液体硅橡胶(LSR)注射成型工艺的设计
多通道手术操作平台(LSR液态硅胶)工艺浅析

多通道手术操作平台(LSR液态硅胶)工艺浅析来源:东昊模具1液态硅胶多孔平台的功能多通道手术操作平台(以下简称多孔平台)有多个通道,穿刺套管从该孔内穿过,下端卡接有腰鼓形的底座,底端连接有碗形密封圈,既起到密封作用又起到保护作用。
2液态硅胶多孔平台的特点多孔平台采用液态硅胶(LSR)材料方式,一方面耐磨,耐高温,重复灭菌性高,另一方面整体密封性较好,回弹性,耐水防水性都较好。
液态硅胶多孔平台▲3液态硅胶多孔平台结构特征难点产品结构复杂,且整体深孔腔体结构较多,易产生困气现象,对模腔抽真空要求较高,且入子拆分较多,易产生毛边,表面光洁度高,易产生静电灰尘吸附导致的脏污、手指纹等。
4液态硅胶多孔平台的模具特征多孔平台对应的模具结构精密,其产品外观要求较高,尤其是液态硅胶流动性好,易跑毛边,对模具的整体精度要求高,多深腔孔结构特征导致产品极易困气,对模具的排气以及抽真空要求更高。
模具穴数主要采用1*2的排位方式,依据产品多种结构特征,有1+1排位方式,进胶方式为热嘴大水口侧进胶。
5多孔平台的常见问题分析及解决方案1.产品尺寸超差:分析:模具设计缺陷,模具加工精度不够,模架精度不够,及尺寸管控不到位导致。
方案:(1) 模具设计上,重点尺寸需标注清晰,公差标注合理,各工序针对重点尺寸及装配尺寸,从零件加工到装配组立,均需严格量测管控到位;(2) 模架精度也要保证开框精度及定位精度;(3) 根据所选硅胶材料的物性表及产品本身结构特征抓取准确的收缩率。
2.产品毛边分析:多孔平台结构复杂,入子拆分较多,本身液态硅胶流动性好,溢边值小,分模面,入子处等极易产生毛边,对模具整体加工精度及各镶件的配合精度要求较高。
方案:(1) 模具设计需要合理严谨,综合评估液态硅胶材料特性,并定义各工件的尺寸公差装配要求;(2) 镶件和模仁的配合尺寸精度需加工管控到位;(3) 需要设计合理的撕边槽结构。
3.多孔平台抽抽真空结构浅析多孔平台结构复杂,深腔结构多,入子拆分较多,产品结合线较多,极易产生困气现象,需做抽真空机构才能较好解决困气现象,但入子拆分多及产品结构复杂,实现完全抽真空需要的密封结构更复杂,同步要确保模腔实际完全实现抽真空,才能较好的解决产品困气现象。
液体硅橡胶LSR注射成型工艺的设计

液体硅橡胶L S R注射成型工艺的设计seek; pursue; go/search/hanker after; crave; court; woo; go/run after液体硅橡胶LSR注射成型工艺的设计在过去的三到五年里,热固性液体硅橡胶LSR的注塑技术得到了快速的发展.LSR的注塑设计与刚性工程热塑料有着重要的差别,这主要是因为这两种橡胶的物理性质,如低粘度,流变学性质快速固化,剪切变稀性质,以及较高的热膨胀系数等区别较大.由于LSR的粘度较低,因此它在注射成型过程中,即使在注射压力较低的情况下,填充流速也可以较快,但是为了避免空气滞留,对模具通风的要求更加严格.总的来说,现代LSR的快速硫化的循环时间更短某些情况下循环时间不到20秒,为了充分利用这一特性,加工机械、注射成型机以及部件转移系统等必须相互配合,作为一个高度集成的整体运作.冷流道成型现代冷流道体系充分利用了LSR剪切变稀的性质,真正达到了无浪费,无毛边成型.在过去的三到五年里,冷流道模塑在制造业中的优势地位急速上升,并导致橡胶产品的产量增加、废品减少、劳动成本降低等良好的势头.LSR不会在模具中收缩,这一点和热塑性塑料类似.