橡胶注射成型设备技术进步及发展动向
中国橡胶机械工业的发展及现状
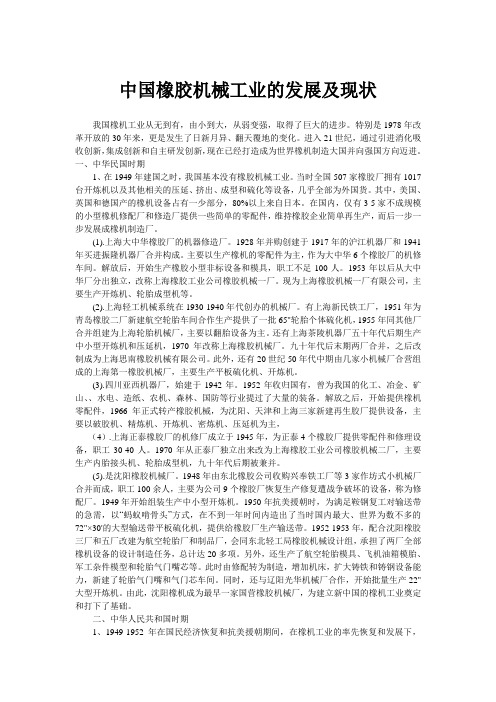
中国橡胶机械工业的发展及现状我国橡机工业从无到有,由小到大,从弱变强,取得了巨大的进步。
特别是1978年改革开放的30年来,更是发生了日新月异、翻天覆地的变化。
进入21世纪,通过引进消化吸收创新,集成创新和自主研发创新,现在已经打造成为世界橡机制造大国并向强国方向迈进。
一、中华民国时期1、在1949年建国之时,我国基本没有橡胶机械工业。
当时全国507家橡胶厂拥有1017台开炼机以及其他相关的压延、挤出、成型和硫化等设备,几乎全部为外国货。
其中,美国、英国和德国产的橡机设备占有一少部分,80%以上来自日本。
在国内,仅有3-5家不成规模的小型橡机修配厂和修造厂提供一些简单的零配件,维持橡胶企业简单再生产,而后一步一步发展成橡机制造厂。
(1).上海大中华橡胶厂的机器修造厂。
1928年并购创建于1917年的沪江机器厂和1941年买进振隆机器厂合并构成。
主要以生产橡机的零配件为主,作为大中华6个橡胶厂的机修车间。
解放后,开始生产橡胶小型非标设备和模具,职工不足100人。
1953年以后从大中华厂分出独立,改称上海橡胶工业公司橡胶机械一厂。
现为上海橡胶机械一厂有限公司,主要生产开炼机、轮胎成型机等。
(2).上海轻工机械系统在1930-1940年代创办的机械厂。
有上海新民铁工厂,1951年为青岛橡胶二厂新建航空轮胎车间合作生产提供了一批65"轮胎个体硫化机,1955年同其他厂合并组建为上海轮胎机械厂,主要以翻胎设备为主。
还有上海茶陵机器厂五十年代后期生产中小型开炼机和压延机,1970年改称上海橡胶机械厂。
九十年代后末期两厂合并,之后改制成为上海思南橡胶机械有限公司。
此外,还有20世纪50年代中期由几家小机械厂合营组成的上海第一橡胶机械厂,主要生产平板硫化机、开炼机。
(3).四川亚西机器厂,始建于1942年。
1952年收归国有,曾为我国的化工、冶金、矿山、、水电、造纸、农机、森林、国防等行业提过了大量的装备。
注塑成型机的发展史

注塑成型机的发展史摘要:一、注塑成型机的定义及工作原理二、注塑成型机的发展历程1.初期阶段2.中期阶段3.现代阶段三、注塑成型机的应用领域四、注塑成型机的未来发展趋势正文:一、注塑成型机的定义及工作原理注塑成型机是一种将塑料原料通过加热和压力作用下,使其熔融后注射入闭合好的模腔内,经过固化定型后取得制品的工艺设备。
它的工作原理与打针用的注射器相似,借助螺杆(或柱塞)的推力,将已塑化好的熔融状态(即粘流态)的塑料注射入模腔内。
注射成型是一个循环的过程,每一周期主要包括:定量加料——熔融塑化——施压注射——充模冷却——启模取件。
取出塑件后又再闭模,进行下一个循环。
二、注塑成型机的发展历程1.初期阶段:上世纪50 年代,注塑成型机主要应用于生产低精度、简单的塑料制品,如塑料袋、瓶子等。
这一时期的注塑成型机结构简单,功能单一,生产效率较低。
2.中期阶段:从上世纪70 年代开始,随着塑料工业的迅速发展,注塑成型机得到了改进和升级。
