FAI流程
FAI流程
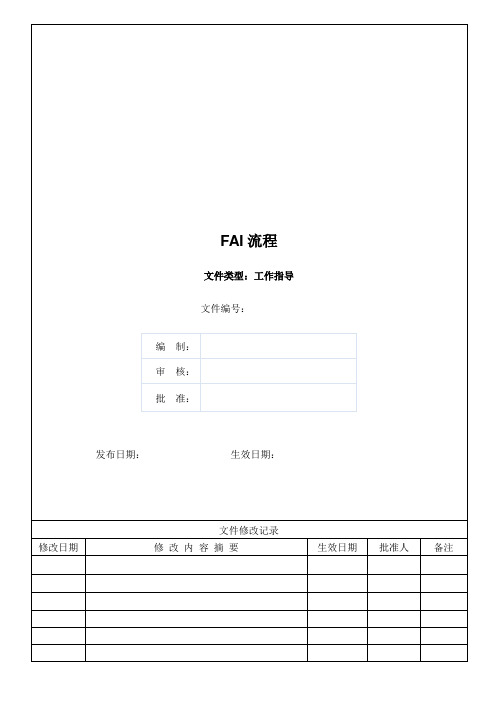
1.目的规范新供应商提交零部件或供应商提交新项目零部件流程,确保公司产品所使用零部件及材料皆能符合公司要求,以保证制程的相对稳定,获得稳定的产品以满足客户需求。
2. 适用范围2.1 新零部件:第一次生产的量产零部件(通过计划下采购订单的零部件定义为量产零部件);2.2 转移零部件:已经有一个供应商量产,现在转移开发另一供应商,转移零部件不一定同时有要求交货的订单,时间比较充裕;2.3 设计变更零部件:是有设计变更的零部件,此过程也包括供应商的产品设计更改或过程更改后的首批产品;2.4 停止供货超过两年以上的零部件和材料,若要再次采购时,须重新做首件检验;3. 术语和定义FAI—First Article Inspection,意为首件检查A.狭义FAI: 通常是指FAI检验报告,(尺寸检测、功能测试、外观检查);B.广义FAI的理解1.包含:FAI报告、FAI承认文件、FAI承认样品、还包括FAI制程、设备、检具和产能;2.包含新产品开发段的工艺管控、品质管控、生产管控;3.侧重于品管,重点在工管、目标在生管;4.对于OEM而言,FAI在于客户的承认;4. 职责4.1 质保部4.1.1质保部负责供应商首件样品检验,并填写《样品检测报告》;4.1.2初步审核供应商所提交的各类质量报告(包括测试报告和供应商提交的技术文件);4.1.3把检验结果和初步审核结论填写在《供应商首件确认报告》上;4.1.4提交《供应商首件确认报告》至技术部研发科进行最终确认;4.2 技术部4.2.1技术部研发科负责提供所有首件检验零部件的图纸、技术要求/规范(有可靠性要求的零部件,需在技术要求/规范条款中明确之);4.2.2若标准件和目录件有特定的技术要求时,需定义标准件和目录件的首件检验的零部件,并提供相应的技术要求/规范;4.2.3技术部研发科最终批核供应商首件样品并在《供应商首件认可报告》上签字确认;4.2.4技术部工艺科配合制造部进行样品的试制,并对试制中的工艺参数进行记录,为样品量产后编制过程作业指导书做准备;4.3 采购部4.3.1采购部负责把技术规范、图纸和供应商所需提交的技术文件等信息传递给供应商及协调供应商实施,并实施零部件样品报质保部检验;4.3.2采购部仓库负责首件样品的接收、入库、储存、防护及发料4.4 制造部负责配合按产品图纸和相关技术要求进行样品的试装和试验;5. 作业内容5.1 对外购零部件(非标准件和非目录件的零部件)首次使用时都需进行首件检验,技术部研发科提供图纸、技术要求/规范,有可靠性要求的零部件,研发科需在技术要求/规范条款中明确此要求,并让供应商确认之;若现有外购零部件更换供应商时,也需要进行首件检验,合格后才能采购。
fai法则

fai法则
FAI法则是指柴尔德·PETRI提出的Feedforward、Action、Integration 这三个步骤的管理方法。
它是一种管理流程,用于优化系统的功能和效率。
1. Feedforward(预见性):在进行任何行动之前,需要先进行预见性的思考和计划。
这包括对目标和期望结果进行明确的规划,并确定实现这些目标所需的资源和措施。
