不等厚对接管道焊缝射线检测技术探究
厚壁管焊接接头中间射线检验技术

厚壁管焊接接头中间射线检验技术摘要:厚壁管焊接接头的中间射线检测技术具有显著的专业性特征。
之所以需要对焊接接头区域进行检测,主要是由于金属管道在实践应用中会遇到一些含有危害物质的气体和液体。
尤其是应用于输送这些液体气体的管道,其在焊接完成后,焊接区域的探伤检测中必然会涉及一部分损害或侵蚀性。
因此,更需要应用先进技术完成射线检测任务。
为了取得更好的射线检测效果。
现阶段需结合后壁管道焊接接头的实际问题,应用透照方式进行比较,以便明确问题所在区域应用科学有效的技术进行检测处理。
关键词:厚壁管道;焊接接头;射线检测引言:厚壁管道焊接接头的检测技术应用对于取得更好的焊接接头区域探伤检测效果有重要作用。
厚壁管道由于透光性相对较差,因此,在检测时更需要借助中间射线的作用,对接头区域的具体情况进行精准显示和判断,在探伤时,检测探伤的检验方式仍然与超声波技术紧密相关,应用超声波作为探伤检测的主要性。
传递介质依托规范有效的操作流程完成检测工作任务,体现出厚壁管焊接接头中间射线检测技术的应用优势。
一、透照方式的比较分析不同类型的透照方式会给检测工作带来不同的影响。
本文研究外部透照和内部透照两种方法。
观察不同透照方式所呈现出的实际效果,进一步比较论证应当如何选择透照方式,为检验工作做好准备。
从外部入手进行透照的方法,需要分段达到透照效果。
设置固定的透照焦距数值设置具体的透照角度比例,实现对透照厚度和衡量检出效果的观察检出效果。
主要依靠剪出角进行控制和判断,在完成基础透照操作后,需要进一步通过数据计算的方式对检测结果进行确认。
在透照方式分析的过程中可见,应用不同透照方式所取得的透照结果可能产生一定的差异[1]。
但应用外透法能够确保底部影像的清晰度达到一定的水平。
尤其是中心射线和管道轴心区域所经过的区域,在显示信息的准确性上会更进一步的提升,能够针对管道根部区域比较难以观察的缺陷进行精准显示。
但这种透照方式可能会造成检验区域与片段逐步接近的状态,检出率会由于接近度过强而有所降低,一些细节性的问题无法精准解除。
论“超声波无损检测”技术在不等厚对接焊缝上的应用

论“超声波无损检测”技术在不等厚对接焊缝上的应用文章针对不等厚焊缝缺陷提出了一种超专用检测技术,利用正交超声探头组对焊缝进行扫描检测,可较好地解决钢质药筒不等厚薄板焊缝缺陷的在线自动无损检测。
标签:不等厚焊缝;缺陷;板波;超声检测在工程上,有时需要将两段不同厚度的薄壁圆筒对焊在一起,由于多种焊接因素的影响,在焊接过程中可能会在焊接区域形成各种焊接缺陷,因此在焊接之后,需要对焊接区域的焊接缺陷进行定性、定量、定位的检测。
对于大批量生产的焊接件,这种检测需要在线自动完成。
1 不等厚对接焊接缝特点在不等厚薄壁筒对接焊缝进行自动检测探伤中,该焊缝结构特点如下:(1)筒体的壁厚较小,通常为1.6mm,而筒底焊接区厚度为2.6mm。
(2)焊缝为不等厚对焊,筒底向左方厚度逐渐增大,几何形状复杂,焊道外侧表面粗糙,残留明显的车削刀纹。
(3)筒体和筒底以及焊道金属的化学成分不同。
常见的焊缝缺陷有气孔,夹渣,裂纹,未焊透,焊偏等形式,其中未焊透和裂纹是焊缝中危险性缺陷,它们大多与基体表面呈垂直状态形成。
文章的目的就是要解决这种不等厚薄壁筒对焊缺陷的无损检测技术,进而利用这种技术探讨钢质药筒焊缝缺陷在线检测问题。
对于焊缝的探伤,目前已有多种检测手段,比较常见的有:射线检测、涡流检测,磁粉探伤和超声检测等技术。
但对于这种薄壁不等厚对接的焊接方式,还没有一种成熟的技术可供在线检测使用。
针对这种不等厚薄壁筒焊接情况进行了原理探索,在理论分析和实践的基础上,提出了一种水浸正交超声检测法。
