5000kN液压剪断机在连铸线上的应用
连铸切割系统在炼钢企业中的应用及优化
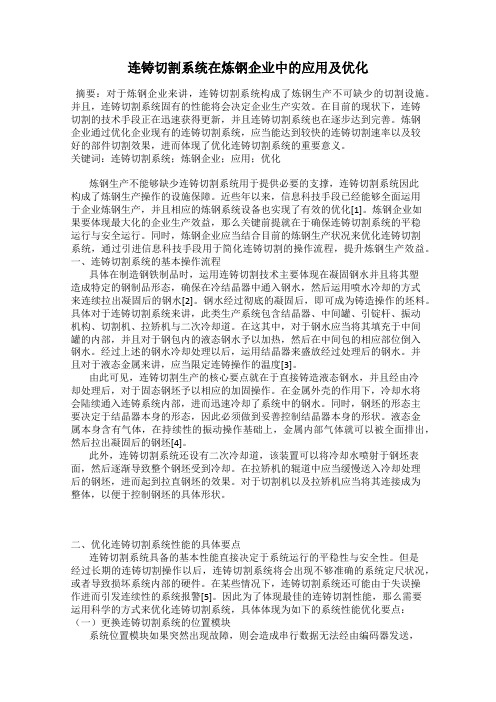
连铸切割系统在炼钢企业中的应用及优化摘要:对于炼钢企业来讲,连铸切割系统构成了炼钢生产不可缺少的切割设施。
并且,连铸切割系统固有的性能将会决定企业生产实效。
在目前的现状下,连铸切割的技术手段正在迅速获得更新,并且连铸切割系统也在逐步达到完善。
炼钢企业通过优化企业现有的连铸切割系统,应当能达到较快的连铸切割速率以及较好的部件切割效果,进而体现了优化连铸切割系统的重要意义。
关键词:连铸切割系统;炼钢企业;应用;优化炼钢生产不能够缺少连铸切割系统用于提供必要的支撑,连铸切割系统因此构成了炼钢生产操作的设施保障。
近些年以来,信息科技手段已经能够全面运用于企业炼钢生产,并且相应的炼钢系统设备也实现了有效的优化[1]。
炼钢企业如果要体现最大化的企业生产效益,那么关键前提就在于确保连铸切割系统的平稳运行与安全运行。
同时,炼钢企业应当结合目前的炼钢生产状况来优化连铸切割系统,通过引进信息科技手段用于简化连铸切割的操作流程,提升炼钢生产效益。
一、连铸切割系统的基本操作流程具体在制造钢铁制品时,运用连铸切割技术主要体现在凝固钢水并且将其塑造成特定的钢制品形态,确保在冷结晶器中通入钢水,然后运用喷水冷却的方式来连续拉出凝固后的钢水[2]。
钢水经过彻底的凝固后,即可成为铸造操作的坯料。
具体对于连铸切割系统来讲,此类生产系统包含结晶器、中间罐、引锭杆、振动机构、切割机、拉矫机与二次冷却道。
在这其中,对于钢水应当将其填充于中间罐的内部,并且对于钢包内的液态钢水予以加热,然后在中间包的相应部位倒入钢水。
经过上述的钢水冷却处理以后,运用结晶器来盛放经过处理后的钢水。
并且对于液态金属来讲,应当限定连铸操作的温度[3]。
由此可见,连铸切割生产的核心要点就在于直接铸造液态钢水,并且经由冷却处理后,对于固态钢坯予以相应的加固操作。
在金属外壳的作用下,冷却水将会陆续通入连铸系统内部,进而迅速冷却了系统中的钢水。
同时,钢坯的形态主要决定于结晶器本身的形态,因此必须做到妥善控制结晶器本身的形状。
连铸机范文

连铸机范文连铸机连铸机是一种金属连续铸造设备,主要用于铸造钢铁等金属材料。
它是传统铸造工艺的一种改进技术,能够实现连续铸造,提高生产效率和产品质量。
本文将详细介绍连铸机的原理、结构和主要应用。
连铸机的工作原理是通过铸模、冷却装置、钢液收集系统和铸坯传送系统等组成的连续铸造系统实现的。
连铸机的主要结构包括坯料箱、浇注箱、结晶器、支撑框架、拉伸装置、切割机、传送装置等。
首先,坯料箱用于储存铸造钢液,通过加热保温设备保持一定的温度,以保证钢液的铸造质量。
然后,钢液通过浇注箱进入结晶器,结晶器是连铸机的关键部件之一、结晶器保持一定的温度,并通过冷却水冷却结晶器表面,使钢液迅速凝固,形成钢坯。
接下来,钢坯通过支撑框架被拉伸装置拉伸,从而使钢坯的截面积减小,并延长钢坯的长度。
拉伸装置通常由两组或多组辊轮组成,驱动辊轮以恒定的速度旋转,从而达到拉伸效果。
拉伸后的钢坯通过切割机进行切割,切割机通常采用高速切割轮,能够迅速切割钢坯,并将切割好的钢坯送入传送装置。
传送装置负责将切割好的钢坯送往下游工序,如热轧或冷轧作进一步处理。
连铸机的主要应用是生产中小型钢材和铸造坯料。
