钣金制造过程流程图
钣金工艺流程表
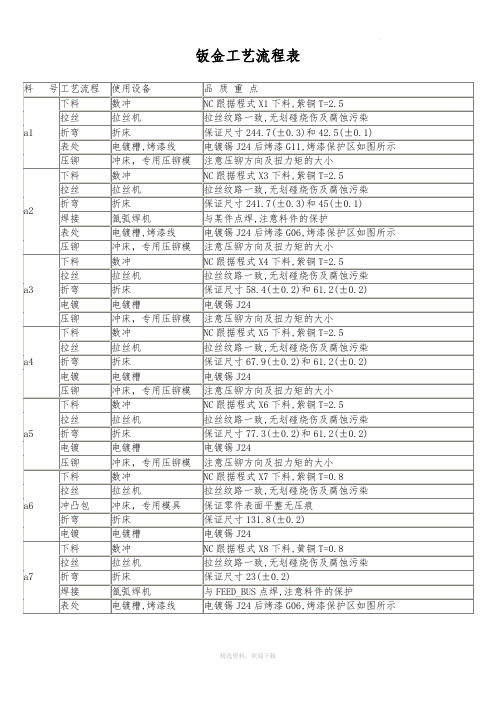
钣金工艺流程表钣金基础介绍(一),钣金业的发展非常迅速,所以应该了解一下钣金加工的基本常识.一.材料的选定.钣金加工一般用到的材料:有冷轧板(SPCC)、镀锌板(SECC)、铜板、铝板、不锈钢板、铝材等.其作用各不相同.至于如何选用,一般需从其用途及成本上来考虑.1.冷轧板.简称SPCC,用于表面处理是电镀五彩锌或烤漆件使用.2.镀锌板.简称SECC,用于表面处理是烤漆件使用.在无特别要求下,一般选用SPCC,可减少成本.3.铜板.一般用于镀镍或镀铬件使用,有时不作处理.跟据客户要求而定.4.铝板.一般用于表面处理是铬酸盐或氧化件使用.5.不锈钢板.分镜面不锈钢和雾面不锈钢,它不需要做任何处理.6.铝型材.一般用于表面处理是铬酸盐或氧化件使用.主要起支撑或连接作用,大量用于各种插箱中.二.钣金加工的工艺流程.对于任何一个钣金件来说,它都有一定的加工过程,也就是所谓的工艺流程.随着钣金件结构的差异,工艺流程可能各不相同,但总的不超过以下几点.1.设计并绘出其钣金件的零件图,又叫三视图.其作用是用图纸方式将其钣金件的结构表达出来.2.绘制展开图.也就是将一结构复杂的零件展开成一个平板件.3.下料.下料的方式有很多种,主要有以下几种方式:a.剪床下料.是利用剪床剪出展开图的外形长宽尺寸.若有冲孔、切角的,再转冲床结合模具冲孔、切角成形. b.冲床下料.是利用冲床分一步或多步在板材上将零件展开后的平板件结构冲制成形.其优点是耗费工时短,效率高,可减少加工成本,在批量生产时经常用到.c.NC数控下料.NC下料时首先要编写数控加工程序.就是利用编程软件,将绘制的展开图编写成NC数控加工机床可识别的程序.让其跟据这些程序一步一步的在一块铁板上,将其平板件的结构形状冲制出来.d.激光下料.是利用激光切割方式,在一块铁板上将其平板件的结构形状切割出来.4.翻边攻丝.翻边又叫抽孔,就是在一个较小的基孔上抽成一个稍大的孔,再在抽孔上攻丝.这样做可增加其强度,避免滑牙.一般用于板厚比较薄的钣金加工.当板厚较大时,如2.0、2.5等以上的板厚,我们便可直接攻丝,无须翻边.5.冲床加工.一般冲床加工的有冲孔切角、冲孔落料、冲凸包、冲撕裂、抽孔等加工方式,以达到加工目的.其加工需要有相应的模具来完成操作.冲凸包的有凸包模,冲撕裂的有撕裂成形模等.6.压铆.压铆就本厂而言,经常用到的有压铆螺柱、压铆螺母、压铆螺钉等,其压铆方式一般通过冲床或液压压铆机来完成操作,将其铆接到钣金件上.7.折弯.折弯就是将2D的平板件,折成3D的零件.