数控机床主轴静动态特性分析与优化设计
基于SAMCEF平台的机床整机动态特性分析

基于SAMCEF平台的机床整机动态特性分析机床的动态性能决定了机床的加工能力。
为分析优化机床的动态特性,研发人员在SAMCEF平台下,建立了机床的动力学模型,对该模型进行模态分析,同时采用LMS设备对该机床进行模态测试。
对比发现有限元计算振型与实验基本一致,计算得到的固有频率与实验得到的频率误差在16%之内,验证了该模型的可靠性。
利用该有限元模型,把所有部件作为柔性体建立动力学模型,进行多体动力学分析,研究载荷作用下导向部件及结构部件的动态应力变化情况,分析结果为机床优化设计提供方向。
机床作为生产的重要工具和设备,也被称为工作母机,其动态性能与其加工性能紧密相关,并直接影响所加工零件的精度。
随着现代设计方法的广泛运用,对机床进行动态特性分析,用动态设计取代静态设计已成为机床设计发展的必然趋势。
在设计中,仅对机床部件进行动态分析无法全面反映机床的整体性能。
因此,要对机床性能进行准确的预测,必须对机床整机进行动力学分析。
伴随着计算机计算速度的飞速提升,有限元分析成为分析计算复杂结构的一种极为有效的数值计算方法,为机床整机的振动模态理论分析提供了有力的工具。
本文利用SAMCEF动力学仿真平台和模态实验相结合的方式,对机床进行有限元计算和模态实验分析,为新产品研发设计提供了参考。
一、模态分析的基本理论振动现象是机械结构经常需要面对的问题之一。
由于振动会造成结构的共振或疲劳,从而破坏结构,所以必须通过模态分析了解模型的各阶固有频率和振型,避免在实际工况中因共振因素造成结构的损坏。
模态分析可以用来确定模型或结构的振动特性,对复杂结构进行精确的模态分析,将为评价现有结构的动态特性,诊断及预报结构系统的故障,新产品动态性能的预估及优化设计提供科学的依据。
三、机床模态实验本次试验是与LMS公司中国区技术支持工程师共同合作完成,针对VMC0540d立式加工中心进行模态实验,确定该机床的结构动力学参数,如图4所示。
同时,此次试验采用了LMS提供的测试设备及相应的分析软件:LMS SC310前端、PCB 333B30单向加速度计、激振器及功率放大器(3台)以及LMS Test Lab 9B模态测试分析软件等。
基于iSIGHT的主轴动静态性能优化设计方法
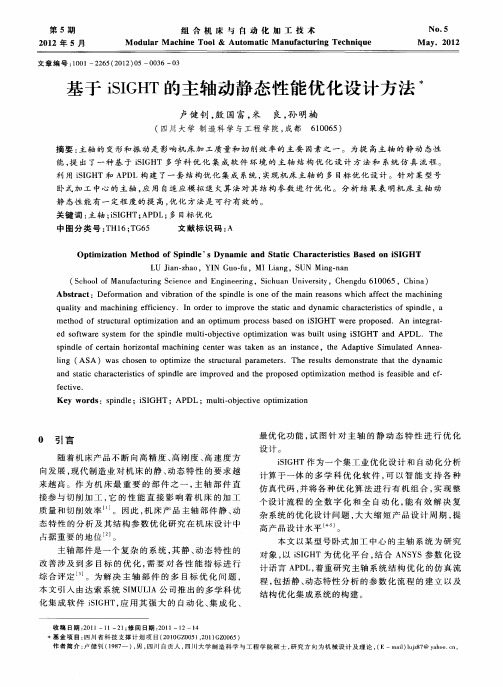
Absr t:De o m ai n a d v b ai n o h pi l so e o h an r a o swh c fe tte m a hi ng tac f r to n i r to ft e s nd ei n ft em i e s n i h a f c h c ni
L Ja z a U in—h o,YI Gu —u,MILin N o f a g,S UN n — a Mi g n n
( c o l fMa ua trn ce c n n ie r g ih a iest S h o n fcu igS in ea d E gn ei ,Sc u n Unv ri o n y,C e g u6 0 6 h n d 1 0 5,C ia hn )
利 用 iI S GHT和 AP DL构 建 了一 套 结 构 优 化 集 成 系 统 , 现 机 床 主 轴 的 多 目标 优 化 设 计 。 针 对 某 型 号 实
卧式加 工 中心 的主 轴 , 用 自适应模 拟 退 火算法对 其结 构参 数进 行 优化 。 分析 结 果表 明机 床 主轴 动 应 静 态性能 有一 定程 度 的提 高 , 优化 方 法是 可行 有 效的 。
e o t r y tm o h pn l mut o jcieo t z t n wa ul u ig i I d sf ess wa e f rte s ide l be t pi ai sb i sn S GHT a d AP i v mi o t n DL.T e h
关于数控机床主轴结构的改进设计

