APQP产品质量策划和控制计划概述.PPT
合集下载
APQP产品质量先期策划ppt课件

产品质量策划的基本原则
组织小组 确定范围 小组间沟通 培训 顾客和供方的参与 同步工程 控制计划:样件、试生产、生产 问题的解决:文件化、职责、解决问题的方法和分析技术 产品质量的进度计划 供方与顾客的进度计划
并行工程、同步工程(CE)
现代企业面临的主要课题——创新, 创新又面临着两个风险:市场不确定性和
(14)
零件/ 过 过 程 名 机器、装置 特性
特殊特 方法
反应计
程编号 称/操作 夹具、工装 编号 产品 过程 性分类 产品/过程 评 价 / 样本(24) 控制方 划(26)
(15) 描述
(17) (18) (19) (20) (21) 规格/公差 测量技 容量 频率 法(25)
(16)
(22) 术(23)
QS-9000核心工具
APQP
产品质量先期策划和控制计划 Advanced Product Quality Planning
and Control Plan
产品质量策划循环
产品质量策划责任矩阵图
*设计责任
*仅限制造
服务供方如热处理 贮存、运输 等等
确定范围
X
X
X
计划和确定(第一章)
X
产品设计和开(第二章) X
3.1包装标准
顾客提供包装标准,为产品包装设计的输 入
如无相应标准提供时,要求包装保证产品 质量不损坏
3.2产品/过程质量体系评审
评审依据:质量手册、控制计划 检查表A-4
3.3过程流程图
列出过程变化的原因(人、机、料、 法、环)
为PFMEA和控制计划的输入 检查表A-6
3.4场地平面布置图
什么是多方论证小组?小组应包括 哪些方面的人员?
APQP产品质量先期策划和控制计划(ppt 118页)

生产---对发生在批量生产过程中的产品/过程特性、过
2020/8/10
11
概述(续)
程控制、试验和测量系统的综合描述。
3.8 问题的解决 APQP的过程是解决问题的过程; 解习问题可用职责---时间矩阵表形成文件; 遇到困难情况下,推荐使用论证的问题---解决方
法; 可使用附录B中的分析技术。 3.9 产品质量时间计划 APQP小组在完成组织活动后的第一件工作
目的是尽早促使高质量产品实现生产;
小组保证其他领域/小组的计划和活动支持共同的目标。
3.7 控制计划
控制计划---控制零件和过程的系统的书面描述。每个 控制计划包括三个阶段:
样件---对发生在样件制造过程中的尺寸测量、材料与 性能试验的描述;
试生产---对发生在样件之后,全面生产之前的制造过 程中的尺寸测量、材料和性能试验的描述;
产品质量先期策划和控制计划 (APQP)
刘焕明
2020/8/10
1
目录
一、概述 1.什么是APQP 2.APQP的益处 3.APQP的基础 4.常用的分析技术 5.APQP进度图 6.产品质量策划循环 7.产品质量策划责任矩阵图 8.APQP与QSR 9.APQP与防错
2020/8/10
缺陷预防依靠---产品设计和制造技术的同步工程;
2020/8/10
14
概述(续)
策划小组应准备修改产品策划计划以满足顾客期望;
策划小组的责任---确保进度满足或超出顾客的要求。
4 常用的分析技术(附录B)
装配产生的变差分析
基准确定
因果图
特性矩阵图
关键路径法
试验设计(DOE)
可制造性和装配性设计
3.2 确定范围 最重要的指:识别顾客需要、期望和要求。 具体内容包括: 确定小组负责人; 确定各成员职责; 确定内\外顾客;
2020/8/10
11
概述(续)
程控制、试验和测量系统的综合描述。
3.8 问题的解决 APQP的过程是解决问题的过程; 解习问题可用职责---时间矩阵表形成文件; 遇到困难情况下,推荐使用论证的问题---解决方
法; 可使用附录B中的分析技术。 3.9 产品质量时间计划 APQP小组在完成组织活动后的第一件工作
目的是尽早促使高质量产品实现生产;
小组保证其他领域/小组的计划和活动支持共同的目标。
