文献综述-液压机设计
液压机文献综述
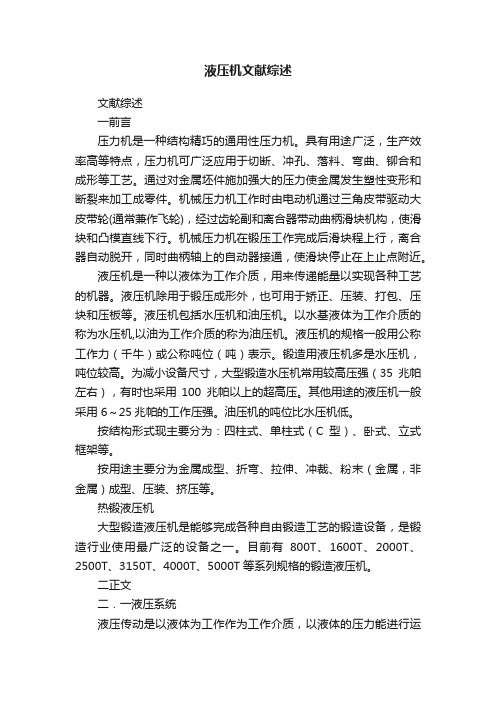
液压机文献综述文献综述一前言压力机是一种结构精巧的通用性压力机。
具有用途广泛,生产效率高等特点,压力机可广泛应用于切断、冲孔、落料、弯曲、铆合和成形等工艺。
通过对金属坯件施加强大的压力使金属发生塑性变形和断裂来加工成零件。
机械压力机工作时由电动机通过三角皮带驱动大皮带轮(通常兼作飞轮),经过齿轮副和离合器带动曲柄滑块机构,使滑块和凸模直线下行。
机械压力机在锻压工作完成后滑块程上行,离合器自动脱开,同时曲柄轴上的自动器接通,使滑块停止在上止点附近。
液压机是一种以液体为工作介质,用来传递能量以实现各种工艺的机器。
液压机除用于锻压成形外,也可用于矫正、压装、打包、压块和压板等。
液压机包括水压机和油压机。
以水基液体为工作介质的称为水压机,以油为工作介质的称为油压机。
液压机的规格一般用公称工作力(千牛)或公称吨位(吨)表示。
锻造用液压机多是水压机,吨位较高。
为减小设备尺寸,大型锻造水压机常用较高压强(35兆帕左右),有时也采用100兆帕以上的超高压。
其他用途的液压机一般采用 6~25兆帕的工作压强。
油压机的吨位比水压机低。
按结构形式现主要分为:四柱式、单柱式(C型)、卧式、立式框架等。
按用途主要分为金属成型、折弯、拉伸、冲裁、粉末(金属,非金属)成型、压装、挤压等。
热锻液压机大型锻造液压机是能够完成各种自由锻造工艺的锻造设备,是锻造行业使用最广泛的设备之一。
目前有800T、1600T、2000T、2500T、3150T、4000T、5000T等系列规格的锻造液压机。
二正文二.一液压系统液压传动是以液体为工作作为工作介质,以液体的压力能进行运动和动力的传递的一种传动方式。
它先通过能量转换装置(液压泵),将原动机(电动机)的机械能转变为液体的压力能,再通过封闭管道、液压控制元件等,经另一能量转换装置(液压缸、液压马达)将液体的压力能转变为机械能,以驱动负载,实现执行机构所需的直线或旋转运动。
与机械传动相比液压系统具有许多优点,因此在机械工程中广泛应用。
液压系统双面钻床文献综述
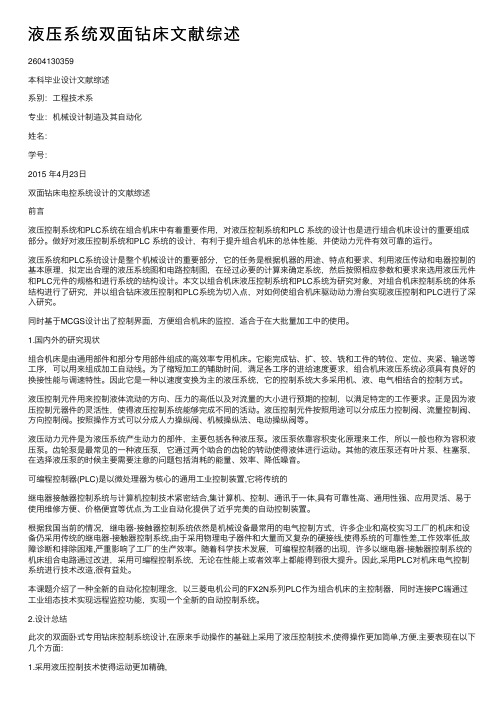
液压系统双⾯钻床⽂献综述2604130359本科毕业设计⽂献综述系别:⼯程技术系专业:机械设计制造及其⾃动化姓名:学号:2015 年4⽉23⽇双⾯钻床电控系统设计的⽂献综述前⾔液压控制系统和PLC系统在组合机床中有着重要作⽤,对液压控制系统和PLC 系统的设计也是进⾏组合机床设计的重要组成部分。
做好对液压控制系统和PLC 系统的设计,有利于提升组合机床的总体性能,并使动⼒元件有效可靠的运⾏。
液压系统和PLC系统设计是整个机械设计的重要部分,它的任务是根据机器的⽤途、特点和要求、利⽤液压传动和电器控制的基本原理,拟定出合理的液压系统图和电路控制图,在经过必要的计算来确定系统,然后按照相应参数和要求来选⽤液压元件和PLC元件的规格和进⾏系统的结构设计。
本⽂以组合机床液压控制系统和PLC系统为研究对象,对组合机床控制系统的体系结构进⾏了研究,并以组合钻床液压控制和PLC系统为切⼊点,对如何使组合机床驱动动⼒滑台实现液压控制和PLC进⾏了深⼊研究。
同时基于MCGS设计出了控制界⾯,⽅便组合机床的监控,适合于在⼤批量加⼯中的使⽤。
1.国内外的研究现状组合机床是由通⽤部件和部分专⽤部件组成的⾼效率专⽤机床。