这一阶段的注塑成型机采用了液压驱动,具有较高的注射压力和速度,能够生产精度较高的塑料制品。
同时,机型也逐渐丰富,出现了立式、卧式、全电式等不同类型的注塑成型机。
3.现代阶段:进入21 世纪以来,注塑成型机在技术上取得了重大突破,主要体现在以下几个方面:(1)节能环保:采用伺服驱动技术,降低了能耗,减少了噪音污染。
(2)高速高精度:采用三轴联动功能,实现储料、托模、开模同步进行,提高了生产效率和制品质量。
(3)智能化:通过集成应用,实现自动化生产,提高了生产效率,降低了劳动成本。
三、注塑成型机的应用领域注塑成型机广泛应用于塑料、橡胶、陶瓷等制品的生产,涉及行业包括汽车、家电、电子、包装、建筑等。
橡胶制品行业的先进制造技术与装备
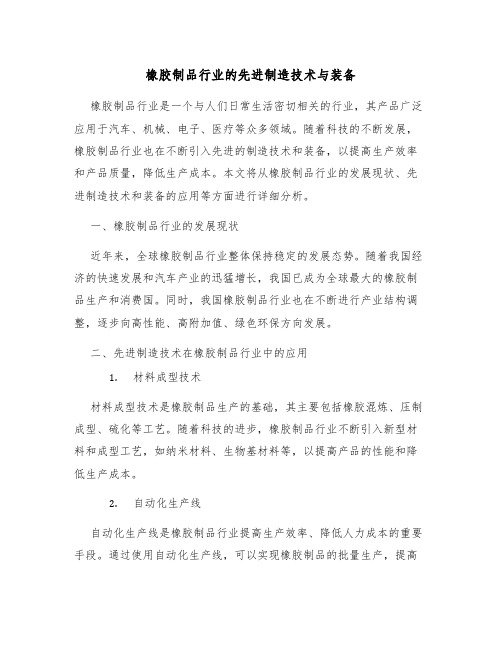
橡胶制品行业的先进制造技术与装备橡胶制品行业是一个与人们日常生活密切相关的行业,其产品广泛应用于汽车、机械、电子、医疗等众多领域。
随着科技的不断发展,橡胶制品行业也在不断引入先进的制造技术和装备,以提高生产效率和产品质量,降低生产成本。
本文将从橡胶制品行业的发展现状、先进制造技术和装备的应用等方面进行详细分析。
一、橡胶制品行业的发展现状近年来,全球橡胶制品行业整体保持稳定的发展态势。
随着我国经济的快速发展和汽车产业的迅猛增长,我国已成为全球最大的橡胶制品生产和消费国。
同时,我国橡胶制品行业也在不断进行产业结构调整,逐步向高性能、高附加值、绿色环保方向发展。
二、先进制造技术在橡胶制品行业中的应用1.材料成型技术材料成型技术是橡胶制品生产的基础,其主要包括橡胶混炼、压制成型、硫化等工艺。
随着科技的进步,橡胶制品行业不断引入新型材料和成型工艺,如纳米材料、生物基材料等,以提高产品的性能和降低生产成本。
2.自动化生产线自动化生产线是橡胶制品行业提高生产效率、降低人力成本的重要手段。
通过使用自动化生产线,可以实现橡胶制品的批量生产,提高产品质量稳定性,降低生产事故率。
目前,国内许多橡胶制品企业都已实现了自动化生产,部分企业已开始向智能化生产线转型。
3.信息化管理技术信息化管理技术在橡胶制品行业的应用,可以提高企业管理效率,缩短产品研发周期,加快市场响应速度。
通过使用企业资源计划(ERP)、产品生命周期管理(PLM)等信息化管理系统,可以实现企业生产、销售、研发等环节的协同管理,提高企业的核心竞争力。
4.检测与测试技术检测与测试技术是保证橡胶制品质量的关键环节。
先进的检测与测试技术可以实时监控生产过程中的各项指标,确保产品质量符合国家标准。
目前,橡胶制品行业已广泛应用光学、电子、超声波等检测技术与设备,实现了对产品质量和生产过程的全面监控。
三、先进装备在橡胶制品行业中的应用1.高性能橡胶混炼设备高性能橡胶混炼设备可以提高橡胶材料的性能,降低生产成本。
注射成型LSR的最新进展

注射成型LSR的最新进展图1 热塑性塑料/LSR包覆成型的一个应用是水龙头滤网。
在这一制品中,用作滤网的LSR被包覆成型到尼龙66上得益于材料、设备和工艺的改进与革新,液态硅橡胶(LSR)逐渐摆脱了小众需求的现状,扩大了应用领域。