但是由于膨胀系数较高,加热时会发生膨胀,冷却时却仅有微小的收缩.因此,部件通常不能在模具中保持准确的侧边距,只有在表面积较大的空腔中才可以保持.与热流道模塑相似,在冷流道加工中,热固LSR应保持较低温度和可流动性,以确保没有物料的损失.这种加工方法最适用于在清洁的室内环境中生产大小、结构相似的大体积部件.理想模型是在人为因素影响最小的设备中昼夜不停的运转,并逐步增大运转周期日或周.目前所用的冷流道设备有两种基本类型,即闭合系统和开放系统,它们各有优缺点.注射循环中,闭合系统在每一个管道中都采用“开动销”或“针形阀”来控制LSR橡胶的流量.而开口系统则根据注射压力的大小,利用“收缩嘴”和阀门来控制物料的流量.与开口系统相比较,闭合系统最典型的特点是在较低的注射压力下进行注塑.设备中可调控的“节流口”可以对不平衡的分流道以及物料的不同剪切变稀性能进行微调.缺点是对某些给定大小的部件和模具,设备需作额外的调整.开放系统利用通过喷嘴或者阀门的高剪切速率,在注射压力降低时,进行截流.一般情况下,开放系统的空腔填充时间要比闭合系统稍微短一些.开放系统由于分流道和喷嘴较小,空腔密度较高.分流道则要求自然平衡,并与物料本身的流变性能严格匹配.因为开放系统的流道尺寸较小,所以通常不用可调“节流口”,只需普通阀门就可以很好的控制流量,并获得最佳的压力点.分模线设计液体硅橡胶注射成型模具时,首先要考虑分模线的位置,因为分模线内部需设置一些通道,利用这些通道完成通风任务,通风孔必须设置在注射物料最后到达的模具末端.预先考虑以上因素,有助于避免空气的夹带和焊接线边缝强度的损失.由于LSR的粘度低,所以必须确保分模型线的精确度,避免出现毛边.虽然如此,最终产品上的分模线清晰可见.部件的几何形状和分模线的位置还会影响脱膜过程.在部件设计中,轻微的根切有助于确保被塑部件与模具空腔之间坚固的结合在一起.收缩虽然液体硅橡胶在注射成型过程中没有收缩,但是由于硅橡胶具有较高的热膨胀系数,因而在脱膜、冷却后通常会有2%-3%的收缩.确切的收缩数据主要取决于物料配方,但是从加工的观点来看,设计者如果在构思的时候,预先对影响收缩的一些因素有所考虑的话,最后的收缩情况会有所变化,这些因素主要包括加工的温度,物料脱膜的温度,空腔压力等.另外要考虑的是注入口的位置,因为通常物料在流动方向上的收缩要比其垂直方向的收缩来得明显些.另外,部件的尺寸也是一个影响因素,一般来说,部件越厚,收缩越小如果在实际应用中要求二次硫化,则还要考虑额外增加0.5%-0.7%的收缩.通风当模具空腔关闭时,空气滞留在内,随着LSR的注射,空气首先被挤压,接着逐渐被填料赶出空腔,由于LSR的粘度较低,空腔很快被填充.在快速填料过程中,如果空气不能完全被赶出空腔,将会夹带在硫化后的物料中通常表现为沿部件周边一圈白边或是内部光滑的小气泡.典型的通气管道宽1-3mm,深0.004-0.005mm,现已成功应用于生产中.排除空腔滞留空气的最佳方法,是在每一个注射成型循环中,采用抽真空的办法将空腔中滞留空气赶走.就是说,在设计分模线时确保模具密闭,真空泵通过模具开关下面的夹具将所有空腔抽真空.一旦真空度达到预想标准要求,立刻关闭模具,开始注射.还有一种成功应用的方法是,利用调节夹具力度达到赶走空气的目的.制造者在夹具力较低时LSR 填充至空腔的90%-95%,之后再将夹具力度调高,同时避免积压液体硅橡胶溢出,产生毛边.注入口一个合适的加工设计,既希望阀门的痕迹小而坚固,又希望阀门的位置不易察觉,这是非常困难的.