钣金制作工艺流程
钣金外壳工艺流程

钣金外壳工艺流程钣金外壳工艺流程是指在钣金部件的生产过程中,通过一系列的工艺步骤,将原材料加工成最终的外壳产品。
以下是一个典型的钣金外壳工艺流程。
第一步:材料准备钣金外壳的材料通常是金属薄板,如不锈钢、铝合金等。
在开始生产之前,首先需要对材料进行准备,包括切割、拉直、折弯等。
第二步:模具制作根据产品的要求和设计图纸,制作相应的模具。
模具可以分为压力模具和冲裁模具,用于将金属薄板加工成所需形状。
第三步:冲压将金属薄板放置在冲床上,利用冲床的冲裁模具进行冲压加工。
冲压过程中,通过对薄板进行切割、拉伸等操作,将其加工成所需的外壳形状。
第四步:折弯将冲压好的外壳进行折弯加工,使其获得所需的弯曲形状。
折弯通常使用折弯机进行,可以根据产品图纸上的要求进行精确的折弯角度。
第五步:焊接将折弯好的外壳进行组装焊接。
焊接可以采用手工焊接、气焊或激光焊接等方式进行,确保外壳的接缝牢固、密封。
第六步:表面处理对焊接好的外壳进行表面处理,以保护其外观和耐腐蚀性能。
常见的表面处理方法包括喷涂、电泳、阳极氧化等。
第七步:成品检验对成品外壳进行严格的质量检验,包括外观检查、尺寸测量、强度测试等。
确保外壳符合设计要求和客户的需求。
第八步:包装与发货将符合检验要求的成品外壳进行包装,通常采用纸箱、木箱等包装材料。
然后安排发货,将成品外壳送至客户指定的地点。
综上所述,钣金外壳加工的工艺流程包括材料准备、模具制作、冲压、折弯、焊接、表面处理、成品检验和包装发货等多个步骤。
通过这些工艺流程,可以生产出高质量的钣金外壳产品,满足不同领域的使用需求。
钣金加工筒体工艺流程
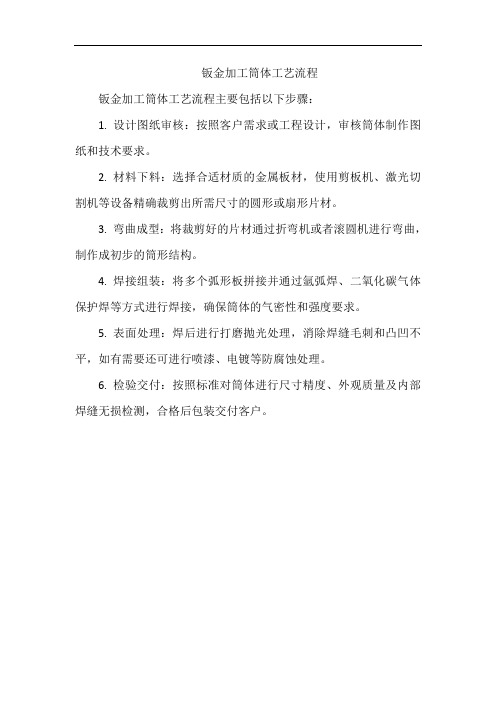
钣金加工筒体工艺流程
钣金加工筒体工艺流程主要包括以下步骤:
1. 设计图纸审核:按照客户需求或工程设计,审核筒体制作图纸和技术要求。
2. 材料下料:选择合适材质的金属板材,使用剪板机、激光切割机等设备精确裁剪出所需尺寸的圆形或扇形片材。
3. 弯曲成型:将裁剪好的片材通过折弯机或者滚圆机进行弯曲,制作成初步的筒形结构。
4. 焊接组装:将多个弧形板拼接并通过氩弧焊、二氧化碳气体保护焊等方式进行焊接,确保筒体的气密性和强度要求。
5. 表面处理:焊后进行打磨抛光处理,消除焊缝毛刺和凸凹不平,如有需要还可进行喷漆、电镀等防腐蚀处理。
6. 检验交付:按照标准对筒体进行尺寸精度、外观质量及内部焊缝无损检测,合格后包装交付客户。
钣金件加工工艺流程

钣金件加工工艺流程钣金件加工工艺流程钣金件是一种制造工艺,通过对金属材料进行切割、成型、焊接、折弯和涂装等加工工艺,将金属板材加工成所需形状和尺寸的零部件。
下面是一种常见的钣金件加工工艺流程。
1. 零件设计首先,需要对钣金件进行设计,包括确定零件的形状、尺寸和所需材料等。
在设计过程中,需要考虑到零件的功能需求和使用环境,确保设计出的零件能够满足所需的工作要求。
2. 材料选择选择适合的金属板材作为材料。
常见的钣金材料有铝板、不锈钢板和冷轧板等。
根据零件的要求和工作环境的要求,选择合适的材料。
3. 材料切割将金属板材根据设计要求,通过剪板机、数控切割机或激光切割机等设备进行切割。
确保切割出来的板材尺寸准确且平整。
4. 成型对切割好的板材进行成型,将其折弯、冲压或滚圆等,使其形成所需的形状和曲面。
成型过程中需要根据工艺要求选用合适的工艺设备和工具。
5. 焊接如果所设计的钣金件需要进行焊接,根据零件的要求,采用合适的焊接方式,如点焊、氩弧焊或激光焊等。
通过焊接将零件的各个部分连接起来,确保其结构牢固。
6. 折弯将已经成型的钣金件进行折弯,使其形成所需的角度和形状。
