure 6(top)and the results deduced from the EXAFS fitting summarized in Table4.After impregnation and drying,the Pt neighborhood for Pt(0.3)/CoMo ox sample consists of O and Cl atoms.For the Pt(0.3)/CoMo sulf sample,there is no O shell contribution but XAS is not able to distinguish between Cl or S neighboring atoms.Thus,either the platinum chloride precursor remains unmodified at the surface of alumina or,more probably,interacts with S surface atoms(SH entities)and a partial substitution of Cl by S atoms occurs in the neighboring shell of Pt atoms(both cases are presented in Table4).These Pt-S bonds are rather stable,and they are not expected to be strongly oxidized by the drying procedure.32After sulfidation, the Pt local structure is schematized in Figure6(bottom)by the magnitude of the Fourier transform,as a function of real space separation R.For both samples,only one main contribu-tion is visible,and data fitting indicates that Pt is surrounded by four sulfur atoms like in the PtS structure.However,we were not able to introduce a second Pt-M shell.This is indicative of the high dispersion of PtS particles as observed in the case of sulfided Pt(0.3)/CoMo sulf sample by HRTEM.Due to the high disorder of the Pt phase,it has not been possible either to characterize any interaction with WS2for sulfided Pt-(0.3)CoMo ox as proposed above for explaining the HRTEM data.DiscussionThe calcined state of CoMo,NiMo,and NiW supported on alumina catalysts has been studied by many techniques.33It was proposed by several authors that at this precursor stage an interaction between the promoter,Co or Ni,and the polymo-lybdate or polytungstate phase already exists.This interaction would prevent the formation of MoO3or WO3at high Mo or W loading and would lead to a high dispersion of the promoter.Table4.Structural Parameters Obtained from EXAFS Fitting for Impregnated and in Situ Sulfided PtCoMo Catalysts Prepared from the Oxidic or Sulfidic Statesample M neighbor K min(Å-1)K max(Å-1)R Pt-M N Pt-M E0(eV)σ2(Å2)Impregnated StatePtCoMo ox O313.7 2.064120.008 PtCoMo sulf Cl a313.7 2.33 1.5160.002 PtCoMo sulf Cl313.7 2.31 3.69.20.005 PtCoMo sulf S a 2.3348.30.0049Sulfided StatePtCoMo ox S313.5 2.3448.20.005 PtComo sulf S313.5 2.3347.80.005a S or Cl cannot be distinguished by XAS.Ind.Eng.Chem.Res.,Vol.46,No.12,20073881The interaction of Pt with molybdenum or a tungsten oxidic phase has also been addressed previously.In a comprehensive study of PtW catalysts,De Penguilly observed several kinds of interaction between both components depending on W concen-tration.34At high W loadings,Pt can be either grafted on the free alumina space left after polytungstates formation or linked to the tungstate phase by hydrogen bonding.Such a kind of interaction between Pt and W would explain HRTEM results since it has not been possible to detect distinct Pt particles in sulf Pt(0.3)NiW ox,probably because they are in close vicinity of the dense WS2sulfide phase either in a kind of decoration or between alumina and WS2slabs.In accordance with EXAFS data,the Pt phase is very well dispersed.However,whatever the nature of the mixed catalysts, CoMo or NiW,a large decrease in the catalytic properties was observed when Pt was added on the oxide form of the catalyst precursor.The close neighboring of Pt and WS2may prevent the formation of some highly active so-called“CoMoS”(or “NiWS”)entities.In the case of sulfided Pt(0.3)/NiW sulf catalyst,the isolated PtS particles independently contribute to the catalytic activity providing an additive effect.The benefit of the sulfidation for the formation of“CoMoS”is kept even after impregnation of the Pt,indicating that the negative effect originates from oxidic interactions.However in order to keep the additive effect,only a small content of Pt(0.2<wt%Pt<0.4)must be added. We can suggest that a higher Pt content gives rise to larger and less active particles.ConclusionIn order to achieve ultra-deep desulfurization,improved catalysts are needed.In