铜带热轧机无芯上卷取机的改造
带钢可逆冷轧卷取机兼作开卷机的改造

增加 自 动对中装置和功能 , 确保带钢卷取整 齐。其 次, 增设轧机的摆动导 向辊等装置 , 方便开卷穿带 , 节省 时 间人力 。
显然 两种 技 改 方 案 差别 很 大 、 有 优 劣 。第 一 各
种方案技术先进 、 成熟和可靠 , 但是设备多、 投资大 、 占地多。全套 自 动对中开卷机组 , 包括有上卷小车 、
S L n —i U i g x
( inN nfr u tlryD s nadR sac tue, in7 0 0 , hn ) X k o- r s aug ei n eerhI i t X h 10 1C ia e o Me l g Nst
Ab t a t n v e fi c n i in e i t p t r a i ga d u s a y e si p r t n f r h od sr l a d c i rd u l sr c :I iw o o vn e c n sr e dn n n t d n s o e ai o e c l t p mi n ol o b e n i h e n o t i l e
部 电气控 制 系统 ; 外增 加 1台相 同的 自动 对 中开 另 卷机 取代 开 卷箱 , 并且 配备 上卷小 车 。 第二 种 技改方 案 : 主要 改造 酸洗卷 取机 等设备 ,
程度和张力大小 等等。因此 , 酸洗机组卷取 区段适 当增 加对 中立辊 数量 和调 整 对 中立 辊位 置 ; 高卷 升
2 技 术 改造 方 案 的 比较 选择
已有 的 闲置 开卷 机组设 备 和不相 匹配 的现 用开
持和带钢“ 跑偏 ” 的随动 , 从而保证卷取带 钢边缘能
够 始终对 齐 。
实际上 , 自动 对 中 卷 取 机 的 上 述 对 中 功 能 即
热轧卷取机设计

热轧卷取机设计简介热轧卷取机是用于将热轧板材定尺卷成卷材的设备。
在钢铁工业中,热轧卷取机起着至关重要的作用,它能够实现快速高效的卷取过程,为后续的加工提供了便利。
本文将对热轧卷取机的设计进行详细介绍。
设计要求在进行热轧卷取机的设计时,需要考虑以下几个方面的要求:1.卷取速度:热轧卷取机需要具备较高的卷取速度,以满足生产需求。
2.卷取精度:热轧卷取机需要保证卷取的板材能够达到一定的卷取精度,以提高生产效率。
3.卷取力:热轧卷取机需要具备足够的卷取力,以确保板材能够被紧密卷取。
4.自动化程度:热轧卷取机需要具备一定的自动化程度,减少人工操作。
设计方案卷取速度为了实现较高的卷取速度,可以采用以下设计方案:1.采用高功率的电动机驱动卷取器,提供足够的动力。
2.优化传动系统的设计,减少能量损失。
3.使用较轻的材料制造卷取器,减小惯性负载。
4.优化卷取材料的过程控制,减少卷取过程中的阻力。
卷取精度为了保证卷取的精度,可以采用以下设计方案:1.采用闭环控制系统,结合传感器实时监测卷取过程,并根据监测数据进行反馈控制。
2.优化卷取机的结构设计,减少运动过程中的震动和变形。
3.使用高精度的滚轮和轴承,减小运动过程中的摩擦。
卷取力为了确保足够的卷取力,可以采用以下设计方案:1.采用高功率的液压系统,提供足够的液压力。
2.优化液压系统的设计,减小能量损失。
3.使用高强度的材料制造卷取器,增加卷取力的传递效率。
自动化程度为了提高热轧卷取机的自动化程度,可以采用以下设计方案:1.采用PLC控制系统,实现自动化控制。
2.加装自动化传感器,实现自动检测和自动调节。
3.结合网络技术和远程监控,实现远程操作和监测功能。
结论本文对热轧卷取机的设计进行了详细介绍,包括卷取速度、卷取精度、卷取力和自动化程度等方面的设计要求和设计方案。