折弯时需要考虑到板材的弯曲强度,确保折弯后的钣金件不会出现变形或断裂等问题。
7. 表面处理对已经加工好的钣金件进行表面处理,包括打磨、喷涂、烤漆或镀锌等。
表面处理可以提高钣金件的表面硬度、防腐蚀性能和外观质量。
8. 质量检验对加工好的钣金件进行质量检验,包括尺寸检验、外观检查和性能测试等。
确保加工的钣金件符合设计要求和质量标准。
如果发现存在问题,进行修复或重新加工。
9. 包装与出库将检验合格的钣金件进行包装,并进行标识,准备出库。
包装要求保护钣金件不受损坏或腐蚀。
10. 交付客户将加工好的钣金件按照客户需求进行交付。
确保钣金件的数量、质量和交货时间符合客户要求。
总结钣金件加工工艺流程一般包括:设计、材料选择、切割、成型、焊接、折弯、表面处理、质量检验、包装和交货等步骤。
钣金制造工艺流程
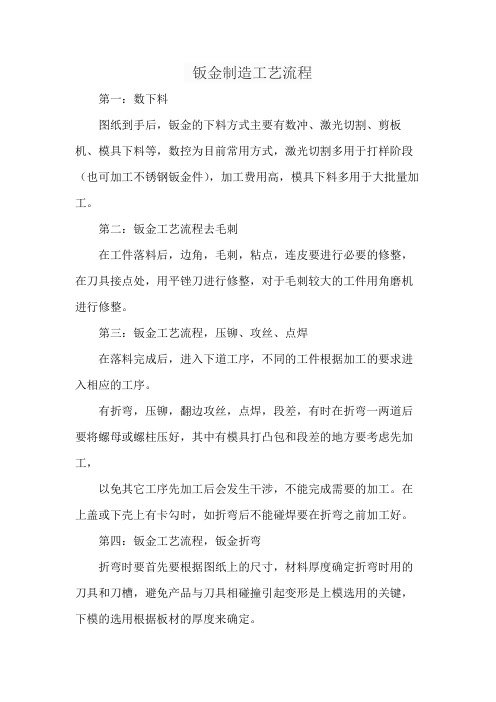
钣金制造工艺流程第一:数下料图纸到手后,钣金的下料方式主要有数冲、激光切割、剪板机、模具下料等,数控为目前常用方式,激光切割多用于打样阶段(也可加工不锈钢钣金件),加工费用高,模具下料多用于大批量加工。
第二:钣金工艺流程去毛刺在工件落料后,边角,毛刺,粘点,连皮要进行必要的修整,在刀具接点处,用平锉刀进行修整,对于毛刺较大的工件用角磨机进行修整。
第三:钣金工艺流程,压铆、攻丝、点焊在落料完成后,进入下道工序,不同的工件根据加工的要求进入相应的工序。
有折弯,压铆,翻边攻丝,点焊,段差,有时在折弯一两道后要将螺母或螺柱压好,其中有模具打凸包和段差的地方要考虑先加工,以免其它工序先加工后会发生干涉,不能完成需要的加工。
在上盖或下壳上有卡勾时,如折弯后不能碰焊要在折弯之前加工好。
第四:钣金工艺流程,钣金折弯折弯时要首先要根据图纸上的尺寸,材料厚度确定折弯时用的刀具和刀槽,避免产品与刀具相碰撞引起变形是上模选用的关键,下模的选用根据板材的厚度来确定。
其次是确定折弯的先后顺序,折弯一般规律是先内后外,先小后大,先特殊后普通。
有要压死边的工件首先将工件折弯到30°—40°,然后用整平模将工件压死。
压铆时,要考虑螺柱的高度选择相同不同的模具,然后对压力机的压力进行调整,以保证螺柱和工件表面平齐,避免螺柱没压牢或压出超过工件面,造成工件报废。
第五:钣金工艺流程,钣金焊接焊接有氩弧焊,点焊,二氧化碳保护焊,手工电弧焊等,点焊首先要考虑工件焊接的位置,在批量生产时考虑做定位工装保证点焊位置准确。
为了焊接牢固,在要焊接的工件上打凸点,可以使凸点在通电焊接前与平板均匀接触,以保证各点加热的一致,同时也可以确定焊接位置同样的,要进行焊接,要调好预压时间,保压时间,维持时间,休止时间,保证工件可以点焊牢固。
点焊后在工件表面会出现焊疤,要用平磨机进行处理,亚弧焊主要用于两工件较大,又要连接在一起时,或者一个工件的边角处理,达到工件表面的平整,光滑。
钣金加工工艺流程
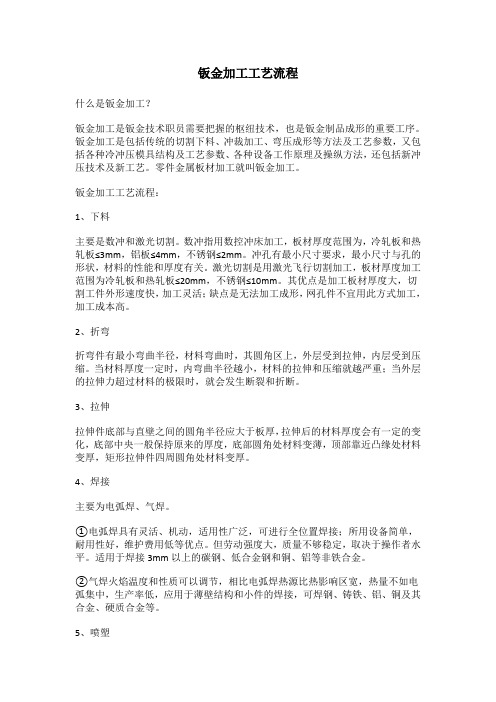
钣金加工工艺流程什么是钣金加工?钣金加工是钣金技术职员需要把握的枢纽技术,也是钣金制品成形的重要工序。
钣金加工是包括传统的切割下料、冲裁加工、弯压成形等方法及工艺参数,又包括各种冷冲压模具结构及工艺参数、各种设备工作原理及操纵方法,还包括新冲压技术及新工艺。
零件金属板材加工就叫钣金加工。
钣金加工工艺流程:1、下料主要是数冲和激光切割。
数冲指用数控冲床加工,板材厚度范围为,冷轧板和热轧板≤3mm,铝板≤4mm,不锈钢≤2mm。
冲孔有最小尺寸要求,最小尺寸与孔的形状,材料的性能和厚度有关。
激光切割是用激光飞行切割加工,板材厚度加工范围为冷轧板和热轧板≤20mm,不锈钢≤10mm。
