Mechanical properties of gangue-containing aluminosilicate based cementitious materials
3Reading material-Mechanical Properties of Metals(搞定)

Shaft Design-- Torque transmitting element
Common torque-transfer elements are: • Keys • Pins • Press fits • Tapered fits • Clamp collars
These devices are designed to fail if the torque exceeds acceptable operating limits, protecting more expensive components.
◆ The physical properties of metals 金属的物理性质/物理 性能 Electrical conductivity: 电导性, 导电率 The ability to transmit electricity Types of electrically conductive materials
◆ The physical properties of metals 金属的物理性质/物理 性能 examples of metal which withstand very high temperatures Titanium 钛 Nickel alloys 镍合金 Ceramics 陶瓷 Nickel alloys become stronger as the temperature rises (up to 800°C).
Shaft Design-- Torque transmitting element Example: Press fits are used for securing the bearings to the shafts. keys are used for securing the hubs to the shafts. clamps collar with screws is use to clamp the hub to the shaft.
铁筒磨磨机纤维器纤维器机械性性能分析说明书

Analysis of Mechanical Properties of IronRoughneck’s Spin-RollersYongbai Sha1(B),Quan Li1,and Xiaoying Zhao21School of Mechanical and Aerospace Engineering,Jilin University,Changchun,China*************.cn2Changchun V ocational Institute of Technology,Changchun,ChinaAbstract.The spinner mechanism of the iron roughneck is used to realize therapid screwing in or screwing out of the drill pipe thread.The spin-rollers are oneof the main components of the spinner mechanism,which directly contacts thedrill pipe and applies clamping force and torque to the drill pipe.Good mechan-ical performance is the premise to ensure its reliable work.In this paper,thestructure and working principle of the spinner mechanism are introduced.Thespinner mechanism adopts a new type of spin-rollers,which makes the structureof the mechanism more compact and better restricts the position of the drillingtool.In order to ensure the mechanical performance of the spinning roller,thestress analysis of the spinner mechanism and the drill pipe is conducted,and theforce between the roller and the drill pipe and the required oil cylinder thrust areobtained.According to the obtained force,thefinite element simulation analysisof the spin-rollers and drill pipe is carried out,and the distribution of stress anddeformation is obtained.The analysis results show that the designed spin-rollersmeets the requirements of mechanical properties.Keywords:Iron roughneck·Spin-roller·mechanical properties·finite elementanalysis1IntroductionWith the demand of modern drilling operation,the requirements for the automation of drilling operation are gradually increased[1,2].Iron roughneck is the wellhead operation equipment to realize the automatic makeup and shackle operation of drilling tools,and its application is more and more common[3,4].The spinner mechanism is one of the main working mechanisms of the iron roughneck,which is used to realize the rapid screwing in and screwing out of the drilling tool thread,and the spin-rollers are the direct force bearing part of the spinner mechanism[5].Good mechanical performance is the premise to ensure its reliable work.The mechanical performance of the spin-rollers is analysed in this paper.©The Author(s)2023L.Yan and J.Na(Eds.):ICFPMCE2022,AHE10,pp.393–404,2023.https:///10.2991/978-94-6463-022-0_33394Y.Sha et al.2Working Principle of the Spinner MechanismThe three-dimensional model of the spinner mechanism is shown in Fig.1,which is mainly composed of clamping oil cylinder,cross beam,wedge plate,return spring,tan-gent wheel,follow-up roller,clamping arm,driving roller,hydraulic motor,and upright column.The cylinder body of the clamping oil cylinder is hinged with the cross beam, and the piston rod is connected with the wedge plate.The tangent roller is installed on the pin shaft at the end of the clamping arm and can roll along the edge of the wedge plate.The return spring is used to limit the position of the clamping arm,keep the tangent roller at the end of the clamping arm in contact with the edge of the wedge plate,and the clamping arm can open automatically when the piston rod of the clamping oil cylinder retracts.The spin-rollers include two driving rollers and two groups of follow-up rollers installed on the roller frame.The driving roller is driven to rotate by the hydraulic motor, and the follow-up roller is used for limit and auxiliary support.This type of spin-rollers