奥氏体不锈钢焊接裂纹的射线及渗透检测方法
五种焊缝检测方法

五种焊缝检测方法焊接是工业生产中常见的连接方式之一,它通过熔化金属材料并使其冷却后形成的连接,广泛应用于航空航天、汽车制造、建筑等领域。
然而,焊接过程中难免会出现焊缝缺陷,如气孔、裂纹、夹渣等,这些缺陷会降低焊接件的强度和耐久性,因此需要进行焊缝检测。
本文将介绍五种常见的焊缝检测方法。
1. 目视检测目视检测是最简单、最常用的焊缝检测方法之一。
焊接工人通过肉眼观察焊缝表面,判断是否存在明显的缺陷。
这种方法主要适用于焊缝表面缺陷的检测,如气孔、夹渣等。
然而,目视检测只能检测到表面缺陷,对于深层缺陷难以发现,因此需要结合其他检测方法使用。
2. 渗透检测渗透检测是一种利用液体渗透性原理来检测焊缝缺陷的方法。
该方法通过将渗透剂涂覆在焊缝表面,待一定时间后再用显色剂处理,观察是否有渗透剂渗入焊缝缺陷并显色。
这种方法适用于检测各种缺陷,如裂纹、气孔等,且对于深层缺陷也能较好地检测。
然而,渗透检测需要较长的处理时间,且对工作环境要求较高。
3. 超声波检测超声波检测是一种利用超声波在材料中传播和反射的原理来检测焊缝缺陷的方法。
该方法通过超声波探头向焊缝传输超声波,利用超声波在不同材料中传播速度不同的特性,来判断焊缝是否有缺陷。
超声波检测能够检测到各种类型的缺陷,如裂纹、夹渣等,且对深层缺陷和材料内部缺陷也能进行检测。
然而,超声波检测的设备较为昂贵,操作技术要求较高。
4. 射线检测射线检测是一种利用射线在材料中透射和吸收的原理来检测焊缝缺陷的方法。
常用的射线检测方法有X射线检测和γ射线检测。
该方法通过将射线照射在焊缝上,通过观察射线透射和吸收情况来判断焊缝是否有缺陷。
射线检测能够检测到各种类型的缺陷,且对于深层缺陷和材料内部缺陷也能进行检测。
然而,射线检测设备昂贵且操作技术要求较高,同时也存在辐射安全问题。
5. 磁粉检测磁粉检测是一种利用磁粉在磁场中受到磁力作用的原理来检测焊缝缺陷的方法。
该方法通过在焊缝表面涂覆磁粉,待一定时间后观察磁粉排列情况来判断焊缝是否有缺陷。
焊缝X射线探伤施工工艺

焊缝X射线探伤施工工艺焊缝X射线探伤是一项重要的质量检测方法,为了保证检测的准确性和安全性,需要遵守以下一般要求:首先,射线检测人员需要接受辐射安全知识的培训,并持有放射工作人员证。
同时,他们的视力需要符合标准,未经矫正或经矫正的近(距)视力和远(距)视力应不低于5.0.从事评片的人员每年需要检查一次视力。
其次,观片灯的亮度应能满足评片的要求,并且其主要性能指标包括亮度的均匀性、外壳温度、噪声、绝缘程度等,需要符合标准要求。
底片评定范围内的黑度≤2.5时,观片灯的亮度不应低于9400cd/m2,当底片评定范围内的黑度2.5<D≤4.0时,观片灯的亮度不应低于cd/m2.第三,黑度计可测的最大黑度应不小于4.5,测量值的误差应不超过±0.05.黑度计至少每6个月校验一次,校准黑度计用的标准黑度片必须在有效期内,并通过计量部门的鉴定。
新购置的标准黑度片只要在有效期内也允许使用。
第四,X射线照相和Ir-192射线源时选用铅屏增感屏。
Ir-192射线源时铅屏增感屏的前屏和后屏的厚度均不能小于0.1mm。
前屏和后屏的厚度可以相同也可以不同。
第五,底片影像质量采用线型像质计测定。
线型像质计的型号和规格应符合规定,未包含的丝径、线号等内容,应符合有关规定。
像质计的材料可选择碳钢或奥氏体不锈钢。
第六,射线检测之前,对接焊接接头的表面应经外观检测并合格。
