挤压机预应力框架压柱变形原因分析
压铸产品变形原因分析及系统改善

压铸产品变形原因分析及系统改善一、目的通过对铸铝产品在生产过程中压铸变形原因的分析,从中找出影响产品品质的主要因素,为后期系统性改善提供基础,从而达到提高产品品质,降低生产成本的目的。
二、各种变形原因分析及解决方案:1 成型不良1.1外观特征(CHARACTER):金属液充满型腔,铸件表面有不规则的孔洞、凹陷或棱角不齐,表面形状呈自然液流或舆液面相似。
1.2产生原因(REASON):1)内浇道宽度不够或压铸模排气不良。
2)合金流动性差。
3)浇注温度低或压铸模温度低,压射速度低。
4)压射比压不足。
5)压铸型腔边角尺寸不合理、不易填充。
6)喷水太多或没吹干。
1.3防止方法(METHOD OF IMPROVEMRNT)1)改进内浇道,改进排气条件,适当提高压铸模温度和浇注温度。
2)提高压射比压和压射速度。
3)注意喷水量适当且注意吹干。
2 变形2.1外观特征(CHARACTER):铸件歪(弯)曲,超出图纸公差。
2.2产生原因(REASON):(1)铸件结构不合理,各部收缩不均匀。
(2)开模时间太短。
(3)顶出过程铸件偏斜,受力不均。
(4)必要时可以进行整(校)形。
(5)堆放不合理或去除浇口不当。
2.3防止方法(METHOD OF IMPROVEMENT):(1)改进铸件结构,使铸件壁厚均匀。
(2)不要堆栈存放,特别是大而薄的铸件。
(3)加强刚性。
注意开模时间以及顶出时间和顶出速度的调整。
(4)铸件刚性不够。
3 顶针凸凹3.1外观特征(CHARACTER):顶针位凸出、凹入铸件表面。
3.2产生原因(REASON):(1)顶针长短配置不合理。
(2)修省出模难处。
(3)模具局部温度过高,顶针易卡。
3.3防止方法(METHOD OF IMPROVEMENT):(1)顶针长短要配置合理。
(2)模具局部温度偏高需多喷水,降低模温。
(3)模具局部出模困难。
4 冷格4.1外观特征铸件表面有不规则的明显下陷线形纹路,多出现在离浇口较远区域,对各种零件产生于一定部位。
钢结构柱弯曲变形
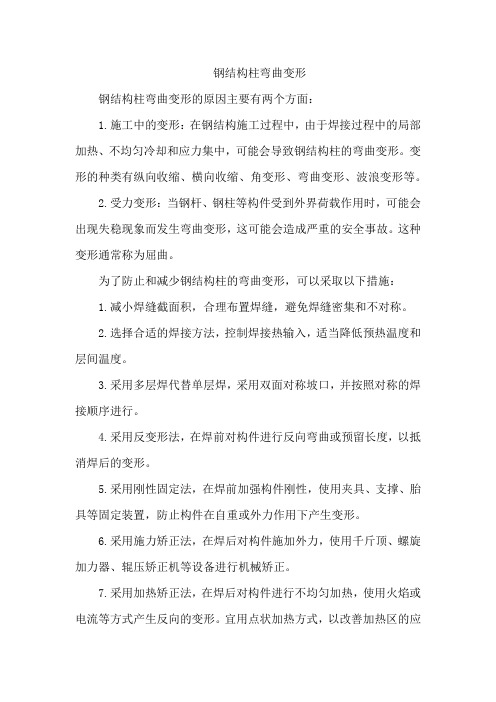
钢结构柱弯曲变形
钢结构柱弯曲变形的原因主要有两个方面:
1.施工中的变形:在钢结构施工过程中,由于焊接过程中的局部加热、不均匀冷却和应力集中,可能会导致钢结构柱的弯曲变形。
变形的种类有纵向收缩、横向收缩、角变形、弯曲变形、波浪变形等。
2.受力变形:当钢杆、钢柱等构件受到外界荷载作用时,可能会出现失稳现象而发生弯曲变形,这可能会造成严重的安全事故。
这种变形通常称为屈曲。
为了防止和减少钢结构柱的弯曲变形,可以采取以下措施:
1.减小焊缝截面积,合理布置焊缝,避免焊缝密集和不对称。
2.选择合适的焊接方法,控制焊接热输入,适当降低预热温度和层间温度。
3.采用多层焊代替单层焊,采用双面对称坡口,并按照对称的焊接顺序进行。
4.采用反变形法,在焊前对构件进行反向弯曲或预留长度,以抵消焊后的变形。
5.采用刚性固定法,在焊前加强构件刚性,使用夹具、支撑、胎具等固定装置,防止构件在自重或外力作用下产生变形。
6.采用施力矫正法,在焊后对构件施加外力,使用千斤顶、螺旋加力器、辊压矫正机等设备进行机械矫正。
7.采用加热矫正法,在焊后对构件进行不均匀加热,使用火焰或电流等方式产生反向的变形。
宜用点状加热方式,以改善加热区的应
力状态。
请注意,以上措施在具体实施时应根据实际情况进行调整和优化。
压力容器制造过程中变形问题的控制对策分析

