复合材料-组合模型
复合材料用有限元分析

复合材料用有限元分析引言复合材料是由不同类型的材料组合而成的,具有优异的力学性能和轻质化的特点,在航空航天、汽车工程、建筑结构等领域得到广泛应用。
有限元分析是一种常用的工程分析方法,可用于预测复合材料结构在受力过程中的应力和变形情况。
本文将介绍复合材料用有限元分析的基本原理、建模过程、分析方法和结果解读。
有限元分析基本原理有限元分析基于有限元法,将复杂的结构分割成许多简单的单元,再利用数学方法求解这些单元的力学行为,最终得出整个结构的应力和变形情况。
复合材料的有限元分析一般采用3D固体单元或板单元,考虑复合材料的各向异性和层合板的分层结构。
有限元分析的基本原理可以总结为以下几个步骤:1.确定有限元模型:–根据复合材料结构的几何形状和材料性质,选择适当的有限元单元类型。
–确定网格划分方案,将结构划分为单元网格。
–确定边界条件和加载方式,包括约束条件和外部加载。
2.确定单元性质:–根据复合材料的材料力学性质,将其转化为有限元单元的材料刚度矩阵。
–考虑各向异性和分层结构,将材料刚度矩阵进行相应的转换。
3.确定单元相互连接关系:–根据结构的几何体系,确定单元之间的连接关系,包括单元之间的约束和边界条件。
4.求解方程组:–根据单元的刚度矩阵和边界条件,建立整个结构的刚度矩阵。
–考虑加载情况,求解结构的位移和应力。
5.结果后处理:–分析结构的应力和变形分布,评估结构的安全性和性能。
–对结果进行解读和优化。
复合材料有限元分析的建模过程复合材料的有限元分析建模过程与传统材料的有限元分析类似,但在材料性质和单元连接方面存在一些特殊性。
下面是复合材料有限元分析的建模过程的简要步骤:1.几何建模:–根据实际结构的几何形状,利用建模软件(如Solidworks或CATIA)进行3D建模。
–根据复合材料的分层结构,将各层材料的几何形状分别绘制。
2.材料定义:–根据复合材料的材料属性,定义合适的材料模型和参数。
–考虑复合材料的各向异性和分层结构,定义材料的力学参数。
复合材料的力学模型与性能预测
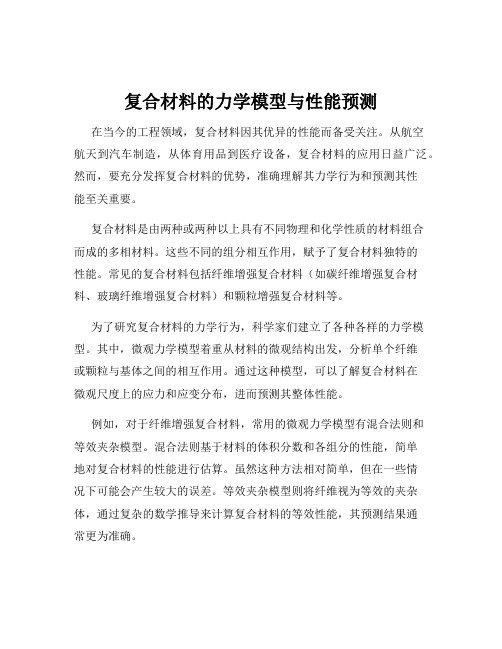
复合材料的力学模型与性能预测在当今的工程领域,复合材料因其优异的性能而备受关注。
从航空航天到汽车制造,从体育用品到医疗设备,复合材料的应用日益广泛。
然而,要充分发挥复合材料的优势,准确理解其力学行为和预测其性能至关重要。
复合材料是由两种或两种以上具有不同物理和化学性质的材料组合而成的多相材料。
这些不同的组分相互作用,赋予了复合材料独特的性能。
常见的复合材料包括纤维增强复合材料(如碳纤维增强复合材料、玻璃纤维增强复合材料)和颗粒增强复合材料等。
为了研究复合材料的力学行为,科学家们建立了各种各样的力学模型。
其中,微观力学模型着重从材料的微观结构出发,分析单个纤维或颗粒与基体之间的相互作用。
通过这种模型,可以了解复合材料在微观尺度上的应力和应变分布,进而预测其整体性能。
例如,对于纤维增强复合材料,常用的微观力学模型有混合法则和等效夹杂模型。
混合法则基于材料的体积分数和各组分的性能,简单地对复合材料的性能进行估算。