2. Action( 行动):根据预见性的计划,采取行动来实施计划,并达成预定的目标。
在这个阶段,需要协调和组织团队、分配工作任务,并确保执行的高效性和准确性。
3. Integration( 整合):在行动完成后,需要对结果进行评估和整合。
这包括比较实际行动的结果与预期目标的差距,分析原因和影响,并从中获取反馈信息。
根据反馈信息,可以进行必要的修正和改进,以最大程度地提高系统的效能和质量。
FAI法则强调了计划、执行和反馈的重要性,将管理过程划分为三个阶段,并使其成为一个连续循环的过程。
通过预见性的计划,及时有效的行动和持续的整合和反馈,FAI法则可以帮助管理者不断优化和改进组织的运作,提高工作效率和达成预期目标。
FAI流程

1.目的规范新供应商提交零部件或供应商提交新项目零部件流程,确保公司产品所使用零部件及材料皆能符合公司要求,以保证制程的相对稳定,获得稳定的产品以满足客户需求。
2. 适用范围2.1 新零部件:第一次生产的量产零部件(通过计划下采购订单的零部件定义为量产零部件);2.2 转移零部件:已经有一个供应商量产,现在转移开发另一供应商,转移零部件不一定同时有要求交货的订单,时间比较充裕;2.3 设计变更零部件:是有设计变更的零部件,此过程也包括供应商的产品设计更改或过程更改后的首批产品;2.4 停止供货超过两年以上的零部件和材料,若要再次采购时,须重新做首件检验;3. 术语和定义FAI—First Article Inspection,意为首件检查A.狭义FAI: 通常是指FAI检验报告,(尺寸检测、功能测试、外观检查);B.广义FAI的理解1.包含:FAI报告、FAI承认文件、FAI承认样品、还包括FAI制程、设备、检具和产能;2.包含新产品开发段的工艺管控、品质管控、生产管控;3.侧重于品管,重点在工管、目标在生管;4.对于OEM而言,FAI在于客户的承认;4. 职责4.1 质保部4.1.1质保部负责供应商首件样品检验,并填写《样品检测报告》;4.1.2初步审核供应商所提交的各类质量报告(包括测试报告和供应商提交的技术文件);4.1.3把检验结果和初步审核结论填写在《供应商首件确认报告》上;4.1.4提交《供应商首件确认报告》至技术部研发科进行最终确认;4.2 技术部4.2.1技术部研发科负责提供所有首件检验零部件的图纸、技术要求/规范(有可靠性要求的零部件,需在技术要求/规范条款中明确之);4.2.2若标准件和目录件有特定的技术要求时,需定义标准件和目录件的首件检验的零部件,并提供相应的技术要求/规范;4.2.3技术部研发科最终批核供应商首件样品并在《供应商首件认可报告》上签字确认;4.2.4技术部工艺科配合制造部进行样品的试制,并对试制中的工艺参数进行记录,为样品量产后编制过程作业指导书做准备;4.3 采购部4.3.1采购部负责把技术规范、图纸和供应商所需提交的技术文件等信息传递给供应商及协调供应商实施,并实施零部件样品报质保部检验;4.3.2采购部仓库负责首件样品的接收、入库、储存、防护及发料4.4 制造部负责配合按产品图纸和相关技术要求进行样品的试装和试验;5. 作业内容5.1 对外购零部件(非标准件和非目录件的零部件)首次使用时都需进行首件检验,技术部研发科提供图纸、技术要求/规范,有可靠性要求的零部件,研发科需在技术要求/规范条款中明确此要求,并让供应商确认之;若现有外购零部件更换供应商时,也需要进行首件检验,合格后才能采购。
