机床主轴主参数的优化设计
机床主轴结构优化设计

机床主轴结构优化设计指导老师:姓名:学号:机床主轴结构优化设计一.机械优化设计的一般过程① 建立优化设计的数学模型② 选择适当的优化方法③ 编写计算机程序④ 准备必要的初始数据并上机计算⑤ 对计算机求得的结果进行必要的分析其中,建立优化设计的数学模型是首要的和关键的一步,其基本原则仃: 1、 设计变量的选择在充分了解设计要求的基础上,应根据各设计参数对目标函数的彤响程度认真分析 其主次,尽最减少设计变最的数目,以简化优化设计问题。
另外,还应注意设计变 量应当相互独立,否则会使目标函数出现“山脊”或“沟谷”,给优化带来困难。
2、 目标函数的确定常取其中最主要的指标作为目标函数,而其余的指标列为约束条件。
3、 约束条件的确定在选取约束条件时应当避免出现相互矛盾的约朿。
因为相互矛盾的约束必然 导致可行域为一空集,使问题的解不存在。
另外应当尽量减少不必要的约束。
不必要的约束不仅增加优化设计的计算臺,而且可能使可行域缩小,影响优 化结果。
二、优化实例机床主轴是机床中重耍零件之般为多支承空心阶梯轴。
为了便丁使用材料力 学公式进行结构分析,常将阶梯轴简化成以当量直径表示的等截面轴。
下面以两支 承主轴为例,说明优化设计的全过程。
右图所示的是一个己经简化的机床主轴。
已知主轴内 径d=30mm,外力 215000N,许用挠度 yO=O. 05mm« 主 轴材料是铸钢。
密度p = 7.8 x 10"6Kg/ mm 3,弹性模 * E=210GPa 设计变量数n=3,约束函数个数m=5,设 计变量的初值、上下限列于设计变量 XIX2 X3 初始值 480100 120 下限值 30060 90 上限值 650 140 150 表8-1初始数据-- --- ―一殳表8-1中。
设计变量的确定当主轴的材料选定时,其设计方案由四个设计变量决定。
即孔径d 、外径D 、跨距1及外伸端长度a 。
由丁•机床主轴内孔常用于通过待加工的棒料, 其大小由机床型号决定,不能作为设计变量。
数控机床主轴的多目标优化设计

Mu t o jcieOp i z to sg fMan Axei li be t t _ v miain Dein o i l n CNC M a hn o l c i eT o
Ab ta tTh tu t r p i z t nd s no h i xei src : esr cu eo t ai ei f emana l CNC ma hn o lssu id mi o g t n c ieto t de .A li be t eo t z— i mu t o jci pi a — v mi
设计 , 以简化 求解过程 , 有一 定的 工程 实用价值 。 可 具
关 键词 : 数控机 床 ; 主轴 系统 ; 目标 优化 设计 ; 多 邻域培 植遗 传算 法 ; aeo最优 解 ; I P rt i GHT S
中 图 分 类 号 : 3 . TB 5 3 1 文献 标志码 : A
op i z to e i oc s . tmia i n d sgn pr e s
Ke o d : y w r s CNC ma hn to ,M an a l , ut o jcie o tmiain d sg c ie o l i xe M l— be t pi z t ein,NCGA ,P r t o t m s lto s i v o aeo p i mu ouin ,
得 以减 少 , 得 综合 成 本 大 大 降低 。数 控机 床 往 往 使
数控机床主轴结构的改进和优化设计
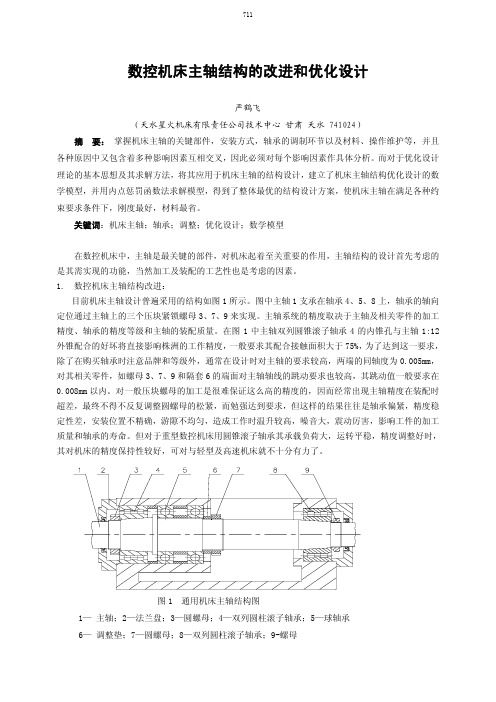