the framework of a two-stage process, a tentative solution is provided by the addition of a small amount of noble metal to a conventional catalyst.This allows a20%to 40%increase in the activity as compared to the unpromoted sulfide catalyst.The benefit originates from the addition of the catalytic properties of each individual system.However,such an effect requires the impregnation of Pt on a sulfided NiW on alumina catalyst otherwise,if Pt addition is performed on the oxidic catalyst,detrimental interactions between Pt and“NiWS”or“CoMos”occur.AcknowledgmentThis work received support from TotalFina,ELF,IFP, Procatalyse,and CNRS-Ecodev.We thank the French-CRG committee for providing machine-time.F.Bourgain and M. Cattenot are gratefully acknowledged for the realization of the in situ cell.We thank also mbert for fruitful discussion on the Pt-W system.Literature Cited(1)European Union,EU directive98/70/EC,1998.EPA,Control of air pollution from new motor vehicles amendment to the tier-2/gasoline sulfur regulations,U.S.Environmental Protection Agency,April13,2001.(2)Breysse,M.;Djega-Mariadassou,G.;Pessayre,S.;Geantet,C.; Vrinat,M.;Perot,G.;Lemaire,M.Deep desulfurization:reactions,catalysts and technological challenges,Catal.Today2003,84,129-138.(3)Song,C.An overview of new approaches to deep desulfurization for ultra-clean gasoline,diesel fuel and jet fuel.Catal.Today2003,86, 211-263.(4)Sie,S.T.Reaction order and role of hydrogen sulfide in deep hydrodesulfurization of gas oils:consequences for industrial reactor configuration.Fuel Process.Technol.1999,6,149-171.(5)Stork,W.H.J.Molecules,catalysts and reactors in hydroprocessing of oil fractions.Stud.Surf.Sci.Catal.1997,106,41-67.(6)Bej,S.K.Revamping of diesel hydrodesulfurizers:options available and future research needs.Fuel Process.Technol.2004,85,1503-1517.(7)Whitehurst,D.D.;Isoda,T.;Mochida,I.Present state of the art and future challenges in the hydrodesulfurization of polyaromatic sulfur compounds.Ad V.Catal.1998,42,345-471.(8)Bataille,F.;Lemberton,J.L.;Michaud,P.;Pe´rot,G.;Vrinat,M.; Lemaire,M.;Schulz,E.;Breysse,M.;Kasztelan,S.Alkyldibenzothiophenes hydrodesulfurization:promoter effect,reactivity and reaction mechanism. J.Catal.2000,191,409-422.(9)Reinhoudt,H.R.;Troost,R.;van Langeveld,A.D.;Sie,S.T.;van Veen,J.A.R.;Moulijn,J.A.Catalysts for second-stage deep hydrodes-ulfurisation of gas oils.Fuel Process.Technol.1999,61,133-147.(10)Reinhoudt,H.R.;Troost,R.;van Schalkwijk,S.;van Langeveld,A.D.;Sie,S.T.;Schulz,H.;Chadwick,D.;Cambra,J.;de Beer,V.H.J.; van Veen,J.A.R.;Fierro,J.L.G.;Moulijn,J.A.Application of ASA supported noble metal catalysts in the deep hydrodesulfurization of diesel fuels.Stud.Surf.Sci.Catal.1997,106,237-244.(11)Navarro,R.;Pawelec,B.;Fierro,J.L.G.;Vasudevan,P.T. Dibenzothiophene hydrodesulfurization on silica-alumina-supported transi-tion metal sulfide catalysts.Appl.Catal.A1996,148,23-40.(12)Merino,L.I.;Centeno,A.;Giraldo,S.A.Influence of the activation conditions of bimetallic catalysts NM-Mo/g-Al2O3(NM)Pt,Pd and Ru) on the activity in HDT reactions.Appl.Catal.A2000,197,61-68.(13)Vit,Z.;Cinibulk,J.;Gulkova,D.Promotion of Mo/Al2O3sulfide catalysts by noble metals in simultaneous hydrodesulfurization of thiophene and hydrodenitrogenation of pyridine:a comparative study.Appl.Catal.A.2004,272,99-107.(14)Vı´t,Z.;Gulkova´,D.;Kaluzˇa,L.;Zdrazˇil,M.Synergetic effects of Pt and Ru added to Mo/Al2O3sulfide catalyst in simultaneous hydrodes-ulfurization of thiophene and hydrogenation of cyclohexene.J.Catal.2005, 232,447-455.(15)Grange,P.;Vanhaeren,X.Hydrotreating catalysts,an old story with new challenges.Catal.Today1997,36,375-391.(16)U.S.Patent5152885,1992.(17)Paskach,T.J.;Hilsenbeck,S.J.;Thompson,R.K.;McCarley,R.E.;Schrader,G.L.Synthesis and characterization of a novel platinum molybdenum sulphide containing the Mo6S8cluster.J.Alloys Compd.2000, 311,169-180.(18)Vanhaeren,X.Ph.D.thesis,Universite´Catholique de Louvain,1997.