虽然这种方法相对简单,但在一些情况下可能会产生较大的误差。
等效夹杂模型则将纤维视为等效的夹杂体,通过复杂的数学推导来计算复合材料的等效性能,其预测结果通常更为准确。
宏观力学模型则将复合材料视为均匀的连续体,不考虑其微观结构。
这种模型主要用于分析复合材料在宏观尺度上的力学响应,如梁、板等结构的弯曲、拉伸和压缩等行为。
常见的宏观力学模型包括经典层合板理论和有限元方法。
经典层合板理论将复合材料层合板视为由多层不同方向的单层板组成,通过叠加各单层板的贡献来计算层合板的整体性能。
这一理论在工程中得到了广泛的应用,但它对于复杂的加载情况和边界条件的处理能力有限。
有限元方法则是一种更为强大的工具,它可以模拟各种复杂的几何形状、加载条件和边界约束。
通过将复合材料结构离散为有限个单元,并对每个单元的力学行为进行分析,最终得到整个结构的响应。
有限元方法在复合材料的设计和分析中发挥着重要的作用,但它需要较高的计算资源和专业的软件支持。
《复合材料》课程笔记

《复合材料》课程笔记第一章:复合材料概述1.1 材料发展概述复合材料的发展历史可以追溯到古代,人们使用天然纤维(如草、木)与土壤、石灰等天然材料混合制作简单的复合材料,例如草绳、土木结构等。
然而,现代复合材料的真正发展始于20世纪40年代,当时因航空工业的需求,发展了玻璃纤维增强塑料(俗称玻璃钢)。
此后,复合材料技术经历了多个发展阶段,包括碳纤维、石墨纤维和硼纤维等高强度和高模量纤维的研制和应用。
70年代,芳纶纤维和碳化硅纤维的出现进一步推动了复合材料的发展。
这些高强度、高模量纤维能够与合成树脂、碳、石墨、陶瓷、橡胶等非金属基体或铝、镁、钛等金属基体复合,形成了各种具有特色的复合材料。
1.2 复合材料基本概念、特点复合材料是由两种或两种以上不同物质以不同方式组合而成的材料,它可以发挥各种材料的优点,克服单一材料的缺陷,扩大材料的应用范围。
复合材料具有以下特点:- 重量轻:复合材料通常具有较低的密度,比传统材料轻,有利于减轻结构重量。
例如,碳纤维复合材料的密度仅为钢材的1/5左右。
- 强度高:复合材料可以承受较大的力和压力,具有较高的强度和刚度。
例如,碳纤维复合材料的拉伸强度可达到3500MPa以上。
- 加工成型方便:复合材料可以通过各种成型工艺进行加工,如缠绕、喷射、模压等。
这些工艺能够适应不同的产品形状和尺寸要求。
- 弹性优良:复合材料具有良好的弹性和抗冲击性能,能够吸收能量并减少损伤。
例如,橡胶基复合材料在受到冲击时能够吸收大量能量。
- 耐化学腐蚀和耐候性好:复合材料对酸碱、盐雾、紫外线等环境因素具有较好的抵抗能力,适用于恶劣环境下的应用。
例如,聚酯基复合材料在户外长期暴露下仍能保持较好的性能。
1.3 复合材料应用由于复合材料的优异性能,它们在各个领域得到了广泛的应用。
主要应用领域包括:- 航空航天:飞机、卫星、火箭等结构部件。
复合材料的高强度和轻质特性使其成为航空航天领域的重要材料,能够提高飞行器的性能和燃油效率。
复合材料的复合原理及界面
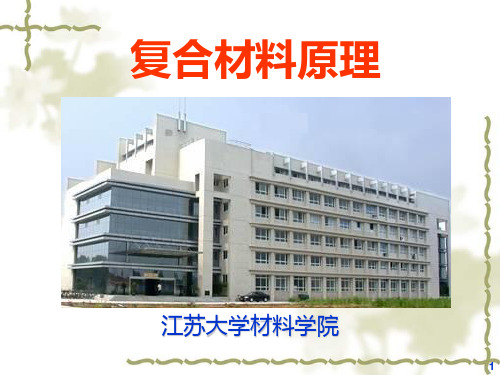
作用,而且在不同的生产过程中或复合材料的使
