半导体制程简介
半导体制程节点

半导体制程节点,可以看作是摩尔定律下,集成电路芯片集成度大小的一个指标,例如180nm、130nm、90nm、65nm、45nm、28nm、14nm、7nm、5nm、3nm等,这些数字就是表示半导体工艺的"技术节点(technology
node)",也称作"工艺节点"。
长期以来,栅极长度和半间距Half-pitch(芯片上两个相同特征之间的距离的一半)与工艺节点名称相匹配,但最后一次以栅极长度命名是1997年,之后半间距数继续与节点名匹配,但从实际意义上不再与之相关。
但是各个厂家真正的工艺节点发展和规划不一定是完全一致的,有时候芯片厂商为了确保实现制造工艺的平稳过渡,会生产"半节点"产品,所以市场上出现120nm、110nm、80nm、70nm等不符合0.7倍的工艺节点也是常见的。
半导体中段制程-概述说明以及解释

半导体中段制程-概述说明以及解释1.引言1.1 概述概述半导体中段制程是半导体制造过程中的一个重要阶段。
在半导体制造过程中,通常将整个过程分为前段制程、中段制程和后段制程三个阶段。
中段制程是在前段制程完成后,将晶圆表面的介电层、金属层等进行加工和处理的阶段。
在中段制程中,主要涉及到的工艺包括光刻、沉积、刻蚀、清洗等步骤。
光刻是中段制程中的重要步骤之一。
它通过使用光刻胶和掩模光罩,将光刻胶涂覆在晶圆表面上,并通过紫外光照射,将掩模上的图形转移到光刻胶上。
然后,通过化学处理,将光刻胶上未曝光部分或曝光后进行过浸蚀、清洗等处理,最终形成所需的图案。
沉积是中段制程中另一个重要的步骤。
它主要是将金属、介电材料等沉积在晶圆表面,形成所需的层。
常用的沉积方法包括物理气相沉积(PVD)、化学气相沉积(CVD)等,根据不同的材料和需求,选择适合的沉积方法。
刻蚀是中段制程的一项关键步骤,它通过使用化学气相或物理方法,将不需要的材料层进行去除或定义。
刻蚀方法包括湿法刻蚀、干法刻蚀等,根据材料的不同选择不同的刻蚀方式。
清洗是中段制程中不可或缺的一步。
它的主要目的是去除杂质、残留物以及刻蚀产物,保证晶圆表面的纯净度和平整度。
清洗过程主要包括超声清洗、化学清洗等方法。
总之,半导体中段制程是半导体制造过程中至关重要的一步。
通过精确的加工和处理,可以实现对晶圆表面的图案形成和层之间的连接,为后续的工艺步骤打下坚实的基础。
在不断发展的半导体技术中,中段制程的优化和改进对于提高半导体器件的性能和可靠性具有重要意义。
1.2 文章结构文章结构部分的内容可以包括以下内容:在本篇长文中,我们将对半导体中段制程进行详细的探讨和分析。
文章分为引言、正文和结论三个部分。
引言部分首先对半导体中段制程进行概述,包括其定义、作用以及在半导体工业中的重要性。
接着,介绍文章的结构和目的,以及本文所要探讨的主要内容。
正文部分将分为两个要点来详细讨论半导体中段制程。
半导体封装制程及其设备介绍
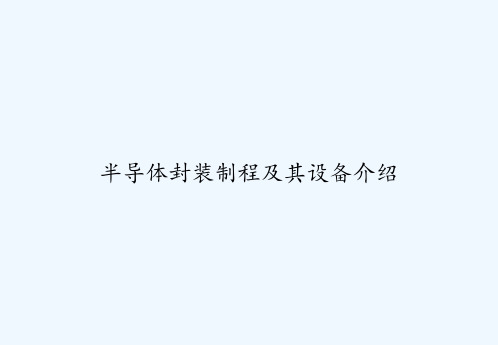
Solder paste
Die Prepare(芯片预处理) To Grind the wafer to target thickness then separate to single chip
---包括来片目检(Wafer Incoming), 贴膜(Wafer Tape),磨片(Back Grind),剥膜(Detape),贴片(Wafer Mount),切割(Wafer Saw)等系列工序,使芯片达到工艺所要求的形状,厚度和尺寸,并经过芯片目 检(DVI)检测出所有由于芯片生产,分类或处理不当造成的废品.
