冲模冲裁件凸凹模尺寸计算
冲裁模刃口尺寸的设计计算

2 计算方法
1)凸模与凹模分开加工:
是指凸模和凹模分别按图样加工至尺寸。 此种方法适用于圆形或形状简单的工件,为了 保证凸、凹模间初始间隙小于最大合理间隙, 不而且仅要凸求、有凹较模高分的别制标造注精公度差。(凸模δp,凹模δd),
1 计算原则
确定凸、凹模刃口尺寸时,必须遵循下述原则: 1 落料模先确定凹模刃口尺寸,其标称尺寸应
取接近或等于制件的最小极限尺寸。
凸模 凹模
凸模 凹模
落料
冲孔
2 冲孔模先确定凸模刃口尺寸,其标称尺寸应 取接近或等于制件的最大极限尺寸。凹模刃口 的标称尺寸应比凸模大一个最小合理间隙。
3 选择刃口制造公差时,要考虑工件精度与模 具精度的关系,既要保证工件的精度要求,又 要保证有合理的间隙值。 工件尺寸公差应按“入体”原则标注为单向公 差。
Dd
(D
x)
0
d
Dp (Dd Z min)0p (D x Z min)0p
式中Dd、Dp—分别为落料凹、凸模标称尺寸(mm);
D——落料件标称尺寸(mm);
△——工件制造公差(mm);
Zmin——凸、凹模最小合理间隙(双边)(mm);
δ p、δd——凸、凹模的制造公差(mm),可查表,或近似计算; X——磨损系数,是为了使冲裁件的实际尺寸尽量接近冲裁件公 并带的中间尺寸,与工件制造精度有关 ,见表3-5
Bp
(B
x)
p 0
冲裁模刃口尺寸的设计计算
冲裁件的尺寸精度主要决定于模具刃口 的尺寸精度,合理间隙的数值也靠模具 刃口尺寸来保证。
冲裁模(冲压模具)课程设计 说明书

弓形连接固定片复合模设计零件名称:弓形连接固定片生产批量:中批量材料:零件材料为08钢,厚度为1.5mm图1-1一、零件工艺性分析弓形双孔连接固定块片是家用发电风扇中的一连接固定零件,零件的精度要求较低,具有较高的强度和刚度。
外形最大尺寸为70mm,属于小型零件。
该零件应中批量生产,外精度不高,只需平整,外轮廓是该零件需要保证的重点。
该零件用到的冲压工序有冲孔、落料,因此可设计冲孔落料复合模生产此零件。
二、工序设计及工艺计算1、排样毛坯最大尺寸70mm,不算太小,为保证冲裁件的质量,模具寿命和操作方便,采用有搭边,单排排样,如下图2-1所示,冲裁件之间的搭边值a=1.5mm,冲裁件与条料件侧边之间的搭边值a=2.3mm。
1图2-1-1计算条料的宽度:B=70+2×2.3+c=74.7(mm)其中c为调料可能的摆动量,c=0.1mm计算条料的步距:A=20+1.5=21.5(mm)图2-1-2一个步距内材料的材料利用率:η=985.182/(74.7*21.5)×100%= 61.34%2、压力中心确定和压力机的选择(1)、冲裁力的计算冲裁力 F p=Lt σb Kp (2-2-1) 其中:由图2-2知,周长L=213.057mm;=900Mpa, 此时,Kp=1,则:材料:08F钢板,查表,σbFp=213.057X1X900X1=191.75(kN) (2-2-2) 根据以上模具结构类型,采用弹性卸料和漏料出件,卸料力F q=KF,取K=0.05,则:F q =0.05×191.75=9.59(kN) (2-2-3)推料力Fq1=nK1Fp,去凹模刃壁垂直部分高度h=5mm,t=1mm,n=5/1=5;取K1=0.06,则:F q1=5X0.06X191.75=57.53(kN) (2-2-4)顶件力Fq2=K2Fp,K2=0.06,则:Fq2=0.06X191.75=11.51 (kN) (2-2-5) 本套模具用到的由压力机提供的有冲裁力和推料力,因此:总冲压力F=FP+ F