【通用文档】fai计算流程.doc

一、所需数据每日的500米分辨率的HDF文件二、几何校正ENVI下File -> Open External File ->EOS -> MODIS->打开500米的HDF文件->找到太湖->右键ROIMap-> Georeference MODIS ->对辐亮度和反射率数据分别进行几何校正->编辑spatial subset->ROI/EVF->选择区域->OK在Georeference MODIS parameters下,投影选择Taihu->OK->输出:日期taihu_radiance_proj日期taihu_reflect_proj 三、记录红光-近红外-短波红外辐亮度值针对MODIS数据,对辐亮度数据,1、2、5波段分别查看每个波段的平均辐亮度值,记录下来,在使用6S模型时使用。
也可记录下1、2、5波段的反射率值(那样是话,在6S 中RAPP那项前面需加上负号)。
如下图四、运行6S模型参数如下:GEOMETRICAL CONDITIONS:---------------------igeom (0-7)= 0 传感器类型YOUR OWN CONDITION:---------------------25.44 127.91 14.04 98.67 6 5 太阳天顶角与方位角,卫星天顶角与方位角,日期ATMOSPHERIC MODEL:---------------------idatm (0-8) = 2 大气模式。
2代表Midlatitude Summer AEROSOL MODEL (TYPE):---------------------iaer (0-12) = 1 气溶胶类型。
1代表Continental AEROSOL MODEL (CONCENTRATION):------------------------------v (visibility) = 15.0 能见度,需要查阅当地的气象资料xps (in km) = -0.120 当地的海拔,加上-号xpp =-705 传感器的高度,加上-号ENTER THE SPECTRAL CONDITIONS:------------------------------iwave (-1 to 34) = 42 传感器接收波段,如MODIS为42-48GROUNRD REFLECTANCE (TYPE)--------------------------inhomo (0-1) = 0 是否为均质地物,0均一,1,不均一idirec = 0 是否考虑二向性,0表示没有,1表示有igroun = 4 地物类型,如1表示植被,4表示湖泊rapp = 48.06356 RAPP=gias*DN+bias,大气层顶太阳辐亮度(1、2、5波段分别计算)分别计算1、2、5波段,6S的结果中,在第3页找到计算的瑞利散射反射率值,记录下来五、计算FAI①ENVI下打开反射率数据②计算R TOA-R6S,R6S为1、2、5波段分别用6S计算出来的值。
FAICPK的讲解