它可以生产各种形状的钢材,如圆坯、方坯和矩形坯等。
连铸机可以生产高品质的钢材,具有良好的内部结构和表面平整度。
因此,它被广泛应用于汽车制造、船舶建造、机械制造和建筑行业等。
与传统的铸造工艺相比,连铸机具有以下优点:首先,连铸机能够实现钢液的连续铸造,从而提高了生产效率。
与传统的铸造工艺相比,连铸机的生产速度更快,能够满足大规模生产的需求。
其次,连铸机可以生产高品质的钢材。
因为钢液在连铸机中迅速冷却,形成细小的晶粒,具有良好的内部结构和表面平整度。
此外,连铸机可以根据需要调整钢坯的截面积和长度,从而满足不同客户的需求。
尽管连铸机具有许多优点,但也存在一些限制。
首先,连铸机的设备投资和运营成本较高。
其次,连铸机的操作技术要求较高,需要熟练的操作人员才能正常运行。
板坯连铸机高精度扇形段的应用与发展

2010年第5期梅山科技·53·檭檭檭檭檭檭檭檭檭檭殐殐殐殐综述板坯连铸机高精度扇形段的应用与发展宣守蓉1汪洪峰2(1.梅山钢铁公司技术中心2.梅山钢铁公司炼钢厂南京210039)摘要:依赖于可以远程控制的高精度扇形段的动态轻压下技术可使连铸坯内部质量特别是中心偏析得到较大改善,大大提高产品质量及经济效益。
着重对不同结构形式和控制方式的高精度扇形段进行了分析和比较,指出SMART 扇形段和CyberLink 扇形段将成为板坯连铸机高精度扇形段发展的趋势。
关键词:板坯连铸机;扇形段;动态轻压下Application and Development of High Accuracy Segment for Slab Continuous CasterXuan Shourong 1Wang Hongfeng 2(1.Technology Center of Meishan Iron &Steel Co.,2.Steelmaking Plant of Meishan Iron &Steel Co.,Nanjing 210039)Key words :slab continuous caster ;segment ;dynamic soft reduction 连铸动态轻压下技术是20世纪90年代中后期,随着高精度液压扇形段制造和远程控制技术的进步而产生的提高连铸坯质量的一种经济高效的新技术,它通过在连铸坯凝固区域末端施加压力产生一定的压下量来补偿铸坯的凝固收缩量,防止晶间富集溶质元素的钢液向铸坯中心横向流动,促进钢液中的溶质元素进行重新分配,从而使铸坯的凝固组织更加均匀致密,以减少铸坯中心偏析和中心疏松。
动态轻压下技术主要由热跟踪模型、自动调节系统和能够实现远程控制的高精度扇形段3个部分组成。
高精度扇形段根据指令动态调整液压缸压力设置,从而改变辊缝和压下量,保证非稳态浇铸的轻压下效果。
连铸机液压系统分析与总结

连铸机液压系统分析与总结祝家兴,王勇(马钢集团设计研究院有限责任公司,安徽马鞍山243000)摘要:文章介绍了近几年国内外异型坯及方坯连铸机液压系统的结构特点,对钢包回转台、中间罐车及出坯区设备等典型液压回路进行了总结,并描述了在设计过程中提出的优化方案。
关键词:连铸机;液压系统Metallurgy and materials作者简介:祝家兴(1981-),男,辽宁锦州人,大学本科,工程师,研究方向:液压、润滑系统设计。
随着国内外连铸机生产工艺的不断进步,液压控制系统作为连铸机生产线的重要组成部分其技术得到迅速发展并日渐成熟。