用期间,粘结机理还会发生变化,如由静电粘结 变成反应粘结。
33
体系不同,粘结的种类或机理不同,这主要取决于
基体与增强材料的种类以及表面活性剂(或称偶联剂) 的类型等。 界面粘结机理主要有机械作用理论、静电作用理论、 界面反应理论、浸润理论、可变形层理论、约束层 理论等。
28
为了提高复合材料组元间的浸润性,常常通过对增
强材料进行表面处理的方法来改善润湿条件,有时也可
通过改变基体成分来实现。
29
多数陶瓷基复合材料中增强材料与基体之间不发生化
学反应,或不发生激烈的化学反应。
有些陶瓷基复合材料的增强材料与其基体的化学成分 相同。
30
例如,如SiC晶须或SiC纤维增强SiC陶瓷,这种复合材 料也希望建立一个合适的界面,即合适的粘接强度、界面层 模量和厚度以提高其韧性。
外,还有基体中的合金元素和杂质、由环境带来的
杂质。 这些成分或以原始状态存在,或重新组合成新的化 合物。 界面上的化学成分和相结构非常复杂。
7
复合材料界面的作用可以归纳为以下几种效应: 1、传递效应 界面能传递力,即将外力传递给增强 体,起到基体和增强体之间的桥梁作用。 2、阻断效应 结合适当的界面有阻止裂纹扩展、中 断材料破坏、减缓应力集中的作用。 3、不连续效应 在界面上产生物理性能的不连续性 等现象,如抗电性、耐热性、尺寸稳定性等。
26
对于一个指定的体系,接触角随着温度、保持时 间、吸附气体等而变化。 浸润性仅仅表示了液体与固体发生接触时的情况, 而并不能表示界面的粘结性能。
27
一种体系的两个组元可能有极好的浸润性,但它们之 间的结合可能很弱,如范德华物理键合形式。
航空航天结构材料:4.复合材料力学性能特点与结构设计理念
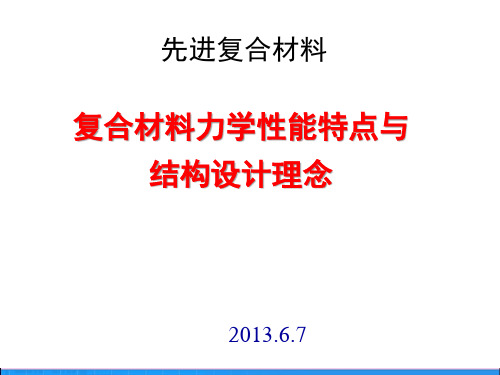
3.1 结构设计一般原则
(2) 按使用载荷设计时,采用使用载荷所 对于的许用值称为使用许用值;按设 计载荷校核时,采用设计载荷所对应 的许用值,称为设计许用值。 许用值是计算中允许采用的性 能值,由一定的试验数据确定。
3.1 结构设计一般原则
数据统计方法
制造期间的操作差异 原材料批间差异 检验差异 材料固有差异
界面区能量流散的因素
界面能量流散与基体类型(脆性、韧性)、界面 粘结状态、固化反应化学键分布等很有关系
19
2. 复材界面与纤维/树脂匹配
裂纹的扩展与能量流散过程
能量
树脂 纤维
界面粘结很强:裂纹未在界面区扩展,较多能量集中于裂纹尖端,冲断纤维 复合材料呈现脆性破坏特征
纤维
能量
树脂
界面粘结很弱或裂纹尖端能量很大:在界面产生大面积脱粘破坏,同时于裂 纹尖端能量依然集中,引起纤维断裂
环境 室温 室温 室温 室温 室温 室温 室温 室温 室温 室温 室温
1. 复合材料力学性能特点
层压板力学性能
编号 1 2 3 4 5 6
性能项目 开孔拉伸强度 填孔拉伸强度 开孔压缩强度 填孔压缩强度 冲击后压缩强度
挤压强度
环境
室温干态 室温湿态 高温干态 高温湿态
1. 复合材料力学性能特点
数据归一化
纵L 向 (x)
强度、模量 强度、模量
横T 向 (y)
强度、模量
剪切
纵横剪切强度、纵横剪切模量
1. 复合材料力学性能特点
