石油管道焊缝检测共13页文档
《石油管道焊缝检测》课件
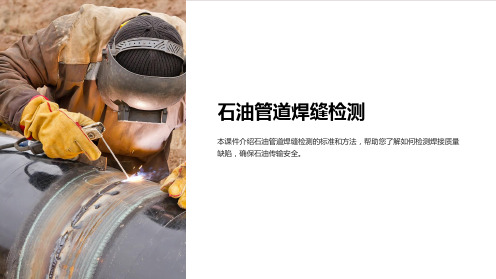
焊缝X射线检测技术
1
优点
可以对不同类型的材料进行检测。
2
应用场景
焊接件、铸造件、铸钢件的内部缺陷。
焊缝磁粉检测技术
优点
可以发现可见缺陷和表面裂纹等不易被其他检测方法发现的缺陷。
应用场景
焊接结构物、车轮轮辋、坦克炮管等缺陷检测。
局限性
只能对磁性部件进行检测。
GB 50253-2015《金属管道焊接规 范》等。
行业标准
P309:管道输送系统焊接质量标 准等。
法律法规
《中华人民共和国安全生产法》 等相关法律法规。
焊缝质量缺陷分类介绍
1
裂纹
2
焊缝或母材中出现的开裂。
3
凹坑
在焊接过程中出现的坑洞或者碳化物。
气孔
焊接时产生的气体在焊缝中形成的圆形 空洞。
检测方法概述
石油管道焊缝检测
本课件介绍石油管道焊缝检测的标准和方法,帮助您了解如何检测焊接质量 缺陷,确保石油传输安全。
石油管道焊缝检测的目的
安全性
防止因焊接质量问题导致石 油泄漏事故。
经济性
保证管道交付质量,减少返 修和重新焊接的成本。
法规要求
符合国家和行业相关的标准 和规定。
石油管道相关标准及规定
国家标准
1 超声波检测
利用声波在材料中的传播 规律进行缺陷检测。
2 X射线检测
利用X射线对材料进行穿 透性检测。
3 磁粉检测
在涂有磁性粉末的零件上, 发现经过磁场拉伸后的铁 磁性裂纹。
焊缝超声波检测技术
优点
• 有非常高的灵敏度。 • 可以在操作难度大的位置检测。
应用场景
• 石化、航天等行业的焊接检测。 • 各种金属或非金属材料的焊缝检测。
油气管道环焊缝检测

图2(e)所示是l0=1500mm,t=7mm,r0=100mm的管道,取测线r=0,θ=0°时,管道内磁场的分 布。可见,较长管道内的磁场分布与较短管子的类似,只是轴向分量和径向分量的平坦部分 更长一些。可以预见当管道很长时,管道内可近似认为是一匀强磁场。
α=0°
α=90°α=0° α=90°
r=0r0,θ=0°
(d)500mm管道测线4上磁场分布
α=0°
α=0°
α=90°
α=90°
r=0r0,θ=0°
磁化角度、不同长度管道内磁场分布;α=0°,15°,30°,45°,60°,75°,90°;r0=100mm;t=7mm;
(a)-(d)l0=500mm,(e)l0=1500mm
(a)500mm管道测线1上磁场分布
α=0°
α=90°α=0° α=90°
r=0.2r0,θ=0°
(b)500mm管道测线2上磁场分布
α=0°
α=90° α=0° α=90°
r=0.2r0,θ=72°
(c)500mm管道测线3上磁场分布
α=0°
α=90°α=0° α=90°
r=0.2r0,θ=144°
等效磁荷法可以有效获得铁磁性材料表面磁荷密度分布,进而方便地求出其周围磁 场分布。本文首次采用等效磁荷法,针对不同的磁化方向计算了非轴向磁化圆柱管状铁 磁性材料表面磁荷密度分布及管内磁场分布并分析了管道内环焊缝处异常磁场产生的 原因及特点。然后设计了一个用于测量管道内磁场的球形载体,测量了某输油气实验管 道内的磁场,以验证上述分析的正确性。最后对所测数据进行处理,通过对管道内环焊 缝处异常磁场的识别和定位而实现对管道环焊缝的识别和定位。