通过优化设计,可以提高热轧卷取机的卷取效率和生产质量,满足钢铁工业中对高效卷取的需求。
同时,也为后续的热轧卷取机的研发和生产提供了参考。
邯钢冷轧重卷线开卷机芯轴改造方案探讨

邯钢冷轧重卷线开卷机芯轴改造方案探讨发布时间:2022-11-27T06:00:27.771Z 来源:《科学与技术》2022年15期作者:高永杨哲[导读] 通过对重卷线开卷机芯轴工作原理、设备结构、使用中产生问题进行了分析,找出问题产生的根本原因,提出改造技术方案,对改造方案进行分析,若实施后,将有效延长了开卷机芯轴拉杆使用时间,减少了故障对生产影响,降低了备件使用费用。
高永杨哲(邯郸钢铁股份有限责任公司冷轧厂,河北邯郸 056001)摘要通过对重卷线开卷机芯轴工作原理、设备结构、使用中产生问题进行了分析,找出问题产生的根本原因,提出改造技术方案,对改造方案进行分析,若实施后,将有效延长了开卷机芯轴拉杆使用时间,减少了故障对生产影响,降低了备件使用费用。
关键词冷轧重卷开卷机芯轴一、概述邯钢重卷线是由美国吉森总公司设计,融合了当今世界最先进的板带剪切及矫直技术。
关键设备进口及其它设备国内制作,年设计产量28万吨/年,机组生产速度380m/min(最高速度),来料厚度0.3-2.mm,钢卷外径1500-2000mm。
该机组主要设备由开卷机、焊机、张力辊、拉矫机、活套、切边剪、涂油机、卷取机等主要设备及附属公辅设备组成,开卷机是产线关键设备,主要功能是接收钢卷,并对钢卷进行开平,在生产过程中提供张力。
二、开卷机的结构和工作原理开卷机是接收钢卷并将其喂入生产线。
开卷机是悬臂膨胀卷筒式,从钢卷小车接收钢卷并为生产线开卷,开卷方式为上下开卷式。
带有滑动机座将钢卷与生产线对中。
压辊用来辅助穿带。
齿轮箱齿轮用材质为40CrNiMO材料加工件。
开卷机滑动底座钢结构,有横移液压缸根据板带中心位置随动,滑轨配有可更换青铜衬板,滑轨座在主机座上。
开卷机压辊的钢辊带聚氨酯涂层,带50mm宽底拆带槽。
由液压马达驱动,以适应上开卷。
用一个由电磁阀控制的液压缸升降,行程从钢卷的最大外径到卷筒的直径。
开卷机芯轴卷筒由4块膨胀式铸钢扇形块组成,带有相互啮合的蛇形边缘,青铜膨胀楔块和一根45号钢制作芯轴。
安钢炉卷轧机卷取轧制和控制改进

S e k e mi n A y n t e. C u e a ay i n mp o e n swee c rid o t o h x s n l t c c n rlp be . t l l i n a g S e 1 a s n l ssa d i rv me t r a r u rte e it g ee r o t r l ms c l e f i c i o o
重要 ( 1 。 图 )
( 引导钢板进出卷曲炉) I ;热检 ; 高温计。 J
2 2 卷 取轧 制工艺 .
安 钢炉卷 轧机 在 卷 轧 生 产时 , 轧 道 次 采 用 平 粗 轧, 当带钢厚 度 小 于 2 n 时 , 行 卷 取 工 艺 轧 制 5r m 进
过程 。
穿 带过程 : 钢进轧 机前 , 取侧 穿带 板 和裙板 带 卷 分别下 降 和升起 、 卷筒定 位槽 口对 准 导板 , 夹送 辊 卷 辊缝控 制在 带钢 厚度 +10m 的位 置 , 送辊 和 偏 5 m 夹
1 引 言
安钢炉卷轧线是 引进达涅利技术和关键设备 , 选用 T I M C自动化控制 的一条具有 国际先进水平 的 板材 生产 线 , 计 能力 10万 ta 产 品规 格 :. 设 1 /, 4 5—
5 i ×( 0 32 0 im×( 0 0m l 1 0— 0 )n l 6 60 0—1 0 ) 8 0 mm。 0
2 炉 卷 轧 机 卷取 设 备和 卷 轧 工 艺
2 1 炉卷 轧机 主要卷 取设 备及 功能 .
