压缩模脱模机构设计
脱模机构设计
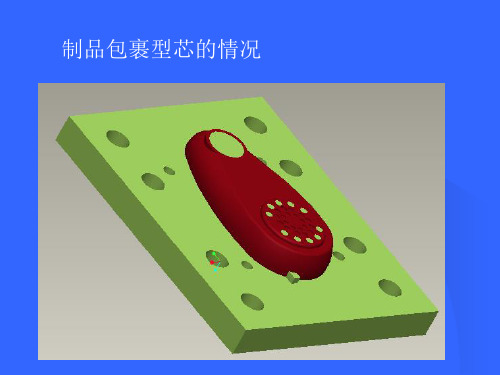
2、 滑块二级脱模
六、二级脱模机构
3、摆杆二级脱模
3、摆杆二级脱模
3、摆杆二级脱模
六、二级脱模机构
4、U形限制架二级脱模
4、U形限制架二级脱模
4、U形限制架二级脱模
4、U形限制架二级脱模
第六节 塑件脱模机构设计
七、浇注系统凝料的自动脱落
七、浇注系统凝料的自动脱落
五、顺序脱模机构
(1)弹簧顺序脱模 限位杆的设计:
限位杆的长度; 限位杆的直径; 型腔板的支撑。
五、顺序脱模机构
(2) 尼龙销顺序脱模
五、顺序脱模机构
(3)拉钩顺序脱模
第六节 塑件脱模机构设计
六、二级脱模机构
1、摆块二级脱模
1、摆块二级脱模
1、摆块二级脱模
1、摆块二级脱模
六、二级脱模机构
2. 按模具结构分: 简单脱模机构 顺序脱模机构 二次脱模机构
二、脱模力的计算
(一)薄壁件的脱模力 当制品的璧厚与型芯直径的比小于0.05时,我 们称其为薄璧制品,其脱模力可按下式计算。 1.1 型芯为圆形截面
2π tESL cos α ( f − tg α ) Q= (1 − µ ) k
1.2 型芯为矩形截面
b 方形顶杆 Ebw 3 方形顶杆的脱模阻力F = 4.9 2
L
其中:b—方形顶杆长度方向上的尺寸, cm; w—方形顶杆宽度方向上的尺寸,cm。
(8)顶杆的位置分布 顶杆的位置分布以对 注射机顶杆中心的合力矩为零为最佳,一 般情况下,顶杆的数目以少为宜,且均匀 分布。 (9)材料:45 、T8 、T10等,头部淬火 HRC>50。 表面粗糙度:配合部分 (10 )顶杆行程:一般情况下,大于制品型 芯的高度。
第四章 推出机构的设计6

•
压缩空气配合推板脱模
• 设置引气装置以后:
4. 推块推出机构 平板状带凸缘的塑件,如 用推板件推出会黏附模具 时,则应使用推块推出机 构推出,如图所示。推块 是型腔的组成部分,因此 应有较高的硬度和较低的 表面粗糙度值,推块与型 腔及型芯应有良好的间隙 配合,既要求滑动灵活, 又不允许溢料。推块所使 用的推杆与模板不必要求 精度很高的配合。
难,同时因增加推件板而使模具质量增加。12
为减少脱模过程中推件板与 型芯之间的摩擦,两者之间 留有0.2~ 0.25mm的间隙, 并采用锥面配合,以防止推 件板 偏斜溢料,锥面的斜 度约取3~5˚左右,
4
推件板推出机构形式-4zzzzz 对于大型深腔的容器,尤其是采用软质塑料时, 如果用推件板脱模,应考虑附设引气装置,以防止在 脱模过程中内腔形成真空,造成脱模困难,甚至使塑 件变形损坏(见下图)。
(4)推管外径应比塑件外壁尺寸小0.5mm左右;推管内 径比塑件内径每边大0.2 ~0.5mm。 (5)推管与型芯的配合长度比推出行程S长3~5 mm,推 管与模板的配合长度一般为(1.5~2)D;其余部分扩 孔,推管扩孔d+l,模板扩孔D十1。推管的厚度一般取 1.5 ~5mm,以保证刚性。
• 3. 推件板推出机 构 • 深腔薄壁的容器、 壳体形塑件以及 不允许有推杆痕 迹的塑件都可采 用推件板推出机 构。推件板推出 机构的结构形式 与原理如图所示。
2、影响塑件脱模力的因素: 1) 脱模力的大小主要与塑件包络型芯侧面积的大小有关 2)脱模力大小与型芯的脱模斜度有关 脱模斜度越大,脱模力越小。 3) 脱模力的大小与型芯的表面粗糙度有关 表面粗糙度值越低,型芯表面越光洁,所需的脱 模力 就越小。 4) 脱模力的大小与塑件的结构有关 塑件厚度越大、形状越复杂,冷却凝固时所引起的包 紧力和收缩应力越大,则所需的脱模力越大。 5)脱模力的大小还与塑件底部是否有孔有关。
模具设计第5章 压缩模设计

(3)挤压环( l 3 )