3.7 控制计划
控制计划---控制零件和过程的系统的书面描述。每个 控制计划包括三个阶段:
样件---对发生在样件制造过程中的尺寸测量、材料与 性能试验的描述;
试生产---对发生在样件之后,全面生产之前的制造过 程中的尺寸测量、材料和性能试验的描述;
产品质量先期策划和控制计划 (APQP)
刘焕明
2020/8/10
1
目录
一、概述 1.什么是APQP 2.APQP的益处 3.APQP的基础 4.常用的分析技术 5.APQP进度图 6.产品质量策划循环 7.产品质量策划责任矩阵图 8.APQP与QSR 9.APQP与防错
2020/8/10
缺陷预防依靠---产品设计和制造技术的同步工程;
2020/8/10
14
概述(续)
策划小组应准备修改产品策划计划以满足顾客期望;
策划小组的责任---确保进度满足或超出顾客的要求。
4 常用的分析技术(附录B)
装配产生的变差分析
基准确定
因果图
特性矩阵图
关键路径法
试验设计(DOE)
可制造性和装配性设计
3.2 确定范围 最重要的指:识别顾客需要、期望和要求。 具体内容包括: 确定小组负责人; 确定各成员职责; 确定内\外顾客;
APQP产品质量先期策划和控制计划概述

Threats)
2023/12/28
34
APQP阶段1:计划和确定项目
PLAN AND DEFINE PROGRAM
产品/过程指标 关键术语和基本概念
何为指标
-- 用于识别可供比较的标准的系统性方法,提 出可测量的性能目标
-- 包括世界水平或最优水平的识别
一种能成功地实施下列活动的方法
-- 识别合适的基准
2023/12/28
20
典型的开发三部曲
2023/12/28
21
工具/文件联接
顾客需求 设计特性
潜在需求和/约束
过程特性
过程流程
特性矩阵
DFMEA
PFMEA
测量系统分析
控制计划
2023/12/28
过程能力
SPC
过程指导书 22
APQP 阶段
• 阶段1 计划和确定项目 • 阶段2 产品设计和开发验证 • 阶段3 过程设计和开发验证 • 阶段4 产品和过程确认 • 阶段5 反馈、评定和纠正措施
2023/12/28
5
质量策划循环 PDCA
• PLAN 首先改善你的操作,通过找出事件中存在的问题( 确定应着手的问题点),得出解决这次问题的方案
• DO 首先在小范围内改变设定去解决问题,在测试中判定 这一改变是否可行
• CHECK 判定所希望的效果达成与否,同时,继续确定变 动因素,从而判定任何可能出现的问题
2023/12/28
8
小组组成
多功能小组 • 工程(典型的领导者) • 质保 • 采购 • 工程制造 • 原料控制 • 销售/营销
资源 可能包括顾客和供应商的参与
2023/12/28
9
确定范围
2023/12/28
34
APQP阶段1:计划和确定项目
PLAN AND DEFINE PROGRAM
产品/过程指标 关键术语和基本概念
何为指标
-- 用于识别可供比较的标准的系统性方法,提 出可测量的性能目标
-- 包括世界水平或最优水平的识别
一种能成功地实施下列活动的方法
-- 识别合适的基准
2023/12/28
20
典型的开发三部曲
2023/12/28
21
工具/文件联接
顾客需求 设计特性
潜在需求和/约束
过程特性
过程流程
特性矩阵
DFMEA
PFMEA
测量系统分析
控制计划
2023/12/28
过程能力
SPC
过程指导书 22
APQP 阶段
• 阶段1 计划和确定项目 • 阶段2 产品设计和开发验证 • 阶段3 过程设计和开发验证 • 阶段4 产品和过程确认 • 阶段5 反馈、评定和纠正措施
2023/12/28
5
质量策划循环 PDCA
• PLAN 首先改善你的操作,通过找出事件中存在的问题( 确定应着手的问题点),得出解决这次问题的方案
• DO 首先在小范围内改变设定去解决问题,在测试中判定 这一改变是否可行
• CHECK 判定所希望的效果达成与否,同时,继续确定变 动因素,从而判定任何可能出现的问题
