止动片落料冲孔复合模具设计资料
落料冲孔复合模具设计说明

落料冲孔复合模具设计说明一、模具结构设计1.模具类型:落料冲孔复合模具由上模、下模和导向列组成。
根据工件的要求和形状,模具可以分为单向落料冲孔模、双向落料冲孔模和多向落料冲孔模等类型。
2.上模设计:上模一般由模座、上模板、射针等部分组成。
上模板与下模具配合使用,冲击力传递到工件上。
上模板应尽可能减小重量,提高模具寿命。
3.下模设计:下模由模座、下模板、导柱等部分组成。
下模板与上模具配合使用,负责支撑工件并传递冲压力。
下模板应具备足够的强度和刚度,以保证冲孔过程中不变形。
4.导向列设计:导向列用于保证上模与下模的定位精度。
导向柱是最常见的导向结构,其作用是使上模和下模在冲孔过程中保持相对位置的稳定性和精确性。
二、材料选择1.模具材料:常用于落料冲孔复合模具的材料有Cr12MoV、SKD11、SKH-9等。
这些材料具备良好的硬度、抗磨性和耐冲击性能,能够满足加工要求,并延长模具使用寿命。
2.工作板材:根据冲孔工件的特点和材料选择不同的板材,如不锈钢板、铝合金板、冷轧板等。
工作板材的选择应考虑其刚度、强度和耐磨性能,以提高冲孔质量和效率。
三、加工工艺1.毛坯选择:根据工件要求,选择适合的板材作为冲孔模具的毛坯。
在选择毛坯时,要注意其尺寸和平整度,以便后续的加工和使用。
2.模具加工:模具的加工过程包括车削、铣削、铣孔、磨削、钳工和装配等工序。
在加工过程中要注意控制尺寸精度和表面质量,确保模具在使用中的稳定性和寿命。
3.表面处理:模具的表面处理可以采用镀铬、硬质合金喷涂、表面渗碳等技术。
表面处理能够提高模具的耐磨性和抗腐蚀性,延长模具的使用寿命。
4.模具调试:模具制造完成后,需要进行调试和试模。
通过调试,可以检查模具的定位精度、冲孔质量和加工效率,确保模具满足设计要求。
综上所述,落料冲孔复合模具设计需要考虑模具结构、材料选择和加工工艺等方面。
通过合理的设计和加工,可以提高模具的使用寿命和冲孔质量,满足金属加工的需求。
落料冲孔复合模具设计
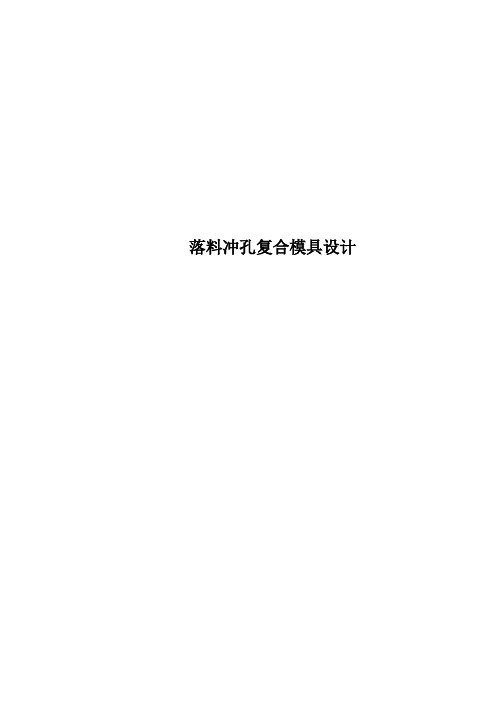
落料冲孔复合模具设计落料冲孔复合模具设计绪论模具主要类型有:冲模,锻模,塑料模,压铸模,粉末冶金模,玻璃模,橡胶模,陶瓷模等。
除部分冲模以外的的上述各种模具都属于腔型模,因为他们一般都是依靠三维的模具形腔是材料成型。
(1)冲模:冲模是对金属板材进行冲压加工获得合格产品的工具。
冲模占模具总数的50%以上。
按工艺性质的不同,冲模可分为落料模,冲孔模,切口模,切边模,弯曲模,卷边模,拉深模,校平模,翻孔模,翻边模,缩口模,压印模,胀形模。
按组合工序不同,冲模分为单工序模,复合模,连续模。
(2)锻模:锻模是金属在热态或冷态下进行体积成型是所用模具的总称。
按锻压设备不同,锻模分为锤用锻模,螺旋压力机锻模,热模锻压力锻模,平锻机用锻模,水压机用锻模,高速锤用锻模,摆动碾压机用锻模,辊锻机用锻模,楔横轧机用锻模等。
按工艺用途不同,锻模可分为预锻模具,挤压模具,精锻模具,等温模具,超塑性模具等。
(3)塑料模:塑料模是塑料成型的工艺装备。
塑料模约占模具总数的35%,而且有继续上升的趋势。
塑料模主要包括压塑模,挤塑模,注射模,此外还有挤出成型模,泡沫塑料的发泡成型模,低发泡注射成型模,吹塑模等。
(4)压铸模:压铸模是压力铸造工艺装备,压力铸造是使液态金属在高温和高速下充填铸型,在高压下成型和结晶的一种特殊制造方法。
压铸模约占模具总数的6%。
(5)粉末冶金模:粉末冶金模用于粉末成型,按成型工艺分类粉末冶金模有:压模,精整模,复压模,热压模,粉浆浇注模,松装烧结模等。
目前,我国17000多个模具生产厂点,从业人数五十多万。
除了国有的专业模具厂外,其他所有制形式的模具厂家,包括集体企业,合资企业,独资企业和私营企业等,都得到了快速发展。