它能完成钻、扩、铰、铣和⼯件的转位、定位、夹紧、输送等⼯序,可以⽤来组成加⼯⾃动线。
为了缩短加⼯的辅助时间,满⾜各⼯序的进给速度要求,组合机床液压系统必须具有良好的换接性能与调速特性。
因此它是⼀种以速度变换为主的液压系统,它的控制系统⼤多采⽤机、液、电⽓相结合的控制⽅式。
液压控制元件⽤来控制液体流动的⽅向、压⼒的⾼低以及对流量的⼤⼩进⾏预期的控制,以满⾜特定的⼯作要求。
正是因为液压控制元器件的灵活性,使得液压控制系统能够完成不同的活动。
液压控制元件按照⽤途可以分成压⼒控制阀、流量控制阀、⽅向控制阀。
按照操作⽅式可以分成⼈⼒操纵阀、机械操纵法、电动操纵阀等。
液压动⼒元件是为液压系统产⽣动⼒的部件,主要包括各种液压泵。
【文献综述】液压立式绞钢机的设计

文献综述机械设计制造及其自动化液压立式绞钢机的设计绞钢机的发展过程绞纲机是浙江省沿海渔船使用最广泛的绞纲、起网设备。
它由机械传动,通过摩擦鼓轮的后拉力来绞收纲绳。
立式设置与卧式相比,纲绳来向不受限制,因而操作方便,适应性强。
它适用于对网(大围增)、拖网、围网等作]1[业,可以起吊鱼货、起锚、扬帆等多种用途。
自70年代由舟山海洋研究所和舟山船厂共同开发以来,至今已有30多年的历史。
由于它的结构简单,渔船上的机舱人员都能自己维修,并能在捕捞作业时排除故障;又因它的价格适中,使用寿命长,所以,深受渔民欢迎。
]2[随着渔业生产的发展。
船网的增大,功率和拉力的提高,起网速度的加快,致使立式机械传动绞纲机的设计参数、本体结构、传动系统、材料·选用及离合器的形式等方面在不断改进提高,形成系列,从而使绞纲机能适应各类渔船、各种作业的需要。
现将近年来绞钢机参数的变化统计如下:绞纲机设计参数系列是随着渔船吨位、功率的增加。
网具的增大,拖速的加快而形成的,使绞纲机能适应多种捕捞作业的需要,以增加投网次数和捕捞量。
]3[绞纲机主要参数的变化:参数型号拉力KN线速度m/min功率kW时间(年代)JJL2 x 0. 5/40 5x2 40 10 50 JJL2x 1/4U 10x2 40 20 60 JJL2 x 1. 5/40 15x2 40 30 70-80JJL2 x 2/4U 20x2 40 40 70-80 JJL2 x 2. 5/60 25x2 60 75 90(初)JJL2 x 3/6U 30x2 60 92 90绞纲机的液压系统随着改革开放浪潮推向神州大地, 舟山市海洋捕捞业也得到迅猛发展。
由原来的近海浅海作业的小功率小吨位强劳力捕捞渔船,向外海远洋捕捞的大功率]4[大吨位及先进装备条件发展。
为适应大功率、大吨位群众双船底拖网渔船的发展, 向渔船提供技术先进、可靠、拉力二尺、效率高的绞纲机4 以提高渔船总体性能水平显得尤为重要。
文献综述-液压机设计

文献综述-液压机设计一、课题国内外现状液压机是一种以液体为工作介质,用来传递能量以实现各种工艺的机器。
液压机是制品成型生产中应用最广的设备之一。
自19世纪问世以来发展很快,已成为工业生产中必不可少的设备之一。
由于液压机在工作中的广泛适应性,使其在国民经济各个部门获得了广泛应用。
四柱式(通用)液压机属于板料冲压液压机,这类液压机主要用于各种金属板料的冲压成型,包括落料、冲裁、拉伸、弯曲、翻边、精密冲裁等,还可以用于冷挤、校正、压装、粉末制品、磨料制品、塑料制品和绝缘材料的压制成型。
液压机由于具有以下多方面的优点,因此在很多领域得到广泛应用。