其加工需要有折床及相应的折弯模具来完成操作.它也有一定的折弯顺序,其原则是对下一刀不产生干涉的先折,会产生干涉的后折.8.焊接.焊接就是将多个零件组焊在一起,达到加工的目的或是单个零件边缝焊接,以增加其强度.其加工方一般有以下几种:CO2气体保护焊、氩弧焊、点焊、机器人焊接等.这些焊接方式的选用是根据实际要求和材质而定.一般来说CO2气体保护焊用于铁板类焊接;氩弧焊用于铝板类焊接;机器人焊接主要是在料件较大和焊缝较长时使用.如机柜类焊接,可采用机器人焊接,可节省很多任务时,提高工作效率和焊接质量.9.表面处理.表面处理一般有磷化皮膜、电镀五彩锌、铬酸盐、烤漆、氧化等.磷化皮膜一般用于冷轧板和电解板类,其作用主要是在料件表上镀上一层保护膜,防止氧化;再来就是可增强其烤漆的附着力.电镀五彩锌一般用冷轧板类表面处理;铬酸盐、氧化一般用于铝板及铝型材类表面处理;其具体表面处理方式的选用,是根据客户的要求而定.10.组装.所谓组装就是将多个零件或组件按照一定的方式组立在一起,使之成为一个完整的料品。
钣金车间生产流程图
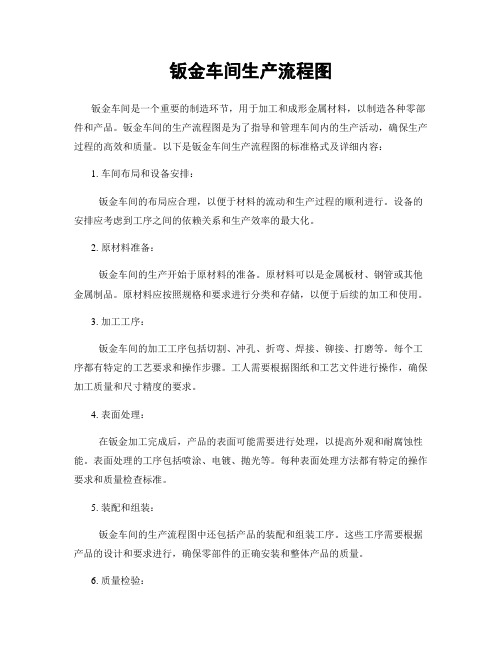
钣金车间生产流程图钣金车间是一个重要的制造环节,用于加工和成形金属材料,以制造各种零部件和产品。
钣金车间的生产流程图是为了指导和管理车间内的生产活动,确保生产过程的高效和质量。
以下是钣金车间生产流程图的标准格式及详细内容:1. 车间布局和设备安排:钣金车间的布局应合理,以便于材料的流动和生产过程的顺利进行。
设备的安排应考虑到工序之间的依赖关系和生产效率的最大化。
2. 原材料准备:钣金车间的生产开始于原材料的准备。
原材料可以是金属板材、钢管或其他金属制品。
原材料应按照规格和要求进行分类和存储,以便于后续的加工和使用。
3. 加工工序:钣金车间的加工工序包括切割、冲孔、折弯、焊接、铆接、打磨等。
每个工序都有特定的工艺要求和操作步骤。
工人需要根据图纸和工艺文件进行操作,确保加工质量和尺寸精度的要求。
4. 表面处理:在钣金加工完成后,产品的表面可能需要进行处理,以提高外观和耐腐蚀性能。
表面处理的工序包括喷涂、电镀、抛光等。
每种表面处理方法都有特定的操作要求和质量检查标准。
5. 装配和组装:钣金车间的生产流程图中还包括产品的装配和组装工序。
这些工序需要根据产品的设计和要求进行,确保零部件的正确安装和整体产品的质量。
6. 质量检验:在钣金车间生产流程的各个环节中,质量检验是一个非常重要的环节。
质量检验可以包括尺寸检查、外观检查、功能测试等。
质量检验的结果将决定产品是否合格,是否可以进入下一个生产环节或出货。
7. 包装和出货:钣金车间生产流程的最后一个环节是产品的包装和出货。