这一原理的关键在于针对轴向敏感缺陷采用轴向板波检测,针对周向敏感缺陷采用周向板波检测,从而达到对焊缝实施定性、定量和定位的在线检测的目的。
2 试验数据分析2.1 测试结果为验证理论分析结果,分别用厚度30mm和50mm的碳钢板制作两组试块进行试验,每组四块试样,加工成倾角分别为10°,12°,14°和16°。
厚壁管道对接焊缝的射线探伤技术

厚壁管道对接焊缝的射线探伤技术摘要:厚壁管道对接焊缝在电厂安装建设中的应用广泛,射线探伤技术已成为厚壁管道焊接质量的重要工艺。
由于厚壁管道的特点,给射线探伤施工带来了较大的难度。
本文对焊缝射线探伤时胶片紧贴焊缝和胶片紧贴管壁两种透照方式的实验对比,验证了不同透照方式对缺陷检出的影响效果,具有一定的参考价值。
关键词:厚壁管道焊缝检测射线探伤1、厚壁管道焊缝射线擦伤的布片方式受结构尺寸和安装条件的影响,厚壁管道焊缝射线探伤常用双壁单影法透照。
常采用的布片方式因其焊接形式特殊而与常规检验方法有很大不同。
两种布片方式胶片紧贴焊缝(方法a)和胶片紧贴管壁外(方法b)的示意图见图1。
2、两种布片方式的特点2.1 方法a(1)优点:射线照相灵敏度高,小缺陷检出率高(小缺陷是指垂直于射线透照方向的,尺寸远小于射线源焦点尺寸的缺陷),同种透照条件下焦距可选得较近,从而适当减少曝光量。
(2)缺点:底片可评定区域受焊缝坡口及暗袋影响,再加上必需的定位和识别标记,造成两侧坡口处无法检测。
且由于布片时底片与两侧管壁摩擦,易造成暗袋破损漏光或用力不当,使胶片折压感光而产生废片。
2.2 方法b采用方法b布片时,首先需在暗袋表面边缘处用记号笔标出各种定位和识别标记,然后将各种定位和识别标记粘贴在标定的位置上。
再在暗袋中间部位覆盖上一块宽60mm,略长于暗袋的厚3mm铅板。
接着进行第一次曝光,曝光量应尽可能小,以底片冲洗后能清晰显示出各种定位和识别标记为宜。
将经过第一次曝光的暗袋贴在焊缝外的管子上,注意将第一次曝光时被铅板覆盖的部分对准焊缝上方;同时将暗袋上各种定位和识别标记标在管子的同一位置上,以利于超标缺陷返修,最后按照焊缝厚度和焦距等确定曝光量,进行第二次曝光,完成全部曝光过程。
(1)优点:底片分两次曝光,底片可评定区域不受焊缝坡口、暗袋宽度、定位和识别标记等影响,可评定区域为整个焊缝宽度。
布片方便,不会因暗袋破损漏光或胶片折压感光而产生废片,废片评定、整理和保存叫方便。
对接环焊缝射线检测技术探讨

对接环焊缝射线检测技术探讨在输气管线环焊缝射线检测过程中,建立和加强射线检测质量管理体系,是保证管线施工质量的重要环节,是关系到管线长期安全服役的大事。
目前大多数管线建设部门对管线质量要求相脱节,与国际上广泛采用的设计标准相抵触,因此,敦促国家相关部门重新制定适应新形势下质量要求的管线设计标准已势在必行。
一.检测技术和检测比例针对管线环焊缝焊接工艺和焊接缺陷产生的特点,环焊缝无损检测通常采用射线检测和超声波检测以达到质量控制的目的。
(一)射线检测管线环焊缝射线检测一般分为X 射线检测和γ射线检测,前者用于壁厚在26 mm 以下的管线环焊缝检测,后者多用于大壁厚、架空或射线机难于架设的部位。
目前管线环焊缝检测采用了先进的检测工艺(如爬行器),由于X 射线检测的清晰度、灵敏度均高于γ射线检测,因此一般尽可能采用X 射线检测。
(二)超声波检测利用超声波穿过介质存在差异性界面时发生反射的特点,通过选用不同折射角探头可对不同壁厚的环焊缝面积性缺陷进行检测,主要用于检测裂纹、未焊透缺陷,对部分体积性缺陷也有一定的检出率。
超声波检测工艺制定,目前最先进的方法是按管线设计要求。