1)基于液压传动原理,执行元件结构简单,结构上易于实现很大的工作压力,较大的工作空间和较长的工作行程,因此适应性强,便于压制大型工件或较长、较高的工件。
2)由于执行元件结构简单,具有灵活布置的特点,因此可以根据工艺要求进行多方位的布置以及多地点分散布置。
3)在行程的任何位置均可产生液压机额定的最大压力。
)活动衡量的总行程可以在一定范围内任意无极改变,行程的下转换点也4 可以根据工艺要求方便的控制和改变。
5)可以用不同阀的组合来实现工艺过程的不同程序,方便的适应程序的变化,便于实现程序控制及计算机自动控制。
6)工作平稳、撞击、振动和噪声较小,对工人健康、厂房基础、周围环境及设备本身都有很大好处。
由于液压机的液压系统和整机结构方面,已经比较成熟,国内外液压机的发展主要体现在控制系统方面。
微电子技术的飞速发展,为改进液压机的性能、提高稳定性、加工效率等方面提供了可能。
相比来讲,国内机型虽种类齐全,但技术含量相对较低,缺乏技术含量高的高档机型,这与机电液一体化,中小批量柔性生产的发展趋势不相适应。
在国内外液压机产品中,按照控制系统,液压机可分为三种类型:一种是以继电器为主控元件的传统型液压机;一种是采用可编程控制器控制的液压机;第三种是应用高级微处理器(或工业控制计算机)的高性能液压机。
液压压力机设计范文

液压压力机设计范文液压压力机是一种利用压力液体传递力和能量的装置。
它可以将液压系统的压力转化为机械动力,将压机活塞的压力传递到工件上,从而完成工件的加工、成形、压制等工作。
液压压力机具有结构简单、工作稳定、压力大、运行灵活、操作方便等优点。
液压压力机广泛应用于冶金、机械、造船、建筑、电力、核工业等各个行业。
在设计液压压力机时,需要考虑以下几个方面的因素:1.压力计算:设计液压压力机时,首先需要计算所需的最大压力。
根据工件的材料和形状,选择合适的压力级别。
同时还需要计算所需的液压缸的直径和活塞面积,以实现所需的压力。
2.结构设计:液压压力机的结构设计需要考虑机身、液压缸、工作台和传动系统等部分。
机身应具有足够的刚性和稳定性,以承受所需的工作压力。
液压缸的设计也需要考虑其尺寸和重量以及密封性能。
工作台的设计应根据具体工件的要求确定。
3.液压系统设计:液压系统是液压压力机的核心部分,主要包括液压缸、油泵、液压阀和液压管路等。
在设计液压系统时,需要考虑压力、流量、速度、回油和密封等因素。
选择合适的油泵和液压阀,以保证液压系统的工作效率和稳定性。
4.安全设计:液压压力机的安全性是设计中的重要考虑因素。
在设计过程中,需要考虑压力释放、紧急停机和过载保护等安全措施。
为了保证操作人员的安全,还需要在机身周围设置安全防护装置,避免事故的发生。
5.自动化设计:液压压力机的自动化设计可以提高生产效率和产品质量。
通过添加PLC控制系统和传感器,实现压力的自动调节和工作过程的监控。
同时还可以添加自动上料、下料和工件定位装置等,以进一步提高生产效率。
综上所述,液压压力机的设计需要考虑压力计算、结构设计、液压系统设计、安全设计和自动化设计等因素。
通过合理的设计,可以实现液压压力机的稳定工作和高效生产,满足不同工件加工的需求。
【文献综述】船用液压马达虚拟样机设计
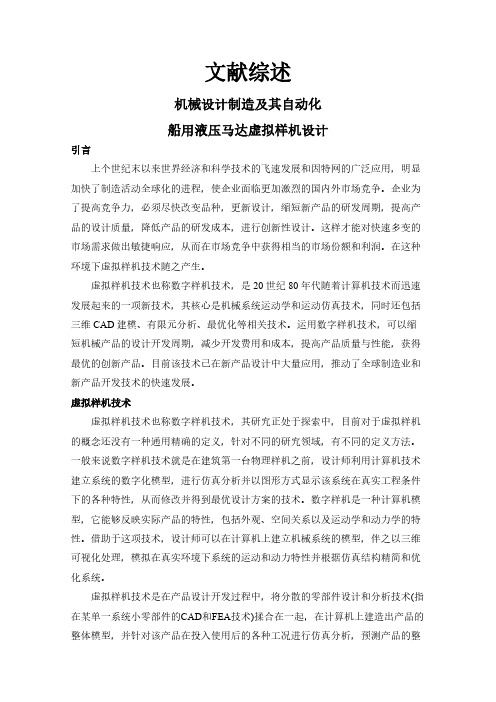
文献综述机械设计制造及其自动化船用液压马达虚拟样机设计引言上个世纪末以来世界经济和科学技术的飞速发展和因特网的广泛应用,明显加快了制造活动全球化的进程,使企业面临更加激烈的国内外市场竞争。