产品应按照客户的要求进行包装,并进行标识和记录。
包装的目的是保护产品不受损坏,并确保产品在运输过程中的安全。
钣金车间生产流程图是车间管理和生产指导的重要工具。
它可以帮助车间管理者和工人了解整个生产过程的顺序和要求,提高生产效率和产品质量。
同时,生产流程图也可以用于培训新员工,使他们快速掌握工序和操作要点。
通过不断优化和改进生产流程图,钣金车间可以实现更高效、更精确的生产,满足客户的需求和要求。
钣金前处理 工艺流程图
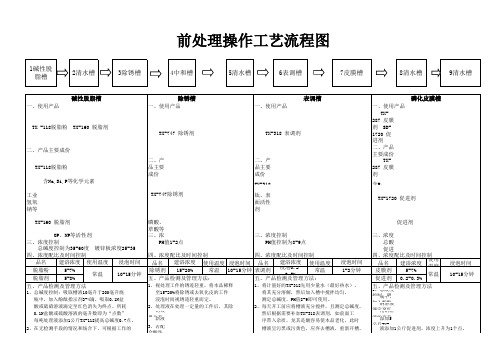
2、在无检测手段的情况和场合下,可根据工作的
磷酸、 草酸等 三、浓
PH值1-2点
三、浓度控制 PH值控制为8-9点
四、浓度配比及时间控制
四、浓度配比及时间控制
品名 建浴浓度 使用温度 浸泡时间 品名 建浴浓度 使用温度
除锈剂 15-20%
常温
10-15分钟 表调剂
浸泡0.20.3%
常温
五、产品检测及管理方法:
浸泡时间 10-15分钟
五、产品检测及管理方法 1、总酸度
控制瓶:中吸,
加入钠酚溶酞液
滴定化至钠红溶
液的添毫加升5
公斤TX液添加1公斤促进剂,浓度上升为1个点。
处理量而补充。
3、处理时如采用搅拌的方法,可加速油脂的去除。 4、处理液处理一定量的工作后,如继续加脱脂剂
已不能使除油脱脂顺利进行,则应及时更换槽液。 5、除油后需将工件用水洗净才能进入下道工序。
五、产品检测及管理方法:
浸泡时间 1-2分钟
1、视处理工件的锈迹轻重,将本品稀释
1、将计量好的TX-318先用少量水(最好热水),
至15-20%将除锈或去氧化皮的工件
将其充分溶解,然后加入槽中搅拌均匀,
浸泡时间视锈迹轻重而定。
测定总碱度,PH值8-9即可使用。
2、处理液在处理一定量的工件后,其除 锈效
品名 建浴浓度 使用温度 浸泡时间
脱脂粉 脱脂剂
5-7% 5-8%
常温
10-15分钟
五、产品检测及管理方法 1、总碱度控制:吸取槽液10毫升于200毫升烧
瓶中,加入酚酞红色消失为终点。所耗
0.1N盐酸或硫酸溶液的毫升数即为“点数”
每吨处理液添加1公斤TX-118提高总碱度0.7点。
钣金制造工艺流程
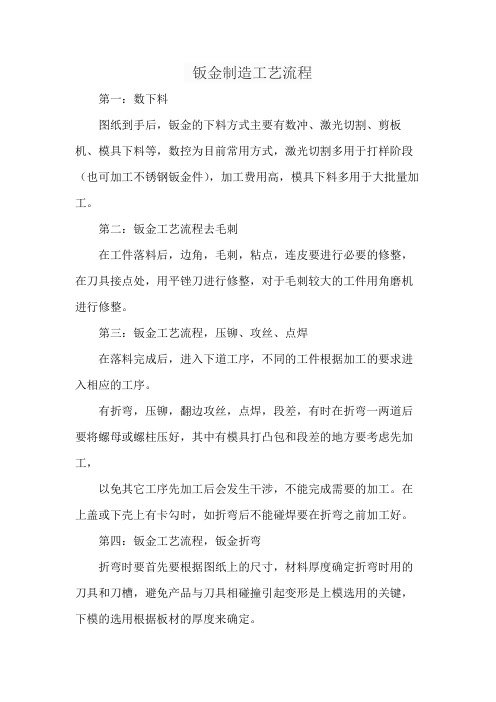
钣金制造工艺流程第一:数下料图纸到手后,钣金的下料方式主要有数冲、激光切割、剪板机、模具下料等,数控为目前常用方式,激光切割多用于打样阶段(也可加工不锈钢钣金件),加工费用高,模具下料多用于大批量加工。
第二:钣金工艺流程去毛刺在工件落料后,边角,毛刺,粘点,连皮要进行必要的修整,在刀具接点处,用平锉刀进行修整,对于毛刺较大的工件用角磨机进行修整。