但是如果将阀门设置在非临界区域或内表面上,就可以避免很多麻烦,例如前面提到的,利用冷流道系统进行LSR材料的注射成型就可以省去注入口痕迹的消除,从而避免了劳动集约型的生产过程和大量物料的浪费.很多情况下,无注入口设计也将缩短循环时间.如果采用冷流道系统,在热空腔与冷流道之间设置有效的隔离温度是十分重要的.如果分流道太热,物料在注射前就开始固化,而如果冷却太快的话,它会从模具阀门区域吸收过多热量,防碍固化的完成.闭合系统的阀门或是开动销,一般设计为0.5-0.8mm之间,以保证销和它周围流动的物料的活动空间.而开口系统中,喷嘴和阀门通常要小一些0.2-0.5mm,这样可以较好的控制流量.对于低粘度的LSR来讲,若是通过传统注入口注入物料,例如潜伏式阀门或是锥形阀门,那么喂料直径要略小些.注入口直径通常在0.2-0.5mm之间.脱模除非是较特殊的配方,一般固化LSR容易粘在金属表面上,这给脱模带来了一定的困难.虽然如此,目前LSR橡胶的热撕裂强度还是能够满足脱模要求的,在脱模后基本没有损失.应用最为普遍的脱模技术设备,包括分馏柱塔板,推顶销和空气推顶.其他应用较多的方法包括滚筒扫除机,排除塔,和机器人操作.使用推顶系统时,必须使推顶系统保持在相近的公差范围内.如果推顶销和套管之间清除过度,或是元件磨损时间过长,都会引起部件毛边的出现.反锥形或蘑菇形推顶器的接触压比较大,可增进系统的密闭性,因而功效很强.模具材料一般情况下,护圈板都是采用非合金加工钢no.1.1730,DINcodeC45W来制造的.由于模板要暴露在170℃-210℃的高温下,所以应该采用预回火的钢材no.1.2312,DINcode40CrMnMoS86制造,以提高抗冲压性能.具有空腔的模板最好采用耐温性好的弹性热钢为材料.针对像抗油品级这类高填充LSR材料,推荐使用更强硬的材料,例如镀铬钢和粉末金属都在这一应用上有了较大的发展钢.在为研磨性物料制作模具时,要注意使用特别的插件或者其他可替换加工工具,这样元件磨损后可以单独替换,而不必更换整个模具.模具空腔表面的优劣对部件的品质有重要的影响,简单讲,铸好的部件会将模具空腔的原貌准确的复制下来.抛光钢对于透明部件显得十分重要.表面经过处理的钛/镍钢具有很高的抗磨损能力,而PTFE/镍更加容易脱膜.LSR材料在某种程度上具有研磨特性,因而最好不要选择铝质材料.在经济条件允许的情况下,选用最好的金属材料,以便得到更好的相容性,同时便于由粗产品加工为最终产品.温度控制LSR成型工艺中,典型的加热方式是电加热,通常采用电热丝加热器、加热管或者加热盘.LSR的一次型固化过程中,模具内温度的均匀分配是非常重要的.在大型模具中,最经济的加热方法是“油温控制法”.用绝缘板包裹模具,也有助于减少热损失.如果表面温度下降过快,会使物料的固化速度降低,不断抑制部件的释放,影响部件的品质.加热器与分模线之间保留一段距离,可以大大避免模板的弯曲与变形,但是会使铸好的部件出现毛边.如果模具是为冷流道系统设计的,那么在冷热界面上必须有适合的隔离,这是必不可少的.像3.7165TiAl6V4这样的钛合金,相比其他钢材料来说,其热导性能差,因此是冷热隔离的良好材料.对于整体模具加热体系,应该在模具与模板之间放置绝缘层,把热损失降低到最小.模拟设计LSR分流道系统中,LSR将均匀填充所有的模具空腔,在这样的一个体系中,LSR分流道规划的平衡显得十分重要.采用电脑物流动力学模拟软件来设计分流道阀门和通风口,可以帮助模具的改进,避免反复试错法的高消耗.其实验结果可以用填充研究来论证,但是,正确的模拟要求工程师对所注塑的LSR配方的机械反应性能了如指掌.利用有限元分析法进行部件设计的实验,可忽略高应力区.小结予以恰当的设计和规划,LSR材料的注射成型是一项经济收益好,操作相对简洁的生产工艺.充分理解注射成型与流程设计的原则,制造者即可在避免出现问题的同时,进行高效生产,相信LSR出色的空腔填充性能和快速硫化特性,必将带来高品质、高产出的工业效应.来源:机电之家·机电行业电子商务平台。