can not only meet the requirements of spin torque,but also better restrict the position of the drilling tools to achieve smooth spinning.Afloating mechanism is installed between the cross beam and the upright column.When subjected to external force,the cross beam canfloat back or forth along the guide rail on the upright column to adapt to the position of the drill pipe.When working,the piston rod of the clamping oil cylinder extends to push the wedge plate to drive the follow-up rollers to approach the drill pipe.At the same time,the two sides of the wedge plate push the tangent wheel installed at one end of the clamping arm to swing outward,and then driving the clamping arm to rotate around the middle pin shaft,to realize the inward rotation of the driving roller installed at the other end of the clamping arm.This form of spinner mechanism reduces the number of clamping oil cylinders and has a compact structure.However,when working,the driving rollersFig.1.Spinner mechanism.In thefigure:1-clamping oil cylinder,2-cross beam,3-wedge plate, 4-return spring,5-tangent wheel,6-follow-up roller,7-clamping arm,8-driving roller,9-hydraulic motor,10-upright column.Analysis of Mechanical Properties of Iron395 and the following rollers will not contact the drilling tool at the same time.When the roller in one direction contacts the drilling tool,the contact force will be generated. Due to the action of thefloating mechanism,the whole spinner mechanism outside the upright column will move back or forth under the action of force until all the spin-rollers completely clamp the drilling tool.When the spin-rollers clamp the drilling tool,the hydraulic motor drives the driving roller to rotate,to drive the drilling tool to rotate clockwise or anti-clockwise to complete the rapid screwing in or screwing out of the drilling tool thread.3Calculation of Clamping Force and Oil Cylinder ThrustThe maximum spin torque of the spinner mechanism is M max=2373Nm,which cor-responds to the drill tool with a diameter of311mm.During spinning,the resistance between the follow-up rollers and the drilling tool and the force generated by the return spring are small and ignored.When the holding force of the spinner mechanism is the maximum,the tangent rollers are at the limit position on both sides of the wedge plate near the follow-up rollers.The stress diagram of the mechanism when clamping the drill tool with a diameter of311mm is shown in Fig.2.The spinner mechanism is symmet-rical.In order to make the analysis diagram concise and clear,only the force on one side is drawn in the diagram,and the other side is symmetrical and not drawn.Taking the components composed of clamping arm,driving roller and tangent wheel as the research object,the torque equation of point K is as follows:F a d a=F b d b(1)Where,F a is the force exerted by the wedge plate on the tangent wheel;F b is the force exerted by the drill pipe on the driving roller,which is the reaction force of F b,Fig.2.Calculation diagram of clamping force396Y.Sha et al.and F b is the force exerted by the driving roller on the drill pipe;d a and d b are the force arms of the force F a and F b relative to the hinge point K of the clamping arm.The relationship between d a,d b and the lengths L a,L b of the clamping arm is as follows:d a=L a sinθ1(2)d b=L b cosθ2The spin torque M max applied by the driving roller on the drilling tool is as follow:M max=2μF b R(3) Where,μis the friction coefficient and R is the drilling tool radius.According to the materials of the drilling tools and the rollers,the friction coefficient between them is about0.2[6].The force balance equation of the drill tool in y direction is as follow:F by+F C1=0(4)Where:F by=F b sinθ3,F C1=F C cosθ4(5)Where,F by and F C1are the components of F b and F C in the y direction respectively, and F C is the force of the follow-up roller on the drill pipe.The stress equation in the y direction of the wedge plate is as follow:F−2F C1−2F ay=0(6) Where,F is the thrust of the oil cylinder,F C1 is the reaction force of F C1,F ay is the component force in y direction which exerted by the one-sided tangent wheel on the wedge plate,and F ay is the reaction force of F ay,and its size is:F ay=F ay=F a cos60◦(7)The values of relevant parameters are shown in Table1.Table1.Parameter valuesParameter ValueL a320mmL b332mmθ140.77°θ20.91°θ326.15°θ421.56°R155.5mmAnalysis of Mechanical Properties of Iron397 