焙烧炉热平衡分析与节能措施讨论
焙烧炉节能措施分析
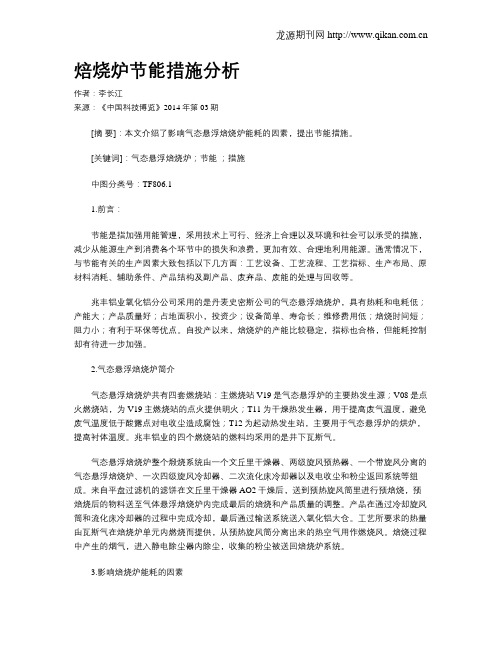
焙烧炉节能措施分析作者:李长江来源:《中国科技博览》2014年第03期[摘要]:本文介绍了影响气态悬浮焙烧炉能耗的因素,提出节能措施。
[关键词]:气态悬浮焙烧炉;节能;措施中图分类号:TF806.11.前言:节能是指加强用能管理,采用技术上可行、经济上合理以及环境和社会可以承受的措施,减少从能源生产到消费各个环节中的损失和浪费,更加有效、合理地利用能源。
通常情况下,与节能有关的生产因素大致包括以下几方面:工艺设备、工艺流程、工艺指标、生产布局、原材料消耗、辅助条件、产品结构及副产品、废弃品、废能的处理与回收等。
兆丰铝业氧化铝分公司采用的是丹麦史密斯公司的气态悬浮焙烧炉,具有热耗和电耗低;产能大;产品质量好;占地面积小,投资少;设备简单、寿命长;维修费用低;焙烧时间短;阻力小;有利于环保等优点。
自投产以来,焙烧炉的产能比较稳定,指标也合格,但能耗控制却有待进一步加强。
2.气态悬浮焙烧炉简介气态悬浮焙烧炉共有四套燃烧站:主燃烧站V19是气态悬浮炉的主要热发生源;V08是点火燃烧站,为V19主燃烧站的点火提供明火;T11为干燥热发生器,用于提高废气温度,避免废气温度低于酸露点对电收尘造成腐蚀;T12为起动热发生站,主要用于气态悬浮炉的烘炉,提高衬体温度。
兆丰铝业的四个燃烧站的燃料均采用的是井下瓦斯气。
气态悬浮焙烧炉整个煅烧系统由一个文丘里干燥器、两级旋风预热器、一个带旋风分离的气态悬浮焙烧炉、一次四级旋风冷却器、二次流化床冷却器以及电收尘和粉尘返回系统等组成。
来自平盘过滤机的滤饼在文丘里干燥器AO2干燥后,送到预热旋风筒里进行预焙烧,预焙烧后的物料送至气体悬浮焙烧炉内完成最后的焙烧和产品质量的调整。
产品在通过冷却旋风筒和流化床冷却器的过程中完成冷却,最后通过输送系统送入氧化铝大仓。
工艺所要求的热量由瓦斯气在焙烧炉单元内燃烧而提供,从预热旋风筒分离出来的热空气用作燃烧风。
焙烧过程中产生的烟气,进入静电除尘器内除尘,收集的粉尘被送回焙烧炉系统。
阳极焙烧炉节能降耗的对策(1)(1)

阳极焙烧炉节能降耗的对策唐林、高守磊(索通发展股份有限公司山东德州251500)摘要:焙烧炉经过4年以上运行后,炉室密封不好,漏风系数高,造成燃料利用效率低,能耗高,制品温度下降,影响了产品质量。
本文从改进焙烧工艺以及焙烧操作等方面采取相应的对策,改善焙烧炉保温措施,降低焙烧炉燃料消耗、提高焙烧产品质量。
关键词:焙烧炉;燃料利用效率;产品质量METHODS TO IMPROVE FUEL UTILIZATION FOR OPEN TOPANODE BAKING FURNACESLin Tang,Shoulei GaoSunstone Development Co.,Ltd,Shandong Dezhou251500Abstract t:As a baking furnace ages,cracks and openings develop in the furnace Abstracwhich allow outside air to enter.Unless proper corrective actions are implemented, gas consumption can increase,final baking temperatures can decrease,and baked anode properties can deteriorate.In this paper,methods are presented for improving the efficiency of fuel utilization for aging furnaces,and thereby lowering fuel consumption,while maintaining or improving anode finishing temperatures and anode properties.Keywords:Baking furnace,Fuel utilization,Products quality一、前言铝用预焙阳极生产过程中,焙烧是最后和最重要的工序之一[1]。