数控机床主轴结构的改进和优化设计严鹤飞(天水星火机床有限责任公司技术中心 甘肃 天水 741024) 摘 要: 掌握机床主轴的关键部件,安装方式,轴承的调制环节以及材料、操作维护等,并且各种原因中又包含着多种影响因素互相交叉,因此必须对每个影响因素作具体分析。
而对于优化设计理论的基本思想及其求解方法,将其应用于机床主轴的结构设计,建立了机床主轴结构优化设计的数学模型,并用内点惩罚函数法求解模型,得到了整体最优的结构设计方案,使机床主轴在满足各种约束要求条件下,刚度最好,材料最省。
关键词:机床主轴;轴承;调整;优化设计;数学模型在数控机床中,主轴是最关键的部件,对机床起着至关重要的作用,主轴结构的设计首先考虑的是其需实现的功能,当然加工及装配的工艺性也是考虑的因素。
1. 数控机床主轴结构改进:目前机床主轴设计普遍采用的结构如图1所示。
图中主轴1支承在轴承4、5、8上,轴承的轴向定位通过主轴上的三个压块紧锁螺母3、7、9来实现。
主轴系统的精度取决于主轴及相关零件的加工精度、轴承的精度等级和主轴的装配质量。
在图1中主轴双列圆锥滚子轴承4的内锥孔与主轴1:12外锥配合的好坏将直接影响株洲的工作精度,一般要求其配合接触面积大于75%,为了达到这一要求,除了在购买轴承时注意品牌和等级外,通常在设计时对主轴的要求较高,两端的同轴度为0.005mm,对其相关零件,如螺母3、7、9和隔套6的端面对主轴轴线的跳动要求也较高,其跳动值一般要求在0.008mm以内。
对一般压块螺母的加工是很难保证这么高的精度的,因而经常出现主轴精度在装配时超差,最终不得不反复调整圆螺母的松紧,而勉强达到要求,但这样的结果往往是轴承偏紧,精度稳定性差,安装位置不精确,游隙不均匀,造成工作时温升较高,噪音大,震动厉害,影响工件的加工质量和轴承的寿命。
但对于重型数控机床用圆锥滚子轴承其承载负荷大,运转平稳,精度调整好时,其对机床的精度保持性较好,可对与轻型及高速机床就不十分有力了。
某机床主轴的优化设计

某机床主轴的优化设计一、问题来源机床主轴是机床的执行件,它的功用是支承并带动工件或刀具完成表面成形运动,同时还起到传递运动和扭矩、承受切削力和驱动力等载荷的作用,结构复杂,价格昂贵,是机床最重要的部件之一。
主轴的前端安装着卡盘与工件,直接参与切削加工,它的变形和振动对机床的加工精度和表面质量影响最大,直接影响到机床的加工质量和生产率。
因此,机床设计的成功关键取决于主轴设计的优劣。
主轴优化设计是机床设计中主轴设计的有效手段,它可以克服以往设计方法中的盲目性,提高主轴的设计质量、设计效率及设计的科学性和可靠性。
二、已知条件题目中的主轴是一个阶梯轴,支撑采用角接触轴承,机床主轴的输入功率P=1.5kW ,主轴的转速n=940r/min ,主轴的悬臂端受到的切削力F=20kN ,主轴内径d=40mm ,悬臂端许用挠度mm 05.0y 0=,取[]m /121='ϕ,[] 0025.0=θ。
要求主轴两支承跨距(L )为350mm ≤L ≤600mm ,外径(D )为70mm ≤D ≤150mm ,悬臂端长度(a )为80mm ≤a ≤160mm .主轴的材料采用40Cr ,密度3kg/m 7800=ρ。
从机床主轴制造成本和加工精度的要求出发,考虑主轴的自重和外伸段挠度这两个重要因素,选取主轴的质量最轻和最小轴端位移为设计目标,将主轴的刚度作为约束条件。
三、数学建模图1 主轴示意图1设计变量本文设计的机床主轴结构主要由5个参数来确定: (1)主轴悬伸段直径Da ; (2)主轴前后支承间轴径D ; (3)支承跨距L ; (4)主轴悬臂端长度a ; (5)主轴内孔直径d 。