(19)Letourneur,D.;Vrinat,M.;Bacaud,R.Hydrodesulfurization of dibenzothiophene in a micro trickle bed reactor.Stud.Surf.Sci.Catal.1997, 106,491-497.(20)Letourneur,D.;Bacaud,R.;Vrinat,M.;Schweich,D.;Pitault,I. Hydrodesulfurization catalyst evaluation in an upflow three-phase microre-actor Ind.Eng.Chem.Res.1998,37,2662.(21)Pessayre,S.;Bacaud,R.;Geantet,C.;Vrinat,M.Deep desulfur-ization of diesel oils.Matrix effect in the analysis of low sulphur diesel oils by energy dispersive X-ray fluorescence spectroscopy.Fuel1999,78, 857-860.(22)Geantet,C.;Soldo,Y.;Glasson,C.;Matsubayashi,N.;Lacroix, M.;Proux,O.;Ulrich,O.;and Hazemann,J.L.In-situ QEXAFS investiga-tion at Co K edge of the sulfidation of a CoMo/Al2O3hydrotreating catalyst. Catal.Lett.2001,73,95.(23)Aberdam, D.SEDEM,a software package for EXAFS data extraction and modeling.J.Synchrotron Radiat.1998,5,1287-1297.(24)Rehr,J.J.;Zabinsky,S.I.;Albers,R.C.High-order multiple-scattering calculations of X-ray-absorption fine structure.Phys.Re V.Lett. 1992,69,3397.(25)Macaud,M.;Milenkovic,A.;Schultz,E.;Lemaire,M.;Vrinat,M. Hydrodesulfurization of alkyldibenzothiophenes:Evidence of highly un-reactive aromatic sulfur compounds J.Catal.2000,193,255.(26)Breysse,M.;Frety,R.;Vrinat,M.;Grange,P.;Genet,M. unsupported CoMo sulfide catalysts part II:characterization and evolution of physico-chemical properties during catalytic reaction.Appl.Catal.1984, 12,165.(27)Yasuda,H.;Higo,M.;Yoshitomi,S.;Sato,T.;Imamura,H.; Matubayashi,H.;Shimada,H.;Nishijima,A.;Yoshimura,Y.Hydrogenation of tetralin over sulfided nickel-tungstate/alumina and nickel-molybdate/ alumina catalysts.Catal.Today1997,39,77-87.(28)Breysse,M.;Cattenot,M.;Decamp,T.et al.Influence of sulfidation conditions on the properties of NiW on alumina hydrotreating catalysts. Catal.Today1988,4,39-55.(29)Ouafi,D.;Mauge,F.;Lavalley,J.C.;Payen,E.;Kasztelan,S.; Houari,M.Grimblot,J.;Bonnelle,J.P.nature and structure of tungsten3882Ind.Eng.Chem.Res.,Vol.46,No.12,2007。
离子液体脱硫

离子液体在汽油柴油脱硫生产清洁燃料中的技术现状摘要:离子液体是一种具有优良特性的绿色材料,本文综述了离子液体的组成、分类和性质,综述了近几年来离子液体在萃取脱硫、萃取脱硫与氧化脱硫耦合、萃取脱硫与烷基化脱硫耦合等方面的研究。
认为离子液体萃取脱硫具有操作简便、可循环使用、环境友好、能深度脱硫等特点,是一项具有广阔发展前景的技术。
若要实现该技术的工业化应用,还需进一步加强离子液体在合成工艺、脱硫选择性及回收再生等方面的研究。
关键词:离子液体;汽油;柴油;脱硫;萃取Technology Status of ionic liquid in desulfurization of gasolineanddiesel oil for producting clean fuelsAbstract: Ionic liquids as a environmental protected material has the characteristic performance.The composition, classification and property of them were reviewed in this paper.Researches for extractive desulfurization, coupling of extractive and oxidative desulfurizations, and coupling of extractive and alkylation desulfurizations at room temperature with ionic liquids as extractants were reviewed. Trend for extractive desulfurization of fuel oil with ionic liquids was forecasted. Technology of using ionic liquids in extractive desulfurization of fuel oil possesses advantages of mild operation conditions, recycling of ionic liquid, environmental friendly and deep desulfurization capacity. For the sake of commercialization of the desulfurization technology, synthesis of appropriate ionic liquid extractant, their selectivity in extractive desulfurization and recycling of the used ionic liquids should further be concentrated on.Keywords: ionic liquid; gasoline; diesel oil; desulfurization; extraction随着石油工业和汽车工业的飞速发展,汽车尾气所造成的环境污染问题日益严重。
- 1、下载文档前请自行甄别文档内容的完整性,平台不提供额外的编辑、内容补充、找答案等附加服务。
- 2、"仅部分预览"的文档,不可在线预览部分如存在完整性等问题,可反馈申请退款(可完整预览的文档不适用该条件!)。
- 3、如文档侵犯您的权益,请联系客服反馈,我们会尽快为您处理(人工客服工作时间:9:00-18:30)。