氧化铝焙烧项目节能分析

氧化铝焙烧项目节能分析首先,节能分析需要从设备方面入手。
氧化铝焙烧设备主要包括烧结机、窑灶和烟气处理系统。
对于烧结机,可以通过优化烧结机结构设计,改进燃料供给方式,提高燃烧效率,减少能源浪费。
而对于窑灶,可以通过加强隔热措施,减少热损失。
此外,烧结机和窑灶的运行维护也需要合理规范,确保设备的正常运行,提高设备利用率。
其次,节能分析需要从能源方面入手。
氧化铝焙烧过程中主要使用的能源是煤炭和天然气。
为了节约能源,可以采取以下措施:一是改进燃料选择和供应方式,选择高热值、低硫和低氮的燃料,减少废气的排放;二是优化燃料燃烧过程,提高燃烧效率,减少能源浪费;三是使用余热回收技术,将烟气余热用于预热燃料或提供热能给其他工艺流程,提高能源利用效率。
再次,节能分析需要从工艺方面入手。
氧化铝焙烧工艺中,热交换是一个重要环节。
通过合理设计热交换器,提高热交换效果,减少热能的浪费;同时,还可以采用节能型的辅助设备,如高效的风机和泵等,减少能耗。
另外,还可以优化生产计划,减少停炉、开炉的次数,提高生产过程的稳定性,降低能耗。
最后,节能分析还需要从管理方面入手。
在氧化铝焙烧项目中,建立完善的能源管理体系是非常重要的。
通过制定能源消耗标准、能源消耗指标和能源消耗限额,建立能耗监测和统计体系,对能源消耗进行监控和分析,及时发现问题并采取相应的措施。
此外,还要加强员工的能源管理培训,提高员工的节能意识,形成全员参与、共同节能的氛围。
综上所述,氧化铝焙烧项目的节能分析涉及设备、能源、工艺和管理等多个方面。
通过优化设备结构和运行维护,选择合适的燃料和提高燃烧效率,加强热交换和使用节能型设备,建立完善的能源管理体系等措施,可以实现氧化铝焙烧过程的节能降耗。
焙烧炉节能措施分析
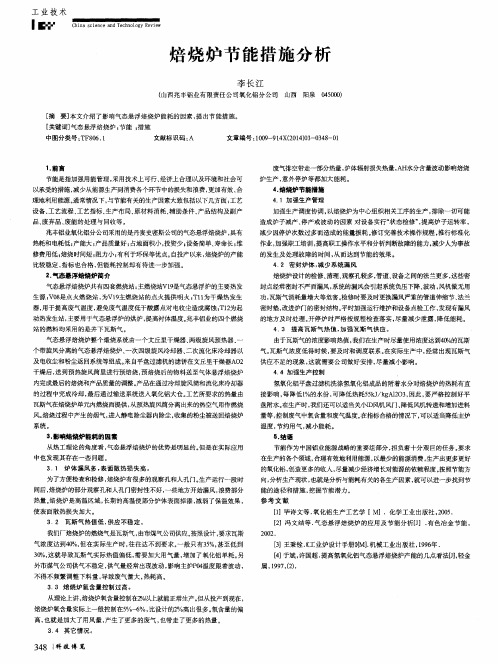
3 . 影响焙 烧 炉能 耗的 因素
工 业技 术
I ■
C h i n aቤተ መጻሕፍቲ ባይዱ s c i e n c e a n d T e c h n o l o g y R e v i e w
焙 烧 炉 节 能措 施 分 析
李长 江
( 山西 兆 丰铝业 有 限责 任 公司 氧化 铝分 公 司 山西 [ 摘 要] 本 文介 绍 了影响 气态 悬浮 焙烧 炉能 耗 的 因素 , 提 出节 能措施 。 [ 关键 词] 气 态悬 浮焙 烧炉 ; 节能 ; 措 施
系统
4 . 焙烧炉节能措施
4 . 1加 强生产 管理
加强 生产调 度协调 , 以焙烧 炉为 中心组 织相 关工序 的生产 , 排 除一切 可能 造成炉 子减 产 、 停产 或波动 的因素 对设备 实行 “ 状 态检 修” , 提 高炉 子运 转率 , 减 少 因停炉 次数过 多而 造成 的能量 损耗 。 修订 完善 技术操 作规 程 , 推行标 准化
封点经常密封不严而漏风, 系统的漏风会引起系统负压下降、 波动 , 风机做无用
功, 瓦斯气 消耗量增 大等苊 害 。 检 修时要 及时更换 漏风严重 的管道 伸缩节 、 法 兰 密封 垫 , 改进 炉 门的密封结 构 。 平 时加强 运行维 护和设备 点检工作 , 发 现有漏 风 的地 方及 时处 理 。 开停 炉 时严格 按规 程检 查落 实 , 尽量 减少 泄露 , 降低能 耗 。
