机床主轴结构的优化设计资料
关于数控机床主轴结构的改进设计

关于数控机床主轴结构的改进设计目前,数控机床主轴结构主要包括主轴箱、主轴、轴承和冷却系统等部分。
针对这些部分的改进设计将有助于提高数控机床的性能和使用效果。
下面将从主轴箱结构、主轴结构和轴承结构三个方面进行详细的改进设计讨论。
一、主轴箱结构的改进设计主轴箱结构是数控机床主轴的重要组成部分,其设计对主轴的稳定性、刚性和传动精度等方面有着重要影响。
在当前主轴箱结构中,存在一些问题,如难以满足高速、高功率主轴的需求,容易产生振动和噪音等。
为了解决这些问题,需要对主轴箱结构进行改进设计。
可以采用卧式主轴箱结构替代立式主轴箱结构。
卧式主轴箱结构相对于立式主轴箱结构具有更好的刚性和稳定性,可以有效降低振动和噪音,提高主轴的加工精度和稳定性。
卧式主轴箱结构也更适合于高速、高功率主轴的设计和加工。
可以采用分体式主轴箱结构。
分体式主轴箱结构将主轴箱分为上下两部分,通过精密调整螺母来调整主轴箱的上下间隙,从而使主轴箱具有更好的密封性和刚性。
这种结构不仅可以有效防止主轴箱内部润滑油渗漏,还可以提高主轴箱的动态刚性和热稳定性,有利于主轴的高速、高精度加工。
可以采用陶瓷复合材料制造主轴箱。
陶瓷复合材料具有良好的耐磨性、耐热性和耐腐蚀性,通过采用陶瓷复合材料制造主轴箱,可以有效提高主轴箱的使用寿命和可靠性。
陶瓷复合材料还具有较低的热膨胀系数和较高的热导率,有利于主轴箱的热稳定性和散热性能。
可以采用空气动力主轴结构替代机械传动主轴结构。
空气动力主轴结构采用气体压力来传递动力,不需要传统的机械传动部件,可以实现零摩擦、零磨损的运转。
空气动力主轴结构的传动效率高、温升小、运转平稳性好,有利于提高主轴的加工精度和稳定性。
可以采用磁悬浮主轴结构。
磁悬浮主轴结构通过磁场来支撑和传递动力,不需要机械轴承,可以实现无接触、无摩擦的运转。
磁悬浮主轴结构具有较高的刚性和稳定性,可以有效降低振动和噪音,提高主轴的加工精度和寿命。
可以采用弹性变形主轴结构。
机床主轴结构优化设计

机床主轴结构优化设计指导老师:姓名:学号:机床主轴结构优化设计一.机械优化设计的一般过程① 建立优化设计的数学模型② 选择适当的优化方法③ 编写计算机程序④ 准备必要的初始数据并上机计算⑤ 对计算机求得的结果进行必要的分析其中,建立优化设计的数学模型是首要的和关键的一步,其基本原则仃: 1、 设计变量的选择在充分了解设计要求的基础上,应根据各设计参数对目标函数的彤响程度认真分析 其主次,尽最减少设计变最的数目,以简化优化设计问题。
另外,还应注意设计变 量应当相互独立,否则会使目标函数出现“山脊”或“沟谷”,给优化带来困难。
2、 目标函数的确定常取其中最主要的指标作为目标函数,而其余的指标列为约束条件。
3、 约束条件的确定在选取约束条件时应当避免出现相互矛盾的约朿。
因为相互矛盾的约束必然 导致可行域为一空集,使问题的解不存在。
另外应当尽量减少不必要的约束。
不必要的约束不仅增加优化设计的计算臺,而且可能使可行域缩小,影响优 化结果。
二、优化实例机床主轴是机床中重耍零件之般为多支承空心阶梯轴。
为了便丁使用材料力 学公式进行结构分析,常将阶梯轴简化成以当量直径表示的等截面轴。
下面以两支 承主轴为例,说明优化设计的全过程。
右图所示的是一个己经简化的机床主轴。
已知主轴内 径d=30mm,外力 215000N,许用挠度 yO=O. 05mm« 主 轴材料是铸钢。