第三:钣金工艺流程,压铆、攻丝、点焊在落料完成后,进入下道工序,不同的工件根据加工的要求进入相应的工序。
有折弯,压铆,翻边攻丝,点焊,段差,有时在折弯一两道后要将螺母或螺柱压好,其中有模具打凸包和段差的地方要考虑先加工,以免其它工序先加工后会发生干涉,不能完成需要的加工。
在上盖或下壳上有卡勾时,如折弯后不能碰焊要在折弯之前加工好。
第四:钣金工艺流程,钣金折弯折弯时要首先要根据图纸上的尺寸,材料厚度确定折弯时用的刀具和刀槽,避免产品与刀具相碰撞引起变形是上模选用的关键,下模的选用根据板材的厚度来确定。
其次是确定折弯的先后顺序,折弯一般规律是先内后外,先小后大,先特殊后普通。
有要压死边的工件首先将工件折弯到30°—40°,然后用整平模将工件压死。
压铆时,要考虑螺柱的高度选择相同不同的模具,然后对压力机的压力进行调整,以保证螺柱和工件表面平齐,避免螺柱没压牢或压出超过工件面,造成工件报废。
第五:钣金工艺流程,钣金焊接焊接有氩弧焊,点焊,二氧化碳保护焊,手工电弧焊等,点焊首先要考虑工件焊接的位置,在批量生产时考虑做定位工装保证点焊位置准确。
为了焊接牢固,在要焊接的工件上打凸点,可以使凸点在通电焊接前与平板均匀接触,以保证各点加热的一致,同时也可以确定焊接位置同样的,要进行焊接,要调好预压时间,保压时间,维持时间,休止时间,保证工件可以点焊牢固。
点焊后在工件表面会出现焊疤,要用平磨机进行处理,亚弧焊主要用于两工件较大,又要连接在一起时,或者一个工件的边角处理,达到工件表面的平整,光滑。
钣金件工艺流程图
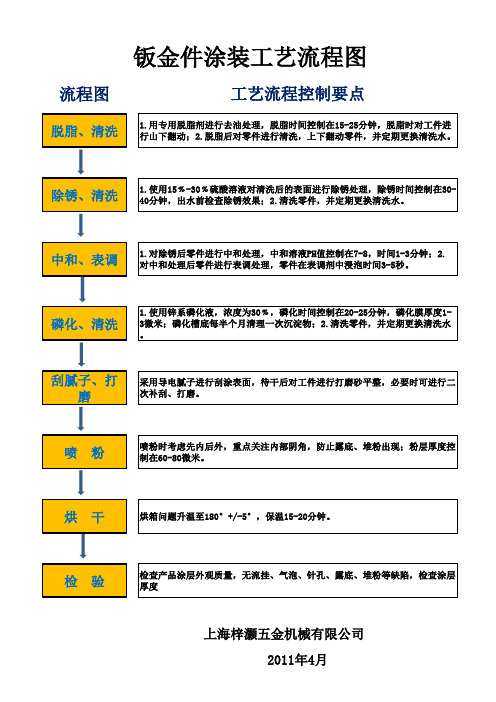
中和、 中和、表调
对除锈后零件进行中和处理,中和溶液PH值控制在7 PH值控制在 时间1 分钟; 1.对除锈后零件进行中和处理,中和溶液PH值控制在7-8,时间1-3分钟;2. 对中和处理后零件进行表调处理,零件在表调剂中浸泡时间3 对中和处理后零件进行表调处理,零件在表调剂中浸泡时间3-5秒。
磷化、清洗 磷化、
刮腻子、打磨 刮腻子、
采用导电腻子进行刮涂表面,待干后对工件进行打磨砂平整, 采用导电腻子进行刮涂表面,待干后对工件进行打磨砂平整,必要时可进行二 次补刮、打磨。 次内后外,重点关注内部阴角,防止露底、堆粉出现;粉层厚度控 喷粉时考虑先内后外, 重点关注内部阴角, 防止露底、 堆粉出现; 制在60 80微米 60- 微米。 制在60-80微米。