企业为了提高竞争力,必须尽快改变品种,更新设计,缩短新产品的研发周期,提高产品的设计质量,降低产品的研发成本,进行创新性设计。
这样才能对快速多变的市场需求做出敏捷响应,从而在市场竞争中获得相当的市场份额和利润。
在这种环境下虚拟样机技术随之产生。
虚拟样机技术也称数字样机技术,是20世纪80年代随着计算机技术而迅速发展起来的一项新技术,其核心是机械系统运动学和运动仿真技术,同时还包括三维CAD建模、有限元分析、最优化等相关技术。
运用数字样机技术,可以缩短机械产品的设计开发周期,减少开发费用和成本,提高产品质量与性能,获得最优的创新产品。
目前该技术已在新产品设计中大量应用,推动了全球制造业和新产品开发技术的快速发展。
虚拟样机技术虚拟样机技术也称数字样机技术,其研究正处于探索中,目前对于虚拟样机的概念还没有一种通用精确的定义,针对不同的研究领域,有不同的定义方法。
一般来说数字样机技术就是在建筑第一台物理样机之前,设计师利用计算机技术建立系统的数字化模型,进行仿真分析并以图形方式显示该系统在真实工程条件下的各种特性,从而修改并得到最优设计方案的技术。
数字样机是一种计算机模型,它能够反映实际产品的特性,包括外观、空间关系以及运动学和动力学的特性。
借助于这项技术,设计师可以在计算机上建立机械系统的模型,伴之以三维可视化处理,模拟在真实环境下系统的运动和动力特性并根据仿真结构精简和优化系统。
虚拟样机技术是在产品设计开发过程中,将分散的零部件设计和分析技术(指在某单一系统小零部件的CAD和FEA技术)揉合在一起,在计算机上建造出产品的整体模型,并针对该产品在投入使用后的各种工况进行仿真分析,预测产品的整体性能,进而改进产品设计、提高产品性能的一种新技术。
液压机的设计与分析

液压机的设计与分析摘要:随着我国制造业的快速发展,大型精密液压机的需求也随之快速增长,这也对生产设备精度、自动化程度和生产效率提出更高的技术要求。
本文通过对液压机系统的工作原理、液压机运转的设计思路、液压机的整体控制方案设计三方面进行分析,阐述了液压控制系统的变频器的设计、液压机工程分析、应用程序开发过程中的关键技术。
关键词:液压机设计分析工程1 液压系统的工作原理液压机的工作原理是由上、下滑块顶出机构的运动,上滑块机构由主液压缸也就是上缸来驱动,顶出机构由辅助液压缸也就是下缸驱动。
液压机上滑块通过四个导柱导向和主缸驱动,实现上滑块机构的驱动,详细驱动如下所示。
上缸的快速下行→上缸的慢速下行→上缸的慢速加压→上缸的预卸→上缸的慢速回程→上缸的快速回程→停止。
下缸一般布置在工作台的中间孔内,用来驱动下滑快的顶出机构,详细驱动瑞如下。
下缸的向上顶出→下缸的向下退回。
2 液压机运转的设计思路使用液压机前必须要仔细阅读分析液压机的使用手册。
在滑块的运行过程中,绝对不允许身体的任何部位进入危险区内,尽可能地防止人身伤害事故的发生。
液压机使用的电器元件都是有使用寿命的,如果达到了使用寿命,就必须要更换元件,以此来确保作业的安全。
非技术人员绝对不允许打开控制箱,以防止发生危险事故。
不能随便将电气箱门打开。
在对电气箱箱门进行开启时,首先要把箱门上的电源开关关掉,并让手柄和延伸杆脱开,然后才可以打开门锁。
滑块的封闭高度彻底调整完成以后,必须要把滑块调整开关关掉,这时机床才可以正常地进行冲压。
液压机床操作完成后,必须要看管好操作的按钮开关。
