第一章机械加工工艺规程设计(第二部分)
机械制造工艺
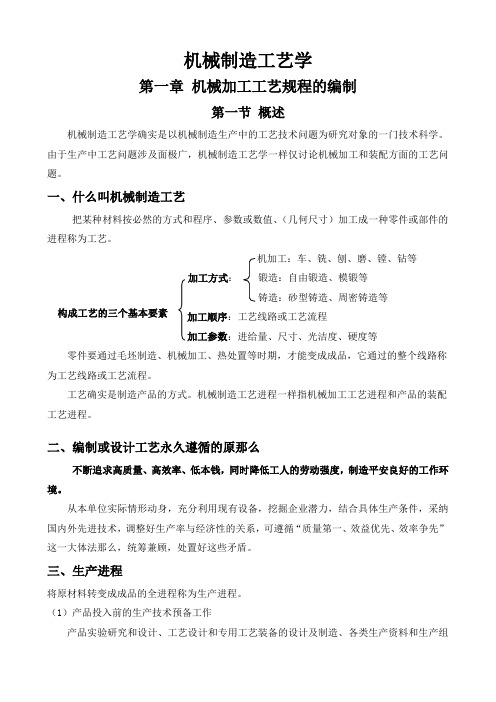
机械制造工艺学第一章机械加工工艺规程的编制第一节概述机械制造工艺学确实是以机械制造生产中的工艺技术问题为研究对象的一门技术科学。
由于生产中工艺问题涉及面极广,机械制造工艺学一样仅讨论机械加工和装配方面的工艺问题。
一、什么叫机械制造工艺把某种材料按必然的方式和程序、参数或数值、(几何尺寸)加工成一种零件或部件的进程称为工艺。
机加工:车、铣、刨、磨、镗、钻等加工方式:锻造:自由锻造、模锻等铸造:砂型铸造、周密铸造等构成工艺的三个基本要素加工顺序:工艺线路或工艺流程加工参数:进给量、尺寸、光洁度、硬度等零件要通过毛坯制造、机械加工、热处置等时期,才能变成成品,它通过的整个线路称为工艺线路或工艺流程。
工艺确实是制造产品的方式。
机械制造工艺进程一样指机械加工工艺进程和产品的装配工艺进程。
二、编制或设计工艺永久遵循的原那么不断追求高质量、高效率、低本钱,同时降低工人的劳动强度,制造平安良好的工作环境。
从本单位实际情形动身,充分利用现有设备,挖掘企业潜力,结合具体生产条件,采纳国内外先进技术,调整好生产率与经济性的关系,可遵循“质量第一、效益优先、效率争先”这一大体法那么,统筹兼顾,处置好这些矛盾。
三、生产进程将原材料转变成成品的全进程称为生产进程。
(1)产品投入前的生产技术预备工作产品实验研究和设计、工艺设计和专用工艺装备的设计及制造、各类生产资料和生产组织等方面的预备工作。
(2)毛坯制造毛坯的锻造、铸造和冲压等。
(3)零件的加工进程机械加工、特种加工、焊接、热处置和表面处置。
(4)产品的装配进程部件装配、总装配、查验和调试等。
(5)各类生产效劳活动原材料、半成品、工具的供给、运输、保管和产品的油漆和包装等。
从上述进程能够看出,机械产品的生产进程是相当复杂的,为了便于组织生产和提高劳动生产率,现代机械工业的进展要求组织专业化生产,即一种产品的生产是分散在假设干个工厂进行的,如此各有关工厂的生产进程就比较简单,有利于保证质量、提高生产率和降低本钱。
机械加工操作规程(三篇)

机械加工操作规程第一章总则第一条本规程是根据机械加工工艺和操作要求,制定的操作规程。
第二条本规程适用于机械加工工人。
第三条加工前,应先熟悉加工零件的图纸和加工工艺,掌握所操作设备的结构、性能和操作方法。
第四条加工作业前,应按规程对设备进行检查,检查应包括加工设备电源是否正常,各操作部位是否灵活,加工刀具磨损情况等。
第五条操作时,应按要求使用安全防护装置,严禁戴手套、带卷发或长发等操作。
第六条加工过程中,发现异常情况应及时停机,并向上级报告。
第七条加工完成后,应及时对加工设备进行清洁,刀具归位,加工废料清理完毕。
第二章机床操作规程第八条加工前,应检查机床各操作部位是否灵活,机床轴向、刀具刃部是否有磕碰。
第九条加工过程中,应严禁手放机床上进行加工,禁止用手直接触摸正在运转的主轴、工件、刀具等。
第十条进给运动方向的选择应根据工件的形状和尺寸来确定,并按照正确的进给路径进行操作。
第十一条加工中,严禁调节喷气冷却装置,更换刀具等操作。
第十二条加工结束后,应彻底清洗机床切削液,及时清理加工废料和刀屑,在加工下一个工件之前,应对机床进行保养和维护。