q1总=191.75+57.53=249.28(kN) (2-2-6) (2)、压力中心的确定压力中心在两小圆垂直中心线上(3)、压力机的选择,取系数为1.3,则选用的压力机公称压力P≥(1.1~1.3) F总=1.3×249.28=324(kN)P≥1.3F总初选压力机公称吨位为400kN,型号为J23-40,其主要工艺参数如下:公称压力:400KN;滑块行程:100mm;行程次数:80次∕分;最大闭合高度:300mm;最大装模高度:220mm;闭合高度调节量:80mm;工作台尺寸(前后×左右):150mm×300mm;模柄孔尺寸:直径50mm,深度70mm;工作垫板:厚度80mm,孔径200mm;电动机功率:1.5kW。
第2章冲裁模设计-4_凹模尺寸计算

(2)凹模外形尺寸(外形及紧固孔布置)1. 外形尺寸(1) 厚度尺寸)(=理mm LP H 6225.0值)修磨量(表=理实h H H 52−+小型 H 实际=10~25mm大型 H 实际≤50mm ,时加固理mm H 50>(2) 长宽尺寸(图2-28),,,理理理H W H W H W 0.25.12.1321≥≥≥两形孔之间最小壁厚不得小于5mm 。
注:W1平滑曲线到凹模边界距离,W2直线到凹模边界距离,W3复杂情况或尖端到凹模边界距离。
2. 紧固件(螺钉、圆柱销)尺寸(1) 直径与配合长度1)直径d 表2-2,通常取理H 31 2)配合长度 通常取d 5.1≥(2) 位置尺寸1)孔心-外部边距离,一般可取1.5d2)孔心-(光滑)孔边距离,一般可取1.5d 。
3)螺孔间距 一般约等于10d例题一已知某冲件如图,求凹模结构尺寸解:求外廓尺寸1. 冲裁周长L =20+20+20+10π=91.4162. 冲裁力P =1.3×91.416×1×200=23768.160(P =1.3lt τ)3. 厚度H(取整数进一位)===理1626.1525.062LP H 考虑刃磨量,据表2-5,刃口厚度h =5,21516==实+H4. 长宽尺寸(1) 边宽 W 1=1.2×16=19.2,W 2=1.5×16=24(2) 压力中心 X 0=0,Y 0=-6.6(压力中心6.656.6432144332211−≈−=++++++=l l l l y l y l y l y l y c ) (3) 长度尺寸20-6.6+W 2=37.4,10+6.6+W 1=35.8压力中心定为凹模几何中心,则凹模长度为2×37.4=74.8=75(进一位取整数)(4) 宽度尺寸20+2W 2 =68∴凹模外形尺寸为75×68×21注:通常凹模板外廓尺寸应按标准选取,可加大取为:80×80×22求紧固孔尺寸 料厚=1抗剪强度20016=5.3进一位取61. 紧固件直径:由d≈H理/3=3如内六角螺钉GB70-85 M6×L圆柱销GB119-86 A6×L A表示过度配合B表示间隙2. 紧固件长度L 紧固件配合长度L’应大于1.5d3. 紧固件位置及数量(1)距边尺寸,取1.5d=9(2)螺孔间距75-2×9=5768-2×9=50(3)销孔位置:销孔边距螺孔中心≥1.5d=9销孔中心距螺孔中心≥2d=12销孔中心距57-2×12=33。
冲压工艺及模具

②当Z过大:
拉伸作用强,挤压作用弱,光亮带窄,相对滑动距
离短,冲件弹性恢复与上相反 。凸凹模磨损大为减轻。
③同一间隙Z:凸模端面比凹模端面磨损小。
凸模侧面比凹模侧面磨损大。 为提高模具寿命,一般采用较大间隙。若采用小间隙 应提高模具硬度,模具制造精度高,表面粗糙度低,并改 善润滑条件,以减小磨损。
冲压件尺寸减小,因此,尺寸误差是两者的综合结果。
② 模具制造精度低,工件的尺寸精度无法保证。
冲裁件内外形能达到的经济精度IT11—14,尺寸越大,精度越高,不
同的冲压件尺寸精度所对应的模具制造精度不同。