液态硅胶成型概述

LSR对环境是安全的,可降解性 3、卫生安全
5
LSR是一种新兴的环保材料
如今,LSR渐渐从高端制品的神坛上走下来,为广大的民众所
接受。如今广泛应用于健康用品、汽车、婴儿用品、医疗用品、潜水
7
LSR的成型过程
卧式液态硅胶成型系统
8
LSRLSR的成型过程
LSR成型系统与普通的注塑机的区别 1、LSR是热固性材料。
2、LSR的流动性很好,所以对锁模力和注射压力要求不高,但对射 胶精确性要求更高。
3、LSR的排气相对较难,排气间隙一般为0.02mm。所以对模具精度 要求更高。
4、料筒与进胶冷却
5、螺杆需带混炼头的螺杆
10
应用实例
11
1
LSR是一种新兴的环保材料 与固态硅胶的区别。
1、更具卫生安全性 A、过氧化合物硫化体系。(固体硅胶) B、铂金硫化体系(液态硅胶)
2、更高效 3、更节省人工 (不再需要炼胶、切胶、人工投料、清理飞边等工序)
2
LSR是一种新兴的环保材料
现在液态硅胶代替固态硅胶越来越成为一种不可逆转的趋势。这给 注塑成型带来新的发展机会。
3
LSR是一种新兴的环保材料
LSR燃烧之后的残留物。 SiO2+CL2(氯硅烷)--水解成D3、D4、D5---聚成大分子+封端剂---液态硅
胶 燃烧生成物:白碳黑(SiO2) 烟(硅油),白烟的原因(SiO2) 。没有碳燃烧,因为碳化合物燃烧所
以会呈现黑烟。
4
LSR是一种新兴的环保材料
LSR是目前塑料最安全的替代材料 1、价格问题
液态硅橡胶模具设计要点

液态硅橡胶模具设计要点摘要该文介绍了液态硅橡胶模具设计的若干要点,旨在提高液态硅橡胶制品的质量和产量,使加工者获益匪浅。
关键词:LSR;固化;充模;注压热固性液态硅橡胶(LSR)注压模具的结构,总的来说跟热塑性胶料所用的模具结构相似,但也有不少显著差别。
例如,LSR胶料一般粘度较低,因而充模时间很短,即使在很低的注射压力下也是如此。
为了避免空气滞留,在模具中设置良好的排气装置是至关重要的。
另外,LSR胶料在模具内不会像热塑性胶料那样收缩,它们往往遇热膨胀,遇冷轻微收缩。
因而,其制品并不总是如所期望的那样留在模具的凸面上,而是滞留在表面积较大的模腔内。
1 收缩率虽然LSR并不会在模内收缩,但它们在脱模和冷却后,常常会收缩2.5%-3%。
至于究竟收缩多少,在一定程度上取决于该胶料的配方。
不过,从模具角度考虑,收缩率可能受到几种因素的影响,其中包括模具的温度、胶料脱模时的温度,以及模腔内的压力和胶料随后的压缩情况。
注射点的位置也值得斟酌,因为胶料流动方向的收缩率通常比与胶料垂直流动方向的收缩率大一些。
制品的外形尺寸对其收缩率也有影响,较厚的制品的收缩率一般要比较薄者小。
如果需进行二次硫化,则可能再额外地收缩0.5%-0.7%。
2 分型线确定分型线的位置是设计硅橡胶注压模具的前几个步骤之一。
排气主要是通过位于分型线上的槽沟来实现的,这样的槽沟必经处在注压胶料最后到达的区域内。
这样有助于避免内部产生气泡和降低胶接处的强度损失。
由于LSR粘度较低,分型线必须精确,以免造成溢胶。