FAICPK的讲解FAI讲解⼀﹑FAI的定义⼆﹑测量FAI的⽬的三﹑FAI的测量步骤四﹑FAI检测流程五﹑FAI修模流程六﹑结论⼀﹑定义FAI:FirstArticleInspectionReport.汉语译作:⾸件全尺⼨检验报告.⼆﹑⽬的制作FAI报告是为了检查成型后的产品尺⼨是否在设计公差之内序号FAI步骤1从⼯程⼈员或⽣管⼈员拿到样品3组和图纸⼀份。
2内容对照图纸分析产品上的尺⼨需⽤何种仪器测量。
⼯具设备图纸﹑3组样品﹑卡尺﹑投影仪﹑三次元⽅法从⼯程⼈员⼿⾥拿到产品图纸。
对照图纸分析产品上的尺⼨需⽤何种仪器测量。
3内容对产品上可以⽤卡尺和测⾼仪测量的尺⼨进⾏测量⼯具设备图纸﹐样品3组﹐FAI测量记录单⼀份。
卡尺﹑测⾼仪器﹑温湿度计﹑空调⽅法根据产品特性调整空调温度﹐直到温湿度计达到规定温湿度后﹐对照图纸尺⼨﹐固定好产品﹐⽤卡尺和测⾼仪测量3组样品上可以测量的尺⼨﹐并在FAI测量记录单上记录测量值三﹑步骤5.1﹑对FAI报告进⾏分析六﹑结论模具⼚以FAI报告为依据﹐检查模具尺⼨﹐进⾏修模动作﹐使得模具被承认﹐最终满⾜量产要求⼀﹑定义⼆﹑⽬的三﹑计算⽅法四﹑结论CPK讲解⼀﹑定义CPK:ComplexProcessCapabilityindex.汉语译作:制程能⼒指数.CPK是制程准确度(Ca)与制程精确度(Cp)两者的中和反应Ca反应的是位置关系(集中趋势),Cp反应的是散布关系(离散趋势)⼆﹑⽬的根据加⼯成形产品尺⼨的变差,来验证单⼀设备的加⼯能⼒或反映整个制程的稳定性及可靠性.三﹑计算⽅法CA=X-X(USL-LSL)/2CP=(USL-LSL)6σX:标准值USL:上限值LSL:下限值CPK=(1-|CA|)×CPσ:标准偏差Ca:制程准确度Cp:制程精确度σ=Sqr(∑(xn-xbar)^2/(n-1))∑:总和Xbar:x的算术平均值^2:⼆次⽅Sqr:平⽅根注1标准偏差(StdDev,StandardDeviation)-统计学名词⼀种量度数据分布的分散程度之标准,⽤以衡量数据值偏离算术平均值的程度标准偏差越⼩,这些值偏离平均值就越少,反之亦然标准偏差公式:S=Sqr(∑(xn-xbar)^2/(n-1))统计学名词解释注1范例﹕⼯件名称﹕BACKBONE重点尺⼨﹕12SPEC:123+/-0.5某⼀天进料量测值如下﹕X=123USL=123.5LSL=122.5X=123.1016σ=0.0715CA=0.2032CP=2.3310CPK=1.8573CPK值的意义:主要体现制程的稳定性.1.制程能⼒很好:CPK值⼤于2以上2.制程能⼒好:CPK值⼤于1.67~2之间3.制程能⼒良好:CPK值在1.33~1.67之间4.制程能⼒⼀般﹕CPK值1.0~1.33之间5.制程能⼒差:CPK值在1.0以下四﹑结论。
FAI流程
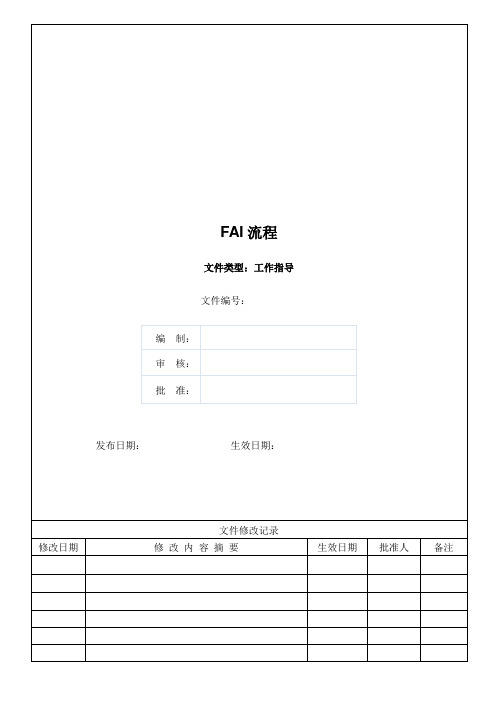
1.目的规范新供应商提交零部件或供应商提交新项目零部件流程,确保公司产品所使用零部件及材料皆能符合公司要求,以保证制程的相对稳定,获得稳定的产品以满足客户需求。