其优点是加工板材厚度大,切割工件外形速度快,加工灵活;缺点是无法加工成形,网孔件不宜用此方式加工,加工成本高。
2、折弯折弯件有最小弯曲半径,材料弯曲时,其圆角区上,外层受到拉伸,内层受到压缩。
当材料厚度一定时,内弯曲半径越小,材料的拉伸和压缩就越严重;当外层的拉伸力超过材料的极限时,就会发生断裂和折断。
3、拉伸拉伸件底部与直壁之间的圆角半径应大于板厚,拉伸后的材料厚度会有一定的变化,底部中央一般保持原来的厚度,底部圆角处材料变薄,顶部靠近凸缘处材料变厚,矩形拉伸件四周圆角处材料变厚。
4、焊接主要为电弧焊、气焊。
①电弧焊具有灵活、机动,适用性广泛,可进行全位置焊接;所用设备简单,耐用性好,维护费用低等优点。
但劳动强度大,质量不够稳定,取决于操作者水平。
适用于焊接3mm以上的碳钢、低合金钢和铜、铝等非铁合金。
②气焊火焰温度和性质可以调节,相比电弧焊热源比热影响区宽,热量不如电弧集中,生产率低,应用于薄壁结构和小件的焊接,可焊钢、铸铁、铝、铜及其合金、硬质合金等。
5、喷塑通过烤炉等机器对五金件的表面进行自动喷油、喷粉等处理,使产品外表亮丽美观,达到包装出货的需求。
6、检验产品生产过程由质检部门实时把控,降低生产损耗和次品率,保证生产质量。
钣金工艺流程

生产工艺流程一:工艺流程:下料拉丝折弯焊接表处压铆二:材料的选定1: 不锈钢板。
分镜面和雾面不锈钢,它不需要做任何处理。
2:镀锌钢板。
在无听定要求下,一般选用。
随着钣金件结构的差异,工艺流程可能各不相同,但总的不超过以下几点. (本公司选用2-c)1.设计并绘出其钣金件的零件图,又叫三视图.其作用是用图纸方式将其钣金件的结构表达出来.2.绘制展开图.也就是将一结构复杂的零件展开成一个平板件.3.下料.下料的方式有很多种,主要有以下几种方式:a.剪床下料.是利用剪床剪出展开图的外形长宽尺寸.若有冲孔、切角的,再转冲床结合模具冲孔、切角成形.b.冲床下料.是利用冲床分一步或多步在板材上将零件展开后的平板件结构冲制成形.其优点是耗费工时短,效率高,可减少加工成本,在批量生产时经常用到.c.NC数控下料.NC下料时首先要编写数控加工程序.就是利用编程软件,将绘制的展开图编写成NC数控加工机床可识别的程序.让其跟据这些程序一步一步的在一块铁板上,将其平板件的结构形状冲制出来.d.激光下料.是利用激光切割方式,在一块铁板上将其平板件的结构形状切割出来.4.翻边攻丝.翻边又叫抽孔,就是在一个较小的基孔上抽成一个稍大的孔,再在抽孔上攻丝.这样做可增加其强度,避免滑牙.一般用于板厚比较薄的钣金加工.当板厚较大时,如2.0、2.5等以上的板厚,我们便可直接攻丝,无须翻边.5.冲床加工.一般冲床加工的有冲孔切角、冲孔落料、冲凸包、冲撕裂、抽孔等加工方式,以达到加工目的.其加工需要有相应的模具来完成操作.冲凸包的有凸包模,冲撕裂的有撕裂成形模等.6.压铆.压铆就本厂而言,经常用到的有压铆螺柱、压铆螺母、压铆螺钉等,其压铆方式一般通过冲床或液压压铆机来完成操作,将其铆接到钣金件上.7.折弯.折弯就是将2D的平板件,折成3D的零件.其加工需要有折床及相应的折弯模具来完成操作.它也有一定的折弯顺序,其原则是对下一刀不产生干涉的先折,会产生干涉的后折.8. 焊接.焊接就是将多个零件组焊在一起,达到加工的目的或是单个零件边缝焊接,以增加其强度.其加工方一般有以下几种:CO2气体保护焊、氩弧焊、点焊、机器人焊接等.这些焊接方式的选用是根据实际要求和材质而定.一般来说CO2气体保护焊用于铁板类焊接;氩弧焊用于铝板类焊接;机器人焊接主要是在料件较大和焊缝较长时使用.如机柜类焊接,可采用机器人焊接,可节省很多任务时,提高工作效率和焊接质量.9. 表面处理.表面处理一般有磷化皮膜、电镀五彩锌、铬酸盐、烤漆、氧化等.磷化皮膜一般用于冷轧板和电解板类,其作用主要是在料件表上镀上一层保护膜,防止氧化;再来就是可增强其烤漆的附着力.电镀五彩锌一般用冷轧板类表面处理;铬酸盐、氧化一般用于铝板及铝型材类表面处理;其具体表面处理方式的选用,是根据客户的要求而定.10.组装.所谓组装就是将多个零件或组件按照一定的方式组立在一起,使之成为一个完整的料品。