压力容器制造过程中变形问题的控制对策分析压力容器是工业生产中不可或缺的设备之一,它的制造涉及到多个工艺环节,其中变形问题在制造过程中不可避免。
变形问题严重影响了产品的质量,更具有安全隐患。
因此,通过对变形问题进行分析与控制,对提高产品质量和安全性具有重要作用。
压力容器的变形问题主要包括壁厚偏差、圆度误差、直线度误差、端面平行度误差等。
造成变形问题的原因主要有以下几方面:一是材料本身的特点,不同的材料在受到外力或加工过程中的变形特点不同。
例如铝合金的塑性大,容易产生变形。
二是制造工艺的工艺参数调节不当。
例如,焊接温度过高或者过低,焊接速度过快或者过慢,焊接角度不合适,都会导致容器的变形。
三是生产设备的问题。
设备的精度不高、设备的磨损以及设备的调试不当等问题都可能导致容器的变形。
针对以上问题,可以采取以下控制对策:一是合理选材。
生产压力容器需要选用合适的材料,合理控制材料的性能,以减小变形的发生。
二是严格控制生产工艺。
生产中需要对工艺参数进行严格控制,对于焊接温度、速度、角度、压力等参数进行监测和控制。
三是加强设备维护。
坚持定期检修、保养,确保设备正常操作,从而保证生产过程中的精度和稳定性。
四是应用数控技术。
数控技术可以大大提高生产过程中的精度和稳定性,减小变形的产生。
总之,控制压力容器制造中的变形问题是提高产品质量和安全性的有效措施。
只有在加强材料选择、严格控制生产工艺、加强设备维护和应用数控技术等方面,才能减小变形的产生,保证产品的质量和安全性。
挤压变形过程应力分布

挤压变形过程应力分布引言挤压变形是一种重要的金属加工工艺,通过挤压金属材料可以改变其形状和结构,使其具备所需的力学性能。
在挤压变形过程中,所施加的应力分布对于成品的质量和性能至关重要。
本文将探讨挤压变形过程中的应力分布情况,详细分析挤压变形过程中各个阶段的应力分布特点。
挤压变形过程概述挤压变形是指通过挤压机将金属坯料挤压至模具中,通过模具的形状和尺寸来实现所需形状和尺寸的加工过程。
挤压变形过程可分为预留段、施加最大载荷段、减载段和释放段等多个阶段。
挤压变形过程应力分布分析预留段在预留段,金属坯料开始进入模具,因受到模具壁的约束,坯料的横向膨胀受到限制,导致坯料材料内部产生剪应力。
同时,坯料上、下端面受到挤压机针尖的约束,产生法向压力。
在预留段,应力分布主要集中于坯料的边缘区域,较小的应力分布于坯料的中心部分。
施加最大载荷段当施加最大载荷后,坯料被挤压进一步塑性变形,在此阶段,应力分布更加均匀。
在横截面上,靠近模具边缘的区域应力较大,而靠近中心轴线的区域应力较小。
在轴向方向,较靠近挤压机针尖的区域应力较大,而靠近挤压机进料端的区域应力较小。
减载段减载段是指在达到最大压力后,开始减小压力以实现坯料产生塑性变形的过程。
在减载段,应力分布开始发生变化。
模具边缘区域的应力开始减小,而中心轴线附近的应力增加,这是由于模具边缘区域的材料首先失去强度。
释放段在释放段,挤压机不再施加压力,坯料开始回弹。
此时,应力分布开始恢复到变形前的状态,模具边缘区域的应力较小,中心轴线附近的应力逐渐减小。
挤压变形过程应力分布的影响因素挤压变形过程的应力分布受到多个因素的影响,包括坯料的材料性质、变形速度、变形温度等。
•材料性质:不同材料的应力分布特点不同,具体表现在屈服强度、韧性等方面。
某些材料可能在变形过程中出现局部应力集中现象,需要采取合适的工艺措施来避免产生缺陷。
•变形速度:变形速度的增加会导致应力分布的改变,快速变形更容易产生较大的应力集中。
液压支架立柱损坏原因分析与预防措施

)*+,-.. 型 立 柱 外 径 理 论 计 算 壁 厚 :
