高压一级涡轮叶片
高压涡轮叶片定向凝固技术

RENE150定向凝固高温合金涡轮叶片摘要:政府和工业界4年合作项目,属于MATE先进涡轮发动机材料项目,经改善铸造和加工方法的镍基高温合金RENE150定向凝固转子零件已经实施用于发动机测试。
该部件制造用于CF6-50高压一级涡轮转子叶片,本项目的目标是:(1)表明在推力可调、先进的商用CF6-50发动机(提升燃油效率1.45%sfc)上提高运行温度的能力;(2)改善叶片铸造工艺,该工艺允许叶片在保证质量的前提下不超过原RENE80叶片制造成本的1.5倍。
本项目分成八个任务:TASK1:包括涡轮叶片的设计和分析;TASK2:包括合金制备和评估、机匣/核心机选择、初步铸造参数设计;TASK3:包括RENE150涡轮叶片外部涂层系统的适配和选择;TASK4:确定RENE150涡轮叶片铸造工艺,包括试制铸造过程和项目铸造成本分析。
TASK5:包括涡轮叶片成品制造,该叶片用于部件试验;TASK6:包括用于发动机试车的成品叶片制造;TASK7:包括地面发动机RENE150涡轮叶片成品测试;TASK8:地面发动机测试结果分析。
第二册文件是TASK5核心机试车结果和最后两个任务的结论。
RENE150高压涡轮叶片已成功完成投产型DS铸造,有涂层和没有涂层两种叶片机械和物理性能符合设计要求,叶片已完成加速持久试车,结论在第二册中分别给出。
1 概述本项目的任务是扩大先进的DS涡轮叶片合金Rene150在CF6-50发动机HPT一级涡轮叶片的应用范围。
本次扩展应用将许可RENE150提升运行温度(超过RENE80)以期实现商用发动机CF6-50提升1.45%燃油效率。
本项目将通过改进铸造工艺,使得该叶片制造成本能够在不超过Rene80叶片1.5倍的前提下,完成批量生产。
项目开始阶段使用的是1977年9月的RENE150性能数据(见表1),初步设计分析确定RENE150材料应用于CF6-50叶片上时抗温度、载荷和应力的性能。
某机高压涡轮叶片振动模态分析

某机高压涡轮叶片振动模态分析摘要:以某机高压涡轮工作叶片为研究对象,讨论其模态振动理论,采用UG建立叶片实体模型,利用有限元软件ANSYS Workbench对其进行模态分析,并与电动振动台测量结果进行对比,得到有限元分析结果具有一定的可靠性,为数值模拟振动测试数据提供一定的可信度依据,尤其对一些科研机种叶片的数值振动模态仿真分析提供了参考价值。
关键字:振动测试;模态分析;叶片;ANSYS Workbench引言叶片是航空发动机重要组成部分,工作时主要承受离心载荷、气动载荷、热载荷以及工况环境变化导致的交变载荷,工作中很容易发生故障,据统计振动故障占发动机总故障的15%,而叶片振动故障又占振动故障的75%。
而据粗略统计,我国现役航空发动机发生的重大事故中,涡轮叶片的断裂高达80%以上[1]。
因此叶片工作时的可靠性直接关系到整个发动机的运行安全性及使用寿命,为避免叶片振动故障的出现,在设计、制造及维修过程中对叶片进行振动模态分析,得到其固有频率、振型以及振动应力分析就显得尤其重要。
然而,高压涡轮叶片在发动机工作状态下直接对叶片进行频率及振动形态的观察及测试是比较困难甚至是不可能的。
在生产及制造中,一般只对叶片进行自由振动分析,测得其固有频率及振动形态。
单从使用角度来看,仅仅对叶片进行自由模态分析是不精确的,无法获得叶片全生命使用周期内的准确频率及振动形态。