B Wafer roughness Measurement 粗糙度测量仪 主要为光学反射式粗糙度测量方式;
4.Grinding 配套设备
A Taping 贴膜机 B Detaping 揭膜机 C Wafer Mounter 贴膜机
Wafer Taping -- Nitto DR300II
Alignment
1.27, 0.762 mm (50, 30miles)
Ceramic 2, 4 direction lead
20~80
Ceramic
1.27,1.016, 0.762 mm (50, 40, 30
miles)
20~40
大家应该也有点累了,稍作休息
大家有疑问的,可以询问和交流
Surface Mount
半导体设备供应商介绍-前道部分
半导体设备供应商介绍-前道部分
常用术语介绍
1. SOP-Standard Operation Procedure 标准操作手册 2. WI – Working Instruction 作业指导书 3. PM – Preventive Maintenance 预防性维护 4. FMEA- Failure Mode Effect Analysis 失效模式影响分析 5. SPC- Statistical Process Control 统计制程控制 6. DOE- Design Of Experiment 工程试验设计 7. IQC/OQC-Incoming/Outing Quality Control 来料/出货质量检验 8. MTBA/MTBF-Mean Time between assist/Failure 平均无故障工作时间 9. CPK-品质参数 10. UPH-Units Per Hour 每小时产出 11. QC 7 Tools ( Quality Control 品管七工具 ) 12. OCAP ( Out of Control Action Plan 异常改善计划 ) 13. 8D ( 问题解决八大步骤 ) 14. ECN Engineering Change Notice ( 制程变更通知 ) 15. ISO9001, 14001 – 质量管理体系
半导体制程 gd 工艺
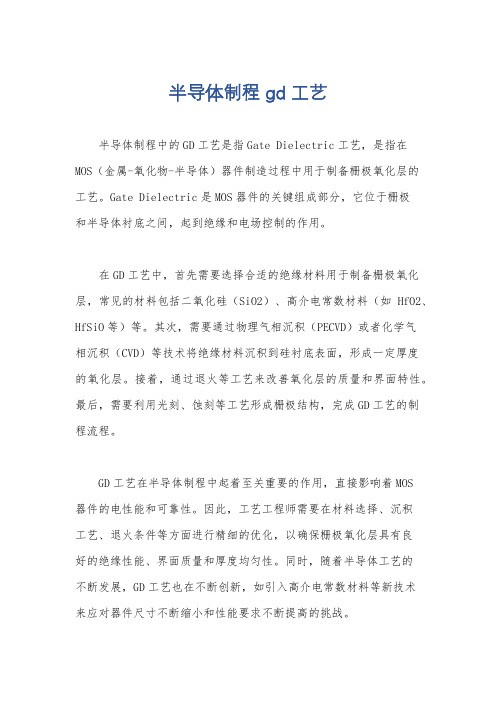
半导体制程 gd 工艺
半导体制程中的GD工艺是指Gate Dielectric工艺,是指在MOS(金属-氧化物-半导体)器件制造过程中用于制备栅极氧化层的
工艺。
Gate Dielectric是MOS器件的关键组成部分,它位于栅极
和半导体衬底之间,起到绝缘和电场控制的作用。
在GD工艺中,首先需要选择合适的绝缘材料用于制备栅极氧化层,常见的材料包括二氧化硅(SiO2)、高介电常数材料(如HfO2、HfSiO等)等。
其次,需要通过物理气相沉积(PECVD)或者化学气
相沉积(CVD)等技术将绝缘材料沉积到硅衬底表面,形成一定厚度
的氧化层。
接着,通过退火等工艺来改善氧化层的质量和界面特性。
最后,需要利用光刻、蚀刻等工艺形成栅极结构,完成GD工艺的制
程流程。
GD工艺在半导体制程中起着至关重要的作用,直接影响着MOS
器件的电性能和可靠性。
因此,工艺工程师需要在材料选择、沉积
工艺、退火条件等方面进行精细的优化,以确保栅极氧化层具有良
好的绝缘性能、界面质量和厚度均匀性。
同时,随着半导体工艺的
不断发展,GD工艺也在不断创新,如引入高介电常数材料等新技术
来应对器件尺寸不断缩小和性能要求不断提高的挑战。
总的来说,GD工艺是半导体制程中至关重要的一环,其制备的栅极氧化层直接影响着器件的电性能和可靠性,因此需要工艺工程师们不断努力和创新,以满足不断发展的半导体市场需求。