Simultaneous formula(1)–formula(7)and substituting the data in Table1,the fol-lowing results can be obtained:F a=60605N,F b=38151N,F c=18079N;F c1= 16814N,F ay=30302.5N,F by=16814N;and the required hydraulic cylinder thrust is F=94233N.4Simulation AnalysisIn the process of spinning,the spin-rollers clamp the drilling tool and generate friction, and the torque is transmitted through the contact friction[7,8].In this paper,ABAQUS software is used for simulation analysis.By establishing thefinite element simulation model of the spin-rollers and the drilling tool,and analysing and calculating,the stress and deformation caused by the contact between the spin-rollers and the drilling tool can be obtained,and the mechanical properties of the spin-rollers can be verified.4.1Establishment of Simulation ModelThis paper focuses on the force generated by the interaction between the spin-rollers and the drilling tool.In order to improve the calculation speed,the three-dimensional model used in the simulation does not need to import the complete iron roughneck’s spinner mechanism,but only the three-dimensional model of the contact section of the drilling tool,the driving rollers,and the follower-up rollers.The imported three-dimensional model is shown in Fig.3.In the Fig.3,the diameter of the drilling tool is311mm.In this case,the force required to hold the drilling tool is the largest,so the stress generated by the contact of each component is also the largest.4.2Mesh Division and Material Attribute AssignmentConsidering the accuracy of analysis and calculation and the rapidity of calculation, the mesh division is distinguished according to the stress of each component and the different contact area during spinning.The contacts between the drilling tool and the driving rollers and the follow-up rollers are only in a small range,so the mesh in the contact area between the drilling tool and the rollers is densified,and the mesh in otherFig.3.Simulation model398Y.Sha et al.Fig.4.Mesh division of drilling toolFig.5.Mesh division of driving rollerFig.6.Mesh division of follow-up rollerpositions is sparse.The focus area of the driving roller is the contact force between the lugs of the roller and the drilling tools.Therefore,the mesh is densified for the lugs while the mesh for the rest is not densified.The simplified structure of the follow-up roller is a circle and the mesh does not need to be differentiated.Figures4,5and6show the meshing of the drilling tool,the driving roller,and the follow-up roller respectively. The number of mesh units of the drilling tool is248112,and the unit type is a mixture of tetragonal pyramid and hexahedron.The mesh unit number of the driving roller is 104592,and the unit type is a mixture of tetragonal pyramid and hexahedron.The number of mesh units of the follow-up roller is3600and the unit type is hexahedron.The assembly effect of the drilling tool,the driving rollers and the follower-up rollers after meshing is shown in Fig.7.In the model,the material density of each component is7.9×103kg/m3,the elastic modulus is210GPa and the Poisson ratio is0.3.The section properties of each component are set as uniform distribution of a single material.Analysis of Mechanical Properties of Iron399Fig.7.Model import and assembly4.3Adding Constraints and Loads4.3.1Constraint SettingsThe simulation is divided into initial step and loading step1.The initial step is the contact-generated analysis step,so all components are constrained to the full degree of freedom in this step.Constraints are added to each component by referring to the assembly relationship in the three-dimensional model of the iron roughneck and the process of tightening.The driving roller releases x-axis of its reference coordinate system in step1, which is the degree of freedom of translation relative to the radial direction of the drill tool.In step1,the drilling tool releases the degree of freedom of translation along the x-axis and y-axis of its coordinate system.The follow-up roller limits its full degree of freedom in step1.4.3.2Load SettingsAccording to the calculation above,the force between the driving roller and the drilling tool is F b=38151N,pointing to the drilling tool axis along the axis of the driving roller,which is the x-axis direction of the reference coordinate system of the driving roller.This force is set as the driving roller load and added to the coupling reference point established.4.3.3Contact