一般大管径(610 mm 以上)、高钢级、全自动焊接或半自动焊接管线,通常采用全自动探伤系统(如涩宁兰和西气东输管线),采用全自动检测系统主要基于检测效率高,适合快速多机组施工现场。
二.检测单位资质和人员资格认定单位检测资格和人员检测资质认定是国家行业管理正规化的具体表现。
目前国内管线建设中管线环焊缝检测的管理已基本遵循了国际惯例,实行了由具有检测资质独立的第三方机构承担检测工程。
在管理上呈现与业主构成独立的质量负责关系,从根本上解决和理顺了管线焊接质量控制的问题。
对于国内管线环焊缝检测工程项目,无损检测人员必须按照GB /T9445—1999《无损检测人员资格鉴定与认证》、TSG Z8001-2013《特种设备无损检测人员考核规则》标准和规范进行培训。
不等厚对接管道焊缝射线检测技术总结

不等厚对接管道焊缝射线检测技术总结本文通过对福清核电站一期中GPV系统不等厚对接管道焊接接头的射线照相检测,试验证明,选用合适的透照工艺以及使用双胶片法可使射线照相得到较高的对比灵敏度、合适的黑度等,满足了工程及相关技术标准的要求。
标签:射线检测;双胶片法;GPV系统;不等厚对接管道1 透照工艺试验研究针对以上分析,提高射线照相的对比度和保证黑度是不等厚管道焊缝透照工艺的关键。
认真分析影响射线照相灵敏度和缺陷检出率的各种因素,并排除选择余地少或对射线照相灵敏度影响小的因素,选择以下几个因素进行透照工艺的试验研究。
根据现场的实际情况,不等厚管道射线检测可以采取三种方法:双胶片法、放射源偏心法和高电压法。
1.1 放射源不等厚管道的规格626×33/614×25mm余高为2mm,部分不等厚管道留了射线曝光孔,因此透照方式可以采用选择单壁内透和双壁单影两种方法。
为保证射线照相的对比度、清晰度和颗粒度,直接关系到射线照相的灵敏度,为提高射线照相的灵敏度,根据DL821-2002的要求对于透照厚度差较大的工件,当透照厚度(TA)大于或等于10mm时,采用适宜的γ射线源透照,可获得较大的检测范围,所以放射源选用Ir92,焦点尺寸尽量小。
X射线机选择上方公司的型号为3505。
1.2 底片黑度DL821-2002标准规定X射线底片黑度为 1.5-3.5,γ射线的底片黑度为1.8-3.5。
由于不等厚管道管径不同,存在厚度差,导致底片一半黑一半白,底片黑度无法满足要求,采用了双胶片法、放射源偏心法及高电压法,使底片黑度达到要求。
1.3 像质计的选择及放置图像质量必须能使规定直径的金属丝在底片上清楚的显示出来。
像质计的选择按照表1所示。
像质计应放在被检部位射线源侧,当无法在源侧放置像质计时,可放在胶片侧的工件表面上,此时应在像质计附近附加“F”铅示标记以示区别,像质计灵敏度应该提高一级或通过对比试验使底片的质量达到规定的要求。
非平面(不等厚)工件对接焊缝TOFD检测工艺

非平面工件对接焊缝TOFD检测工艺肖 雄1 刘东梅2(1.江苏中宇检测有限公司 南京210012;2.徐州东方工程检测有限责任公司徐州 221008)摘要:本文主要介绍非平面工件对接焊缝TOFD检测工艺的设置,针对特种设备行业比较常见的不等厚工件组焊时,厚的一侧会进行削边处理,对TOFD检测时探头的放置及声束角度都会产生影响,本文通过仿真软件模拟探头声场对被检工件的覆盖及计算,对不同形状的非平面工件,总结了2个简单实用的计算公式,帮助现场检测人员快速方便地对这类工件的对接焊缝进行TOFD检测。