钣金工艺流程
钣金工艺流程钣金工艺流程是指通过对金属板材进行切割、弯曲、拼接等加工工序,制作出具有一定形状和功能的金属制品的过程。
钣金工艺具有灵活性、精密性和高效性等特点,被广泛应用于电子、通信、汽车、机械等行业。
钣金工艺流程主要包括以下几个步骤:1.工程设计:根据客户提供的需求和要求,进行产品的设计和方案制定。
包括结构设计、材料选择、工艺路线等。
2.材料准备:根据设计要求,选择适当的金属板材进行加工。
常用的金属材料有冷轧板、热轧板、不锈钢板等。
根据不同的材料性质和要求,还需要进行材料的预处理,如去除油污、氧化皮等。
3.投料加工:将准备好的金属板材投入到钣金加工设备中进行切割、冲孔等工序。
常用的钣金加工设备有激光切割机、剪板机、冲床等。
根据产品的不同要求,需进行不同的加工操作。
4.弯曲成型:将切割好的金属板材进行弯曲操作,使其得到所需的形状和角度。
常用的弯曲工艺有冷弯和热弯。
冷弯可以通过机械力产生,热弯则需要通过加热来使金属材料变软。
5.焊接拼接:将各个零部件进行焊接拼接,形成整体结构。
常用的焊接方式有点焊、气焊和激光焊等。
根据不同的材料和工艺要求,选择适合的焊接方式。
6.表面处理:对成型后的产品进行表面处理,如喷漆、喷粉等。
这样可以增加产品的美观性和保护性,防止氧化和腐蚀。
7.检测质量:对成品进行质量检测,以确保其符合客户的要求和标准。
常用的检测手段有外观检测、尺寸测量、力学性能测试等。
8.包装运输:对合格的产品进行包装和标识,以便于运输和存储。
根据产品的特点和重量等因素,选择适当的包装方式。
钣金工艺流程的每一步都需要进行精确的操作和控制,以确保产品的质量和性能。
随着科技的不断进步,钣金工艺流程也在不断发展和创新,应用范围越来越广泛。
钣金件的设计及制造工艺流程
钣金件的设计及制造工艺流程钣金件是一种广泛应用于工业制造领域的零部件,它主要通过对金属板材的冲剪、弯曲、焊接等工艺来实现设计所需要的形状和功能。
下面是钣金件的设计及制造工艺流程的详细介绍。
第一步:需求分析和设计准备在设计钣金件之前,首先需要进行需求分析,明确产品的使用需求和设计要求。
然后,根据需求确定材料、尺寸、厚度等设计参数,并进行初步的构思和草图绘制。
第二步:CAD建模和工程设计基于设计参数和构思草图,使用计算机辅助设计(CAD)软件进行钣金件的三维建模。
在建模过程中,需要考虑材料的可用性、加工工艺的可行性等因素。
同时,根据钣金件的实际应用场景,进行工程设计,包括强度分析、结构优化等。
第三步:工艺规划和冲裁在完成CAD建模和工程设计后,进行工艺规划,确定钣金件的制造工艺流程。
其中,冲裁是制造钣金件的第一步。
根据设计的形状和尺寸,在金属板材上使用剪切工具或冲裁机进行冲剪,将板材切割成所需的形状和大小。
第四步:弯曲和压制在冲裁之后,对已经切割好的钣金件进行弯曲和压制工艺。
通过应用压力和热力将钣金件弯折成所需的形状,并使用模具进行成形。
这个步骤通常需要使用弯曲机、热处理设备和模具。
第五步:焊接和装配根据设计要求,对钣金件进行焊接和装配。
焊接可以使用手工焊接、点焊、氩弧焊等不同的焊接方法,将不同的部件进行连接。
在焊接完成后,将其他辅助件(如螺钉、螺母等)进行装配,并进行测试和调整。
第六步:表面处理和涂装为了提高钣金件的外观和耐腐蚀性能,通常需要对表面进行处理和涂装。