SettingsFor each component in the simulation,the attributes are Surface to Surface type when contacting,the friction coefficient is0.2,and the other attributes are default settings. There are six contact surfaces in the model,including two pairs of driving rollers-drilling tools and four pairs of follow-up rollers-drilling tools.In order to improve the astringency of calculation,the clearance tolerance of contact surface is set at0.1mm.4.4Simulation Results and AnalysisAfter solving the simulation model,the assembly stress distribution diagram(Fig.8a) and deformation distribution diagram(Fig.8b)as shown in Fig.8are obtained.It can be seen that large stress and deformation basically appear in the contact area.The maximum stress in the assembly is366MPa and the maximum deformation is0.3616mm,which are located at the contact position between the spin-rollers and the drilling tool.400Y.Sha et al.Fig.8.Stress and deformation of the assembly:(a)Stress distribution diagram;(b)Deformation distribution diagram.The stress distribution at the contact area of the drilling tool is shown in Fig.9. The leftfigure shows the perspective of the drilling tool in contact with the follower-up rollers,and the rightfigure shows the perspective of the drilling tool in contact with the driving roller.It can be seen that the relatively large stress is distributed in the area in contact with two driving rollers and the area in contact with four follow-up rollers. The maximum value appears at the position in contact with the driving rollers,which isAnalysis of Mechanical Properties of Iron401Fig.9.Drilling tool stress distributionFig.10.Stress distribution of driving roller281MPa.It is less than the allowable stress of the drill pipe material621MPa,so the strength of the drill pipe meets the requirements.The stress distribution of the driving rollers is shown in Fig.10.The maximum stress appears at the edge of the boss,which is366MPa,and less than the allowable stress of the material523MPa.Therefore,the strength of the driving roller meets the requirements.The stress distribution of the four follow-up rollers is shown in Fig.11.Their stress distribution forms are basically the same.The maximum stress value appears at the edge of the rollers,which is92.85MPa,less than the allowable stress of the material523MPa. Therefore,the strength of the driving roller meets the requirements.In conclusion,the designed driving rollers and follow-up rollers meet the strength requirements,and the force exerted by the rollers will not damage the drill pipe.Accord-ing to the situation that the maximum stress appears at the edge of the boss of the driving rollers and the edge of the follow-up rollers,it can be seen that there is stress concen-tration at this part.The stress condition can be further improved and the overall service402Y.Sha et al.Fig.11.Stress distribution of follow-up rollerFig.12.Working photo of spinner mechanismperformance can be improved by machining the transitionfillet at the corresponding position.Figure12is the working photo of the spinner mechanism.The application shows that the spin-rollers can reliably clamp the drill pipe,and the spin torque meets the design requirements,and the rollers and drill pipe are not damaged.5ConclusionsA new type of iron roughneck’s spinner mechanism is designed in this paper.The spin-rollers of the mechanism consist of two driving rollers and two groups of follow-up rollers installed on the roller frame.The clamping action of the driving rollers uses wedge plate force transmission mechanism.This form of spinner mechanism reduces the number of clamping cylinders and makes the overall structure of the spinner mechanism moreAnalysis of Mechanical Properties of Iron403compact while meeting the requirements of spin torque and restricting drilling tool position.The spinner mechanism uses the hydraulic motor to drive the driving rollers to rotate,and drives the drill pipe to rotate through the friction between the driving rollers and the drill pipe,to realize the screwing in and screwing out of the drill pipe thread.The sufficient clamping force of the rollers on the drill pipe is the prerequisite to realize this function.According to the requirements of the spin torque,the mechanical analysis is carried out,and the force of the driving rollers and follow-up rollers on the drilling tool and the required thrust of clamping oil cylinder are obtained.According to the calculation