另外,主轴轴端有作用力F 和弯矩M ,设:X=[]Tx x x x 43214321a x x x x a L D D =⎥⎥⎥⎥⎦⎤⎢⎢⎢⎢⎣⎡=⎥⎥⎥⎥⎦⎤⎢⎢⎢⎢⎣⎡2 目标函数在满足主轴传动要求下,减轻重量,节约材料,降低成本.以最小自重为追求的目标.机床主轴的质量:()()[]L d D a d D 4W 2222a⨯-+⨯-=πρ式中:(),令为主轴密度3m /kg ρ()=x f ()()[]3222422a X d X X d D 4W ⨯-+⨯-=πρ目标函数()x f x F min )(=3 约束条件(1)刚度约束机床主轴变形对加工质量影响很大,因此,对主轴的要求主要表现为刚度要求,即主轴伸出端的挠度(或位移)Y 尽可能小。
机床主轴结构优化设计
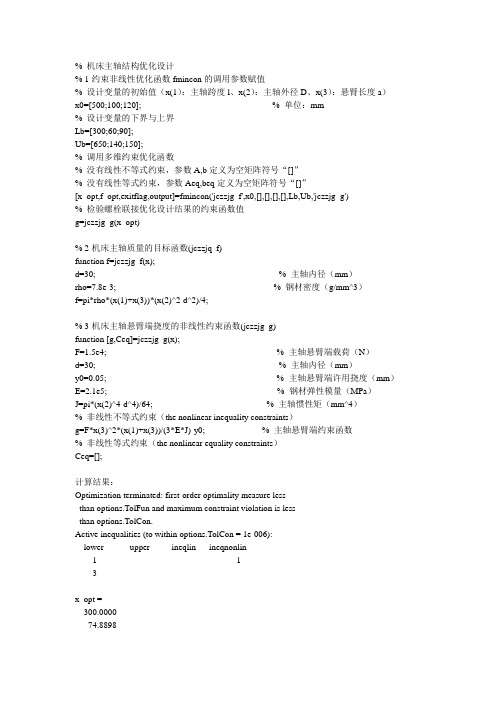
% 机床主轴结构优化设计% 1-约束非线性优化函数fmincon的调用参数赋值% 设计变量的初始值(x(1):主轴跨度l、x(2):主轴外径D、x(3):悬臂长度a)x0=[500;100;120]; % 单位:mm% 设计变量的下界与上界Lb=[300;60;90];Ub=[650;140;150];% 调用多维约束优化函数% 没有线性不等式约束,参数A,b定义为空矩阵符号“[]”% 没有线性等式约束,参数Aeq,beq定义为空矩阵符号“[]”[x_opt,f_opt,exitflag,output]=fmincon('jczzjg_f',x0,[],[],[],[],Lb,Ub,'jczzjg_g')% 检验螺栓联接优化设计结果的约束函数值g=jczzjg_g(x_opt)% 2-机床主轴质量的目标函数(jczzjq_f)function f=jczzjg_f(x);d=30; % 主轴内径(mm)rho=7.8e-3; % 钢材密度(g/mm^3)f=pi*rho*(x(1)+x(3))*(x(2)^2-d^2)/4;% 3-机床主轴悬臂端挠度的非线性约束函数(jczzjg_g)function [g,Ceq]=jczzjg_g(x);F=1.5e4; % 主轴悬臂端载荷(N)d=30; % 主轴内径(mm)y0=0.05; % 主轴悬臂端许用挠度(mm)E=2.1e5; % 钢材弹性模量(MPa)J=pi*(x(2)^4-d^4)/64; % 主轴惯性矩(mm^4)% 非线性不等式约束(the nonlinear inequality constraints)g=F*x(3)^2*(x(1)+x(3))/(3*E*J)-y0; % 主轴悬臂端约束函数% 非线性等式约束(the nonlinear equality constraints)Ceq=[];计算结果:Optimization terminated: first-order optimality measure lessthan options.TolFun and maximum constraint violation is lessthan options.TolCon.Active inequalities (to within options.TolCon = 1e-006):lower upper ineqlin ineqnonlin1 13x_opt =300.000074.889890.0000f_opt =1.1249e+004exitflag =1 % 返回值exitflag>0表示计算收敛output =iterations: 10 % iterations是优化过程中迭代次数funcCount: 51 % funcCount是代入函数值的次数stepsize: 1 % 1algorithm是优化所采用的算法(中等规模,拟牛顿SQP)algorithm: 'medium-scale: SQP, Quasi-Newton, line-search'firstorderopt: 7.5880e-007 % 一阶优化精度cgiterations: []message: [1x144 char]g =-3.4694e-017。