节能 是指 加强用 能管 理 , 采用技术 上 可行 、 经济上 合理 以及环 境和社 会 可
以承受的措施, 减少从能源生产到消费各个环节中的损失和浪费, 更加有效、 合
理 地利 用能源 通常情 况下 , 与节 能有 关 的生产 因素大致包 括 以下 几方面 : 工 艺 设备 、 工 艺流程 、 工 艺指 标 、 生产布 局 、 原材 料消 耗 、 辅助条 件 、 产 品结构及 副产 品、 废弃 品 、 废 能的 处理 与回 收等 。 兆 丰铝 业氧 化铝分公 司采用 的是丹麦 史密 斯公司 的气态悬浮 焙烧炉 , 具有 热耗 和电耗低 ; 产 能大 ; 产品质量 好 ; 占地 面积小 , 投资少 ; 设备 简单 、 寿命 长 ; 维 修费 用低 , 焙烧 时间短 ; 阻力小 ; 有 利于环保 等优点 。 自投产 以来 , 焙烧 炉的产 能 比较稳定 , 指标 也合格 , 但能耗 控制 却有 待进 一步 加强 。 2 . 气态 悬 浮焙烧 炉简 介 气态悬 浮焙烧 炉共有 四套燃 烧站 : 主燃烧 站V1 9 是气 态悬浮 炉 的主 要热 发 生源; V 0 8 是点火 燃烧 站 , 为V1 9 主 燃烧 站的 点火 提供 明火 ; T 1 1 为干 燥热 发生 器, 用于 提高废 气 温度 , 避免废 气温 度低于 酸露 点对 电收尘造成 腐蚀 ; T 1 2 为起 动 热发生 站 , 主要 用于 气态悬浮 炉的烘炉 , 提 高衬体温 度。 兆 丰铝业 的 四个 燃烧 站 的燃料 均 采用 的是 井下 瓦斯 气 。 气态悬 浮焙烧 炉 整个煅烧 系统 由一个 文丘 里干燥 器、 两级旋 风预 热器 , 一 个 带旋 风分 离的气 态悬 浮焙烧 炉 、 一次 四级旋 风冷 却器 、 二次 流化 床冷却器 以 及 电收尘 和粉尘 返回系 统等组成 。 来 自平盘 过滤机 的滤饼在 文丘里 干燥器 A O 2 干 燥后 , 送 到预 热旋风 筒里进 行预 焙烧 , 预焙 烧后 的物料 送至 气体 悬浮焙 烧炉 内完成最 后的焙烧 和产 品质量的调 整 。 产 品在通 过冷却旋 风筒和 流化床冷 却器 的过程 中完 成冷 却 , 最后通 过输送 系统 送人 氧化铝 大仓 工 艺所要 求的 热量 由 瓦斯气在 焙烧炉 单元 内燃烧而提供 , 从 预热旋 风筒分离 出来的热 空气用作 燃烧 风。 焙烧 过程 中产生 的烟气 , 进入静 电 除尘器 内除尘 , 收集 的粉尘 被送 回焙 烧炉
炭素焙烧炉改造节能减排分析
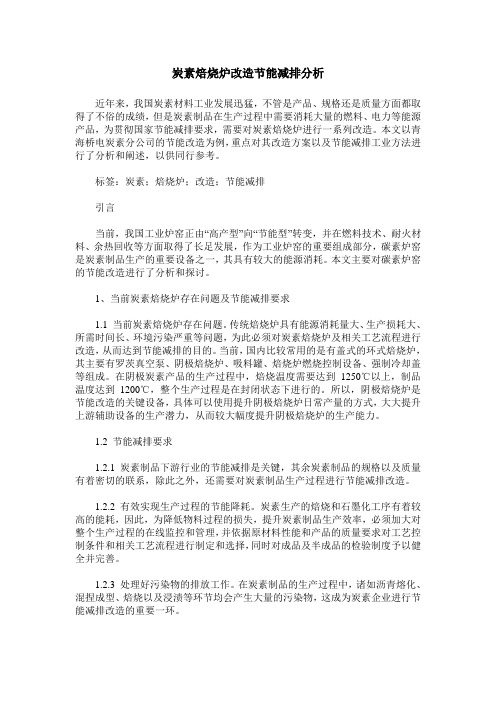
炭素焙烧炉改造节能减排分析近年来,我国炭素材料工业发展迅猛,不管是产品、规格还是质量方面都取得了不俗的成绩,但是炭素制品在生产过程中需要消耗大量的燃料、电力等能源产品,为贯彻国家节能减排要求,需要对炭素焙烧炉进行一系列改造。
本文以青海桥电炭素分公司的节能改造为例,重点对其改造方案以及节能减排工业方法进行了分析和阐述,以供同行参考。
标签:炭素;焙烧炉;改造;节能减排引言当前,我国工业炉窑正由“高产型”向“节能型”转变,并在燃料技术、耐火材料、余热回收等方面取得了长足发展,作为工业炉窑的重要组成部分,碳素炉窑是炭素制品生产的重要设备之一,其具有较大的能源消耗。
本文主要对碳素炉窑的节能改造进行了分析和探讨。
1、当前炭素焙烧炉存在问题及节能减排要求1.1 当前炭素焙烧炉存在问题。
传统焙烧炉具有能源消耗量大、生产损耗大、所需时间长、环境污染严重等问题,为此必须对炭素焙烧炉及相关工艺流程进行改造,从而达到节能减排的目的。
当前,国内比较常用的是有盖式的环式焙烧炉,其主要有罗茨真空泵、阴极焙烧炉、吸料罐、焙烧炉燃烧控制设备、强制冷却盖等组成。
