原料车间工艺流程
浸出车间工艺流程
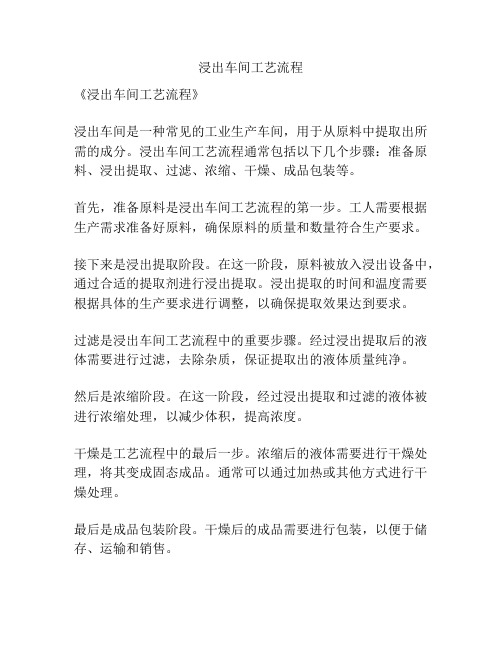
浸出车间工艺流程
《浸出车间工艺流程》
浸出车间是一种常见的工业生产车间,用于从原料中提取出所需的成分。
浸出车间工艺流程通常包括以下几个步骤:准备原料、浸出提取、过滤、浓缩、干燥、成品包装等。
首先,准备原料是浸出车间工艺流程的第一步。
工人需要根据生产需求准备好原料,确保原料的质量和数量符合生产要求。
接下来是浸出提取阶段。
在这一阶段,原料被放入浸出设备中,通过合适的提取剂进行浸出提取。
浸出提取的时间和温度需要根据具体的生产要求进行调整,以确保提取效果达到要求。
过滤是浸出车间工艺流程中的重要步骤。
经过浸出提取后的液体需要进行过滤,去除杂质,保证提取出的液体质量纯净。
然后是浓缩阶段。
在这一阶段,经过浸出提取和过滤的液体被进行浓缩处理,以减少体积,提高浓度。
干燥是工艺流程中的最后一步。
浓缩后的液体需要进行干燥处理,将其变成固态成品。
通常可以通过加热或其他方式进行干燥处理。
最后是成品包装阶段。
干燥后的成品需要进行包装,以便于储存、运输和销售。
总的来说,浸出车间工艺流程涉及多个步骤,每个步骤都需要严格控制和操作,以确保最终的产品符合质量标准。
同时,工艺流程的每个环节都需要根据实际情况进行调整,以提高生产效率和产品质量。
造粒车间工艺流程图
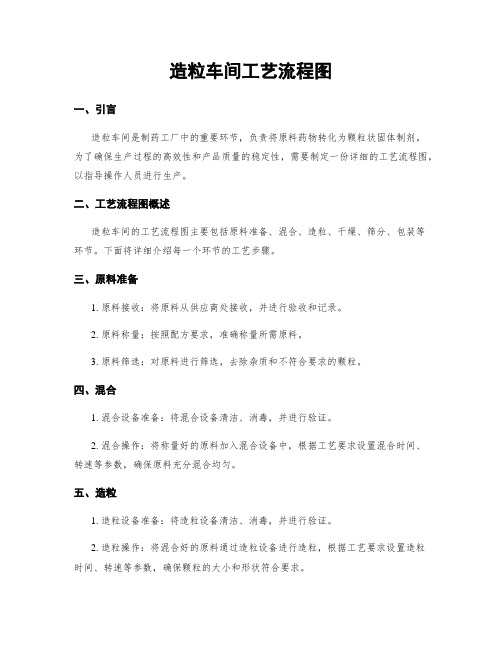
造粒车间工艺流程图一、引言造粒车间是制药工厂中的重要环节,负责将原料药物转化为颗粒状固体制剂。
为了确保生产过程的高效性和产品质量的稳定性,需要制定一份详细的工艺流程图,以指导操作人员进行生产。
二、工艺流程图概述造粒车间的工艺流程图主要包括原料准备、混合、造粒、干燥、筛分、包装等环节。
下面将详细介绍每一个环节的工艺步骤。
三、原料准备1. 原料接收:将原料从供应商处接收,并进行验收和记录。
2. 原料称量:按照配方要求,准确称量所需原料。
3. 原料筛选:对原料进行筛选,去除杂质和不符合要求的颗粒。
四、混合1. 混合设备准备:将混合设备清洁、消毒,并进行验证。
2. 混合操作:将称量好的原料加入混合设备中,根据工艺要求设置混合时间、转速等参数,确保原料充分混合均匀。
五、造粒1. 造粒设备准备:将造粒设备清洁、消毒,并进行验证。
2. 造粒操作:将混合好的原料通过造粒设备进行造粒,根据工艺要求设置造粒时间、转速等参数,确保颗粒的大小和形状符合要求。
1. 干燥设备准备:将干燥设备清洁、消毒,并进行验证。
2. 干燥操作:将造粒后的颗粒放入干燥设备中,根据工艺要求设置干燥时间、温度等参数,确保颗粒的含水量符合要求。
七、筛分1. 筛分设备准备:将筛分设备清洁、消毒,并进行验证。
2. 筛分操作:将干燥后的颗粒通过筛分设备进行筛分,去除过大或者过小的颗粒,确保产品的粒径分布符合要求。
八、包装1. 包装材料准备:准备符合要求的包装材料,并进行清洁、消毒。
2. 包装操作:将筛分后的颗粒进行包装,根据工艺要求设置包装方式、包装数量等参数,确保产品的包装符合要求。
九、清洁和消毒1. 设备清洁:在每次操作结束后,对使用的设备进行清洁,确保下次使用时无污染。
2. 车间清洁:定期对整个车间进行清洁和消毒,确保生产环境的卫生和无菌。
十、记录和文件管理1. 生产记录:对每一个操作环节进行记录,包括原料批号、操作人员、操作时间等信息。
2. 文件管理:对工艺流程图、设备验证报告、清洁消毒记录等进行管理,确保文件的完整性和可追溯性。
炼铁厂原料车间工艺流程

炼铁厂原料车间工艺流程
炼铁厂原料车间工艺流程一般包括以下主要步骤:
1. 配料:根据炼铁生产的需要,将铁矿石、焦炭、石灰石等原料按照一定比例进行配比。
2. 破碎:将铁矿石进行粗碎、细碎,使其颗粒度适合炼铁反应。
3. 混匀:将破碎后的铁矿石均匀混合,以保证每个配料中含有相应的金属元素。
4. 算法掺铁:在配料中加入一定比例的回收料(如废铁、废钢等),提高铁的含量。
5. 焙烧:将混合均匀的原料进行焙烧,以去除其中的水分和挥发性成分。
6. 制球:将焙烧后的原料进行制球,以提高炼铁反应时的流动性。
7. 预热:将制球后的原料通过预热炉预热至一定温度,以减少高温环境对反应容器的腐蚀。
8. 炼铁反应:将预热后的原料送入高炉,与高炉内的冶炼渣反应,产生液态铁。
9. 出铁:将高炉中的液态铁通过铁口流出,形成铁水。
10. 出渣:将高炉中的冶炼渣通过渣口流出,形成渣水。
11. 煮铁水:将铁水进行加热,使其温度达到需要的热处理温度。
12. 铁水净化:通过去除铁水中的杂质,例如硫、磷等,提高铁水的纯度。
13. 铁水浇注:将净化后的铁水倒入铸造模具中,进行冷却凝固,形成铸铁产品。
14. 冷却、清理:待铸铁产品冷却后,将其从模具中取出,进行清理和后续处理。
这只是炼铁厂原料车间工艺流程的基本步骤,实际生产中可能还会有其他环节和工艺。
具体的工艺流程还需根据具体的炼铁厂和生产需求进行调整和细化。
生产车间工作流程
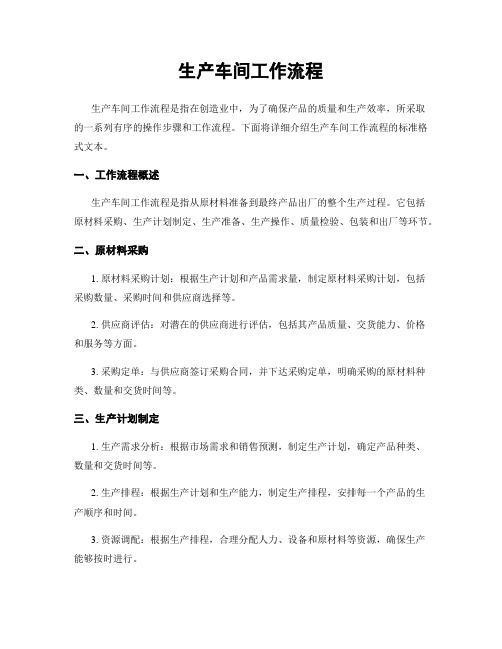
生产车间工作流程生产车间工作流程是指在创造业中,为了确保产品的质量和生产效率,所采取的一系列有序的操作步骤和工作流程。
下面将详细介绍生产车间工作流程的标准格式文本。
一、工作流程概述生产车间工作流程是指从原材料准备到最终产品出厂的整个生产过程。
它包括原材料采购、生产计划制定、生产准备、生产操作、质量检验、包装和出厂等环节。
二、原材料采购1. 原材料采购计划:根据生产计划和产品需求量,制定原材料采购计划,包括采购数量、采购时间和供应商选择等。
2. 供应商评估:对潜在的供应商进行评估,包括其产品质量、交货能力、价格和服务等方面。
3. 采购定单:与供应商签订采购合同,并下达采购定单,明确采购的原材料种类、数量和交货时间等。
三、生产计划制定1. 生产需求分析:根据市场需求和销售预测,制定生产计划,确定产品种类、数量和交货时间等。
2. 生产排程:根据生产计划和生产能力,制定生产排程,安排每一个产品的生产顺序和时间。
3. 资源调配:根据生产排程,合理分配人力、设备和原材料等资源,确保生产能够按时进行。
四、生产准备1. 设备检查:对生产所需的设备进行检查和维护,确保其正常运行。
2. 原材料准备:根据生产计划,准备好所需的原材料,并进行质量检验。
3. 工艺准备:根据产品的工艺要求,准备好生产所需的工艺文件、工装和工具等。
4. 人员培训:对生产操作人员进行培训,确保其熟悉产品工艺和操作流程。
五、生产操作1. 生产指导:根据工艺要求,对生产操作人员进行指导,确保其按照正确的工艺流程进行操作。
2. 生产过程监控:对生产过程进行监控,包括设备运行状态、原材料消耗和产品质量等方面。
3. 异常处理:及时发现和处理生产过程中的异常情况,如设备故障、原材料不合格等。
4. 生产记录:记录生产过程中的关键参数和数据,以备后续分析和追溯。
六、质量检验1. 抽样检验:按照质量管理要求,抽取样品进行质量检验,包括外观检查、尺寸测量和性能测试等。
车间生产工艺流程
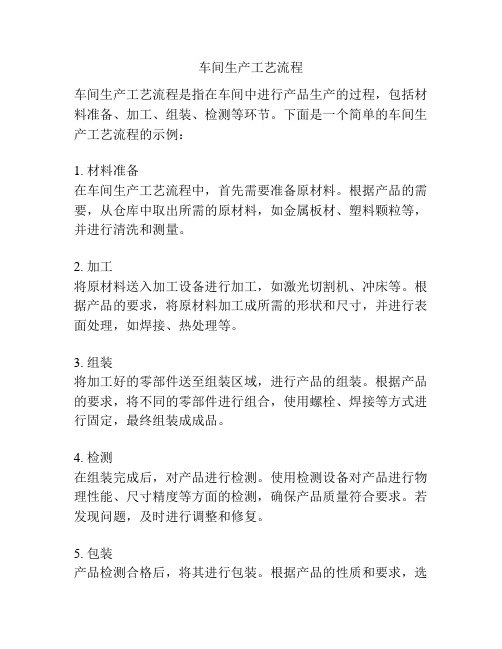
车间生产工艺流程车间生产工艺流程是指在车间中进行产品生产的过程,包括材料准备、加工、组装、检测等环节。
下面是一个简单的车间生产工艺流程的示例:1. 材料准备在车间生产工艺流程中,首先需要准备原材料。
根据产品的需要,从仓库中取出所需的原材料,如金属板材、塑料颗粒等,并进行清洗和测量。
2. 加工将原材料送入加工设备进行加工,如激光切割机、冲床等。
根据产品的要求,将原材料加工成所需的形状和尺寸,并进行表面处理,如焊接、热处理等。
3. 组装将加工好的零部件送至组装区域,进行产品的组装。
根据产品的要求,将不同的零部件进行组合,使用螺栓、焊接等方式进行固定,最终组装成成品。
4. 检测在组装完成后,对产品进行检测。
使用检测设备对产品进行物理性能、尺寸精度等方面的检测,确保产品质量符合要求。
若发现问题,及时进行调整和修复。
5. 包装产品检测合格后,将其进行包装。
根据产品的性质和要求,选择适当的包装材料和方式进行包装,如纸箱、泡沫等。
确保产品在运输和储存过程中不受损。
6. 存放包装完成后,将产品放置在指定的区域进行存放。
根据产品特性和市场需求,将产品分类存放,方便后续的出货和发货。
7. 出货当有订单或需求时,根据客户要求进行发货。
将存放好的产品装车,送至订单指定的地点进行交付。
总结:车间生产工艺流程是一个复杂的过程,需要进行材料准备、加工、组装、检测、包装、存放和出货等环节。
每个环节都需要严格控制和管理,确保产品质量符合要求。
同时,还需要考虑成本控制、时间管理等因素,以提高生产效率和产品竞争力。
炼胶车间工艺流程图

炼胶车间工艺流程图引言概述:炼胶车间是橡胶制品生产过程中的重要环节,工艺流程图对于指导生产操作、提高生产效率具有重要意义。
本文将详细介绍炼胶车间的工艺流程图,包括原料准备、混炼、成型和硫化四个部份。
一、原料准备1.1 原料配比:根据产品要求,将橡胶、填充剂、增塑剂、硫化剂等原料按照一定比例进行配比,确保产品的质量和性能。
1.2 原料检测:对原料进行外观检查、密度测试、粒度分析等,确保原料的质量符合要求。
1.3 原料存储:将配好的原料存放在指定的仓库中,按照先进先出的原则管理,确保原料的新鲜度和稳定性。
二、混炼2.1 加料:将配好的原料按照工艺要求挨次加入混炼机中,确保各种原料充分混合。
2.2 混炼过程:混炼机对原料进行剪切、翻转、加热等处理,使原料份子间发生交联,形成均匀的橡胶混炼胶料。
2.3 混炼检测:对混炼胶料进行外观检查、黏度测试、硫化特性分析等,确保混炼胶料的质量和性能。
三、成型3.1 橡胶炼胶料处理:将混炼好的胶料送入成型机中,通过压力和温度的作用,使胶料在模具中形成所需的形状。
3.2 成型过程:成型机对胶料进行挤出、压缩、注塑等处理,使其变为具有一定形状和尺寸的橡胶制品。
3.3 成型检测:对成型后的橡胶制品进行外观检查、尺寸测量、物理性能测试等,确保成型质量符合要求。
四、硫化4.1 硫化条件设定:根据产品要求,确定硫化温度、硫化时间等硫化条件。
4.2 硫化过程:将成型好的橡胶制品放入硫化炉中,通过加热和硫化剂的作用,使橡胶份子间发生交联,提高制品的硬度、强度和耐磨性。
4.3 硫化检测:对硫化后的橡胶制品进行外观检查、硬度测试、拉伸试验等,确保硫化质量符合要求。
结论:炼胶车间工艺流程图是橡胶制品生产过程中的重要指导工具,它对于确保产品质量、提高生产效率具有重要意义。
通过原料准备、混炼、成型和硫化四个部份的详细阐述,我们可以更好地理解炼胶车间的工艺流程,并在实际生产中加以应用。
惟独合理遵循工艺流程,才干生产出优质的橡胶制品。
陶瓷厂原料车间工作流程
陶瓷厂原料车间工作流程1. 原料采购
- 根据生产计划确定所需原料种类和数量
- 对供应商进行评估和选择
- 下达采购订单并跟踪物流
2. 原料检验
- 对收货的原料进行取样检测
- 检查原料质量是否符合标准
- 对不合格原料进行退货或隔离处理
3. 原料储存
- 根据原料特性选择合适的储存环境
- 建立原料入库和出库管理制度
- 定期盘点库存,确保供应充足
4. 原料预处理
- 对部分原料进行破碎、磨粉等预处理
- 控制粒度大小和均匀性
- 确保预处理后的原料符合使用要求
5. 原料配料
- 根据产品配方,精确称量各种原料
- 将原料均匀混合,形成可塑性好的陶浆
- 对陶浆进行老化和调节
6. 原料输送
- 将配好的陶浆输送到成型车间
- 保证输送管路的畅通和密闭性
- 控制输送压力和流量
7. 质量检测
- 对整个工序的关键环节进行质量监控
- 采集数据并进行统计分析
- 发现问题及时调整并追溯原因
8. 设备维护
- 制定设备保养计划,定期检修
- 监控设备运行状态,预防故障发生
- 对故障设备及时维修,确保生产连续
以上是陶瓷厂原料车间的主要工作流程,在实际操作中还需结合具体情况进行优化和改进,以提高效率、降低成本、确保产品质量。
密炼车间工艺流程图
密炼车间工艺流程图密炼车间是橡胶制品生产过程中的重要环节,它涉及到橡胶原料的混炼和加工,以及最终产品的品质控制。
为了确保生产过程的顺利进行和产品质量的稳定性,密炼车间需要制定一套科学合理的工艺流程,并将其以流程图的形式展示出来。
本文将详细介绍密炼车间的工艺流程图。
一、橡胶原料准备1. 原料配送:原料从仓库中配送至密炼车间,配送方式可以是手工搬运或者使用搬运设备,如叉车等。
2. 原料称量:将配送来的原料进行称量,确保每一批原料的比例准确。
二、橡胶混炼1. 混炼设备准备:确保混炼机、冷却器、送料器等设备的正常运行和清洁。
2. 原料投料:按照配方要求,将称量好的橡胶原料投入混炼机中。
3. 加入助剂:根据产品要求,将各种助剂逐一加入混炼机中,如硫化剂、活性剂、防老剂等。
4. 混炼过程:启动混炼机,调节温度、时间和转速等参数,使原料和助剂充分混合,形成均匀的混炼胶料。
5. 冷却和切料:将混炼好的胶料通过冷却器冷却后,使用切胶机将其切成适当大小的块状,以便后续加工使用。
三、橡胶加工1. 加工设备准备:确保加工设备的正常运行和清洁,如压延机、挤出机、模具等。
2. 胶料预热:将切好的橡胶胶料放入预热机中进行预热处理,提高胶料的流动性和可塑性。
3. 加工过程:将预热好的胶料送入压延机或挤出机中,通过辊压或挤出的方式将胶料塑形成所需的产品形状。
4. 模具成型:将加工好的橡胶制品放入模具中,进行成型,以获得最终的产品形态。
5. 加工后处理:如修整、修边、烘干等工序,以提高产品的外观质量和性能。
四、产品质量控制1. 抽样检测:从生产线上随机抽取产品样品,进行外观、尺寸、硬度、拉伸强度等指标的检测。
2. 质量分析:根据抽样检测结果,对产品质量进行分析,发现问题及时调整工艺参数或原料配比。
3. 质量记录:将每次产品质量检测的结果进行记录,建立质量档案,以便追溯和分析。
五、设备维护与清洁1. 日常维护:对密炼车间的设备进行定期检查、润滑和维护,确保设备的正常运行。
车间生产工艺流程图
车间生产工艺流程图车间生产工艺流程图是指将车间生产过程中的各个环节和步骤以图形的形式展示出来,以便于工人和管理人员理解和遵循工艺流程,提高生产效率和产品质量。
下面是一个关于汽车零部件生产车间的工艺流程图的标准格式文本。
一、工艺流程图概述汽车零部件生产车间的工艺流程图是为了确保生产过程的顺利进行,保证产品质量和交货期而设计的。
本工艺流程图涵盖了从原材料采购到最终产品出货的全过程。
二、工艺流程图详细描述1. 原材料采购阶段:a. 与供应商联系,确认所需原材料的规格、数量和交货时间;b. 下达采购订单,并进行物料接收登记;c. 对原材料进行质量检验,包括外观、尺寸、化学成分等;d. 合格原材料入库,进行标识和分类。
2. 切割和加工阶段:a. 根据产品的设计要求,将原材料进行切割,得到所需的零部件;b. 对切割后的零部件进行加工,包括冲压、钻孔、铣削等;c. 检查加工后的零部件的尺寸和表面质量,确保符合要求;d. 对加工后的零部件进行清洗和防锈处理。
3. 组装阶段:a. 根据产品的装配图纸,将各个零部件进行组装;b. 对组装后的产品进行功能测试,确保各个部件的正常工作;c. 进行外观检查,确保产品的外观无缺陷;d. 根据客户要求进行包装,并进行产品标识。
4. 质量控制阶段:a. 配备专门的质检人员,对生产过程中的各个环节进行抽样检查;b. 对产品进行全面的质量检测,包括尺寸、外观、性能等;c. 记录并分析质量检测数据,及时发现和解决质量问题;d. 对不合格产品进行返工或废品处理。
5. 成品入库和出货阶段:a. 对合格的成品进行入库管理,包括分类、标识和存储;b. 根据客户订单,进行产品的出货准备,包括包装、装车等;c. 对出货产品进行质量检验,确保产品符合客户要求;d. 安排物流运输,将产品按时交付给客户。
6. 售后服务阶段:a. 建立售后服务团队,负责处理客户的投诉和问题;b. 提供产品的维修和保养指导,确保产品的正常使用;c. 收集客户反馈信息,进行产品改进和优化。
熔铸车间工艺流程
熔铸车间工艺流程一、工艺流程概述熔铸车间是一个关键的生产环节,主要用于将金属材料加热至熔化状态,然后通过浇铸成型的方式创造出各种金属制品。
本文将详细介绍熔铸车间的工艺流程,包括原料准备、熔炼、浇铸、冷却、清理和质检等环节。
二、原料准备1. 原料选择:根据产品要求和生产计划,选择适当的金属材料作为熔铸的原料,常见的金属材料包括铁、铜、铝等。
2. 原料检验:对原料进行外观检查、化学成份分析和物理性能测试等,确保原料的质量符合要求。
3. 原料切割:根据产品的尺寸要求,将原料切割成适当的大小。
三、熔炼1. 熔炼设备准备:确保熔炼炉设备干净、无杂质,并进行必要的维护和保养。
2. 加热炉预热:将熔炼炉加热至适当的温度,以便后续的熔炼操作。
3. 原料投入:将预先准备好的原料投入熔炼炉中,控制炉内的温度和燃料供应,使原料逐渐熔化。
4. 熔化和搅拌:通过燃烧炉内的燃料,使炉内的温度达到原料的熔点,并通过搅拌设备将熔化的金属均匀混合。
四、浇铸1. 浇注准备:准备好浇注模具和浇注工具,确保其干净无损。
2. 浇注操作:将熔化的金属倒入模具中,控制浇注速度和角度,使金属充分填充模具,并避免产生气泡或者其他缺陷。
3. 冷却:待金属在模具中冷却固化,通常需要一定的时间,以确保产品的质量和形状。
五、冷却和清理1. 冷却:将已浇铸的金属制品从模具中取出,然后将其放置在冷却设备中,以便金属迅速冷却至室温。
2. 清理:清理金属制品表面的残留物和氧化层,通常使用机械或者化学方法进行清洁。
六、质检1. 外观检查:对金属制品的外观进行检查,确保其表面光滑、无裂纹、无气泡等缺陷。
2. 尺寸检测:使用测量工具对金属制品的尺寸进行检测,确保其符合设计要求。
3. 化学成份分析:通过化学分析仪器对金属制品的化学成份进行检测,确保其符合产品标准。
4. 物理性能测试:对金属制品的物理性能进行测试,如硬度、强度等,以确保其满足产品要求。
以上是熔铸车间的工艺流程,通过严格按照这个流程进行操作,可以确保熔铸产品的质量和性能符合要求。
- 1、下载文档前请自行甄别文档内容的完整性,平台不提供额外的编辑、内容补充、找答案等附加服务。
- 2、"仅部分预览"的文档,不可在线预览部分如存在完整性等问题,可反馈申请退款(可完整预览的文档不适用该条件!)。
- 3、如文档侵犯您的权益,请联系客服反馈,我们会尽快为您处理(人工客服工作时间:9:00-18:30)。
公分50%,5公分30%,4公分15%,3公分5%(一般用中铝球旦
石);3T球旦石3公分60%,2公分40%(中高铝或高铝球旦石)。 12. 球磨机正常运转速度:60T球约9.5圈/分钟,40T约11圈/分钟。
13.球磨时间:根据实际而定,同浆料细度大小有关,细度越小,机对球 磨时间越长;细度越大,相对球磨时间越短。
原料车间学习培训内容
一
原料加工过程
二 原料车间基本情况
原料加工过程
原材料组成(坭、砂、石粉类) 球磨机放完浆料后开始入球 停下副机,开主机正常运转 项工艺是否达标 铲车铲料入喂料机(根据生产需要,根 待相应 据配方工艺单) 铲好料入喂料机后,准备所需要的各种化工料 全部入到球内,包括入球用的水 一次性把喂料机内的原材料及所需的化工料 入完后盖好球盖,开副机转3-5分钟 如有两次磨 待预计球磨时间够钟后停球开盖检测浆料各 达到工艺要求则
17.浆料种类:微粉、大理石、通体大理石、瓷片,为什么要这么多种类?
同配方结构、生产成本及烧成等有关系。
18、浆料加工过程(混色):硅酸锆起到增白的效果,那么其它颜色 相应效果对应。 19、喷粉:高压雾化干燥法。喷料主要设备有:柱塞泵、喷枪、喷头、 喷片、热风炉、煤灰除尘塔、喷雾塔、尾粉除尘、抽湿大风机。 20、喷粉主要工艺参数:粉料水份控制、颗粒级配控制、粉料进仓前 温度控制。 21、粉料进仓前准备工作:洗干净粉仓、计划好粉料所入的仓号、各 种粉料需要的数量及有计划为下一步做好送料准备并合理安排好粉料 入仓。
22.配送料:根据技术科工艺要求,有计划、有步骤提前做好各项配料
工作,有配比的先配好入中转仓,没有配比的直接送入压机压砖,但 在送料过程同样要除好铁及过好筛,减少砖表面缺陷的产生。同时要
再一次调节好各项工艺要求:水份、颗粒级配、粉料沉腐时间,尽量
控制在工艺指标范围内。并且要多同下工序压机部门沟通协调好工作, 尽量满足适应压机压砖。
14.浆料水份、细度要求:浆料水份一般要求32-34%,浆料细度要求低温
类0.4%以下、高温类0.6%以下、大理石类和底料类0.6-1.0%、瓷片 3.8-4.2%。
15.细度大小同什么有关系:同成本及砖坯坯温有关系。
16.浆料水份大小影响研磨效率、水煤浆耗用成本、粉料颗粒、喷料产量, 大家取一个最合适的平衡点即可。
高×6.5米长,3T球磨机 2.25米高×3米长。
8. 入完球旦石后球内空间:60T球 2.5米—2.6米,40T球 2米—2.2 米,3T球 1.4米—1.6米。
9.
球旦石种类:天然鹅卵石、中铝球石、中高铝球石、高铝球石。
10. 球旦石规格:常用一般有2公分、3公分、4公分、5公分、6公分。 11. 各种规格球球旦石比例:40T、60T球第一次研磨球旦石比例约6
不达标则浆入小球石球磨内细磨 放浆,达不到继续返磨
把各种相应的浆料品种用柱塞泵抽入相应大缸过筛、除铁、储存、中
转、混合、均化
如果不用冲色的普通浆料则可抽入喷雾塔再次过筛
除铁喷料,如果需要冲色对板的浆料,则抽入中转小缸除铁、过筛对 板、对色(为什么要反复过筛除铁?) 技术科对色对板合格后再抽
入喷雾塔小缸再次过筛喷料
浆料变成粉料后送入到相应的粉仓储存
配送料根据技术科工艺 如果是干粉通体大理石则在压
(粉料储存时间原则不少于一天才能使用) 单实施粉料配料、中转、除铁、过筛 (微粉),不是微粉则不用破碎压砖。
机三楼实施干粉混色配料,再送入相应压机中转斗,供压机破碎打砖
7. 球磨机净空高:60T球磨机 3.7米高×7米长,40T球磨机 3.5米