二. 理论分析
采用三维磁体表面磁荷分析方法分析任意方向均匀磁化的铁磁性管道表面的磁荷 密度分布,如式(1)所示。其中,rs 为磁体表面某一点的位置矢量,r’为磁体表面除去 rs 以后剩余表面上任一点的位置矢量,H0为磁化磁场强度,n 为磁体表面 rs处单位法向量, μ 为磁体相对磁导率。
石油天然气钢质管道无损检测-SY-T4109-2013

编号 SGB—1 SGB—2 SGB—3 SGB—4
SGB—5
SGB—6
200
平面
>360~600
>600
SRB对比试块
说明:Φ---被检管线外径; T---被检管线公称壁厚; h---内壁环状矩形槽的槽深; h=10%T且h≤1.5mm。
声能损失
仪器性能的调节
直探头测定,垂直线性,水平线性 斜探头测定,入射点,前沿距离,分辨力,折射角, 灵敏度余量
检测准备
检测面 探头移动区应清除飞溅、锈蚀、油污及其他外部 杂质,检测表面应修磨平整光滑,其表面粗糙度不应 超过6.3μm。焊缝及检测面应经外观检查合格方可进行 检测。
探头移动要求
探头移动区的确定应符合下列规定: 1.采用一次反射法检测时,探头移动区不应小于1.25P, P应按式(6.7.3)计算: P=2KT (6.7.3) 式中:P—跨距(mm); T—板厚(mm); K—声束在工件中的折射角β的正切值(tanβ)。 2.采用直射法检测时,探头移动区不应小于0.75P。
扫查方法
应采用单面双侧直射法和反射波法检测。 扫查灵敏度不应低于评定线灵敏度。 扫查速度不应大于150mm/s,当采用自动报警装臵扫 查时不受此限制;在平行扫查方向上,每个探头的 扫查路径应重叠,其范围至少为探头(压电晶片) 垂直于扫查方向尺寸的10%。
为探测纵向缺欠,探头应垂直焊缝中心线做矩形或 锯齿形扫查,探头前后移动范围应保证能扫查到全 部焊缝截面及热影响区,在保持探头垂直焊缝作前 后移动的同时,应作10°~15°的左右扫查。为观察 缺陷动态波形和区分缺陷信号或伪缺陷信号,确定 缺陷的位臵、方向和形状,可采用前后、左右、转 角、环绕等四种探头基本扫查方式。 检测横向缺欠时,应将波幅曲线灵敏度均提高6dB。 检测时,可在焊接接头两侧边缘使探头与焊接接头 中心线成10°~20°作两个方向的斜平行扫查。
管道对接焊缝的超声波检测..-共11页
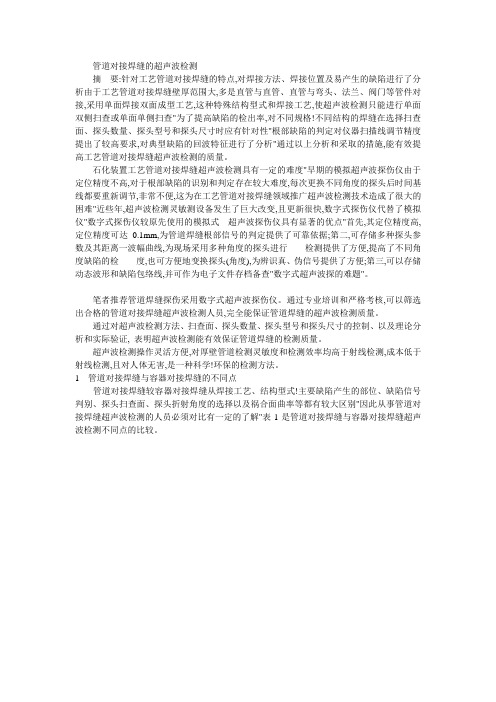
管道对接焊缝的超声波检测摘要:针对工艺管道对接焊缝的特点,对焊接方法、焊接位置及易产生的缺陷进行了分析由于工艺管道对接焊缝壁厚范围大,多是直管与直管、直管与弯头、法兰、阀门等管件对接,采用单面焊接双面成型工艺,这种特殊结构型式和焊接工艺,使超声波检测只能进行单面双侧扫查或单面单侧扫查"为了提高缺陷的检出率,对不同规格!不同结构的焊缝在选择扫查面、探头数量、探头型号和探头尺寸时应有针对性"根部缺陷的判定对仪器扫描线调节精度提出了较高要求,对典型缺陷的回波特征进行了分析"通过以上分析和采取的措施,能有效提高工艺管道对接焊缝超声波检测的质量。