A new approach for the deep desulfurization of diesel fuels by extraction with ionic liquids is described.In recent years deep desulfurization of diesel fuel has attracted much attention due to the gradual reduction of the statutory sulfur content in most western countries. In 2005 the max. S-content will be limited down to 10–50 ppm compared to today’s value of 500 ppm S. These efforts aim to limit SO2emission from diesel engines and to protect equipment from corrosion. Moreover, lower sulfur content of diesel fuels would allow the use of other catalysts for the reduction of NO x emissions.In industry, desulfurization of diesel is actually carried out by hydrotreating. Generally, this allows the elimination of aliphaticand alicyclic sulfur compounds.1However, dibenzothiophene (DBT) and especially 4,6-alkyl-substituted DBTs are difficult to convert into H2S due to the sterically hindered adsorption of these compounds on the catalyst surface.2–4The expenses (hydrogen pressure, reactor size) to meet future legal specifica-tions with classical hydrotreating processes are therefore high. Thus, alternative ways for the production of low or even ultra-low sulfur contents in diesel oil are attractive.In the present paper, the use of ionic liquids (ILs) for the selective extraction of sulfur compounds from diesel fuel is described for the first time. ILs are low melting (<100 °C) salts which represent a new class of non-molecular, ionic solvents.5,6 Up to now, ILs have been mainly studied with respect to biphasic homogeneous catalysed processes. The range of known and available ILs has been expanded so that many different candidates are accessible today.7,8In a first set of experiments, the desulfurization of a model diesel oil obtained by dissolving 500 ppm DBT in n-dodecane was investigated. Based on the initial idea to extract the sulfur compound by chemical interaction, the extraction with Lewis-and Brønsted-acidic ILs was studied. As Lewis-acidic ILs, acidic mixtures of 1-n-butyl-3-methylimidazolium ([BMIM]) chloride and 1-ethyl-3-methylimidazolium ([EMIM]) chloride8 with AlCl3(molar ratio [cation]Cl/AlCl3= 0.35/0.65) were investigated. A 1+1 (mol/mol) mixture of two trialkylammon-ium methanesulfonate salts was tested as Brønsted-acidic ILs. All ILs formed a biphasic system with the model oil at room temperature. Application of the methanesulfonate melt had the additional advantage of having an easy analytical control of IL leaching into the (for this specific experiment S-free) oil, although this was never observed.For the extraction experiments, the IL was added to an excess of model oil in a mass ratio of 1/5. The obtained biphasic mixture was then stirred at room temperature. Samples were taken every 5 min. However, it was found that the extraction process proceeded quickly. Consequently, the final sulfur concentration was reached after 5 min and longer stirring did not result in lower sulfur contents. All sulfur contents presented were determined with an Antek Pyroreactor 771, which was equipped with an Antek UV-sulfur-detector 714. Repeated measurements indicated an average error of this method of ± 5 ppm.The results of a single extraction step with selected Lewis-and Brønsted-acidic ILs are presented in Table 1. All ILs under investigaton showed good properties to extract DBT out of the model oil. The comparison of the extraction experiments with the two different chloroaluminate melts suggests a certain influence of the ionic liquid’s cation (compare entries a and b in Table 1). The relatively good extraction properties of the Brønsted-acidic methanesulfonate mixture indicates both good extraction power for DBT and no (or at least not measurable) leaching of the ionic liquid into the model oil. The solubility of hydrocarbons in ILs compared to S-compounds is very low. In order to understand in more detail the observed DBT extraction, the extraction with the neutral methanesulfonate mixture [N(C6H11)Et2Me][CH3SO3]/[NBu3Me][CH3SO3] = 1/1 (C6H11= cyclohexyl) under otherwise identical conditions was investigated. The latter was obtained in a simple manner by mixing equimolar amounts of N(C6H11)Et2and NBu3with a stoichiometric amount of methanesulfonic acid methylester. Surprisingly, the sulfur content of the model oil was found to be as low as 300 ppm after a single extraction step. This demonstrates—at least for the methanesulfonate melts under investigation—that the ionic liquid’s extraction power for DBT is not uniquely based on chemical interactions