关键词:非平面工件;不等厚;削边;TOFD;PCSNon-planar workpiece butt welds TOFD inspection processXIAO Xiong1LIU Dong Mei2(1.Jiangsu ZhongYu Nondestructive Test Co., Ltd Nanjing 210012 China;2.Xuzhou Oriental Engineering Testing Co., Ltd. Xuzhou 221008 China)Abstract: This article describes the setting of non-planar workpiece butt welds TOFD inspection process, for special equipment industries the more common unequal thickness workpieces welds, thickside will conduct chamfered edge, the probes placement and the ultrasonic beam angle will beimpacted when TOFD testing, this article simulate and calculation the sound field of probes byusing simulation software to cover of the workpieces, for the non-planar workpieces ofdifferent shapes, summed up the two simple and practical formula to help people quickly andeasily on-site testing the butt welds of such workpieces for TOFD testing.Key words: non-planar workpiece; unequal thickness; chamfered edge; TOFD; PCSTOFD(衍射时差法)超声检测技术近年来在国内各行业发展很快,包括检测人员的培训交流、检测仪器的研究开发、检测标准的颁布实施等,特别是在特种设备行业,许多大的压力容器制造单位、检验检测机构都陆续开始应用此项检测技术。
厚壁管道对接焊缝无损检测技术探究

厚壁管道对接焊缝无损检测技术探究作者:诸子辉来源:《经济技术协作信息》 2018年第35期无损检测技术作为一种常用的检测技术,能够将金属管道的焊缝缺陷实施检测。
本文结合厚壁管道对接焊缝无损检测技术应用经验,进一步探讨厚壁管道对接焊缝无损检测技术应用方式,希望能够为其技术的应用与发展提出相应的发展建议。
厚壁管道对接焊缝无损检测技术在应用过程之中,需要结合厚壁管道的使用状况以及使用环境来选择检测方法的选择,技术人员要结合厚壁管道对接焊缝无损检测技术应用规范,来提升技术使用效率。
一、明确电站安装高压焊口中厚壁管道对接焊缝无损检测技术方法选择随着无损检测技术的发展,为目前的电站安装以及高压焊口工作提供了多样化的检测方法,比如TOFD超声检测技术、相控阵控监测技术等,应该结合电站安装高压焊口的实际要求,以及厚壁管道的厚度距离以及探伤比例来选取适当的检测方法。
TOFD超声检测技术就是利用了时频分析技术、自适应滤波技术对所测得的图像进行重新构建,结合声能衰减以及散射激励对于厚壁管道中存在的缺陷衍射波信号进行识别与激励;往往在检测过程中其声束与柱状晶夹角的变化是焊缝各项异性特征的主要体现。
所以在应用TOFD技术过程之中,应该注重波形的变化,因为不同波形在缺陷深度以及缺陷位置上都有不同的体现,应该在正确使用声束折射角以及探头位置的基础之上,加强对于不同特征波的信号了解,明确各个特征波信号的表现形式。