单向板力学性能工程常数
编号 1 2 3 4 5 6 7 8 9 10 11
性能项目 0°拉伸强度 0°拉伸模量
泊松比 90°拉伸强度 90°拉伸模量 0°压缩强度 0°压缩模量 90°压缩强度 90°压缩模量 面内剪切强度 面内剪切模量
复合材料基础知识
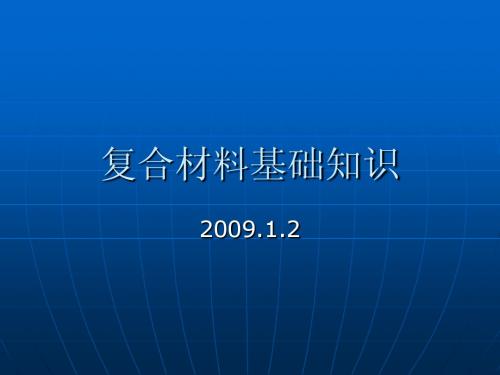
复合材料在中国
起始于1958年 ,首先用于军工制品,而后逐渐 扩展到民用。 1958年以手糊工艺研制了玻璃钢艇,以层压和卷 制工艺研制玻璃钢板、管和火箭弹 1961年研制成用于远程火箭的玻璃纤维-酚醛树 脂烧蚀防热弹头 1962年引进不饱和聚酯树脂、喷射成型和蜂窝夹 层结构成型技术,并制造了玻璃钢的直升机螺旋 桨叶和风洞叶片,同年开始纤维缠绕工艺研究并 生产出一批氧气瓶等压力容器。 1970年用玻璃钢蜂窝夹层结构制造了一座直径 44m的雷达罩
物理性质
相对密度在1.11~1.20左右 ,固化时体积收缩 率较大 耐热性。绝大多数不饱和聚酯树脂的热变形温度 都在50~60℃,一些耐热性好的树脂则可达 120℃ 力学性能。不饱和聚酯树脂具有较高的拉伸、弯 曲、压缩等强度 耐化学腐蚀性能。不饱和聚酯树脂耐水、稀酸、 稀碱的性能较好,耐有机溶剂的性能差,同时, 树脂的耐化学腐蚀性能随其化学结构和几何开关 的不同,可以有很大的差异。 ⑷介电性能。不饱和聚酸树脂的介电性能良好。
环氧树脂的性能和特性
1、 形式多样。各种树脂、固化剂、改性剂体系几乎可以适应各种应用对形式提出的 要求,其范围可以从极低的粘度到高熔点固体。 2、 固化方便。选用各种不同的固化剂,环氧树脂体系几乎可以在0~180℃温度范围 内固化。 3、 粘附力强。环氧树脂分子链中固有的极性羟基和醚键的存在,使其对各种物质具 有很高的粘附力。环氧树脂固化时的收缩性低,产生的内应力小,这也有助于提高粘 附强度。 4、 收缩性低。环氧树脂和所用的固化剂的反应是通过直接加成反应或树脂分子中环 氧基的开环聚合反应来进行的,没有水或其它挥发性副产物放出。它们和不饱和聚酯 树脂、酚醛树脂相比,在固化过程中显示出很低的收缩性(小于2%)。 5、 力学性能。固化后的环氧树脂体系具有优良的力学性能。 6、 电性能。固化后的环氧树脂体系是一种具有高介电性能、耐表面漏电、耐电弧的 优良绝缘材料。 7、 化学稳定性。通常,固化后的环氧树脂体系具有优良的耐碱性、耐酸性和耐溶剂 性。像固化环氧体系的其它性能一样,化学稳定性也取决于所选用的树脂和固化剂。 适当地选用环氧树脂和固化剂,可以使其具有特殊的化学稳定性能。 8、 尺寸稳定性。上述的许多性能的综合,使环氧树脂体系具有突出的尺寸稳定性和 耐久性。 9、 耐霉菌。固化的环氧树脂体系耐大多数霉菌,可以在苛刻的热带条件下使用。
基于PythonAbaqus复合材料代表性体积元的数值模型

基于PythonAbaqus复合材料代表性体积元的数值模型一、本文概述随着复合材料在工程领域中的广泛应用,对其性能预测和优化的需求也日益增长。
复合材料由多种不同性质的组分材料组成,其性能不仅取决于各组分的性质,更与组分之间的相互作用和排布方式密切相关。