2023/12/28
8
小组组成
多功能小组 • 工程(典型的领导者) • 质保 • 采购 • 工程制造 • 原料控制 • 销售/营销
资源 可能包括顾客和供应商的参与
2023/12/28
9
确定范围
APQP内容介绍PPT课件

输出
试生产 测量系统评价 初始过程能力研究 生产件批准 生产确认试验 生产控制计划 质量策划认定和管理者支持
第15页/共21页
四、APQP具体内容-产品和过程确认-输出
1、试生产:应采用正式生产工装、设备、环境(包括生产操作者)、设施和循环时间 来进行试生产 。 2、测量系统评价 :针对测量系统的有效性和稳定性进行评价。 3、初始过程能力研究 :PPK 4、生产件批准 :确认由正式生产工装和过程制造出来的产品是否满足工程要求 。 5、生产确认试验 :确认由正式生产工装和过程制造出来的产品是否满足工程标准的 工程试验 。 6、包装评价 :所有的试装运(可行的情况下)和试验方法都应评价产品免受在正常运 输中损伤和在不利环境下受到保护,顾客规定的包装不排除APQP小组对包装方法的 评价 。 7、生产控制计划 :是对控制零件和过程的体系的书面描述。 8、质量策划认定和管理者支持 :FORMEL-Q&2DP。
第9页/共21页
四、APQP具体内容-产品设计和开发-输出
1、新设备、工装和设施要求 :包括能力要求及时间要求。 2、产品和过程特殊特性: 应形成产品和过程特殊特性的清单。 3、量具/试验设备要求:包括能力要求及时间要求。 4、小组可行性承诺和管理者的支持 :小组应确保所提出的设计能按预定的时间以 顾客可接受的成本付诸于制造、装配、试验、包装和足够数量的交货。
第16页/共21页
试生产 针对测量方法、测量人、测量环境、测量标准的评价
过程稳定性的评价 自制件及外购件的认可
各试验项目的认可 对包装防护效果的评价
过程的质量控制计划
第17页/共21页
四、APQP具体内容-反馈、评定和纠正措施
产品策划不随过程确认和就绪而终止 。
APQP经典培训资料(PPT 143页)

汽车行业特点-高附加值
时间与进度 稳定的好产品 一致的好产品 信心保证
产品 APQP 进度图表
概念 提出/批准
项目批准
样件
试生产
投产
策划
产品设计和开发. 过程设计和开发
产品和过程确认
反馈、评定和纠正措施
策划 生产
计划和确 定项目
产品设计 和开发
过程设计 和开发
产品和过程 确认
反馈、评定 和纠正措施
2、确定范围(即应明确的有关事项)
在策划的最开始阶段,项目小组重要的是识别 顾客需要、期望和要求。小组必须召开会议,应明 确如下的事项: 1)确定项目小组各成员的职责和作用; 2)识别顾客——内部和外部; 3) 确定顾客的要求; 4)理解顾客的要求和期望; 5)评定所提出来的设计、性能要求和制造过程的可行性,形 成《新产品制造可行性报告》; 6)确定成本、进度和必须考虑的限制条件,形成相应文件; 7)明确需要的来自顾客的帮助; 8)确定文件化的过程或方法。
产品质量先期策划 和控制计划
(Advanced Product Quality Planning and Control Plan)
APQP&CP
本课程主要内容:
一、什么是APQP; 二、为什么要进行APQP; 三、何时进行APQP; 四、APQP的职责范围; 五、APQP的基本原则; 六、APQP的五个过程。
反馈、评 定与纠正
措施
里程碑 概念 项目
样件
试生产
投产
计划情况 实际完成情况
任务栏中有“◇”标识为关键点
六、APQP的五个过程
APQP策划包括5个过程和49项输入和输出: 所有的输入和输出都是建议性的; 输入和输出应根据产品、过程和顾客满意
《APQP培训资料》PPT大纲

制定生产控制计划,明确关键控制点和检验标准 。
过程设计和开发阶段
01
进行过程能力分析,确保生产过程的能力满足设计要求。
02
开发生产工装和夹具,确保生产效率和产品质量。
03