图 I中 , A为卷取 炉 ( 取 轧制模 式下 通 过卷 取 卷 钢板以保持其温度) B为卷筒 ( ; 卷取钢板 , 并与主 轧机或夹 送辊 形成 张 力 ) C为偏 导 辊 ( 夹 送 辊 和 ; 在 卷 筒之 间 以减少 带 钢 的振 动 ) D为 夹送 辊 ( 送 钢 ; 夹 板并 与 主轧机 、 卷筒形 成 张力 ; 少 带钢 振动 ) E为 减 ; 立辊轧 机 ; 主轧 机 ; F为 G和 H分 别 为穿 带 板 、 板 裙
1500轧线卷取机交流变频改造word精品文档6页

1500轧线卷取机交流变频改造前言银山型钢板带厂1#卷取机卷筒由两台功率为N=320kW,转速n=360/900r/min的直流电机通过中间联轴器及变速齿轮箱传动。
如果卷筒中两台直流电机不同步或者现场的检测设备简陋导致张力计算不够准确,直接会产生一系列严重的问题。
1、现状分析1.1卷取机卷筒中两台直流电机之间的中间联轴器易损坏如果卷取机卷筒中两台直流电机中的一台直流电机出现故障不能正常运行,而另一台直流电机以正常转速运行,两台直流电机的转速不一致,从而导致它们的中间联轴器被扭环。
1.2卷取机的维护费用高、工人劳动强度大由于卷取机卷筒中两台直流电机的速度存在着匹配问题,如果出现故障它们的中间联轴器容易被损坏,我们得及时更换中间联轴器。
每月需对卷筒电机进行4~5次维护工作,每次维护工作至少需要2~3小时。
每月不仅增加了维护费用的支出,而且增大了工人的劳动强度。
1.3卷取机的张力不够,卷钢时易造成拉钢和堆钢现象系统卷取张力通过自动化TDC 控制器控制,现场的激光检测器检测到带钢后,测出带钢的直径,这样测出的直径数值不精确,利用直径根据公式计算出卷取张力,这样计算出的张力不准确,在轧制直径为1500―1900 mm 的带钢时,往往会因为卷取机的张力不够会造成拉钢和堆钢现象。
2、改造措施2.1基本描述:双绕组交流变频异步电动机传动控制系统采用西门子原装6SE70系列12相整流回馈单元加四象限工作逆变器的交-直-交控制方式[1]。
整流回馈装置进线柜设框架断路器,过电压保护。
两个整流回馈单元构成12相的公共直流母线。
每个整流回馈单元配进线电抗器及自耦变压器。
异步电动机的双绕组分别由两台逆变器供电,进行主从控制。
主逆变器中配带卷绕控制软件工艺模板T400,实现基于最大力矩原则的间接张力控制,完成系统的张力控制,卷径计算和动态过程中的力矩补偿,断带保护等功能。
每个逆变器输出侧安装出线电抗器。
采用矢量控制方式的逆变器不仅可在调速范围上与直流电动机相匹配,而且可以控制异步电动机产生的转矩,同时逆变器变频器中具备异步电动机参数自动检测、自动辨识、自适应功能,可以自动地对异步电动机的参数进行辨识,并根据辨识结果调整控制算法中的有关参数,从而满足卷取电机基速以下恒转矩、基速以上恒功率的调速要求。
热轧带钢设备的创新改进介绍

热轧带钢设备的创新改进介绍作者:耿进财来源:《科技创新与应用》2015年第25期摘要:随着我国房地产事业的不断快速发展,我国对于钢材的需求也在变的越来越多,随着各式各样的型材的不断的需求,我国的热轧带钢产业也得到了快速的发展,相比较而言,对热轧带钢的生产设备的制造水平和设计技术也有了更高的要求。
文章就是针对生产热轧带钢的相关设备来进行介绍,系统的分析和研究热轧带钢的生产设备的相关问题。