研究和发展模具技术,对于促进国民经济的发展具有特别重要的意义,模具技术已成为衡量一个国家产品制造技术的重要标志之一,随着工业生产的迅速发展,模具工业在国民经济中的地位日益提高,并在国民经济发展过程中发挥越来越大的作用。
落料冲孔复合模设计说明书

I摘要本次设计了一套冲孔﹑落料的模具。
经过查阅资料,首先要对零件进行工艺分析,经过工艺分析和对比,采用冲孔落料工序,通过冲裁力、顶件力、卸料力等计算,确定模具的类型。
得出将设计的模具类型后将模具的各工作零部件设计过程表达出来。
在论文中第一部分,主要叙述了冲压模具的发展状况,说明了冲压模具的重要性,接着是对冲压件的工艺分析,完成了工艺方案的确定。
第二部分,对零件排样图的设计,完成了材料利用率的计算。
再进行冲裁工艺力的计算和冲裁模工作部分的设计计算,对选择冲压设备提供依据。
最后对主要零部件的设计和标准件的选择,为本次设计模具的绘制和模具的成形提供依据。
通过前面的设计方案画出模具各零件图和装配图。
本模具性能可靠,运行平稳,能够适应大批量生产要求,提高了产品质量和生产效率,降低劳动强度和生产成本。
关键词:冲压;落料冲孔模;模具结构;目录1冲压基础知识 (1)2工艺分析 (3)2.1零件的功用与经济性分析 (3)2.2零件钣金成形工艺性分析 (3)2.2.1结构形状与尺寸分析: (3)2.2.2 精度与表面粗糙度 (4)2.2.3 材料 (4)3制定工艺方案 (5)3.1工艺方案的分析 (5)3.2工艺方案的确定 (5)4工艺计算 (6)4.1排样及材料的利用率 (6)4.11排样的选用原则 (6)4.12材料利用率的计算 (6)4.2落料力、冲孔力、卸料力、推件力的计算 (7)4.4模具刃口的尺寸和公差的确定 (10)4.41冲裁间隙的确定 (10)4.42凸、凹模刃口尺寸计算 (10)5 主要零部件设计 (13)5.1 凹模设计 (13)5.2 凸模的设计 (14)5.3 凸凹模设计 (15)5.4 卸料橡胶的设计 (16)5.5 卸料板的设计 (17)5.6 固定板的设计 (17)5.7 上下模座、模柄的选用 (18)6 冲压设备的校核与选定 (20)6.1 冲压设备的校核 (20)6.2 冲压设备的选用 (20)7 绘制模具总装图及零件图 (21)7.1装配图绘制 (21)参考文献 (22)1冲压基础知识冲压是利用模具使板料沿一定的轮廓形状产生分离的一种冲压工序。
落料冲孔复合模设计说明书范本

目录第一章绪论 (1)1.1冲压模具的现状与发展趋势 (1)1.1.1我国模具技术的现状 (1)1.1.2未来冲压模具制造技术发展趋势 (2)1.2课题研究的理论依据 (4)第二章冲压成型工艺分析和工艺方案的确定 (5)2.1 冲压的基本工序分类及模具类型的选择 (5)2.2 冲模设计与制造的程序 (5)2.3 冲压工艺编制与冲模设计的步骤和内容 (6)2.3.1冲压工艺编制 (6)2.3.2冲模设计 (7)2.3.3冲模制造工艺的选择 (9)2.4设计任务 (9)2.5工件的工艺分析 (10)2.6工艺方案的确定 (10)2.7模具结构方案的确定 (11)2.8小结 (11)第三章落料冲孔模工艺计算及模具结构设计 (12)3.1排样设计与计算 (12)3.2 冲裁力计算 (13)3.3压力机选择 (13)3.3.1冲压设备的选择原则 (13)3.3.2选择压力机及压力机参数 (14)3.4 确定模具压力中心 (14)3.5凸、凹模刃口尺寸计算 (15)3.5.1刃口尺寸计算的一般原则 (15)3.5.2刃口尺寸计算方法 (15)3.5.3落料-冲孔模刃口尺寸的计算 (15)3.6确定凹模外形尺寸,选择标准 (16)3.7冲模结构设计 (17)3.7.1装配图 (17)3.7.2模具结构型式分析 (18)3.7.3模具主要零部件的结构和设计 (18)3.7.4模具的工作过程 (20)3.8小结 (20)第四章冲压模具工件的机械加工 (21)4.1冲压工作零件的技术要求 (21)4.2冲模工作零件的热处理 (21)4.3冲模工作零件机械加工工艺过程 (21)4.3.1凸模加工工艺工程 (21)4.3.2凹模加工工艺过程 (21)4.4小结 (22)第五章模具装配 (23)5.1冲模装配 (23)5.2冲模的安装 (24)5.3小结 (24)第六章结论 (25)参考文献 (26)致谢 (27)附零件图、装配图第一章绪论1.1冲压模具的现状与发展趋势1.1.1我国模具技术的现状改革开放以来,随着国民经济的高速发展,市场对模具的需求量不断增长。
落料冲孔复合模设计说明书

摘要我的毕业设计是落料冲孔复合模的设计,冲压模具主要是将板料分离或成形而得到制件的加工方法。
因为模具的生产主要是大批量的生产,而且模具可以保证冲压产品的尺寸精度和产品质量,模具的设计与制造主要考虑到模具的设计能否满足工件的工艺性设计,能否加工出合格的零件,以及后来的维修和存放是否合理等。
在本次设计中,不仅要考虑要使做出的零件能满足工作要求,还要保证它的使用寿命。
其次设计中还要考虑到它的实际工作环境和必须完成的设计任务,采用倒装复合模,凸凹模的外形和内型孔、凹模型孔采用数控线切割机床加工,在设计中我要考虑到很多关于我所设计模具的知识,包括它的使用场合、外观要求等,从这里可以知道模具设计是一项很复杂的工作,所以在设计要不断的改进直到符合要求。
关键词:落料;工艺性;凸凹模;复合模;AbstractMy graduation project is the blanking piercing die, stamping die mainly to isolated or forming the sheet metal processing methods are workpiece. Because molds are mainly high volume production, and stamping die products can ensure the dimensional accuracy and quality, mold design and manufacture of primary consideration to the mold design can meet the design process the workpiece, can process a qualified parts, and, later, maintenance and storage is reasonable. In this design, not only to consider making the parts to make to meet the job requirements, but also to ensure its service life.Second, the design should also take into account the actual work environment and must complete the design task, using inverse compound die, the shape of main punch the holes, die hole model used CNC Cutting Machine, I have to take into account in the design a lot on my knowledge of mold design, including its use of occasions, appearance requirements, from here you can know that mold is a very complex task, so to continuous