#<
$# 451/(/. < < /14 ! "" > $ /14 & /..>451/
( !" ) (实 际 壁 厚 ) A/1/,!" B强 度 足 够 。 -15-
)*+,-.. 型 立 柱 中 缸 理 论 计 算 壁 厚 :
#<
$# 3.(-3 < < /14 ! "" > $ /14 & /..>3.
E E
F
F
G ’) 9)
G
/) 立 柱 的 稳 定 性 验 算
设计人员在立柱的设计及验算过程中,一般将 立柱考虑为两端铰接,无偏心载荷等截面细长杆受 轴向载荷的情况,在这里我们略去活柱与小导向套 间隙的影响, 将活柱和中缸视为一体, 受纵向压力来 研究其稳定性。 无 偏 心 载 荷 时 的 纵 向 弯 曲 极 限 力 $’ 的 计 算 : 计 算 柔 度 %: ’1 以 )*+,-.. 立 柱 为 研 究 对 象 ,
! " # ) $ *& % & ’ (
的好坏,对井下工作面的顶板维护和安全生产起着 极其重要的作用, 因此, 找出立柱的损坏原因, 使损 坏降低到最低点, 有着十分重要的意义。 液压支架的 立柱结构有单伸缩型、 双伸缩型、 单伸缩带机械加长 段型三种, 由于双伸缩立柱最具有代表性, 故本文仅 以双伸缩立柱为研究对象, 根据各种损坏形式, 找出 其损坏原因, 提出预防措施。
*%
"
立柱损坏原因分析 从多年的支架大修中发现,每套支架大修时立
压铸件变形的解决措施是什么
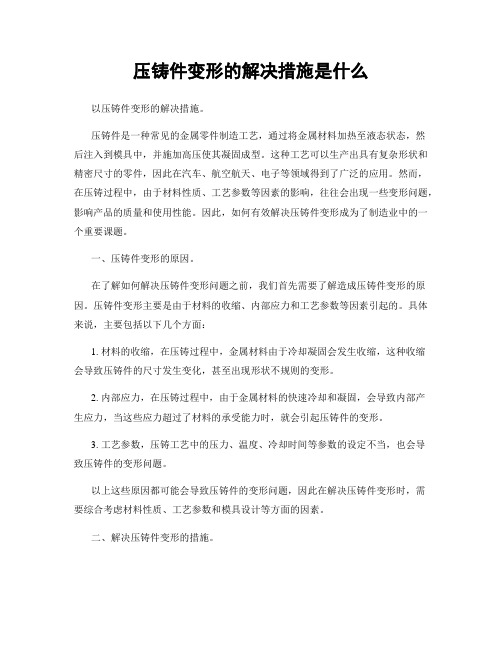
压铸件变形的解决措施是什么以压铸件变形的解决措施。
压铸件是一种常见的金属零件制造工艺,通过将金属材料加热至液态状态,然后注入到模具中,并施加高压使其凝固成型。
这种工艺可以生产出具有复杂形状和精密尺寸的零件,因此在汽车、航空航天、电子等领域得到了广泛的应用。
然而,在压铸过程中,由于材料性质、工艺参数等因素的影响,往往会出现一些变形问题,影响产品的质量和使用性能。
因此,如何有效解决压铸件变形成为了制造业中的一个重要课题。
一、压铸件变形的原因。
在了解如何解决压铸件变形问题之前,我们首先需要了解造成压铸件变形的原因。
压铸件变形主要是由于材料的收缩、内部应力和工艺参数等因素引起的。
具体来说,主要包括以下几个方面:1. 材料的收缩,在压铸过程中,金属材料由于冷却凝固会发生收缩,这种收缩会导致压铸件的尺寸发生变化,甚至出现形状不规则的变形。
2. 内部应力,在压铸过程中,由于金属材料的快速冷却和凝固,会导致内部产生应力,当这些应力超过了材料的承受能力时,就会引起压铸件的变形。
3. 工艺参数,压铸工艺中的压力、温度、冷却时间等参数的设定不当,也会导致压铸件的变形问题。
以上这些原因都可能会导致压铸件的变形问题,因此在解决压铸件变形时,需要综合考虑材料性质、工艺参数和模具设计等方面的因素。
二、解决压铸件变形的措施。
针对压铸件变形的原因,我们可以采取一系列的措施来解决这一问题,主要包括以下几个方面:1. 合理选择材料,在进行压铸件的材料选择时,需要考虑材料的收缩率、热膨胀系数等因素,选择合适的材料可以降低压铸件的收缩变形。
2. 优化工艺参数,在压铸过程中,通过合理调整压力、温度、注射速度等工艺参数,可以减小内部应力的产生,降低压铸件的变形。
3. 设计合理的模具,模具的设计对于压铸件的质量和形状有着重要的影响,合理设计模具可以减小压铸件的收缩变形,减少内部应力的产生。
4. 采用热处理工艺,通过对压铸件进行热处理,可以消除内部应力,提高材料的稳定性,减少变形问题的发生。