1.使用锌系磷化液,浓度为30﹪,磷化时间控制在20-25分钟,磷化膜厚度1使用锌系磷化液,浓度为30﹪,磷化时间控制在20-25分钟,磷化膜厚度1 30﹪,磷化时间控制在20 分钟 微米;磷化槽底每半个月清理一次沉淀物; 清洗零件, 3微米;磷化槽底每半个月清理一次沉淀物;2.清洗零件,并定期更换清洗水 。
钣金件涂装工艺流程图流程图工艺流程控制要点脱脂清洗除锈清洗中和表调磷化清洗刮腻子打磨检查产品涂层外观质量无流挂气泡针孔露底堆粉等缺陷检查涂层厚度上海梓灏五金机械有限公司1
钣金件涂装工艺流程图
流程图
脱脂、 脱脂、清洗
工艺流程控制要点
用专用脱脂剂进行去油处理,脱脂时间控制在15 25分钟 15- 分钟, 1.用专用脱脂剂进行去油处理,脱脂时间控制在15-25分钟,脱脂时对工件进 行山下翻动; 脱脂后对零件进行清洗,上下翻动零件,并定期更换清洗水。 行山下翻动;2.脱脂后对零件进行清洗,上下翻动零件,并定期更换清洗水。
钣金制作工艺流程

九江乐图钣金制作工艺流程锯床↗确认图纸金工→压铆↗↗设计→展开平面图→制造部→数冲→折弯→齐套→磷化→成型→打磨↘↘编程激光→补焊→打磨→清焊渣→喷塑→装机→成品包装设计根据客户提供的三维结构图和提供的部件图及零件图展开零件平面图,在平面图中标出外形尺寸,孔径,孔距。
转入编程,并指定加工流程(另附设计工作流程)设计人员将图纸流转到制造部,制造部按零件图要求,分三中形式进行加工一、对于方管及槽钢一类的零件,转入金工车间加工,按已下程序加工①按图纸长度要求到阿玛达H-250SAH锯床进行下料加②下料后的毛坯料需要钻孔的零件采用数冲加工模版,来对工件定位③先钻R1.5定位孔④按图纸要求的孔径尺寸钻孔⑤攻丝、拉铆、压铆等后续加工的孔,攻丝采用攻丝和手工攻丝机相结合的方法加工⑥需沉孔的零件,选用合适尺寸的90°钻头或沉孔器,进行沉孔加工⑦拉铆采用手动拉铆枪完成以上工序后,经检验确认合格后转入齐套库二、对于需要激光加工的零件,按要求激光切割,切割的零件,经检验合格后转入齐套库三、对于需要板材加工的零件内部安装板,及前后门板顶底板,侧板、前后屏蔽框,内部支架等钣金工件需要数控冲床来加工,来保证零件的度要求,操作工,按展开尺寸的要求,板材的厚度要求,来对板材进行数冲加工(数冲加工的程序另附)对加工完的平面零件检验,合格后转入到修毛刺工序,修毛刺接到数冲转来的板材进行逐一拆除连接部位,对零件的四周毛边修锉,修锉的工具有修边器具,平锉,半圆锉等工具来修毛刺,对修毛刺零件做到、不刮手、无尖角,边角圆润滑,经检验合格后零件与图纸一起流转到折弯处。