基于MATLAB的机床主轴结构优化设计

机械装备优化设计三级项目题目:基于MATLAB的机床主轴结构优化设计班级:12级机械装备-1班设计人员(按贡献大小排序):张彦亭邢朝阳张俊志一、优化设计问题分析:对下图所示车床主轴进行优化设计,已知主轴内径d=30mm,外力F=15000N,许用挠度00.05mmy 。
初始数据二、优化设计方案选择:首先我们用罚函数法求取最优点该目标函数在可行域外性质较复杂,因此采用内点法求取最优点。
内点法算法步骤:针对车床主轴问题,首先构造内点惩罚函数为:使用迭代法求解如下:经过21次迭代后,1510k k X X ---≤ ,求得最优解300.000064.800990.0000x *⎡⎤⎢⎥=⎢⎥⎢⎥⎣⎦()7.9323f x *= 可见,用数学方法非常复杂,所以我们又采用MATLAB 求取该值。
三、 具体任务分工:张彦亭 word 制作、问题的分析以及MATLAB 的程序求解 邢朝阳 PPT 制作 张俊志 PPT 答辩四、优化设计内容与步骤1、优化设计问题的数学建模2、所选择的优化方法及MatLab程序3、优化结果及分析所以当机床主轴跨距L、外径D和外伸端长度a分别为300.0000,64.8009,90.0000时,机床主轴的重量最轻为7.9323千克。
五、结论通过建立数学模型,运用MATLAB优化工具箱对机床主轴进行优化设计。
由计算过程和结果发现,使用该MATLAB方法对机床主轴可以较快速的求得最优解,与惩罚函数发相比,在设计效率和使用性方面都大为提高参考文献[1].机械与工程优化设计张鄂主编[2].肖伟,刘忠,曾新勇,等,MATLAB程序设计与应用,北京;清华大学出版社,2005。
数控车床加工参数的优化设计

数控车床加工参数的优化设计随着科学技术的不断进步,数控技术在制造业中逐渐被广泛应用。
数控车床作为数控机床的重要代表之一,其应用范围也越来越广泛。
在数控车床加工中,参数的设计和优化是保证产品质量和生产效率的重要关键。
本文将从数控车床加工的基本原理、常用参数、参数优化设计等方面进行探讨。
一、数控车床加工的基本原理数控车床加工是将工件夹于车床主轴上,通过主轴旋转实现工件的加工和成形。
加工过程中,切削刀具对工件进行切削、抛光、镗孔等操作。
区别于手动车床,数控车床采用先进的电子控制技术,避免了手工操作对加工精度和生产效率的影响,提高了加工的稳定性和可靠性。
同时,数控车床还具有自动换刀、自动计数、自动监测等功能,大大减少了人工干预和加工周期。
在实际应用中,数控车床在自动控制阶段可以实现对加工数据的精确掌控,改善生产效率,降低成本。
二、常见的数控车床加工参数1. 车床主轴转速车床主轴转速是指车床主轴转动的圈数。
主轴转速会影响车刀的进给速度、工件的切削效果和表面粗糙度等因素。
在加工不同材料的工件时,需要根据工件材质和形状等因素进行选择和调整。
2. 进给速度车床进给速度是指车刀沿工件轴向方向的运动速度。
进给速度的大小决定了加工效率和切削质量。
进给速度较慢时,车刀切削深度过大,容易导致切削阻力太大,加工效率低;进给速度过快则会对车刀和工件表面产生损伤,影响加工质量。
3. 切削深度切削深度是指车刀在加工时与工件表面的距离。
切削深度的大小直接影响到加工效率和工件表面质量。
一般来说,切削深度过大会导致车刀和工件的表面温度和磨损过高,进而影响加工质量和工件寿命。