压力容器制造过程中变形问题的控制对策分析

压力容器制造过程中变形问题的控制对策分析
压力容器是一种高强度的金属结构,被广泛应用于石油、化工、能源等领域。
在压力容器制造过程中,会面临变形问题。
变形会影响容器的性能和使用寿命,严重时会导致容器破裂发生危险事故。
因此,控制压力容器制造过程中的变形问题是非常重要的。
变形问题的主要原因有:
1.材料性质不均匀。
由于金属材料的制造过程中难免存在缺陷或变异,会导致容器在制造过程中产生变形。
2.热应力。
在焊接过程中,因为局部加热和冷却速度的不同,容易引起变形。
3.机械应力。
在制造过程中的加工和组装过程中,机械加工力和装配力等容易引起变形。
针对这些原因,可以采取以下控制对策:
1.选择合适的材料。
可以选择性能稳定、变异小的材料,如使用各种标准化的板材和管材进行制造。
2.采用热处理工艺。
可以采用预热、后热、回火等热处理工艺,消除焊接过程中的热应力,保证容器的稳定性。
3.优化焊接工艺。
可以采用多层多道焊接和逐层平整的方法,控制热量输入和冷却速度,减少焊接变形。
4.合理设计加工和组装工艺。
在制造过程中,可以根据容器的形状、大小等特点,选择合适的加工和组装工艺,避免机械应力对容器造成影响。
5.控制制造精度。
可以采用数控机床、自动焊接等先进设备,控制制造误差,保证容器精度。
总的来说,控制压力容器制造过程中的变形问题是需要广泛关注的,通过科学、合理的控制对策来实现,可以有效的保证容器的稳定性和安全性。
装配式建筑施工中的变形与结构调整

装配式建筑施工中的变形与结构调整随着现代建筑技术的不断发展,装配式建筑在市场上得到了越来越广泛的应用。
装配式建筑具有快速、高效、环保等优势,然而,在施工过程中往往存在着一些变形问题,需要进行结构调整。
本文将探讨在装配式建筑施工中的变形问题以及相应的结构调整方法。
一、装配式建筑中的变形问题:1. 热胀冷缩引起的变形:由于温度的变化会导致材料膨胀和收缩,从而引起施工过程中的变形问题。
特别是在装配式建筑中,由于组件之间的连接点较多且材料种类多样,因此热胀冷缩带来的影响更为复杂。
2. 水平荷载引起的变形:装配式建筑在运输和安装过程中可能会受到水平荷载的作用,例如地震、风力等。
这些水平荷载会对建筑产生弯曲和扭转等变形影响。
3. 装修材料收缩引起的变形:在装配式建筑中,装修材料的种类多样,而不同材料的收缩系数也各不相同。
这就需要在施工过程中进行合理控制和调整,以避免装修材料收缩引起的变形问题。
二、装配式建筑中的结构调整方法:1. 优化设计:在装配式建筑施工前,对结构进行优化设计是预防变形问题的重要手段。
通过使用现代的计算机辅助设计软件,可以模拟不同条件下的变形情况,并进行相应调整。
2. 强度分析与加固措施:在面对装配式建筑施工中可能会发生的荷载和变形问题时,需要进行强度分析,并采取相应的加固措施。
例如增加梁柱连接点刚性、加大构件厚度等方法可以有效地提高结构的稳定性。
3. 温度控制与隔热保温:针对热胀冷缩引起的变形问题,在施工过程中可以采取一些温度控制和隔热保温措施。
例如设置伸缩缝、使用合理温度感应材料等方法可以有效减少热胀冷缩带来的影响。
4. 拼装精度控制:装配式建筑中,各构件之间的连接是非常重要的。
因此,在施工过程中需要严格控制拼装精度,确保构件之间的连接紧密且准确,避免由于不良连接引起的变形问题。
5. 采用预压技术:在装配式建筑施工中,可以采用预压技术来消除构件之间的间隙,提高结构整体的稳定性。
通过预先施加适当的压力,可以有效地减少后期变形和松动现象。
- 1、下载文档前请自行甄别文档内容的完整性,平台不提供额外的编辑、内容补充、找答案等附加服务。