其中,大型、微型和发泡制品,以及多色或多材料的组合是LSR应用的新领域。
液态硅橡胶(LSR)对于注塑加工商的商业机会的拓宽,要归功于更新的成型工艺,如发泡、多色或者多硬度注射,以及热塑性塑料/热固性塑料包覆技术的涌现。
材料、设备和模具的改进增加了产品的多功能性,提高了产品质量,降低了注塑加工商准入的门槛。
今天的LSR注塑加工商拥有更多的原材料选择、更大的模具选择余地以及更好的工艺技术,不但可以成型小至数千分之一g的制品,而且也能够加工32kg以上的巨大产品。
材料、模具和加工设备供应商表示,在过去的几年里,对LSR感兴趣的人逐渐增加。
“一些塑料公司对此感兴趣,一些新公司也希望开拓他们的业务,同时医疗领域的加工商也更多地加入进来。
” Roembke Mfg. & Design模具公司副总裁Greg Roembke说。
“我们发现,汽车工业已开始应用LSR。
也许传统的硅橡胶在汽车工业中的应用已达到了极致,下一步需要从LSR获得更多的东西。
”他补充说。
图2 LSR的双注射包覆成型通常在一个成型单元内完成,而LSR和热塑性塑料则分别在不同的注射机上成型LSR注塑加工商表示,他们已经从高温硅橡胶(HCR)、EPDM、乳胶、天然橡胶、TPE、PVC甚至陶瓷的应用领域中抢占了一些市场。
Momentive Performance Materials(前GE Silicones)的弹性体和RTV总经理Bill French 说,由于LSR惰性、耐热且耐化学品,因此可用于生产奶嘴和奶头、医用装置阀门或密封条、医疗植入体、医用手套和汽车密封条等。
另外,在电子连接器、O型圈、衬垫、膜、引擎内零部件和燃料系统零部件方面,LSR也将获得更大的市场份额。
橡胶制品行业的智能制造与数字化转型

橡胶制品行业的智能制造与数字化转型随着科技的飞速发展,橡胶制品行业正面临着巨大的变革。
智能制造与数字化转型已成为橡胶制品行业发展的必然趋势。
本篇文章将深入分析橡胶制品行业的智能制造与数字化转型,探讨其发展现状、挑战及对策。
橡胶制品行业的现状橡胶制品行业是我国的传统产业之一,拥有丰富的原材料资源和完整的产业链。
然而,长期以来,我国橡胶制品行业存在生产效率低、能耗高、产品质量不稳定等问题。
随着全球经济一体化的推进,国际市场竞争日益激烈,我国橡胶制品行业亟待进行产业升级和技术改造。
智能制造在橡胶制品行业中的应用智能制造是橡胶制品行业转型升级的关键途径。
通过引入智能制造技术,可以实现生产过程的自动化、信息化和智能化,提高生产效率和产品质量,降低生产成本。
智能制造技术在橡胶制品行业中的应用主要包括以下几个方面:1.智能生产设备:采用高精度、高性能的智能生产设备,如数控成型机、智能硫化机等,实现生产过程的自动化和精确控制。
2.智能控制系统:通过引入先进的控制算法和传感器技术,实现生产过程的实时监控和智能调控,提高产品的一致性和可靠性。
3.智能物流系统:建立智能物流系统,实现原材料、半成品和成品的快速、准确配送,降低库存成本。