第三章刀具操作规程第十三条加工前,应检查刀具磨损情况,如严重磨损应更换新刀具。
第十四条更换刀具时,应关闭机床电源,并将主轴锁上。
第十五条刀具安装时,应确保刀具刀尖与工件接触时是垂直的,夹持紧固螺母要适度,避免过紧或过松。
第十六条切削过程中,要注意切屑的排出,保证冷却液的喷射。
第十七条刀具分为粗加工刀具和精加工刀具,加工过程中要根据要求进行合理选择。
第十八条加工结束后,要及时清洗刀具,并进行涂油保养,以防刀尖生锈。
第四章加工操作规程第十九条加工前,应检查工件的尺寸和形状,确保符合要求。
第二十条加工过程中,应掌握加工工艺和操作要领,避免出现加工失误。
第二十一条加工过程中,要注意切削力的大小和方向,调整刀具进给量和转速。
第二十二条加工结束后,要对工件进行清洁,严禁在不符合要求的情况下交付。
最新-轴承座零件机械加工工艺规程设计(刨主视图上平面及轴承孔左右两面)
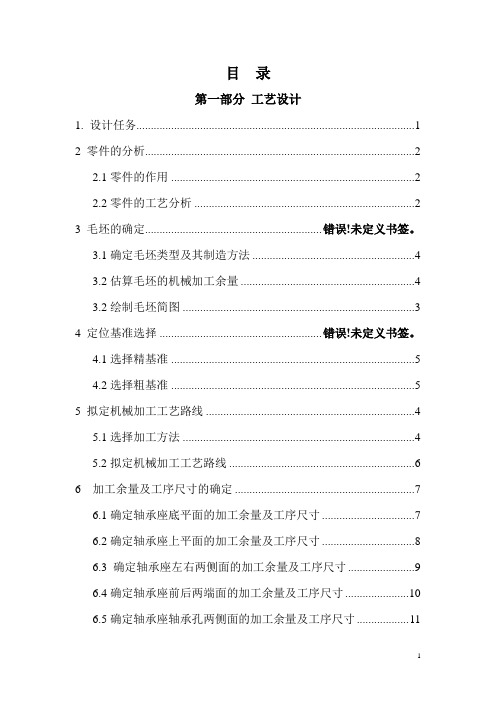
目录第一部分工艺设计1. 设计任务 (1)2 零件的分析 (2)2.1零件的作用 (2)2.2零件的工艺分析 (2)3 毛坯的确定.......................................................... 错误!未定义书签。
3.1确定毛坯类型及其制造方法 (4)3.2估算毛坯的机械加工余量 (4)3.2绘制毛坯简图 (3)4 定位基准选择 ..................................................... 错误!未定义书签。
4.1选择精基准 (5)4.2选择粗基准 (5)5 拟定机械加工工艺路线 (4)5.1选择加工方法 (4)5.2拟定机械加工工艺路线 (6)6 加工余量及工序尺寸的确定 (7)6.1确定轴承座底平面的加工余量及工序尺寸 (7)6.2确定轴承座上平面的加工余量及工序尺寸 (8)6.3 确定轴承座左右两侧面的加工余量及工序尺寸 (9)6.4确定轴承座前后两端面的加工余量及工序尺寸 (10)6.5确定轴承座轴承孔两侧面的加工余量及工序尺寸 (11)6.6 确定轴承座槽的加工余量及工序尺寸 (12)6.7 确定轴承座沉孔的加工余量及工序尺寸 (13)6.8 确定轴承座气孔φ6和φ4的加工余量及工序尺寸 (14)6.9确定轴承孔Φ30和Φ35的加工余量及工序尺寸 (15)第二部分夹具设计1. 设计任务 (15)2. 确定定位方案 (15)7、设计总结.......................................................... 错误!未定义书签。
参考文献 (17)第一部分工艺设计1.设计任务本次所要加工的零件为轴承座,以下为轴承座示意图:材料:HT200零件生产纲领:中等批量2.零件的分析2.1零件的作用轴承座是用于支撑轴类零件的,镗孔的目的是为了满足滚动轴承的外圈和轴承孔的配合要求,或者是滑动轴承外圆与轴承孔的配合,两个孔是用于固定轴承座的,单边固定是出于满足结构和安装位置的要求。
差速器壳零件的机械加工工艺规程及钻端面12孔钻床夹具设计
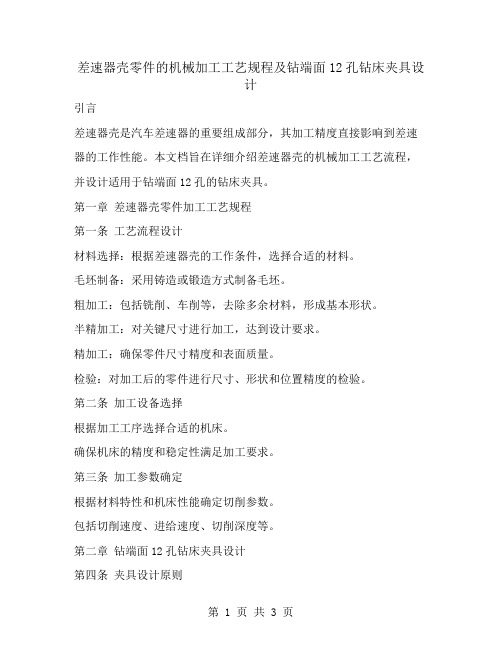