results,the simulation analysis is carried out by using thefinite element simulation software,and the stress distribution and deformation distribution of the driving rollers, the follower-up rollers and the drilling tool are obtained.The simulation results show that the designed spin-rollers mechanism meets the application requirements. Acknowledgments.This research was funded by the Ministry of Land and Resources of China, grant number SinoProbe-09-05;China Geological Survey,grant number12120113017600;and Program for JLU Science and Technology Innovative Research Team,grant number2017TD-13.Authors’Contributions.Conceptualization,Y.S.and Q.L.;methodology,Y.S.and Q.L.;soft-ware,Y.S.and Q.L.;validation,Y.S.,Q.L.and X.Z.;formal analysis,Y.S.and X.Z.;investigation, Y.S.and Q.L.;resources,Y.S.,Q.L.and X.Z.;data curation,Y.S.and Q.L.;writing—original draft preparation,Y.S.;writing—review and editing,Y.S.,Q.L.and X.Z.;visualization,Q.L.;supervi-sion,Y.S.;project administration,Y.S.;funding acquisition,Y.S.All authors have read and agreed to the published version of the manuscript.References1.Ramba,V.,Selvaraju,S.,Subbiah,S.,Palanisamy,M.,Srivastava,A.:Optimization of drillingparameters using improved play-back methodology.J.Pet.Sci.Eng.206,108991(2021).https:///10.1016/j.petrol.2021.1089912.Godhavn,J.M.,Pavlov,A.,Kaasa,G.O.,Rolland,N.L.:Drilling seeking automatic controlsolutions.In:Proceedings of the18th IFAC World Congress(IFAC2011),Milano,Italy,28 August–2September2011.https:///10.3182/20110828-6-IT-1002.005513.Sun,Y.H.,Zhang,F.Y.,Wang,Q.Y.,Gao,K.:Application of“Crust1”10k ultra-deep scientificdrilling rig in Songliao Basin Drilling Project(CCSD-SKII).J.Pet.Sci.Eng.145,222–229 (2016).https:///10.1016/j.petrol.2016.04.0034.Zhdaneev,O.V.,Frolov,K.N.,Petrakov,Y.A.:Predictive systems for the well drilling oper-ations.In:Kravets,A.G.,Bolshakov,A.A.,Shcherbakov,M.(eds.)Cyber-Physical Systems: Design and Application for Industry4.0.SSDC,vol.342,pp.347–368.Springer,Cham(2021).https:///10.1007/978-3-030-66081-9_285.Qin,D.T.,Xie,L.Y.:Modern Mechanical Design Handbook,(vol.1).Chemical Industry Press(2011)6.Liu,J.,Wen,Y.Q.:Analysis of the control strategy of the intelligent iron Roughneck’s make-upand break-out fusion with fuzzy adaptive control algorithm.J.Phys.Conf.Ser.1992,032099 (2021).https:///10.1088/1742-6596/1992/3/032099404Y.Sha et al.7.Shah,D.B.,Patel,K.M.,Trivedi,R.D.:Analyzing Hertzian contact stress developed in a doublerow spherical roller bearing and its effect on fatigue life.Ind.Lubr.Tribol.68,361–368(2016).https:///10.1108/ILT-06-2015-00828.Hu,Z.J.,Ma,Q.F.,Liu,J.L.:Load analysis and calculation of makeup and breakout device oncontinuous circulation system.China Pet.Mach.47,31–37(2019).https:///10.16082/j.cnki.issn.1001-4578.2019.12.005Open Access This chapter is licensed under the terms of the Creative Commons Attribution-NonCommercial 4.0International License(/licenses/by-nc/4.0/), which permits any noncommercial use,sharing,adaptation,distribution and reproduction in any medium or format,as long as you give appropriate credit to the original author(s)and the source, provide a link to the Creative Commons license and indicate if changes were made.The images or other third party material in this chapter are included in the chapter’s Creative Commons license,unless indicated otherwise in a credit line to the material.If material is not included in the chapter’s Creative Commons license and your intended use is not permitted by statutory regulation or exceeds the permitted use,you will need to obtain permission directly from the copyright holder.。
机械工程材料双语课件第二章
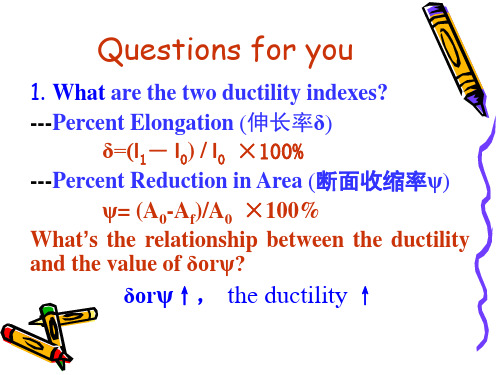
Fatigue strength
§2 Iron-carbon phase diagram
铁碳合金相图
Phase and Phase diagrams (相与相图)
•Phase:a region that differs in its state, microstructure, and /or composition from another region.
两组元在液态下无限溶解,固态下有限 溶解的二元合金相图。
The characteristics of eutectic system (共晶相图特点):
eutectic reaction(共晶反应)
Eutectic reaction equation
共晶反应式
Eutectic system
(共晶相图)
Toughness What’s the relationship between the
value of ak and toughness? ak ↑,toughness↑
Questions for you
4. When a metal is subjected to repetitive stresses , even when the stress is much lower than that which the metal can withstand under a static stress, the metal will fail to work. What do we call this phenomenon?
(共析相图)
The eutectoid reaction takes place completely in the solid state.
章跃机械制造工程专业英语---Lesson 1 Mechanical Properties of Metals