improvement in the design until it meets the requirements.Keyword: blanking; Technological efficiency;main punch;compound die;前言随着科学技术的发展需要,模具已成为现代化不可缺少的工艺装备,模具设计是机械专业一个最重要的教学环节,是一门实践性很强的学科,是我们对所学知识的综合运用,通过对专业知识的综合运用,使学生对模具从设计到制造的过程有个基本上的了解,为以后的工作及进一步学习深造打下了坚实的基础。
落料冲孔复合模设计实例

落料冲孔复合模设计实例(一)零件工艺性分析工件为图1所示的落料冲孔件,材料为Q235钢,材料厚度2mm,生产批量为大批量。
工艺性分析内容如下:图1 工件图1.材料分析Q235为普通碳素结构钢,具有较好的冲裁成形性能。
2. 结构分析零件结构简单对称,无尖角,对冲裁加工较为有利。
零件中部有一异形孔,孔的最小尺寸为6mm,满足冲裁最小孔径≥的要求。
另外,经计算异形孔距零件外形之间的最小孔边距为5.5mm,满足冲裁件最小孔边距≥的要求。
所以,该零件的结构满足冲裁的要求。
3. 精度分析:零件上有4个尺寸标注了公差要求,由公差表查得其公差要求都属IT13,所以普通冲裁可以达到零件的精度要求。
对于未注公差尺寸按IT14精度等级查补。
由以上分析可知,该零件可以用普通冲裁的加工方法制得。
(二)冲裁工艺方案的确定零件为一落料冲孔件,可提出的加工方案如下:方案一:先落料,后冲孔。
采用两套单工序模生产。
方案二:落料—冲孔复合冲压,采用复合模生产。
方案三:冲孔—落料连续冲压,采用级进模生产。
方案一模具结构简单,但需两道工序、两副模具,生产效率低,零件精度较差,在生产批量较大的情况下不适用。
方案二只需一副模具,冲压件的形位精度和尺寸精度易保证,且生产效率高。
尽管模具结构较方案一复杂,但由于零件的几何形状较简单,模具制造并不困难。
方案三也只需一副模具,生产效率也很高,但与方案二比生产的零件精度稍差。
欲保证冲压件的形位精度,需在模具上设置导正销导正,模具制造、装配较复合模略复杂。
所以,比较三个方案欲采用方案二生产。
现对复合模中凸凹模壁厚进行校核,当材料厚度为2mm时,可查得凸凹模最小壁厚为4.9mm,现零件上的最小孔边距为5.5mm,所以可以采用复合模生产,即采用方案二。
(三)零件工艺计算1.刃口尺寸计算根据零件形状特点,刃口尺寸计算采用分开制造法。
(1)落料件尺寸的基本计算公式为尺寸,可查得凸、凹模最小间隙Zmin=0.246mm,最大间隙Zmax=0.360mm,凸模制造公差,凹模制造公差。
止动垫片冲裁复合模模具设计说明书

止动垫片冲裁复合模模具设计摘要本次设计了一套冲孔、落料的模具。
首先要对止动垫片进行工艺分析,经过工艺分析和对比确定模具架及压力机,确定压力机的型号。
再分析对冲压件加工的模具适用类型选择所需设计的模具。
得出将设计的模具类型后将模具的各工作零部件设计过程表达出来。
在说明书中第一部分,主要叙述了冲压模具的发展状况,说明了冲压模具的重要性与本次设计的意义,对冲压件的工艺分析,工艺方案的确定。
通过,对零件排样图的设计,完成了材料利用率的计算。
再进行冲裁工艺力的计算和冲裁模工作部分的设计计算。
最后对主要零部件的设计和标准件的选择,为本次设计模具的绘制和模具的成形提供依据,以及为装配图各尺寸提供依据。
通过前面的设计方案画出模具各零件图和装配图。