表面处理可以采用砂轮抛光、喷砂、酸洗等方式来清洁和改善表面质量。
然后,进行锌镀、电镀、喷涂等涂装工艺,保护钣金件表面,并赋予其所需的颜色和质感。
第七步:质量检验和包装在钣金件的制造过程中,需要进行质量检验,包括尺寸精度、外观质量、材料成分等方面。
通过使用测量仪器和设备,对每个工序的产品进行检验,确保其符合设计要求和质量标准。
最后,对通过检验的钣金件进行包装,以便运输和保护。
钣金产品生产加工步骤详解(图文)
钣金产品制作步骤详解我们常见的钣金加工,主要由六大步骤组成,下面跟大家具体介绍:钣金加工图纸设计——>激光加工或(数控冲压)——>折弯——>焊接成型——>静电喷粉或(液体油漆)——>包装出货.1、图纸设计:一般客户提供图纸或样品,由公司工程人员进行尺量,设计,展开,形成加工分解图和组装图提交给生产部加工。
2、激光加工:激光切割机,可进行碳钢、不锈钢等材质材料进行切割下料,使用激光切割下料,工件加工后断面整齐、平滑漂亮,尺寸精准,对带有弧线的工件更具优势,是一般数控冲压无法替代的加工方式。
3、数控冲压:转塔数控冲床主要针对产品加工材料厚度较薄,一般在2.5mm以下材料较适合,钣金加工工件的孔较多或者需要开特殊模具才能加工的工件,批量较大的时候用数控冲压具有一定的成本优势。
4、折弯:工件下好料后如大部分需要进行折弯成型,公司拥有多台电脑折弯机,不仅速度快,工件加工更加精准。
5、焊接成型:工件在下好料后一般需要组装成型,组装方式有多种,有的直接用螺丝、拉铆等非焊接工艺成型,一般机械外壳钣金多使用焊接成型,公司一般采取氩弧焊接,碰焊,二氧化碳焊接等,焊接后对工件进行打磨抛光,这样工件就比较牢固,美观。
5、静电喷粉:静电喷粉主要针对碳钢材质工件,在工艺上一般先进行除油除锈,表调清洗,磷化处理,静电喷粉,高温烘烤等工艺,处理后工件表面美观,数年内不会生锈,成本低廉等优点。
液体油漆:此工艺和静电喷粉有差异,一般针对大工件,在无法搬运的情况下使用液体油漆有方便,成本低廉等优点,液体油漆一般分两步,在工件处理后上底漆再上面漆。
6、包装出货:包装前进行100%检查,并提供检查数据。
出货要求以及包装方式由客户正方代表现场确认OK,特此记录,以供客户再次确认流程工艺介绍1、钣金加工方法:(1)非模具加工:通过数冲、激光切割、剪板机、折床、铆钉机等设备对钣金进行加工的工艺方式,一般用于样品制作或小批量生产,成本较高.(2)模具加工:通过固定的模具,对钣金进行加工,一般有下料模,成型模,主要用于大批量生产,成本较低.2、钣金加工工艺下料:数冲、激光切割、剪板机成型—折弯、拉伸、冲孔:折弯机、冲床等其它加工:压铆、攻牙等焊接钣金的连接方式表面处理:喷粉、电镀、拉丝、丝印等1、钣金加工工艺——下料钣金的下料方式主要有数冲、激光切割、剪板机、模具下料等,数冲为目前常用方式,激光切割多用于打样阶段,加工费用高,模具下料多用于大批量加工。
钣金生产工艺流程
钣金生产工艺流程
《钣金生产工艺流程》
钣金加工是一种将金属板材经过切割、成型、焊接、打磨等工艺加工成各种零部件的加工方法。
钣金生产工艺流程通常包括如下步骤:
1.设计
首先,根据客户的要求和产品的用途,设计师需要制定钣金产品的设计方案。
这一步骤通常包括绘制产品图纸、确定材料和工艺要求等。
2.材料准备
在加工过程中,需要准备相应的金属板材作为原材料。
不同的材料和厚度对产品的性能和外观都有影响,因此选择合适的材料至关重要。
3.切割
将原材料按照设计图纸的要求进行切割。
常见的切割方式包括剪板机、数控切割机等。
4.成型
通过冲压、折弯、拉伸等工艺将金属板材成型为所需的零部件。
这一步骤需要根据产品的形状和要求选择合适的成型工艺。
5.焊接