石化装置工艺管道对接焊缝超声波检测具有一定的难度"早期的模拟超声波探伤仪由于定位精度不高,对于根部缺陷的识别和判定存在较大难度,每次更换不同角度的探头后时间基线都要重新调节,非常不便,这为在工艺管道对接焊缝领域推广超声波检测技术造成了很大的困难"近些年,超声波检测灵敏测设备发生了巨大改变,且更新很快,数字式探伤仪代替了模拟仪"数字式探伤仪较原先使用的模拟式超声波探伤仪具有显著的优点"首先,其定位精度高,定位精度可达0.1mm,为管道焊缝根部信号的判定提供了可靠依据;第二,可存储多种探头参数及其距离一波幅曲线,为现场采用多种角度的探头进行检测提供了方便,提高了不同角度缺陷的检度,也可方便地变换探头(角度),为辨识真、伪信号提供了方便;第三,可以存储动态波形和缺陷包络线,并可作为电子文件存档备查"数字式超声波探的难题"。
笔者推荐管道焊缝探伤采用数字式超声波探伤仪。
通过专业培训和严格考核,可以筛选出合格的管道对接焊缝超声波检测人员,完全能保证管道焊缝的超声波检测质量。
通过对超声波检测方法、扫查面、探头数量、探头型号和探头尺寸的控制、以及理论分析和实际验证, 表明超声波检测能有效保证管道焊缝的检测质量。
油管焊缝外观检验规范
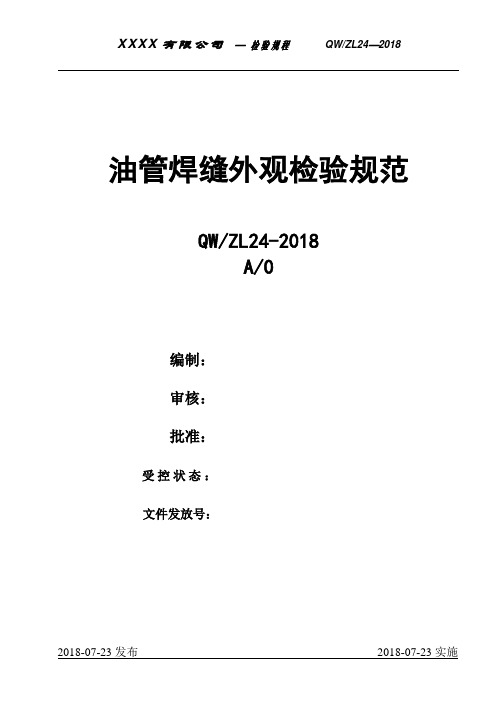
XXXX有限公司—检验规程QW/ZL24—2018油管焊缝外观检验规范QW/ZL24-2018A/0编制:审核:批准:受控状态:文件发放号:一、目的指导焊工及焊接检验人员工作,确保焊接质量。
二、适用范围本标准适用于公司油管焊缝外观质量检验(自检和专检)。
三、焊接部外观检查项目3.1 焊接缺陷:3.1.1咬边:由于焊接参数选择不当,或操作工艺不正确,沿焊趾的母材部位产生的沟槽或凹陷。
3.1.2焊缝表面气孔:焊接时,熔池中的气泡在凝固时未能逸出而残留下来形成的空穴叫气孔。
表面气孔指露在表面的气孔。
3.1.3裂纹:在焊接应力及其它致脆因素共同作用下,焊接接头中局部地区的金属原子结合力遭到破坏而形成的新界面而产生的缝隙,它具有尖锐的缺口和大的长宽比的特征。
3.1.4未焊满:由于填充金属不足,在焊缝表面形成的连续或断续的沟槽。
3.1.5焊瘤:焊接过程中,熔化金属流淌到焊缝之外未熔化的母材上所形成的金属瘤。
3.2焊缝形状缺陷:3.2.1焊缝成形差:熔焊时,液态焊缝金属冷凝后形成的焊缝外形叫焊缝成形,焊缝成形差是指焊缝外观上,焊缝高低、宽窄不一,焊缝波纹不整齐甚至没有等。
3.2.2余高超差:余高高于要求或低于母材。
3.2.3漏焊:要求焊接的焊缝未焊接。
表现在整条焊缝未焊接、整条焊缝部分未焊接、未填满弧坑、焊缝未填满未焊完等。
3.2.4 飞溅。
3.2.8电弧擦伤。
3.3 焊缝打磨。
焊缝打磨要求:打磨后焊缝符合本检验标准,焊缝圆滑过渡或焊缝与母材圆滑过渡,不允许破坏母材。
四、检验方法。
4.1检验方法:肉眼观察。
4.2缺陷判定后应作好标识,标明缺陷性质。
4.3标明的缺陷必须返工,缺陷返工后应重新对缺陷位置进行检验。
五、检验标准(单位为mm )序号 缺陷内容标准举例超差后的处理1h m i n25h m a x焊缝表面高低 在焊缝任意25mm 长度范围内,h max -h min≤2.5 h max ≤5h max =4 h min =1 5-1=3修磨或补焊。