3 液压机的整体控制方案设计一般的液压机主要是用于小型机械零件冲压和定形的。
生产线把材料送入用液压机冲压成型,并经过输料线输出。
本液压机为可编程控制器控制。
由凸轮控制器发出液压机运转所需角度。
液压机的结构和功能描述如下。
300t的液压机一般使用刚性转键式离合器,这样可以在使用和维修时比较方便。
液压机的设计与分析

液压机的设计与分析摘要:随着我国制造业的快速发展,大型精密液压机的需求也随之快速增长,这也对生产设备精度、自动化程度和生产效率提出更高的技术要求。
本文通过对液压机系统的工作原理、液压机运转的设计思路、液压机的整体控制方案设计三方面进行分析,阐述了液压控制系统的变频器的设计、液压机工程分析、应用程序开发过程中的关键技术。
关键词:液压机设计分析工程1液压系统的工作原理液压机的工作原理是由上、下滑块顶出机构的运动,上滑块机构由主液压缸也就是上缸来驱动,顶出机构由辅助液压缸也就是下缸驱动。
液压机上滑块通过四个导柱导向和主缸驱动,实现上滑块机构的驱动,详细驱动如下所示。
上缸的快速下行→上缸的慢速下行→上缸的慢速加压→上缸的预卸→上缸的慢速回程→上缸的快速回程→停止。
下缸一般布置在工作台的中间孔内,用来驱动下滑快的顶出机构,详细驱动XXX如下。
下缸的向上顶出→下缸的向下退回。
2液压机运转的设计思路使用液压机前必须要仔细阅读分析液压机的使用手册。
在滑块的运行过程中,绝对不允许身体的任何部位进入危险区内,尽可能地防止人身伤害事故的发生。
液压机使用的电器元件都是有使用寿命的,如果达到了使用寿命,就必须要更换元件,以此来确保作业的安全。
非技术人员绝对不允许打开控制箱,以防止发生危险事故。
不能随便将电气箱门打开。
在对电气箱箱门进行开启时,首先要把箱门上的电源开关关掉,并让手柄和延伸杆脱开,然后才可以打开门锁。
滑块的封闭高度彻底调整完成以后,必须要把滑块调整开关关掉,这时机床才可以正常地进行冲压。
液压机床操作完成后,必须要看管好操作的按钮开关。
3液压机的整体控制方案设计一般的液压机首要是用于小型机械零件冲压和定形的。
生产线把材料送入用液压机冲压成型,并颠末输料线输出。
本液压机为可编程控制器控制。
由凸轮控制器发出液压机运转所需角度。
液压机的结构和功能描述如下。
300t的液压机一般使用刚性转键式离合器,如许能够在使用和维修时比较方便。
- 1、下载文档前请自行甄别文档内容的完整性,平台不提供额外的编辑、内容补充、找答案等附加服务。
- 2、"仅部分预览"的文档,不可在线预览部分如存在完整性等问题,可反馈申请退款(可完整预览的文档不适用该条件!)。
- 3、如文档侵犯您的权益,请联系客服反馈,我们会尽快为您处理(人工客服工作时间:9:00-18:30)。
一、课题国内外现状液压机是一种以液体为工作介质,用来传递能量以实现各种工艺的机器。
液压机是制品成型生产中应用最广的设备之一。
自19世纪问世以来发展很快,已成为工业生产中必不可少的设备之一。
由于液压机在工作中的广泛适应性,使其在国民经济各个部门获得了广泛应用。
四柱式(通用)液压机属于板料冲压液压机,这类液压机主要用于各种金属板料的冲压成型,包括落料、冲裁、拉伸、弯曲、翻边、精密冲裁等,还可以用于冷挤、校正、压装、粉末制品、磨料制品、塑料制品和绝缘材料的压制成型。
液压机由于具有以下多方面的优点,因此在很多领域得到广泛应用。
1)基于液压传动原理,执行元件结构简单,结构上易于实现很大的工作压力,较大的工作空间和较长的工作行程,因此适应性强,便于压制大型工件或较长、较高的工件。