表面的不规则状态在底片上的影像不得掩盖或干扰缺陷影像,否则应对表面作适当修整。
为防止延迟裂纹倾向,射线检测应在焊接完成24小时后进行。
最后,现场进行X射线检测时,应按规定划定控制区和管理区、设置警告标志。
检测工作人员应佩戴个人剂量计,并携带剂量报警仪。
现场进行γ射线检测时,也需要按规定划定控制区和监督区、设置警告标志,并围绕控制区边界测定辐射水平。
检测工作人员同样需要佩戴个人剂量计,并携带剂量报警仪。
透照布置方面,可以选择中心法和双壁单影法。
透照时射线束中心一般应垂直指向透照区中心,需要时也可选用有利于发现缺陷的方向透照。
焊缝渗透检测的技术要点

焊缝渗透检测的技术要点摘要:我公司的渗透检测主要是焊缝表面的PT检测,在具体检测操作过程中,一些检测人员根据惯检测,忽视一些关键技术要点,易造成漏检,误检。
本文从方法、材料的选用、检测环境、安全防护、被检测面准备、检测过程、质量控制等环节提出了相应的技术措施和控制要点。
用于实际操作,提高了缺陷检出率。
关键词:PT检测方法检测环境检测过程控制1检测方法、材料1.1由于现场条件(无水源,有时电源不具备)的限制,施工现场焊缝的渗透检测一般使用溶剂去除型着色渗透检测(溶剂悬浮显像剂)(ⅡC-d)的检测方法,适用温度范围为10-50℃。
当温度低于10℃或高于50℃时,应用A型标准试块做灵敏度对比试验。
1.2当被检工件的材料为镍合金时,一定要购买并使用渗透检测剂蒸发后残渣中的硫元素含量的重量比小于等于1%的检测剂;当被检工件的材料为奥氏体不锈钢、钛及钛合金材料时,一定要购买并使用渗透检测剂蒸发后残渣中的氯、氟含量的重量比小于等于1%的检测剂。
当现有的检测剂合格证书上没有注明硫、氯、氟的含量时,应根据检测剂的牌号和批次委托有资质的实验室进行化学分析,经验证符合标准要求才可使用。
1.3对同一检测工件,渗透剂、清洗剂、显像剂原则上必须采用同一厂家提供的同族组的产品,不能混用不同类型的渗透检测剂。
2检测环境、安全防护2.1由于现场渗入渗出检测经常进行高空作业,以是要特别注意施工安全。
如果脚手架搭设的不好,不但会对检测人员的人身安全造成威胁,还会影响不安全部位的缺陷检出率,以是在渗入渗出检测前,检测人员一定要亲自对检测区域的脚手架搭设情况进行检查,对不合格的地方通知有关单位进行整改,这样不但能够消除安全隐患,还能够保证渗入渗出检测操纵和缺陷的观察评定质量。
2.2如果自然光线不足,可用冷光源灯补充照明,保证被检表面的照度不低于500Lx。
增加照度不可以使用碘弧灯,因为碘弧灯的温度太高,溶剂去除型渗透检测剂中含有大量的挥发性易燃物质,可能引起火灾爆炸。
奥氏体不锈钢焊缝缺陷的超声波定位方法

大连
16 1 1 13)
摘要 :奥 氏体 不锈 钢 焊 缝 接 头 一 般情 况 下 都 采 用 射线 探 伤 方 式 检 测 焊缝 内部 质 量 。 射线 探 伤 无 法对 焊
缝 中所发现的缺陷准确定位 ,故考虑利用现有的常规超声波检测方法来弥补射线探伤的不足 。 关键词 :粗晶组织 ;纵波斜探头 ;直探 头;声衰减
1  ̄ 6m/ n 3 1 mi。
4 结 语
上述 圆圈螺 母加 工方 法 ,是 在实 际工 作 中总 结 出来 的 。在 生产 实践 中得 到充 分 验证 ,切实 可 行 ,保 证 了质 量 ,提 高 了效率 ,适 用 于各种 圆圈
螺母 的加 工 。
收 稿 日期 :20 - 8 0 修 回 日期 :2 0 - 8 2 06 0-2 - 0 6- - 6 0