它的作用是在半溢式 压缩模中用以限制凸模下 行的位置,并保证最薄的 飞边。挤压环l3值视塑件 大小及模具用钢而定。一 般中小型塑件,模具用钢 较好时l3可取2~4mm;大 型模具,l3可取3~5mm。 采用挤压环时,凸模端圆 角R取0.5~0.8mm,凹模 端圆角R取0.3~0.5mm。
(2)配合环( l 1 )
它是凸、凹模配合的部位, 保证凸、凹模正确定位,阻止 溢料,通畅地排气。凸、凹模 的配合间隙以不产生溢料和不 擦伤模壁为原则,单边间隙一 般取0.025~0.075mm,也可采用 H8/f7或H9/f9配合,移动式模 具间隙取小值,固定式模具间 取较大值。配合长度l1,移动 式模具取4~6mm,固定式模具, 当加料腔高度h1≥30mm时,可 取8~10mm。间隙小取小值,间 隙大取大值。
3. 按分型面特征分类
(1) 水平分型面压缩模 (2) 垂直分型面压缩模
5.2 压缩模与压机的关系 5.2.1 压机种类与技术规范 1. 压机种类 压机的型式种类很多,分类的方法也不 一致。按传动方式压机可分为机械式和液压 式两种。 液压机是热固性塑料模压成型所用的主 要成型设备。我国标准的液压机以立式为主, 机架结构可分为框架连接及立柱连接两类。
(2)半溢式压缩模(又称半封闭式压缩模) 半溢式压缩模如图5-4所示。
由于这种模具有以上 该模具的特点是在型腔上 优点,因而应用较广泛。 在每一循环压制中加料量 方设一断面尺寸大于塑件 适用于成型流动性较好 稍有过量,过剩的原料通 尺寸的加料腔,凸模与加 塑料及形状较复杂的、 过配合间隙或在凸模上开 料腔呈间隙配合。加料腔 带有小型嵌件的塑件。 设专门的溢料槽排出。溢 与型腔分界处有一环形挤 料速度可通过间隙大小和 但半溢式压缩模由 压面,对中小型模具其宽 溢料槽多少进行调节,其 于有挤压边,故不适于 度为 2~4mm,大型模具其 塑件的致密度比溢式压缩 压制以布片或长纤维作 宽度为 3~5mm,凸模下压 模好。 填料的塑料。 到与挤压面接触时为止
第五章压缩成型工艺与模具设计

•压缩模类型选用原则
•塑件批量大•—— 固定式模具 •批量中等•—— 固定式或半固定式模具 •小批量或试生产•—— 移动式模具
•水平分型面模具结构简单,操作方便,优先选用。
•流动性差的塑料,塑件形状复杂•——不溢式模具 •塑件高度尺寸要求高,带有小型嵌件•—— 半溢式模具 •形状简单,大而扁平的盘形塑件•—— 溢式压缩模
▪特别适合压制有棉布、玻璃布、长纤维 填充的制品; ▪飞边与分型面垂直分布,便于去除。
5、不溢式压缩模 ➢不溢式压模特点:
▪因溢料量很少,加料精度直接影响制品高度尺寸,要求准确计量; ▪型芯与型腔侧壁摩擦严重,制品脱模易刮擦,改进结构见图所示; ▪不溢式压模必须设脱模机构。
6、半溢式压缩模
➢半溢式压模特点:
6、半溢式压缩模
➢半溢式压模改进: ▪将加料腔制成可移动式,方便挤压面和模具型腔的清理 。
7、多型腔压缩模
➢多型腔压模:如图,可为溢式或半溢式结构,图a)、b) 需对每个型腔单独加料,个别型腔损坏不影响模具工作。
7、多型腔压缩模
➢为方便多腔模加料,可 采用右图所示的加料器 快速加料。
➢多腔共用加料室有利于 缩小模具尺寸,方便加料 ,但边角的型腔易缺料。
第五章压缩成型工艺与 模具设计
2020年7月10日星期五
第五章 压缩成型工艺及模具设计
•成型压缩原理
一、 压缩成型原理及特点
压缩成型原理 压缩成型特点
•压缩成型过程 •原料放入模具 •加热加压使材料成型硬化 •取出塑件
•一、 压缩成型原理:
将塑料加入高温的型腔和加料室,然 后以一定的速度将模具闭合,塑料在热和压 力的作用下熔融流动,并且很快地充满整个 型腔,树脂和固化剂作用发生交联反应,生 成不熔不溶的体型化合物,塑料因而固化, 成为具有一定形状的制品,当制品完全定型 并且具有最佳性能时,即开启模具取出制品.