4.数据分析与优化:通过收集生产过程中的海量数据,运用大数据分析技术和算法,挖掘潜在的优化方案,实现生产过程的持续改进。
数字化转型在橡胶制品行业中的应用数字化转型是橡胶制品行业实现智能制造的基础。
通过数字化技术,可以实现设计、生产、管理等方面的全面数字化,提高企业的核心竞争力。
数字化转型在橡胶制品行业中的应用主要包括以下几个方面:1.产品设计数字化:采用三维设计软件,实现产品设计的虚拟仿真,提高产品设计的效率和质量。
2.生产过程数字化:通过引入数字化生产管理系统,实现生产过程的实时监控、数据采集和分析,提高生产效率和产品质量。
3.企业管理数字化:建立企业资源规划(ERP)系统,实现企业内部各部门之间的信息共享和协同工作,提高管理效率。
橡胶制品成型技术的新进展
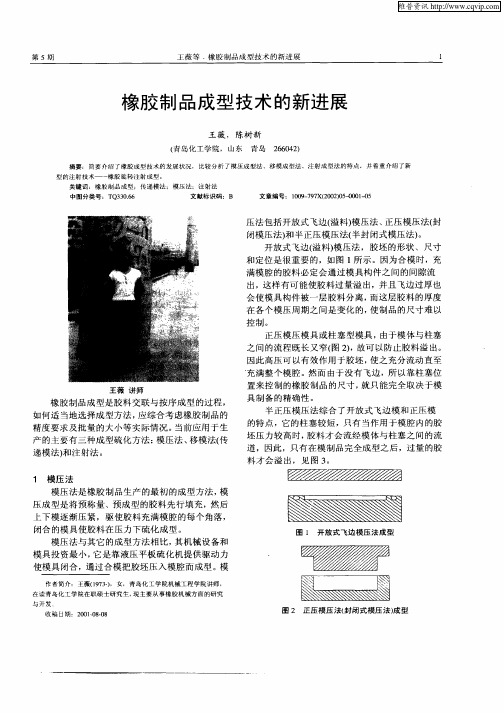
使 模 具 闭合 ,通 过 合 模把 胶坯 压 入 模腔 而 成型 。模
作者 简 介: 王薇 (9 3) 17一,女 ,青 岛化 工学 院机 械 工程 学 院讲 师 , 在 读 青 岛化 工学 院在 职硕 士 研究 生 , 主要 从 事橡 胶机 械 方面 的 研究 现
关键 词 :橡 胶制 品 成型 ;传递 模法 ;模 压法 :注 射 法
中图 分类 号 :T 3 0 6 Q 3. 6
文献 标 识码 :B
文 章编 号 : 10 - 9X(0 20 M 10 09 7 7 20 )5  ̄0 - 5
压法 包 括 开放 式 飞边 ( 料 ) 压法 、 溢 模 正压 模压 法( 封
1 模 压 法
模 压法 是 橡 胶制 品生 产 的最初 的成 型方 法 , 模 压 成型 是将 预 称 量 、预 成 型 的胶 料先 行填 充 ,然 后 上 下模 逐渐 压 紧 ,驱 使 胶料 充 满模 腔 的每 个 角落 , 闭合 的模 具使 胶 料在 压 力 下硫化 成型 。 模 压 法与 其 它 的成 型方 法 相 比 , 机 械设 备 和 其 模 具投 资 最 小 , 是靠 液 压平 板 硫 化机 提 供驱 动 力 它
王 薇 讲 师
置来 控制 的 橡胶 制 品 的尺 寸 , 只 能完 全 取 决于 模 就 具 制 备 的精确 性 。 半 正压 模压 法 综 合 了开放 式 飞边 模 和 正压 模 的特 点 ,它的 柱塞 较 短 ,只 有 当作 用 于模 腔 内的胶 坯 压 力较 高 时 , 料 才 会流 经 模体 与 柱塞 之 间 的流 胶 道 ,因此 ,只有 在模 制 品完全 成 型之 后 ,过 量 的胶
控制。
一步法注射成型技术与设备研究的进展和应用开发

吕柏 源 薛胜 火 杨 福 昌 ( 科技大学机电工程学院, 青岛 山东青岛2 02 6 4) 6
摘要 : 此 文介 绍了橡胶 一步法注射成 型技 术发展 的四个阶段 。作者 以通 用型 注射机 和注射法制 造轮胎 为例 。 出 了橡胶一步 法注射成型技 术在七个方面的应用和开发价值 。 提 关键词 : 一步法注射成 型 ; 轮胎
有先 天性 的缺陷 。 为 了弥补 模 压 法 的缺 陷 , 们 开 发 了传 递 人 模 压法 。这 种方 法是将 经预 成 型定 量 的胶 料适