中 图分 类 号 :T 4 1 文 献 标 识 码 :B 文章 编 号 :17 — 35 (0 6 6 04 — 2 G4. 7 6 3 3 5 20 )0 — 0 2 0
目前的检测标准和技术条件 中对类奥 氏体不 12 探 头的选择 及模 拟试块 的制 作 . 锈钢粗 晶焊缝 的检测 ,一般只要求进行射线探伤 ()探 头 的选择 1 和渗透探伤。这两种探伤方法对焊缝中的 内部缺 奥 氏体不 锈 钢焊 缝 具 有粗 晶组 织 的特点 ,采 陷无 法准 确定 位 深 度 ,给 清 除缺 陷带来 不 便 ,特 用超声波检测时影响因素远 比普通碳钢或低合金 别对厚 壁 焊缝 更 是 如此 。为 了弥 补 射线 检 测 的不 钢 检 测 时多 。选 择 探头 时 应选 用 宽 频 带 、窄 脉 冲 足 ,我们做了试验 ,寻找 出利用超声波检测定位 探头。考虑到双晶探头能聚焦声束 ,发出的能量 缺陷 的方 法 ,并 在 实 践 中得 到 了充 分 的验 证 ,切 比较集 中、信噪比高 ,利于发现焊缝 中的近表 面 实可行 。 缺 陷 ,最 终选 择德 国的 MS B E 4双 晶纵波直 探 头和 VY0 S4 S 6 、V Y 5双 晶 纵波 斜 探 头 进行 试 验 。这 两 1 定 位 方 法 的试 验 过 程 种 探 头 的频 谱 及 波 形见 图 1 。选 择 双 晶纵 波 直 探 头 是 为 了发 现焊 缝 中的层 间未 熔 合 缺 陷 。在实 际 11 方 法的选 择 . 探 伤 中 ,采 用合 适 检测 灵 敏度 的情 况下 ,不受 此 由于横波本身的特性 。用 于奥 氏体不锈钢粗 限制 。 晶焊缝检测时,与纵波相 比衰减严重 , 信噪 比低 , f1模 拟试 堤的 制作 2 无法满足超声波探伤要求 。采用纵波的方式检测 取 两 块 材质 为 34的奥 氏体 不锈 钢板 f 7 0 厚 0 该类 焊 缝 ,效 果好 得 多 ,试验 充分 证 明了这 一点 。 mm . 然 后 采 用 丝 极 手 工 焊 打 底 ( 材 为 ) 焊 另外 .有关资料也推荐使用纵波的方式检测该类 WE TG 0 ), 丝 极 自 动 焊 填 充 ( 材 为 L I3 8 焊 粗 晶焊 缝 。因此 ,决 定采 用 超声 波 纵 波检 测 的方 WE A T ,G 01的方 法 焊接 。焊 接完成 后钻 孔 L U 0r 3 8 I 式 进行 下面 的试验 。 削。散热不好 ,易开焊 ,这种刀具不适合 A 3材 质方牙螺纹切削 ,质量不稳定 ,效率低。选择高 速 钢套 体 刀 具 f 1C4 ), 种 刀 具 硬 度 适 中 , W 8 rV 该 易刃磨 ,它红硬性差 ,但不打刀 ,经试用它适合 于A 3材 质方 牙螺 纹 中速 切 削 ,而且 质 量 好 。效 率高 。两 者 对 比之 后 ,后 者优 于 前 者 ,最终 选 择 后者 。 切 削 方 法选 择 :粗 加 工 采 用 直 进 法 切 削 螺 纹 。切 削 参数 :前 角 2一 。 。4 ,后角 6 。 o8,付后 角
渗透检验规程0316(PT)1

渗透检验规程(PT)编制:审核:批准:受控文件■2007年10月30日发布2007年10月30日实施1、适用范围本规程规定了金属材料或非金属材料制成的承压设备及其零部件的液体渗透检测方法和缺陷等级评定。
适用于非多孔性材料表面开口缺陷的检测。
2、引用标准JB4730-2005 《压力容器无损检测》GB/T5097-1985《黑光源的间接评定方法》GB11533-1989 《标准对数视力表》3、人员要求3.1 从事渗透检测的人员必须持有国家质检总局制发的并与其工作相适应的特种设备无损检测人员资格证书。