差速器壳零件的机械加工工艺规程及钻端面12孔钻床夹具设计引言差速器壳是汽车差速器的重要组成部分,其加工精度直接影响到差速器的工作性能。
本文档旨在详细介绍差速器壳的机械加工工艺流程,并设计适用于钻端面12孔的钻床夹具。
第一章差速器壳零件加工工艺规程第一条工艺流程设计材料选择:根据差速器壳的工作条件,选择合适的材料。
毛坯制备:采用铸造或锻造方式制备毛坯。
粗加工:包括铣削、车削等,去除多余材料,形成基本形状。
半精加工:对关键尺寸进行加工,达到设计要求。
精加工:确保零件尺寸精度和表面质量。
检验:对加工后的零件进行尺寸、形状和位置精度的检验。
第二条加工设备选择根据加工工序选择合适的机床。
确保机床的精度和稳定性满足加工要求。
第三条加工参数确定根据材料特性和机床性能确定切削参数。
包括切削速度、进给速度、切削深度等。
第二章钻端面12孔钻床夹具设计第四条夹具设计原则保证加工精度:夹具设计要确保加工过程中零件的位置精度。
操作简便:夹具操作要简单快捷,便于工人使用。
安全可靠:夹具结构要牢固,防止加工过程中的意外。
第五条夹具结构设计底座:设计稳定的底座,用于固定夹具。
夹紧机构:设计合理的夹紧机构,确保零件在加工过程中的稳定性。
定位元件:设计定位元件,确保零件在夹具中的准确位置。
钻模板:设计钻模板,用于引导钻头进行钻孔。
第六条夹具操作流程将差速器壳零件放置在夹具的定位元件上。
操作夹紧机构,将零件牢固夹紧。
调整钻模板位置,确保钻头与待钻孔对准。
启动钻床,进行钻孔加工。
加工完成后,松开夹紧机构,取出加工好的零件。
第七条夹具维护与保养定期检查夹具各部件的磨损情况,及时更换损坏部件。
清洁夹具,防止油污和金属碎屑影响夹具性能。
定期对夹具进行润滑,保证其运动部件的顺畅。
第三章加工质量控制第八条加工质量标准制定差速器壳加工的质量标准,包括尺寸精度、表面粗糙度等。
严格按照质量标准进行加工和检验。
第九条质量检验方法采用量具和测量仪器对加工后的零件进行检验。
课程设计-零件的机械加工工艺规程的编制及工装设计

课程设计-零件的机械加工工艺规程的编制及工装设计摘要本文旨在介绍零件机械加工工艺规程的编制方法和工装设计要点,为机械加工领域的学生和工程师提供参考。
引言机械加工工艺规程的编制是确保加工质量、提高生产效率的关键环节。
合理的工艺规程和工装设计能够显著提升加工精度和生产效率。
第一章:零件加工工艺规程编制1.1 零件分析对零件的几何形状、尺寸、材料等进行详细分析。
1.2 加工工艺路线确定根据零件特点确定加工顺序和加工方法。
1.3 工艺参数选择选择合适的切削参数,如切削速度、进给速度、切削深度等。
1.4 工艺文件编制编制工艺卡片、工艺流程图等工艺文件。
第二章:工装设计2.1 工装设计原则介绍工装设计的基本原则,如定位精度、夹紧稳定性等。
2.2 夹具设计根据加工工艺要求设计夹具,确保零件的定位和夹紧。
2.3 刀具选择选择合适的刀具,考虑刀具材料、类型、尺寸等因素。
2.4 量具与检测选择合适的量具,制定检测方案,确保加工质量。
第三章:工艺规程编制实例3.1 零件选择选择一个具体的零件作为工艺规程编制的实例。
3.2 工艺路线分析对选定零件的加工工艺路线进行详细分析。
3.3 工艺参数确定确定加工过程中的工艺参数。
3.4 工艺文件编制编制该零件的工艺卡片和工艺流程图。