射成 型 机 结构 的复 杂化 和 注 射容 量 的 限制 , 导
致橡 胶注射 成 型方法 难 以广泛 推广 。
1 橡 胶 一 步 法 注 射 成 型 技 术 的 开
缠贴 法成 型技术 主要 是为 了提 高大型 橡胶 制 品
模 压 法成 型技 术 、 传递 法成 型技术 、 贴法成 型 缠
技 术 和注 射法 成 型技术 四大类 。
的生 产 效率 并 形 成较 精 确 的胶 坯 , 制 品 的致 对
密性 没有 很大 作用 。 注射 成 型方 法在 上 世 纪 4 O年 代 就应 用在
・
3 ・ O
世
界
橡
胶
工
一
业
术, 其工作过程是胶料被塑化后直接通过 信息
定量 , 注入 模 腔 , 当模腔 里 的胶 料 达 到预定 的密
步法注射成型实验室高难度原理考核研
究 的实 验室 装 置如 图 2所 示 。
度后 , 注射机停止注射 。可见这种方法的塑化 、 定量 、 注射是 同步进行的 , 这种技术称为一步法 注射成型技术 , 其加工设备称一步法注射成型
发 和 推 广
我国注塑机的特点及发展方向
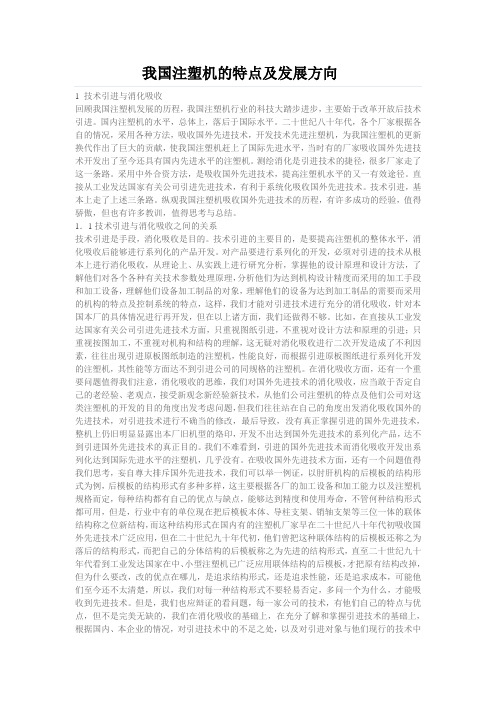
我国注塑机的特点及发展方向1 技术引进与消化吸收回顾我国注塑机发展的历程,我国注塑机行业的科技大踏步进步,主要始于改革开放后技术引进。
国内注塑机的水平,总体上,落后于国际水平。
二十世纪八十年代,各个厂家根据各自的情况,采用各种方法,吸收国外先进技术,开发技术先进注塑机,为我国注塑机的更新换代作出了巨大的贡献,使我国注塑机赶上了国际先进水平,当时有的厂家吸收国外先进技术开发出了至今还具有国内先进水平的注塑机。
测绘消化是引进技术的捷径,很多厂家走了这一条路。
采用中外合资方法,是吸收国外先进技术,提高注塑机水平的又一有效途径。
直接从工业发达国家有关公司引进先进技术,有利于系统化吸收国外先进技术。
技术引进,基本上走了上述三条路。
纵观我国注塑机吸收国外先进技术的历程,有许多成功的经验,值得骄傲,但也有许多教训,值得思考与总结。
1.1技术引进与消化吸收之间的关系技术引进是手段,消化吸收是目的。
技术引进的主要目的,是要提高注塑机的整体水平,消化吸收后能够进行系列化的产品开发。
对产品要进行系列化的开发,必须对引进的技术从根本上进行消化吸收,从理论上、从实践上进行研究分析,掌握他的设计原理和设计方法,了解他们对各个各种有关技术参数处理原理,分析他们为达到机构设计精度而采用的加工手段和加工设备,理解他们设备加工制品的对象,理解他们的设备为达到加工制品的需要而采用的机构的特点及控制系统的特点,这样,我们才能对引进技术进行充分的消化吸收,针对本国本厂的具体情况进行再开发,但在以上诸方面,我们还做得不够。
比如,在直接从工业发达国家有关公司引进先进技术方面,只重视图纸引进,不重视对设计方法和原理的引进;只重视按图加工,不重视对机构和结构的理解,这无疑对消化吸收进行二次开发造成了不利因素,往往出现引进原板图纸制造的注塑机,性能良好,而根据引进原板图纸进行系列化开发的注塑机,其性能等方面达不到引进公司的同规格的注塑机。