3.2 渗透检测人员裸视或矫正视力不得低于1.0,按GB11533规定的测试方法每年检查一次,并不得有色盲、色弱。
4、设施和器材4.1 采用荧光渗透检测方法时,检测现场应保持清洁,检测时可见光照度不大于20LX;黑光灯的紫外线波长应在0.32-0.40μm范围内,被检表面的紫外线强度应不低于1000μw/cm2。
4.2 渗透检测剂渗透检测剂包括渗透剂、乳化剂、清洗剂和显像剂。
4.2.1 渗透检测剂应配套使用,不同厂家、不同牌号、不同批号的渗透检测剂不得混用,本规程推荐选用国际型、标准型或适用型渗透检测剂。
4.2.2 用于检测镍基合金、奥氏体不锈钢或钛钢的渗透检测剂应有氟(F)、氯(CL)和硫(S)含量的控制,当无专门要求时,用于奥氏体不锈钢或钛钢的渗透检测剂,其氟(F)、氯(CL)总含量不得超过1%,用于高温下的镍基合金钢的渗透检测剂,其硫(S)含量不得超过1%;当有专门要求时,应按要求严格控制其含量。
4.2.3 荧光渗透剂的荧光效率不得低于75%,试验方法按GB/T5097标准附录A中的有关规定执行。
4.3 对比试块4.3.1 铝合金试块(A型对比试块)铝合金试块是由具有相同大小且具有细密相对称裂纹的两部分组成。
主要作用如下:a)在正常使用的情况下,检验渗透检测剂能否满足要求,以比较两种渗透检测剂性能的优劣;b)对用于非标准温度下的渗透检测方法作出鉴定。
四种无损检测方法对比

四种无损检测方法对比无损检测就是利用声、光、磁和电等特性,在不损害或不影响被检对象使用性能的前提下,检测被检对象中是否存在缺陷或不均匀性,给出缺陷的大小、位置、性质和数量等信息,进而判定被检对象所处技术状态(如合格与否、剩余寿命等)的所有技术手段的总称。
常用的无损检测方法:超声检测(UT)、磁粉检测(MT)、液体渗透检测(PT)及X射线检测(RT)。
磁粉检测首先来了解一下,磁粉检测的原理。
铁磁性材料和工件被磁化后,由于不连续性的存在,工件表面和近表面的磁力线发生局部畸变,而产生漏磁场,吸附施加在工件表面的磁粉,形成在合适光照下目视可见的磁痕,从而显示出不连续性的位置、形状和大小。
磁粉检测的适用性和局限性有:1、磁粉探伤适用于检测铁磁性材料表面和近表面尺寸很小、间隙极窄目视难以看出的不连续性。
2、磁粉检测可对多种情况下的零部件检测,还可多种型件进行检测。
3、可发现裂纹、夹杂、发纹、白点、折叠、冷隔和疏松等缺陷。
4、磁粉检测不能检测奥氏体不锈钢材料和用奥氏体不锈钢焊条焊接的焊缝,也不能检测铜铝镁钛等非磁性材料。
对于表面浅划伤、埋藏较深洞和与工件表面夹角小于20°的分层和折叠很难发现。
液体渗透检测液体渗透检测的基本原理,零件表面被施涂含有荧光染料或着色染料后,在一段时间的毛细管作用下,渗透液可以渗透进表面开口缺陷中;经去除零件表面多余的渗透液后,再在零件表面施涂显像剂,同样,在毛细管的作用下,显像剂将吸引缺陷中保留的渗透液,渗透液回渗到显像剂中,在一定的光源下(紫外线光或白光),缺陷处的渗透液痕迹被现实,(黄绿色荧光或鲜艳红色),从而探测出缺陷的形貌及分布状态。
渗透检测的优点有:1、可检测各种材料;2、具有较高的灵敏度;3、显示直观、操作方便、检测费用低。
而渗透检测的缺点有:1、不适于检查多孔性疏松材料制成的工件和表面粗糙的工件;2、渗透检测只能检出缺陷的表面分布,难以确定缺陷的实际深度,因而很难对缺陷做出定量评价。
高Ni-Cr奥氏体不锈钢焊接裂纹渗透检测方法