四、折弯接到平面料和加工图之后按以下程序加工①看清图纸的技术要求,工艺要求②对加工的来料进行材质与料厚的分类摆放;③要求对称加工的零件,对称摆放整齐④料厚一样的板料放在一起⑤模具的选用,1.0mm用V6下摸,1.5mm用V8下模,2.0mm 用V12下模,2.5mm用V14下模,3.0用V16下模,确保料后一样,加工后零件R角一致,(折弯机加工的参数另附)⑥对要求提前压铆螺母的零件是先折一道边,压铆后再折二道弯,要看清工艺流程。
钣金制作工艺流程
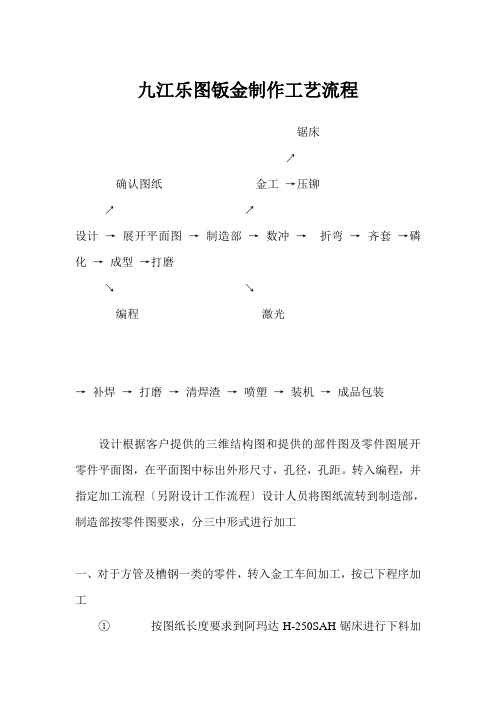
九江乐图钣金制作工艺流程锯床↗确认图纸金工→压铆↗↗设计→展开平面图→制造部→数冲→折弯→齐套→磷化→成型→打磨↘↘编程激光→补焊→打磨→清焊渣→喷塑→装机→成品包装设计根据客户提供的三维结构图和提供的部件图及零件图展开零件平面图,在平面图中标出外形尺寸,孔径,孔距。
转入编程,并指定加工流程〔另附设计工作流程〕设计人员将图纸流转到制造部,制造部按零件图要求,分三中形式进行加工一、对于方管及槽钢一类的零件,转入金工车间加工,按已下程序加工①按图纸长度要求到阿玛达H-250SAH锯床进行下料加②下料后的毛坯料需要钻孔的零件采用数冲加工模版,来对工件定位③④按图纸要求的孔径尺寸钻孔⑤攻丝、拉铆、压铆等后续加工的孔,攻丝采用攻丝和手工攻丝机相结合的方法加工⑥需沉孔的零件,选用合适尺寸的90°钻头或沉孔器,进行沉孔加工⑦拉铆采用手动拉铆枪完成以上工序后,经检验确认合格后转入齐套库二、对于需要激光加工的零件,按要求激光切割,切割的零件,经检验合格后转入齐套库三、对于需要板材加工的零件内部安装板,及前后门板顶底板,侧板、前后屏蔽框,内部支架等钣金工件需要数控冲床来加工,来保证零件的度要求,操作工,按展开尺寸的要求,板材的厚度要求,来对板材进行数冲加工〔数冲加工的程序另附〕对加工完的平面零件检验,合格后转入到修毛刺工序,修毛刺接到数冲转来的板材进行逐一拆除连接部位,对零件的四周毛边修锉,修锉的工具有修边器具,平锉,半圆锉等工具来修毛刺,对修毛刺零件做到、不刮手、无尖角,边角圆润滑,经检验合格后零件与图纸一起流转到折弯处。
四、折弯接到平面料和加工图之后按以下程序加工①看清图纸的技术要求,工艺要求②对加工的来料进行材质与料厚的分类摆放;③要求对称加工的零件,对称摆放整齐④料厚一样的板料放在一起⑤模具的选用,1.0mm用V6下摸,1.5mm用V8下模,2.0mm 用V12下模,2.5mm用V14下模,3.0用V16下模,确保料后一样,加工后零件R角一致,〔折弯机加工的参数另附〕⑥对要求提前压铆螺母的零件是先折一道边,压铆后再折二道弯,要看清工艺流程。
附: 车身钣金工艺流程图:
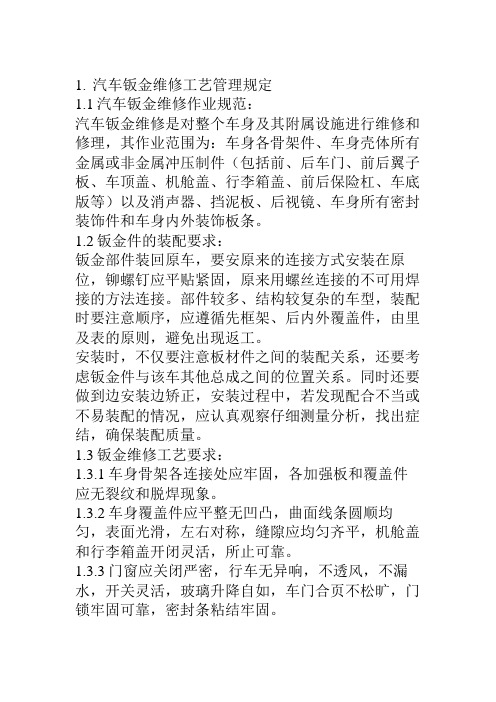