关键词:热轧带钢;生产设备;创新技术;工艺方法1 热轧带钢的相关简要介绍热轧带钢的生产设备热轧机在我国已经有着近七十年的发展历史,七十年的发展主要是从提高生产效率和提升产品的生产尺寸的精度入手,同时也相应了国家关于环保的要求号召,生产出了节能又环保的热轧机设备,这样就使热轧设备的投入降低,让热轧线的长度下降,进而实现了热轧机设备的跨越发展,从紧凑化的热轧机设备发展到了热连轧机设备及热铸轧机设备。
不同的时期,热轧机设备的发展不尽相同,下面就详细了介绍了热轧机的发展历程。
第一个时期的热轧机的发展在上世纪六十年代前。
这时的我国第一代热轧机设备刚刚研制出来,这种热轧机设备的创新点在于将厚度自动控制的先进技术应用到了热轧机设备中,精确的控制了热轧机设备生产的钢板的厚度。
第二个时期的热轧机的发展在上世纪七十年代。
这时的我国第二代热轧机设备已经研制成功,这种第二代热轧机设备的创新点在于已经非常娴熟的将连铸技术应用在了热轧机设备生产中。
第三个时期的热轧机的发展是在上世纪八十年代。
这时的热轧机设备虽然没有研制出第三代的热轧机设备,但是对于第二代的热轧机设备进行了全方位的改良创新,这一时期我们把板带的钢板形控制相关先进技术应用在了研制热轧机设备中,更加的注重钢板的生产质量,提高了钢板的生产产量。
第四个时期的热轧机的发展在上世纪的九十年代。
这时期的热轧机设备主要是引进了日本的先进无头连续轧制技术,将这一先进的技术应用在了我国的热轧机的设备研制之中,给热轧机设备的生产钢板的生产工艺带来了飞跃的提升。
概述1880热轧机组卷取机导尺改造
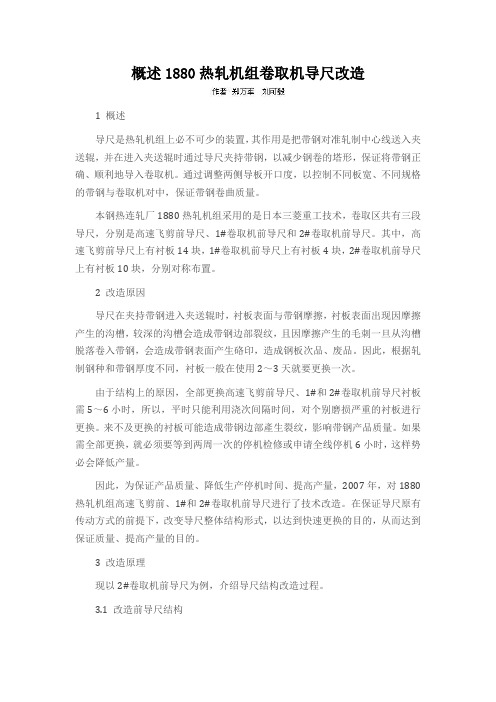
概述1880热轧机组卷取机导尺改造1 概述导尺是热轧机组上必不可少的装置,其作用是把带钢对准轧制中心线送入夹送辊,并在进入夹送辊时通过导尺夹持带钢,以减少钢卷的塔形,保证将带钢正确、顺利地导入卷取机。
通过调整两侧导板开口度,以控制不同板宽、不同规格的带钢与卷取机对中,保证带钢卷曲质量。
本钢热连轧厂1880热轧机组采用的是日本三菱重工技术,卷取区共有三段导尺,分别是高速飞剪前导尺、1#卷取机前导尺和2#卷取机前导尺。
其中,高速飞剪前导尺上有衬板14块,1#卷取机前导尺上有衬板4块,2#卷取机前导尺上有衬板10块,分别对称布置。
2 改造原因导尺在夹持带钢进入夹送辊时,衬板表面与带钢摩擦,衬板表面出现因摩擦产生的沟槽,较深的沟槽会造成带钢边部裂纹,且因摩擦产生的毛刺一旦从沟槽脱落卷入带钢,会造成带钢表面产生硌印,造成钢板次品、废品。
因此,根据轧制钢种和带钢厚度不同,衬板一般在使用2~3天就要更换一次。
由于结构上的原因,全部更换高速飞剪前导尺、1#和2#卷取机前导尺衬板需5~6小时,所以,平时只能利用浇次间隔时间,对个别磨损严重的衬板进行更换。
来不及更换的衬板可能造成带钢边部產生裂纹,影响带钢产品质量。
如果需全部更换,就必须要等到两周一次的停机检修或申请全线停机6小时,这样势必会降低产量。
因此,为保证产品质量、降低生产停机时间、提高产量,2007年,对1880热轧机组高速飞剪前、1#和2#卷取机前导尺进行了技术改造。
在保证导尺原有传动方式的前提下,改变导尺整体结构形式,以达到快速更换的目的,从而达到保证质量、提高产量的目的。
3 改造原理现以2#卷取机前导尺为例,介绍导尺结构改造过程。
3.1 改造前导尺结构2#卷取机前导尺总长4.75m(见图1),两侧导尺各有5块衬板对称安装在导板体上。