第四章:工装设计实例4.1 夹具设计针对选定零件的加工特点,设计相应的夹具。
4.2 刀具选择与设计选择和设计适合该零件加工的刀具。
4.3 量具选择与检测方案选择适合的量具,并制定检测方案。
第五章:质量控制与优化5.1 加工质量控制制定加工过程中的质量控制措施。
5.2 工艺优化分析工艺过程中的瓶颈,提出优化建议。
5.3 成本控制考虑加工成本,提出成本控制措施。
结论机械加工工艺规程的编制和工装设计是确保加工质量和效率的重要环节。
通过合理的工艺设计和精确的工装配合,可以有效提升零件加工的精度和生产效率,为企业创造更大的价值。
双联齿轮轴机械加工工艺流程

双联齿轮轴机械加工工艺流程全文共四篇示例,供读者参考第一篇示例:双联齿轮轴是一种常见的传动装置,通常用于机械设备中的传动系统。
它由两个齿轮轴相互咬合,通过齿轮的旋转来传递力和运动。
双联齿轮轴的制作需要经过一系列的机械加工工艺流程,下面我们就来详细介绍一下。
1.材料准备双联齿轮轴通常由优质的合金钢或碳素钢制成,这种材料具有良好的强度和硬度,适合用于制作齿轮轴。
在进行机械加工之前,首先需要对材料进行切割、锻造或铸造等工艺,将其加工成符合设计要求的毛坯。
2.车削加工在进行车削加工之前,需要对毛坯进行表面清洁和粗加工处理,去除表面的氧化层和杂质。
然后将毛坯装夹在车床上,进行外径、内径、端面和键槽等部位的车削加工。
通过车削加工,可以使齿轮轴的各个部位具有精确的尺寸和光洁的表面。
3.齿轮加工双联齿轮轴上的齿轮通常是其中的一个关键部件,它需要经过齿轮加工工艺来加工成型。
首先需要根据设计要求确定齿轮的模数、齿数和齿轮箱数等参数,然后使用齿轮加工机床进行铣削或滚齿加工。
通过齿轮加工,可以使齿轮具有精确的齿形和尺寸,确保它与其他齿轮的咬合匹配度和传动精度。
4.热处理在齿轮轴的加工过程中,还需要对其进行热处理工艺。
热处理可以提高齿轮轴的强度、硬度和耐磨性,同时消除加工过程中产生的残余应力。
常见的热处理工艺包括淬火、回火、正火等,根据不同的要求进行选择。
5.装配经过以上工艺流程之后,齿轮轴的各个部件就可以进行装配了。
首先需要在齿轮轴上进行配合孔和键槽的加工,然后通过配合销、压板或螺栓等连接方式,将齿轮、轴套、轴承等部件装配到齿轮轴上。
在装配过程中,需要保证各个部件的配合精度和装配间隙,确保齿轮轴的传动性能和运转稳定性。
6.检测对装配好的齿轮轴进行全面的检测和调试。
通过检测工艺来检验齿轮轴的各项性能指标,如尺寸精度、径向跳动、轴向跳动、齿形精度等。
通过调试工艺来确保齿轮轴的运转平稳、传动精度和效率等。
通过上述的机械加工工艺流程,我们可以生产出符合设计要求的双联齿轮轴,这种齿轮轴具有较高的传动精度、稳定性和耐久性,广泛应用于工程机械、轨道交通、船舶船舶等领域。
机械制造讲义工艺学_第一章
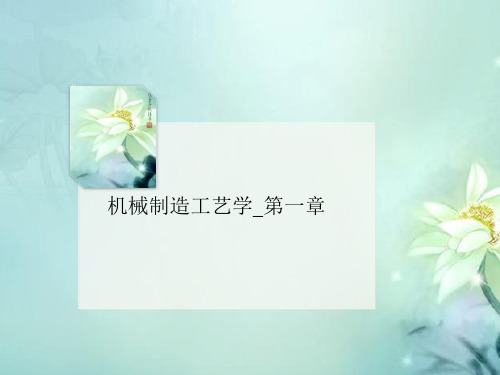
更适用 于单件小批 量生产,因 为效率不是 主要问题, 主要应减少 设备使用及 人员分配。
工序号 1
2
3
表1 生产的工艺过程
工序内容
车一端面,钻中心孔;调头,车另一 端面,钻中心孔;
车大外圆及倒角;车小外圆、切槽及 倒角
铣键槽、手工去毛刺
设备 车床I
车床II
铣床
1.2 生产过程、工艺过程与工艺系统