积塔半导体 制程

积塔半导体制程积塔半导体制程概述积塔半导体制程是一种用于生产半导体芯片的工艺流程。
在制程中,通过一系列的步骤和工艺,将半导体材料转变为功能完善的集成电路芯片。
这些芯片被广泛应用于各种电子设备中,如计算机、智能手机、电视等。
前期准备工作在进行积塔半导体制程之前,需要进行一系列的前期准备工作。
首先是选择合适的半导体材料,常见的有硅、砷化镓等。
然后,将选定的材料进行切割和抛光,得到所需的晶圆。
接下来,对晶圆进行清洗和去除杂质的处理,以保证制程的顺利进行。
光刻工艺光刻工艺是积塔半导体制程中的关键步骤之一。
在光刻工艺中,首先将光刻胶涂覆在晶圆表面,然后通过光刻机将光刻胶上的图案投射到晶圆上。
这个图案是通过使用掩膜板上的图案进行投射的。
光刻胶的部分被照射后会发生化学反应,形成图案。
通过控制光刻胶的曝光时间和光强度,可以得到所需的图案。
蚀刻工艺蚀刻工艺是制程中的另一个重要步骤。
在蚀刻工艺中,通过将晶圆放置在蚀刻设备中,利用化学气相反应或离子轰击的方式,将光刻胶未被覆盖的部分或者所需蚀刻掉的部分材料去除。
这样就形成了芯片上的各个结构和电路。
沉积工艺沉积工艺是制程中的另一个重要步骤。
在沉积工艺中,通过将晶圆放置在沉积设备中,将所需的材料以气相或液相的形式沉积在晶圆表面。
这样可以形成薄膜或者填充孔隙。
常见的沉积工艺包括化学气相沉积、物理气相沉积和溅射沉积等。
清洗和检测在制程的最后阶段,需要对芯片进行清洗和检测。
清洗是为了去除制程中产生的残留物和杂质,保证芯片的质量。
检测则是为了验证芯片的功能和性能是否符合要求。
常见的检测手段包括电学测试、光学测试和扫描电子显微镜等。
总结通过以上的步骤和工艺,积塔半导体制程可以将半导体材料转变为功能完善的芯片。
这些芯片广泛应用于各个领域,推动了科技的发展和电子设备的普及。
随着技术的不断进步,制程也在不断革新和改进,以满足不断增长的市场需求。
积塔半导体制程将继续发挥重要作用,推动半导体行业的进一步发展。
半导体后端铝制程

半导体后端铝制程摘要:一、半导体后端铝制程概述二、半导体后端铝制程的关键工艺1.化学气相沉积(CVD)2.物理气相沉积(PVD)3.电化学沉积(ECD)4.溅射沉积三、半导体后端铝制程的应用1.芯片制造2.微电子器件3.光学器件四、半导体后端铝制程的发展趋势与挑战1.发展趋势1.高分辨率2.高性能3.绿色环保2.挑战1.技术突破2.成本控制3.环境保护正文:半导体后端铝制程是指在半导体芯片制造过程中,采用铝材料作为导体薄膜的一种关键技术。
半导体后端铝制程在现代电子产业中具有重要地位,广泛应用于芯片制造、微电子器件、光学器件等领域。
本文将简要介绍半导体后端铝制程的概述、关键工艺、应用以及发展趋势与挑战。
一、半导体后端铝制程概述半导体后端铝制程主要包括化学气相沉积(CVD)、物理气相沉积(PVD)、电化学沉积(ECD)和溅射沉积等方法。
在这些方法中,铝薄膜沉积是关键步骤,对半导体器件的性能和可靠性具有重要影响。
二、半导体后端铝制程的关键工艺1.化学气相沉积(CVD):CVD是通过化学反应在半导体基板上形成铝薄膜的一种方法。
CVD制程具有沉积速率快、薄膜厚度均匀等特点,适用于大规模生产。
2.物理气相沉积(PVD):PVD是利用真空蒸发、溅射等技术在半导体基板上沉积铝薄膜的过程。
PVD制程具有薄膜密度高、附着力强等优点,但设备成本较高。
3.电化学沉积(ECD):ECD是通过电解液中将金属离子还原成金属沉积在半导体基板上的方法。
ECD制程具有沉积速度快、薄膜质量好等特点,但工艺复杂、成本较高。
4.溅射沉积:溅射沉积是利用高速氩离子轰击铝靶,将铝原子溅射到半导体基板上形成薄膜的过程。