抚顺 市某 化工 厂 的 白油 加氢 反应 器 ,轧制 简体 材 质 为 X1 NC S3 — 2 iri6 6奥 氏 体 不 锈 钢 ,筒 节 规 格 为  ̄ 7 b 8mmx 8mix 0 m 3 3 n 5O 0 m。工 作 压力 1 a 2MP ,工 作 温度 4 0c 6 C。外 部保 温 材 料 厚 度 8 m ( 温砖 + 0m 保 包 敷材料 ) ;露天 安 置 。工 作 介质 : 内部装 有 ( i N 基
O 前 言
X1 N C s3 — 6奥 氏体 耐 热 不 锈 钢 是 从 原 西 德 2 iri6 1 引进 的 一种 高 N — r 相 奥 氏 体 不 锈 钢 ,广 泛 应 用 iC 单 于石 油 化 工 装 备 的 高 温 转 化 炉 和 乙 烯 裂 解 装 置 中 。
该 钢 种 热 导 率 小 ,线 膨 胀 系 数 大 。在 焊 接 冷 却 过 程 中 焊 缝 中 会 产 生 较 大 的结 晶 应 力 ;其 合 金 成 分 复
催 化 剂 颗粒 )8 ,加 工 原 料 为 2# 油 和 氢 气 。工 9% 0机
作 过程 :原 料进 入反 应器 后 ,在 高温 高压作 用下 ,反
层 ,盖 面 焊选 用 西 . m 焊 条 ,焊 1层 。焊 前 按 焊 40 m 条使 用说 明 书进行 烘干 。
应 生成 白油 ,其 白油 产 品等级 分别 为 :食 品级 、医药
焊接 坡 口形式 如 图 2所示 。采用 填丝 式手 工钨极
5 ・ 接 质量 控 制 与管 理 ・ O 焊
焊 接 技 术
第4 0卷第 4期 2 1 年 4月 01
氩 弧焊 单 面焊 双面 成形 工艺 封底 ;焊 条 电弧焊 多层 多
焊缝渗透检测的技术要点
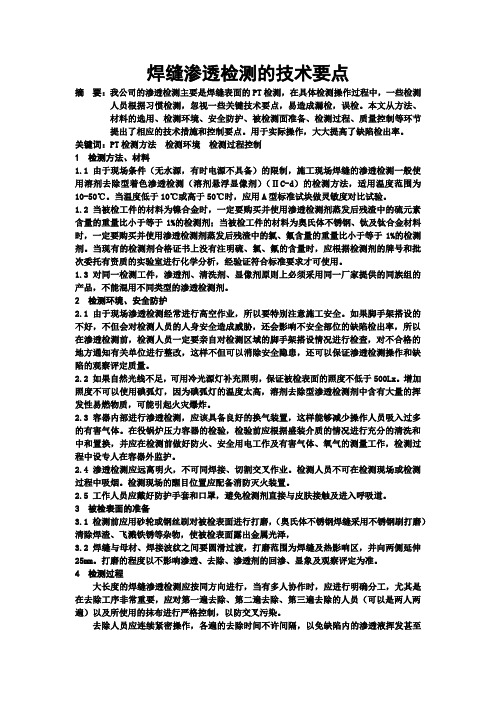
焊缝渗透检测的技术要点摘要:我公司的渗透检测主要是焊缝表面的PT检测,在具体检测操作过程中,一些检测人员根据习惯检测,忽视一些关键技术要点,易造成漏检,误检。
本文从方法、材料的选用、检测环境、安全防护、被检测面准备、检测过程、质量控制等环节提出了相应的技术措施和控制要点。
用于实际操作,大大提高了缺陷检出率。
关键词:PT检测方法检测环境检测过程控制1 检测方法、材料1.1 由于现场条件(无水源,有时电源不具备)的限制,施工现场焊缝的渗透检测一般使用溶剂去除型着色渗透检测(溶剂悬浮显像剂)(ⅡC-d)的检测方法,适用温度范围为10-50℃。
当温度低于10℃或高于50℃时,应用A型标准试块做灵敏度对比试验。
1.2 当被检工件的材料为镍合金时,一定要购买并使用渗透检测剂蒸发后残渣中的硫元素含量的重量比小于等于1%的检测剂;当被检工件的材料为奥氏体不锈钢、钛及钛合金材料时,一定要购买并使用渗透检测剂蒸发后残渣中的氯、氟含量的重量比小于等于1%的检测剂。
当现有的检测剂合格证书上没有注明硫、氯、氟的含量时,应根据检测剂的牌号和批次委托有资质的实验室进行化学分析,经验证符合标准要求才可使用。
1.3 对同一检测工件,渗透剂、清洗剂、显像剂原则上必须采用同一厂家提供的同族组的产品,不能混用不同类型的渗透检测剂。
2 检测环境、安全防护2.1 由于现场渗透检测经常进行高空作业,所以要特别注意施工安全。
如果脚手架搭设的不好,不但会对检测人员的人身安全造成威胁,还会影响不安全部位的缺陷检出率,所以在渗透检测前,检测人员一定要亲自对检测区域的脚手架搭设情况进行检查,对不合格的地方通知有关单位进行整改,这样不但可以消除安全隐患,还可以保证渗透检测操作和缺陷的观察评定质量。