脱模机构的设计与加工教案
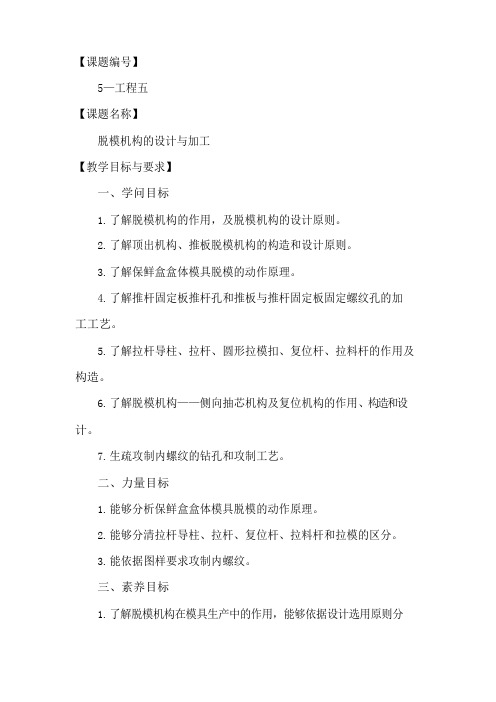
【课题编号】5—工程五【课题名称】脱模机构的设计与加工【教学目标与要求】一、学问目标1.了解脱模机构的作用,及脱模机构的设计原则。
2.了解顶出机构、推板脱模机构的构造和设计原则。
3.了解保鲜盒盒体模具脱模的动作原理。
4.了解推杆固定板推杆孔和推板与推杆固定板固定螺纹孔的加工工艺。
5.了解拉杆导柱、拉杆、圆形拉模扣、复位杆、拉料杆的作用及构造。
6.了解脱模机构——侧向抽芯机构及复位机构的作用、构造和设计。
7.生疏攻制内螺纹的钻孔和攻制工艺。
二、力量目标1.能够分析保鲜盒盒体模具脱模的动作原理。
2.能够分清拉杆导柱、拉杆、复位杆、拉料杆和拉模的区分。
3.能依据图样要求攻制内螺纹。
三、素养目标1.了解脱模机构在模具生产中的作用,能够依据设计选用原则分析保鲜盒脱模方式的动作过程。
2.了解各种不同杆在脱模机构中的作用,侧向抽芯机构与各种复位机构的作用和构造特点。
3.生疏螺纹孔的钻孔和攻螺纹的过程。
四、教学要求1.了解推杆固定板推杆孔与推板和推杆固定板固定螺纹孔的加工工艺。
2.了解脱模机构的作用、构造及设计原则。
3.能够分析保鲜盒盒体模具脱模方式的动作过程及其优点。
4.了解圆形拉模和安装孔的加工工艺。
5.了解各种杆件在脱模中的作用和构造。
6.了解侧向抽芯机构和复位机构的组成、动作原理及设计方法。
7.把握攻内螺纹的工艺过程。
【教学重点】1.保鲜盒盒体模具脱模过程分析。
2.推杆固定板推杆孔、推板和推杆固定板固定螺纹孔、圆形拉模扣安装孔的加工工艺。
【难点分析】1.脱模机构中的各种机构、构件的设计。
2.侧向抽芯机构和复位机构的作用与设计。
3.攻内螺纹前底孔直径确实定。
【分析学生】要了解脱模机构的构造与设计要求,首先要生疏塑料制作的生产过程,了解脱模机构的作用及动作过程,才能理解脱模机构的构造,设计出合理有用的脱模机构。
侧向抽芯机构的构造比较特别,假设对模具的制作和制件的生产过程不生疏,是比较不简洁理解的。
学生需要具备肯定的根底学问和实践学问后,才能比较简洁理解侧向机构的构造特点。
第10讲-脱模机构设计-PPT
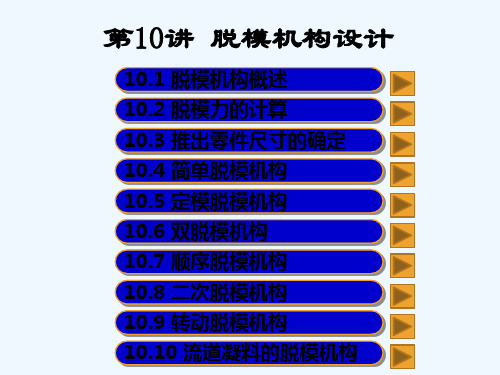
推杆的位置 1-推杆(兼复位杆)2-塑件 3-推杆 4-型芯 5-盘形推杆
10.4.1 常见脱模机构的类型
1.推杆脱模机构
2)应设在塑件强度刚度 较大处。
推杆不宜设在塑件的薄壁
处,应尽可能设在塑件厚壁、
凸缘处及筋与筋或壁与筋的交
点上,以免使塑件变形损坏。
如必须设在薄壁处时,应
增大推杆截面积,以降低单位
大家有疑问的,可以询问和交流
可以互相讨论下,但要小声点
10.2 脱模力的计算
概念
(1)定义:指将塑件从型芯上脱出时所需克服的阻力。 包括:
成型收缩的包紧力; 不带通孔的壳体类塑件的大气压力; 机构运动的摩擦力; 塑件对模具的粘附力;