溅射沉积具有薄膜厚度均匀、结构稳定等优点,但设备成本较高。
三、半导体后端铝制程的应用半导体后端铝制程在现代电子产业中具有重要地位,广泛应用于以下领域:1.芯片制造:铝薄膜作为芯片的导电层,可以提高芯片的导电性能和散热性能。
2.微电子器件:铝制程可以用于制造微电子器件的导电层和互连线。
什么是半导体工艺制程,16nm、10nm都代表了什么
什么是半导体⼯艺制程,16nm、10nm都代表了什么什么是半导体⼯艺制程,16nm、10nm都代表了什么随着智能⼿机的发展,半导体⼯艺也急速提升,从28nm、16nm、10nm到7nm 这些半导体代⼯⼚们每天争相发布最新的⼯艺制程,让很多吃⽠群众⼀脸懵逼不知道有啥⽤。
半导体⾏业离我们似乎很遥远,FinFET是什么东西,EUV⼜是什么新技术,每次看到这种相关的新闻都让我们如同云⾥雾⾥,不知所谓。
其实它离我们很近,⽆论是FinFET还是EUV都是为了完善制程⼯艺所做的努⼒。
⽽⼀款处理器的性能表现、散热效率、功耗等等都和制程息息相关。
今天,我们来聊聊⼿机处理器的这些事。
●16nm、10nm,这些数字到底是啥?说起这个话题,我们要先搞清楚什么是制程。
那些20nm、16nm什么的到底代表了什么。
其实这些数值所代表的都是⼀个东西,那就是处理器的蚀刻尺⼨,简单的讲,就是我们能够把⼀个单位的电晶体刻在多⼤尺⼨的⼀块芯⽚上。
⼿机处理器不同于⼀般的电脑处理器,⼀部⼿机中能够给它留下的尺⼨是相当有限的。
蚀刻尺⼨越⼩,相同⼤⼩的处理器中拥有的计算单元也就越多,性能也就越强。
这也是为何⼚商会频繁强调处理器制程的原因。
同时,因为随着频率的提升,处理器所产⽣的热量也随之提⾼,⽽更先进的蚀刻技术另⼀个重要优点就是可以减⼩晶体管间电阻,让CPU所需的电压降低,从⽽使驱动它们所需要的功率也⼤幅度减⼩。
所以每⼀代的新产品不仅是性能⼤幅度提⾼,同时还有功耗和发热量的降低。
综合以上,可以发现处理器的制程对于⼿机⼗分重要,更⾼的性能带来更流畅的游戏体验,⽽⼀个保持正常温度的机⾝更是能保证⼤家拥有⼀个良好的使⽤体验。
⼀次制程的升级,带来了散热效果与计算性能的双重提升。
半导体封装制程与设备材料知识介绍-FE
半导体封装制程与设备材料知识介绍-FE半导体封装制程是半导体工业中不可或缺的一部分,其随着市场需求的变化不断地在更新换代。
本文将主要介绍半导体封装的制程步骤及相关设备材料知识。
半导体封装制程步骤半导体封装制程主要按照以下步骤进行:1.按照需要封装的芯片布局,设计封装排线和金属引线等结构。
同时,设计封装的外观结构,包括尺寸、形状、数量和分布等。
2.使用设计软件,制作电路图样,该图样包含标准的元器件符号、等电线和连接符等信息。
3.基于制作的电路图样,制作光刻版,在载片上进行银河线蚀刻。
因为光刻版制作的精度较高,可以制作很细的线路和高保真度的图案。
4.将加载的原件(如晶体管芯片等)与抛光后的铜器系排线粘结在一起,其中的薄胶层在压合交联后,铜器系排线被粘在原件表面上。
通过紫外线固化胶水,以确保清洗过程中不再分离。
5.将元器件放入封装内部,并对外壳进行粘接焊接或压力焊接以完成封装。
半导体封装设备材料1.电池板:电池板全名为半导体电池板,是半导体制造中的必要材料之一。
它通常被用作制造微芯片和其他半导体产品的基础材料。
电池板通常由纯硅制成,因为硅是制造半导体的最佳材料之一。
2.排线:排线是半导体封装中最常用的材料之一,因为它可以连接到各种元器件和芯片,从而使它们可以在更广泛的电路中工作。
排线通常由铜、铝或金刚石制成。
铜是最常用的材料之一,因为其导电性能优良,且价格较为实惠。
3.烟雾处理设备:烟雾处理设备是半导体封装过程中至关重要的设备之一。