2.2 如果自然光线不足,可用冷光源灯补充照明,保证被检表面的照度不低于500Lx。
增加照度不可以使用碘弧灯,因为碘弧灯的温度太高,溶剂去除型渗透检测剂中含有大量的挥发性易燃物质,可能引起火灾爆炸。
- 1、下载文档前请自行甄别文档内容的完整性,平台不提供额外的编辑、内容补充、找答案等附加服务。
- 2、"仅部分预览"的文档,不可在线预览部分如存在完整性等问题,可反馈申请退款(可完整预览的文档不适用该条件!)。
- 3、如文档侵犯您的权益,请联系客服反馈,我们会尽快为您处理(人工客服工作时间:9:00-18:30)。
b) 随着射线能量的增加, 射线的平均波长变 短, 线质变硬, 在物质中的衰减变小, 穿透能力增强。 对比度 $D 降低, 固有不清晰 U i 增大, 底片颗粒也 将增大, 其效果是射线照相灵敏度下降。选择的射线 能量过低, 穿透力不够, 到达胶片的透射线强度过 小, 造成底片黑度不足, 灰雾增大, 曝光时间过分延 长; 可以获得较高的对比度 $D , 不过较高的 $D 却 意味着较低的透照厚度宽容度L 。( 很小的透照厚度 差将产生很大的底片黑度差, 使得底片黑度值超出 允许范围: 或是厚度大的部位底片黑度太小, 或是厚 度小的部分黑度太大。)
由于射线检测对表面裂纹检测的灵敏度低, 因 此增加渗透表面检测是十分必要的, 通常采用常规 的检测方案 Òc- d 就行。但一定要用 B 型试块校 验操作方法和工艺系统灵敏度来保证检测灵敏度。 注意渗透探 伤剂 应控制 氯、氟元素 含量 不得 超过 1% 。 4. 3 检测结果
大口径管道焊缝, 发现有裂纹, 小口径管焊道抽 查未见裂纹。对有裂纹的大口径管道裂纹, 若热影 响区有裂纹, 不管裂纹大小, 一律割除; 若热影响区 无, 只存在焊缝内, 则打磨消除渗透检测确认, 直至 无裂纹为止, 该装置开车后运行至今, 奥氏体大口径 管道焊缝无异常。
第4期
宋仕伟: 奥氏体不锈钢焊接裂纹的射线及渗透检测方法
39
dm " = d , R= 1, 即 v D 0 = k ; 对于圆形缺陷: 当W ' = d 时, dm " = 0. 785d, R= P/ 4 = 0. 785, 即 v D0 = 0. 785k 其中: K = 0. 434Gd L/ ( 1 + n) 。
裂纹的表征参数: 长度 l , 走向 A, 裂纹离试件表 面的距离( 即深度 h) , 裂纹平面对工件表面法线的 倾角 H, 裂纹自身高度 d, 裂纹开口宽度 W ( 对自然裂 纹, W 是变化的) 。其中后三个 是射线检测的 关键 参数。
( 2) 裂纹检出率与像质计灵敏度关系: 一般像质 计灵敏度描述底片的质量, 灵敏度越高像质越好, 但 对于裂纹的检测而言这个规律不一定适用。原因如 下:
第 35 卷第 4 期 2011 年 8 月
无 损探 伤 NDT
Vol. 35No. 4 August . 2011
奥氏体不锈钢焊接 重庆华川油建装备制造( 集团) 有限公司, 重庆 400042)
摘 要: 阐述了在压力容器制造过程中, 针对奥氏体不锈钢产生的焊接裂纹, 运用射线检测和着色渗透 检测两种方法进行检测, 对其表示形式、产生部位、性质、大小、可能的产生原因进行分析, 得出奥氏体不锈钢 焊接裂纹在不同检测方法的表现特征。说明这两种检测方法的结合在奥氏体不锈钢焊接裂纹的检测工作中 是一种非常有效的措施。