在消化吸收方面,还有一个重要问题值得我们注意,消化吸收的思维,我们对国外先进技术的消化吸收,应当敢于否定自己的老经验、老观点,接受新观念新经验新技术,从他们公司注塑机的特点及他们公司对这类注塑机的开发的目的角度出发考虑问题,但我们往往站在自己的角度出发消化吸收国外的先进技术,对引进技术进行不确当的修改,最后导致,没有真正掌握引进的国外先进技术,整机上仍旧明显显露出本厂旧机型的烙印,开发不出达到国外先进技术的系列化产品,达不到引进国外先进技术的真正目的。
- 1、下载文档前请自行甄别文档内容的完整性,平台不提供额外的编辑、内容补充、找答案等附加服务。
- 2、"仅部分预览"的文档,不可在线预览部分如存在完整性等问题,可反馈申请退款(可完整预览的文档不适用该条件!)。
- 3、如文档侵犯您的权益,请联系客服反馈,我们会尽快为您处理(人工客服工作时间:9:00-18:30)。
在模具稍微开启的状态下向模腔内注射胶料,在按所需的用量注射完毕的同时,进行合模加压成型硫化。采用这种成型工艺方法可生产精密 O 型密封圈、隔膜或其它精密制品等不允许有浇注口痕迹和胶边扩展线的制品。
5.注射传递成型
模具在合模后锁紧前,把经过计量的胶料注射进入传递室,有注射压力的胶料迫使传递室开档增大,直到所需的胶料完全注入传递室中,然后才将模具完全锁紧,这时用传递室的活塞将传递室中的胶料加压注入模腔中,这种成型工艺方法可生产出残余飞边很小的橡胶制品。
工业化国家已在注射机控制系统配备了各种微处理的控制器和软件包,它能方便地对每台注射机的硫化时间、硫化温度和硫化压力实行检测和控制,同时控制系统与设备相匹配,并有中央计算机输入数据,综合企业生产管理信息进行进一步处理和 SPC 评估。大多数注射机的网络系统都具有“分级数据收集和处理”功能,可进行实时过程的检测、过程的控制、注射机监控以及管理控制。如果注射机有相关的控制器,即可定期监测注射机的变量,并可将注射程序直接送到注射机上,还可设置警报器,以发出故障或临界参数偏差的警告,同时还有故障自诊、原材料计划、选择最佳使用条件以及记录生产数据等等。
4.效率强化
目前的橡胶注射成型机不论生产小型橡胶制品还是生产大中型橡胶制品,基本上是采用一台注射机对应一台压力硫化装置 ( 机 ) 。由于硫化时间一般要比注射时间长,导致橡胶注射机系统闲置时间太长,利用效率太低。这种情况的产生与橡胶注射成型设备的生产工艺和结构有关系。因此,强化橡胶注射机的效率也就成了技术的追求目标。强化效率将从两个方面发展:一是采用新工艺、新材料、新配方,在保证质量前提下,提高硫化速度,缩短生产周期;二是采用多工位橡胶注射成型方法,包括注射机移动注射、模具移动注射以及转盘注射等。
3.容量提高
在橡胶工业中,许多大型的橡胶制品,如轮胎胶囊,深井油田泵橡胶衬套,大型防震建筑物和工业胶辊等等都是一些大型制品。传统的模压方法存在着工艺过程复杂、质量不稳定、生产效率低、浪费原材料、劳动强度过大以及加工精度低等缺点。采用大型橡胶注射成型机生产时,上述缺点都可以克服。目前正在开发的螺杆旋转注射成型技术及加工设备将是提高注射容量的一个发展趋势。