• 工件以外圆柱面定位 • 工件以外圆柱面定位有两种形式:定心定位和支承定位。 • 定心定位与工件以圆孔定位情况相仿。 • 工件以外圆柱面支承定位元件常采用V形块——短V形块 限制两个自由度,长V形块(或两个短V形块组合)限制 四4个自由度。
1.4 工件加工时的定位和基准
一工件的定位
• 定位原理
1.2 生产过程、工艺过程与工艺系统
二 机械加工工艺过程 • 组成
• 工位:在工件的一次安装中,通过分度或移位装置,使工件相对 于机床床身变换加工位置,则把每一个加工位置上的安装内容称 为工位。
工件 机床夹具回转部分 夹具固定部分
分度机构
1.2 生产过程、工艺过程与工艺系统
二 机械加工工艺过程
• 组成
找正线 加工线
毛坯孔
1.4 工件加工时的定位和基准
一工件的定位
• 工件装夹
• 夹具装夹 将工件装夹在夹具中,由夹具上的定位元件来确定工件的位置, 由夹具上的夹紧装置进行夹紧。精度和效率均高,广泛采用。
1.4 工件加工时的定位和基准
一工件的定位
• 定位原理
• 六点定位原理
采用六个按一定规则布置的约束点来限制工
• 工艺特点
划分生产类型的意义在于:有利于进行生产规划和管理。由于生 产类型的不同,其零件在加工工艺性、工艺装备、毛坯制造方法 以及对工人的技术要求等存在很大差异。
油缸盖零件机械加工工艺规程设计
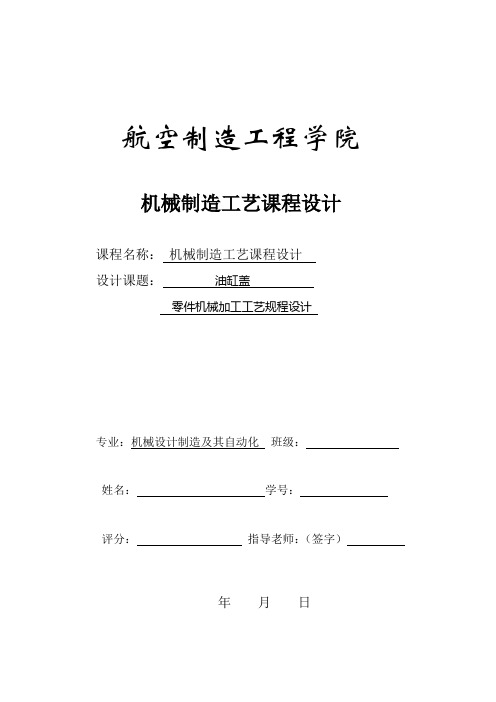
航空制造工程学院机械制造工艺课程设计课程名称:机械制造工艺课程设计设计课题:油缸盖零件机械加工工艺规程设计专业:机械设计制造及其自动化班级:姓名:学号:评分:指导老师:(签字)年月日航空制造工程学院机械设计制造及其自动化专业《机械制造工艺及装备》课程设计课题单班级学生课题油缸盖零件机械加工工艺规程设计原始条件油缸盖零件图生产纲领:中等批量设计要求 1.绘制油缸盖零件图2.编制油缸盖零件机械加工工艺规程(含机械加工工艺过程卡和机械加工工序卡)3. 设计“铣削四方”夹具。
(含装配图1份、零件图1~3张)4.编写课程设计说明书。
课题发给日期 2012年11月12日课程设计完成日期 2012年11月30日指导教师(签名)目录第一部分工艺设计1.设计任务............................................................² (4)2..零件工艺性分析 (5)3.毛坯的选择.........................................................² (6)4.工艺过程设计.........................................................² (7)5.确定毛坯尺寸、机械加工余量及工序尺寸 (13)第二部分夹具设计1.设计任务 (17)2.确定定为方案、选择定位元件 (18)3.夹紧机构的选择和设计 (19)4.定位误差的计算 (20)5.对刀装置的选择 (20)6.夹具在机床上的定位和夹紧 (20)小结 (22)参考书目 (23)第一部分工艺设计1.设计任务本次所要加工的零件为油缸盖,示意图如下图1:2.零件的工艺分析本零件是油缸盖,零件图的视图正确、完整,尺寸、公差齐全。
材料为35号钢,良好的塑性和适当的强度。