除此之外近年来随着国内炼钢和轧钢技术的发展,钢铁工业结构的变化和对产品规格、质量的新要求,同样促进了连铸工艺技术的提高。
连铸机液压系统具有以下优点:体积小、重量轻;传动效率高、传动功率大;结构紧凑并便于安装维护;伺服、比例系统控制精度高;蓄能器的独特蓄能作用可确保在事故状态下连铸机还能工作一段时间,减少经济损失。
1连铸机液压系统分区传统的连铸机液压系统为确保经济、节能等指标均设一套液压传动系统,为整条连铸机生产线机械设备的液压执行元件提供动力液压油。
由于伺服、比例系统逐渐发展以及液压控制系统与PLC 的紧密结合,使得液压系统的污染控制要求远高于八九十年代。
从技术和经济的观点出发完全去除液压系统油液中的污染物是不现实的,这样液压系统的合理分区就显得非常关键,关键设备、关键元件譬如伺服系统独立分割出来,对系统清洁度要求相对较低的元件共用另外一套动力源。
当然处于设备日常操作维护的角度,越少的检修作业区越便于保证连铸机的长时间正常工作。
结合国内外连铸机液压系统的设计思路,考虑连铸机生产线不同工艺段的实际需求,现阶段异型坯、方坯连铸机线上液压系统大致可划分为4个系统回路。
(1)钢水区液压系统。
钢水区液压系统为钢包回转台、滑动水口、中间罐车、长水口机械手及铸流切断设备提供动力液压油。
(2)结晶器振动台液压系统。
小方坯连铸机切割方式对比分析

态,气源不稳定直接影响铸坯切割,需增加伴热输送
(比如采用电伴热)装置输送。焦炉煤气因其中含有较
多杂质,管道容易堵塞。部分钢厂设计之初釆用焦炉
煤气切割铸坯,在生产过程中因无法改善这一问题,
随后改为丙烷气切割铸坯。如果想使用焦炉煤气,_
种方法是提高煤气压力到0.6 MPa,必要时定期更换 煤气管道。对于火切机由于其结构简单,更换方便快
个方面的对比,旨在说明小方坯连铸机两种切割的
优劣势,让企业在连铸机初步设计阶段的设备选型 、
费用投入和人员配备等方面综合考虑 ,以避免出现
投产后不满足安全环保、生产组织等要求,被迫进行
改造等问题发生。
参考文献
[1] 谷士强.冶金机械安装工程手册[M]惊:冶金工>出版社,1997.
[2] 刘川俊.36吨转炉系统方坯连铸机改造工程竣工[J].柳钢科技,
0.45元/t钢,备件费约为0.4元/t钢,液压油费约为 0.2元/t钢,维修费约为0.1元/t钢,总计约1.15 元/t钢。液压剪剪切铸坯没有割缝,大大地减少了 铸坯损失。
2.6日常维护 丙烷气在钢瓶中以液态形式存在,从钢瓶出来
后变为气态输送,境温度过低时,部分气态丙烷又会变成液
液压剪在切割过程中不存在烟尘,为避免在线 漏油导致火灾发生,液压油可选择水乙二醇等不易 燃的介质。相比火焰切割,液压剪每年可减少大量
CO2、SO2等有害气体排放。 2.2适用范围
火焰切割适应性广,异型坯、板坯、小方坯均能 切割。液压剪目前只限于165 mn?以下小断面铸坯 使用。对于断面在165 mn?以上的小方坯,要求液压 剪工作压力较高,目前液压技术尚不能满足。对于断 面不大于165 mn?的小方坯连铸机,近年来由于液 压剪技术进步,液压剪故障率及维修费率大幅下降, 只要温度符合要求(3850七),不论特种钢、合金钢 还是普通钢种,剪切均可满足要求。
连铸的切割辊道等附属设备

连铸的切割辊道等附属设备切割机A)作用将被连续拉出的铸坯按定尺要求切断的连铸设备。
即根据成品规格及后步工序的要求,在连铸坯完全凝固后,进行在线定尺或倍尺切割。