10.2.1 影响脱模力的因素
(2)影响脱模力的因素
型芯成型部分的表面积及其形状. 收缩率及摩擦系数. 塑件壁厚和包紧型芯的数量. 型芯表面粗糙度. 成型工艺:P注、t冷.
对于生产批量很大的制品,为提高生产率,可 采用结构比较复杂、自动化程度比较高的脱模机构。
10.1.3 推出机构的设计原则
5)推出零件应有足够的强度、刚度和硬度。 6)合模时应正确复位。并保证不与其他模具零 件相干涉。 7)脱模行程应恰当。应保证推出零件运动的初 始位置和终止位置恰当合理,以保证制品可靠脱模。
由上面的式子可以看影响因素脱模力的大小主要有以下几点:
(l)主要与塑件包络型芯侧面积的大小有关。型芯的侧面积越大,所需的脱 模力也越大。 (2)与型芯的脱模斜度有关。脱模斜度越大,所需的脱模力越小。 (3)与型芯的表面粗糙度有关。表面粗糙度值越低,型芯表面越光洁,所需 的脱模力就越小。 (4)与塑件的结构有关。塑件厚度越大、形状越复杂,冷却凝固时所引起的 包紧力和收缩应力越大,则所需的脱模力越大。 (5)与注射工艺有关。 注射压力越大,则包紧型芯的力越大,所需脱模力越大; 脱模时模具温度越高,所需的脱模力越小; 塑件在模内停留时间越长,所需的脱模力越大。 (6)与成型塑件的塑料品种有关。不同的塑料品种,由于分子的结构不一样, 因而它们的脱模力也不一样。
简单脱模机构设计
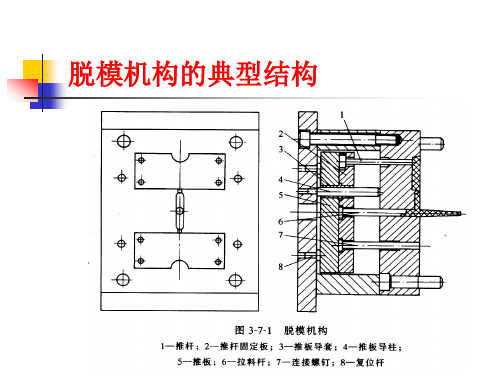
多元脱模方式联合脱模机构
推杆与推件板联合推出机构
多元脱模方式联合脱模机构
推杆与推件板联合推出机构
多元脱模方式联合脱模机构
推杆与推管联合推出机构
多元脱模方式联合脱模机构
推管与推板联合推出机构
脱模机构的典型结构
脱模机构的组成
① 推出元件——推出制件的元件 如推杆、推管、推块、推板及顶针板、面针板等。 ② 复位元件——使推出元件复位 如复位杆(回程杆 )、弹簧等。 ③ 导向元件——对脱模机构起导向作用 如中托司(导柱、导套)。 ④ 传动元件——拖动脱模机构的元件 (指某些螺纹制件的脱模传动) 如齿轮、齿条、链轮、链条等。 ⑤ 限位元件:垃圾钉,限位块。 ⑥ 拉料杆。
推件板脱模机构设计要点
①导向 ②定距 ③摩擦 ④进气
活动镶件脱模机构
气压脱模机构
采用压缩空气推出塑件,塑件受力均匀 且可以简化模具结构,由于不需要在模内设 推板及其运动空间,因此模具总高度可减小。 其推出力为塑件内腔投影面积与气体压强的 乘积,故断面尺寸越大的薄壁壳体越易脱出。
气压脱模机构
气压脱模机构
脱模机构的分类
A)按驱动方式分 1、手动脱模 2、机械脱模 3、液压脱模 4、气压脱模 B)按模具结构分 1)简单脱模机构 2)定模脱模机构 3)双脱模机构 4)顺序脱模机构 5)二级脱模机构
6)浇注系统凝料自动脱出机构
7) 带螺纹制件脱模机构
脱模机构的设计要求