2. 适用范围2.1 新零部件:第一次生产的量产零部件(通过计划下采购订单的零部件定义为量产零部件);2.2 转移零部件:已经有一个供应商量产,现在转移开发另一供应商,转移零部件不一定同时有要求交货的订单,时间比较充裕;2.3 设计变更零部件:是有设计变更的零部件,此过程也包括供应商的产品设计更改或过程更改后的首批产品;2.4 停止供货超过两年以上的零部件和材料,若要再次采购时,须重新做首件检验;3. 术语和定义FAI—First Article Inspection,意为首件检查A.狭义FAI: 通常是指FAI检验报告,(尺寸检测、功能测试、外观检查);B.广义FAI的理解1.包含:FAI报告、FAI承认文件、FAI承认样品、还包括FAI制程、设备、检具和产能;2.包含新产品开发段的工艺管控、品质管控、生产管控;3.侧重于品管,重点在工管、目标在生管;4.对于OEM而言,FAI在于客户的承认;4. 职责4.1 质保部4.1.1质保部负责供应商首件样品检验,并填写《样品检测报告》;4.1.2初步审核供应商所提交的各类质量报告(包括测试报告和供应商提交的技术文件);4.1.3把检验结果和初步审核结论填写在《供应商首件确认报告》上;4.1.4提交《供应商首件确认报告》至技术部研发科进行最终确认;4.2 技术部4.2.1技术部研发科负责提供所有首件检验零部件的图纸、技术要求/规范(有可靠性要求的零部件,需在技术要求/规范条款中明确之);4.2.2若标准件和目录件有特定的技术要求时,需定义标准件和目录件的首件检验的零部件,并提供相应的技术要求/规范;4.2.3技术部研发科最终批核供应商首件样品并在《供应商首件认可报告》上签字确认;4.2.4技术部工艺科配合制造部进行样品的试制,并对试制中的工艺参数进行记录,为样品量产后编制过程作业指导书做准备;4.3 采购部4.3.1采购部负责把技术规范、图纸和供应商所需提交的技术文件等信息传递给供应商及协调供应商实施,并实施零部件样品报质保部检验;4.3.2采购部仓库负责首件样品的接收、入库、储存、防护及发料4.4 制造部负责配合按产品图纸和相关技术要求进行样品的试装和试验;5. 作业内容5.1 对外购零部件(非标准件和非目录件的零部件)首次使用时都需进行首件检验,技术部研发科提供图纸、技术要求/规范,有可靠性要求的零部件,研发科需在技术要求/规范条款中明确此要求,并让供应商确认之;若现有外购零部件更换供应商时,也需要进行首件检验,合格后才能采购。
FAI流程图

整改报告 《首件(小批)样品认可报告》 《首件(小批)样品认可报告》 《首件(小批)样品认可报告》 整改报告 《合格供方名录》
供应 商FAI 控制 程序 流程 图
5、实验
5、实验 // 6、根据试装实验结果 做出判断 7、提交整改报告,整 改后重新FAI
6、根据试装实验结果做出判断
拒收
// // //
附件1:供应商FAI控制程序流程图
阶段 供应商 采购部 质量部 制造部 研发部 阶段过程 控制要点 // 《首件(小批)样品认可报告》 // 根据《检验操作规程》进行检验 出现重大缺陷,质量部通知采购部 或重新选择供应商,或整改后重新 FAI 配合质量部安排试装 试验室根据实验大纲进行试验 根据首件报告,质量部和研发部确 认结果 供应商提交整改报告后重新FAI 供应商通过FAI后,进行小批量生 产,采购部将其纳入合格供方名录 《首件(小批)样品认可报告》 《首件(小批)样品认可报告》 《首件(小批)样品认可报告》 操作说明 输入 输出
通过?