衬板为上下两侧对称,衬板的单侧磨损后需被卸下,换到对面的导尺上使用另一侧。
图1 2#卷取机前导尺图2 原导尺结构图每块装有衬板的导板体被“T”型拉紧螺栓拉紧后固定在导尺上(见图2)。
1500mm铜板带热轧机换辊装置改造

1500mm 铜板带热轧机换辊装置改造摘要:介绍了铜板带热轧机的组成。
重点阐述了对国内某铜板带加工厂1500mm热轧机的换辊装置的改造方案及项目施工成果。
改造后,解决了原有的换辊装置刚性不足,极大地减少了换辊时间及工人的劳动负荷,提高了生产效率。
关键词:铜板带加工;1500mm铜板带热轧机;换辊装置改造前言目前,国际上铜板带加工厂发展迅速,加工设备的大型化、现代化、规模化成为世界铜板带加工项目建设追求的目标。
我国铜板带加工行业起步较晚,现代化程度低于国外同行业,但是近些年来已开始高速发展。
现今,我国的铜板带加工行业已经开始采用大锭加热、提高卷重与板宽,从而提高生产效率和成品率。
在增加带长与带宽的同时,采用配备自动对中、液压压下、高效的工艺润滑和在线检测装置,保护气氛退火设备,高精度的清洗设备及分切设备。
从而保证产品机械性能稳定均匀、表面质量好、尺寸精度高。
在铜板带加工设备中,热轧机又是极为关键的设备。
它承担着铜板带轧制过程中绝大部分的变形量。
同时,在现代化的企业中,对热轧生产线的精度及生产效率得要求也越来越高。
热轧机由牌坊、辊系装配、轧制线标高调整装置、上辊电动压下及AGC压下装置、主传动装置、接轴轴套夹紧装置及换辊装置等组成。
本文主要针对1500mm铜板带热轧机的换辊装置相关内容进行论述,对于其他的设备本文不再赘述。
1项目背景在铜板带加工设备中,热轧机为其关键设备。
辊系又为整个热轧轧机的核心。
轧辊在使用一段时间后,轧辊表面会产生缺陷,需要更换后下线将缺陷层修磨掉。
由于高精度宽幅热轧机的辊系重量大、精度要求高,换辊装置的好用与否直接影响到整个热轧生产线的生产效率。
目前大多数的企业采用的是自动或半自动的换辊装置。
国内某铜加工企业年产10万吨高精度宽幅铜板带项目中,1500mm铜板带热轧机换辊装置采用的是半自动换辊,具体配置见图1图1 原换辊装置简图其换辊动作顺序如下:1.轧机停机,将上辊落下,放置于下辊上;2.序号4(机内升降轨道)升起,带动整个辊系上升,同时序号4(机内升降轨道的上表面与序号2(机外固定轨道)的上表面齐平;3.序号1(推拉油缸)伸出,人工使用销轴将油缸前端与下辊换辊钩子连接;4.序号1(推拉油缸)缩回,将旧辊拉出轧机本体;5.使用天车将旧辊吊走,将新辊吊运至轧机前合适位置;6.与抽旧辊相反的动作顺序将新辊装入轧机。
- 1、下载文档前请自行甄别文档内容的完整性,平台不提供额外的编辑、内容补充、找答案等附加服务。
- 2、"仅部分预览"的文档,不可在线预览部分如存在完整性等问题,可反馈申请退款(可完整预览的文档不适用该条件!)。
- 3、如文档侵犯您的权益,请联系客服反馈,我们会尽快为您处理(人工客服工作时间:9:00-18:30)。
第39卷第3期2010年6月有色金属加工NONFERROUSMETALSPROCESSINGVOI.39No.3June2010
铜带热轧机无芯上卷取机的改造陆辉(金威铜业设备科,安徽铜陵,244000)