即便如此在定型的制品上还常能看见分型线。
脱模受制品的几何尺寸和分型面位置的影响。
将制品设计成稍有倒角,有助于保证制品对所需的另一半模腔有一致的亲合力。
3 排气随着LSR的注入,滞留在模腔内的空气在模具闭合时被压缩,然后随着充模过程而通过通气槽沟被排出。
空气如果不能完全排出,就会滞留在胶料内(这样往往会造成制品部分露出白边)。
通气槽沟一般宽度为lmm-3mm,深度为0.004mm-0.005mm。
LIM&LSR液体硅橡胶加工成型及应用

自动化对比 (1)
设备投资 模具维修保养 脱模形式 每啤时间 原料损耗 后加工处理
全自动化生产线
(冷流道模具系统 + 卧式注射成型设备)
半自动化生产线
(传统流道模具 + 立式注射成型设备)
相对较高
相对较低
4百万次注射开合后
90万次注射开合后
全自动
手动(如需)
20-30 秒 / 啤
35-90 秒 / 啤 (手动操作)
主要因素
機密文件
Copyright © 2007 硅橡膠服務有限公司·版權所有·不得轉載
生产线录像
全自动化生产线 —— 婴儿奶咀
• 迈图Momentive LSR2650-pailkit-TH; • 6腔针阀式冷流道模具系统; • 卧式注射成型设备(百科MT-90MI-LSR); • 物料供应输送系统(2KM SilcoStar 922A)。
用解决方案。
香港·新界·荃灣 柴灣角街83-93號·榮興工業大廈4樓4室 電話: (852) 2889 2521 傳真: (852) 2557 3787
機密文件
Copyright © 2007 硅橡膠服務有限公司·版權所有·不得轉載
液體硅橡膠
香港·新界·荃灣 柴灣角街83-93號·榮興工業大廈4樓4室 電話: (852) 2889 2521 傳真: (852) 2557 3787
香港·新界·荃灣 柴灣角街83-93號·榮興工業大廈4樓4室 電話: (852) 2889 2521 傳真: (852) 2557 3787
機密文件
Copyright © 2007 硅橡膠服務有限公司·版權所有·不得轉載
行业应用
电子电力
• 避雷器 • 绝缘子 • 阳极帽 • 按键 • 电线 • 中空套管 • 胶辊
液体硅橡胶复合外套产品成型工艺的研究

偶联剂干燥条件Z 25 !下干燥 40 min RH 为 90%O
胶料硫化温度Z 120 !O 硫化时间对环氧板粘接强度的影响见表 5O
表5 硫化时间对环氧板粘接强度的影响
硫化时间 / min 15 30 60 75 90
剥离强度 / kN~m-1
Key words iiguid siiicon rubber; coupiing agent; adherent strength; vuicanizing process
0 前言
液体硅橡胶(简称 LSR 材料具有优良的电性能
为外绝缘产品的硫化工艺O
1 实验
和耐候性a 已被广泛应用于避雷器\ 绝缘子等产品 !!! 实验材料
生产出了避雷器\ 绝缘子\ 电容器套管和互感器套 !!" 实验仪器
管等产品O 笔者主要研究了偶联剂的干燥条件\ 胶
选用 WOB-500B 型 拉 力 试 验 机 a 江 都 试 验 机
料 的 硫 化 工 艺 对 界 面 强 度 的 影 响 a 确 定 了 以 LSR 器厂生产O OS37 型高压电桥a 上海精密科学仪器
收稿日期 2006-12-18
作者简介 焦芳(1963- a 女a 陕西蒲城人a 高级工称师a 主要从事有机材料配方及工艺的研究工作O
!