密度p = 7.8 x 10"6Kg/ mm 3,弹性模 * E=210GPa 设计变量数n=3,约束函数个数m=5,设 计变量的初值、上下限列于设计变量 XIX2 X3 初始值 480100 120 下限值 30060 90 上限值 650 140 150 表8-1初始数据-- --- ―一殳表8-1中。
设计变量的确定当主轴的材料选定时,其设计方案由四个设计变量决定。
即孔径d 、外径D 、跨距1及外伸端长度a 。
由丁•机床主轴内孔常用于通过待加工的棒料, 其大小由机床型号决定,不能作为设计变量。
关于数控机床主轴结构的改进设计

关于数控机床主轴结构的改进设计数控机床作为现代制造业中的重要设备,其主轴结构的设计对于机床性能和加工质量具有非常重要的影响。
随着制造技术的不断发展,传统的数控机床主轴结构已经不能满足现代制造业对高精度、高效率、高稳定性的需求。
对数控机床主轴结构进行改进设计已成为当今的研究热点之一。
一、数控机床主轴结构的基本形式数控机床主轴结构是由主轴箱、主轴和主轴驱动系统组成的,其中主轴箱起到支撑和导向主轴的作用,主轴承载加工刀具和承受切削负载,主轴驱动系统则负责驱动主轴旋转。
传统的数控机床主轴结构通常采用滚动轴承或滑动轴承支撑主轴,由电机通过皮带传动或直接连接方式驱动主轴旋转。
由于滚动轴承和滑动轴承在高速、高负载工况下易产生磨损和热变形,从而影响机床的加工精度和稳定性。
二、数控机床主轴结构的改进设计方向针对传统数控机床主轴结构存在的问题,现代研究者提出了一系列的改进设计方案,主要包括以下几个方向:采用高速轴承技术、使用直接驱动技术、应用新材料和新工艺等。
这些改进设计方案旨在提高数控机床主轴的转速、承载能力和稳定性,从而提高机床的加工精度和效率。
1. 采用高速轴承技术传统数控机床主轴结构采用的滚动轴承或滑动轴承在高速工况下容易出现磨损和热变形,限制了主轴的转速和稳定性。
而采用高速轴承技术可以有效地提高主轴的转速和承载能力,同时减小主轴的振动和磨损,从而改善机床的加工精度和稳定性。
目前,国内外一些制造商已经开始使用陶瓷轴承和陶瓷滚珠轴承等高速轴承技术来改善数控机床主轴结构。
2. 使用直接驱动技术传统数控机床主轴结构通常采用电机通过皮带传动或直接连接方式来驱动主轴旋转,然而这种方式存在传动效率低、振动大、维护成本高等问题。
使用直接驱动技术成为了现代数控机床主轴结构改进的重要方向。
直接驱动技术通过在主轴内部集成电机,利用电磁力直接驱动主轴旋转,不仅可以减小机床的占地面积,提高传动效率,还可以减小振动和噪音,从而提高机床的加工精度和稳定性。
关于数控机床主轴结构的改进设计

关于数控机床主轴结构的改进设计数控机床主轴是数控机床的关键部件,其性能直接影响机床加工精度和加工效率。
随着数控技术的不断发展,对数控机床主轴结构的要求也越来越高。
为了满足市场对数控机床加工精度的需求,需要对数控机床主轴结构进行改进设计,以提高其性能和可靠性。
一、数控机床主轴结构存在的问题1. 结构复杂:传统的数控机床主轴结构通常采用多个轴承和润滑系统,结构复杂,加工成本高。
2. 刚性不足:部分数控机床主轴刚性不足,加工时容易产生振动和变形,影响加工精度。
3. 温升大:部分数控机床主轴在高速加工时容易产生较大的温升,影响机床稳定性和使用寿命。
4. 维护困难:传统数控机床主轴结构维护和保养较为繁琐,需要定期更换润滑油和轴承。
以上问题严重影响了数控机床的加工精度和稳定性,需要通过改进设计来解决。