B)类型连铸机的切割设备有火焰切割机和机械剪切(剪切机)两大类。
⑴火焰切割机①工作原理火焰切割机使用预热氧和燃气混合燃烧的火焰使切割缝处的金属熔化,并利用高压切割氧的能量把熔化的金属吹掉,形成切缝,切断铸坯。
燃料有高压精制焦炉煤气、天然气、丙烷和乙炔等。
②特点火焰切割机设备简单,质量轻,投资省,设备也易于维护;不受铸坯断面尺寸和温度的限制(冷坯也可切割),切口平整不变形;但切缝金属损失较多(切割时有一定量的金属损耗)③应用目前绝大多数连铸机采用火焰切割。
小断面连铸坯只用一支切割枪切割,大断面连铸坯需用双枪从铸坯两侧同时进行切割。
火焰切割机广泛用于板坯、方坯、圆坯和异型坯的定尺切割和头、尾切割等。
同步机构是使切割车与铸坯在无相对运动的条件下完成切割的机构。
常用的有夹钳式、背负式和坐骑式等几种方式。
夹钳式靠气缸使两侧夹臂的夹头夹住铸坯。
背负式靠自重或气缸的推力使夹紧臂直接压在铸坯上达到与铸坯同步的目的,适用于宽板坯和宽度变化大的板坯连铸机上。
坐骑式为切割枪小车直接骑在板坯上,这种方式已很少采用了割枪小车是用于支承切割枪并使之运动的装置。
割枪运动方式有直线式和摆动式两种,安装在切割车上。
割枪小车的速度可灵活调速,有起切、正常切割、高速返回和高速接近等不同的速度。
切割枪对铸坯进行切割。
它由枪体和割嘴组成。
割嘴的种类主要有内混式、外混式和内预混式。
以内预混式为最好,加热效率高,焰心长,有利于优质快速切割。
还有一种带喷粉的割嘴,用于高合金钢和不锈钢铸坯的切割。
气水分配系统包括氧气、燃气、压缩空气和冷却水的各种阀门、管线以及测量仪表等。
切割设备的电控系统一般采用PLC控制。
⑵机械剪切(剪切机)A)分类①按驱动方式有电动和液压(机械剪和液压剪)两种;②按其与铸坯同步运动方式分摆动式和平移式;③按剪切运动方式分上切式和下切式。
友荃能源氢氧发生器在连铸坯切割中的应用
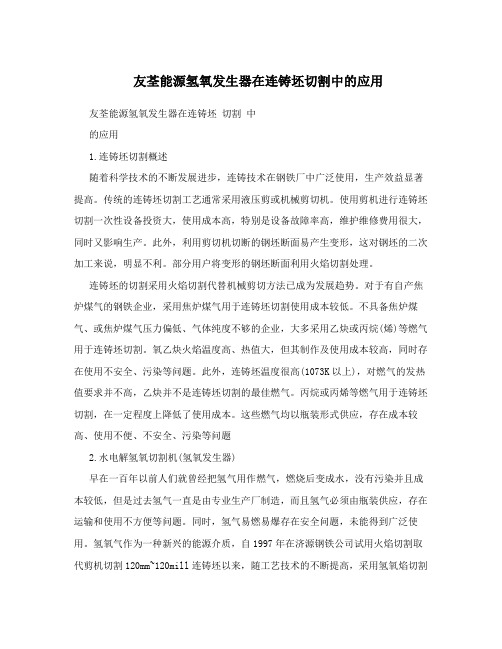
友荃能源氢氧发生器在连铸坯切割中的应用友荃能源氢氧发生器在连铸坯切割中的应用1.连铸坯切割概述随着科学技术的不断发展进步,连铸技术在钢铁厂中广泛使用,生产效益显著提高。
传统的连铸坯切割工艺通常采用液压剪或机械剪切机。
使用剪机进行连铸坯切割一次性设备投资大,使用成本高,特别是设备故障率高,维护维修费用很大,同时又影响生产。
此外,利用剪切机切断的钢坯断面易产生变形,这对钢坯的二次加工来说,明显不利。
部分用户将变形的钢坯断面利用火焰切割处理。
连铸坯的切割采用火焰切割代替机械剪切方法已成为发展趋势。
对于有自产焦炉煤气的钢铁企业,采用焦炉煤气用于连铸坯切割使用成本较低。
不具备焦炉煤气、或焦炉煤气压力偏低、气体纯度不够的企业,大多采用乙炔或丙烷(烯)等燃气用于连铸坯切割。
氧乙炔火焰温度高、热值大,但其制作及使用成本较高,同时存在使用不安全、污染等问题。
此外,连铸坯温度很高(1073K以上),对燃气的发热值要求并不高,乙炔并不是连铸坯切割的最佳燃气。
丙烷或丙烯等燃气用于连铸坯切割,在一定程度上降低了使用成本。
这些燃气均以瓶装形式供应,存在成本较高、使用不便、不安全、污染等问题2.水电解氢氧切割机(氢氧发生器)早在一百年以前人们就曾经把氢气用作燃气,燃烧后变成水,没有污染并且成本较低,但是过去氢气一直是由专业生产厂制造,而且氢气必须由瓶装供应,存在运输和使用不方便等问题。