不断调整对称位置、中心轴线上的实际深度以及一次波检测声束的夹角与柱状晶生长方向交角的有效差值,即可得出探头在管道的不同位置范围,能够得到的不同的数值。
在技术应用时最好在厚壁管道的坡口处找到斜线形状的位置,让TOFD的探头尽可能保持科学的均质以及实际夹角,常规操作方式是将超声波入射角控制在45度到60度的范围内这样能够促进衍射波进一步激发,为后期的特征信号收集与判断工作奠定基础。
而TOFD二次波无损检测技术有其自身的利弊,虽然能够提升检测效率;但是对于厚壁管道中存在缺陷的位置锁定程度时没有一次波技术那样准确的,所以还需要提升无损检测技术应用水平,提升检测效果。
管道焊缝射线检测报告
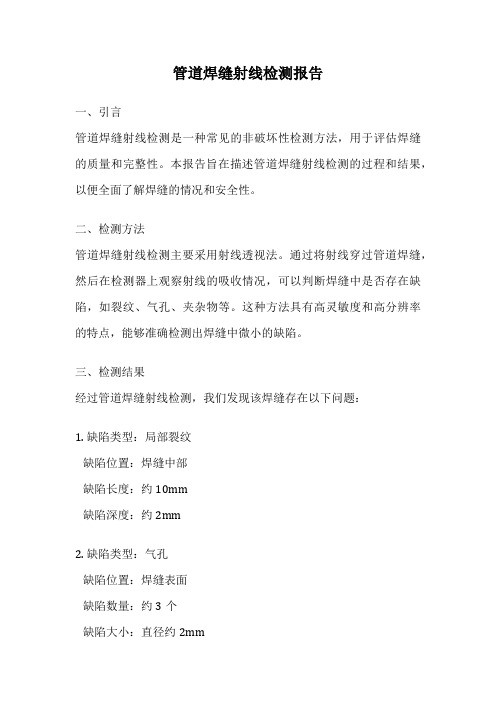
管道焊缝射线检测报告一、引言管道焊缝射线检测是一种常见的非破坏性检测方法,用于评估焊缝的质量和完整性。
本报告旨在描述管道焊缝射线检测的过程和结果,以便全面了解焊缝的情况和安全性。
二、检测方法管道焊缝射线检测主要采用射线透视法。
通过将射线穿过管道焊缝,然后在检测器上观察射线的吸收情况,可以判断焊缝中是否存在缺陷,如裂纹、气孔、夹杂物等。
这种方法具有高灵敏度和高分辨率的特点,能够准确检测出焊缝中微小的缺陷。
三、检测结果经过管道焊缝射线检测,我们发现该焊缝存在以下问题:1. 缺陷类型:局部裂纹缺陷位置:焊缝中部缺陷长度:约10mm缺陷深度:约2mm2. 缺陷类型:气孔缺陷位置:焊缝表面缺陷数量:约3个缺陷大小:直径约2mm四、分析与评估1. 关于局部裂纹由于局部裂纹的存在,焊缝的强度和密封性可能会受到影响。
需要及时修复或更换焊缝,以确保管道的安全运行。
2. 关于气孔尽管气孔的大小较小,但其存在可能导致焊缝的脆性增加,降低焊缝的强度。
建议对气孔进行修复,以保证焊缝的完整性和可靠性。
五、结论管道焊缝射线检测结果显示,该焊缝存在局部裂纹和气孔等缺陷。
这些缺陷可能会对管道的安全性和可靠性产生潜在影响。
建议采取相应的措施,及时修复焊缝,以确保管道的正常运行和安全性。
六、致谢在此,我们感谢所有参与管道焊缝射线检测工作的人员的辛勤付出和专业精神。
他们的努力为管道的安全运行提供了有力的保障。
以上是本次管道焊缝射线检测报告的全部内容。
我们将持续关注管道焊缝的情况,并采取适当的措施,确保管道的安全性和可靠性。
- 1、下载文档前请自行甄别文档内容的完整性,平台不提供额外的编辑、内容补充、找答案等附加服务。
- 2、"仅部分预览"的文档,不可在线预览部分如存在完整性等问题,可反馈申请退款(可完整预览的文档不适用该条件!)。
- 3、如文档侵犯您的权益,请联系客服反馈,我们会尽快为您处理(人工客服工作时间:9:00-18:30)。
不等厚对接管道焊缝射线检测技术探究
作者:刘昕
来源:《中国新技术新产品》2016年第24期
摘要:选用合适的透照工艺,能够显著提升射线检测的精准度,满足工程应用及相关领域技术标准的要求。
对不等厚对接管道的焊缝进行射线检测,技术人员应该采用科学的管道焊接数字射线检测方法,在管道内采用X射线机进行焊缝的透射检测,技术人员应该控制透照厚度,并且根据射线编号和射线直径计算管道像质指数,及时发现对接管道内壁中存在的缺陷问题。
本文从不等厚对接管道焊缝射线检测技术应用特点展开分析,提出几点有利于提升检测有效性的建议。
关键词:对接管道;焊缝射线;检测技术;不等厚
中图分类号:TG441 文献标识码:A
使用焊缝射线检测技术对不等厚对接管道缺陷进行检测,技术人员应该采用数字射线检测技术,进行对接管道连接口进行检测。
采用工控机配合X射线机的检测方法,进行管道焊缝缺陷检测。
工控机采用千兆网线的技术标准支持,使用同步发射接收机对检测数据进行解读。