在阴极炭素产品的生产过程中,焙烧温度需要达到1250℃以上,制品温度达到1200℃,整个生产过程是在封闭状态下进行的。
所以,阴极焙烧炉是节能改造的关键设备,具体可以使用提升阴极焙烧炉日常产量的方式,大大提升上游辅助设备的生产潜力,从而较大幅度提升阴极焙烧炉的生产能力。
1.2 节能减排要求1.2.1 炭素制品下游行业的节能减排是关键,其余炭素制品的规格以及质量有着密切的联系,除此之外,还需要对炭素制品生产过程进行节能减排改造。
1.2.2 有效实现生产过程的节能降耗。
炭素生产的焙烧和石墨化工序有着较高的能耗,因此,为降低物料过程的损失,提升炭素制品生产效率,必须加大对整个生产过程的在线监控和管理,并依据原材料性能和产品的质量要求对工艺控制条件和相关工艺流程进行制定和选择,同时对成品及半成品的检验制度予以健全并完善。
浅谈焙烧炉的节能途径

浅谈焙烧炉的节能途径张卿轩(中国铝业广西分公司,广西 平果 531400)摘 要:氢氧化铝焙烧是氧化铝生产的最后一道工序。
其能耗约占氧化铝生产工艺能耗的10%。
煅烧工艺的生产能力直接影响着氧化铝企业的整体生产能力。
气体悬浮焙烧炉(G.S.C.)是当前最普遍应用的煅烧设备,如何充分发挥焙烧炉的性能,对于降低氧化铝生产能耗有着积极作用。
关键词:气态悬浮焙烧炉;节能技术改造;氧化铝生产中图分类号:TQ151 文献标识码:A 文章编号:11-5004(2018)05-0031-2氢氧化铝焙烧是氧化铝生产的最后一步。
其原理是通过高温焙烧去除氢氧化铝中的水和结晶水,转化生产合格的氧化铝以满足电解生产的要求的过程。
因此,氢氧化铝焙烧工艺是为铝电解生产提供冶金氧化铝材料的关键[1]。
1 气态悬浮焙烧炉的生产原理来自平盘过滤机的氢氧化铝经过皮带的输送,首先进入小料仓L01,经由可调转速的皮带称F01称重后经过中转皮带F02、再由喂料螺旋A01送入文丘里干燥器A02进行干燥,干燥后的氢氧化铝被送到预热旋风筒P01、P02里进行预焙烧,预焙烧后的物料送至气体悬浮焙烧炉(焙烧炉)P04内完成最后的焙烧,经过P03进行产品质量的调整后,生成的产品依次通过冷却旋风筒C01、C02、C03、C04与冷空气进行热交换实现降温,从冷却旋风筒出来的氧化铝最后进入流化床冷却器K01、K02实现最后的冷却,温度低于80℃的氧化铝经由风动溜槽、氧化铝输送皮带被送入氧化铝大仓进行存储或者包装。
工艺所要求的热量由煤气在焙烧炉单元内燃烧而提供,从冷却旋风筒分离出来的热空气用作燃烧风[2]。
焙烧过程中产生的烟气,进入静电除尘器内除尘后由烟道排出,收集的粉尘被送回焙烧炉系统。
静电收尘及返灰系统包括静电收尘器P11、料封泵、返灰风机和返灰管道,其作用是对烟气净化,将烟气中的粉尘由返灰系统收集送回焙烧炉系统,避免污染同时减少氧化铝损失。
流程如图1所示。
焙烧炉能耗分析与优化

焙烧炉能耗计算与分析陆敏,吴海文中国铝业广西分公司,广西 百色 531400摘要:焙烧炉的能源消耗在生产消耗中占有较大的比重,通过对焙烧炉的热平衡计算,分析影响焙烧炉能耗的几个因素,并提出了进一步降低能源消耗的主要途径。
关键词:焙烧炉;能耗;热平衡1.前言氧化铝生产中,焙烧过程最常用的设备主要有气体悬浮焙烧炉、回转窑等。
其中气体悬浮焙烧炉以工艺的先进性和能源的高效利用在行业有广泛的应用。
目前气体悬浮焙烧炉的燃料采用重油等液态燃料或者发生炉煤气、天然气等气体燃料,采用多级换热的方式对热量进行梯级回收,能源转换效率高(见图1)。
但是,受世界范围内能源紧缺的制约,如何进一步降低焙烧炉的能源消耗,是节约能源的一个重要发展方向。
2.焙烧炉热平衡计算焙烧炉的热量主要来源于燃料(本文中以发生炉煤气进行计算)燃烧提供的热量。