技术要求:1.尺寸精度和粗糙度:Φ31公差为0.062,粗糙度为1.6、Φ25公差为0.033,粗糙度为1.6等2.位置度:同轴度25Φ和Φ35.86、Φ40分别为Φ0.03、Φ0.02垂直度正方体底面和A为0.043.锐边倒钝去毛刺4.未标注倒角为C0.55.表面热处理:发蓝6.其余表面粗糙度为6.3该零件的结构特点是:它的上体是个正方体,端面上有4-Φ14、4-Φ9、4-M5、Φ5及Φ31等孔。
- 1、下载文档前请自行甄别文档内容的完整性,平台不提供额外的编辑、内容补充、找答案等附加服务。
- 2、"仅部分预览"的文档,不可在线预览部分如存在完整性等问题,可反馈申请退款(可完整预览的文档不适用该条件!)。
- 3、如文档侵犯您的权益,请联系客服反馈,我们会尽快为您处理(人工客服工作时间:9:00-18:30)。
例1:
小轴
例:如图所示小轴零件,毛坯为普通精度的热轧 圆钢,装夹在车床前、后顶尖间加工,主要工序: 下料–––车端面–––钻中心孔–––粗车外圆–––精车外 圆–––磨削外圆。
表7-11 工序尺寸及公差的计算(单位:mm) 1)确定各工序加工方法
工序 名称 磨削 工序 余量 工序经济 加工精度 IT7 0.021 工序基本尺寸 工序尺寸及偏差 0 -0.021
(4)量具的选择 单件、小批生产应广泛采用通 用量具,如游标卡尺、百分尺和千分表等;大 批、大量生产应采用极限量块和高效的专用检 验夹具和量仪等。量具的精度必须与加工精度 相适应。
第六节 加工余量 工序尺寸及公差的确定
这是工艺规程设计中的一个重要环节
1)图纸分析(阅读装配图、零件图 ); 2)工艺审查; 3)确定毛坯; 4)确定加工工艺路线; 5)确定各工序的工艺装备(包括机床、夹具、刀具和量 具); 6)确定各主要工序的技术要求和检验方法;
• 按尺寸链在空间分布的位置关系: 分为直线尺寸链、平面尺寸链和空间尺寸链。
一、尺寸链的组成 和尺寸链图的作法
A2=155-0.036 A0=99-0.087
封闭环:间接获得的尺寸A0称为封闭环;
组成环:加工过程中直接获得的尺寸如A1、A2是组成环;
A增环:该环变动引起封闭环同向变动的组成环。如A2 1和A2是在加工过程中直接获得,尺寸A0是间接保证的, A减环:该环变动引起封闭环反向变动的组成环。如A1 1、A2 和A0构成一个封闭的尺寸组,都叫尺寸链的环。
3 .经验法
由一些有经验的工程技术人员或工人根据经 验确定加工余量的大小。由经验法确定的加工余 量往往偏大。这主要是因为主观上怕出废品的缘 故。 这种方法多在单件小批生产中采用。
三.简单工序尺寸及其公差的确 定
基准重合:工艺基准和设计基准重合
工序尺寸与公差的确定步骤(基准重合情况) 1)确定各工序的加工方法; 2)确定各工序的加工余量; 3)计算各工序的基本尺寸,顺序由后向前; 4)确定各工序加工经济精度和表面粗糙度,确定 各工序尺寸公差; 5)并按“入体原则”标注。
Z min Ta R y H a ea b
2)对于双边余量:
Z min
Ta
2
Ry H a ea b
二.加工余量的确定
优点:精确 缺点:花费时间多 适用范围:大批大量生产中一些重要的工序 在分析计算时,要具体分析: a.用无心外圆磨床磨外圆,加工外圆,εb =0 Z min Ta / 2 Ry H a ea