1、脱模机构应动作可靠,结构简单,制造方便。 2、不损坏塑件的外观质量 3、塑件在推出过程中不发生变形和损坏 对模具包紧力和粘附力大小的分析与计算,合理地选择推出的 方式、推出的位置、推出零件的数量和推出面积等。 4、让塑件留于动模 5、合模时应使脱模机构正确复位 在斜导杆和斜导柱侧向抽芯及其他特殊的情况下,还应考虑脱 模机构的先复位问题等
塑件脱模机构设计共56页文档

11、用道德的示范来造就一个人,显然比用法律来约束他更有价值。—— 希腊
12、法律是无私的,对谁都一视同仁。在每件事上,她都不徇私情。—— 托马斯
13、公正的法律限制不了好的自由,因为好人不会去做法律不允许的事 情。——弗劳德
14、法律是为了保护无辜而制定的。——爱略特 15、像房子一样,法律和法律都是相互依存的。——伯克
41、学问是异常珍贵的东西,从任何源泉吸 收都不可耻。——阿卜·日·法拉兹
42、只有在人群中间,才能认识自 己。——德国
43、重复别人所说的话,只需要教育; 而要挑战别人所说的话,则需要头脑。—— 玛丽·佩蒂博恩·普尔
44、卓越的人一大优点是:在不利与艰 难的遭遇里百折不饶。——贝多芬
45、自己的饭量自己知道。—苏联
- 1、下载文档前请自行甄别文档内容的完整性,平台不提供额外的编辑、内容补充、找答案等附加服务。
- 2、"仅部分预览"的文档,不可在线预览部分如存在完整性等问题,可反馈申请退款(可完整预览的文档不适用该条件!)。
- 3、如文档侵犯您的权益,请联系客服反馈,我们会尽快为您处理(人工客服工作时间:9:00-18:30)。
压缩模脱模机构设计
压缩模的脱模(推出)机构与注射模相似,常见的有推杆脱模机构、推管脱模机构、推件板脱模机构等。
6-4-1 固定式压缩机构设计
1. 脱模机构的分类
压缩模的脱模机构按动力来源可分为机动式、气动式、手动式三种。
(1)气动式
气动式脱模机构如图6-27所示,即利用压缩空气直接将塑件吹出模具。
当采用溢式压缩模或少数半溢式压缩模时,如果塑件对型腔的粘附力不大,则可采用气吹脱模方式。
气吹脱模适用于薄壁壳形塑件。
当薄壁壳形塑件对凸模包紧力很小或凸模斜度较大时,开模后塑件会留在凹模中,这时压缩空气吹入塑件与模壁之间因收缩而产生的间隙里,将使塑件升起,如图6-27a所示。
图6-27b为一矩形塑件,其中心有一孔,成型后压缩空气吹破孔内的溢边,压缩空气便会钻入塑件与模壁之间,使塑件脱出。
图6-27 气吹脱模
(2)手动式
手动式脱模机构是利用人工通过手柄,用齿轮齿条传动机构或卸模架等将塑件脱模。
图6-28所示为摇动压力机下方带有齿轮的手柄,齿轮带动齿条上升进行脱模的形式。
图6-28 压力机中的手动推顶装置
1-推杆;2-压力机下工作台;3-手柄;4-齿轮;5-齿条
(3)机动式
机动式脱模机构如图6-29所示。
图6-29a所示是利用压力机下工作台下方的顶出装置推出脱模的形式;图6-29b所示是利用上横梁中的拉杆1随上横梁(上工作台)上升带动托板4向上移动而驱动推杆6推出脱模。
图6-29 压力机推顶装置