产生的热量主要用来提供氢氧化铝转变成氧化铝所需要的化学能以及结晶水、附着水气化所需要的能量,最终以烟气和焙烧氧化铝为载体将热量带出系统,还有少量能量通过设备表面辐射、换热的形式流失。
通过热平衡计算,可得到各种热支出的分布情况。
以我厂的1#焙烧炉为例,采用发生炉煤气作为燃料。
原始条件如下(2011年):空气AO 出料图1 焙烧炉工艺简图表1 焙烧炉操作条件进料量 进料附水 进料温度 煤气流量 煤气温度 剩余氧含量106t/h2.60%61℃ 33420Nm3 34℃2.20%表2 煤气成分在热平衡计算中,氢氧化铝的反应热可根据下面的公式计算:)()1001868.42.191001868.43.117821000γα⋅⨯+⋅⨯⋅⨯⋅=M Q式中, M —干氢氧化铝量, kg/t.AO ;α—成品氧化铝中 -Al2O3的质量分数,%;γ—成品氧化铝中 -Al2O3的质量分数,%;78—氢氧化铝的分子量,g/mol ;11.3×4.1868—2mol 氢氧化铝反应生成 -Al2O3的吸热量,kJ/mol ; 19.2×4.1868—2mol 氢氧化铝反应生成 -Al2O3的吸热量,kJ/mol 。
降低焙烧炉能耗提高经济效益
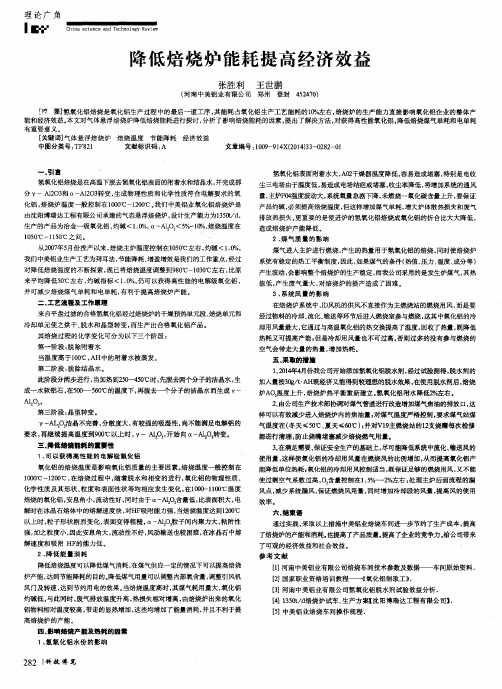
A L O 3 。
第 三 阶段 : 晶型转 变 。 Y— AL ) 0 洁 晶不完善 , 分散 度大 , 有 较强 的吸 湿性 , 尚不能 满足 电解铝 的
却用风量最大, 它通过与高温氧化铝的热交换提高了温度, 回收了热量, 既降低 热耗又可提高产能 ・ 但是冷却用风量也不可过高. 否则过多的没有参与燃烧的
空气会 带走 大量 的热 量 , 增 加热耗 。
五 采取的措施
1 、 2 0 l 4 = q 1 4 月份 我公司开 始添 加氢氧 化铝脱水 剂 , 经过试验 测得 , 脱水 剂的
1 0 5 0 " C- 1 1 5 0 ℃ 之间 。
从2 0 0 7 年5 月份投产以来, 焙烧主炉温度控制在1 0 5 0 " C左右 , 灼碱<1 . 0 %, 我们中美铝业生产工艺为拜耳法 , 节能降耗、 增盈增效是我们的工作重点, 经过
对 降低焙 烧温 度的 不断探 索 , 现 已将焙 烧温度 调整 到9 8 0 " ( 2 -1 0 3 0 " ( 2 左右 , 比原 来 平均 降低 5 0 " ( 2 左右, 灼碱 指标 <1 . O %, 仍可 以获得 高性 能 的电解级 氧化 铝 ,
理论广角
I ■
降 低 焙 烧 炉 能耗 提 高 经 济 效 益
张胜 利 王世鹏
( 河南中美铝业有限公司 郑州
登封 4 5 2 4 7 0 ) 要】 氢 氧化 铝 焙烧 是氧 化铝 生产 过程 中的最后 一道 工序 , 其 能耗 占氧 化铝 生产 工艺 能耗 的 1 0 %2  ̄ 右, 焙烧 炉 的生产 能力 直接 影 响氧化 铝 企业 的整 体产 能和经济效益。 本文对气体悬浮焙烧炉降低焙烧能耗进行探讨 , 分析了影响焙烧能耗的因素, 提 出了解决方法 , 对获得高l 『 生能氧化铝, 降低焙烧煤气单耗和 电单耗 有 重要 意义 。 [ 关键词 ] 气体 悬 浮焙 烧 炉 焙烧 温 度 节能 降耗 经济 效益 中 图分类 号 : T F 8 2 1 文献标 识码 : A 文章 编号 : 1 0 0 9 — 9 1 4 X( 2 0 1 4 ) 3 3 — 0 2 8 2 一 O l
- 1、下载文档前请自行甄别文档内容的完整性,平台不提供额外的编辑、内容补充、找答案等附加服务。
- 2、"仅部分预览"的文档,不可在线预览部分如存在完整性等问题,可反馈申请退款(可完整预览的文档不适用该条件!)。
- 3、如文档侵犯您的权益,请联系客服反馈,我们会尽快为您处理(人工客服工作时间:9:00-18:30)。