involving the acid proton.Encouraged by these results, different cation/anion combina-tions of neutral ILs in the extraction of DBT were tested. Selected results of an anion variation with ILs of the general type [BMIM][anion] are given in Table 2.The data indicate that the desulfurization is hardly affected by the chemical nature of the anion. Only the IL with the somewhat bigger octylsulfate ion showed significantly better extraction properties. From these results it can be concluded that the size of the ions is rather important for the extraction effect. This Table 1Desulfurization of model diesel fuel (500 ppm sulfur in n-dodecane) by extraction with Lewis- and Brønsted-acidic ionic liquids a Entry Ionic liquidSulfurcontent/ppma[BMIM]Cl/AlCl3= 0.35/0.65b275b[EMIM]Cl/AlCl3= 0.35/0.65335c[HN(C6H11)Et2][CH3SO3]/[HNBu3][CH3SO3] = 1/1310a General conditions: room temperature, mass ratio model oil/IL= 5/1, extraction time: 15 min, initial sulfur content 500 ppm.b Mol/mol.Table 2Comparison of different anions in the desulfurization process of a model diesel oil (500 ppm sulfur in n-dodecane) by extraction with neutral ionic liquids of the general type [BMIM][anion]aEntry AnionSulfurcontent/ppma[PF6]2440b[CF3SO3]2430c[BF4]2420d Cl2410e[MeSO4]2410f[MeSO3]2410g[OcSO4]2350a General conditions: 60 °C (except entry d: 80 °C), mass ratio model oil/ IL= 5/1, reaction time 15 min, initial sulfur content: 500 ppm.This journal is © The Royal Society of Chemistry 20012494Chem. Commun., 2001, 2494–2495DOI: 10.1039/b108411aassumption was further supported by extraction experiments with different tetrafluoroborate salts (Table 3).In this context, it is important to note that the comparison of different ILs in Tables 2 and 3 is based on equal mass ratio model oil/IL. A comparison on the base of equal molar levels would show an even more pronounced effect of the cation’s/ anion’s size on the extraction power of the ILs. A possible explanation for this behaviour may be that the physical solubility of DBT in the IL is dependent on steric factors in the IL.In order to check the feasibility of our concept for a deep desulfurization process, we tried to reach very low sulfur levels by application of a multistage extraction process (mixer–settler-system). For these experiments the best IL candidate [BMIM]Cl/AlCl3: 0.35/0.65 was chosen as extraction medium. The desulfurized model oil from the first extraction step was again treated with fresh ionic liquid. This process was repeated up to four times. The results with different mass ratios model oil/IL are presented in Fig. 1.As expected, Fig. 1 shows that a lower mass ratio of model oil to ionic liquid results in lower sulfur contents. However, sulfur contents below 50 ppm can be reached for all mass ratios if the number of extraction steps is high enough. The almost linear relationship of log(S-content) vs.the number of extraction steps indicates that the extraction can be formally described by a partition coefficient according to Nernst’s law. This is con-firmed by re-extraction experiments (mixture of IL with extracted S-compound and S-free n-dodecane): The same distribution of sulfur (ratio of concentration in IL to concentra-tion in n-dodecane) is obtained, which was tested by the re-extraction of DBT from the loaded ionic liquid [HN(C6H11)Et2][CH3SO3]/[HNBu3][CH3SO3] = 1/1 with in this case S-free n-dodecane. In this context NMR measurements of the used ILs confirm also that the extracted DBT remains unreacted. Thus regeneration of the ILs should be generally achievable, although more systematic experiments are needed.In a technical extraction process, the IL, which has been loaded with organic sulfur components in the extraction column (or mixer–settler-system), would be continuously regenerated in a second column, and then pumped back into the extraction unit. Thus the potential to regenerate the IL is an important aspect. Interesting re-extraction media are probably light alkanes (C2–C5) or supercritical