关键字:冲压;落料冲孔;模具结构;复合膜Gasket Blanking Stop Mold Design Of ComplexABSTRACTThe design of a punching, blanking die. We must first stop the gasket process analysis, process analysis and comparison through the mold frame and press OK, OK press models. Further analysis of the stamping process to select the desired type of mold for the design of the mold. Types obtained after the design of the mold die design process of the working parts express.In the description in the first part, described the development of stamping die, stamping die shows the importance and significance of this design, the stamping process analysis, process plan determined. Passed, the design of components layout diagram, complete the calculation of material utilization. Blanking process further force calculation and Die Design and calculation of working part. Finally, the main components of the design and selection of standard parts, mold design drawing based time and provide the basis for forming the mold, as well as provide the basis for each size assembly drawings. Draw through the front of the mold design and assembly drawings of parts.Key word:Wash to press;Fall to anticipate to hurtle the bore;Molding tool construction; Composite film目录前言 (1)第1章绪论 (5)1.1 模具行业 (5)1.2国内外模具发展状况及趋势 (5)1.3本次设计的主要方向、目的 (6)第2章制定止动垫片的工艺过程 (8)2.1 设计任务书及产品图 (8)2.2分析零件的工艺性 (9)2.3冲裁零件工艺方案的拟定 (9)2.4排样形式和剪裁方法、材料利用率计算 (11)2.5计算冲压力、选择压力机 (12)2.6确定模具压力中心 (13)第3章止动垫片复合模结构设计 (17)3.1模具类型及结构形式的确定 (17)3.2绘制模具总装配图的步骤 (17)3.2.1工件排样图 (17)3.2.2工作零件 (18)3.2.3定位零件 (19)3.2.4固定板、垫板 (21)3.2.5导向、固定、紧固及其它零件 (22)3.3绘制零件图 (23)3.4导柱导套选择 (24)3.5模座选择 (24)3.6螺钉、销钉的选用 (25)第4章模具加工技术要求 (26)4.1表面粗糙度及标准 (26)4.2加工精度 (27)4.2.1尺寸偏差 (27)4.2.2形位公差 (27)4.2.3配合要求 (27)结论 (29)谢辞 (30)参考文献 (31)前言冷冲压是利用安装在压力机上的冲模对材料施加压力,使其产生分离或塑性变形,从而获得所需要零件(俗称冲压件或冲件)的一种压力方法。
模具设计课程设计垫片落料冲孔复合模