本文首先在电动振动台ES-10-240上对高压涡轮叶片进行振动测试,得出其平均固有频率。
然后再UG中建立叶片实体模型,利用有限元软件ANSYS Workbench对其进行模态分析,对比有限元分析结果与试验结果。
在此基础上对高压涡轮叶片进行预应力模态分析,得到更准确的振动频率及振动形态,为高压涡轮叶片设计及加工提供一定的参考价值。
1 模态分析理论模态分析是结构动力学分析中最基础、也是最重的一种分析类型,其主要是用于计算结构的振动频率和振动形态,每一个模态都有特定的固有频率、阻尼比和模态阵型。
毕业设计论文:涡轮叶片断裂故障的分析与预防措施[管理资料]
![毕业设计论文:涡轮叶片断裂故障的分析与预防措施[管理资料]](https://img.taocdn.com/s3/m/b70f4ec7ee06eff9aff807bc.png)
Civil Aviation University of China 毕业设计(论文)专业:发动机动力工程学号:XXXXXXXX学生姓名:XXX所属学院:中国民航大学指导教师:XXX二〇一一年十月中国民航大学本科生毕业设计(论文)涡轮叶片断裂故障的分析与预防措施THE ANALYZING AND PREVENTIVE MEASURE OF TURBINE BLADE CRACKFAULT专业:发动机动力工程学生姓名:XXX学号:XXXXXXX学院:中国民航大学指导教师:XXXX2011年 10月创见性声明本人声明:所呈交的毕业论文是本人在指导教师的指导下进行的工作和取得的成果,论文中所引用的他人已经发表或撰写过的研究成果,均加以特别标注并在此表示致谢。
与我一同工作的同志对本论文所做的任何贡献也已在论文中作了明确的说明并表示谢意。
毕业论文作者签名:签字日期:年月日本科毕业设计(论文)版权使用授权书本毕业设计(论文)作者完全了解中国民航大学有关保留、使用毕业设计(论文)的规定。
特授权中国民航大学可以将毕业设计(论文)的全部或部分内容编入有关数据库进行检索,并采用影印、缩印或扫描等复制手段保存、汇编以供查阅和借阅。
同意学校向国家有关部门或机构送交毕业设计(论文)的复印件和磁盘。
(保密的毕业论文在解密后适用本授权说明)毕业论文作者签名:指导教师签名:签字日期:年月日签字日期:年月日涡轮叶片断裂故障的分析与预防措施XXX摘要:涡轮转子叶片是把高温燃气的能量转变为转子机械功的重要零件工作时,它不仅被经常变化着的高温燃气所包围并且还承受着高速旋转产生的巨大离心力气体和振动负荷等,此外还要经受高温燃气引起的腐蚀和侵蚀,因而涡轮转子叶片的工作条件是恶劣的,它是决定发动机寿命的主要零件之一,因此涡轮转子叶片的故障是不可忽视的。
涡轮叶片的断裂故障往往导致下面整个阶段的损失并且对涡轮机的可用性造成重大影响。
涡轮叶片断裂故障的研究分析对于涡轮机耐用性的有效管理是非常必要的。
飞机发动机原理与结构—涡轮
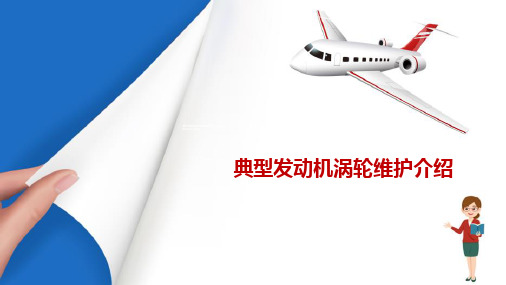
二、典型发动机涡轮的维护及注意事项高 压涡轮 进口Fra bibliotek 向叶片 的检查
1 级高压涡轮导向叶片,腐蚀,涂层丢失
1 级高压涡轮罩环,刮磨痕迹,剥落;2级高 压涡轮导向叶片腐蚀,涂层丢失和烧蚀痕迹
二、典型发动机涡轮的维护及注意事项
4. 高压涡轮转子叶片的检查 ✓ 涡轮转子叶片的叶尖一般设计有磨损指示槽,可以用来判断叶片和环罩的 磨损情况。 ✓高压涡轮转子叶片的检查区域包括:叶片的前缘,后缘,叶尖等 。