(3)间隙对弯曲度的影响(图2-11)
Z增大,h增大,为提高制件的平整度,可加压料板或反向压板,要求 太高可以加整形工序。
二、模具间隙
模具间隙——指凸、凹模刃口间的间缝隙,单边用C表
示,双边用Z表示。 间隙是冲裁模设计的关键尺寸。间隙大小对冲裁件质量和 模具使用寿命都有很大影响。
1、间隙对冲裁件质量的影响(断面、尺寸、形状即
弯曲度)
(1)间隙对断面质量的影响(图2-10)
a——Z过小,断面平直,双光亮带,挤长毛刺薄,易去除。 b——Z合理,有一定的斜度,比较平直,光洁,光亮带1/2-1/3。 c——Z过大,斜度大,粗糙,光亮带小,拉长毛刺厚,难去除。
4. 合理间隙的确定
生产中选用一个适当的范围作为合理间隙,只要间隙在这个范围内, 就可冲出良好产品,这个范围的最小值称为最小合理间隙,最大值称为 最大合理间隙。 新设计模具应采用最小值。
⑴ 理论确定法:
根据两裂纹重合,获得良好断面依据。
单边 c=t(1—ho/t)tgβ ho/t——相对压入深度
β ——裂纹与垂线间夹角
冲裁模刃口尺寸的计算2

0.03 mm 35.690 mm
0 DT DA Z min t (35 .69 0.04) 0 mm 35 . 65 0.02 0.02 mm
校核: 0.03 + 0.02 = 0.05 > 0.02 (不能满足间隙公差条件), 因此,只有缩小,提高制造精度,才能保证间隙在合理范围内, 由此可取:
冲裁模具刃口尺寸计算实例
图表数据请参考《冲压工艺与模具 设计》
第二章 冲裁工艺与冲裁模设计 2.5 冲裁模工作部分尺寸的计算
——实例
冲制图示零件,材料为Q235钢,料厚 t=0.5mm。计算冲裁凸、凹模刃口尺寸及 公差。 解:由图可知,该零件属于无特殊要求 的一般冲孔、落料。 0.12 2 6 mm mm 外形 360 由落料获得, 0 0.62
2.5 冲裁模工作部分尺寸的计算 ——单配加工实例
凸模的刃口尺寸按 凹模实际尺寸配置, 并保证双面间隙 0.04~0.06.凸模基本尺 寸和凹模相同,如右 图.
116tu 115.57m m 34tu 33.69m m 17tu 16.79m m 14tu 14.22m m 82tu 82.2m m
A类尺寸: 0.43 140 B类尺寸: 0.4 820 C类尺寸: 按照配合加工 时凹模刃口计算 公式:
0 0 1160 , 34 , 17 0.87 0.62 0.43
116ao (116 0.5 * 0.87) 0 34ao (34 0.5 * 0.62) 17ao (17 0.5 * 0.43)
360 0.62 mm 查表2.6 ,取x = 0.5;
设凸、凹模制造公差查表2-7,则δT=-0.02,δA=+0.02
冲裁模凸模与凹模刃口尺寸的计算

冲压工艺与模具设计冲裁模凸模与凹模刃口尺寸的计算落料件大端尺寸冲孔件小端尺寸1、 基准件的确定 落料件尺寸由凹模尺寸决定,以凹模为基准,间隙取在凸模上; 冲孔件尺寸由凸模尺寸决定;以凸模为基准, 间隙取在凹模上。
2.3.1 凸模、凹模刃口尺寸计算的依据和原则2、考虑冲模的磨损规律 落料模:凹模基本尺寸应取落料件公差范围的较小尺寸; 冲孔模:凸模基本尺寸应取冲孔件公差范围的较大尺寸。
冲裁间隙采用最小合理间隙值3、制件和冲模刃口尺寸偏差应按“入体”原则标注“入体”原则:向材料实体方向单向标注落料件和凸模上偏差为零,下偏差为负;冲孔件和凹模上偏差为正,下偏差为零。
2.3.2 凸、凹模刃口尺寸的计算方法图 2.3.1冲模的制造公差与冲裁间隙之间关系图 a)落料;b)冲孔 1、凸模与凹模分别加工计算模具刃口尺寸分开加工:是指凸模和凹模分别按图纸标注的尺寸和公差进行加工特点:制造周期短,互换性好,但是间隙受模具制造影响,适合于简单形状的冲压件。