二、改进设计方案针对数控机床主轴结构存在的问题,可以采取以下几点改进设计方案:1. 优化结构:采用轴向预紧轴承和径向预紧轴承的组合方式,降低轴承数量,简化结构,减小主轴体积和重量。
2. 提高刚性:采用高强度材料和优化设计,提高数控机床主轴的刚性,减小振动和变形,提高加工精度。
3. 降低温升:采用先进的冷却系统和材料,减小高速加工时的温升,提高机床稳定性和使用寿命。
4. 简化维护:采用自动润滑系统和可拆卸设计,简化维护和保养,减小维护成本和时间。
上述改进设计方案可以有效解决传统数控机床主轴结构存在的问题,提高数控机床的加工精度和稳定性,提升竞争力。
三、改进设计实施过程改进设计实施过程中,需要参考市场需求和技术发展趋势,充分调研国内外同类产品的主轴结构和性能,进行方案比较和优化设计。
1. 方案比较:对不同的数控机床主轴结构方案进行技术比较和性能测试,寻找最适合产品需求的方案。
2. 优化设计:在方案确定后,对数控机床主轴结构进行进一步的优化设计,满足产品性能指标和质量要求。
3. 样机制造:根据优化设计方案制作数控机床主轴样机,进行性能测试和验证,验证设计方案的可行性和有效性。
基于matlab的机床主轴结构优化设计

基于matlab的机床主轴结构优化设计机床主轴是机床的核心部件,其结构设计的好坏直接影响到机床的加工精度和效率。
因此,对机床主轴的结构优化设计具有重要的意义。
本文将介绍基于matlab的机床主轴结构优化设计方法。
一、机床主轴结构分析机床主轴结构一般由主轴箱、主轴轴承、主轴轴颈、主轴电机等组成。
其中,主轴箱是主轴的支撑结构,主轴轴承是主轴的支撑部件,主轴轴颈是主轴的转动部件,主轴电机是主轴的驱动部件。
主轴箱的结构设计应考虑刚度、强度和稳定性等因素,主轴轴承的选型应考虑承载能力、转速和寿命等因素,主轴轴颈的设计应考虑转速、径向载荷和刚度等因素,主轴电机的选型应考虑功率、转速和效率等因素。
二、机床主轴结构优化设计方法1.建立机床主轴有限元模型建立机床主轴有限元模型是机床主轴结构优化设计的基础。
有限元模型应包括主轴箱、主轴轴承、主轴轴颈和主轴电机等部件。
有限元模型应考虑主轴的静态和动态特性,包括主轴的刚度、强度、自然频率和振动模态等。
2.确定机床主轴结构优化目标机床主轴结构优化目标应包括主轴的刚度、强度、自然频率和振动模态等。
优化目标应根据机床主轴的工作条件和加工要求确定。
3.确定机床主轴结构优化设计变量机床主轴结构优化设计变量应包括主轴箱、主轴轴承、主轴轴颈和主轴电机等部件的尺寸、材料和结构参数等。
设计变量应根据机床主轴的工作条件和加工要求确定。
4.建立机床主轴结构优化设计模型机床主轴结构优化设计模型应包括有限元模型、优化目标和设计变量等。
优化模型应考虑主轴的静态和动态特性,包括主轴的刚度、强度、自然频率和振动模态等。
5.进行机床主轴结构优化设计机床主轴结构优化设计应采用优化算法进行求解。
常用的优化算法包括遗传算法、粒子群算法、模拟退火算法等。
优化算法应根据机床主轴的工作条件和加工要求选择。
6.验证机床主轴结构优化设计结果机床主轴结构优化设计结果应进行验证。
验证方法包括有限元分析、试验验证等。
验证结果应与优化设计目标相符合。
某机床主轴的优化设计

某机床主轴的优化设计一、问题来源机床主轴是机床的执行件,它的功用是支承并带动工件或刀具完成表面成形运动,同时还起到传递运动和扭矩、承受切削力和驱动力等载荷的作用,结构复杂,价格昂贵,是机床最重要的部件之一。