目录1、冲压工艺性分析及工艺方案的确定 (3)1.1 冲压工艺性分析 (3)1.2 冲压工艺性方案 (3)2、毛坯展开及毛坯排样 (3)3、冲压力和压力中心计算 (4)3.1 落料力的计算 (4)3.2 冲孔力的计算 (4)3.3 冲裁力的计算 (4)3.4 卸料力的计算 (4)3.5 推件力的计算 (5)3.6 总冲压力的计算 (5)3.7 压力中心的确定 (5)4、冲压设备的选用 (5)5、凸模凹模凸凹模刃口及结构尺寸计算 (5)5.1 计算模具刃口尺寸 (5)5.2 落料凹模结构尺寸计算 (7)5.3 冲孔凸模与凸凹模结构尺 (8)6、模具总体结构设计 (9)7、模具总装图 (10)题目:图为一垫片零件图,材料为Q235,厚度2mm,大批量生产。
要求按照冷冲模具的设计步骤完成整体设计,编写设计说明书画出模具总装图1、冲压工艺性分析及工艺方案的确定1.1 压工艺性分析该材料为Q235钢,冲压性能较好,形状结构简单,尺寸精度不高,且孔与边缘的距离较大。
因此,该零件具有良好的工艺性。
1.2 冲压工艺性方案由该零件的形状特点可看出,该零件的成形包括冲孔、落料2种基本工序。
由于该零件的生产批量大,形状简单,而且它的孔边距满足凸凹模壁厚要求,因此,该零件宜采用复合模成形方式加工。
2、毛坯展开及毛坯排样根据该零件毛坯的形状特点,可确定采用直列单排的排样模式,查表可得条料边缘的搭边和工件间的搭边分别为1.5mm和2mm。
从而可计算出条料宽度和送进步距分别为:送进步距 h=52+b=52+1.5=53.5mm条料宽 B=52+2a=52+4=56mm排样图3、冲压力和压力中心计算3.1 落料力的计算F落=KLtτ F落---落料力L----冲裁轮廓总长 t----材料厚度τ----材料抗拉强度 K=1.3L=πD=3.14×52=163.28τ=340MPaF落=1.3×163.28×2×340=144.34KN3.2 冲孔力的计算F=KLtτL=πD=3.14×25=78.5mmF冲孔=1.3×78.5×2×340=69.39KN3.3 冲裁力的计算F冲裁力=F落+F冲孔=144.3+69.39=213.69KN3.4 卸料力的计算F K F=卸卸落料力卸K—卸料力因数卸K=0.05F卸=0.05×144.34=7.217KN3.5 推件力的计算F推=KF冲孔力推K—推件力因数推K=0.55F推=0.55×69.39=38.16KN 3.6 总冲压力的计算F总=F冲裁力+推卸FF+=213.69+7.21+38.16=259.06KN初选设备为开式压力机J23—353.7 压力中心的确定该零件形状结构对称,所以选用零件的几何中心为压力中心。
- 1、下载文档前请自行甄别文档内容的完整性,平台不提供额外的编辑、内容补充、找答案等附加服务。
- 2、"仅部分预览"的文档,不可在线预览部分如存在完整性等问题,可反馈申请退款(可完整预览的文档不适用该条件!)。
- 3、如文档侵犯您的权益,请联系客服反馈,我们会尽快为您处理(人工客服工作时间:9:00-18:30)。
广西大学《冲压工艺及模具设计》课程设计说明书设计题目止动片落料冲孔复合模具设计系别机械工程系专业班级机制082班学生姓名王猛学号2008333221指导教师钟得分日期2011年12月20日目录第一章设计任务 3 第二章工艺分析和方案选择 4 第三章计算冲裁压力、压力中心和选用压力机 6 第四章模具工作部分尺寸及公差 9 第五章零件图 11 第六章装配图 21 感想 23 参考文献 24第一章设计任务1.零件设计任务生产批量:大批量材料:H62材料厚度:0.7mm工件精度:IT9级图1设计该零件的落料冲孔复合模第二章工艺分析和方案选择1.冲压件工艺分析①材料:该冲裁件的材料是普通黄铜,有良好的力学性能,切削性好,可冲压。
②零件结构:结构简单,2×Φ9孔和圆弧R20,适合冲裁。
③尺寸精度:该冲裁件精度为IT9级。