铝化物涂层);
• 对叶片采取冷却措施(高压和中压需要冷却,低压不需要)。 • 叶片的冷却措施:对流,冲击,气膜。
导向器叶片的安装
• 注意事项:叶片受热要自由膨胀,叶片要承力。 • 常见安装方式:挂钩式,螺栓固定。
2. 涡轮导向器
涡轮的导向器叶片
2. 涡轮导向器
V2500的高压涡轮 第一级导向叶片
二、典型发动机涡轮的维护及注意事项
高压涡轮转子叶片的检查
1级高压涡轮转子叶片,腐蚀,涂层丢失 2级高压涡轮转子叶片腐蚀,涂层丢失和烧蚀痕迹
涡轮的分类和原理
涡轮功用:把高温、高压燃气的热 能和压力能转变成旋转的机械功,从
而带动压气机及其它附件工作。在涡扇发动机中,涡轮 还带动风扇;在涡 桨发动机中,它带动螺旋桨;在涡轴发动机中,它输出轴功带动旋翼。
2
涡轮的工作特点
3 燃气在涡轮中的流动
4
涡轮的主要参数
1. 涡轮叶片比压气机叶片要厚。
• 工作气体的温度高,涡轮叶片受热严重, 金属材料的强度随着温度的升 高而降低, 为了保证叶片的强度, 所以涡轮叶片较厚。
• 涡轮叶片需要冷却, 所以有的涡轮 叶片是空心的, 以便通冷却空气。 2. 涡轮叶片比压气机叶片弯曲的程度要大。其原因是单级功率大,气动力矩
发动机涡轮叶片内部结构

发动机涡轮叶片内部结构一、引言发动机涡轮叶片是内燃机中的关键部件,它负责将高温高压气体流动能转化为机械能,推动涡轮旋转,从而带动压气机或涡轮机的运转。
本文将从叶片的结构和工作原理两个方面进行介绍。
二、叶片结构发动机涡轮叶片主要由叶片根部、叶片身和叶片尖部组成。
1. 叶片根部叶片根部是连接叶片和涡轮盘的部分。
它通常由金属材料制成,具有较高的强度和耐高温性能。
叶片根部通过特定的连接方式固定在涡轮盘上,以确保叶片能够承受来自流体的力和转动力矩。
2. 叶片身叶片身是叶片的主要工作部分,它负责将气体流动能转化为机械能。
叶片身通常采用空心的叶型结构,能够使气体在叶片内部流动,并通过叶片的弯曲形状将气体的动能转化为叶片的转动动能。
叶片身的材料通常选用高温合金,以保证其在高温高压环境下的强度和耐腐蚀性能。
3. 叶片尖部叶片尖部是叶片的末端部分,它通常与相邻叶片的尖部形成间隙,以减小气体泄漏和提高叶片的效率。
叶片尖部通常采用特殊的设计和制造工艺,以提高其耐磨损和耐高温性能。
三、叶片工作原理发动机涡轮叶片通过叶片的结构和气流的作用,实现动能转换和力的传递。
1. 动能转换当高温高压气体进入叶片内部时,气体将受到叶片弯曲形状的影响,产生压力差和动能转换。
气体在叶片内部流动时,受到叶片曲率的作用,气体的动能逐渐转化为叶片的转动动能。
叶片身的空心结构和叶片尖部的设计,能够有效地改变气体流动的方向和速度,从而提高叶片的转动效率。
2. 力的传递当气体流动通过叶片时,气体对叶片施加了一个压力力和一个剪切力。
压力力使叶片产生向外的径向力,而剪切力使叶片产生切向力。
这两个力共同作用下,使叶片产生转动力矩,推动涡轮旋转。
叶片根部的连接方式和材料的选择,能够使叶片能够承受来自气体的力和转动力矩,并将其传递给涡轮盘。
四、总结发动机涡轮叶片是发动机中至关重要的部件,其内部结构和工作原理决定了发动机的性能和效率。
叶片的结构包括叶片根部、叶片身和叶片尖部,每个部分都有特定的功能和要求。
涡轮机叶片的设计和优化研究

涡轮机叶片的设计和优化研究涡轮机是一种常见的动力机械,它主要通过燃烧燃料产生高温高压气体,然后将气体经过涡轮机叶片推动叶轮转动,最终驱动机械设备工作。