同时,氢气易燃易爆存在安全问题,未能得到广泛使用。
氢氧气作为一种新兴的能源介质,自1997年在济源钢铁公司试用火焰切割取代剪机切割120mm~120mill连铸坯以来,随工艺技术的不断提高,采用氢氧焰切割连铸坯具有使用安全、成本低、无污染、切割断口质量好等优点。
受到中小钢铁企业的普遍重视。
水电解氢氧发生器主要由整流及控制装置、电解槽、补水系统、集气装置、滤水系统、以及泄爆设施、报警和压力控制系统、水封装置等组成。
交流电经整流供给电解槽作用于含有约20%氢氧化钾或氢氧化钠的水溶液,氧离子在电解槽的阳极释放电子析出氧气,氢离子在电解槽的阴极获得电子析出氢气,钾(或钠)离子用于提高水溶液的导电能力。
连铸机工作原理
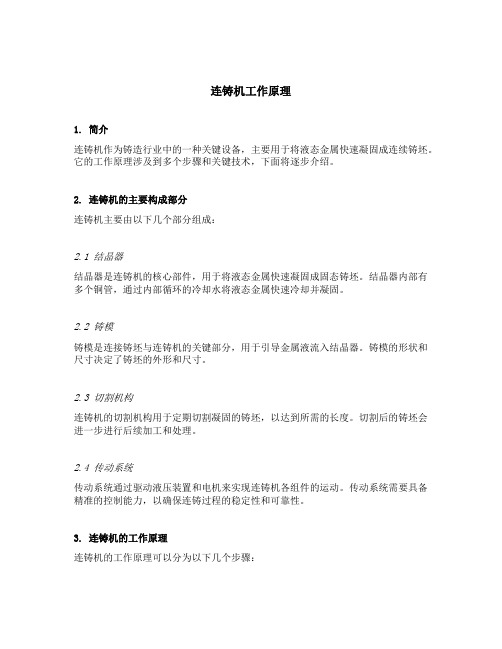
连铸机工作原理1. 简介连铸机作为铸造行业中的一种关键设备,主要用于将液态金属快速凝固成连续铸坯。
它的工作原理涉及到多个步骤和关键技术,下面将逐步介绍。
2. 连铸机的主要构成部分连铸机主要由以下几个部分组成:2.1 结晶器结晶器是连铸机的核心部件,用于将液态金属快速凝固成固态铸坯。
结晶器内部有多个铜管,通过内部循环的冷却水将液态金属快速冷却并凝固。
2.2 铸模铸模是连接铸坯与连铸机的关键部分,用于引导金属液流入结晶器。
铸模的形状和尺寸决定了铸坯的外形和尺寸。
2.3 切割机构连铸机的切割机构用于定期切割凝固的铸坯,以达到所需的长度。
切割后的铸坯会进一步进行后续加工和处理。
2.4 传动系统传动系统通过驱动液压装置和电机来实现连铸机各组件的运动。
传动系统需要具备精准的控制能力,以确保连铸过程的稳定性和可靠性。
3. 连铸机的工作原理连铸机的工作原理可以分为以下几个步骤:3.1 准备阶段在连铸机开始工作之前,需要对连铸机进行各项检查和准备工作。
包括检查冷却水系统、液压系统、电气系统等是否正常运行,确保铸坯模具的清洁和正确安装。
3.2 浇注铸坯首先,将液态金属通过浇注设备注入铸模中。
连铸机通过液压系统控制浇注速度,以保证液态金属在铸模中的填充均匀性和稳定性。
3.3 凝固过程液态金属在结晶器中快速冷却并凝固。
内部的冷却水通过铜管与液态金属接触,将金属温度快速降低,使其凝固成固态铸坯。
凝固过程中,结晶器的移动速度要与液态金属的凝固速度相匹配,以保证凝固界面的稳定和铸坯的质量。
3.4 切割铸坯当铸坯达到所需长度后,连铸机的切割机构会进行切割,将铸坯从连铸机上分离。
同时,切割后的铸坯会被传送到后续的加工设备进行进一步加工和处理。
3.5 循环再铸连铸机可以实现连续工作,即一块铸坯完成后,下一块铸坯可以立即开始制备。
通过循环再铸,可以提高生产效率和连铸机的利用率。
4. 连铸机的优势和应用领域连铸机具有以下几个优势:4.1 提高生产效率连铸机的连续工作方式,使得生产效率大大提高。
- 1、下载文档前请自行甄别文档内容的完整性,平台不提供额外的编辑、内容补充、找答案等附加服务。
- 2、"仅部分预览"的文档,不可在线预览部分如存在完整性等问题,可反馈申请退款(可完整预览的文档不适用该条件!)。
- 3、如文档侵犯您的权益,请联系客服反馈,我们会尽快为您处理(人工客服工作时间:9:00-18:30)。