2.设备简化
通常的橡胶注射设备必须包括锁模机构及模具系统、塑化与轴向注射系统、液压系统等。设备的复杂化使设备变得庞大,注射一个很小的制品也需要一台较庞大的注射设备。为了简化设备,橡胶注射机的结构将往两个方面发展:一是锁模压力机构将向全电机和简化运动副的结构方向发展,如带信号反馈的螺旋副机构,二是预塑化结构和轴向移动系统将合二为一,并采用全电动结构。
2.橡胶注射成型工艺的技术进步
橡胶注射机在一般情况下是将模型锁紧,然后将塑化好的胶料注入模腔。为了提高制品质量和节省原材料,人们先后发展了许多注射成型新工艺。
3.抽真空注射成型
减少修边工序的措施是提高模具精度,从而提高制品精度。但这样合模后,模腔内的空气不易排出来,会产生模腔边角部位缺胶、焦烧或制品产生气泡,这些缺陷采用抽真空注射成型工艺就可以得到解决。
6.冷流道注射成型
冷流道注射成型是流道、进胶道的胶料在模具内以一定的温度停留,然后在下次注射时注入模腔内成为制品。这种方法改善了胶Βιβλιοθήκη 的利用率,同时还节省了胶料和能源。
7.气体辅助注射成型
这种成型工艺是注射机向模具注射进料量不足的胶料,然后通过注射机喷嘴、模型主流道或分流道把气体 ( 一般为氮气 ) 向模腔注入,使在逐渐冷却中的胶料全部进入模腔内部。这种方法能有效地降低原材料的消耗、节省能源和提高制品质量。
[2004-09-08]
一、橡胶注射成型设备的技术进步主要包括以下几个方面:
1.橡胶注射成型设备主机的技术进步
橡胶注射成型机的发展,经历了柱塞式注射成型机至螺杆柱塞式注射成型机,再至螺杆往复式注射成型机的过程。近年来,各行业对橡胶制品质量提出了更高的要求,市场对大型橡胶制品的需求量也大增。目前大中型橡胶制品一般采用螺杆柱塞式注射成型机,较小型的则可采用螺杆往复式注射成型机。
8.橡胶注射成型设备自动化的技术进步
在橡胶注射机中,工业化国家的竞争主要体现在控制系统和自动化程度上的竞争,从而使设备的控制系统和自动化得到迅速发展。近年来,可编程控制器有了很大的发展,并赋予微机的功能,出现了执行联机的统计工程控制 (SPC) 、计算机集成管理生产控制 (CM) 、分级数据收集和处理控制 (Mm) 以及信息控制管理系统 (MCS2) 等等。这些控制器具有数据采集功能强,数据处理能力强,存储量大,运算速度快,精度高以及传递通讯能力强等优点,使橡胶注射机的控制水平得到突破性进展。
二、橡胶注射成型设备的最新发展动向包括以下几个方面:
1.用途拓展
橡胶注射成型设备及其相关的工艺经过几十年的实践和研究已经比较成熟。但是目前其用途还是停留在一些传统的常规橡胶制品上,也就是说,许多橡胶制品仍然采用平板硫化的模压方法,这是对一种具有高质、高效、先进的橡胶注射成型技术的浪费。从一般原理来说,能用平板硫化机模压方法生产的橡胶制品都能使用橡胶注射方法来生产。随着技术的进一步发展,越来越多的橡胶制品都将会采用注射成型方法,包括轮胎胎冠、胎侧、实芯轮胎、深井油田高温螺旋泵衬套、码头护舷、各种橡胶胶囊、橡胶浮标、汽车橡胶配件、轮胎翻新以及各种工业胶辊等等。