结论:适合冲裁.2.分析比较和确定工艺方案2.1加工方案的分析.由零件图可知,该零件包含冲孔和落料两个工序。
形状较为规则,尺寸较小,精度要求IT9。
材料低硬度.根据止动片(如图1)包括冲孔、落料两道冲压工序。
模具形状较为规则即可以在一个工位完成所有工序。
可采用以下两种方案可采用以下几个方案:①方案一(级进模)止动片包括冲孔、落料两道冲压工序在内。
形状较为规则,尺寸较小,精度要求IT9。
可采用级进模。
②方案二(倒装复合模)将冲孔、落料两道冲压工序用一副模具直接完成冲孔、落料两道工序。
采用冲孔、落料倒装复合模(弹性卸料)。
③方案三(正装复合模)正装复合模方案完成工序和倒装复合模完成的工序一样。
凸凹模在上模。
弹性卸料板卸料。
方案比较:方案一:采用级进模,安全性好,,但是考虑到级进模结构复杂,工件精度加工精度不高,对称度和位移误差较大,以及加工难度较大,装配位置精度要求高,按照实际生产,级进模成本也高。
方案二:倒装复合模,冲孔废料由下模漏出,工件落在下模表面,需要及时清理。
安全性相对较低。
但工件精度较高,同轴度,对称度及位置度误差较小,生产效率较高,对材料要求不严,可用边角料.方案三:正装复合模,冲孔废料和工件都落在下模表面,安全性更差。
结论:综合以上两个方案分析比较结果说明,本零件采用第二方案最为合适。
2.2模具结构型式的选择确定冲压工艺方案后,应通过分析比较,选择合理的模具结构型式,使其尽量满足以下要求:(1)能冲出符合技术要求的工件;(2)能提高生产率;(3)模具制造和维修方便;(4)模具有足够的寿命;(5)模具易于安装调整,且操作方便、安全。
1、模具结构型式在确定采用复合模后,便要考虑采用正装式还是倒装式复合模。
大多数情况优先采用倒装式复合模,这是因为倒装式复合模的虫孔废料可以通过凸凹模从压力机工作台孔中漏出。
工件由上面的凹模带上后,由推荐装置推出,再由压力机附上的接件装置接走。
条料由下模的卸料装置脱出。
这样操作方便而且安全,能保证较高的生产率。
而正装式复合模,冲孔废料由上模带上,再由推料装置推出,工件则由下模的推件装置向上推出,条料由上模卸料装置脱出,三者混杂在一起,如果万一来不及排出废料或工件而进行下一次冲压,就容易崩裂模具刃口。
故本零件采用倒装式复合模结构。
2、定位装置为了使条料送料时有准确的位置,保证冲出合格的制件,所以采用定位销定位。
因为板料厚度t=0.7mm,属于较小厚度的板材,且制件尺寸不大,固采用侧面两个固定挡料销定位导向,在送料方向由于受凸模和凹模的影响,为了不至于削弱模具的强度,在送给方向采用一个弹簧挡料装置的活动挡料销.3、推件装置在倒装式复合模中,冲裁后工件嵌在上模部分的落料凹模内,需由刚性或弹性推件装置推出。
刚性推件装置推件可靠,可以将工件稳当地推出凹模。
但在冲裁时,刚性推件装置对工件不起压平作用,故工件平整度和尺寸精度比用弹性推件装置时要低些。
由于刚性推件装置已能保证工件所有尺寸精度,又考虑到刚性推件装置结构紧凑,维护方便,故这套模具采用刚性结构。
4、卸料装置复合模冲裁时,条料将卡在凸凹模外缘,因此需要在下模设置卸料装置。
在下模的弹性卸料装置一般有两种形式:一种是将弹性零件(如橡胶),装设在卸料板与凸凹模固定板之间;另一种是将弹性零件装设在下模板下。
由于该零件的条料卸料力不大,故采用前一种结构,并且使用橡胶作为弹性零件。
5、导向装置采用二导柱式模架。
第三章计算冲裁压力、压力中心和选用压力机1、排样方式的确定及材料利用率计算1.1排样方式的确定查《冲压工艺与冲模设计》表2.5.2,两工件之间按矩形取搭边值a=2.5mm,侧边取a1=2.5mm。