因此,建立能够准确反映复合材料宏观性能的数值模型,对于理解其力学行为、预测其性能表现以及优化其设计具有重要意义。
本文旨在探讨基于Python和Abaqus的复合材料代表性体积元(Representative Volume Element, RVE)数值模型的建立与应用。
我们将介绍复合材料RVE模型的基本原理和重要性,阐述其在复合材料性能预测中的关键作用。
接着,我们将详细介绍如何使用Python 编程语言和Abaqus有限元分析软件,构建复合材料的RVE模型。
在这一过程中,我们将涵盖模型建立的关键步骤,包括材料属性的定义、几何模型的建立、边界条件的设置以及求解过程的实现。
本文还将探讨如何对建立的RVE模型进行验证和校准,以确保其能够准确反映复合材料的实际性能。
我们将介绍一些常用的验证方法和技术,包括与实验结果的对比、模型预测精度的评估等。
我们将通过一些具体的案例,展示基于Python和Abaqus的复合材料RVE模型在预测复合材料性能、分析材料失效模式以及优化材料设计等方面的实际应用。
本文旨在为从事复合材料研究的学者和工程师提供一个有效的数值建模工具和方法,以帮助他们更好地理解和预测复合材料的力学行为,优化材料设计,推动复合材料在工程领域的应用和发展。
二、复合材料基础知识复合材料是由两种或两种以上具有不同物理和化学性质的材料,通过物理或化学的方法,在宏观尺度上组成具有新性能的材料。
这种材料在保持各组成材料主要特点的基础上,通过复合效应获得单一材料难以达到的综合性能,如更高的强度、更好的刚度、更低的密度、更高的耐温性能、更好的电磁性能等。
复合材料的性能不仅与组成材料的性能有关,而且与各组分材料的含量、分布、界面结合状态以及复合工艺等因素密切相关。
第2章 复合材料的结构形式与复合效应

图2-1复合材料的结构图2-1复合材料的结构
图2-2几种典型复合材料结构
7混合效应也称平均效应,是组份材料性能取长
单向连续纤维增强复合材料模型
14
(3)泊松比
12,I I νν
30
时对应的基
39当纤维体积含量太小时,复合材料的
破坏由基体控制,其纵向拉伸强度
mt f
为了修正误差,可采用基体模量前乘以小于1的修正系数β,即
βυ
E E
2-9单根纤维埋入基体模型受力前后变形示意图
2-10 平行于外载荷的伸直不连续纤维微元体的平衡
(a)受力前b)受力后
2-12 理想塑性基体的剪应力一应变曲线
max
()2f f t s
L d στ=能够达到连续纤维应力时的最短纤维长度定义为载荷传递长度Lt ,可以得到:
物理关系为
11C
εβ=1
f C σεβ=
+。
- 1、下载文档前请自行甄别文档内容的完整性,平台不提供额外的编辑、内容补充、找答案等附加服务。
- 2、"仅部分预览"的文档,不可在线预览部分如存在完整性等问题,可反馈申请退款(可完整预览的文档不适用该条件!)。
- 3、如文档侵犯您的权益,请联系客服反馈,我们会尽快为您处理(人工客服工作时间:9:00-18:30)。
f f m (1 f )
考虑到实际复合材料中存在着空隙,裂纹,损伤,缺陷,残余应力,界 面结合不完善及纤维微观屈曲等因素,应在式(3-68)中乘上一个修正系 数 K1,即