焙烧炉热平衡分析与节能措施讨论李鹏,孙毅(沈阳铝镁设计研究院有限公司,辽宁沈阳110001)[摘要]焙烧炉是铝用阳极生产过程中耗能较大的设备,通过对其热平衡进行计算与分析,找到其耗能大的影响因素;通过系统的理论分析,给出焙烧炉节能措施;结合实际应用效果,表明本文所述节能措施在实际生产中取得了较好效果。
[关键词]焙烧炉;热平衡;节能[中图分类号]TF806. 1[文献标志码]B[文章编号]1003 -8884(2018)03 -0038 -040 刖言铝电解工业是国家的支柱产业,近两年随着 500 kA、600 k A等大容量预焙电解槽的成功研发和 应用,我国电解铝工业的技术装备水平逐渐接近世 界先进水平。
但是,作为电解铝生产的“心脏”一预焙阳极的生产技术,发展却十分缓慢,存在能耗 高、产品质量差、单位生产能力低、环境污染严重等 问题[1]。
阳极焙烧工艺十分复杂,伴随着焦油不均匀溢 出燃烧、非线性升温控制、间接耦合加热等过程,无 法从单一手段入手,一次性完全解决以上问题。
目前,制约阳极焙烧发展的一个瓶颈问题是阳极焙烧 过程能耗过高,大多数阳极企业焙烧过程每吨阳极 平均能耗[2]为4.2 GJ,是国外同类炉型的1.55〜2.57倍。
对于如此大的能源消耗,如何寻求一种科 学、有效的方法,降低吨阳极能耗,是近年来阳极研 究的主要方向。
本文通过对敞开式阳极焙烧炉进行 热平衡分析,找到其节能潜力所在,指明今后阳极焙 烧炉生产和设计过程中的节能方向。
1热平衡计算与结果分析1.1敞开式阳极焙烧炉热平衡概述长期以来,人们一直在为提高各种用能设备的 效率而努力。
随着人类社会的现代化,能源的消费 量越来越大,供求矛盾十分尖锐。
从目前国内情况[收稿日期]2018 -02 -21[作者简介]李鹏(1986 -),男,辽宁沈阳人,工程师,硕士研究生,主要从事炭素工艺设计与研发工作,现任沈阳铝镁设计研究院有限公司专业副组长。
38来看,持续多年能源紧张,对工农业生产和人民生活 都带来了很大影响。
我国能源利用率较低,管理水 平和工艺设备较落后,节能技术的研究落后于生产 实践的需要等,都说明节能工作的长期性和艰巨性。
那么,热平衡正是对用能情况进行科学的数量分析, 探索能源使用的最优化方法,是做好节能的基础工 作。
阳极焙烧炉作为耗能大户,有必要对其热工工 艺进行分析,编制热平衡,从而找到其节能潜力所 在。
目前,国内对于阳极焙烧炉热平衡在计算和分 析上做了大量工作[3-4],焙烧炉热收入主要包括:燃 料化学热、挥发份燃烧反应热、填充料烧损化学热、炉体初始蓄热量、余热空气带人热、炭块物理热、填 充料物理热等,焙烧炉热支出主要包括:焙烧块带走 热、填充料带走热、烟气带走热、炉体蓄热量、烟气化 学热、炉体散热等。
1.2实例研究以某80室11料箱敞开式阳极焙烧炉为例,编 制其物料平衡和热平衡,计算结果如下:(1) 初始条件实例初始条件包括炉室数,料箱尺寸及控制温 度等,如表1所示。
(2) 物料平衡物料平衡反应物料收入与支出的关系,是衡量 一台炉子物料收支状况的关键,如表2所示。
(3) 热平衡热平衡是衡量一个过程或单体能量收入与支出 的关系,是评价用能情况的关键,如表3所示。
1.3热平衡分析由热平衡计算可知,热收入项主要为挥发份燃表1初始条件烧化学热41郾49%、燃料燃烧化学热30郾27%和预热内容数值空气带入热24郾66% ;热支出主要有焙烧块带走热炉室数/个8035郾84%、炉体蓄热量30郾67%和烟气带走热单个炉室料箱数/个1115郾30%。
单个料箱内阳极数/个21由于焙烧块带走热与生产工艺要求的终了保温料箱尺寸/mm830 x5858 伊6400温度和产量有关,而本文不着重讨论改进生产工艺,横墙长度/mm462所以如何降低此部分热损失暂不讨论。