冲模的制造公差与冲裁间隙之间应满足:∣δp∣+ ∣δd∣≤2c max-2c minδp ——凸模下偏差;δd——凹模上偏差。
若:∣δp∣+ ∣δd∣>2c max-2c min取δp = 0.4(2c max-2c min) ;δd = 0.6(2c max-2c min)(1)落料(以凹模为基准,先确定凹模尺寸)落料凹模的尺寸:D d=(D max-xΔ)0+ δd落料凸模的尺寸:D p=(D d- 2c min)0-δp(2)冲孔(以凸模为基准,先确定凸模尺寸)冲孔凸模的尺寸:d p=(d min+ xΔ)0-δp冲孔凹模的尺寸:d d=(d p+2c min)0+ δd(3)凹模型孔中心距:L d=(L min+0.5Δ)±0.125Δ2、凸模和凹模配制加工计算刃口尺寸按尺寸和公差制造出凹模或凸模其中一个(基准件),然后依此为基准再按最小合理间隙配作另一件。
冲裁模配合间隙及凸凹模公差设定

选用冲裁间隙的依据和原则
遇到下列情况应加大间隙值
1、厚料冲小孔,即冲孔直径小于料厚
2、同样条件下,冲孔间隙比落料可大些
3、硬质合金冲模需加大30%
4、凹模壁或复合模的凸、凹模壁较薄时
5、硅钢片料中含硅量大
6、高速冲压时,如冲程次数超过200次/min时,模具易发热,需增大10%左右
遇到下列情况应减小间隙值
1、凹模为斜刃口
2、采用电火花穿孔加工凹模型孔的,间隙值应比磨削加工取小(0.2%-0.3%)t
3、加热冲裁
4、冲孔后需攻螺纹的制件
间隙方向的确定原则
1、落料时,因制件尺寸随凹模尺寸而定,故间隙应在减小凸模尺寸方向取得
2、冲孔时,因孔尺寸随凸模尺寸而定,故间隙应在增大凹模尺寸方向取得
考虑到凸、凹模的磨损,尺寸将有变化,在制造新模具时,应采用最小合理间隙。
计算凸凹模尺寸
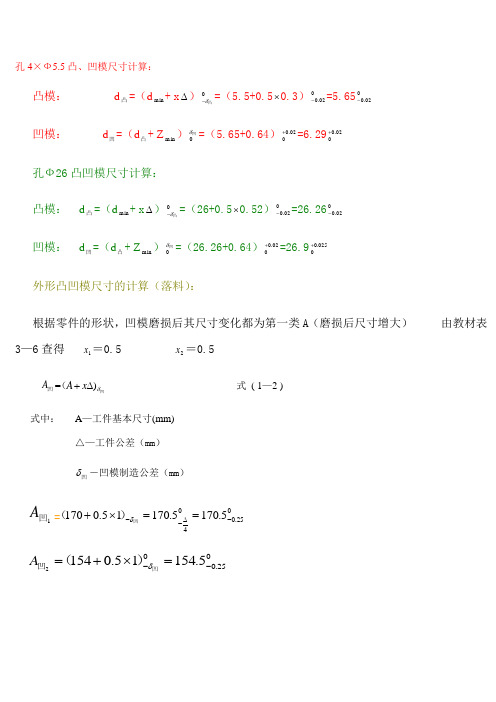
孔4×Ф5.5凸、凹模尺寸计算:凸模: d 凸=(d min + x ∆)0凸δ-=(5.5+0.5⨯0.3)002.0-=5.65002.0- 凹模: d 凹=(d 凸+ Z min )凹δ0=(5.65+0.64)02.00+=6.2902.00+ 孔Ф26凸凹模尺寸计算:凸模: d 凸=(d min + x ∆)0凸δ-=(26+0.5⨯0.52)002.0-=26.26002.0- 凹模: d 凹=(d 凸+ Z min )凹δ0=(26.26+0.64)02.00+=26.9025.00+ 外形凸凹模尺寸的计算(落料):根据零件的形状,凹模磨损后其尺寸变化都为第一类A (磨损后尺寸增大) 由教材表3—6查得 1x =0.5 2x =0.5凹A =凹(δ)∆+x A 式 ( 1—2 ) 式中: A —工件基本尺寸(mm) △—工件公差(mm ) 凹δ-凹模制造公差(mm )1凹A =025.0045.1705.17015.0170-∆--==⨯+凹)(δ025.005.15415.01542--=⨯+=凹)(凹δA凹模的外形一般有矩形与原形两种。
凹模的外形尺寸应保证凹模有足够的强度与刚度。
凹模的厚度还应包括使用期内的修磨量。
凹模的外形尺寸一般是根据材料的厚度和冲裁件的最大外形尺寸来确定的。
查《冲压工艺及模具设计》万战胜主编中国铁道出版社表2—22 凹模外形尺寸得凹模最小壁厚C=52mm 凹模厚度H=36mm故凹模板的外形尺寸:长 L=L1+2C=170+52×2=274mm宽 B=L2+2C=154+52×2=258mm故L×B×H=274×258×36 mm又查《模具手册之四—冲模设计手册》编写组编著机械工业出版社表14-6 矩形和圆形凹模外行尺寸(GB2858-81)将上述尺寸改为315×250×40mm。