摘要:文章从多方面介绍了铜带热轧机无芯上卷取机的技术改造,包括上卷取机的机械结构及其速度控制、三辊预弯装置辊缝预设定、6RA70直流调速器参数设定以及2台S7—300问的数据通讯等。通过技术改造,提高了生产效率,减少了天然气、水、电等能源介质的单耗。同时文章也总结了技术改造中存在的不足。关键词:元芯上卷取;6RA70控制器;三辊预弯中图分类号:TG335文献标识码:A文章编号:1671—6795(2010)03—0043—04
我公司步进炉一热轧机一铣面机生产线用于将最大厚度为250ram的铜铸锭由步进式加热炉从常温加热到750—900气,再由热轧机进行热轧开坯,得到厚度在13ram左右的带材,之后直接由铣面机进行在线面铣和边铣,并卷取成卷后为下道工序提供来料。热轧机在设计制造之初,公司从减少投资、加快建设进度的角度考虑,同时认为热轧后的板材不经卷取直接铣面,可以减少工序,降低能耗,因此上卷取机只完成了机械设计,未进行制造及安装调试。经过两年多的实际生产。发现这种工艺存在以下问题:①三台设备联机生产,可靠性大大降低,任何一台设备发生故障,整条生产线要全部停机等料。特别是步进炉在等料的时间里燃气用于保温,浪费严重;同时频繁的升温降温,对炉体及耐火材料的寿命非常不利。②铣面机为了带材剪尾需停机一次,由此产生的铣刀痕在下道工序无法消除,影响产品质量。③产量受限,能源消耗大。铣面机正常铣削速度只有10m/s,单根铸锭从步进炉出炉到铣面成卷约需30一35分钟,生产效率低。因此,公司决定在热轧机和铣面机之间安装一台无芯上卷取机,热轧后的带材由上卷取机卷取后为铣面机提供来料。电气部分的设计、安装和编程调试由公司设备科承担。1热轧机自动化配置示意图S7—300PLC、3台操作电脑、1台OPT面板以及Siemens公司6RA70直流调速器和现场传感器组成,用以执行生产线所有设备的顺序、联锁和其他控制功能。HMI的界面基于分层菜单系统,操作人员可通过HMI完成对设备进行操作、监控。同时一级系统以近乎实时的方式将生产数据和内部计算数据传送至二级系统。二级系统由2台服务器、2台工程师站和1台打印机组成,包括在数据库中存储产品和质量数据、道次表管理以及从三级系统下载新道次表的功能。见图1。
图1自动化系统配置示意图整条生产线的一级控制系统由3套siemen。司的2上卷取机区域机械示意图
收稿日期:2009—09一02在图2中,①入口导卫辊,②人口夹送辊,③三辊预弯装置,④三辊预弯装置液压马达,⑤三辊预弯装
万方数据有色金属加工第39卷置液压缸,⑥边部导卫,⑦卸料小车,⑨卸卷器。长8m、厚250ram、温度高达850℃的铸锭经过热轧后,长度延展为150m,厚度减薄为13ram,经过冷却水在线冷却后温度低于400C,由辊道电机驱动,进入上卷取机区域。首先由入口导卫辊①进行对中,在卷取过程中入口导卫辊①同时还起着夹持作用。上卷取电机经变速箱减速后再经过分配箱同时驱动入口夹送辊②和三辊预弯装置③,其余辊子由皮带传动。带卷经过入口夹送辊②后,下夹送辊液压缸向上运动,将带材夹紧,在卷取过程中起协助带材向前运动的作用。三辊预弯装置③的辊缝,即上下辊间的重叠量,由操作人员人工设定,其中液压缸⑤用于粗调,液压马达④用于精调。当带卷通过三辊预弯装置③时,带材被弯曲成直径750ram左右的圆形,并层层相压,直到卷取过程结束。在卷取过程中,边部导卫⑥的宽度与人口导卫辊①的宽度保持一致,保证料卷有良好的塔形。最后由卸卷器⑨通过左右和上下运动将料卷吊运至卸料小车⑦上,并由卸料小车⑦将料卷摆放在指定的料台。圈2上卷取机区域机械示意围3三辊预弯装置辊缝的预设定