主轴的前端安装着卡盘与工件,直接参与切削加工,它的变形和振动对机床的加工精度和表面质量影响最大,直接影响到机床的加工质量和生产率。
因此,机床设计的成功关键取决于主轴设计的优劣。
主轴优化设计是机床设计中主轴设计的有效手段,它可以克服以往设计方法中的盲目性,提高主轴的设计质量、设计效率及设计的科学性和可靠性。
二、已知条件题目中的主轴是一个阶梯轴,支撑采用角接触轴承,机床主轴的输入功率P=1.5kW ,主轴的转速n=940r/min ,主轴的悬臂端受到的切削力F=20kN ,主轴内径d=40mm ,悬臂端许用挠度mm 05.0y 0=,取[]m /121='ϕ,[] 0025.0=θ。
要求主轴两支承跨距(L )为350mm ≤L ≤600mm ,外径(D )为70mm ≤D ≤150mm ,悬臂端长度(a )为80mm ≤a ≤160mm .主轴的材料采用40Cr ,密度3kg/m 7800=ρ。
从机床主轴制造成本和加工精度的要求出发,考虑主轴的自重和外伸段挠度这两个重要因素,选取主轴的质量最轻和最小轴端位移为设计目标,将主轴的刚度作为约束条件。
三、数学建模图1 主轴示意图1设计变量本文设计的机床主轴结构主要由5个参数来确定: (1)主轴悬伸段直径Da ; (2)主轴前后支承间轴径D ; (3)支承跨距L ; (4)主轴悬臂端长度a ; (5)主轴内孔直径d 。
另外,主轴轴端有作用力F 和弯矩M ,设:X=[]Tx x x x 43214321a x x x x a L D D =⎥⎥⎥⎥⎦⎤⎢⎢⎢⎢⎣⎡=⎥⎥⎥⎥⎦⎤⎢⎢⎢⎢⎣⎡2 目标函数在满足主轴传动要求下,减轻重量,节约材料,降低成本.以最小自重为追求的目标.机床主轴的质量:()()[]L d D a d D 4W 2222a⨯-+⨯-=πρ式中:(),令为主轴密度3m /kg ρ()=x f ()()[]3222422a X d X X d D 4W ⨯-+⨯-=πρ目标函数()x f x F min )(=3 约束条件(1)刚度约束机床主轴变形对加工质量影响很大,因此,对主轴的要求主要表现为刚度要求,即主轴伸出端的挠度(或位移)Y 尽可能小。
机床主轴结构优化设计
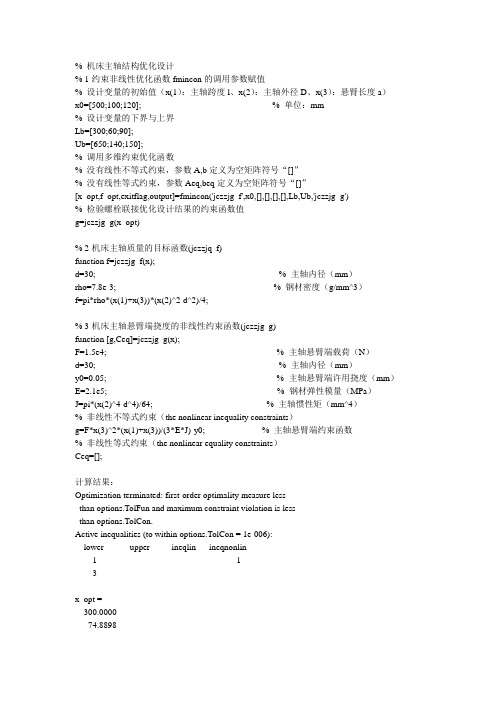
% 机床主轴结构优化设计% 1-约束非线性优化函数fmincon的调用参数赋值% 设计变量的初始值(x(1):主轴跨度l、x(2):主轴外径D、x(3):悬臂长度a)x0=[500;100;120]; % 单位:mm% 设计变量的下界与上界Lb=[300;60;90];Ub=[650;140;150];% 调用多维约束优化函数% 没有线性不等式约束,参数A,b定义为空矩阵符号“[]”% 没有线性等式约束,参数Aeq,beq定义为空矩阵符号“[]”[x_opt,f_opt,exitflag,output]=fmincon('jczzjg_f',x0,[],[],[],[],Lb,Ub,'jczzjg_g')% 检验螺栓联接优化设计结果的约束函数值g=jczzjg_g(x_opt)% 2-机床主轴质量的目标函数(jczzjq_f)function f=jczzjg_f(x);d=30; % 主轴内径(mm)rho=7.8e-3; % 钢材密度(g/mm^3)f=pi*rho*(x(1)+x(3))*(x(2)^2-d^2)/4;% 3-机床主轴悬臂端挠度的非线性约束函数(jczzjg_g)function [g,Ceq]=jczzjg_g(x);F=1.5e4; % 主轴悬臂端载荷(N)d=30; % 主轴内径(mm)y0=0.05; % 主轴悬臂端许用挠度(mm)E=2.1e5; % 钢材弹性模量(MPa)J=pi*(x(2)^4-d^4)/64; % 主轴惯性矩(mm^4)% 非线性不等式约束(the nonlinear inequality constraints)g=F*x(3)^2*(x(1)+x(3))/(3*E*J)-y0; % 主轴悬臂端约束函数% 非线性等式约束(the nonlinear equality constraints)Ceq=[];计算结果:Optimization terminated: first-order optimality measure lessthan options.TolFun and maximum constraint violation is lessthan options.TolCon.Active inequalities (to within options.TolCon = 1e-006):lower upper ineqlin ineqnonlin1 13x_opt =300.000074.889890.0000f_opt =1.1249e+004exitflag =1 % 返回值exitflag>0表示计算收敛output =iterations: 10 % iterations是优化过程中迭代次数funcCount: 51 % funcCount是代入函数值的次数stepsize: 1 % 1algorithm是优化所采用的算法(中等规模,拟牛顿SQP)algorithm: 'medium-scale: SQP, Quasi-Newton, line-search'firstorderopt: 7.5880e-007 % 一阶优化精度cgiterations: []message: [1x144 char]g =-3.4694e-017。
关于数控机床主轴结构的改进设计

关于数控机床主轴结构的改进设计
数控机床是生产加工零件的重要设备,主轴是其中的关键组成部分,作用至关重要。
因此,进行主轴结构的改进设计,旨在提高机床的生产率和加工效率,保证加工精度和质量。
首先,主轴结构要结实耐用,并能够承受高转速和重负荷,以满足机床的功能要求。
主轴结构的改进设计应当采用最经济实惠的材料,可以是铸铁、钢材等。
因此,合理选择和使用这些材料,使其能够维持主轴结构的稳定性和耐用性,从而满足加工的要求。
此外,改进主轴结构的设计还要考虑机床的结构关系,可以采用弹性悬臂结构、矩形结构、二维和三维结构等,以构成数控机床的主要结构。
这些结构不仅可以帮助机床抵抗振动及其影响,而且可以改善负载能力和刚性,同时增加机床的精度和耐用性。
最后,主轴的改进设计还应考虑到控制系统的影响,即控制系统对加工精度的影响。
主轴结构应采用最新的技术,比如电脑数控技术、激光测量技术和传感器技术,以保证机床的加工精度和操作可靠性。
同时,控制系统也应符合人机交互设计原则,使操作更加方便快捷,以实现更高效的加工水平。
综上所述,改进主轴结构的设计是数控机床提高加工效率的关键所在。
有效解决了主轴的材料选择、结构布置和控制系统的问题,可以有效地提高加工精度、保证加工效率,以及加工质量和节省生产成本。
当然,数控机床主轴结构改进设计也需要依据实际情况,通过完善技术设计,才能取得有效的效果。