因此,焙烧单个生块重量/kg1440炉节能应主要从降低炉体蓄热、加强烟气余热回收、单个熟块重量/kg1370提高燃烧效率、减少炉体散热损失等角度考虑。
沥青百分比/%14.52节能措施移炉周期/h32火道保温温度/益1 1602.1降低炉体蓄热损失空气预热温度/益702Q蓄=G伊c伊A t(1)排烟架烟气平均温度/益200式中G—耐火材料重量,kg;燃料天然气C—比热,J/(k g.K);驻t一平均温差,K。
表2物料平衡物料收人物料支出收人项质量/(kg/h)%支出项质量/(k^h)%生块量10 39518.71熟块量9 88917. 80空气量18 19632. 76填充料量 3 8036.85燃气量3630.65烟气量41 85875.35填充料量 3 8526.93漏气量22 74440. 94总量55 550100. 00总量55 550100. 00表3热平衡热收人热支出收人项热量/(kj/h)%支出项热量/(kj/h)%燃料化学热17 799 40030. 27焙烧块带走热21 073 45435. 84挥发份燃烧化学反应热24 394 09541. 49填充料带走热 6 293 82210.71填充料烧损化学热1659 7452.82烟气带走热8 998 54115.30炉体初始蓄热量444 9180.76炉体蓄热量18 032 84330. 67预热空气带入热14 497 95624. 66烟气化学热497 8390.85炭块物理热267 8060.46炉体散热 3 899 6156.63填充料物理热80 4060. 14总量58 796 114100. 00总量58 796 114100. 00对于周期性生产的炉子,每一个加热周期,都伴 位面积的产能一一炉底强度,减少设计过程中吨产随着炉体吸收大量热量,因此,根据公式(1)中决定 品的耐火材料用量;其次需选用较低导热系数的耐蓄热损失的几个因素,降低此热损失,首先需增加单 火材料;最后需调整工艺制度,降低加热过程的温39差。
具体措施如下:(1) 提高料箱的有效容积率,提高单位炉底面 积的炭块堆积量,可以考虑将传统的料箱堆块方式 (三层)改为三层立装、一层卧装的“三加一”堆块 模式;(2) 减小料箱和火道尺寸,优化炉体结构,在满 足火道整体负压的前提下,优先采用较小宽度的火道设计;(3)合理选用耐火材料,科学设计耐火材料厚 度,在保证炉体的强度和耐高温条件下,尽量使用导 热系数小的轻质耐火材料,最大限度减少炉墙的热量损失。
2.2减少炉体散热损失炉体散热损失取决于炉体表面积、表面温度和 综合对流换热系数,其中综合对流换热系数是对流 换热系数和辐射换热系数的耦合值,影响因素较多, 不在本文研究范围之内,所以减少炉体散热损失,主 要从降低表面温度和炉体表面积两个角度考虑。
具 体措施如下:(1)采用保温性能较好的保温材料,同时注意 炉底的强制通风冷却,降低炉体表面温度;(2) 除通过优化炉体设计降低炉体体积外,还 应考虑采用大型焙烧炉设计,可以降低单位产能的 炉体体积,同时可以最大限度的减少边火道数量,因 为通过大量实际测量,发现边火道热损失较大,是造 成焙烧炉能耗高的主要原因。
2. 3减少炉体漏风敞开式焙烧炉漏风现象较为明显,其主要源于 火道在大负压操作下,空气通过填充料缝隙进而穿 过火道竖缝深入火道或直接通过火道上部观察孔和 侧墙缝隙流入火道内。
漏风一方面造成了冷空气取 代预热空气燃烧,降低了燃烧温度和燃烧效率,另一 方面降低了火道和阳极炭块温度,由于燃烧过程控 制是依据目标温度调节燃料喷入量的控制模式,这 就需要增大燃料喷入量来维持目标温度,造成更多 的燃料损失。