2)由于执行元件结构简单,具有灵活布置的特点,因此可以根据工艺要求进行多方位的布置以及多地点分散布置。
3)在行程的任何位置均可产生液压机额定的最大压力。
4)活动衡量的总行程可以在一定范围内任意无极改变,行程的下转换点也可以根据工艺要求方便的控制和改变。
5)可以用不同阀的组合来实现工艺过程的不同程序,方便的适应程序的变化,便于实现程序控制及计算机自动控制。
6)工作平稳、撞击、振动和噪声较小,对工人健康、厂房基础、周围环境及设备本身都有很大好处。
由于液压机的液压系统和整机结构方面,已经比较成熟,国内外液压机的发展主要体现在控制系统方面。
微电子技术的飞速发展,为改进液压机的性能、提高稳定性、加工效率等方面提供了可能。
相比来讲,国内机型虽种类齐全,但技术含量相对较低,缺乏技术含量高的高档机型,这与机电液一体化,中小批量柔性生产的发展趋势不相适应。
在国内外液压机产品中,按照控制系统,液压机可分为三种类型:一种是以继电器为主控元件的传统型液压机;一种是采用可编程控制器控制的液压机;第三种是应用高级微处理器(或工业控制计算机)的高性能液压机。
三种类型功能各有差异,应用范围也不尽相同。
但总的发展趋势是高速化、智能化。
(l)继电器控制方式是延续了几十年的传统控制方式,其电路结构简单,技术要求不高,成本较低,相应控制功能简单,适应性不强。
其适用于单机工作、加工产品精度要求不高的大批量生产(如餐具、厨具产品等),其也可组成简单的生产线,但由于电路的限制,稳定性、柔性差。
现在,国内许多液压机厂家是以这种机型为主,使用对象多为小型加工厂,或加工精度要求不高的民用产品。
国外众多厂家只是保留了对这种机型的生产能力,而主要面向以下两种技术含量高的机型组织生产。
(2)可编程控制器是在继电器控制和计算机控制发展的基础上开发出来的,并逐渐发展成以微处理器为核心,把自动化技术,计算机技术,通讯技术溶为一体的新型工业自动控制装置。
目前已被广泛的应用于各种生产机械以及自动化生产过程中。
随着技术的不断发展,可编程序控制器的功能更加丰富。
早期的可编程序控制器在功能上只能进行简单的逻辑控制。
后来一些厂家开始采用微电子处理器作为可编程序控制器的中央处理单元(CPU),从而扩大了控制器的功能,使其不仅可以进行逻辑控制,而且还可以对模拟量进行控制。
因此,可编程控制器控制方式是介于继电器方式和工业控制机控制方式之间的一种控制方式。
可编程控制器有较高的稳定性和灵活性,但在功能方面与工业控制机相比有一定差异。
现在,国内有些厂家采用可编程控制器控制方式,如天津锻压机械厂有近60%的产品装有PLC。
通过采用PLC 控制,使系统的控制性能和可靠性大大提高。
国外厂家如丹麦的STENHOJ 公司采用了SIEMENS 的可编程控制器,实现对压力和位移的控制。
(3)工业控制机控制方式是在计算机控制技术成熟发展的基础上采用的一种高技术含量的控制方式。
这种控制方式以工业控制机或单片/ 单板机作为主控单元,通过外围接口器件(如A/ D,D/ A 板等)或直接应用数字阀实现对液压系统的控制,同时利用各种传感器组成闭环回路式的控制系统,达到精确控制的目的。
这种控制方式的主要特点如下:①具有友好的人机交互性,操作简单。
如:BROWNBOGGS 公司的产品,可通过数字面板显示输入压力、快进和回程速度、压制速度及保压/ 停机时间参数,极大减轻了劳动强度。
②控制精度高。