l-拉杆;2-压力机工作台;3-活塞杆(顶杆);4-托板;5-液压缸;6-推杆
2. 脱模机构与压力机的连接方式
压力机有的带顶出装置有的不带顶出装置,不带顶出装置的压力机适用于移动式压缩模。
当必须采用固定式压缩模和机动顶出时,可利用压力机上的顶出装置使模具上的推出机构工作推出塑件。
当压力机带有液压顶出装置时,液压缸的活塞杆即为压力机的顶杆,一般活塞杆上升的极限位置是其端部与工作台表面相平齐的位置。
压力机的顶杆与压缩模脱模机构的连接有间接连接和直接连接两种方式。
(1)间接连接
当压力机顶杆端部上升的极限位置只能与工作台面平齐时,必须在顶杆端部旋入一适当长度的尾轴。
尾轴的另一端与压缩模脱模机构无固定连接,如图6-30a所示,尾轴也可以反过来利用螺纹与模具推板相连,如图6-30b所示,但这两种形式都要设计复位杆等复位机构。
图6-30 与压力机顶杆不相连的推出机构
l-下模座板;2-挡销;3-尾轴;4-压力机顶杆
(2)直接连接
如图6-31所示,压力机的顶出机构与压缩模脱模机构通过尾轴固定连接在一起.这种方式在压力机下降过程中,能带动脱模机构复位,故不必再设复位机构。
机动脱模一般应尽量让塑件在分型后留在压力机上有顶出装置的模具一边,然后采用推出机构将塑件从模具中推出。
为了保证塑件准确地留在模具一边,在满足使用要求的前提下可适当地改变塑件的结构特征,如图6-32所示。
为使塑件留在凹模内,图6-32a所示的薄壁件可增加凸模的脱模斜度,减少凹模的脱模斜度;有时也可将凹模制成轻微的反斜度(3’~5’),如图6-32b所示;图6-32c是在凹模型腔内开设0.1~0.2mm的侧凹槽,使塑件留在凹模,开模后塑件从凹模内被强制推出;为了使塑件留在凸模上,可采取与上述相反的方法,图6-32d 所示在凸模上开出环形浅凹槽,开模后塑件由上推杆强制脱出。
图6-31 与压力机顸杆相连的推出机构
图6-32 使塑件留模的方法
2 半固定式压缩模的脱模机构
半固定式压缩模是指压缩模的上模或下模可以从压力机上移出,在上模或下模移出后,再进行塑件脱模和嵌件安装。
(1)带活动上模的压缩模
这类模具可将凸模或模板制成沿导滑槽抽出的形式,故又称抽屉式压缩模.如图6-33所示,开模后塑件留在活动上模2上,用手把l沿导滑板3把活动上模拉出模外取出塑件,然后再把活动上模送回模内。
图6-33 上模活动的压缩模
l-手把;2-活动上模;3-导滑板;4-凹模
(2)带活动下模的压缩模
这类模具的上模是固定的,下模可以移出,图6-34所示为一典型的模外脱模机构。
该脱模机构工作台3与压力机工作台等高,工作台支承在四根立柱8上。
在脱模工作台3上装有宽度可调节的导滑槽2,以适应不同模具宽度。
在脱模工作台正中装有推出板4、推杆和推杆导向板10,推杆与模具上的推出孔相对应,当更换模具时则应调换这几个零件。
工作台下方设有液压推出缸9,在液压缸活塞杆上段有调节推出高度的丝杠6,为了使脱模机构上下运动平稳而设有滑动板5,该板上的导套在导柱7上滑动。