通过以上三个阶段的实施,APQP旨在确保产品在设计和生产过程中充分满足 顾客需求,减少浪费和返工,提高产品质量和生产效率。同时,APQP也强调 跨部门协作和团队合作,以确保项目的顺利实施和成功完成。
03
APQP的关键点和注意事项
有效的项目管理和团队沟通
项目计划制定
确立明确的项目目标、时间表和资源需求,确保项目顺利进行。
团队组织结构和角色分配
明确各个团队成员的职责和权限,促进团队协作和沟通。
有效的沟通渠道
建立定期的项目会议、进度报告和沟通渠道,确保项目信息在团队 内部及时传递。
设计和开发过程中的灵活性和变更管理
目标
03
04
05
确保产品设计满足顾客 需求和期望。
通过早期识别潜在问题 ,减少后期更改和浪费 。
促进跨部门团队合作, 确保整个产品实现流程 中的质量。
APQP的重要性和意义
重要性 提高产品质量,减少缺陷和召回。
降低成本,通过减少浪费和返工。
APQP的重要性和意义
• 增强顾客满意度,确保产品满足或超越顾客期望。
阶段目标:完成产 品设计,确保满足 顾客需求和期望。
设计产品功能和性 能,确保满足顾客 要求。
进行设计评审,确 保设计的可行性、 可制造性和可测试 性。
过程设计和开发阶段
• 阶段目标:确定生产流程,确保高效、稳定地生 产出满足设计要求的产品。
过程设计和开发阶段
主要任务
设计生产过程,包括工艺流程、设备布局、人员 配置等。
过程设计和开发阶段
01
进行过程能力分析,确保生产过程的能力满足设计要求。
02
开发生产工装和夹具,确保生产效率和产品质量。
03
通过以上三个阶段的实施,APQP旨在确保产品在设计和生产过程中充分满足 顾客需求,减少浪费和返工,提高产品质量和生产效率。同时,APQP也强调 跨部门协作和团队合作,以确保项目的顺利实施和成功完成。
03
APQP的关键点和注意事项
有效的项目管理和团队沟通
项目计划制定
确立明确的项目目标、时间表和资源需求,确保项目顺利进行。
团队组织结构和角色分配
明确各个团队成员的职责和权限,促进团队协作和沟通。
有效的沟通渠道
建立定期的项目会议、进度报告和沟通渠道,确保项目信息在团队 内部及时传递。
设计和开发过程中的灵活性和变更管理
目标
03
04
05
确保产品设计满足顾客 需求和期望。
通过早期识别潜在问题 ,减少后期更改和浪费 。
促进跨部门团队合作, 确保整个产品实现流程 中的质量。
APQP的重要性和意义
重要性 提高产品质量,减少缺陷和召回。
降低成本,通过减少浪费和返工。
APQP的重要性和意义
• 增强顾客满意度,确保产品满足或超越顾客期望。
阶段目标:完成产 品设计,确保满足 顾客需求和期望。
设计产品功能和性 能,确保满足顾客 要求。
进行设计评审,确 保设计的可行性、 可制造性和可测试 性。
过程设计和开发阶段
• 阶段目标:确定生产流程,确保高效、稳定地生 产出满足设计要求的产品。
过程设计和开发阶段
主要任务
设计生产过程,包括工艺流程、设备布局、人员 配置等。
APQP管理程序PPT课件
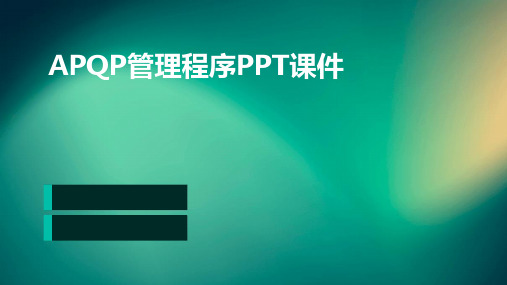
APQP管理程序PPT课件
contents
目录
• APQP概述 • APQP管理程序的核心要素 • APQP管理程序的实施步骤 • APQP管理程序的效益与挑战 • APQP管理程序的应用案例
01 APQP概述
APQP的定义与重要性
定义
APQP(Advanced Product Quality Planning)是一种先进的产品质量策 划方法,旨在确保产品在设计和开发 阶段就达到高质量标准。
跟踪项目进度,确保项 目按计划进行,及时调
整计划以应对变化。
评估项目风险
识别项目潜在的风险, 制定应对措施,降低风
险对项目的影响。
设计与开发
01
02
03
04
需求分析
明确产品或过程的需求,分析 用户期望和竞争对手表现。
设计概念
根据需求分析,提出设计概念 ,确定产品的主要特性和功能
。