数字控制的行程长度及工作行程与传统的机械式的行程开关控制相比,精度有极大的提高。
一般控制精度可达到0.05mm[2]。
③易于实现高速化,提高生产效率。
如美国的FERRA 公司通过采用电子微处理控制方式,工作循环比以前快60%。
④可顺利实现对工作参数(压力、速度、行程等)的单独调整。
通过对控制参数的单独控制,调整被加工材料的流动,能进行复杂工件、不对称工件的加工。
⑤预存工作模式,可对不同工件的工艺过程、工艺参数预先存储和重复调用,缩短调整时间。
这与柔性加工要求相适应。
⑥对高速下的换向冲击可利用软件来消除,以降低噪声,提高系统的稳定性。
⑦在安全方面,可利用软件进行故障预诊断,并自动修复故障和显示错误。
如STENHOF 的机型和BROWN BOGGS 公司都有此项功能。
⑧易实现生产线的集成控制,组成柔性生产线及与上位机进行通讯和实现调度控制。
现在,国外众多液压机生产厂家生产这种高性能的工业控制机控制方式的液压机产品,如美国MULTIPRESS丹麦STENHOJ 及加拿大的BROWN BOGGS 等公司。
正是因为采用这种先进的控制方式,使整机的控制性能,生产效率都有很大提高。
而与国外发展情况相比,国内极少有采用工业控制机控制方式的产品,成熟的产品是采用可编程控制器(PLC)的控制方式。
作为液压机两大组成部分的主机和液压系统,由于技术发展趋于成熟,国内外机型无较大差距。
主要差别在于加工工艺和安装方面。
良好的工艺使机器在过滤、冷却及防止冲击和振动方面,有较明显改善。
在油路结构设计方面,国内外液压机都趋向于集成化、封闭式设计。
插装阀、叠加阀和复合化元件及系统在液压系统中得到较广泛的应用。
国外已开始广泛采用封闭式循环油路设计。
这种油路设计有效地防止泄油和污染。
更重要的防止灰尘、污物、空气、化学物质侵入系统,延长了机器的使用寿命。
由于加工工艺等方面的原因,国内采用封闭式循环油路设计的系统还不多见。
在安全性方面,国外某些采用微处理器控制的高性能液压机利用软件进行故障的检测和维护,如BROWNBOGGS 产品可实现负载检测、自动模具保护以及错误诊断等功能。
二、研究主要成果早在1662年,帕斯卡就发现了利用液体产生很大力量的可能性,1795年,英国人Bramah取得了第一个手动液压机的专利,但真正液压机的发展历史不到200年。
随着西方资本主义的发展,蒸汽机的发明,引发了工业革命,具有悠久历史的锻造工艺也逐步由手工锻造转变为机器锻造。
16世纪初,出现了第一批水利机械锤。
1893年,第一台蒸汽锤出现。
此后,伴随着机械工业的发展,锻件尺寸越来越大,锻锤已做到落下部分超过100吨,如此笨重的锤,操作困难,振动十分巨大。
1859~1861年在维也纳铁路工厂有了第一批用于金属加工的7000KN,10000KN,和12000KN的液压机。
1884年,英国曼彻斯特首先使用了锻造钢锭用的锻造水压机,与锻锤相比,运动部件不必那么重,振动又小,发展很快。
在1887~1888年间,制造了一系列锻造水压机,其中包括一台40000KN的大型水压机。
1893年,建造了当时最大的120MN锻造水压机。
1934年,德国制造了70000KN模锻水压机;1938~1944年之间,为了第二次世界大战的需要,又相继制造了三台150MN的锻造水压机和一台300MN的大型模锻水压机。
美国在1955年左右先后制造了两台315MN及两台450MN的大型模锻水压机。
苏联则在20世纪50年代中期到60年代初期,先后建造了几台300MN模锻水压机以及世界上最大的750MN模锻水压机。