进料步距为A=20+2.5=22.5mm;条料宽度为B=(D+2a1+δ)0-δ,查《冲压工艺与冲模设计》表2.5.3得,条料下料剪切公差δ=0.5mm,冲裁件垂直于送料方向的尺寸为D=65mm,则B=(D+2a1+δ)0-δ=(65+2×2.5+0.5)0-0.5=70.50-0.5mm1.2材料利用率计算板料规格选用 0.7×1000×1800mm;采用纵裁时:每板的条数 n1=1000/70.5=14条余0.18每条的工件数 n2=1800/22.5=80件余0每板的工件数 n=n1×n2=14×80=1120个一个步距内的材料利用率为:η=F/F×100%=F/AB×100%=1025.06/(22.5×70.5)×100%=64.62% 板料利用率ηB=nF/1000×1800×100%=1120×1025.06/1000×1800×100%=63.78% 采用横裁时:每板的条数: n1=1800/70.5=25条余0.53每条的工件数: n2=1000/22.5=44件余0.44每板的工件数: n=n1×n2=25×44=1100个板料利用率ηB=nF/1000×1800×100%=1100×1025.06/1000×2500×100%=62.64% 经计算横裁.纵裁时板料利用率高于横裁.故选择纵裁排样。
排样方式(如图2)所示:图22.2计算冲裁力、卸料力材料H62的抗拉强度为δb=500MPa;冲裁周边总长:L1=174.13;冲圆形孔尺寸:L2=56.55(1)落料力F落=KPL1tδb=1×174.13×0.7×500=60945.5N(2)冲孔力F冲=KPL2tδb=1×56.55×0.7×500=19792.5 N(3)冲孔推件力F推=nK推F冲(查表计算n=10 k=0.06 F冲=19792.5N)F推=10×0.06×19792.5=11875.5 N (4)落料时的卸料力F卸=K×F落=0.04×60945.5=2437.82 N总冲压力F总=F冲+F推+F落+F卸= 60945.5+19792.5+11875.5+2437.82=95051.32N2.3压力机的选择需选择的压力机压力:F机=1.2F总=95.05KN×1.2=114.06KN选择压力机型号为 J21-16规格型号公称力(KN)公程力行程(mm)滑块行程(mm)行程次数(次/分)装模高度(mm)装模高度调节量(mm)滑块中心至机身距离(mm)工作台尺寸(mm)模柄孔尺寸(mm)工作台厚度(mm)工作台板孔尺寸(mm)电机功率(KW)机身两立柱间距离(mm)外形尺寸长×宽×高(mm)整机重量约(Kg)J2 1 -1 616260141740500前后32左右49φ3540φ121.52101120×560×17014002.4 确定模具压力中心用UG软件计算压力中心为(32.5 11.03)第四章模具工作部分尺寸及公差1.工作零件刃口尺寸计算落料部分以落料凹模为基准计算 ,落料凸模按间隙值配制;冲孔部分以冲孔凸模为基准计算,冲孔凹模按间隙值配制。
既以落料凹模、冲孔凸模为基准,凸凹模按间隙值配制。
刃口尺寸计算见表1。
2.工作零件结构尺寸2.1 凹模外形尺寸确定=Kb=0.22×65=14.3mm 14.3<15 H=20mm 凹模厚度 H1凹模壁厚 c=(1.5~2)H=30~40mmA=40×2+65=145mmB=40×2+20=100mm所以,凸模板外形尺寸为:160×100×152.2 凸模的长度凸模的长度为40mm,其中工作部分为20mm。
2.3凸凹模的长度凸凹模的长度为42.6mm。
2.4其他主要零件结构上模垫板160×160×6mm;凸模固定板160×160×15mm;下模卸料板160×160×10mm;凸凹模固定板160×160×20mm。
第五章零件图凸模凹模凸凹模上垫板凸模固定板卸料板凸凹模固定板推件块第六章装配图感想通过这次课程设计,我学到了很多东西,把课堂上学到的知识和实践结合到一起,形成了对知识的升华,但其中有很多的不足之处,望老师给予指出,感想钟得分老师的教育和指导。
王猛 2011.12.20参考文献冲压工艺与模具设计简明冲压模具设计手册。