关于数控机床主轴结构的改进设计数控机床主轴是数控机床的关键部件,其性能直接影响机床加工精度和加工效率。
随着数控技术的不断发展,对数控机床主轴结构的要求也越来越高。
为了满足市场对数控机床加工精度的需求,需要对数控机床主轴结构进行改进设计,以提高其性能和可靠性。
一、数控机床主轴结构存在的问题1. 结构复杂:传统的数控机床主轴结构通常采用多个轴承和润滑系统,结构复杂,加工成本高。
2. 刚性不足:部分数控机床主轴刚性不足,加工时容易产生振动和变形,影响加工精度。
3. 温升大:部分数控机床主轴在高速加工时容易产生较大的温升,影响机床稳定性和使用寿命。
4. 维护困难:传统数控机床主轴结构维护和保养较为繁琐,需要定期更换润滑油和轴承。
以上问题严重影响了数控机床的加工精度和稳定性,需要通过改进设计来解决。
二、改进设计方案针对数控机床主轴结构存在的问题,可以采取以下几点改进设计方案:1. 优化结构:采用轴向预紧轴承和径向预紧轴承的组合方式,降低轴承数量,简化结构,减小主轴体积和重量。
2. 提高刚性:采用高强度材料和优化设计,提高数控机床主轴的刚性,减小振动和变形,提高加工精度。
3. 降低温升:采用先进的冷却系统和材料,减小高速加工时的温升,提高机床稳定性和使用寿命。
4. 简化维护:采用自动润滑系统和可拆卸设计,简化维护和保养,减小维护成本和时间。
上述改进设计方案可以有效解决传统数控机床主轴结构存在的问题,提高数控机床的加工精度和稳定性,提升竞争力。
三、改进设计实施过程改进设计实施过程中,需要参考市场需求和技术发展趋势,充分调研国内外同类产品的主轴结构和性能,进行方案比较和优化设计。
1. 方案比较:对不同的数控机床主轴结构方案进行技术比较和性能测试,寻找最适合产品需求的方案。
2. 优化设计:在方案确定后,对数控机床主轴结构进行进一步的优化设计,满足产品性能指标和质量要求。
3. 样机制造:根据优化设计方案制作数控机床主轴样机,进行性能测试和验证,验证设计方案的可行性和有效性。
数控铣床主轴部件动态特性分析

模型 , 用 A S S对主轴部件进行模态分析 , 出主轴部件 的 应 NY 得 固有频率和 主振型 , 判断转速是否远低于主轴的一 阶临界转速 ,
为铣床主轴部件 的优化设计提供普遍的指导意义 。
图 1主 轴 一轴 承 的 简化 模 型 图
2主轴部件 的动力学模 型
21 . 主轴部件的结构分析
L U Da - in , HEN T o , HEN S u — h n W ANG Yu I o qa C a S h n c eg, e
( col f lc o eh ncl nier g Wu a nvr t o eh ooy Wu a 3 0 0 C ia h o o et m c ai g ei , h nU i s y f c n l , hn4 0 7 , hn ) S E r aE n n e i T g (. o i rvneMahnr e sahIs tt C .t. h n a g10 3 ,hn )  ̄ ann Po ic c ie R aec tue o d, e yn 10 2 C ia J g y ni L S
【 摘要 】 以某数控铣床主轴为研 究对象, 了轴和 角接触轴承的等效动力学模 型. 究 了轴承等 建立 研
效刚度和预紧力参数对主轴 系统固有频率影响规律 , 通过模 态分析确定主轴部件的 固有频率和振型, 验证 数控铣 床 主轴部件 结构 设计 的合理性 。 关键词 : 轴部 件 ; 限元分 析 ; 态特 性 ; 主 有 动 数控 铣床
到铣床 的加工精度 , 主轴部件在外力作用下将产生较大的变形 , 容 易引起振动 , 降低加工精度和表面质量。 主轴部件 的变形对机
床 的加工精度 , 表面质量有很大的影响, 为了使数控机床的主轴
机床主轴系统的动态特性研究