其中,解读信号由X射线机透射管道内部结构产生,并且由电池组、PLC、控制电路为X射线机提供附属硬件功能支持。
一、提升透照厚度,控制管道检测几何不清晰度
每一组实验的像质计都放在胶片测,分析对接管道透射的等效值。
把对接管道焊缝情况进行分析,检查角焊缝边沿裂纹的分布情况,重点排查中部孔状缺陷,对管道结构的质量进行分层检测,重点排除对接中部空状缺陷问题。
对接管道的内凹(IC)位置检测,采用射线检测的方法,底片处的射线照相黑度不应该超过相邻母材处最浅黑度的任何长度。
内凹(IC)不同厚度检测效果见表1。
不能超过黑度内凹可允许的存在标准。
内凹处合度超过相邻母材最浅黑度的内凹,其单个长度不大于1t(不等厚取较小母材的厚度)。
在不等厚管道缺陷检测活动中,根据实际焊缝缺陷图像的表格特征提取必要的参数,采用X射线机透射技术进行管道焊缝检测,技术人员应该根据不同厚度的透照情况,分析对接管道的检测质量。
单个长度最大为6.4mm(1/4m)。
运用焊缝检测技术,在焊缝任何连续的300.4mm(12in)的长度或者焊缝总长内(取两者的较小值),其累计长度不大于12.7mm(i/2in)长度或者焊缝总长内(取两者的较小值)。
运用射线技术进行不等厚对接管道的检测,其检测长度不得超过同一级别未焊透的长度。
二、不同金属材料的管道焊缝对接检测
对接管道一般为金属材料制成,合金类管道的主要材料为铝和钢。
分析不等厚对接管道材料的射线透照等效系数,能够提升缺陷分析的准确性。
不等厚对接管道图像分析,需要根据不同材料的图像测试结果进行特征提取。
其中,铝制材料管道在管电压值为50kV时,其等效系数为1.0,管电压值为60kV时,其等效系数为
1.0。
管电压值为70kV时,其等效系数为1.0。
管电压值为100kV时,其等效系数为1.0。
管电压值为150kV时,其等效系数为0.12。
不同材料管材图像在输入计算机时,容易出现噪声过多、缺陷边缘模糊的问题。
在提取图像的过程中,应该对原始图像进行处理,计算出特征值。
应用透线技术,对管道焊接质量进行检测,通过对大量曝光曲线进行计算,得出材料的射线透照等效系数。
钢制材料管道在管电压值为50kV时,其等效系数为9.0,管电压值为60kV时,其等效系数为10.0。
管电压值为70kV时,其等效系数为11.3。
不同材料制成的管道焊缝双壁单影透照的IQI灵敏度不同,其中透明厚度占壁厚的百分比不应大于15%。
在检测过程中,技术人员需要优化对比试块的设计方式,重点对未融合缺陷的管道焊缝部位进行检测。
操作人员需要与放射源保持一定的距离,可以采用屏风进行辐射防护。
缝缺陷自身高度小于一定值对于烧穿的不等厚对接管道进行检测,厚度超过相邻母材最浅合度的即为对接位置烧穿。
对检测效果进行分析时,其单个长度不应大于1t(不等厚取较小母材厚度),且最大为634mm(1/4in)。
在焊缝任何连续的300.4mm(12in)长度或者焊缝总长内(取两者的较小值),其累计长度不应大于12.7mm(1/2in)。
在检测过程中,技术人员需要对原始图像进行去噪处理,采用图像增强的方式,进行图像二值化转换。
并且要在缺陷分析中将位置标记出来,根据缺陷数据的采集情况进行特征值的计算。
采用专家系统对检测数据进行分析,技术人员需要根据焊缝缺陷图像特征参数库,得到对比试块焊缝检测结果的评价。
三、对接管道不同穿透厚度的视差检测技术
0.1mm窄间隙缺陷在不同角度下的射线穿透厚度不同,管道填充区域的入射角度为5°时,穿透厚度不应小于1.15mm,放大倍率应该为11.5倍以上,此种射线检测技术的灵敏程度比较高。