关键词: 奥氏体不锈钢; 裂纹; 检测方法; 措施 中图分类号: T G115. 28 文献标志码: A 文章编号: 1671- 4423( 2011) 04- 37- 03
1 引言
我公司生产制造的脱硫装置, 使用 1Cr18Ni9T i 作为主体材料焊接, 在射线检测中发现一条缺陷, 怀 凝是裂纹, 采用较高灵敏度的射线检测, 发现多条裂 纹。考虑到裂纹对 H 2S 的敏感性及射线检测对表 面裂纹的检测灵敏度较差, 为防止裂纹漏检增加了 渗透检测, 结果发现了表面裂纹。笔者就一种奥氏 体不锈钢焊接裂纹, 在射线检测和着色渗透检测中 的表现形式、产生部位、性质、大小及可能的产生原 因、注意事项, 结合工程实践作简要介绍。
由于此设备是脱硫装置, 裂纹是危害性缺陷, 考 虑到裂纹对 H 2S 的敏感性, 故有必要采用较高灵敏 度的检测技术进行检测。 4. 2. 1 射线检测 4. 2. 1. 1 裂纹在射线检测方法中的分析
( 1) 裂纹的特点: ¹ 面积型缺陷, 开口宽度很小; 射线对于体积型缺陷具有很好的检出效果, 而裂纹 是面积型缺陷, 同时裂纹是焊接缺陷中最危险的缺 陷, 因此裂纹检测一直以来都是射线检测技术研究 的重点。 º 尺寸很小( 细微缺陷) 。
形状: 像质计截 面为圆形, 裂 纹的截面 为三角 形、菱形或窄槽型, 而这些形状对成像的对比度有影 响。
投影方向: 像质计为圆形因此与投影方向无关; 裂纹检测具有明显的方向性。
尺寸: 裂纹的开口尺寸非常小, 横向尺寸越小检 测率越低。
( 3) 裂纹检出率的影响因素 a) 透照角度 H的影响 射线方向与裂纹方向一致时, 底片上裂纹影像 的对比度最大, 检出率最高, 应尽量保证主射线束与 裂纹方向一致; 防止横 向裂纹 漏检, 要求 控制透 照厚度 比 K 值; 防止纵向裂纹漏检问题: ¹ 平靶周向 X 射线机对环焊缝周向曝光时 º 双壁单影倾斜透照和双壁双影倾斜透照时 b) 开口宽度和透照几何条件的影响 当裂纹开口宽度远小于焦点尺寸时, 几何因素 对对比度的影响增大; df 、L1 、L 2 共同决定 Wc 值的大小, 而 Wc 与 W 的 比值决定底片上裂纹影像是否有实影, 当 Wc > W , 此时底片上裂纹影像没有实影, 仅由半影组成, 其对 比度急剧下降, 边界模糊。 c) 截面形状的影响 到达胶片上任一点 ( P) 的射线是通过裂纹截 面部分所有路径射线的叠加。P 点的黑度不是由裂 纹高度 d 决定, 而是由到达 P 点的所有射线所穿过 的裂纹面积 $S 决定。 对于裂纹: 当 W ' = W 时, dm " = 0. 5d, R = 01 5, 即 vD 0 = 0. 5k ; 对于方形缺陷: 当 W '= W 时,
17. 37
Ni 9. 0~ 11. 0
9. 19 9. 0~ 11. 0
8. 05
Mn 0. 5~ 2. 5
1. 39 1. 0~ 2. 5
1. 17
MO < 0. 75
0. 46 < 0. 75
0. 85
第 35 卷
Cu < 0. 75
0. 84 < 0. 75
0. 75
但母材铜含量超标确实存在, 而同等铜含量的其他 焊缝未见裂纹。 3. 2. 2 结构因素
图 1 裂纹射线成像特征
着色渗透成像特征是: 椭圆形点状, 色泽鲜艳, 互不相连, 在焊缝或热影响区相同位置出现, 有时单 独出现有时群状出现, 如图 2 所示。
图 2 裂纹渗透成像特征
3 缺陷定性及产生原因
3. 1 缺陷定性 缺陷产生的部位: 一是在热影响区靠熔合线附