涡轮机的性能直接关系到机械设备的输出功率,而叶片作为涡轮机的核心部件之一,对涡轮机的性能有着至关重要的作用。
因此,涡轮机叶片的设计和优化研究一直是热门的研究领域。
本文将对涡轮机叶片的设计和优化研究进行详述。
一、涡轮机叶片的基本形式和分类涡轮机叶片是涡轮机的关键部件,它们负责接受高速气体流入口的高温高压气体,然后通过叶片的曲线形状和数量设计使气体的动能转换为轮毂的旋转能量,从而输出涡轮机的功率。
叶片的设计需要考虑到多种因素,如气体的流动性质、力学受力特点和材料的选择等。
根据叶片的形式和功能,涡轮机叶片可以分为多种类型。
例如,从叶片的用途来看,可分为导叶叶片、固定叶叶片和动叶叶片;从叶片的模式来看,可分为轴对称和非轴对称两种形式;从叶片的数量来看,可分为单排和双排叶片等几种形式。
二、涡轮机叶片的设计原理和方法涡轮机叶片的设计要从多方面考虑,包括叶片的数量、曲线形状、厚度、材质和冷却等方面。
在设计过程中,还需要结合涡轮机的工况参数进行优化,使涡轮机叶片可以达到最佳的性能。
首先,涡轮机叶片的数量和排列方式要根据涡轮机的流量和压降等参数进行设计。
一般情况下,叶子数量多的涡轮机流量大、压降低、效率高,但也会带来更高的制造成本。
而叶片数量少的涡轮机则可以减小制造成本,但是其流量和压降等参数也会受到影响。
因此,需要根据具体的情况选择合适的叶片数量和排列方式。
其次,涡轮机叶片的曲线形状是影响涡轮机性能的重要因素之一。
一般情况下,叶片的曲线形状需要根据气体流动性质和叶片材料等因素进行优化设计。
在叶片的设计过程中,需要采用流场数值模拟等技术进行仿真分析,以得到最优的叶片曲线。
另外,涡轮机叶片的厚度和材质也是需要考虑的因素之一。
涡轮机叶片的厚度一般采用变化的方式,以在不同受力部分得到最优的受力状态。
高压一级涡轮叶片

渗透检测技术
渗透检测的基本步骤: 渗透检测的基本步骤: 表面准备和预清洗 --渗透 --去除表面多余 --渗透 --去除表面多余 --干燥 --显像 渗透液 --干燥 --显像 –后清洗
高压一级涡轮叶片渗透检测的过程
1.预处理 1.预处理 水基清洗剂(浓度6%~10%) 水基清洗剂(浓度6%~10%)或用溶剂清 超声波清洗器清洗, 洗、超声波清洗器清洗,最终要保证零件的所有 表面应干净、干燥、无油污、油漆和其他漆层、 表面应干净、干燥、无油污、油漆和其他漆层、 无锈蚀、氧化皮等。 无锈蚀、氧化皮等。 2.渗透 2.渗透 给零件施加渗透液(牌号:RC-50, 给零件施加渗透液(牌号:RC-50,灵敏度级 别:高),零件、渗透液和环境温度15℃~38℃, ),零件、渗透液和环境温度15℃ 38℃ 零件 接触时间:30min(浸渍15min,滴落15min)。 接触时间:30min(浸渍15min,滴落15min)。
铸件的渗透检测
铸件是由熔融金属浇铸入铸模,经冷却而成的构 铸件是由熔融金属浇铸入铸模, 铸件中常发现的主要缺陷是气孔、夹杂物、 件。铸件中常发现的主要缺陷是气孔、夹杂物、 缩孔、疏松、冷隔、裂纹和白点等。 缩孔、疏松、冷隔、裂纹和白点等。铸件的表面 粗糙,形状复杂, 粗糙,形状复杂,给渗透检测的清理和去除工序 带来困难,为克服这些困难和保证足够的灵敏度, 带来困难,为克服这些困难和保证足够的灵敏度, 常采用水洗型荧光渗透检测工艺。但对重要铸件, 常采用水洗型荧光渗透检测工艺。但对重要铸件, 如涡轮叶片,它采用精密铸造法铸造, 如涡轮叶片,它采用精密铸造法铸造,其表面光 故也采用后乳化型渗透检测工艺。 洁,故也采用后乳化型渗透检测工艺。 高压一级涡轮叶片是精密铸件且技术要求高, 高压一级涡轮叶片是精密铸件且技术要求高,其 检测的灵敏度要求又非常高, 检测的灵敏度要求又非常高,所以选择荧光检测 后乳化——高 后乳化——高。