此外,在英国、法国、联邦德国也都先后建造过200~300MN的各种大型模锻液压机。
1976年,在法国投产了西欧最大的650MN 模锻液压机。
液压机发展到现在,已经广泛应用于国民经济的各个部门,种类繁多,发展迅速,成为机床行业的一个重要组成部分。
在我国,液压行业的发展仅仅有50年左右。
1957~1958年,我国开始自行设计,自行制造25000KN的中型锻造水压机。
20世纪60年代初期,在我国的上海和东北,又各自建立了一台120MN级的大型锻造水压机。
中、后期,我国又先后成套设计并自行制造了一批技术要求更高的大型液压机,其中包括300MN有色金属模锻液压机,120MN有色金属挤压液压机,80MN黑色金属模锻水压机。
20世纪70年代,我国已开始向国外出口了多台各种吨位的锻造液压机。
其中最大的一台为60MN锻造水压机。
至此,我国的液压机设计与制造行业,已经达到了相当高的水平。
三、发展趋势:(l)高速化,高效化,低能耗。
提高液压机的工作效率,降低生产成本。
(2)机电液一体化。
充分合理利用机械和电子方面的先进技术促进整个液压系统的完善。
(3)自动化、智能化。
微电子技术的高速发展为液压机的自动化和智化提供了充分的条件。
自动化不仅仅体现的在加工,应能够实现对系统的自诊断和调整,具有故障预处理的功能。
(4)液压元件集成化,标准化。
集成的液压系统减少了管路连接,有效地防止泄漏和污染。
标准化的元件为机器的维修带来方便。
四、存在问题1)液压元件制造精度要求高由于元件的技术要求高和装配比较困难,使用维护比较严格。
2)实现定比传动困难液压传动是以液压油为工作介质,在相对运动表面间不可避免的要有泄漏,同时油液也不是绝对不可压缩的。
3)油液受温度的影响由于油的粘度随温度的改变而改变,故不宜在高温或低温的环境下工作。
4)不适宜远距离输送动力由于采用油管传输压力油,压力损失较大,故不宜远距离输送动力。
5)油液中混入空气易影响工作性能油液中混入空气后,容易引起爬行、振动和噪声,使系统的工作性能受到影响。
6)油液容易污染油液污染后,会影响系统工作的可靠性。
7)发生故障不易检查和排除。
五、主要参考文献[1].俞新陆.液压机的设计与应用.机械工业出版社,2006.12[2].雷天觉.新编液压工程手册.北京:北京理工大学出版社,1998[3].成大先.机械设计手册.北京:化学工业出版社,1997[4].宋学义.袖珍液压气动手册.机械工业出版社,1995[5].张利平.液压控制系统及设计.北京:化学工业出版社,1997[6].张利平.液压气动系统设计手册.北京:机械工业出版社,1997[7].张利平.现代液压技术应用220例.北京:化学工业出版社,2004[8].官中范.液压传动系统.北京:机械工业出版社,1981[9].路甬祥.液压气动技术手册.北京:机械工业出版社,2002[10].李贵闪, 何晓燕, 荣兆杰.我国液压机行业的现状及发展.合肥锻压机床技术有限公司,2006[11].王孝培.冲压手册.北京:机械工业出版社,1988.[12].宋丽华,毛君.四柱式液压机液压系统设计.辽宁工程技术大学机械工程学院,2009[13].俞新陆,杨津光.液压机的结构与控制.北京:机械工业出版社,1989[14].天津锻压机床厂.中小型液压机设计计算.天津:天津人民出版社,1977[15].王卫卫. 金属与塑料成型设备. 机械工业出版社,1996第一版。