2007年第 1 期
电瓷避雷器
(总第 215 期>
有限公司生产O 1!3 性能检测
T 剥离强度的测定: 将已抽过真空的 LSR 混 合物? 在 涂有 偶 联 剂(其中 60 mm#20 mm#2 mm 的 部 分 涂 抹 脱 模 剂 >的 环 氧 玻 璃 丝 绝 缘 板 (160 mm# 20 mm#2 mm>上 制 成 160 mm#20 mm#2 mm 的 硅 橡 胶 胶 样 ? 要 求 胶 样 的 厚 度 应 均 匀 一 致 O 按 照 GB/ T279011995 测定剥离强度O
液态硅胶(LSR)冷流道介绍

硅橡胶(LSR)特点:
无毒性:对人体无毒 ,无嗅无味,透明度好,可消毒; 耐热性:具有良好的耐热性,长时间持续工作温度达150℃; 耐寒性:良好的低温性能,在-50℃仍具有较好的弹性; 电能性:优良的电绝缘性,硅橡胶具有很高的电阻率,在很宽的温度和频率范围内其阻值保持稳定,同时硅
3)浇注系统更少,成型周期更短,可实现更少的材料损耗,更加节省材料;
4)冷嘴可安装在流道板上,也可以安装在模具上;
5)每个冷咀的冷却水路单独控制,以保证每个冷咀温度一致、平衡;
6)阀针、阀套采用进口钢材,特殊处理工艺,更耐磨耐腐蚀,高精准配合公差, 减少卡针、漏胶
2点冷流道
德恩特冷流道型号: CRM型
硅胶的粘合条件:
在双料成型过程中,硅胶的溶合条件是被溶合的底料;
可溶合不同的底料有:
双料成型工艺参数
液态硅胶生产工艺: 液态硅胶生产设备:
冷流道特点:
1)流道采用开放形式,保证流道光滑无死角,方便清理与维护;
2)冷流道一般为冷半模系统,带有气动阀针式冷嘴,为硅胶注塑成型模具的制 造提供优势,节省时间,提高效率;
硅橡胶(LSR)成型工艺:
由于液态硅橡胶低粘度性,在加工过程中要考虑材料的回流和漏胶,因此对螺杆的止逆环有较高要求,以保 证注射入模具的液体硅胶料量准确,不会出现披锋,对模具封胶位有较高要求,最好在模具中加装抽真空结 构,以保证模腔内的空气及时排出。
对工艺参数要求调整合适的流化时间及模温以保证产品能完全固化和不发生变形,一般不用到保压,但要求 精确设定料量;
LSR技术综述
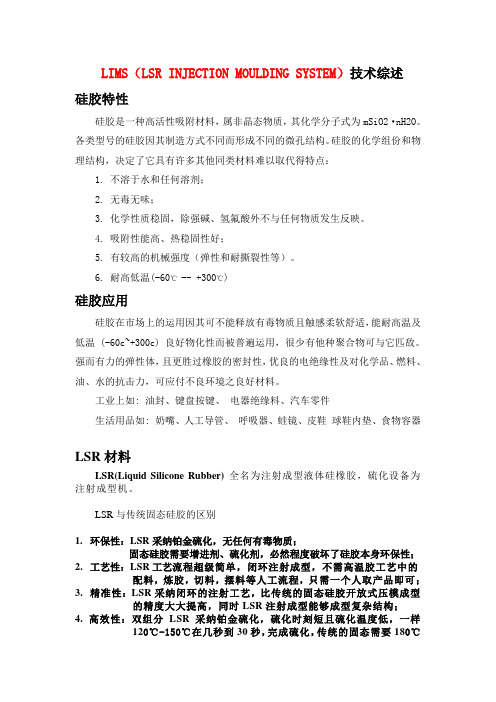
LIMS(LSR INJECTION MOULDING SYSTEM)技术综述硅胶特性硅胶是一种高活性吸附材料,属非晶态物质,其化学分子式为mSiO2·nH2O。
各类型号的硅胶因其制造方式不同而形成不同的微孔结构。
硅胶的化学组份和物理结构,决定了它具有许多其他同类材料难以取代得特点:1.不溶于水和任何溶剂;2.无毒无味;3.化学性质稳固,除强碱、氢氟酸外不与任何物质发生反映。
4.吸附性能高、热稳固性好;5.有较高的机械强度(弹性和耐撕裂性等)。
6.耐高低温(-60℃-- +300℃)硅胶应用硅胶在市场上的运用因其可不能释放有毒物质且触感柔软舒适,能耐高温及低温 (-60c~+300c) 良好物化性而被普遍运用,很少有他种聚合物可与它匹敌。
强而有力的弹性体,且更胜过橡胶的密封性,优良的电绝缘性及对化学品、燃料、油、水的抗击力,可应付不良环境之良好材料。
工业上如: 油封、键盘按键、电器绝缘料、汽车零件生活用品如: 奶嘴、人工导管、呼吸器、蛙镜、皮鞋球鞋内垫、食物容器LSR材料LSR(Liquid Silicone Rubber) 全名为注射成型液体硅橡胶,硫化设备为注射成型机。