长输油气管道对接焊缝射线检测缺陷判析

长输油气管道对接焊缝射线检测缺陷判析本文着重论述了执行SY/T4109-2013《石油天然气钢质管道无损检测》标准对长输油气管道对接焊缝进行射线检测在底片评定方面的实际应用,介绍了作者长期从事长输油气管道焊缝射线检测的一些实践经验和技术见解,通过实践应用,文中针对长输油气管道对接焊缝常见缺陷的产生原因、多发部位、影像的判断分析和评判的注意事项进行了详细论述。
标签:标准;射线检测;检测技术;缺欠评定;应用随着近几年工业的高速发展和能源需求的迅速增长,石油天然气长输管道的建设速度很快,并向着大口径、大壁厚、高钢级和高压力方向发展,管线的焊接质量要求更加严格,同时也对长输管道的无损检测技术提出了更高的要求。
石油天然气长输钢制管道的运行环境和野外施工条件以及管壁较薄的特点决定了长输管道的无损检测与常用承压设备存在不同之处。
油气长输管道射线检测执行的SY/T4109-2013《石油天然气钢质管道无损检测》标准在底片评定及验收标准上与NB/T47013-2015标准存在较大的差别,现就长输管道射线检测的常见缺陷,简单介绍缺陷的评定和影像分析。
1.气孔的评定气孔是管道焊缝中最常见的缺陷。
出现在焊缝的各个部位,层间和盖面层较多。
呈单个、链状、密集气孔出现,主要原因是焊条烘干不彻底或表面污物清理不净,电弧长短、操作技巧和施焊现场风力的影响也很大,特别是采用半自动焊时,如焊接参数调节不好出现气孔的几率较大。
2.夹渣的评定夹渣出现在焊缝的各个部位,在底片上有点状和条状,点状夹渣的外形无规则,轮廓清晰,有棱角,黑度淡而均匀,主要是药皮成渣后残留在焊道和母材或焊道和焊道之间。
条状夹渣在底片上呈现出不规则的、两端棱角、大多沿焊缝方向延伸的条状的宽窄不一的黑色影像,影像的轮廓较清晰,黑度不均。
主要原因是焊接电流过小,运条速度过快、清渣不净致使熔渣或夹杂物来不及浮出形成的。
SY/T4109-2015标准中条渣的评定按缺欠的宽度、单个长度和总长度三个方面来评定:(1)对单个条渣的宽度进行严格控制,宽度不得大于2mm,一旦超宽缺欠则直接评为IV级。
工业管道焊缝外部质量检验
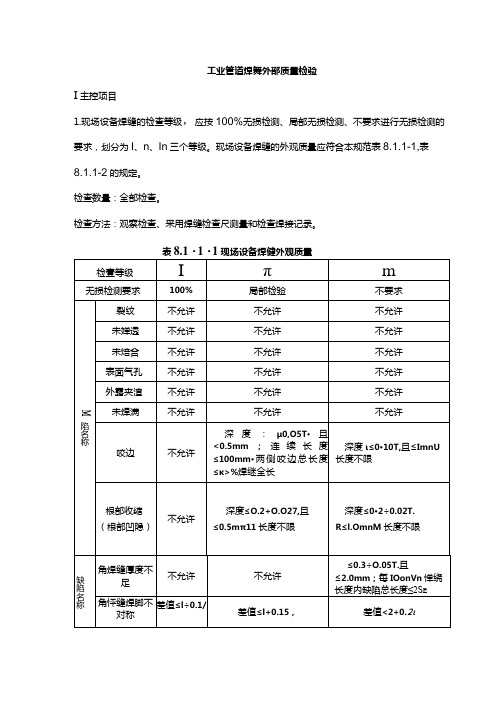
工业管道焊舞外部质量检验I主控项目1.现场设备焊缝的检查等级,应按100%无损检测、局部无损检测、不要求进行无损检测的要求,划分为I、n、In三个等级。
现场设备焊缝的外观质量应符合本规范表8.1.1-1,表8.1.1-2的规定。
检查数量:全部检查。
检查方法:观察检查、采用焊缝检查尺测量和检查焊接记录。
注:1当咬边经磨削修整并平滑过渡时,可按焊缝一侧较薄母材最小允许厚度值评定。
2角焊缝焊脚不对称在特定条件下要求平缓过渡时,不受本规定限制。
3除注明角焊缝缺陷外,其余均为对接、角接焊缝通用。
4表中T为母材厚度;t为设计焊缝厚度。
5表中公式的常量单位为mmβ2、管道焊缝的检查等级,应按现行国家标准《工业金属管道工程施工质量验收规范》GB50184的规定划分为I、n、m、IV、V五个等级。
管道焊缝的外观质量应符合本规范表8.1.2-1、表8.1.2-2的规定。