- 2、"仅部分预览"的文档,不可在线预览部分如存在完整性等问题,可反馈申请退款(可完整预览的文档不适用该条件!)。
- 3、如文档侵犯您的权益,请联系客服反馈,我们会尽快为您处理(人工客服工作时间:9:00-18:30)。
第54卷第1期锻压装备与制造技术 2019年2月Vol. 54 No. 1CHINA METALFORMING EQUIPMENT & MANUFACTURING TECHNOLOGY Feb. 2019挤压机预应力框架压柱变形原因分析王艳鹏(太重(天津L滨海重型机械有限公司,天津300452)摘要:挤压机预应力框架是承受挤压力最基本构件,框架的变形直接影响挤压制品质量。
挤压机在安装调试后要对压机施加不同 工作载荷进行压力试验,同时对两根下压柱在不同工作载荷下的变化情况进行测量,依据测量数据发现变形趋势,本文通过压柱 和拉杆之间的变形关系,前、后梁受力变形情况,整体框架变形情况几个方面,利用力学理论进行变形原因分析。
结果表明:在工 作载荷下压柱外侧导轨面向内弯曲,上导轨面向上弯曲是符合理论设计要求的。
关键词:挤压机;预应力框架;拉杆;压柱;弯曲变形中图分类号f TB375 文献标识码:AD01:10.16316/j.issn.l672-0121.2019.01.013 文章编号:1672-0121(2019)01-0050-03挤压机框架是一个封闭的组合结构,主要由前、后梁、挤压梁和4根压柱组成简称三梁四柱,它是承受挤压力的最基本的构件。
组合框架目前常见的有两种形式,一种是带钩头的厚板叠加成的预应力拉杆和受压柱套组合机架;另一种是圆柱形拉杆和受压柱套组合机架[1],见图1所示。
无论哪种结构,都是通过前梁外侧用预紧专用工具对张力柱加载预紧力使其拉伸,同时压柱受压,整个框架处于预应力的状态。
由于预应力结构框架能大大压机的承载能力,,预应力组合框架其结构成为压机的常用结构[2]。
拉杆后梁压柱前梁图1预应力组合框架形式目前挤压机框架的受力析都是以传统理论计算(利用理论或经式)和有结合的 。
本 是通过和结构力析一 的原因。
收稿日期/ 2018-10-08 ]修订日期:2018-11-20作者简介:王艳鹏1979-),男,工程师,技术科长,从事挤压机、锻造 压机研发及制造。
E-m ail:wypmike_197913@ 1压力试验过程及数据采集1.1压力试验方法由于挤压机四根压柱不仅承受压力,两根下压柱 挤压梁和挤压的 ,承载件的,压柱是 挤压的 ,所压力 两 压柱同工 载 的 形情况。
以20MN挤压机为例,首先在两根下压柱导轨侧面及上面选择测试点,导轨侧面选3个点,导轨上面选3个点,其中一^后梁、另一^ 中间部位、最后一前梁,具体位置见图2所示。
每个用 ,机外的 架 ,受外。
图2压力试验测量点位置图1.2数据采集,后对挤压机加不同的工作载荷,分别是15MPa、28M P a和29.4MPa,保压5min,观察百分表数值变化并进行记录,记录的数值见1所示。
卸载后,百分表数值都能 。
根据数据分析,两根压柱在不同的工 载 都 侧 ,向上弯曲的现象。
是什么原因导致了压柱产生这种-50-王艳鹏:挤压机预应力框架压柱变形原因分析第1期表1压力试验数据记录表(mm)测试15MPa28MPa29.4MPa侧面面侧面面侧面面-0.07+0.08-0.19+0.14-0.19+0.16左下压柱2-0.10+0.08-0.20+0.22-0.20+0.223-0.0++0.09-0.19+0.16-0.20+0.H-0.09+0.05-0.18+0.11-0.17+0.16右下压柱2-0.14+0.10-0.22+0.20-0.25+0.203-0.07+0.10-0.21+0.15-0.19+0.14变形趋势呢?本文通过下面的论述进行分析。