它可以用来过滤设备产生的烟雾和粉尘,以确保制造环境的清洁和卫生。
烟雾处理设备通常包括过滤器、碳过滤器以及粒子清洁器等。
4.封胶设备:封胶设备用于在芯片上涂覆胶水,并紫外线固化粘胶以固定芯片和排线。
封胶设备的选择应根据使用封胶的材料进行调整,因为不同材料的粘合性能不同。
通常使用的封胶设备有涂胶机、涂覆机和喷涂机等。
半导体封装制程在现代电子产业中扮演着重要角色。
从封装的步骤到所需的设备材料,我们可以看出半导体封装制程的复杂性和高技术含量。
半导体制程
半导体制造工艺流程一、半导体相关知识本征材料:纯硅9-10个9250000Ω.cmN型硅:掺入V族元素--磷P、砷As、锑SbP型硅:掺入III族元素—镓Ga、硼BPN结:二、半导体元件制造过程前段(Front End)制程晶圆处理制程(Wafer Fabrication;简称Wafer Fab)、晶圆针测制程(Wafer Probe);后段(Back End)构装(Packaging)、测试制程(Initial Test and Final Test)1.晶圆处理制程晶圆处理制程之主要工作为在硅晶圆上制作电路与电子元件(如电晶体、电容体、逻辑闸等),为上述各制程中所需技术最复杂且资金投入最多的过程,以微处理器(Microprocessor)为例,其所需处理步骤可达数百道,而其所需加工机台先进且昂贵,动辄数千万一台,其所需制造环境为为一温度、湿度与含尘(Particle)均需控制的无尘室(Clean-Room),虽然详细的处理程序是随着产品种类与所使用的技术有关;不过其基本处理步骤通常是晶圆先经过适当的清洗(Cleaning)之后,接着进行氧化(Oxidation)及沈积,最后进行微影、蚀刻及离子植入等反覆步骤,以完成晶圆上电路的加工与制作。
2.晶圆针测制程经过Wafer Fab之制程后,晶圆上即形成一格格的小格,我们称之为晶方或是晶粒(Die),在一般情形下,同一片晶圆上皆制作相同的芯片,但是也有可能在同一片晶圆上制作不同规格的产品;这些晶圆必须通过芯片允收测试,晶粒将会一一经过针测(Probe)仪器以测试其电气特性,而不合格的的晶粒将会被标上记号(Ink Dot),此程序即称之为晶圆针测制程(Wafer Probe)。
然后晶圆将依晶粒为单位分割成一粒粒独立的晶粒3.IC构装制程IC构装制程(Packaging):利用塑胶或陶瓷包装晶粒与配线以成集成电路目的:是为了制造出所生产的电路的保护层,避免电路受到机械性刮伤或是高温破坏。
半导体全制程介绍
《晶圆处理制程介绍》基本晶圆处理步骤通常是晶圆先经过适当的清洗(Cleaning)之后,送到热炉管(Furnace)内,在含氧的环境中,以加热氧化(Oxidation)的方式在晶圆的表面形成一层厚约数百个的二氧化硅层,紧接着厚约1000到2000的氮化硅层将以化学气相沈积Chemical Vapor Deposition;CVP)的方式沈积(Deposition)在刚刚长成的二氧化硅上,然后整个晶圆将进行微影(Lithography)的制程,先在晶圆上上一层光阻(Photoresist),再将光罩上的图案移转到光阻上面。
接着利用蚀刻(Etching)技术,将部份未被光阻保护的氮化硅层加以除去,留下的就是所需要的线路图部份。
接着以磷为离子源(Ion Source),对整片晶圆进行磷原子的植入(Ion Implantation),然后再把光阻剂去除(Photoresist Scrip)。