具体措施如下:(1)预热炉室上表面铺设塑料薄膜,阻止冷空 气从料箱内渗入火道,同时在排烟架后的横墙上设置密封挡板,较少火道间的漏风;(2) 优化侧墙设计,通过侧墙上部的收缩缝外 移,与侧墙下部的收缩缝错开,采用迷宫式方式进行 密封,减少收缩缝孔隙的漏风量,提高侧墙上部的密40封效果。
(3)优化炉体上部浇注块结构,采用小孔浇注 块,降低了炉面温度,较少了漏风。
2.4提高燃烧效率对于敞开式阳极焙烧炉,充分有效的利用燃料固有的能量,以求单位产品消耗最少的燃料,所以应从燃烧工艺曲线和燃烧装置两方面考虑。
具体措施如下:(1)燃烧工艺控制采用预热区高速率升温线辅助以加热区低保温温度、长保温时间的工艺控制方式,预热区测温测压架终温控制在720益左 右,加热区保温温度降低至1 130〜1 150益,延长 保温时间至64〜68 h ,提高成品在加热区的温度 均匀性;(2)采用不等周期移炉的操作方法,提前16 h 先移动排烟架,充分利用高温烟气余热加热 炭块,然后移动其他燃控设备,加热区由7室转回 6室运行。
用此方法可充分利用烟气中的余热,提 高预热段料箱炭块温度水平,降低焙烧炉能耗水平;(3) 优化燃烧自动控制系统。
由于敞开式烧炉烧嘴调节是一个非常复杂的工作,采用人工 调节无法满足工艺要求的稳定性和准确性,所以 通过自动控制技术,实现准确、平稳和适时地控制 和调节焙烧过程。
因此,采用P ID 控制模块,将多 火道负压均衡控制模型、燃烧多点稳定控制模型 及冷却自平衡控制模型应用到燃烧自动控制系统 中,如图1所示。
2. 5能耗效果通过以上关于敞开式阳极焙烧炉的节能分 析,成功的将节能方法应用于某一大型阳极企业的72室14料箱的阳极焙烧炉上,取得了较好的节 能效果,焙烧车间2016年8月至2016年10月的 能耗统计结果如图2所示。
从图2中可以看出,该 阳极焙烧炉的能耗控制在40〜55 Nm 3/t .阳极,折 合每吨阳极能耗约为1. 42〜1. 95 GJ ,达到世界领先的水平。
3结语炉体蓄热损失在阳极焙烧炉热支出中所占比重较大,其应成为焙烧炉节能的主要突破口。
同时,经 过实践证明,采用本文关于敞开式阳极焙烧炉的过程优化层图1阀位压I 力。
1iunn过程控制层2016-2016- 2016- 2016- 201608-01 08-1508-29 09-1209-26日期图2某企业焙烧车间能耗统计Discussion on Heat Balance Analysis and Energy SavingMeasures of Baking FurnaceLI Peng, SUN YiAbstract : The baking furnace is the equipment that consumes more energy in the anode productionprocess of aluminum , the influence factors of its energy dissipation are found based on the heat balance calculation and analysis , the energy saving measures are given through the theoretical analysis of the sys tem ,and the practical application results show that the energy-saving measures in this paper have a chieved good results in practical production .Key words : baking furnace;heat balance;energy saving蒉燃烧自动控制系统模块节能措施,可以将焙烧炉的能耗控制在1. 42〜1. 95GJ /t .阳极,达到世界领先的水平。