涡轮叶片材料

涡轮叶片材料
涡轮叶片是涡轮机的重要部件,其材料选择直接影响着涡轮机的性能和使用寿命。
涡轮叶片材料需要具备高温强度、抗氧化性能和疲劳强度等特点,以应对高温、高速和高压的工作环境。
目前,常见的涡轮叶片材料主要包括镍基合金、钛合金和陶瓷基复合材料等。
镍基合金是涡轮叶片常用的材料之一,具有良好的高温强度和抗氧化性能。
镍
基合金的主要成分为镍、铬、钨、钼等元素,通过合理的配比和热处理工艺,可以获得较高的强度和塑性,同时具有良好的抗氧化和耐蚀性能,适用于高温高压的工作环境。
然而,镍基合金的成本较高,加工难度大,制造成本较高,因此在一些特殊工况下使用。
钛合金是另一种常用的涡轮叶片材料,具有良好的高温强度和抗腐蚀性能。
钛
合金的主要成分为钛、铝、钒等元素,具有较高的比强度和比刚度,同时具有良好的耐热性和耐腐蚀性,适用于高温高速的工作环境。
钛合金的加工性能较好,制造成本相对较低,因此在航空发动机等领域得到广泛应用。
除了镍基合金和钛合金外,陶瓷基复合材料也是涡轮叶片的重要材料之一。
陶
瓷基复合材料具有极高的高温强度和抗氧化性能,同时具有较低的密度和良好的耐磨性能,适用于高温高速的工作环境。
然而,由于陶瓷基复合材料的加工难度大,成型工艺复杂,因此在实际应用中受到一定的限制。
综上所述,涡轮叶片材料的选择需要综合考虑工作环境、成本和加工性能等因素。
不同的材料具有不同的特点和适用范围,需要根据具体的工程要求进行合理的选择。
随着材料科学和加工技术的不断进步,相信涡轮叶片材料将会迎来更多的创新和突破,为涡轮机的性能提升和使用寿命延长提供更多的可能性。
- 1、下载文档前请自行甄别文档内容的完整性,平台不提供额外的编辑、内容补充、找答案等附加服务。
- 2、"仅部分预览"的文档,不可在线预览部分如存在完整性等问题,可反馈申请退款(可完整预览的文档不适用该条件!)。
- 3、如文档侵犯您的权益,请联系客服反馈,我们会尽快为您处理(人工客服工作时间:9:00-18:30)。
铸件的渗透检测
铸件是由熔融金属浇铸入铸模,经冷却而成的构 铸件是由熔融金属浇铸入铸模, 铸件中常发现的主要缺陷是气孔、夹杂物、 件。铸件中常发现的主要缺陷是气孔、夹杂物、 缩孔、疏松、冷隔、裂纹和白点等。 缩孔、疏松、冷隔、裂纹和白点等。铸件的表面 粗糙,形状复杂, 粗糙,形状复杂,给渗透检测的清理和去除工序 带来困难,为克服这些困难和保证足够的灵敏度, 带来困难,为克服这些困难和保证足够的灵敏度, 常采用水洗型荧光渗透检测工艺。但对重要铸件, 常采用水洗型荧光渗透检测工艺。但对重要铸件, 如涡轮叶片,它采用精密铸造法铸造, 如涡轮叶片,它采用精密铸造法铸造,其表面光 故也采用后乳化型渗透检测工艺。 洁,故也采用后乳化型渗透检测工艺。 高压一级涡轮叶片是精密铸件且技术要求高, 高压一级涡轮叶片是精密铸件且技术要求高,其 检测的灵敏度要求又非常高, 检测的灵敏度要求又非常高,所以选择荧光检级涡轮叶片及其缺陷
问题一: 问题一:使用亲水性后乳化渗透
检测乳化时间一般为多久? 检测乳化时间一般为多久?