・214・《机床与液压》2004. No. 105000kN液压剪断机在连铸线上的应用 胡品龙,顾瑞华 (江阴市华宏液压机械厂,江苏江阴214423) 摘要:介绍了全自动液压钢坯在线剪的工作原理。该剪断机利用可编程控制器对设备的动作进行全程控制,辅以变频调速控制设备的行走,适合于大断面钢坯连铸生产线的使用,生产效率高,使用成本低。 关键词:钢坯连铸;液压传动;PLC控制;变频调速 中图分类号:V261. 7 + 6文献标识码:s文章编号:1001-3881 (2004) 10-214-2 The Application of 5000kN Hydraulic Billet Shears in the Continuous一casting Line
HU Pin-long, GU Rui-hua (Jiangyin Huahong H州raulic Machinery Factory,Jiangyin 214423 China) Abstract; The working principle of automatic h州raulic billet shears in continuous一casting steel line was introduced. The shearwas controlled all the processes场PLC, and was equipped with a variable一frequency equipment to control the running. The shearingis suit for the large section steel billet in continuous一casting line, and has high production efficiency and low cost. Keywords; Continuous一casting of steel billet; Hydraulic drive; PLC control; Variable一frequency control0前言左右。 连续铸钢技术已成为当代冶金生产的重大技术成(2)设备简介。该液压在线钢坯剪断机与水平果而被广泛使用。它不仅简化了冶金生产工序,缩短方向成450,剪切方向为钢坯的对角线,由三部分组了冶金生产流程,而且大大节约了能耗,提高了金属成:机械部分、液压控制系统与电气控制系统。机械收得率,改善了铸坯质量。同时,它还改善了劳动生部分主要包括机架机座、行走机构、压料装置、剪切产条件,使生产过程实现了连续化、机械化和自动装置(含剪切导向装置、刀片间隙调整装置)和冷化。作为连铸,按其工艺要求必须进行定尺。在线切却、润滑装置;液压控制系统包括电机油泵、阀组、断钢坯的方式,大多采用自动或人工火焰切割,材料油缸、油箱及连接管道;电气系统由电机控制系统、损耗大、切割成本高。但是随着国内连铸生产能力的PLC控制系统和变频调速控制系统及相应的程序、线不断扩大,大断面钢坯的生产已成为当前生产的主路等组成。这三部分有机地结合在一起,形成一个整流,以上的钢坯切断手段已越来越不能适应当前的生体安装在轨道上。产需求。因此,我厂陆续开发了一系列大吨位液压钢(3)设备动作原理简介。设备处于初始位置,坯剪断机,用于大断面钢坯的在线剪切。连铸钢坯穿过剪切刀口,变频调速电机工作使设备加,设备工作状况及动作原理简介速,钢坯碰到定尺装置的发讯器,设备的前进行走速 (1)设备工作状况简介。