1 K1 f f m (1 f )
当试件的质量很好,对于玻璃纤维/环氧复合材料,大部分的实验结果表明, 在式(3-69)中取0.95<K1<1.0,可以复合得相当好。
1 1 f f m
m
)
根据复合材料的实际情况,可把连续 纤维单向增强复合材料处于应力下的 一般模型看做如图所示的薄片串,并 联组合而成,即整个模型由中间增强 层Ⅰ和表面基体层Ⅱ组成,由基体薄 片和纤维薄片组成的增强层在横向层 串联状态,纵向并联 式中, , m 分别为增强层中纤维和 f 基体的体积含量。
f
m 0.36
将预测结果和试验值画在图中。
从图中可见, 1 的预测值和实验值符合得很好,实验值略低于预测值,这 E 是因为纤维不完全平直或平行。 对于 E 2和 G12,模型Ⅱ 预测值偏高。模型Ⅰ预测值偏低。这是因为有一些 纤维横向接触,纤维 f 越大则接触可能越多。 在此基础上,他给出了半经验公式:
E2
E2
Em ( E f 2 Em ) f
f
f f r ,m f 1 可得
Em E f 2 (1 )
f
Em
如果以a表示表面层厚度为单位值时的增强层厚度,则 r a /(a 2) (3-57) f f r f (a 2) a (3-58) f q 关于a的取值,作者通过研究发现可由下述关系式确定 a p( ) 1 f 式中p和q是与组分材料性质有关 硼纤维 / 环氧复合材料( / E)p 3.2 B 的参数。对于常用的几类复合材 C 料,通过回归分析可知,q=1, 碳纤维 / 环氧复合材料( / E)p 2.8 P的取值为: 玻璃纤维/ 环氧复合材料( / E)p 3.0 G
G12
(3 65)
f 仍由式
B/E C/E G/E
p 3.8, q 0.7 p 3.8, q 1.0 p 2.7, q 1.0
(3 66)
泊松比 确定纵向泊松比 1 可采用类似确定 E1 的方法
1 1r m (1 r )
将式(3-33)代入式(3-67),得 1
E1 E1 E1
E2 (1 c) E2 cE2
1 (1 c) 2 c1
G12 (1 c)G12 cG12
E2 2 1 E1
上式中,C为接触系数,表示纤维横向接触程度,且C=0表示横向 完全隔离,即对应串联模型Ⅰ;C=1表示横向完全连通,即对应并 联模型Ⅱ。实际情况0<C<1,在上述实验下,c 0.4 f 0.025 讨论:对玻璃纤维/环氧复合材料,0.3< f <0.5,E2的计算值和实测 值较接近,当 f >0.5,偏离增大,取值偏高,0.4< f <0.6,G12的计 算值和实测值的一致性很好。 对碳纤维/环氧复合材料,E2和G12的计算值和实测值偏差都较大。
因为实际复合材料中,存在着空隙,缺陷,裂缝和界面结合不完 善等情况,这些又与工艺水平,纤维等结晶构造,热膨胀系数和 固化过程等有关。由于理论推导的简化假设与计算模型和实际情 况相差太多。所以理论公式和实际结果很不一致。对于工程设计 中需要预测单向单层板的纵向泊松比是,用下面的公式:
k (
E1 E f1 f Em (1 f )
E f 2 Em E2 Em f E f 2 (1 f )
f
1 f
m m
G
12
G f Gm G f f G f (1 f )