4. 工件转速工件转速是指工件在车床主轴转动下的圈数。
工件转速与主轴转速是相互独立的,主要作用是控制加工产品的轮廓和表面质量。
在特定工件加工的过程中,需要根据工件材料和形状等参数进行选择。
5. 切削速度切削速度是指车刀在加工时切削的线速度。
切削速度越快,加工效率越高;反之,则会导致切削效果不佳。
机床主轴结构的优化

3.约束条件 刚度约束
主轴的刚度是一个重要性能指标,其外伸端
挠度y,不得超过规定值 y0,即:
y [y]
若外力F已知,则有 y Fa2L 3EI
其中:I (D4 d 4 ) / 64;E 为材料的弹性模量。
将以上两式代入到 g (x1)中得
g1 ( x)
y
[ y]
Fa 2 L 3EI
700
650
600
扭转角约束曲 挠度约束曲线
线
550
L
500
450
400
可行域
350
300
250
45
50
55
60
65
70
75
80
85
D
1.设计变量
当主轴材料一旦选定,其重量只是内径 d 、 外径 D 、跨距 L,d 的大小又决定于机床的型 号,不能作为设计变,故设计变量取为:
x x1 x2 T [ D L]T
建立模型:
2. 目标函数
根据设计要求,以自重最轻为设计目标,即:
f
(x)
1 4
x2
( x12
d
2
)
建立模型:
建立模型:
机床主轴一般为多支撑空心阶梯轴,为了便于使用 材料力学公式进行结构分,将其简化成的以当量直径表 示的等截面轴,并且为两支撑主轴形式,如下图所示。
该问题考虑因数:主轴自 重。
对于普通车床,并不 要求过高的加工精度,已 选取主轴的自重最轻为目 A 标,外伸端的挠度为约束 条件。
B
C
建立模型:
问题解决:
设计变量
x1
x2
- 1、下载文档前请自行甄别文档内容的完整性,平台不提供额外的编辑、内容补充、找答案等附加服务。
- 2、"仅部分预览"的文档,不可在线预览部分如存在完整性等问题,可反馈申请退款(可完整预览的文档不适用该条件!)。
- 3、如文档侵犯您的权益,请联系客服反馈,我们会尽快为您处理(人工客服工作时间:9:00-18:30)。
( 上接 4 页)
变量方法 单目标( W) 优化 多目标( W1 D) 优 化
表 1 设计结果
参数
悬伸段直 支承段直 支承跨 悬伸段长 主轴孔径 主轴质量 主轴轴端
径 Da/ cm 径 D / cm 距 L / cm 度 a/ cm d / cm
W / kg 位移 D/ mm
91 52
71 78
201 66
g10( x ) = 2- 019x2+ x5 [ 0 ( 6) 主轴刚度限制: 主轴孔径 d 增大会削弱 主轴刚度, 主轴端部的刚度与截面惯性矩成正 比。为了避免过多削弱主轴刚度, 一般取 d/ D [ 0. 7, 故:
g11( x ) =
X X
5 2
-
017 [
0
g12( x ) =
X X
5 1
Abstract: Based on the objective function of minimum weight and minimum displacement, the optimum design of the main parameters of the main shaft for machine tools is made in this paper. compared with the one - objective opt imum design, the multi - object ive design is more pract ical and dependable. Key words: main shafe; main parameter; optimum design