LSR与传统固态硅胶的区别1.环保性:LSR采纳铂金硫化,无任何有毒物质;固态硅胶需要增进剂、硫化剂,必然程度破坏了硅胶本身环保性;2.工艺性:LSR工艺流程超级简单,闭环注射成型,不需高温胶工艺中的配料,炼胶,切料,摆料等人工流程,只需一个人取产品即可;3.精准性:LSR采纳闭环的注射工艺,比传统的固态硅胶开放式压模成型的精度大大提高,同时LSR注射成型能够成型复杂结构;4. 高效性:双组分LSR采纳铂金硫化,硫化时刻短且硫化温度低,一样120℃-150℃在几秒到30秒,完成硫化,传统的固态需要180℃-230℃在60-200秒完成硫化;5. 自动化:LIMS技术基于精细流量操纵、精准注塑、周密模具和高稳定操纵系统,能够完成传统硅胶工艺不能完成的产业自动化升级;LSR产品及应用领域汽车领域:耐高温、耐候、周密性能为汽车发动机相关配件提供大量量弹性密封件方案日用品:环保性、人体舒适性和可高温消毒性在高端日用品领域的应用医疗产品:无毒性、生物相容性性和可高温高压消毒性取代塑料弹性体其他新拓展领域:LIMS简介一.工艺简介:硅橡胶成型工艺种类LSR成型工艺示用意图一图二LIMS系统由三大系统组成:①供料系统:双组分的物料及色剂料,由周密定量泵,通过静态混合器输送到射出成型机;②射出成型系统:借鉴塑料注塑成型机技术,提升注射精度和单向射出操纵;③模具系统:包括冷流道针阀模块、模具加热隔热(冷热切换)模块、取件模块;二.设备技术1.供料系统:因液态硅胶材料是双组分1:1(A+B)混合后硫化成型,且要求混合比例精度极高,不然材料难以硫化或成型后性能大大降低,同时因产品颜色的多样性,一样需要输入一样是液态物性的色剂(一样称第三剂)材料,故需要精准稳固的计量混配技术,包括精准定量供给及快速混合技术。
- 1、下载文档前请自行甄别文档内容的完整性,平台不提供额外的编辑、内容补充、找答案等附加服务。
- 2、"仅部分预览"的文档,不可在线预览部分如存在完整性等问题,可反馈申请退款(可完整预览的文档不适用该条件!)。
- 3、如文档侵犯您的权益,请联系客服反馈,我们会尽快为您处理(人工客服工作时间:9:00-18:30)。
液体硅橡胶(LSR)注射成型工艺的设计
在过去的三到五年里,热固性液体硅橡胶(LSR)的注塑技术得到了快速的发展。
LSR的注塑设计与刚性工程热塑料有着重要的差别,这主要是因为这两种橡胶的物理性质,如低粘度,流变学性质(快速固化),剪切变稀性质,以及较高的热膨胀系数等区别较大。
由于LSR的粘度较低,因此它在注射成型过程中,即使在注射压力较低的情况下,填充流速也可以较快,但是为了避免空气滞留,对模具通风的要求更加严格。
总的来说,现代LSR的快速硫化的循环时间更短(某些情况下循环时间不到20秒),为了充分利用这一特性,加工机械、注射成型机以及部件转移系统等必须相互配合,作为一个高度集成的整体运作。
冷流道成型
现代冷流道体系充分利用了LSR剪切变稀的性质,真正达到了无浪费,无毛边成型。
在过去的三到五年里,冷流道模塑在制造业中的优势地位急速上升,并导致橡胶产品的产量增加、废品减少、劳动成本降低等良好的势头。
LSR不会在模具中收缩,这一点和热塑性塑料类似。
但是由于膨胀系数较高,加热时会发生膨胀,冷却时却仅有微小的收缩。
因此,部件通常不能在模具中保持准确的侧边距,只有在表面积较大的空腔中才可以保持。
与热流道模塑相似,在冷流道加工中,热固LSR应保持较低温度和可流动性,以确保没有物料的损失。
这种加工方法最适用于在清洁的室内环境中生产大小、结构相似的大体积部件。
理想模型是在人为因素影响最小的设备中昼夜不停的运转,并逐步增大运转周期(日或周)。
目前所用的冷流道设备有两种基本类型,即闭合系统和开放系统,它们各有优缺点。
注射循环中,闭合系统在每一个管道中都采用“开动销”或“针形阀”来控制LSR橡胶的流量。