将各个零部件进行焊接,通过氩弧焊、激光焊等方法将零部件
连接成整体。
焊接技术的好坏直接关系到产品的质量和使用寿命。
6.表面处理
对成型和焊接后的产品进行打磨、喷涂、电镀等表面处理,以提高产品的耐腐蚀性和美观度。
7.组装
将各个零部件按照设计要求进行组装,最终形成完整的产品。
8.质检
对成品进行质量检测,确保产品符合客户要求和标准。
以上就是钣金生产工艺的基本流程。
这一加工方法因其成本低、效率高、适用范围广等特点而被广泛应用于汽车制造、电子设备、家电等领域,并在工业制造中扮演着重要的角色。
- 1、下载文档前请自行甄别文档内容的完整性,平台不提供额外的编辑、内容补充、找答案等附加服务。
- 2、"仅部分预览"的文档,不可在线预览部分如存在完整性等问题,可反馈申请退款(可完整预览的文档不适用该条件!)。
- 3、如文档侵犯您的权益,请联系客服反馈,我们会尽快为您处理(人工客服工作时间:9:00-18:30)。
九江乐图钣金制作工艺流程锯床↗确认图纸金工→压铆↗↗设计→展开平面图→制造部→数冲→折弯→齐套→磷化→成型→打磨↘↘编程激光→补焊→打磨→清焊渣→喷塑→装机→成品包装设计根据客户提供的三维结构图和提供的部件图及零件图展开零件平面图,在平面图中标出外形尺寸,孔径,孔距。
转入编程,并指定加工流程(另附设计工作流程)设计人员将图纸流转到制造部,制造部按零件图要求,分三中形式进行加工一、对于方管及槽钢一类的零件,转入金工车间加工,按已下程序加工①按图纸长度要求到阿玛达H-250SAH锯床进行下料加②下料后的毛坯料需要钻孔的零件采用数冲加工模版,来对工件定位③先钻R1.5定位孔④按图纸要求的孔径尺寸钻孔⑤攻丝、拉铆、压铆等后续加工的孔,攻丝采用攻丝和手工攻丝机相结合的方法加工⑥需沉孔的零件,选用合适尺寸的90°钻头或沉孔器,进行沉孔加工⑦拉铆采用手动拉铆枪完成以上工序后,经检验确认合格后转入齐套库二、对于需要激光加工的零件,按要求激光切割,切割的零件,经检验合格后转入齐套库三、对于需要板材加工的零件内部安装板,及前后门板顶底板,侧板、前后屏蔽框,内部支架等钣金工件需要数控冲床来加工,来保证零件的度要求,操作工,按展开尺寸的要求,板材的厚度要求,来对板材进行数冲加工(数冲加工的程序另附)对加工完的平面零件检验,合格后转入到修毛刺工序,修毛刺接到数冲转来的板材进行逐一拆除连接部位,对零件的四周毛边修锉,修锉的工具有修边器具,平锉,半圆锉等工具来修毛刺,对修毛刺零件做到、不刮手、无尖角,边角圆润滑,经检验合格后零件与图纸一起流转到折弯处。
四、折弯接到平面料和加工图之后按以下程序加工①看清图纸的技术要求,工艺要求②对加工的来料进行材质与料厚的分类摆放;③要求对称加工的零件,对称摆放整齐④料厚一样的板料放在一起⑤模具的选用,1.0mm用V6下摸,1.5mm用V8下模,2.0mm 用V12下模,2.5mm用V14下模,3.0用V16下模,确保料后一样,加工后零件R角一致,(折弯机加工的参数另附)⑥对要求提前压铆螺母的零件是先折一道边,压铆后再折二道弯,要看清工艺流程。
⑦掌握零件性能的用途,对被包容件(如柜内的安装板之内的零件)尺寸控制在下公差⑧对包容件,(如柜体的的2处的左右侧板,顶底板)尺寸控制为上公差避免在焊接过程中长壳现象的发生⑨对尺寸的标准控制,按钣金一般公差尺寸加工0≤6 ±0.1 6≤30 ±0.2 30≤120 ±0.3 120≤400 ±0.5 400≤1000 ±0.81000≤2000 ±1.2⑩角度公差控制0≤6±0.1°6≤30±0.2°30≤120±0.3°120≤400±0.5°400≤1000±0.8°1000≤2000±1.2°○11折弯是看清零件的方向,尺寸,首件零件自检,自检合格后交专职检验首检,首检合格后进行批量折弯,折弯合格后操作工签字检验员签字后转入齐套按要求齐套将所有零件收理完整后,按材质不同将零件分类,按设计要求在焊接前要磷化的零件流转到酸洗磷化工段把不锈钢的零件,流转到焊接区的待焊处,交成型核对图纸交接数量,签收,签字。