近, 二是在焊缝金属中靠熔合线 1m m ~ 2mm 的位 置出现; 形状如同硬磁材料的 磁滞回线一样, 较短 小, 从目前解剖分析的缺陷看, 基本上在 5mm 长度 以内, 有一定的长宽比, 缺陷两头有尖 角且走向相 反。从以上宏观 观察和 PM I 的 化学成分 分析( 表 1) , 有热裂纹的特征和产 生的条件, 故 定性为热裂 纹。 3. 2 缺陷产生原因 3. 2. 1 材料因素
焊接现场管理程序比 较严格, 又是独立 现场, P MI 验证也无差错, 所以排除焊接材料用错情况;
38
无损探伤
部位 母材 焊缝
表 1 A SM E 标准 5. 4 和 5. 9 的要求与 PM I 检测结果对比
标准要求与检测结果 标准 PMI
标准( 焊条) PMI
Cr 18. 0~ 21. 0
18. 53 19. 5~ 22. 0
4 处理方法
4. 1 检测方法 鉴于此奥氏体不锈钢焊接热裂纹在大口径管道
焊接 上 出 现 的 情 况, 大 口 径 的 同 类 焊 缝 全 部 作 100% 的射 线检 测 和 渗 透检 测; 小口 径 焊 口 作 各 20% 的射线检测和渗透检测抽查, 若发现裂纹, 加倍 射线检测、渗透检测。 4. 2 检测方案
4) 透照厚度对裂纹检出率的影响 随着工件厚度的增加, 各种对影像细节检出不 利的因素在增大: 在照相对比度方面: ¹ 工件厚度越大, 选用射 线的能量越高; º 散射比随工件厚度增加而增大。 在清晰度方面: ¹ 几何不清晰度与工件厚度成 正比, º 固有不清晰度随射线能量增大而增大。 在颗粒度方面: ¹ 射线能量增大后, 颗 粒度增 大。 透照几何条件方面: ¹ 工件越厚, 工件 - 胶片 距离 L 2 越大, 而源 - 工件距离 L 1 则受到限制不可 能很大, 这就使 wc 值增大, 而 wc 值增大后, 可检出 的裂纹的宽度 W 也增大。 5) 射线源及胶片种类的影响 X 射线底片的对比度、清晰度、颗粒度均优于 C 射线底片; 连续谱既含有穿透力较强的主能量部分, 又含 有大量有利于提高对比度的软线质部分, 所以照相 灵敏度比线状谱高; X 射线管的能量可以通过管电压调节, 可以按 试件的厚度选用合适的管电压, 从而获得高对比度 和高灵敏度。而 C射线的能量是由同位素的种类决 定的, 每一种放射性同位素放射出 C射线的波长是 特定的, 其能量不可调节; 改善 C射线成像质量的一个有效方法是使用梯 噪比等级更高的胶片。
因此, 在有透照厚度差的情况下, 选择射线能量 还必须考虑能够得到合适的透照厚度宽容度 L 。在 底片黑度不变的前提下, 提高射线能量可以缩短曝 光时间, 从而可以提高工作效率, 但其代价是灵敏度 降低。为保证透照质量, 标准对透照不同厚度允许 使用的最高管电压进行限制, 并要求有适当的曝光 量。
c) 不同类别胶片有不同的颗粒度, 颗粒度大, 感 光度高、梯度小、宽容度大; 胶片颗粒度大, 则底片颗 粒度大、分辨率低、信噪比低。常用检测技术级别为 AB 级, 选用 T 3 类胶片, 在此设备检测中应提高检 测灵敏度选用高一级 T 2 类胶片。 4. 2. 2 渗透检测
6) 不同透照角度对裂纹检出的影响 照射角度在 10b以 下时, 裂 纹的识别情况 变化 不大; 但 照射角度 超过 15b时, 随 着照射 角度的 增 大, 裂纹不能识别的情况就增多, 裂纹检出率显著降 低。 4. 2. 1. 2 射线检测工艺优化 a) 单壁透照的灵敏度明显高于双壁透照, 源在 内中心透照周向曝光, 透照厚度均一, 横向裂纹检出 角为 0, 底片黑度俱佳, 缺陷检出率高。