将叶片浸入亲水性乳化剂中,乳化剂的 将叶片浸入亲水性乳化剂中, 浓度可按供货商推荐的浓度, 浓度可按供货商推荐的浓度,一般不超过 35%,在乳化过程中, 35%,在乳化过程中,应使叶片完全被乳 化剂浸湿和覆盖,乳化时间不超过2min。 化剂浸湿和覆盖,乳化时间不超过2min。
后乳化型渗透检测的优点及缺点
后乳化型渗透检测的优点: 后乳化型渗透检测的优点: a.具有较高的检测灵敏度 。 a.具有较高的检测灵敏度 b.能检出浅而宽的表面开口缺陷。 b.能检出浅而宽的表面开口缺陷 能检出浅而宽的表面开口缺陷。 c.渗透速度快。 c.渗透速度快 渗透速度快。 d.抗污染能力强,不易受水,酸和铬盐的污染。 d.抗污染能力强 不易受水,酸和铬盐的污染。 抗污染能力强, e.重复检验的重现性好。 e.重复检验的重现性好。 重复检验的重现性好 f.当温度变化时,不会产生分离,沉淀和凝胶等现 f.当温度变化时 不会产生分离, 当温度变化时, 象
渗透检测技术
渗透检测的基本步骤: 渗透检测的基本步骤: 表面准备和预清洗 --渗透 --去除表面多余 --渗透 --去除表面多余 --干燥 --显像 渗透液 --干燥 --显像 –后清洗
高压一级涡轮叶片渗透检测的过程
1.预处理 1.预处理 水基清洗剂(浓度6%~10%) 水基清洗剂(浓度6%~10%)或用溶剂清 超声波清洗器清洗, 洗、超声波清洗器清洗,最终要保证零件的所有 表面应干净、干燥、无油污、油漆和其他漆层、 表面应干净、干燥、无油污、油漆和其他漆层、 无锈蚀、氧化皮等。 无锈蚀、氧化皮等。 2.渗透 2.渗透 给零件施加渗透液(牌号:RC-50, 给零件施加渗透液(牌号:RC-50,灵敏度级 别:高),零件、渗透液和环境温度15℃~38℃, ),零件、渗透液和环境温度15℃ 38℃ 零件 接触时间:30min(浸渍15min,滴落15min)。 接触时间:30min(浸渍15min,滴落15min)。
6.干燥 6.干燥 烘箱温度最高为70℃ 干燥时间最长为20 min, 烘箱温度最高为70℃,干燥时间最长为20 min, 采用热空气循环烘箱干燥。 采用热空气循环烘箱干燥。 7.加显像粉 7.加显像粉 DUBLDUBL-CHEK D-90G,显像时 间最少10 min, D-90G, 间最少10 min, 最长4小时。 最长4小时。用干粉显像剂在喷粉柜喷粉或手工撒的 方法进行。 方法进行。 8.去除多余的显像粉 8.去除多余的显像粉 通过轻轻敲打或用压力小于0.034Mpa的压缩空 通过轻轻敲打或用压力小于0.034Mpa的压缩空 气吹去多余的显像粉。 气吹去多余的显像粉。 9.检验 9.检验 在暗室紫外灯下进行检验,检验员在检验零件之前, 在暗室紫外灯下进行检验,检验员在检验零件之前, 暗场适应时间不小于2 min, 暗场适应时间不小于2 min,不允许戴变色眼镜或墨 µW cm 镜,在零件表面上紫外线照幅不小于1200 在零件表面上紫外线照幅不小于1200 ,环境 ,环境 白光小于20lx。 白光小于20lx。
2
10.评定 10.评定 对没有显示或仅有不相关显示的零件应 予以验收, 予以验收,对有相关显示的零件按照其验 收标准进行评定做出验收、 收标准进行评定做出验收、返修或拒收的 结论。 结论。对有疑问的显示可直接用放大镜观 察,并对照零件的验收标准予以评定,必 并对照零件的验收标准予以评定, 要时可重新处理。 要时可重新处理。 该高压一级涡轮叶片发现一处缺陷, 该高压一级涡轮叶片发现一处缺陷,根 据缺陷的显示判断出其缺陷为裂纹。 据缺陷的显示判断出其缺陷为裂纹。