制程进行至此,我们已将构成集成电路所需的晶体管及部份的字符线(Word Lines),依光罩所提供的设计图案,依次的在晶圆上建立完成,接着进行金属化制程(Metallization),制作金属导线,以便将各个晶体管与组件加以连接,而在每一道步骤加工完后都必须进行一些电性、或是物理特性量测,以检验加工结果是否在规格内(Inspection and Measurement);如此重复步骤制作第一层、第二层...的电路部份,以在硅晶圆上制造晶体管等其它电子组件;最后所加工完成的产品会被送到电性测试区作电性量测。
根据上述制程之需要,FAB厂内通常可分为四大区:1)黄光本区的作用在于利用照相显微缩小的技术,定义出每一层次所需要的电路图,因为采用感光剂易曝光,得在黄色灯光照明区域内工作,所以叫做「黄光区」。
2)蚀刻经过黄光定义出我们所需要的电路图,把不要的部份去除掉,此去除的步骤就> 称之为蚀刻,因为它好像雕刻,一刀一刀的削去不必要不必要的木屑,完成作品,期间又利用酸液来腐蚀的,所以叫做「蚀刻区」。
- 1、下载文档前请自行甄别文档内容的完整性,平台不提供额外的编辑、内容补充、找答案等附加服务。
- 2、"仅部分预览"的文档,不可在线预览部分如存在完整性等问题,可反馈申请退款(可完整预览的文档不适用该条件!)。
- 3、如文档侵犯您的权益,请联系客服反馈,我们会尽快为您处理(人工客服工作时间:9:00-18:30)。
回目次
13-1
半導體製程簡介
二、半導體製程
矽晶圓製作IC 2. IC中的線路及元件製作
IC依功能及使用目的,進行線路及半導體元件的 設計並製作於晶圓表層。
過程:薄膜製作→微影製程→蝕刻→離子植入。
重複上述過程,進行不同位置的線路及元件製作。
課本P.273
回目次
13-1
半導體製程簡介
影像呈現的形式
正片光罩:線路部分透光(其餘部分不透光) 負片光罩:線路部分不透光(其餘皆透光)
課本P.275
回目次
13-1
半導體製程簡介
(2)微影製程:
將光罩上的線路、元件圖案,投影至晶圓表面,以 便後續蝕刻出圖案。
微影製程步驟
光阻塗布 曝光 顯影
課本P.275
回目次
13-1
半導體製程簡介
課本P.270
回目次
13-1
半導體製程簡介
二、半導體製程
矽晶圓製作IC
矽在地球上的含量占25%,僅次於氧。
將矽砂經過一連串的精煉過程後,可以製作成 半導體材料及IC,流程如圖13-4所示。
課本 P.270~271
回目次
13-1
半導體製程簡介
二、半導體製程
矽晶圓製作IC 1.晶棒與晶圓
(1)現況概述: 由矽砂提煉成矽晶棒的最後一關,使用柴氏或稱 CZ製程(Czochralski process),操作方法如圖13-5所示。
第十三章 新興製造技術
13-1 半導體製程簡介 13-2 微細製造簡介
13-3 其他製造技術
總目次
13-1
半導體製程簡介
一、概述
1.半導體、電路與積體電路 材料以導電能力,可以分為
(1)導體
(2)半導體
(3)絕緣體
課本P.268
回目次
13-1
半導體製程簡介
一、概述
(1)半導體: 導電能力介於導體和絕緣體之間的材料,就稱之 為半導體。 半導體材料主要有鍺、矽及砷化鎵。 矽的優點: a.原料便宜
b.耐高溫
c.表面易形成絕緣的二氧化矽
• 矽為現今主要的半導體材料!
課本P.268
回目次
13-1
半導體製程簡介
一、概述
(1)半導體: 半導體產品,如圖所示。
課本P.268
回目次
13-1
半導體製程簡介
一、概述
1.半導體、電路與積體電路
(1)半導體: 砷 化 鎵 適 用 於 製 作 雷 射 二 極 體 及 發 光 二 極 體 ( Light emitting diode,LED ) 的材料。 常用的摻雜劑有帶正電的硼及帶負電的磷或砷。 加入硼則稱為p型半導體,加入磷或砷則稱為n型 半導體。
(2)微影製程:
①光阻塗布 光阻是一種感光材料,由感光劑、樹脂及溶劑 混合而成。
依成分分為
正光阻:不溶於顯影液 負光阻:易溶於顯影液 解析度較佳!