2变形原因分析挤压机预应力框架是由前、后梁、四根压柱和四根拉杆组成,拉杆穿过前、后梁和压柱的孔,拉杆两端用螺母将其紧固为整体框架。
对拉杆预紧后,压柱的全长及前、后梁和螺母贴合处承受压应力,拉杆承受拉应力。
在施加载荷时,前、后梁和压柱都承受着挤压应力和弯矩的作用。
一般情况下,实际预紧应力应大于工作应力,这样挤压机工作时螺母与梁之间在着一的应力,框架为一个整体,增 加了设备的整体刚度[3]。
由于挤压机框架结构是对称于中间平面的,且偏心载荷不大,为便于分析,假载荷对称于中平面或轴对称,框架为平面框架[4]。
2.1压柱和拉杆的变形关系拉杆和压柱的预应力是在弹性范围内施加的,拉杆预紧力与变形量的合 。
压柱和拉杆的形和受力的 3所示,拉杆受预紧力的拉伸,伸长为!',相反,压柱在!。
的压下,其压为!2。
施加工作载荷!后,拉杆长,压柱之,压着减,为"!。
拉杆拉力!(,压柱的压缩力由!J 至!),!)被称为预紧力。
这时拉杆的拉力是残余预紧力!)与工作载荷!之和。
由 3 ,对于预应力框架的挤压机,工作载荷被分为两部分,拉杆和压柱分担一部分,工作载荷中的拉分由拉杆承,弯 分由压柱承担。
而且预紧力的 框架的和安全性。
预紧力 ,将 前、后梁与压柱的合面预紧力 大,将 拉杆形[5]。
2.2后梁的变形分析后梁工作,挤压机加载时,后梁承受油缸的反作用力。
由于后梁的 大于压柱的,将后梁为 梁,为压柱的中心距。
工作压力 为作用于半圆环重心上的两中力[8]。
根挤压机简化出的后梁受力分、力图及弯, 4 。
!为工作压力,"为工作油缸外径。
根据材料力学分析,后梁沿挤压中心向外弯曲。
F F F F图4后梁受力分布、剪力和弯矩图2.3前梁的变形分析前梁在挤压机加载时,承受的是挤压力,假设挤压力作用在模座与前梁中心形触面的重心上,近似取为"/#,其变形情况与后梁类同,就不再赘述。
2.4整体框架分析将件组合成框架结构,利用预紧力将框架进行预紧后成为预应力组合框架。
对 于预应力组合,在实际工作中梁在弯形,有可能引起压柱角开缝,影响框架整体,为了 确保在种载荷工况下梁柱合面均不开,预紧力是保证整体的决定性因素[7'预紧力选取-51-第54卷锻压装备与制造技术的大小,必须保证在最大工作载荷下,压柱中还存在 一定的压应力。
同时考虑了前、后梁的弯曲变形,承 载后拉杆和压柱均不同程度地发生了弯曲变形,其 变形情况见图5所示。
图中!为工作载荷,为压柱 所承受的压力(残余预紧力),"为前、后梁对压柱产 生的弯矩。
从图中可以看出压柱是向内弯曲的,最大 变形位于中部。
3结论(D 当给整个预应力框架施加工作载荷时,压柱由于压缩力减小,同时受到弯矩的作用,导致压柱侧 导轨面向内弯曲,导向上弯曲。
(2) 压力 的压柱变形趋势。
(3)由于前梁采用非中心对称结构,即左右对称、下非对称,后梁为中心对称结[9],在进行压力时压柱还承载压梁和压的,还受到挤压力偏载因素的影响,所以实测数据变化不是 均。