Lesson 1 Mechanical Properties of MetalsMechanical properties are the characteristic responses of a material to applied forces. These properties fall into five broad categories: strength, hardness, elasticity, ductility, and toughness.Strength is the ability of a metal to resist applied forces.Strength properties are commonly referred to as tensile strength, bending strength, compressive strength, torsional strength, shear strength and fatigue strength.Tensile strength is that property which resists forces acting to pull the metal apart. It is one of more important factors in the evaluation of a metal.Compressive strength is the ability of a material to resist being crushed. Compression is the opposite of tension with respect to the direction of the applied load. Most metals have high tensile strength and high compressive strength. However, brittle materials such as cast iron have high compressive strength but only a moderate tensile strength.Bending strength is that quality which resists forces from causing a member to bend or deflect in the direction in which the load is applied. Actually a bending stress is a combination of tensile and compressive stresses.Torsional strength is the ability of a metal to withstand forces that cause a member to twist.Shear strength refers to how well a member can withstand two equal forces acting in opposite directions.Fatigue strength is the property of a material to resist various kinds of rapidly alternating stresses. For example, a piston rod or an axle undergoes complete reversal of stresses from tension to compression. Bending a piece of wire back and forth until it breaks is another exampleof fatigue strength.Hardness is that property in steel which resists indentation or penetration. Hardness is usually expressed in terms of the area of an indentation made by a special ball under a standard load, or the depth of a special indenter under a specific load.Elasticity is the ability to spring back to original shape. Auto bumpers and all springs should have this quality.Ductility is the ability to undergo permanent changes of shape without rupturing. Modern, deep-formed auto bodies and fenders, and other stamped and formed products must have this property.Toughness is the ability to absorb mechanically applied energy. Strength and ductility determine a material’s toughness. Toughness is needed in railroad cars, automobile axles, hammers, rails, and similar products.New Words学习1.Mechanical 力学的,机械的2.Response 反应,响应,答复3.Broad 主要的,概括的4.Category 种类,类别……Notes1.Tensile strength is that property which resists forces actingto pull the metal apart.抗拉强度是金属抵抗外力把它拉断的能力。
激光冲击强化TC4_钛合金强化层弹塑性本构参数反演分析

第52卷第10期表面技术2023年10月SURFACE TECHNOLOGY·411·激光冲击强化TC4钛合金强化层弹塑性本构参数反演分析王淑娜,伏培林,李嘉伟,张旭,阚前华*(西南交通大学 力学与航空航天学院 应用力学与结构安全四川省重点试验室,成都 611756)摘要:目的获取TC4钛合金激光冲击强化层的弹塑性本构模型参数,结合纳米压痕试验和有限元模拟技术,进行激光冲击强化TC4钛合金的材料参数反演计算。
方法首先,在TC4钛合金试样侧面沿强化层深度方向进行纳米压痕测试,获得距表面不同距离处的载荷-压入深度曲线。
进而,基于幂律应变硬化模型,通过无量纲方程和有限元模拟反演得到激光冲击强化TC4钛合金梯度强化层的弹塑性参数。
最后,将反演获得的弹塑性本构模型材料参数用于有限元模拟,将模拟结果与试验结果进行对比,验证参数反演结果的合理性。
结果强化层表面的弹性模量和纳米硬度较母材分别提高了11%和30%,强化层内的应变硬化指数和屈服强度沿深度方向分别递增和递减。
模拟的载荷-压入深度曲线与试验曲线吻合较好,最大压入载荷、弹性模量和纳米硬度的模拟误差分别小于1%、7%和3%,证实了参数反演结果的合理性。
结论通过无量纲方程反演算法得到的强化层本构参数有较强的可信度。
激光冲击强化可有效提升TC4钛合金的表面力学性能,强化层的本构参数呈梯度分布,表面的抗塑性变形能力大幅提升。
关键词:TC4钛合金;激光冲击强化;纳米压痕;无量纲分析;反演分析;有限元模拟中图分类号:TG146.2+3 文献标识码:A 文章编号:1001-3660(2023)10-0411-11DOI:10.16490/ki.issn.1001-3660.2023.10.037Reverse Analysis of Elasto-plastic Constitutive Parameters of Strengthening Layer for Laser Shock Processing TC4 Titanium AlloysWANG Shu-na, FU Pei-lin, LI Jia-wei, ZHANG Xu, KAN Qian-hua*(Applied Mechanics and Structure Safety Key Laboratory of Sichuan Province, School of Mechanicsand Aerospace Engineering, Southwest Jiaotong University, Chengdu 611756, China)ABSTRACT: Laser shock processing (LSP) can form a strengthening layer with a gradient structure on the surface of parts, and thus improves the fatigue life. It is of great significance to obtain the elasto-plastic parameters of TC4 titanium alloy after LSP for the fatigue life prediction. However, there are few reports on the determination of elasto-plastic parameters of LSP TC4 titanium alloy. The reverse algorithm combining the nano-indentation experiments with finite element simulation is an effective method to obtain the constitutive parameters of the thin strengthening layer. Therefore, employing the nano-indentation experiments and finite element simulation, the reverse analysis of the LSP TC4 titanium alloy was conducted to determine the收稿日期:2022-09-02;修订日期:2023-03-10Received:2022-09-02;Revised:2023-03-10基金项目:国家自然科学基金(12072295,12192214,11872321)Fund:National Natural Science Foundation of China (12072295, 12192214, 11872321)引文格式:王淑娜, 伏培林, 李嘉伟, 等. 