8、小批量生产
7、提交整改 报告,整改后 重新FAI 8、小批量 生产
有条件通过
通过
1、提出首件检 验要求
2、组织首件检验 可以试装4、试装
工作
1、提出首件检验要求 2、组织首件检验工作 3、重新选择供应商、 重新FAI 4、试装
3、重新FAI
3、重新选择供应商
或
或 重大《首件(小批)样品认可报告》 《首件(小批)样品认可报告》 《首件(小批)样品认可报告》 《首件(小批)样品认可报告》 《首件(小批)样品认可报告》
FAI首件控制流程图

输入
客户
技术质量部
其他部门
输出
NO
YES
YES
NO
**核心工序
名称:FAI的控制流程
版本:A/0
编制日期:2020.4
条款号:8.6
过程负责人:技术质量部经理
流程类型:SP
工艺/方法/指令要求:
人员/资格/接口部门/支持:
管理:目标/KPIS
1.《采购控制程序》HNMDEXX-QP-8-3
2.《FAI控制程序》HNMDEXX-QP-8-11
3.产品技术规范或订货技术条件
4.检修协议
1.技术质量部
2.物流采Байду номын сангаас部
3.市场部
4.供应商/客户
1.关键物料采购供应商供货合格率
2.内部终端产品一次交验合格率
3.纠正措施按时完成率
工艺/设备/设施:
过程的风险/机会:
1.检测场所
2.检具
3.测试设备
4.生产设备
1.首件交付不符合要求或部分不符影响首件通过
2.没有按要求提供的首件报告资料
- 1、下载文档前请自行甄别文档内容的完整性,平台不提供额外的编辑、内容补充、找答案等附加服务。
- 2、"仅部分预览"的文档,不可在线预览部分如存在完整性等问题,可反馈申请退款(可完整预览的文档不适用该条件!)。
- 3、如文档侵犯您的权益,请联系客服反馈,我们会尽快为您处理(人工客服工作时间:9:00-18:30)。
1.目的
规范新供应商提交零部件或供应商提交新项目零部件流程,确保公司产品所使用零部件及材料皆能符合公司要求,以保证制程的相对稳定,获得稳定的产品以满足客户需求。
2. 适用范围
2.1 新零部件:第一次生产的量产零部件(通过计划下采购订单的零部件定义为量产零部件);
2.2 转移零部件:已经有一个供应商量产,现在转移开发另一供应商,转移零部件不一定同
时有要求交货的订单,时间比较充裕;
2.3 设计变更零部件:是有设计变更的零部件,此过程也包括供应商的产品设计更改或过程
更改后的首批产品;
2.4 停止供货超过两年以上的零部件和材料,若要再次采购时,须重新做首件检验;
3. 术语和定义
FAI—First Article Inspection,意为首件检查
A.狭义FAI: 通常是指FAI检验报告,(尺寸检测、功能测试、外观检查);
B.广义FAI的理解
1.包含:FAI报告、FAI承认文件、FAI承认样品、还包括FAI制程、设备、检具和产能;
2.包含新产品开发段的工艺管控、品质管控、生产管控;
3.侧重于品管,重点在工管、目标在生管;
4.对于OEM而言,FAI在于客户的承认;
4. 职责
4.1 质保部
4.1.1质保部负责供应商首件样品检验,并填写《样品检测报告》;
4.1.2初步审核供应商所提交的各类质量报告(包括测试报告和供应商提交的技术文件);
4.1.3把检验结果和初步审核结论填写在《供应商首件确认报告》上;
4.1.4提交《供应商首件确认报告》至技术部研发科进行最终确认;
4.2 技术部
4.2.1技术部研发科负责提供所有首件检验零部件的图纸、技术要求/规范(有可靠性要求的零
部件,需在技术要求/规范条款中明确之);
4.2.2若标准件和目录件有特定的技术要求时,需定义标准件和目录件的首件检验的零部件,并
提供相应的技术要求/规范;
4.2.3技术部研发科最终批核供应商首件样品并在《供应商首件认可报告》上签字确认;
4.2.4技术部工艺科配合制造部进行样品的试制,并对试制中的工艺参数进行记录,为样品量产
后编制过程作业指导书做准备;
4.3 采购部
4.3.1采购部负责把技术规范、图纸和供应商所需提交的技术文件等信息传递给供应商及协调供
应商实施,并实施零部件样品报质保部检验;
4.3.2采购部仓库负责首件样品的接收、入库、储存、防护及发料
4.4 制造部负责配合按产品图纸和相关技术要求进行样品的试装和试验;
5. 作业内容