参考文献:[1]俞新陆•液压机的设计与应用[M].北京:机械工业出版社,2007:590-592.[2]单东生,贾向东,赵长财.全预紧组合框架液压机的预紧力研究[J]•机械工程学报,2015,51 (14): 86-92-[3]卫凌云,张营杰,杜学斌,等6液压机预应力框架预紧方式探讨[J].重型机械,2012 ( 3): 99-102-[4] 魏军.金属挤压机[M].北京:化学工业出版社,2006:193.[5]段志东,苏铁明6组合机架的刚度分析和拉杆预紧力研究[J ].机械科学与技术,2009,28 (4): 450-454.[6] 吴生富.150MN 锻造液压机[M].北京:国防工业出版社,2012: 73.[7]吴生富,金淼,聂绍珉,等.大型锻造液压机全预紧组合机架的整体性及影响因素分析[J ].塑性工程学报,2006,13(2):110-113.[8]董晓传,金淼.预紧组合结构液压机临界预紧力的研究[J ].中国机械工程,2014,25( 9): 1158-1163.[9]石如磐,王勇,王丽薇.36MN 预应力结构挤压机机架变形分析[J]•锻压技术,2011,36(4): 100-103-Analysis of deformation reason for pre-stressed frame columns in extruderWANG Yanpeng(TZ (Tianjin ) Binhai Heavy Machinery Co ., Ltd ., Tianjin 300452, China )Abstract : The pre-stressed frame of the extruder is the most basic component to withstand the pressingforce . The deformation of the frame directly affects the quality of the extruded product . After the installation and commissioning , the extruder should apply different working loads to the press for pressure test . At the same time , the changes of the two lower pressing columns under different working loads have been measured . According to the measured data , the deformation trend has been found . Through the deformation relationship between the pressing column and the tie rod , the deformation of the front and rear beams , and the deforma tion of the overall frame , the deformation reasons have been analyzed in the text by use of mechanical theo ry . The results show that under the working load , the outer rail of the pressing column is curved inward while the upper rail is curved upward , which meets the theoretical design requirements .Key words : Extruder ; Pre-stressed frame ; Rod ; Pressing column ; Bending deformation-52-。