机床主轴系统的动态特性研究引言:机床作为制造业中的重要设备,起着关键的作用。
而机床的核心部件之一,主轴系统,直接影响着机床的性能和精度。
因此,研究机床主轴系统的动态特性,对于优化机床设计和提高加工效率具有重要意义。
一、机床主轴系统简介机床主轴系统是机床的核心部件之一,主要由电机、轴承、刚性连接件等组成。
它承载着传递动力和负载的功能,同时具备高速运转和精确控制的要求。
二、机床主轴系统的动态特性1. 动态刚性机床主轴系统的动态刚性是指在外界作用下,主轴系统的变形程度。
它直接影响着机床的切削精度和表面质量。
动态刚性的研究中,需要考虑轴承、刚性连接件的刚性和主轴的轻负载刚度。
2. 动态特征频率机床主轴系统具有多个共振频率,它们对应着系统的固有振动频率。
在机床的实际工作中,共振频率的发生会导致机床的振动加剧,甚至发生共振破坏。
因此,研究机床主轴系统的动态特征频率,是保证机床运行安全和精度的重要手段。
3. 动态不平衡机床主轴系统在高速运转时,常常会出现动态不平衡现象。
不平衡会导致系统振动加剧,降低机床的加工精度和表面质量。
因此,研究机床主轴系统的动态不平衡特性,有助于提高机床的稳定性和加工质量。
三、机床主轴系统动态特性的研究方法1. 实验方法实验方法是研究机床主轴系统动态特性的常用手段。
通过在实验台上设置传感器,测量主轴系统的振动和共振频率。
同时,通过调整传动系统的参数,得到不同工况下的动态特性参数。
2. 数值模拟方法数值模拟方法是基于有限元理论和计算流体力学理论,对机床主轴系统进行模拟和分析。
通过建立数学模型,求解主轴系统的振动方程和流体流动方程,得到系统的动态特性。
3. 优化设计方法优化设计方法是通过改变机床主轴系统的结构参数,以优化系统的动态特性。
通过优化设计,可以提高系统的刚性、降低共振频率、减小不平衡量等,从而提高机床的性能和精度。
四、机床主轴系统动态特性研究的应用和前景1. 应用研究机床主轴系统的动态特性对于优化机床设计、提高加工效率和质量具有重要意义。
关于卧式机床主轴组件的优化与设计

关于卧式机床主轴组件的优化与设计摘要数控机床中的关键部件就是主轴部件,主轴部件的动态性能好与坏直接影响着数控机床加工性能的优劣,文章就是针对主轴部件的动态特性展开理论分析和研究。
通过选用弹簧的阻尼单元进行模拟轴承的约束,使用ansys软件对bw60hs系列高速卧式加工中心主轴部件的动态性能展开研究,主要分析了整个主轴部件的谐响应和模态/固有频率等相关动态特性。
结合实际工作中机床动态激振试情况验证了有限元分析的结果。
关键词固有频率;主轴模态;bw60hs中图分类号th18 文献标识码a 文章编号 1674-6708(2011)45-0141-01在日常生产过程中,为了进一步地提高整个产品设计的有效性,通常都是在产品设计的具体过程中,对所有产品的性能要进行必要的评价,从而更近一步地对其进行一定的设计改进。
虚拟样机的制造技术的大量使用,使得产品在设计阶段就建立了机床的虚拟模型,这样就能对产品每一个部件的具体运动进行必要的干涉和检查,更重要的是还能更加完善和全面地对产品性能进行评价和分析。
数控机床中的关键部件就是主轴部件,主轴部件的动态性能好与坏直接影响着数控机床加工性能的优劣,所以说对主轴部件的动态特性进行一定的理论分析和研究具有着不可低估的现实指导意义。
1 卧式机床的技术分析bw60hs系列高速卧式加工中心的设计、制造技术及应用技术完全来源于德国,机床不的关键零部件(如:电主轴、数控转台、滚珠丝杠、线性导轨、轴承、绝对式光栅尺测量系统、液压系统、润滑系统、气动系统、数控系统及驱动控制系统、刀库等)均采用德国进口知名品牌。
bw60hs系列高速卧式加工中心,具有高精度、高速度、高效率、高可靠性的特点,是目前国际先进的现代化机床,广泛适用于汽车、摩托车、仪表、液压件、模具、航空等行业,是加工箱体、壳体、阀体、连杆类零部件加工以及轴类零件端面加工的理想设备。
2 数控车床主轴部件动态性能分析2.1 主轴部件模态分析结合所有能体现整个主轴部件的振动特性每一个阶的模态振型。
数控机床主轴静动态特性分析与优化设计