CO2, as these solvents can be easily recovered and separated from the higher boiling sulfur compounds by evaporation. The organic sulfur would than be converted into elemental sulfur by the common Claus-proc-ess.Subsequently, the new desulfurization concept was tested by additional experiments with a ‘real’ predesulfurised diesel oil (without additives, sulfur content: 375 ppm). As expected, the extraction of real diesel oil is much more complicated due to its complex chemical composition including many different sulfur compounds and other impurities like organic nitrogen and oxygen compounds.Nevertheless, the results of experiments with predesulfurized diesel are also promising. As shown in Table 4, the Lewis-acidic ionic liquid [BMIM]Cl/AlCl3: 0.35/0.65 showed much higher efficiency in the sulfur extraction from real diesel in comparison to the methanesulfonate and octylsulfate melts.This indicates that Lewis acid–base interactions enhance the extraction power of the IL here. Nevertheless, the extraction power of the neutral methanesulfonate and octylsulfate melts is still remarkable. However, more extraction steps are necessary in case of ‘real’ diesel oil to reach future technical sulfur content specifications (<50 ppm). The use of AlCl3-free ILs is particularly promising as the use of AlCl3in desulfurization is probably unlikely to be accepted by refiners.In conclusion, the presented results show a new approach for the deep desulfurization of diesel oil, especially with regard to those sulfur compounds that are very difficult to remove by common hydrodesulfurization techniques. Traces of such sulfur compounds could easily be removed. The new method is based on the extraction of the sulfur compounds with ILs. The application of very mild process conditions (low pressure and temperature) is an additional advantage of this new approach in comparison to traditional HDS.Generally the extraction of polarizeable compounds by ionic liquids may be a possibility to isolate valued products which reside in complex mixtures of a multitude of different organic substances as is likely to occur in aromas and scents. Present work is directed towards a deeper understanding of the extraction properties of ILs, and to identify inexpensive, unchlorinated IL systems with enhanced extraction power. The authors acknowledge Miro refinery/Karlsruhe, Germany for the donation of the predesulfurized diesel oil.Notes and references1S. Zaczepinski, Exxon Diesel Oil Deep Desulfurization (DODD), in Handbook of Petroleum Refining Processes, ed. R. A. Meyers, McGraw-Hill, New York, 1996, ch. 8.7.2C. Kwak, J. J. Lee, J. S. Bae, K. Choi and S. H. Moon, Appl. Catal. A, 2000, 200, 233.3R. Shafi and G. J. Hutchings, Catal. Today, 2000, 59, 423.4X. Ma, K. Sakanishi and I. Mochida, Ind. Eng. Chem. Res., 1994, 33, 218.5P. Wasserscheid and W. Keim, Ang ew. Chem., Int. Ed., 2000, 39, 3772.6T. Welton, Chem. Rev., 1999, 99, 2071.7J. D. Holbrey and K. R. Seddon, Clean Products Processes, 1999, 1, 223.8Many ionic liquids are commercially available nowadays. For example, [BMIM]Cl and [EMIM]Cl can be purchased from Solvent Innovation GmbH, Cologne, Germany (www.solvent-innovation.de).Table 3Comparison of different cations in the extraction of DBT from n-dodecane with different tetrafluoroborate ionic liquids aCation Sulfur content/ppm[EMIM]450[BMIM]420[OMIM]380a General conditions: 50 °C, mass ratio model oil/IL= 5/1, reaction time 15 min, initial sulfur concentration 500 ppm; [OMIM] = 1-methyl-3-n-octylimidazolium.Fig. 1Multistage desulfurization of model diesel oil (500 ppm sulfur in n dodecane) by the IL [BMIM]Cl/AlCl3(0.35/0.65; different mass ratios oil/ IL) at room temperature.Table 4Multistage desulfurization of predesulfurized (real) diesel oil a Stage[BMIM]Cl/AlCl3[HN(C6H11)Et2]-[CH3SO3]/[HNBu3]-[CH3SO3] = 1/1[BMIM]-[octylsulfate]1375375375 2220330320 3160300280 4130270260 575240235a60 °C, mass ratio diesel oil/IL = 5/1, reaction time: 15 min.Chem. Commun., 2001, 2494–24952495。