窄间隙缺陷在不同角度下的射线穿透厚度不同,管道热焊接区域的入射角度为45°时,其射线穿透厚度不应小于0.14mm,放大倍率应该为1.4倍以上,此种射线检测技术的灵敏程度比较低,容易产生放大倍率过低,判断失准的现象,并且穿透的厚度比较小,还容易产生漏检现象。
窄间隙缺陷在不同角度下的射线穿透厚度不同,不等厚的对接管道钝边区域的入射角度为零度时,穿透厚度为无穷大,放大倍率为无穷大,此种射线检测技术的灵敏程度非常高。
技术人员可以根据检测要求,自行调节穿透厚度与放大的倍率,对不等厚管道进行无死角、全方位检测。
窄间隙缺陷在不同入射角度下的射线穿透厚度不同,不等厚的对接管道内坡口区域的入射角度为37.5°时,穿透厚度不应该小于0.16mm,放大倍率为1.6倍左右,此种射线检测技术的灵敏程度非常低。
当不等厚管道缺陷自身高度小于一定值时,其射线检测中的反射波高将小于40%满屏高,未融合的管道位置将出现漏检现象。
当缺陷高度大于一定值时,反射波高将大于40%满屏高,未融合的部分能够被准确检测出来。
四、管道焊缝检测灵敏度对比分析
不等厚对接管道焊缝根部出现未焊透现象,管道的深度小于10%,对接管道壁厚且最大不超过1.5mm。
在300mm焊缝长度内,检测总长度不小于50mm。
不等厚对接管道焊缝射线检测过程中,采用双壁单影透照的IQI检测技术,需要提高IQI灵敏度,并且对比透照厚度与IQI灵敏度的要求,进行管径和壁厚的比值分析。
其中,管径为114mm的管道,壁厚为5mm时,在JB/T4730(AB级)的检测标准下,其透照厚度为10.0mm,DL/T821(余高2mm)的透照高度为12.0mm。
在IQI灵敏度的要求下,在JB/T4730(AB级)的灵敏度不小于W14,DL/T821的灵敏度不小于W14.管径为114mm的管道,壁厚为8.5mm时,在JB/T4730(AB级)的检测标准下,其透照厚度为17.0mm,
DL/T821(余高2mm)的透照高度为19.0mm。
在IQI灵敏度的要求下,在JB/T4730(AB 级)的灵敏度不小于W13,DL/T821的灵敏度不小于W12。
采用焊缝射线检测技术,管径为168mm的管道,壁厚为3.6mm时,在JB/T4730(AB级)的检测标准下,其透照厚度为
7.2mm,DL/T821(余高2mm)的透照高度为9.2mm。
在IQI灵敏度的要求下,在JB/T4730(AB级)的灵敏度不小于W14,DL/T821的灵敏度不小于W14。
结语
在对接管道的焊缝检测活动中,技术人员应该利用不等厚射线反射原理进行投射,从而调整射线辐射的强度,防止由于投射不均匀造成的检测失误问题。
在检测活动中,射线束透过管焊缝,形成X射线的辐射图表。
控制穿过防护体的射线形成图谱,主要检测对接管道焊缝边沿有无出现明显裂纹,对中部裂纹和根部裂纹进行检测,防止出现对接中间部分未熔合的现象。
参考文献
[1]曹媛媛.不等厚对接管道焊缝射线检测技术总结[J].山东工业技术,2015(19):134-20,17.
[2]陈晨.蒸汽管道超声波无损检测焊缝缺陷的分析[J].石油工业技术监督,2015,31(7):34-36,52.
[3]刘芮辰,周重回.不等厚对接环焊缝超声定位问题探讨[J].华东电力,2011,36(5):87-88.
[4]林莉,杨平华,张东辉,等.厚壁铸造奥氏体不锈钢管道焊缝超声相控阵检测技术概述[J].机械工程学报,2012,48(14):12-20.
[5]吴云刚,李朋洲,许泽建,等.冲击载荷作用下管道焊缝裂纹的动态断裂韧性计算[J].原子能科学技术,2008,42(z2):661-663.
[6]卢威,张运平,柯涛,等.不锈钢管道焊缝超声检测中显示信号的定性分析[J].无损检测,2015,37(12):140-143.。