为了将模具固定在正确的位置上,设
有定位板1和可调节的定位螺钉。
开模后将活动下模的凸肩滑人导滑槽2内,并推到与定位板相接触的位置。
开动推出液压缸,推出塑件,待清理和安装嵌件后,将下模重新推入压力机的固定槽中进行下一模的压缩生产。
当下模重量较大时,可以在工作台上沿模具拖动路径设滚柱或滚珠,使下模拖动轻便。
图6-34 模外液压推顸脱模机构
l-定位板;2-导滑槽;3-工作台;4-推出板;5-滑动板;6-丝杠;7-导柱;8-立柱;
9-液压缸;10-推杆导向板
3 移动式压缩模脱模机构
移动式压缩模的脱模方式分为撞击架脱模和卸模架脱模两种形式。
1. 撞击架脱模
撞击架脱模如图6-35所示。
压缩成型后,将模具移至压力机外,在特定的支架上撞击,使上下模分开,然后用手工或简易工具取出塑件。
撞击架脱模的特点是模具结构简单,成本低,可几副模具轮流操作,生产率高。
该方法的缺点是劳动强度大,振动大,而且由于不断撞击,易使模具过早地变形磨损,因此只适用于成型小型塑件。
撞击架脱模的支架形式有两种,如图6-36所示,图6-36a所示是固定式支架,图6-36b所示是尺寸可调节的支架。
图6-35 撞击架脱模
1-模具;2-支架
图6-36 支架形式
2. 卸模架卸模
移动式压缩模可在特制的卸模架上利用压力机的压力进行开模和卸模,这种方法可减轻劳动强度,提高模具使用寿命。
对开模力不大的模具可采用单向卸模,对于开模力大的模具要采用上下卸模架卸模,上下卸模架卸模有下列几种形式:
(1)单分型面卸模架卸模
单分型面卸模架卸模方式如图6-37所示。
卸模时,先将上卸模架1、下卸模架6的推杆插入模具相应的孔内。
在压力机内,当压力机的活动横架即上工作台压到上卸模架或下卸模架时,压力机的压力通过上下卸模架传递给模具,使得凸模2和凹模4分开,同时,下卸模架推动推杆3推出塑件,最后由人工将塑件取出。
图6-37 单分型面卸模架卸模
1-上卸模架;2-凸模;3-推杆;4-凹模;5-下模座板;6-下卸模架
(2)双分型面卸模架卸模
双分型面卸模架卸模方式如图6-38所示。
卸模时,先将上卸模架1、下卸模架5的推杆插入模具的相应孔中。
压力机的活动横梁压到上卸模架或下卸模架时,上下卸模架上的长推杆使上凸模2、下凸模4和凹模3分开。
分模后,凹模3留在上下卸模架的短推杆之间,最后在凹模中取出塑件。
图6-38 双分型面卸模架卸模
l-上卸模架;2-凸模;3-凹模; 4-下凸模;5-下卸模架
(3)垂直分型卸模架卸模
垂直分型卸模架卸模方式如图6-39所示。
卸模时,先将上卸模架l、下卸模架6的推杆插入模具的相应孔中。
压力机的活动横梁压到上卸模架或下卸模架时,上下卸模架的长推杆首先使下凸模5和其它部分分开,当到达一定距离后,再使上凸模2,模套4和凹模3分开。
塑件留在瓣合凹模中,最后打开瓣合凹模取出塑件。
图6-39 垂直分型卸模架卸模
1-上卸模架;2-上凸模;3-瓣合凹模;4-模套;5-下凸模;6-下卸模架。