(A1)
A2
通过保证工序尺 寸A2。
问:求A2? 必须通过工艺尺寸链进行分析计算。
A1=50-0.17
第七节
工艺尺寸链
尺寸链:由相互联系、按一定顺序首尾 相接排列的尺寸封闭图叫作尺寸链。 • 根据用途不同: 分为工艺尺寸链和装配尺寸链
工艺尺寸链:由单个零件在工艺过程中有关尺 寸形成的; 装配尺寸链:机器在装配过程中由相关零件的 尺寸或相互位置关系所组成的尺寸链。
2、热处理及表面处理工序的安排
退火 正火 时效 退火 淬火 渗碳淬火
淬硬
涂镀 发蓝处理
提高耐磨性、 耐腐蚀性、 装饰
调质
改善切 削性能
正火
消除内 应力
粗加工
半精加工
精加工
光整加工Biblioteka 为改善切削性能的热处理工序(退火、正火、 调质)应安排在切削加工之前; 为清除内应力的热处理工序(时效、退火、 正火)应安排在粗加工之后;
工序 名称 磨削 工序 余量 0.3 工序经济 加工精度 IT7 0.021 工序基本尺寸 工序尺寸及偏差 0 -0.021
25.00
Φ25.0
精车
0.8
IT10 0.084
25+0.3=25.3
粗车
毛坯
1.9
IT12 0.210
1.0
25.3+0.8=26.1
26.1+1.9=28.0
总3.0 IT14
工序 名称 磨削 工序 余量 0.3 工序经济 加工精度 IT7 0.021 工序基本尺寸 工序尺寸及偏差 0 -0.021
25.00
Φ25.0
精车
0.8
25+0.3=25.3
粗车
毛坯
1.9
总3.0
25.3+0.8=26.1
26.1+1.9=28.0
表7-11 工序尺寸及公差的计算(单位:mm) 4)确定各工序加工经济精度和表面粗糙度
表7-11 工序尺寸及公差的计算(单位:mm) 4)按“入体原则”标注公差
工序 名称 磨削 工序 余量 0.3 工序经济 加工精度 IT7 0.021 工序基本尺寸 工序尺寸及偏差 0 -0.021 0 -0.084
25.00
Φ25.0
精车
0.8
IT10 0.084
25+0.3=25.3
Φ25.3
7)确定各工序的加工余量,计算工序尺寸和公差
8)确定切削用量; 9)确定时间定额; 10)填写工艺文件。
一.加工余量的基本概念
(一)加工总余量(毛坯余量)与工序余量
总余量Z0与工序余量Zi 的关系: 单边余量
对于非对称表面,其加工余量用单边余量 Zb 表示
Z 0 Z i
i 1
n
Zb =la-lb
七、工艺装备的选择
工艺装备选择的合理与否,将直接影响工件 的加工精度、生产效率和经济效益。应根据生产 类型、具体加工条件、工件结构特点和技术要求 等选择工艺装备。 (1)机床的选择 普通机床、数控机床、专用组 合机床。 机床的精度应与工序要求的精度相适应; 机床的生产率应与该零件生产类型相适应; 机床的加工尺寸范围应与零件的外形尺寸相适应; 应符合本厂现有的实际情况。
设计机械加工工艺规程的步骤和内容:
1)图纸分析(阅读装配图、零件图 ); 2)工艺审查; 3)确定毛坯; 4)确定加工工艺路线; 5)确定各工序的工艺装备(包括机床、夹具、刀具 和量具); 6)确定各主要工序的技术要求和检验方法; 7)确定各工序的加工余量,计算工序尺寸和公差; 8)确定切削用量; 9)确定时间定额; 10)填写工艺文件。