磷化组接到零件,对照要求将零件装入吊柜中,送入封闭式磷化作业区,进行前处理(磷化的工艺流程与参数表另附)磷化的目地:使零件表面生成一层不溶于水的磷化膜,以提高基体金属表面和涂层的结合强度。
其磷化膜的表面质量要求符合国际GB6807-86钢铁工作涂装前磷化处理的技术条件,磷化工序完成后的零件经检验合格后零件流转到成型待焊处交接签收签字。
焊接成型组将上道工序流转来的零件1.做焊接前的准备工作,对照图纸清点数量。
焊接先看零件图是否齐全,再检查每张零件图中是否有检验员签字,再检查设计配置的模板的合理性。
2.上述工序完成后对零件分类理料,摆放,一致的零件逐个一一摆放到把仓板上。
做上标识符号,便于焊接时一目了然。
3.焊接成型前将所有需要倒角的方管及槽钢进行倒角,尺寸控制3*3mm4.检查焊接机是否正常运转,焊电阻柜体的设备有威特力氩弧焊和气体保护焊机。
气体采用99.99高纯度氩气,气保焊丝采用上海金桥焊丝,根据材料厚度采用合适电流操作。
5.工具夹具采用弹簧大力钳,G型夹具,旋转收紧夹具,自制的工装夹具。
6.在焊接过程对尺寸的控制精密处用模板定位控制。
7.对角度控制采用先点焊校正90度后四角处用方管或角钢焊接固定,再采用满焊,完整焊接。
8.在工件一与工件二连接处采用大力钳和G型夹具相结合措施校正尺寸后再焊接。
9.为防止焊渣飞溅到相邻的工件表面,采用防溅剂喷射表面。
10.焊接前对所有的方管和槽钢校直平面防止焊后影响质量。
11.对所有需焊接螺母的钣金件进行螺母焊接,螺母材质为不锈钢材质。
12.对变形后工件我们采取用气焊吹烤加热后用手工校正至公差范围内,之后用冷水冷却。
以上准备工作完成后首先对顶底柜的焊接第一件长度料放在平台上,为防止扭曲变形两头和中间共用4~5个自制的工装夹具。
工件与平台夹紧后方管两侧在与其他零件焊接尺寸的空隙处用点焊形式焊在平台上焊牢定位,再配置两侧竖档与对面横档,先点焊拼接,控制长度,宽度,对角线的尺寸在图纸要求的公差范围以内再用夹具锁紧与平台的连接,同样用点的方法与平台点焊在一起来保证整个平面一致,外形尺寸定位后再配置框架内部竖档及横档。
对照图纸要求尺寸方向根据主次顺序一一点焊在框架内。
操作工自检合格后再由检验员对框架内所有焊接尺寸与孔距尺寸全检,各项尺寸符合要求后电焊工对柜内的点焊处喷防溅剂。
对点焊处用气保焊接焊缝高度不能超过3MM的标准焊缝做满焊处理,焊后等工件完全冷却之后折除工装夹具,切除工件与平台的连接点,然后将顶底柜的焊缝面磨平整,清除焊渣,打磨平台与框架的焊接点,将柜架翻一面焊接另一面用相同的方法完成对另一面的焊接,冷却后取下柜架送到打磨车间进行打磨处理。
打磨按要求打磨两个平面与四角的焊疤及连接点焊处。
经检验合格后工件流转回到焊接平台,再清除焊渣。
完成后顶板对顶柜架进行包裹焊接时大力钳夹紧板料与柜边,夹一点点焊一点,四周点焊完成后,再点中间横档与板料的连接。
有空隙的位置用专用自制夹具夹紧后点焊。
直至焊点全部完成。
底板部件与顶板相同方法加工,顶底板完成后竖起来侧板横向与其配合无疑后用工装夹具再用氩弧焊点焊,四角用相同方法焊接。
左右侧板点焊好后将柜架主体竖起来,逐一将四根立柱用夹具和侧板边缘处夹牢定位点焊后用卷尺校对角线尺寸。
控制在规定尺寸之内。
定位后四周用方管或角钢加以固定直角随后配焊左右两侧内部的横竖档,按零件图尺寸要求点焊定位。
自检合格后,检验现场核对,尺寸合格后再将点焊处全部满焊,冷却后送到打磨车间磨平两侧面平面焊疤,再流转回焊接平台,焊工对侧板与横档加以点焊连接。