激光冲击强化TC4钛合金强化层弹塑性本构参数反演分析[J]. 表面技术, 2023, 52(10): 411-421. WANG Shu-na, FU Pei-lin, LI Jia-wei, et al. Reverse Analysis of Elasto-plastic Constitutive Parameters of Strengthening Layer for Laser Shock Processing TC4 Titanium Alloys[J]. Surface Technology, 2023, 52(10): 411-421.*通信作者(Corresponding author)·412·表面技术 2023年10月elasto-plastic parameters. First, the nano-indentation experiments of the LSP TC4 titanium alloy specimen were carried out based on the Nano indenter G200 nano-indentation experimental apparatus with the Berkovich diamond indenter, and the indentation depth of 1 000 nm was set by the displacement-controlled method. Then the nano-indentation experiments were carried out on a single side of specimen along the depth direction of the strengthening layer, and the corresponding load-displacement curves at different distances from the surface were obtained. Subsequently, the distributions of elastic modulus and nano-hardness along the depth direction of the strengthening layer were obtained after using the Oliver-Pharr method to determine the unloading stiffness and the reduced modulus from the unloading curves. Then, following the power-law strain hardening assumption, the yield stress and strain hardening index of the surface strengthening layer were determined by numerically solvingthe dimensionless equations of the representative stress, the ratio of plastic work to total work, and the ratio of residual depth to pressing depth, respectively. Therefore, the elasto-plastic parameters of the surface strengthening layer of LSP TC4 titanium alloy were obtained. Finally, the elasto-plastic parameters obtained by the reverse analysis were introduced toa two-dimensional axisymmetric nano-indentation finite element model. The effectiveness of the reverse analysis was verifiedby comparing the simulated results with the corresponding experimental results, which took into account the load-displacement curves as well as the variations of elastic modulus and nano-hardness with the distance from the surface. The obtained results showed that the elastic modulus, nano-hardness, yield stress and hardening index possessed a varying distribution along the thickness direction of the strengthening layer (about 300 μm). The surface elastic modulus, nano-hardness and yield stress of the strengthening layer reached 121.2 GPa, 5.0 GPa and 1 396.4 MPa, which were 11%, 30% and 55% higher than that of the substrate, respectively. However, the strain hardening index increased gradually along the depth direction, and the index at the substrate and the surface of the strengthening layer were 0.252 and 0.167, respectively. Additionally, the simulated load- displacement curves agreed with the experimental curves well, and the relative errors of the maximum load, elastic modulus and nano-hardness were less than 1%, 7% and 3%, respectively, demonstrating the effectiveness of the reverse analysis. The calculated results could be great helpful to the fatigue life prediction and the further optimization of LSP process parameters.KEY WORDS: TC4 titanium alloy; laser shock processing; nano-indentation; dimensionless analysis; reverse analysis; finite element simulationTC4钛合金(Ti-6Al-4V)因具有比强度高、耐热性高、耐蚀性好、密度小等特点而广泛应用在船舶、航空航天、车辆工程、生物医学等[1-6]领域。
滚筒法OG泥-钢球接触式干燥过程实验

第53卷第6期2022年6月中南大学学报(自然科学版)Journal of Central South University (Science and Technology)V ol.53No.6Jun.2022滚筒法OG 泥−钢球接触式干燥过程实验王兆宇1,温治1,2,苏福永1,2,邓升安1(1.北京科技大学能源与环境工程学院,北京,100083;2.北京科技大学冶金工业节能减排北京市重点实验室,北京,100083)摘要:针对目前OG 泥热干燥工艺成本高、效率低等问题,提出一种利用热钢球作研磨介质和热载体的滚筒式污泥干燥新技术,并通过试验考察该技术的干燥效果。
首先,设计并搭建滚筒干燥实验台;然后,确定OG 泥含水率与表观状态的关系;最后,通过OG 泥滚筒干燥过程试验,考察钢球直径、钢球初始温度和OG 泥处理量对干燥过程污泥的温度、含水率及最终干燥结果的影响。
研究结果表明:污泥干燥过程中会相继经历预热阶段、快速阶段和降速阶段,不同工况下的各干燥阶段的时间不同;最终干燥结果有3种,即完全干燥、少量结团和黏附筒壁;提高钢球初始温度或减少污泥处理量都可以提高污泥干燥效率和改善最终干燥效果;钢球直径越小,初始干燥速率越快;钢球直径越大,对污泥的破碎效果越好,可以干燥更多污泥;对于一定的钢球初始水当量(由钢球直径、个数和初始温度决定),存在一个最合适工况,该在工况下,干燥效率最高;污泥被完全干燥后,干基含水率低于4%,最终呈粉末状。