整个复合材料单层板由表面层和增强层以并联形式组合而成。如 以r 表示增强层的体积含量, f 表示整个复合材料单层的纤维体 积含量,则可导出单向纤维增强层复合材料弹性常数的计算式。 纵向弹性模量 E1 E1 E1r Em (1 r ) (3 51) 将式(3-23)带入(3-51) 得 E1 E f f Em (1 f ) r Em (1 r )
预测值与实验值的比较
采用国内外文献上的3类有代表性的单向复合材料的实验结果和这 里所得的数据比较。结果表明: 1.预测值与实验结果吻合性好,偏差基本上都在复合材料离散系数范 围内。 2.若这里所采用的组合模型的表面厚度0,则 r 1, f f ,则此 时变为串联模型。可见,串联模型是组合模型的特例,得到的是弹性 特性的下限,与实验值相差很远。 3.这里的导出式能比较精确地适用于各种纤维增强聚合物基体复合材 料和常用的 V 范围。由于实测数据所采用的3类材料构造不同, 性质相差很大,为了使导出式能与各类材料的实验结果比较接近, 在计算a的经验公式中,用了p,q两个修正系数。所以,采用既有 理论背景又有实验依据的半经验公式,在使用上,可以精确的解 决实际问题。
(3 64)
Gm Gm (G f Gm ) f Gm f G f (1 f )
(3 63)
将式(3-62),式(3-63)代入式(3-61),得
G12 G12r Gmm G12 Gm (1 r )
将式(3-39)代入式(3-64),得 式(3-65)中的增强层纤维体积含量 (3-58)和(3-59)得到,
1
E f1 f r Em (1 f r)
因为 f f r
(3 52)
所以
E1 E f 1 f Em (1 f )
(3 53)
由此可见,采用串,并联组合模型和上述简化假定计算 E1 得到了各种 计算模型和计算方法完全相同的结果。计算 E1 的式(3-53)已经经典 化了,这是目前计算弹性常数中最简单,最精确和最重要的公式。如考 虑到纤维不完全平直,取向也不完全平行,以及空隙等因素的影响,应 在式(3-53)中乘上一个修正系数K,即
面内剪切弹性常数模量 G12 由串并联组合模型给出 的代表性体积单元,在正轴1-2方向作用剪切应 力 ,如图
12
静力关系为 几何关系为 物理关系为
12 r12r m12m (3 61)
12 r12 m12
(3 62)
12 12G12 , r12 r12Gr12 , m12 m12Gm12
组合模型的弹性常数
植村山胁经验公式 组合模型的弹性常数
纵向弹性常数 横向弹性常数 面内剪切弹性常数 泊松比 预测值与实验结果的比较
植村山胁在串联模型和并联模型下,做了如下试验:对于玻璃纤维/环氧 f 0.23 单层复合材料,在 E f 7104 MPa
Em 3103 MPa
E1 K ( E f 1 f Emm )
(3 54)
k的取值在0.9与1.0之间,采用式(3-54)预测的 E1 与实验值符合得相当 好。
横向弹性常数模量 E 由于增强层和表面层在单层的横向为并联连接,因此 2 的预测值应为 (3-55) E2 E2 r Em (1 r ) 将式(3-29)代入式(3-55).考虑到