在两侧板外面平面为校平平面用3MM 板条横向点焊加以校平,内部点焊连接有缝隙处用专用自制的夹具辨紧,里面再点焊连接,直至柜架的四周边完成。
主体外框架完成后型材和侧板,底板与侧板之间焊接按要求采用错位密集点焊。
缝口处断续焊,点焊处打磨光滑,焊缝处填充处理。
随后按照图纸要求尺寸对柜体加内部的焊接方管,先焊长方管点焊定位后检验合格后,两头满焊,对长度中容易变形处用角钢加以固定尺寸。
随后内部短横档全部点焊,经检验合格后,对所有型材间焊接全部角焊。
焊接质量为A级焊缝高度3MM柜架内部结构全部完成之后,转打磨车间磨平内部的平面处。
再流转回焊接平台,对内部的安装板,安装支架,扎线支架,部分包边,三角固定板,等配件按图纸要求全部焊完整,零件焊接为继续角焊,焊缝长度为40±5MM焊缝间200±20MM转角处50-100MM有一段焊缝在所有内部配件焊完尺寸检验合格后再流转到打磨车间,对平台上的焊缝及表面的焊疤打磨,用规格125*6*16的磨光片和100*2.5*16MM郑州磨具公司产凯捷牌。
可弯曲不锈钢,磨片对柜体粗打磨,磨后修R角用平板锉加工,有焊缝凹处再补焊处理,再进一步平磨,用百叶磨光片加工表面再修锉R角,打磨工序完成后柜架流转到焊接平台。
焊工对门板的配制,门板上的配件,按图纸要求焊接加强筋及文件袋为防止门板变形。
加强筋及文件袋等部件均采用点焊连接,焊后磨光焊疤。
二.柜架与前门屏蔽柜的配合要求,屏蔽柜材料为拉丝316不锈钢板经折弯成型后的零件左右上下为一个屏蔽柜架体,连接柜架面上有200MM间距两排交错的焊接孔为保证焊接时不锈钢屏蔽门不扭曲不变形。
焊接时用弹簧大力钳夹紧屏蔽条与柜体的间隙,在焊接孔中点焊,采用密集点焊,那边采用断续焊。
密集点焊严格按照型材开孔位置进行点焊,续焊焊缝长度为20±5MM。
焊缝间距200±20MM,距转角处必须有一段50~100MM焊缝。
在长于宽连接处必须满焊,对所有的点焊孔满焊处理。
焊后对焊缝及点焊满焊处进行打磨,打磨后的表面必须进行拉丝处理。
不锈钢焊疤处采用粗磨细抛然后再拉丝,拉丝完成后用绿洁布再擦等工序来完成。
三.后封板侧屏蔽不锈钢焊接时屏蔽条边柜主体采用密集点,内处边同时采用断续焊,焊缝长度20±5MM内外焊缝错开,夹具采用大力弹簧钳夹紧后焊接,焊缝间距200±20MM。
距转角处50~100MM有一段焊缝,其中外侧焊缝高度小于2MM焊缝处填充导电填充材料磨平处理,焊后拉丝处理。
后封板侧屏蔽不锈钢焊接时,注意屏蔽要求。
框架与不锈钢屏蔽体条保证无缝连接,所有的错位开孔点焊处必须满焊。
焊完后磨平处理。
焊接时用大力钳夹紧屏蔽条与框架的位置,间断移动焊接来保证不锈钢与屏蔽条不扭曲不变形。
焊后拉丝处理。
四.每两个不锈钢屏蔽条接触面满焊处理,焊后磨平处理。
五.前门板与框架的连接,(前门板的配件,开孔盒,加强筋,文件袋,螺钉,扎线支架等必须在连接前完成)前门柜上前将铰链用螺钉装在柜架的螺孔上,装上门后校正门的间距尺寸,随后再装配内部的连接螺钉的定位块,为确保定位块的准确性,先把前门不脱落螺钉与支架连接,再用螺钉与定位块连接。
连接后再用点焊形式焊在框架位中,待一块门板中连接全部定位后,不脱落螺钉点焊在门上不脱落螺钉旋转灵活后再将定位块满焊。
支架需编号,避免装配时错位,再配焊屏蔽条支架先把屏蔽条点焊成方柜,再把方柜放到柜架上的屏蔽柜上。
配后无疑问后再把门关上从里面把屏蔽柜点焊在前门上,这样能保证前门的屏蔽柜与柜架的屏蔽柜完全一致。
卸下门后将屏蔽条开孔处点焊,待门板全部配好后,再将铰链焊接在柜架上,铰链与门铰链用插销连接。
焊接工序全部完成后焊工对柜架上的所有零件的焊接尺寸全部自检一遍,以及焊渣的清理内部圆滑处理。