在卷取前,三辊预弯装置辊缝的设定,即上辊与下辊之间的重叠量8的计算对卷取半径至关重要。如图3所示,三只预弯辊A:、A,、A‘直径均为228mm,下辊A,和A.之间的距离固定为260.2ram,假设B点为A,A.的中点,如果要求厚度h=13ram的带材成卷直径币^I=750mm,则有:
削3二辊敞写裘置辊缝坝设足已知:A3B:下A3A4:130.1mm;
AlA3:挈“+华:375+13+114:502mmAIA2:挈一挈:375.114:26lmm则有:sin小硒A3B=等=0.259cosAI=0.966A:A,=扣i万百虿互i啊i百石面=258.8ramA2B=肛忑可=223.7mm
最终可得8=A2B一中^2一①^3=-4.3mm三辊预弯装置在操作侧安装有MTS公司的磁致伸缩位移传感器,可精确测量下辊的位移,操作人员通过对下辊液压缸和液压马达的操作。可以得到想要的重叠量8。
4卷取机速度控制及其与热轧机的数据交换
万方数据第3期有色金属加工45图4卷取机速度控制原理框图图4中Ref为速度设定值,PB+和PB一为加减速按钮,8为每次有效按压加减速按钮后速度的增加或减少值,卷取机点动速度为12mpm,经过限幅器,将其速度限制在5—45mpm之间;再经过速度斜坡发生器、速比转换、旋转方向控制,最终6RA70直流调速器获得速度给定值。由于在卷取过程中需要辊道电机与卷取机同步旋转,协助将带材送向卷取机,因此需要在主轧机S7—300和卷取机区域S7—300之间建立数据通讯。如图l所示,2套PLC通过CP343模块一RJ45线一HuB一光纤转换器一光纤一光纤转换器一HUB—RJ45线一CP343模块的方式来完成硬接线。在NetPro中组态,建立2套PLC之间的ISO—on-TCP连接;在程序中建立通讯专用Fc块,使用专用功能块AGSEND和AGRECV完成数据的发送和接收。在AGSEND块中可将上卷取机电机的实际转速发送到主轧机PLC,作为辊道电机的速度给定值,使其速度与上卷取电机相匹配。辊道电机速度跟随上卷取机速度有诸多前提条件,如轧机主电机速度为零、机前和机后高温计未检测到高温铸锭、主机不在进行轧制等,在程序中必须建立完善的逻辑条件封锁,确保安全。5上卷取电机工作原理上卷取电机直流调速器选用Siemens公司的6RA7081—6DV62—0,其中端子37为合闸命令,端子38为使能信号,其速度给定、电流限幅、实际转速和实际电流等数据均通过PROFIBUS—DP总线与CPU315—2DP通讯,定期进行数据交换。直流调速器的参数设定可通过工程师站,使用DRIVERMONITOR软件来完成,主要参数值如表1所示。如图5所示,当调速器单机容量远小于所在电网变压器的短路容量时,选用进线电抗器可以降低电网中设备与调速器之问的相互影响,降低谐波电流。而选用输出电抗器,可以在不增加变频器容量等级的情况下解决容性充电电流对调速器的影响。表1直流调速器参数设定
图5上卷取电机原理图万方数据46有色金属加工第39卷