在钢坯连铸生产线上,度达到与钢坯同速,压料油缸工作将钢坯压住,压料由于钢坯是连续铸出的,所以要求设备在工作时不能到位后行程开关发讯,剪切油缸工作将钢坯剪断并回出现故障,可靠性要高,在剪切时应根据钢坯的流速程,压料油缸同时回程。剪切油缸和压料油缸回程同步行走,以保证钢坯的定尺精度和铸坯的连续性。时,剪断机在变频电机控制下快速返回,到达起始点同时,由于方形钢坯流出时的状态一般的直剪刀片不等待下一次剪切。整个动作过程可连续完成,也可单适宜使用,所以只能采用V字刀片斜剪(降低断面独手动执行。变形量,方便轧坯)。钢坯流速为1.2一2.5m/min, 2系统组成及工作原理钢坯定尺长度为1一3 m/根,剪切温度大约在7007 2.1系统主要参数(见表1)
剪切系统压料系统行走系统系统额定压力16/31. 5MPa
系统额定压力20 MPa
控制方式变频调速
系统工作压力J决进/回程6 MPa
系统工作压力16 MPa速度范围
0 -5m/min
工进25 MPa
系统工作流量快进/回程415 L/min系统工作流量20 Umin功率
2.2 kW
工进245 L/min
电动机功率52 kW
电动机功率
5.5 kW
2.2液压系统工作原理 (1)剪切系统工作原理说明 如图1所示:剪切系统采用低压大流量、高压小
流量系统。电磁铁1 DT, 2 DT不得电时,低压泵7排出的工作油经调压阀块13一7回油箱,高压泵6排出的工作油经调压阀块13一8回油箱,油泵空负荷运《机床与液压》2004. No. 10・215・行。低压泵7的压力调整由调压阀块13一7设定,压力调定在6MPa。高压泵6的压力调整由调压阀块13-8设定,压力调定在25 MPa。电磁铁1 DT, 2DT,6DT, 3DT得电时,当工作压力小于6MPa时,低压泵7排出的工作油在调压阀块13-7的调定压力下经单向阀块13-2、换向阀块13-4进人剪切油缸15的无杆腔,高压泵6排出的工作油经单向阀块13一1,换向阀块13一4进人剪切油缸15的无杆腔,剪切油向阀14回油箱,压料缸回程。 (3)各动作流量和时间分配 压料过程:流量20 Umin,压料时间2. Os; 压料回程过程:流量20 Umin,压料回程时间1.5s; 快进剪切过程:流量415 Umin,快进剪切时间4. 2s; 工进剪切过程:流量245 Umin,工进剪切时间3. 1 s; 剪切回程过程:流量415 L/min,剪切回程时间3. 4s o 由于压料回程和剪切回程动作同时进行,压料回程时间小于剪切回程时间,所以只计算剪切回程时间。则一个剪切周期所需的时间为10.7s,考虑到油泵的效率和高压泵的排量,剪切周期为12s左右。由于铸造每米钢坯所需的时间为24一50s,所以剪切时间大大小于钢坯铸造时间,符合工艺要求,所选电机、油泵符合要求。同时剪切速度越快,剪切质量越好,剪切断面变形越小。3设备特点 (1)采用了机械、液压传动、PLC控制和交流变频调速控制相结合,是真正机、电、液一体化产品。采用液压传动,剪切力大、易于实现过载保护,惯性小,整个装置结构紧凑,便于自动控制;采用PLC控制,具有可靠性高,编程和使用方便,接线简单,通用性好,网络通讯功能强,易于安装和维护。 (2)整个动作可单独手动也可自动控制,使操作具有灵活性。 (3)采用了恒功率变量柱塞泵技术,节约了能耗。 (4)主机行走机构采用了交流变频调速技术,既符合当前设备发展的主流,又使设备能满足不同钢坯流速变化的要求。 (5)油泵电机组:采用开式系统设计,加载时电磁铁得电,电机启动时不带负荷,既起到了保护电动机的作用,又减少了对电网的负荷和污染。 (6)控制阀组:采用大、小流量双系统,节约了产品成本。同时,设有压力设定功能,并有若干测压点,均可检测到当时的压力情况,向执行机构分配所需的压力能源。 (7)无备用泵:受工作环境的限制不采用备用泵,使设备结构更紧凑。 (8)上、下剪切刀座采用冷却系统,避免在高温环境下金属材料过早失效。 (9)液压系统采用插装阀的集成块结构,具有通油能力大、流动阻力小、响应速度快等特点,使液 (下转第181页右下方)漪皿啊姗器3-51DT 图1液压原理图缸15有杆腔的油经换向阀块13一6回油箱,剪切油缸快速下行。剪切刀下行碰到钢坯,工作压力上升达到或超过6MPa,低压泵7卸荷,高压泵6排出的高压油在调压阀块13一8的设定压力下经单向阀块13一1、换向阀块13-4进入剪切油缸15的无杆腔,剪切油缸15有杆腔的油经换向阀块13 -6回油箱,剪切油缸15工速下行。电磁铁1DT, 2DT, 5DT, 4DT得电时,低压泵7排出的工作油在调压阀块13 -7的调定压力下经单向阀块13-2、换向阀块13一3进人剪切油缸巧的有杆腔,高压泵6排出的工作油经单向阀块13一1、换向阀块13-3进人剪切油缸15的有杆腔,剪切油缸15无杆腔的油经换向阀块13 -5回油箱,剪切油缸快速回程。 (2)压料系统工作原理说明 油泵9排出的工作油经电磁换向阀14回油箱,油泵9空负荷运行,压料油缸16的上升与下降经电磁换向阀14控制:如果电磁铁8DT得电,油泵9排出的高压油在溢流阀12的调定压力下经电磁换向阀14进人压料油缸16的无杆腔,而有杆腔的油经电磁换向阀14回油箱;如果电磁铁7DT得电,油泵9排出的高压油在溢流阀12的调定压力下经电磁换向阀14进人压料油缸16的有杆腔,无杆腔的油经电磁换《机床与液压》2004. No. 10181
(2)限制齿宽最小值为l Omm,得 g2 (x)二10一x, 'x2 }x3<_0 (3) (3)限制模数最小值为2mm,得 93(二)=2一x3 <_0 (4) (4)限制齿宽系数的范围为5/za < ,pd -- 17/z., ,得:94 (x)二5/x。一X,:50 (5) g, (X)==二:一17/x, <_0 (6) (5)根据行星轮齿面接触疲劳强度,得
(6)、根据齿根弯曲疲劳强度,得 2K 'T.97(x)=2一一一一一3・YF・Ys一L,];<o
x,.x2.x3
(7)根据不自锁条件50<a<100,得
g',(x)二5一X5!50g9 (x)=x,一10:50(8)根据太阳轮与行星盘的接触疲劳强度,
(8)
96(x)二Ze 'Z,・(2KT,3 x, 'x2 'x3ZE(i+1)‘’一〔v,一”(7)910 ( x)二
(9)Zv - B
(x,+r2)。,。,_
・—’tgx5一L aJ,< t1 x4 'r2
限制变速器中油的工作温度t, <_ 8WC ,
g>, (x)=to+ad 'tar[(一LN・x, " x3 +40)(一i} "x, "x2 "x3 +40)+(一ifl "x, "x3 +40)2]<80`C
(9)(10)得
(11)得(12)3优化方法的确定 考虑到优化设计的特点,采用混合惩罚函数法进行组合式无级变速器的优化设计,其惩罚函数的构造形式如下: tp(x,rM)二F(:)一;“).
表1组合式无级变速器优化后参数和现有参数的比较优化后参数现有参数z,3436