YM = M
a 6E
3 I
a
a
+
2L ( 1I
E)
+
1- E L2
L+ KA
a
+
a KB
式中 M ) ) ) 主轴前端所受力矩( N1cm) 。
机床主轴 前端位移 Y 可认为 是同平面内 的 YF 和 YM 之和, 故有
Y= YF+ YM
( 1)
另外, 机床主轴轴端所受力矩 M 是由切削加工
时切削力 F 引起的, 为了便于设计计算, 取 M= F#2a, 代入到式( 1) 中, 可得
进一步从金相组织观察, 800 e 加热淬火后 存在大块铁素体; 850 e 淬火后只存在少量铁素 体, 硬度明显提高; 900 e 淬火后得到均匀板条 马氏体, 铁 素 体完 全 消失, 硬度 最高; 1000 ~ 1050 e 淬火后马氏体针粗大, 硬度反 而有所降 低。
需要指出, 合金耐磨钢由于合金元素含量
#3#
¼主轴悬伸段长度 a;
½ 主轴内孔直径 d。另外, 主轴 前支承处 刚度为 KA, 后支承处刚度为 KB, 主轴轴端有作 用力 F 和弯矩 M。设:
Da
x1
D
x2
X= L = x3 = [ x1 x2 x3 x4 x5] T
a
x4
d
x5
112 目标函数
机床主轴的变形对加工质量影响很大, 因
此, 对主轴性质的要求, 主要表现为刚度要求, 即主轴伸出端的挠度( 或位移) Y 尽可能小, 所
a ) ) ) 主轴悬伸段长度( cm) ; d ) ) ) 主轴内孔直径( cm) ;
KA ) ) ) 前支承刚度( N / cm) ;
KB ) ) ) 后支承刚度( N / cm) ;
E ) ) ) 前支承反力矩系数( 取 E= 0. 45) 。
只考虑力矩 M 作用在主轴前端时, 主轴前
端产生位移 YM 为:
1 KA
1+
212X X3
4
+
11
4025X
2 4
X
2 3
+
11 65 KB
X
2 4
X
2 3
同理, 减小主轴的质量在实际工作中具有
重要意义。因此, 本文以质量最小作为机床主
轴优化设计追求的目标之二, 有
W= P4Q[ ( D 2a- d 2) #a+ ( D 2- d2)#L ] 式中 Q) ) ) 金属密度( kg/ cm3)
81 15 3
51 013
71 75
01 0056
12. 13
8. 20
25. 05
8. 22
5. 34
11. 91 0. 0021
从表中可以看出, 多目标优化设计方案比 单目标优化设计方案有明显改善, 特别是支承 跨距 L 和悬伸段直径D a 和长度a 这 3 项, 由于 单目标优化追求目标是最小质量, 因此, 优化结 果是其范围内的下限值, 虽然主轴质量较小, 但 主轴轴端位移已超过允许范围; 而在多目标的 优化中, 这 3 项都取到其范围内的中间值, 这反 映了优化结果不但考虑到主轴质量, 而且考虑 到了主轴的刚度。虽然主轴质量有所增加, 但 其轴端位移已达到了设计要求。所以说, 多目 标优化结果更加合理, 更加切合实际, 可以提高 主轴的可靠性。
A1=
1 21 6
@
103,
A2=
112, 经优化得
出的结果如表 1 所示。
( 下转 17 页)
第1 期
饶启昌, 等: 耐磨材料热处理问题的探讨
#17#
表 1 ZG30CrMnSiMoV 淬火加热温度对其硬 度的影响
淬火加热温度/ e 800 850 900 1000 1050
硬度 HRC
2815 4816 4918 4916 4810
-
0165 [
0
( 7) 主轴前后支 承刚度的确定: 见 图 2, 轴
承刚度随轴颈增大而增长。以 318200 系列为
例, 解得:
D
U-
01006K
2 A
+
018KA +
1.