关键词:滚筒;OG 泥;热干燥;含水率中图分类号:X705文献标志码:A文章编号:1672-7207(2022)06-2007-10Experiment on contact drying process of OG sludge and steel ballin rotary drumWANG Zhaoyu 1,WEN Zhi 1,2,SU Fuyong 1,2,DENG Sheng ’an 1(1.School of Energy and Environmental Engineering,University of Science and Technology Beijing,Beijing 100083,China;2.Beijing Key Laboratory of Energy Saving and Emission Reduction for Metallurgical Industry,University ofScience and Technology Beijing,Beijing 100083,China)Abstract:Aiming at the high cost and low efficiency of the current OG sludge thermal drying process,a new drum-type sludge drying technology using hot steel balls as grinding media and heat carrier was proposed and the drying effect of this technology was investigated through experiments.Firstly,a drum drying experiment platform收稿日期:2021−10−21;修回日期:2021−12−25基金项目(Foundation item):国家重点研发计划项目(2016YFC0401201)(Project (2016YFC0401201)supported by the National KeyR&D Program of China)通信作者:苏福永,博士,副教授,从事余热利用及固体废弃物处理研究;E-mail:***************.cnDOI:10.11817/j.issn.1672-7207.2022.06.003引用格式:王兆宇,温治,苏福永,等.滚筒法OG 泥−钢球接触式干燥过程实验[J].中南大学学报(自然科学版),2022,53(6):2007−2016.Citation:WANG Zhaoyu,WEN Zhi,SU Fuyong,et al.Experiment on contact drying process of OG sludge and steel ball in rotary drum[J].Journal of Central South University(Science and Technology),2022,53(6):2007−2016.第53卷中南大学学报(自然科学版)was designed and built.Then,the relationship between the OG sludge moisture ratio and the apparent state was determined.Finally,the effects of diameter of steel ball,initial temperature of steel ball and treatment amount of OG sludge on the temperature,moisture ratio and final drying result of the sludge during the drying process were investigated through the OG sludge drum drying process experiment.The results show that the sludge drying process will go through the preheating stage,the rapid stage and the deceleration stage successively.The duration time of each drying stage is different in different working conditions.The final drying result includes3kinds, namely complete drying,a little agglomeration and adhesion drum wall.Increasing the initial temperature of the steel ball or reducing the amount of sludge treatment can increase the efficiency of sludge drying and improve the final drying effect.The smaller the diameter of the steel ball,the faster the initial drying rate.The larger the diameter of the steel ball,the better the sludge crushing effect,and more sludge can be dried.For a certain initial water equivalent of steel ball(determined by the diameter,number and initial temperature of the steel ball),there isa most suitable working condition,under which the drying efficiency is the highest.After the sludge is completely dried,its dry basis moisture ratio is less than4%and it is in powder form finally.Key words:rotary drum;OG sludge;thermal drying;moisture ratio随着钢铁产业不断发展,环保问题也日益严重。
mechanical properties中文名演变过程及定义
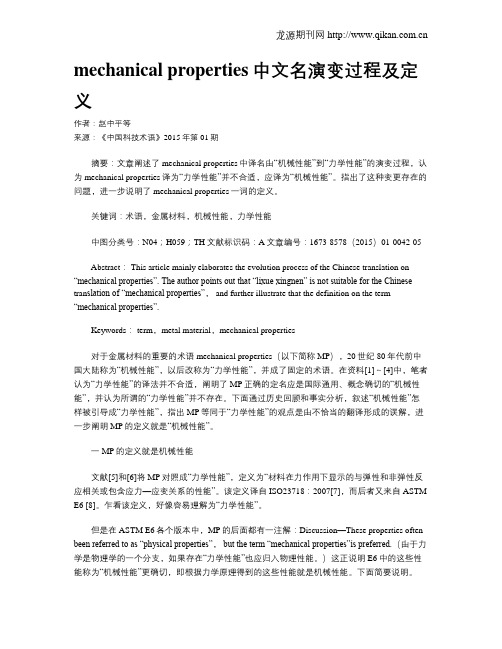
mechanical properties中文名演变过程及定义作者:赵中平等来源:《中国科技术语》2015年第01期摘要:文章阐述了mechanical properties中译名由“机械性能”到“力学性能”的演变过程,认为mechanical properties译为“力学性能”并不合适,应译为“机械性能”。
指出了这种变更存在的问题,进一步说明了mechanical properties一词的定义。
关键词:术语,金属材料,机械性能,力学性能中图分类号:N04;H059;TH文献标识码:A文章编号:1673-8578(2015)01-0042-05Abstract: This article mainly elaborates the evolution process of the Chinese translation on “mechanical properties”. The author points out that “lixue xingnen” is not suitable for the Chinese tran slation of “mechanical properties”, and further illustrate that the definition on the term “mechanical properties”.Keywords: term,metal material,mechanical properties对于金属材料的重要的术语mechanical properties(以下简称MP),20世纪80年代前中国大陆称为“机械性能”,以后改称为“力学性能”,并成了固定的术语。
在资料[1]~[4]中,笔者认为“力学性能”的译法并不合适,阐明了MP正确的定名应是国际通用、概念确切的“机械性能”,并认为所谓的“力学性能”并不存在。
下面通过历史回顾和事实分析,叙述“机械性能”怎样被引导成“力学性能”,指出MP等同于“力学性能”的观点是由不恰当的翻译形成的误解,进一步阐明MP的定义就是“机械性能”。
Mechanical Properties金属力学力学性能

Elastic Deformation: Nonlinear elastic behavior In some materials (many polymers, concrete...), elastic deformation is not linear, but it is still reversible.
σ = F / Ao
F is load applied perpendicular to specimen crosssection; A0 is cross-sectional area (perpendicular to the force) before application of the load. Engineering strain:
University of Tennessee, Dept. of Materials Science and Engineering 7
Introduction To Materials Science, Chapter 6, Mechanical Properties of Metals
Geometric Considerations of the Stress State
• The effect is normally small for metals but can be significant for polymers (“visco-elastic behavior”).
University of Tennessee, Dept. of Materials Science and Engineering
Stress-Strain Behavior: Elastic deformation
In tensile tests, if the deformation is elastic, the stressstrain relationship is called Hooke's law: