FMEA中严重度频度探测度风险序数评价准则
PFMEA的严重度、频度、探测度评分准则
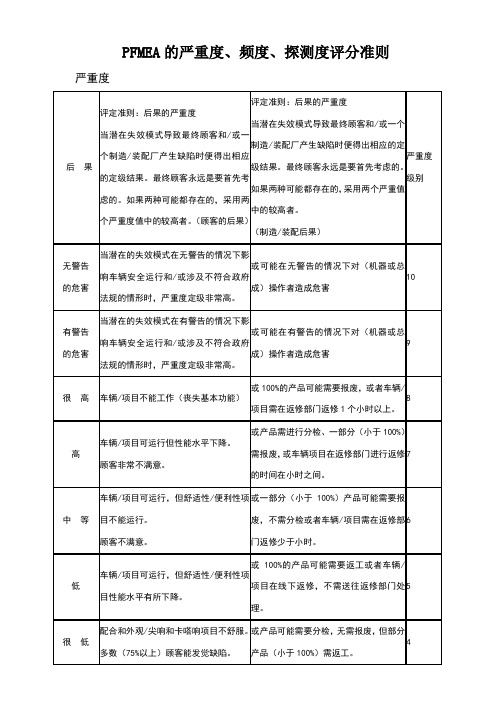
1
1ห้องสมุดไป่ตู้
频度
失效发生可能性
可能的失效率*
频度
很高:持续性失效
≥100个,每1000件
10
50个,每1000件
9
高:经常性失效
20个,每1000件
8
10个,每1000件
7
中等:偶然性失效
5个,每1000件
6
2个,每1000件
5
1个,每1000件
4
低:相对很少发生的失效
个,每1000件
3
个,每1000件
2
极低:失效不太可能发生
2
无
无可辨别的影响
或对操作或操作者而言有轻微的不方便或无影响。
1
探测度
探测性
准则
检查类别
探测方法的推荐范围
探测度
A
B
C
几乎
不可能
绝对肯定不可能探测
X
不能探测或没有检查
10
很微小
控制方法可能探测不出来
X
只能通过间接或随机检查来实现控制
9
微小
控制有很少的机会能探测出
X
只通过目测检查来实现控制
8
很小
控制有很少的机会能探测出
4
高
控制有较多机会可探测出
X
X
在工位上的误差探测,或利用多层验收在后续工序上进行误差探测:供应、选择、安装、确认。不能接受有差异零件。
3
很高
控制几乎肯定能探测出
X
X
在工位上的误差探测(自动测量并自动停机)。不能通过有差异的零件。
2
很高
肯定能探测出
X
由于有关项目已通过过程/产品设计采用了防错措施,有差异的零件不可能产出。
严重度,频度,探测度评分标准(FMEA)

有辨识力的客户(25%以下)能发觉缺 陷。
或部分产品(小于 100%)可能需要 返工,无报废,在生产上原工位返工。
2
无 无可辨别的影响。
或对操作或操作者而轻微的不方便 或无影响。
1
附件二: 失效的机率
很高:持续性失效
高:经常性失效
PFMEA 频度(O)评价准则 失效的比率可能
≥1/2 1/3 1/8 1/20
6
产品/项目可运行但舒适性/便利性项目 性能水平有所下降。
或 100%的产品可能需要返工。
5
多数(75%以上)客户能发觉缺陷。
或产品可能需要分检,无需报废,但 部分产品(小于 100%)需返工。
4
50%的客户能发觉缺陷。
或部分(小于 100%)产品可能需要 返工,无需报废,在生产线上其它工 3 位返工。
高
控制有较多机 会可探测出
×
×
很高
控制几乎肯定 能探测出
×
×
很高 肯定能探测出 ×
在工位上的误差探测,或利用多层 验收在后续工序上进行误差探测: 3 选择、确认。不能接受有差异制品
在工位上的误差探测(自动测量并 自动停机)。不能通过有差异的制 2 品 由于有关项目已通过过程/产品设 计采用了防错措施,有差异的制品 1 不可能产出
CPK <0.33 ≥0.33 ≥0.51 ≥0.67
等级 10 9 8 7
中等:偶然性失效
1/80 1/400
低:相对很少发生的失效
1/2,000 1/15,000
极低:失效不太可能发生
1/150,000 1/1,500,000
≥0.83
6
≥1.00
5
≥1.17
PFMEA的严重度、频度、探测度评分准则
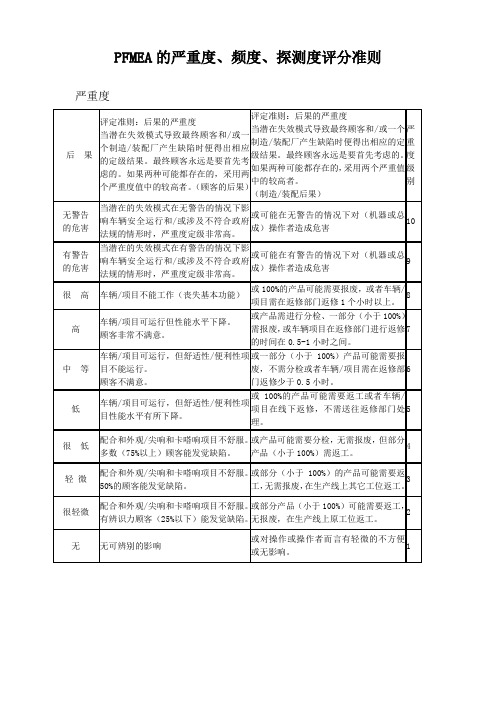
1个,每1000件
4
低:相对很少发生的失效
0.5个,每1
极低:失效不太可能发生
≤0.01个,每1000件
1
或部分产品(小于100%)可能需要返工,无报废,在生产线上原工位返工。
2
无
无可辨别的影响
或对操作或操作者而言有轻微的不方便或无影响。
1
探测度
探测性
准则
检查类别
探测方法的推荐范围
探测度
A
B
C
几乎
不可能
绝对肯定不可能探测
X
不能探测或没有检查
10
很微小
控制方法可能探测不出来
X
只能通过间接或随机检查来实现控制
或可能在有警告的情况下对(机器或总成)操作者造成危害
9
很高
车辆/项目不能工作(丧失基本功能)
或100%的产品可能需要报废,或者车辆/项目需在返修部门返修1个小时以上。
8
高
车辆/项目可运行但性能水平下降。
顾客非常不满意。
或产品需进行分检、一部分(小于100%)需报废,或车辆项目在返修部门进行返修的时间在0.5-1小时之间。
PFMEA的严重度、频度、探测度评分准则
严重度
后果
评定准则:后果的严重度
当潜在失效模式导致最终顾客和/或一个制造/装配厂产生缺陷时便得出相应的定级结果。最终顾客永远是要首先考虑的。如果两种可能都存在的,采用两个严重度值中的较高者。(顾客的后果)
评定准则:后果的严重度
当潜在失效模式导致最终顾客和/或一个制造/装配厂产生缺陷时便得出相应的定级结果。最终顾客永远是要首先考虑的。如果两种可能都存在的,采用两个严重值中的较高者。
X
X
FMEA严重度、频率、探测度评价准则

10件/每千件
每100件中有一件
7
中等
2件/每千件
每500件中有一件
6
0.5件/每千件
每2000件中有一件
5
0.1件/每千件
每10,000件中有一件
4
低
0.01件/每千件
每100,000件中有一件
3
≤0.001件/每千件
每1,000,000件中有一件
2
很低
通过预防控制消除失效。
1
表格Cr3建议的过程FMEA探测度评价准则
对过程,作业或作业员带来轻微的不便。
没有影响
没有可识别的后果。
1
没有影响
没有可识别的影响。
表Cr2建议的过程FMEA频度评价准则
失效可能性
准则:起因发生可能性-过程FMEA(每项/每辆车出现的事故
等级
很高
≥100件/每千件
≥每10件中有1件
10
高
50件/每千件
每20件中有一件
9
20件/每千件
每50件中有一件
9
可能危及作业员(机器或组装)但有警告。
主要功能丧失或降级
丧失基本功能(汽车不能运行,不影响汽车安全运行)
8
严重的破坏
产品可能必须要100%丢弃,生产线停止并停止装运。
主要功能降级(汽车可运行,但是性能层次(少于100%)需被丢弃。主要过程中出现的偏差(生产线速度降低或需增加人力)。
可探测的机率
准则:
过程控制探测可能性
等级
探测可能性
没有探测的可能
没有现行的过程控制,不能探测或不可分析。
10
几乎不可能
在任何阶段不太可能探测
失效模式和/或错误(原因)不容易被探测到(如,随机的审核)。
PFMEA的严重度频度探测度评分准则

有警告
的危害
当潜在的失效模式在有警告的情况下影响车辆安全运行和/或涉及不符合政府法规的情形时,严重度定级非常高。
或可能在有警告的情况下对(机器或总成)操作者造成危害
9
很高
车辆/项目不能工作(丧失基本功能)
或100%的产品可能需要报废,或者车辆/项目需在返修部门返修1个小时以上。
8
高
车辆/项目可运行但性能水平下降。
不能探测或没有检查
10
很微小
控制方法可能探测不出来
X
只能通过间接或随机检查来实现控制
9
微小
控制有很少的机会能探测出
X
只通过目测检查来实现控过双重目测检查来实现控制
7
小
控制可能能探测出
X
X
用制图的方法,如SPC(统计过程控制)来实现控制。
6
中等
控制可能能探测出
X
控制基于零件离开工位后的计量测量,或者零件离开工位后100%的上/通测量
或100%的产品可能需要返工或者车辆/项目在线下返修,不需送往返修部门处理。
5
很低
配合和外观/尖响和卡嗒响项目不舒服。多数(75%以上)顾客能发觉缺陷。
或产品可能需要分检,无需报废,但部分产品(小于100%)需返工。
4
轻微
配合和外观/尖响和卡嗒响项目不舒服。50%的顾客能发觉缺陷。
或部分(小于100%)的产品可能需要返工,无需报废,在生产线上其它工位返工。
当潜在失效模式导致最终顾客和/或一个制造/装配厂产生缺陷时便得出相应的定级结果。最终顾客永远是要首先考虑的。如果两种可能都存在的,采用两个严重值中的较高者。
(制造/装配后果)
严
重
度
FMEA的风险优先数评量准则

文件编号: SPK-P08-W06文件名称:FMEA的风险优先数评量准则一、目的:为通过设计前、量产前的FMEA分析,规范和减少设计及制程中已知和潜在的不良模式并针对不良模式,在设计及量产前提出预防措施,以提高设计之稳定性,可靠性,提高制程品质和制程能力‧二、范围:设计管制活动、设计变更前/后、制程标准订定及变更前/后的潜在失效模式之作业‧三、定义:Failure Mode and Effecting Analysis---潜在失效模式与后果分析‧为一系统化的分析技术,用以评估某一可能缺点的发生机率,及其发生后造成的影响‧而且针对高风险( RPN,Risk PrioriTD Number )项目,事先评估其制程能力,俾能订定适当的制程管制‧四、权责:4‧1‧工程部:FMEA会议召开,产品保证计划,新产品流程草案主导拟定,FMEA作业制定,主导FMEA会议‧4‧2‧制造及成型事业处:流程的讨论确认,潜在不良模式收集,潜在不良原因分析,预防措施的拟定、确认、实施‧4‧3‧品保部:FMEA作业所需之相似制程之统计数据的提供,预防措施的监督执行‧4‧4‧管理代表:FMEA文件的核准‧五、作业内容:设计FMEA1.严重性(S)后果判定准则:后果的严重度级别无警告的严重危害严重级别很高。
潜在失效模式影响车辆安全运行和/或包含不符合政府法规情形。
失效发生时无预警。
10有警告的严重危害严重级别很高。
潜在失效模式影响车辆安全运行和/或包含不符合政府法规情形。
失效发生时无预警。
9很高车辆/系统/产品无法运行(丧失基本功能)。
8 高车辆/系统/产品能运行,但性能下降。
顾客很不满意。
7名称FMEA的风险优先数评量准则页次1/6 依据设计开发管理程序低车辆/系统/产品能运行,但舒适性/方便性方面性能下降。
顾客有些不满意。
5很低装配和外观不符合要求,多数顾客发现有缺陷(多于75%)。
4 轻微装配和外观不符合要求,50%的顾客发现有缺陷。
PFMEA的严重度频度探测度评分准则

严
重
度
级
别
无警告
的危害
当潜在的失效模式在无警告的情况下影响车辆安全运行和/或涉及不符合政府法规的情形时,严重度定级非常高。
或可能在无警告的情况下对(机器或总成)操作者造成危害
10
有警告
的危害
当潜在的失效模式在有警告的情况下影响车辆安全运行和/或涉及不符合政府法规的情形时,严重度定级非常高。
PFMEA的严重度、频度、探测度评分准则
严重度
后果
评定准则:后果的严重度
当潜在失效模式导致最终顾客和/或一个制造/装配厂产生缺陷时便得出相应的定级结果。最终顾客永远是要首先考虑的。如果两种可能都存在的,采用两个严重度值中的较高者。(顾客的后果)
评定准则:后果的严重度
当潜在失效模式导致最终顾客和/或一个制造/装配厂产生缺陷时便得出相应的定级结果。最终顾客永远是要首先考虑的。如果两种可能都存在的,采用两个严重值中的较高者。
1
频度
失效发生可能性
可能的失效率*
频度
很高:持续性失效
≥100个,每1000件
10
50个,每1000件
9
高:经常性失效
20个,每1000件
8
10个,每1000件
7
中等:偶然性失效
5个,每1000件
6
2个,每1000件
5
1个,每1000件
4
低:相对很少发生的失效
个,每1000件
3
个,每1000件
2
极低:失效不太可能发生
7
中等
车辆/项目可运行,但舒适性/便利性项目不能运行。
顾客不满意。
或一部分(小于100%)产品可能需要报废,不需分检或者车辆/项目需在返修部门返修少于小时。
PFMEA的严重度、频度、探测度评分准则
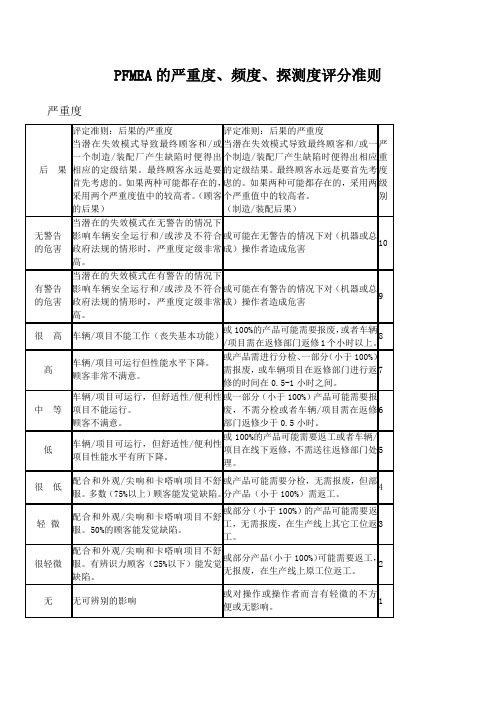
微小
控制有很少的机会能探测出
X
只通过目测检查来实现控制
8
很小
控制有很少的机会能探测出
X
只通过双重目测检查来实现控制
7
小
控制可能能探测出
X
X
用制图的方法,如SPC(统计过程控制)来实现控制。
6
中等
控制可能能探测出
X
控制基于零件离开工位后的计量测量,或者零件离开工位后100%的上/通测量
5
中上
控制有较多机会可探测出
X
X
在后续工位上的误差探测,或在作业准备时进行测量和首件检查(仅适用于作业准备
在工位上的误差探测,或利用多层验收在后续工序上进行误差探测:供应、选择、安装、确认。不能接受有差异零件。
3
很高
控制几乎肯定能探测出
X
X
在工位上的误差探测(自动测量并自动停机)。不能通过有差异的零件。
PFMEA的严重度、频度、探测度评分准则
严重度
后果
评定准则:后果的严重度
当潜在失效模式导致最终顾客和/或一个制造/装配厂产生缺陷时便得出相应的定级结果。最终顾客永远是要首先考虑的。如果两种可能都存在的,采用两个严重度值中的较高者。(顾客的后果)
评定准则:后果的严重度
当潜在失效模式导致最终顾客和/或一个制造/装配厂产生缺陷时便得出相应的定级结果。最终顾客永远是要首先考虑的。如果两种可能都存在的,采用两个严重值中的较高者。
或可能在有警告的情况下对(机器或总成)操作者造成危害
9
很高
车辆/项目不能工作(丧失基本功能)
或100%的产品可能需要报废,或者车辆/项目需在返修部门返修1个小时以上。
8
高
车辆/项目可运行但性能水平下降。
- 1、下载文档前请自行甄别文档内容的完整性,平台不提供额外的编辑、内容补充、找答案等附加服务。
- 2、"仅部分预览"的文档,不可在线预览部分如存在完整性等问题,可反馈申请退款(可完整预览的文档不适用该条件!)。
- 3、如文档侵犯您的权益,请联系客服反馈,我们会尽快为您处理(人工客服工作时间:9:00-18:30)。
主要功能丧
失或降级
丧失基本功能(汽车不能运行
不影响汽车安全运行)
8
严重破坏
产品可能必须要100%丢弃,
生产线停止并停止装运
主要功能降级(汽车可运行
但是性能层次降低)
7
重大破坏
生产运行一部分(少于100%)
需被丢弃。主要过程中出现
的偏差(生产线速度降低或需增加人力)
次要功能丧
失或降级
次要功能丧失(汽车可运行
1
没有影响
没有可识别的影响
频度数(O):推荐的PFMEA频度数评价准则
失效可能性
起因发生可性
等级
很高
≥100件/每千件≥每10件中有1件
10
高
50件/每千件每20件中有1件
9
20件/每千件每50件中有1件
8
10件/每千件每100件中有1件
7
中等
2件/每千件每500件中有1件
6
0.5件/每千件每2,000件中有1件
5
0.1件/每千件每10,000件中有1件
4
低
0.01件/每千件每100,000件中有1件
3
≤0.001件/每千件每1,000,000件中有1件
2
很低
通过预防控制消除失效
1
探测度(D):推荐的PFMEA探测度评价准则
可探测的机率
准则:过程控制探测可能性
等级
探测可能性
没有探测的可能
没有现行的过程控制,不能探测或不可分析
10
几乎不可能
在任何阶段不太可能探测
失效模式和/或错误(原因)不容易被探测到(如,随机的审核)
9
很微小
后加工问题探测
操作人员通过视觉/触觉/听觉在后加工进行失效模式探测
8
微小
从源头进行的问题探测
操作人员通过视觉/触觉/听觉的方式进行工位上的失效模式探测或通过使用特性测量(通/止,手工扭转检查/点击扳手等)进行后加工时的失效模式探测
7
非常低
加工后问题探测
操作人员通过使用各种测量进行后加工失效模式探测或操作人员通过使用各种特性测量(通/止,手工扭转检查/点击扳手等)进行工位上的失效模式探测
6
低
从源头进行的问题探测
由操作人员通过使用各种测量进行后加工失效模式或错误(起因)探测或由工位上的由自动化的控制设备探测不符合零件并通过(指示灯,鸣声)通知操作人员。在作业前准备和首件检查时进行测量(仅用于探测作业前准备的起因)
·RPN≤100
但是舒适度/便利等功能失效)
6
中等破坏
生产运行的100%需要进行下生
产线返工,然后可被接受
次要功能降低(汽车可运行
但是舒适度/便利等功能降低)
5
生产运行的一部分需要进行
下生产线返工,然后可被接受
烦扰的小问题
汽车可运行,但是外观或噪音等
项目不合格,并且大多数(>75%)顾客会发现这些缺陷。
4
中等破坏
生产运行100%需要在其运行
前进行生产线的工站上返工
汽车可运行,但是外观或噪音等
项目不合格,并且许多(50%)顾客会发现这些缺陷
3
生产运行的一部分需要在其运行
前进行生产线的工站上返工
汽车可运行,但是外观或噪音等
项目不合格,并且少数(<25%)有辨识能力的顾客会发现这些缺陷
2
次要破坏
对过程,作业或作业员带来
轻微的不便
没有影响
没有可识别的后果
5
中等
加工后问题探测
由自动化控制进行后加工失效模式探测。这种自动化控制能探测不符合零件并锁定零件以防止进一步的操作
4
中上
从源头进行的问题探测
由自动化控制进行工位上失效模式探测。这种自动化控制能探测不符合零件,并自动锁定工位上的零件以防止进一步的操作
3
高
错误探测和/或问题预防
由自动化控制进行工位上错误(起因)探测,这种自动化控制能探测错误和预防不符合零件的制造
推荐的PFMEA严重度评价准则
后果
顾客后果
等级
后果
制造/组装后果
不符合安全
或法规要求
潜在失效模式影响车辆安全运行和
/或包含不符合政府法规情形。
失效发生时无警告
10
不符合安全
或法规要求
可能危及作业员
(机器或组装)而无警告
潜在失效模式影响车辆安全运行和/或包含
不符合政府法规情形。失效发生时有警告
9
可能危及作业员(机器或组装)
2
很高
探测不可行错误预防
错误(起因)预防是通过固定设施设计,机械设计或零件设计而产生的。通过过程或产品设计进行防错而避免制造不符合零件
1
几乎肯定
•风险顺序数RPN =严重度(S)×频度数(O)×探测度(D)
是一項过程风险的指标。
•RPN值很高,过程设计人员必须采取纠正措施;
•不管RPN多大,只要S高时,就要引起特别注意.