75
得 KA ·2030- ( 4736- 16617X 2) 1/ 2 又 KB = BKA
式中 B) ) ) 系数, 取 0175~ 0. 5 将 KA 、KB 代入 ( 2) 式, 可进行多目标函数
摘 要: 以最小质量和最小轴端位移为目标函数, 对机床主 轴主参数进 行多目标 优化设 计, 与仅以
最小质量为目标函数的优化设计相 比, 其数据更实际、更可靠。
关键词: 机床主轴; 主参数; 优化设计
中图分类号: TP391172: TG50211
文献标识码: B
文章编号: 1006- 6446( 2000) 01- 0002- 03
#4#
水利电力机械
2000 年 2 月
令 f 2( x ) = W= P4Q[ ( x 21- x25)#x 4+ ( x 22x 25) #x 3]
则多目标函数为
F ( x ) = min{ A1f 1( x ) + A2f 2( x ) }
( 2)
式中 A1、A2 ) ) ) 加权值;
f1( x ) 、f2( x ) ) ) ) 目标函数。
参考文献:
[ 1] 孙靖民 1 机械优化设计 [ M]1 哈尔滨工 业大学 出 版社, 19851
[ 2] 李庆芳 1 刚 性镗销 主轴 优化设 计软 件[ J] 1 组 合 机床与自动化加工技术, 19911
[ 3] 戴 曙 1 金属切削机床 设计[ M ]1 机械 工业出 版 社, 19851
作者简介: 储开宇( 1963- ) , 男, 江苏东台 人, 华北电 力 大学机械系讲师; 杜必 强( 1974- ) , 男, 江 西吉安 人, 华 北电力大学 机械 系讲 师; 段松 屏( 1942- ) , 男, 河北 任 丘人, 华北电力大学机械系副教授。
0 引言
在金属切削机床的设计中, 机床主轴的结 构复杂, 价格昂贵, 是机床最重要的部件之一。 而主轴又是刚度薄弱的环节, 它的前端安装着 卡盘与工件, 直接参与切削加工, 主轴的变形和 振动对机床的加工精度和表面质量影响最大。 因此, 机床设计的成功关键取决于主轴设计的 优劣。主轴设计主要是根据零件的加工条件、 加工要求、机床配置参数和结构等合理地选择 主轴的主参数。而参数选择是否合适将对机床 最终的加工精度产生直接影响, 并决定机床的 加工质量和使用性能。
#2#
#设计计算#
水利电力机械
2000 年 2 月
机床主轴主参数的优化设计
An optimum design of the main parameters of the main shaft for machine tools 储开宇, 杜必强, 段松屏
( 华北电力大学 机械系, 河北 保定 071003)
g4( x ) = 7- x2 [ 0
( 3) 支承跨距 L: 支承跨距 L 应为一个适当 值, 过大过小对主轴的变形和质量都有影响, 取 值范围为 20 [ L [ 65, 所以
g5( x ) = x3- 65 [ 0
g6( x ) = 20- x3 [ 0
( 4) 主轴悬伸段长度 a: 其大小对主轴刚度 和质量都有影响, 一般 a= 8~ 15
的优化计算。
2 优化方法和计算实例
由此建立的数学模型可以看出, 它是一个
具有 5 个设计变量, 12 个约束条件的有约束非
线性问题, 故采用 SUMT 惩罚函数内点法求解。
现设计一机床主轴, 知主轴轴端受力 P =
14. 7kN, 前后支承选 318200 系列轴承, KB = 0. 5
KA , 加权值取
113 约束条件 ( 1) 主轴悬伸段直径 Da: 据经验, 其取值范
围一般为 8 [ Da [ 18, 因此可得 g1( x ) = x1- 18 [ 0
g2( x ) = 8- x1 [ 0