特点: 1)设备和工艺装备简单、调整、对刀方便、工人便于掌 握,容易适应产品的变换; 2)对操作工人的技术水平要求较低; 3)设备和工艺装备数量多、操作工人多、生产占地面积 大。 应用:流水线、自动线、组合机床、大批量生产
六、加工阶段的划分
⑴粗加工阶段:切除各加工表面上的大部分余量, 并做出精基准。这一阶段的主要目标是提高生产 率。
双边余量
对于外圆内圆等对称表面加工余量用双边余量2Zb表示
单边余量
Zb =la-lb
双边余量
外圆表面 2 Zb =da-db , 内圆表面 2 Zb =Db-Da
由于各工序尺寸都有公差,故加工余量也有公差。
工序余量又分为公称余量Zb、最大余量Zmax、最小余量Zmin 对于被包容面,本工序的公称余量 工序尺寸公差一般按“入体原则”标 注
b.浮动镗孔,不能纠正偏斜和弯曲,ea,εb =0
Zmin Ta / 2 Ry Ha
c.研磨,衍磨,超精磨和和抛光等光整加工, Z min= Ry
2 .查表法
此法主要以工厂生产实践和实验研究积累
的经验所制成的表格为基础,并结合实际加工 情况加以修正,确定加工余量。
这种方法方便、迅速,生产上应用广泛。
0.05
2/L+0.025
2/L-0.025
4.本工序的装夹误差(εb) 装夹误差包括:定位误差和夹紧误差。 这项误差会直接影响被加工表面与切削刀具 的相对位置。
R-e R+e
三爪卡盘的装夹误差
由于空间误差和装夹误差都是有方向的,所以, 要采用矢量相加的方法,取矢量和的模进行余量计算 综上分析,工序余量的最小值可用以下公式计算: 1)对于单边余量:
⑵半精加工阶段:减小粗加工留下的误差,为主 要表面的精加工作好准备,并完成一些次要表面 的加工。 ⑶精加工阶段:保证各主要表面达到图纸规定的 要求。
⑷光整加工阶段:进一步减小表面粗糙度、提高 精度。
划分阶段原因: 粗加工时,切削层厚,切削热量大,无法 消除因热变形带来的加工误差,也无法消 除因粗加工留在工件表层的残余应力产生 的加工误差。 后续加工容易把已加工好的加工面划伤。 不利于及时发现毛坯的缺陷。 不利于合理地使用设备。 不利于合理地使用技术工人。
特点: 1)有利于采用高效率机床; 2)易于保证各表面间的相互位置精度,减少了装夹次数, 节省时间; 3)工序集中通常需要采用专用设备和工艺装备,使得投 资大,设备和工艺装备的调整、维修较为困难,生产准 备工作量大,转换新产品较麻烦。 应用:高效的自动化机床(例如加工中心,单件小批量多 品种)
2.工序分散 工序分散则是将工件的加工分散在较多的 工序内完成。
Zb =la-lb
Zmax= la – (lb –Tb)= Zb + Tb Zmin =( la – Ta ) – lb= Zb – Ta
工序余量变动范围 Tz = Zmax–Zmin
= Tb + Ta
一般情况下,工序尺寸按“入体原则”标注。 被包容尺寸:指实体尺寸。 例如:轴的外径,长方体的长、宽、高。 其最大尺寸作为工序尺寸的基本尺寸(公称 尺寸d)
25.00
Φ25.0
精车
粗车
毛坯
表7-11 工序尺寸及公差的计算(单位:mm) 2)查表法确定各工序加工余量
工序 名称 磨削 工序 余量 0.3 工序经济 加工精度 IT7 0.021 工序基本尺寸 工序尺寸及偏差 0 -0.021
25.00
Φ25.0