检查数量:全部检查。
检查方法:观察检查、采用焊缝检查尺测量和检查焊接记录。
表8.1.2・1管道焊缝外观质量表管道焊缝外观质量(余高和根部凸出注:对于铝及铝合金的根部凸出,当母材厚度小于或等于2mm时,根部凸出应小于或等于1.5mm;当母材厚度为2mm〜6mm时,根部凸出应小于或等于2.5mm o3、钛及钛合金、错及错合金的焊缝表面应在焊后清理前进行色泽检查。
钛及钛合金焊缝的色泽检查结果应符合表8.1.3的规定。
错及错合金的焊筑表面应为银白色,当出现淡黄色时应予以清除。
检查数量:全部检查。
检查方法:观察检查和检查焊接检查记录。
者为低温氧化,除不掉者为高温氧化。
11一般项目4、焊缝外观应成形良好,不应有电弧擦伤;焊道与焊道、焊道与母材之间应平滑过渡;焊渣和飞溅物应清除干净。
检查数量:全部检查。
检查方法:观察检查。
5、管道对接焊筵处的角变形(图8.1.5)应符合下列规定:1当管子公称尺寸小于100mm时,允许偏差为2mm;2当管子公称尺寸大于或等于100mm时,允许偏差为3mm o图8.1.5管道焊接接头的角变形I-钢板尺;a-角变形(平直度)偏差检查数量:全部检查。
石油天然气钢质管道无损检测[最终版]
![石油天然气钢质管道无损检测[最终版]](https://img.taocdn.com/s3/m/e03aacebf121dd36a32d8277.png)
一、概述1 SY/T4109-2005编制背景和简要经过随着我国石油天然气管道工程建设的发展,管道无损检测技术也得到了很大的发展。
同时管道工程施工技术,特别是管道焊接技术的发展,对无损检测技术提出了新的要求。
为确保工程质量,进一步完善无损检测标准,根据原国家石油和化学工业局《关于下达2001年石油天然气、石油化工行业标准、修订项目计划的通知》(国石化政发(2000)410号)文件要求,由石油天然气管道局盘锦北方无损检测公司负责对SY4056-93《石油天然气管道对接焊缝射线照相及质量分级》、SY4065-93《石油天然气管道对接焊缝超声波探伤及质量分级》、SY/T 0444-98《常压钢制焊接储罐及管道磁粉检测技术标准》及SY/T 0443-98《常压钢制焊接储罐及管道渗透检测技术标准》进行了整合修订,修订后标准名称为《石油天然气钢质管道无损检测》。
本标准在修订过程中,编制人员遵照国家有关方针政策,进行了比较广泛的调查研究,在全面总结和吸纳多年石油天然气钢质管道无损检测经验和技术,充分考虑石油天然气钢质管道工程施工实际特点的基础上,积极参照采用国外有关先进标准,并多次以发函或会议形式征求相关方意见,经反复修改形成送审稿,于2004年12月在海南三亚通过了由石油工程建设专业标准化委员会施工分标委组织的标准审查会的审查。
2 SY/T4109-2005修订的指导思想(1)目前石油天然气管道(含集输管道及其站场),特别是油气长输管道正向着大口径、大壁厚、高钢级及高压力方向发展,而与之相配套的先进的焊接和无损检测技术及设备也在广泛采用。
作为无损检测标准,必须适应和满足这种变化。
另外,管道施工建设不仅要占领国内市场,而且还要走向世界。
因此,与国外标准接轨也是本次标准修订应考虑的的一个重要因素。