后乳化型渗透检测的缺点: 后乳化型渗透检测的缺点: a.操作周期长,检测费用大。 a.操作周期长 检测费用大。 操作周期长, b.必须严格控制乳化时间,才能保证灵敏度。 b.必须严格控制乳化时间 才能保证灵敏度。 必须严格控制乳化时间, c.要求工件表面有较好的光洁度。 c.要求工件表面有较好的光洁度 要求工件表面有较好的光洁度。 d.大型工件用后乳化渗透检验比较困难。 d.大型工件用后乳化渗透检验比较困难 大型工件用后乳化渗透检验比较困难。
渗透检测
渗透检测的定义,原理及作用 渗透检测的定义, 渗透检测是一种以毛细原理为基础用于检测 非疏孔性金属和非金属表面开口缺陷的无损检测 方法。 方法。 将溶有荧光染料或着色染料的渗透液施加于 试件表面,由于毛细现象的作用, 试件表面,由于毛细现象的作用,渗透液渗入到 各类开口于表面的细小缺陷中, 各类开口于表面的细小缺陷中,清除附着于试件 表面上多余的渗透液,经干燥后再施加显像剂, 表面上多余的渗透液,经干燥后再施加显像剂, 缺陷中的渗透液在毛细现象的作用下被重新回渗 到零件表面上,形成放大了的缺陷显示, 到零件表面上,形成放大了的缺陷显示,再黑光 灯下(荧光检验法)或白光灯下(着色检测法) 灯下(荧光检验法)或白光灯下(着色检测法) 观察, 观察,缺陷处可分别相应的发出黄绿色荧光或呈 现红色显示。 现红色显示。
3.清洗 3.清洗 水温10℃ 35℃ 水压≤170kpa, 水温10℃~35℃,水压≤170kpa,自动水洗 时间为2min。 时间为2min。 4.乳化 4.乳化 浸泡乳化剂DUBLER浓度3%~ 浸泡乳化剂DUBL-CHEK ER-83A 浓度3%~ 6%,停留时间小于2 min,在乳化过程中上下移 6%,停留时间小于2 min,在乳化过程中上下移 动零件以便使其充分乳化。 动零件以便使其充分乳化。 5.最终清洗 5.最终清洗 水温:10℃ 35℃ 压力小于170kpa, 水温:10℃~35℃,压力小于170kpa,自动 水洗时间为2min,必要时增加手工补洗, 水洗时间为2min,必要时增加手工补洗,在紫外 灯下冲洗, 灯下冲洗,枪的喷嘴与零件之间的距离至少为 300mm,多余的水分用压缩空气吹去, 300mm,多余的水分用压缩空气吹去,压力小 170kpa,清洗时间应尽量短 清洗时间应尽量短。 于170kpa,清洗时间应尽量短。
高压一级涡轮叶片组件 的检测
无损检测
无损检测就是研发和应用各种技术方法, 无损检测就是研发和应用各种技术方法, 以不损害被检对象未来用途和功能的方式, 以不损害被检对象未来用途和功能的方式, 为探测、定位、测量和评价缺陷, 为探测、定位、测量和评价缺陷,评估完 整性,性能和成分,测量几何特征, 整性,性能和成分,测量几何特征,而对 材料和零件所进行的检验,检查和测试。 材料和零件所进行的检验,检查和测试。
问题二:简述后乳化渗透检测的缺
点。
a.操作周期长,检测费用大。 a.操作周期长,检测费用大。 操作周期长 b.必须严格控制乳化时间,才能保证灵敏度。 b.必须严格控制乳化时间 才能保证灵敏度。 必须严格控制乳化时间, c.要求工件表面有较好的光洁度。 c.要求工件表面有较好的光洁度 要求工件表面有较好的光洁度。 d.大型工件用后乳化渗透检验比较困难。 d.大型工件用后乳化渗透检验比较困难 大型工件用后乳化渗透检验比较困难。