1.汽车钣金维修工艺管理规定1.1汽车钣金维修作业规范:汽车钣金维修是对整个车身及其附属设施进行维修和修理,其作业范围为:车身各骨架件、车身壳体所有金属或非金属冲压制件(包括前、后车门、前后翼子板、车顶盖、机舱盖、行李箱盖、前后保险杠、车底版等)以及消声器、挡泥板、后视镜、车身所有密封装饰件和车身内外装饰板条。
1.2钣金件的装配要求:钣金部件装回原车,要安原来的连接方式安装在原位,铆螺钉应平贴紧固,原来用螺丝连接的不可用焊接的方法连接。
部件较多、结构较复杂的车型,装配时要注意顺序,应遵循先框架、后内外覆盖件,由里及表的原则,避免出现返工。
安装时,不仅要注意板材件之间的装配关系,还要考虑钣金件与该车其他总成之间的位置关系。
同时还要做到边安装边矫正,安装过程中,若发现配合不当或不易装配的情况,应认真观察仔细测量分析,找出症结,确保装配质量。
1.3钣金维修工艺要求:1.3.1车身骨架各连接处应牢固,各加强板和覆盖件应无裂纹和脱焊现象。
1.3.2车身覆盖件应平整无凹凸,曲面线条圆顺均匀,表面光滑,左右对称,缝隙应均匀齐平,机舱盖和行李箱盖开闭灵活,所止可靠。
1.3.3门窗应关闭严密,行车无异响,不透风,不漏水,开关灵活,玻璃升降自如,车门合页不松旷,门锁牢固可靠,密封条粘结牢固。
1.3.4车身内外饰板应符合原厂要求,无凹凸或弯曲,表面无裂痕和铆击印,紧固件排列整齐,安装牢固。
1.4车身钣金修复后,车身骨架及钣金件外形等各部尺寸和工作性能应基本达到原厂要求。
注:各部尺寸及要求参阅相关车型《维修手册》车身部分。
1.5车身钣金维修工艺过程(图示)2涂料的调配工艺及要求:2.1在进行车身喷涂或补漆前,应先确认漆膜类型,即用打磨法在需要喷涂的部位进行打磨,直至露出金属为止,然后观察漆膜结构进行确认。
2.2对有车身漆膜颜色代码的车型,按以下程序及要求调配:a)在被修补的车身上查出其颜色编号并输入电脑;b)根据电脑提供的颜色配比方案选定所需要的漆种;c)根据修补面积计算涂料总用量并输入电脑,电脑会根据配比方案给出各种成分的用量d)用电子天平称取各种色漆及溶剂,并由混漆机将其调匀;e)再进行电脑调漆时,电脑提供的数据只能作为参考值,不能完全依赖电脑配色系统。
- 1、下载文档前请自行甄别文档内容的完整性,平台不提供额外的编辑、内容补充、找答案等附加服务。
- 2、"仅部分预览"的文档,不可在线预览部分如存在完整性等问题,可反馈申请退款(可完整预览的文档不适用该条件!)。
- 3、如文档侵犯您的权益,请联系客服反馈,我们会尽快为您处理(人工客服工作时间:9:00-18:30)。
7.品质部对需要进行不合格评审的质量问题按照不合格品评审工作流程执行;
品质部
9检验员进行产品成检,并填写《成品检验记录》;
品质部
12.对检验合格的成品开具合格证;
物流部
13.对合格品办理入库手续;
品质部
14.每月对装配过程中出现的不合格记录进行统计与分析,必要时开展QC小组活动;
9.操作者本工序加工完成后提出转工序检验:
品质部
10.检验员进行转工序检验,对转工序不合格品转到步骤4执行,对转工序合格转到步骤11执行;
11.对加工未结束的半成品继续进行下一工序首件报检;对加工完成的成品转到步骤12进行成检;
钣金加工过程检验工作流程
部门
输入
钣金加工过程检验工作流程图
部门
输 出
生产部
4装配加工检验工作流程*
部门Biblioteka 输入装配加工检验工作流程图
部门
输 出
技术部
1.提供《检验指导书》
或《装配工艺文件》;
物流部
2.按生产计划集件;
品质部
4.检验员对操作者提出的不合格件和在巡检和关键工序检查过程中发现不合格品要进行记录并填写《过程检验记录》;
生产部
3.操作者按步骤进行组装,并对要进行组装的零部件进行自检,发现不合格品及时通知检验员;
12. 操作者提出成品报检;
N
Y Y
N
品质部
13. 检验员对产成品进行检验,并将结果填写《钣金成品检验记录》;对不合格成品按照步骤4执行;
品质部
物流部
14. 检验员对检验合格的成品开具合格证明,并通知物流部办理登记入库;
品质部
15. 每月对钣金加工过程中出现的不合格记录进行统计与分析,必要时开展QC小组活动。
Y
Y N
N
N
Y
品质部
物流部
5.检验员要及时与库房联系,对不合格件进行更换,保证装配线的正常运转;
生产部
8.操作者合箱;
生产部
10.生产组织人员对不合格成品进行拆箱、调试;
品质部
6.检验员对更换下来的不合格件进行判断是否需要进行不合格品评审;
生产部
11.对需要更换零部件的转到步骤5执行,不需要更换零部件的转到步骤8执行;
品质部
物流部
4.品质部根据实际情况判断该起质量问题能够进行现场处理;
5.对不能现场处理的质量问题所对应的不合格品进行标识,并通知物流部隔离摆放;
6.品质部通知相关部门临时组件不合格品评审小组,开展不合格品评审工作;
7.品质部对能够现场处理的质量问题进行现场处理,并形成记录;
生产部
8.操作者首件加工检验合格后方可进行工序内批生产;
上海永森自动化控制设备有限公司钣金制造过程流程图(四)
钣金加工过程检验工作流程*
部门
输入
钣金加工过程检验工作流程图
部门
输 出
技术部
1.提供《检验指导书》
或《加工工艺文件》;
巡
N
Y
Y
N
检
N
Y
Y
品质部
3.检验员对报检首件进行检验;
检验员根据检验结果填写《检验记录》或《不合格品通知及处置单》;
生产部
2.操作者首件报检;