(2)在检测工艺方面,应总结我国石油天然气企业在国内外长输管道施工检测的成功经验,积极吸纳国内外相关标准的长处来修订。
- 1、下载文档前请自行甄别文档内容的完整性,平台不提供额外的编辑、内容补充、找答案等附加服务。
- 2、"仅部分预览"的文档,不可在线预览部分如存在完整性等问题,可反馈申请退款(可完整预览的文档不适用该条件!)。
- 3、如文档侵犯您的权益,请联系客服反馈,我们会尽快为您处理(人工客服工作时间:9:00-18:30)。
石油管道的焊接——钨极惰性气 体保护(氩弧焊)
氩弧焊的焊接原理 钨极氩弧焊就是把氩气做 为保护气体的焊接。借助产生在钨电极与焊体 之间的电弧,加热和熔化焊材本身(在添加填 充金属时也被熔化),而后形成焊缝金属。钨 电极,熔池,电弧以及被电弧加热的连接缝区 域,受氩气流的保护而不被大气污染。
焊缝检试验.3,焊缝射线照相.4, 超声波探伤.5,磁力探伤.6,渗透 探伤
石油管道无损检测
目前石油天然气管道(含集输管道及其站场), 特别是油气长输管道正向着大口径、大壁厚、 高钢级及高压力方向发展,而与之相配套的先 进的焊接和无损检测技术及设备也在广泛采用。 作为无损检测标准,必须适应和满足这种变化。
渗透探伤
对于不能进行射线探伤和超声波探伤的部位采取渗 透探伤
渗透检测的工作原理是:工件表面被施涂含有荧光 染料或者着色染料的渗透剂后,在毛细作用下,经 过一定时间,渗透剂可以渗入表面开口缺陷中;去 除工作表面多余的渗透剂,经过干燥后,再在工件 表面施涂吸附介质——显像剂;同样在毛细作用下, 显像剂将吸引缺陷中的渗透剂,即渗透剂回渗到显 像中;在一定的光源下(黑光或白光),缺陷处的 渗透剂痕迹被显示(黄绿色荧光或鲜艳红色),从 而探测出缺陷的形貌及分布状态。
石油管道 焊接质量 检测
石油作为重要的能源和化工产品,其 在国民经济和国家安全上作用不言而 喻。
焊接缺陷的危害 焊接缺陷对产品构件,尤其是
压力容器和压力管道在使用中带来了的隐患和 危害是不能低估的 ·由于缺陷的存在,减少了 焊缝的承载面积,削弱了静力拉伸强度。 ·由 于缺陷形成缺口,缺口尖端会发生应力集中和 脆化现象,容易产生裂纹并扩展。 ·缺陷可能 穿透管壁,发生泄漏,影响致密性,留下隐 患。 ·对一些结构件轻者在很大程度上降低产 品的力学性能和缩短产品的使用寿命;重者, 还能产生脆断,导致危及生命财产安全的灾难 性事故,给国民经济带来巨大的损失
射线探伤
利用射线穿透物体来发现物体内部缺陷的探伤 方法。 射线能使胶片感光或激发某些材料发出 荧光。射线在穿透物体过程中按一定的规律衰 减,利用衰减程度与射线感光或激发荧光的关 系可检查物体内部的缺陷。
超声波探伤
超声波探伤操作程序简单、快速,对裂纹、未 熔合危害性缺陷的检测灵敏度高,因此世界上 很多国家对钢结构内部质量的控制采用超声波 探伤,一般已不采用射线探伤。在西气东输中 卫黄河跨越工程中,探伤检测要求比较严格, 对钢结构桁架对接焊缝的无损检测要求采用 100%的超声波探伤,合格后再进行100%的射 线探伤
thanks
更多精品资源请访问
docin/sanshengshiyuan doc88/sanshenglu