- 1、下载文档前请自行甄别文档内容的完整性,平台不提供额外的编辑、内容补充、找答案等附加服务。
- 2、"仅部分预览"的文档,不可在线预览部分如存在完整性等问题,可反馈申请退款(可完整预览的文档不适用该条件!)。
- 3、如文档侵犯您的权益,请联系客服反馈,我们会尽快为您处理(人工客服工作时间:9:00-18:30)。
Security Classification
Date6ຫໍສະໝຸດ 经验公式如下: PX=KX*P(N) PT=nKX*P(N) PD=Kd *P(N) 式中, PX 、PT 、PD------分別为卸料力,推件力和頂件力系数 P------冲裁力 n------同时卡在凹模洞口內的落料件数.n=H/t,H为凹模刃壁垂直 部分高度,t为料厚.当采用锥形洞口时,因无落料件卡在洞口 內,故可不计推件力.
冲压力是指冲裁时,压力机应给出的最小压力。冲 压力是冲裁力,卸料力,推件力和顶出力的总称。 冲裁力的计算公式: P=KLtτ (N) P----冲裁力(N) L----冲裁件周边长度(MM) τ ----材料的抗剪程度(MPA) t----料的厚度(MM) k----系数通常k=1.3
Security Classification
Security Classification Date 8
如有不同意见敬请赐教! 让我们共同进步!
Thanks!
DCS L&P Stamping Team
DEC 2010
Security Classification
Date
9
Date
3
2、降低冲裁力的方法
(1) 斜刃口及波形刃口冲裁法
Security Classification
Date
4
(2) 阶梯凸模冲裁法
Security Classification
Date
5
3、卸料力,推件力,頂件力的計算
卸料力是将箍在凸模上的板料卸下时所需要的力;推料力是 将落料件顺着冲裁凹模洞口推出时所需的力;頂件力是将落料件 逆着冲裁方向顶出凹模刃口时所需的力。
2. 凸、凹模分开加工
凸、凹模分开加工,是指凸模与凹模分別按图加工尺寸,要求 凸、凹模具有互换性,便于成批制造。
3. 凸凹模配合加工时
采用配合加工法,即先加工凸模(或凹模)。这种加工法 容易保证凸凹模间的间隙。
Security Classification
Date
2
冲压力计算:
1. 冲裁力的定义及计算
4. 冲压力的计算
(1) 当冲模采用弹性卸料装置,自然漏料方式冲床要同时克服压 缩 卸料弹簧的弹力、冲裁力、推件力,故冲压力按下式计算: P沖=P+Px+Pt(N)
Security Classification
Date
7
(2) 当冲模采用弹性卸料装置和弹性顶件装置冲裁时,冲床要同时克 服卸料装置和顶件装置的弹力及冲裁力;故冲压力按下式计算. P沖=P+Px+Pd(N)
(3) 当冲模采用钢性卸料装置 , 自然漏料方式冲裁时因钢性料是凸 模在冲裁结束后, 回程时, 实现卸料的, 因此 , 卸料力可以不考虑, 故 冲压力可按下式计算.
P冲=P+Pt(N)
式中P冲------冲床具有的最小冲压力 P------冲裁力 Px------卸料力 Pt ------推件力 Pd ------顶件力
冲裁件的凸凹模
尺寸计算
DCS L&P Stamping Team
DEC 2010
Security Classification
冲裁件的凸、凹模尺寸计算
1. 凸、凹模尺寸计算原则
(1) 落料时,先确定凹模刃口尺寸,其大小应取接近于或等 于制件孔的最大极限尺寸。 (2) 冲孔时,凸模刃口尺寸其大小应接近于或等于冲件孔的 最大極限尺寸。