課本P.275
回目次
13-1
半導體製程簡介
(2)微影製程:
13-1
半導體製程簡介
(1)薄膜製作:
②氧化薄膜 IC製程中二氧化矽是最常使用的氧化薄膜。
製作的方法
乾式氧化(高品質) 溼式氧化(高效率) 以乾→溼→乾的順序來提高生產率製作高 品質的二氧化矽薄膜。
課本P.274~275
回目次
13-1
半導體製程簡介
(2)微影製程: 光罩
一片印製有線路、元件圖案的透明石英玻璃。
課本P.272
回目次
13-1
半導體製程簡介
二、半導體製程
矽晶圓製作IC 1.晶棒與晶圓
(2)矽晶棒的製作: 如圖13-5(續)為晶圓切片與化學機械研磨。
課本P.272
回目次
13-1
半導體製程簡介
二、半導體製程
矽晶圓製作IC 1.晶棒與晶圓
(3)晶圓的製作:圖13-6為不同直徑的晶圓片。
圖13-6
晶圓片直徑朝大尺度展(3~12吋)
課本P.273
ห้องสมุดไป่ตู้
回目次
13-1
半導體製程簡介
二、半導體製程
矽晶圓製作IC 1.晶棒與晶圓 (4)發展狀況:
單顆IC的面積通常只有數mm2很少有大於1cm2 的尺度。
一片直徑12吋的晶圓面積,可以同時製作出數百 個或數千顆IC。 最後再以鑽石砂輪或雷射分割成單顆IC進行封裝。
課本P.269
回目次
13-1
半導體製程簡介
一、概述
2.無塵室
以IC的製程技術而言,其單一線路寬度可細小至 20nm以下,如圖13-3為IC製程尺度。
課本P.269
回目次
13-1
半導體製程簡介
一、概述
3.摩爾定律(Moore's law)
(1)「IC 中可容納的電晶體數每隔18 個月就能增加1 倍,從而使性能也提升1 倍」 (2)預測未來製程微小至7nm後,此定律將不再適用。
B.化學氣相沉積:CVD(Chemical vapor deposition ) 圖13-7所示的常壓式與低壓式二種化學氣相沉 積爐。
圖13-7 常壓式與低壓式化學氣相沉積爐
課本P.274
回目次
13-1
半導體製程簡介
(1)薄膜製作:
①氣相沉積薄膜 低壓式的爐體為密閉設計,可節省大量反應 用的化學氣體。 生產率高且膜厚均勻。 常用於多晶矽、氮化矽及二氧化矽等薄膜的 沉積。
二、半導體製程
矽晶圓製作IC 2. IC中的線路及元件製作
(1)薄膜製作: 薄膜的製作通常採用氣相沉積和氧化等方法。 ①氣相沉積薄膜 A.物理(PVD) B.化學氣相沉積(CVD) C.磊晶
課本P.273~274
回目次
13-1
半導體製程簡介
(1)薄膜製作:
①氣相沉積薄膜 A.物理氣相沉積:PVD(Physical vapor deposition)
課本P.268
回目次
13-1
半導體製程簡介
一、概述
1.半導體、電路與積體電路
積體電路,如圖13-2所示。
課本P.269
回目次
13-1
半導體製程簡介
一、概述
2.無塵室
(1)半導體及IC的製作需要在無塵室中進行。
(2)製程中最大的汙染源是工作人員,因此必須穿著 全身包覆的無塵衣。 (3)無塵室的空氣必須以高效能空氣微粒濾網 ( HEPA ) 過濾,溫度控制在23℃、相對溼度在45%最為適 宜。 (4)奈米(nm)是長度單位,為10-9公尺(m),即 1nm= 0.000000001m。
B.化學氣相沉積:CVD(Chemical vapor deposition )
課本P.274
回目次
13-1
半導體製程簡介
(1)薄膜製作:
①氣相沉積薄膜 C.磊晶 使沉積薄膜的結晶方向與基材(晶圓)相 同或直接相關的一種薄膜製作方法。 磊晶薄膜的雜質少,製成的元件效能較高。
課本P.274
回目次