6不足与缺陷经过多次生产,也暴露出改造存在的不足:①部分辊子由皮带传动,在卷取后期,卷外径越来越大,卷材越来越重,用于部分辊子传动的皮带负载越来越大,容易产生皮带打滑,甚至断裂。为了保证连续生产,只有限制卷取速度不得超过25m/rnin,现已计划将皮带传动改为链条传动。②三辊预弯液压缸分传动侧和操作侧共2只,共用一个阀台和进出油管。在重负荷的情况下,油缸有轻微内泄,而位移传感器只安装在操作侧,无法测得传动侧下辊的精确位置,导致有时三辊预弯装置辊缝不平行,对卷材塔形不利。③铸锭经热轧成带材后,由于不同成分的合金在不同的终轧温度时。其弹性回复不同,而热轧机出口没有测量带厚的传感器,故控制系统无法得知终轧后的带材的厚度,所以三辊预弯装置的重叠量无法由控制系统自动计算后得到。预弯辊的辊缝定位完全由操作工的经验来设定,无法自动摆辊缝。④侧导卫板的强度不够,一旦出现辊缝不平行、卷材严重侧弯等情况,侧导卫板不能很有效地保证工位,对成卷带材塔形不利。
7总结
改造结束后,经过多次生产,证明改造效果良好。卷取时间不超过6分钟,铸锭从出炉、热轧到卷取成卷,耗时约18分钟,相比以前的联机铣面工艺而言,平均每根铸锭可节约12分钟左右,效率大大提高,天然气、水、电吨耗均大幅下降,卷取塔形小于Icm,卷取内径为750±2。
ReconstructionofMandrellessUpcoilerofCopperStripHotRollingMill
LUHui(JinviCopperequipmentdivision,Tongling,Anhui,244000,China)
Abstract:Thearticleintroducesthereconstructionofmandrellessupcoilerofcopperstriphotrollingmill,Includingmechanicalstructureandspeedcontroloftheupcoiler,presettingof3roilsprebendingdevice,parametersettingof6RA70DCconverter,
thedatacommunicationsbetweenS7・300s.Afterthereconstruction.theplantincreasedproductefficiencyandreducedtheconsumptionofnaturalgas,water,electricity,etc.Ontheotherhandthisarticlealsosummarizesthedeficiencyofthisreconstruction.Keywords:mandrellessupcoiler;6RA70converter;3rollsforprebender
(上接第62页)是,为了减小开销,设置一个时钟任务用来管理大部分的时间管理工作,为系统提供时钟服务,让时钟滴答中断做比较少的工作。上面所述的时钟管理功能,被分为两个部分的工作,一部分在时钟中断处理,有点类似于时钟管理的预处理;另一部分在时钟任务中完成。当定时器硬件发出中断信号后,立即中断当前任务的运行,按时钟中断向量转入内核的时钟中断处理程序。首先是关中断,把任务被中断时CPU的所有寄存器,保护在当前运行任务的TcB(任务控制块)中。然后,调用时钟滴答处理函数Clocktiek进行处理。Clocktick仅作一些简单的计时工作,只在必要时,才发消息给时钟任务去处理,并立即返回到用户任务。在这期间,有些任务的状态可能发生变化。所以,在退出内核之前再调用调度程序,对任务进行调度,由调度后的当前任务的TCB中恢复CPU各寄存器内容。最后,打开中断,恢复用户任务的运行。这样就可以大大的简化tick中断的开销。