数控机床主轴静动态特性分析与优化设计数控机床主轴的静动态特性分析与优化设计在机床设计中扮演着重要的角色。
主轴的质量、刚度和动力性能直接影响着数控机床的加工精度和生产效率。
因此,针对数控机床主轴的静动态特性进行分析和优化设计是非常必要的。
首先,对数控机床主轴的静态特性进行分析是基础。
静态特性主要包括主轴的刚度、负载能力和转速范围。
刚度是指主轴在受力时的变形能力,直接影响着机床的切削精度。
负载能力指主轴能够承受的最大切削力或轴向力,取决于主轴的结构和材料。
转速范围则指主轴的最大和最小可工作转速,根据机床加工要求和主轴的功率决定。
其次,对数控机床主轴的动态特性进行分析是优化设计的重要环节。
动态特性主要包括主轴的运行平稳性、动态刚度和各模态的特性频率。
运行平稳性是指主轴在工作状态下的振动情况,对加工表面质量和刀具寿命有重要影响。
动态刚度是指主轴在受力时的变形能力在一定频率下的响应能力。
各模态的特性频率则表征着主轴在不同振动模态下的响应频率和振动幅度。
针对数控机床主轴的静动态特性,可以采取以下优化设计措施。
首先是通过优选材料和适当加工工艺来提高主轴的刚度和负载能力。
其次是采用适当的轴承和润滑方式,减小主轴的摩擦和磨损,提高运行平稳性。
此外,还可以通过调整主轴的结构和参数来提高动态刚度和各模态的特性频率。
例如,增加主轴的直径、改变轴承支撑形式等。
在数控机床主轴静动态特性优化设计过程中,还需要考虑与其他系统和结构的配合,如主轴驱动装置、刀具系统等。
同时,结合实际工艺要求和机床制造能力,进行多种参数的优化设计,以实现最佳的综合性能。
总之,数控机床主轴的静动态特性分析与优化设计是非常重要的工作,直接关系到数控机床的加工质量和生产效率。
通过对主轴材料、结构和参数的优化设计,可以提高数控机床主轴的静态刚度、负载能力和动态性能,进而提高数控机床的加工精度和生产效率。
机床主轴有限元分析

施加约束
施加载荷
机床主轴模态分析
求解固有频率和振型
结构的振动在ANSYS中表现为各阶振型的线性叠 加,其中低阶振型比高阶振型对结构的振动影响 大,故进行结构的振动特性分析时通常取1 ~5 阶即可。
机床主轴模态分析
一阶振型如图:
机床主轴模态分析
二阶振型
机床主轴模态分析
三 阶 阵 型
机床主轴模态分析
机床主轴有限元分析及优化设计
。
不机床主轴相连接的结构示意图
2D示意图 M1、M2处 为弹性支承 位置
主轴连接结构与二维图形
ANSYS三维建模
主轴外观图
Solid92单元材料 参数为:弹性模量 (N/m)2.06e11; 泊松比0.28;密度 7800。
单元类型选择和网格划分
机床的加工精度, 径向刚度主要受到主轴的 跨距材料物理性能结构尺 寸等因素的影响。 从图中可以看出径向力主 要造成主轴前端悬伸部分 的变形,可推断主轴前端 悬伸量是影响主轴静刚度 的主要因素。通过减少伸 出量来增加主轴系统的静 刚度。
一阶 优化前 优化后 二阶 三阶 四阶 1537.6 3034.85 五阶 1809、 2 3562.3
612.01 612.15 1537.2 1523.3 1523.9 3034.76
机床主轴优化设计
因此优化后的主轴在工作过程中更远离共振发生 的区域,更安全。
四阶振型
机床主轴模态分析
五阶振型
机床主轴模态分析
由上可知:上面图型可以看出,主轴在这五个 阶段,发生了弯曲变形。主轴以弯曲变形为主, 同时也发生轴向变形。弯曲是主轴的主要振动。 由于采用近似的线性模型(包括材料特性的线 性化和有限元模型的线形化),因而在阶数越 低的情况下对主轴进行的理论分析值不实验测 得的值就越接近,而在高阶部分就误差越来越 大。
- 1、下载文档前请自行甄别文档内容的完整性,平台不提供额外的编辑、内容补充、找答案等附加服务。
- 2、"仅部分预览"的文档,不可在线预览部分如存在完整性等问题,可反馈申请退款(可完整预览的文档不适用该条件!)。
- 3、如文档侵犯您的权益,请联系客服反馈,我们会尽快为您处理(人工客服工作时间:9:00-18:30)。
数控机床主轴静动态特性分析与优化设计
孙茂悦
【期刊名称】《科技创新导报》
【年(卷),期】2022(19)1
【摘要】现如今,机床主轴系统的静态及动态刚度作为影响机床加工精度的重要因素,因此,应根据CREO基准合理构建相应的三维建模,详细分析模型的实时动态,了解并掌握主轴的变形量、固有频率及振型等各类静动特征。
本文以主轴整体质量达到最优状态为主要优化目标,并优化主轴孔径、支承跨距、主轴外径及前段悬伸量的实时数据,合理比对优化前后的主轴性能。
【总页数】3页(P37-39)
【作者】孙茂悦
【作者单位】沈阳机床(集团)有限责任公司
【正文语种】中文
【中图分类】U463
【相关文献】
1.高速陶瓷电主轴结构设计及静动态特性分析
2.数控机床主轴部件静动态特性优化设计
3.数控机床主轴静动态特性分析与优化设计
4.紧凑型高速电主轴拉刀机构静动态特性分析与优化
5.立式加工中心主轴箱静动态特性分析及拓扑优化
因版权原因,仅展示原文概要,查看原文内容请购买。