设计评估
对设计进行评估和优化,确保 设计满足要求,提高产品的可
供应商改进
与供应商合作,提高供应商的 质量和交货能力,降低采购成
本。
制造与装配
工艺流程设计
根据产品设计,制定制造工艺流程,确保生 产过程的顺畅。
制造与装配
按照工艺流程进行制造与装配,确保产品质 量和生产效率。
生产准备
准备生产所需的设备、工具、材料等资源, 确保生产线的正常运行。
生产监控与改进
监控生产过程的质量和效率,及时调整工艺 参数,提高生产线的性能。
竞争力。
案例三
总结词
机械制造行业是传统制造业的重要组成 部分,APQP管理程序的应用能够帮助机 械制造企业提高产品质量和生产效率, 降低生产成本。
VS
contents
目录
• APQP概述 • APQP管理程序的核心要素 • APQP管理程序的实施步骤 • APQP管理程序的效益与挑战 • APQP管理程序的应用案例
01 APQP概述
APQP的定义与重要性
定义
APQP(Advanced Product Quality Planning)是一种先进的产品质量策 划方法,旨在确保产品在设计和开发 阶段就达到高质量标准。
跟踪项目进度,确保项 目按计划进行,及时调
整计划以应对变化。
评估项目风险
识别项目潜在的风险, 制定应对措施,降低风
险对项目的影响。
设计与开发
01
02
03
04
需求分析
明确产品或过程的需求,分析 用户期望和竞争对手表现。
设计概念
根据需求分析,提出设计概念 ,确定产品的主要特性和功能
。
设计评估
对设计进行评估和优化,确保 设计满足要求,提高产品的可
供应商改进
与供应商合作,提高供应商的 质量和交货能力,降低采购成
本。
制造与装配
工艺流程设计
根据产品设计,制定制造工艺流程,确保生 产过程的顺畅。
制造与装配
按照工艺流程进行制造与装配,确保产品质 量和生产效率。
生产准备
准备生产所需的设备、工具、材料等资源, 确保生产线的正常运行。
生产监控与改进
监控生产过程的质量和效率,及时调整工艺 参数,提高生产线的性能。
竞争力。
案例三
总结词
机械制造行业是传统制造业的重要组成 部分,APQP管理程序的应用能够帮助机 械制造企业提高产品质量和生产效率, 降低生产成本。
VS
APQP培训课件ppt
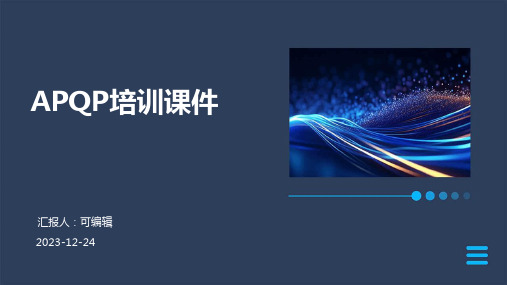
SPC(统计过程控制)
总结词
通过收集和分析数据,监控生产过程,识别异常波动,并采 取措施保持过程的稳定。
详细描述
SPC是一种过程控制工具,通过收集和分析数据来监控生产 过程中的关键特性。它可以帮助识别异常波动,判断过程是 否处于受控状态,并采取相应的措施来调整过程参数,确保 过程的稳定性和产品质量的可靠性。
品质量策划方法。
发展趋势
随着数字化和智能化技术的发展 ,APQP正在向数字化、智能化 方向发展,例如通过数据分析和 人工智能技术来提高产品质量策
划的效率和准确性。
02
APQP实施流程
阶段1:产品设计和开发
总结词:明确产品需求和 目标
确定产品需求和客户期望 。
进行初步设计和工程分析 。
详细描述
制定产品设计方案和目标 。
在项目早期对需求进行确认和冻结,减少后期更改和成 本。
问题三:过程控制不足
• 总结词:过程控制不足可能导致产品质量 不稳定、生产效率低下和不符合预期目标 。
问题三:过程控制不足
详细描述 缺乏有效的过程控制机制,无法确保生产过程的稳定性和一致性。
缺乏对生产过程的监控和记录,导致问题难以追溯和解决。
问题四:供应商问题
• 总结词:供应商问题可能导致供应链不稳定、产品质量下降 和项目进度延误。
问题四:供应商问题
详细描述
供应商交货不及时,影响项目进度和生产计划。
供应商产品质量不符合要求,导致产品性能下降 或不合格率增加。
问题四:供应商问题
• 供应商价格过高或成本不可控,增加项目成本和利 润压力。
评估设计方案的可行性和 可靠性。
阶段2:产品和过程确认
总结词:验证产品和过程的可 行性