5.1 对外购零部件(非标准件和非目录件的零部件)首次使用时都需进行首件检验,技术部研
发科提供图纸、技术要求/规范,有可靠性要求的零部件,研发科需在技术要求/规范条款中明确此要求,并让供应商确认之;若现有外购零部件更换供应商时,也需要进行首件检验,合格后才能采购。
如果有标准件和目录件有特定技术要求时,由研发科定义需要首件检验的零部件,并提供技术要求/规范;
5.2 采购工程师把需要提交的零部件图纸、技术要求/规范及《样品检测报告》和《供应商首
件确认报告》传递至供应商,并要求供应商按规定填写《样品检测报告》和《供应商首件确认报告》;
5.3 供应商对照我公司提供的图纸、技术要求/规范逐一条款进行响应,并把响应结果反馈至
我公司研发科,由项目工程师或研发经理确认这些技术文件,若有异议时,由供应商做出解答;
5.4 供应商依照图纸、技术要求/规范生产并提交首件样品,并将标识好的首件样品和《样品
检测报告》、材质报告(有资质试验室的报告,顾客有要求时按顾客要求)和有关性能试验报告(有资质试验室的报告,顾客有要求时按顾客要求)等一起送至仓库,仓库收到首件样品后,将样品放置于“来料待检区”,同时通知质保部经理安排报检;若质保部经理发现供应商提供的资料不完整,由采购工程师负责向供应商索取。
供应商在首件样品提交时,全尺寸测量报告与被测量样品(可编号)一一对应起来,供应商全尺寸测量至少5件,性能测试至少测量3件;
5.5 首件样品到达后,仓库通知质保部经理进行报检,质保部经理将收到的《样品检测报告》
和《供应商首件确认报告》交IQC,IQC负责样品检验,并把样品检验记录填写于《样品检测报告》中,以及把样品检查的判定结果填写于《供应商首件确认报告》中,并反馈给质保部经理;
5.6 必要时,质保部从认可的零件中挑选1个封样,作好标识,保证帐/物/卡一致,全部首件
样品的资料保存在采购部;
5.7 质保部经理初步审核供应商提交的首件样品《样品检测报告》、《供应商首件确认报告》、材
质报告,然后传递至研发经理审核、批准,质保、采购经理签字确认。
若有异议时,供应商通过电话、邮件或到我公司现场解答,必要时,需重新递交首件样品和各类测试报告等。
如有其他要求,由采购工程师根据提出部门要求及时通知供应商;
5.8 若供应商提供的首件样品需要试装时,由研发经理确定抽查的检验及试验项目/试验方法/
检测手段等,制造部配合按产品图纸和相关技术要求进行试装和试验,研发工程师、工艺工程师和质量工程师一起到生产试装现场进行确认,并对首件样品进行综合判断,质量工程师出具《首件样品试装报告》,并反馈给研发经理审核,若试装现场发现不合格时,由采购工程师立即通知供应商确认,并重新提交首件;
5.9 研发经理、工艺工程师和质保部经理等人员根据《样品检测报告》、《供应商首件确认报告》、
《首件样品试装报告》和材质报告、性能试验报告及技术文件作出认可/不认可的结论,根据不合格的性质,判断是否可以有条件接受,并把认可结果填写于《供应商首件确认报告》中,必要时经顾客认可;
5.10 若供应商样品经过检验之后发现不合格,采购工程师立即通知供应商确认,并重新提交首
件;
5.11 若首件样品是有条件接受时,供应商需在下次发货前把所有的不合格项都整改完毕;
5.12 供应商在得到上海湘俊认可或有条件认可后方可发货,未经认可而发出的产品将被退货,
发生的所有成本都应由供应商支付;
5.13 (可选择)供应商在得到我公司首件样品认可后,依照我公司要求准备“PPAP检查清单”,
并要求供应商在批量生产前提交《PPAP检查清单》至采购工程师,由采购工程师传递《PPAP 检查清单》至质保部经理,由质保部经理审核,有异议时,供应商到我公司现场解答,必要时,需重新递交《PPAP检查清单》;
5.14供应商的产品设计更改或过程更改,需经过研发部确认,同意后方可进行生产,更改后的
首批产品也需按照此程序执行,经过质保部首批FAI检验合格后,供应商才能提供后续产品;
5.15 FAI流程图
6 FAI零件检验和试验项目
附:1:FAI项目表
7 相关文件
<1> 《文件控制程序》
<2> 《质量记录控制程序》
<3> 《采购控制程序》
<4> 《零部件试验规范》
8 质量记录
<1> 样品检测报告
<2> 供应商零件首件确认报告
<3> 首件样品试装报告
<4> 样品采购需求单
附件2:
供应商样品检测管理流程图。