而开口系统则根据注射压力的大小,利用“收缩嘴”和阀门来控制物料的流量。
与开口系统相比较,闭合系统最典型的特点是在较低的注射压力下进行注塑。
设备中可调控的“节流口”可以对不平衡的分流道以及物料的不同剪切变稀性能进行微调。
缺点是对某些给定大小的部件和模具,设备需作额外的调整。
开放系统利用通过喷嘴或者阀门的高剪切速率,在注射压力降低时,进行截流。
一般情况下,开放系统的空腔填充时间要比闭合系统稍微短一些。
开放系统由于分流道和喷嘴较小,空腔密度较高。
分流道则要求自然平衡,并与物料本身的流变性能严格匹配。
因为开放系统的流道尺寸较小,所以通常不用可调“节流口”,只需普通阀门就可以很好的控制流量,并获得最佳的压力点。
分模线
设计液体硅橡胶注射成型模具时,首先要考虑分模线的位置,因为分模线内部需设置一些通道,利用这些通道完成通风任务,通风孔必须设置在注射物料最后到达的模具末端。
预先考虑以上因素,有助于避免空气的夹带和焊接线边缝强度的损失。
由于LSR的粘度低,所以必须确保分模型线的精确度,避免出现毛边。
虽然如此,最终产品上的分模线清晰可见。
部件的几何形状和分模线的位置还会影响脱膜过程。
在部件设计中,轻微的根切有助于确保被塑部件与模具空腔之间坚固的结合在一起。
收缩
虽然液体硅橡胶在注射成型过程中没有收缩,但是由于硅橡胶具有较高的热膨胀系数,因而在脱膜、冷却后通常会有2%-3%的收缩。
确切的收缩数据主要取决于物料配方,但是从加工的观点来看,设计者如果在构思的时候,预先对影响收缩的一些因素有所考虑的话,最后的收缩情况会有所变化,这些因素主要包括加工的温度,物料脱膜的温度,空腔压力等。
另外要考虑的是注入口的位置,因为通常物料在流动方向上的收缩要比其垂直方向的收缩来得明显些。
另外,部件的尺寸也是一个影响因素,一般来说,部件越厚,收缩越小如果在实际应用中要求二次硫化,则还要考虑额外增加0.5%-0.7%的收缩。
通风
当模具空腔关闭时,空气滞留在内,随着LSR的注射,空气首先被挤压,接着逐渐被填料赶出空腔,由于LSR的粘度较低,空腔很快被填充。
在快速填料过程中,如果空气不能完全被赶出空腔,将会夹带在硫化后的物料中(通常表现为沿部件周边一圈白边或是内部光滑的小气泡)。
典型的通气管道宽1-3mm,深0.004-0.005mm,现已成功应用于生产中。
排除空腔滞留空气的最佳方法,是在每一个注射成型循环中,采用抽真空的办法将空腔中滞留空气赶走。
就是说,在设计分模线时确保模具密闭,真空泵通过模具开关下面的夹具将所有空腔抽真空。
一旦真空度达到预想标准要求,立刻关闭模具,开始注射。
还有一种成功应用的方法是,利用调节夹具力度达到赶走空气的目的。
制造者在夹具力较低时LSR填充至空腔的90%-95%,之后再将夹具力度调高,同时避免积压液体硅橡胶溢出,产生毛边。
注入口
一个合适的加工设计,既希望阀门的痕迹小而坚固,又希望阀门的位置不易察觉,这是非常困难的。
但是如果将阀门设置在非临界区域或内表面上,就可以避免很多麻烦,例如前面提到的,利用冷流道系统进行LSR材料的注射成型就可以省去注入口痕迹的消除,从而避免了劳动集约型的生产过程和大量物料的浪费。
很多情况下,无注入口设计也将缩短循环时间。
如果采用冷流道系统,在热空腔与冷流道之间设置有效的隔离温度是十分重要的。
如果分流道太热,物料在注射前就开始固化,而如果冷却太快的话,它会从模具阀门区域吸收过多热量,防碍固化的完成。
闭合系统的阀门或是开动销,一般设计为0.5-0.8mm之间,以保证销和它周围流动的物料的活动空间。
而开口系统中,喷嘴和阀门通常要小一些(0.2-0.5mm),这样可以较好的控制流量。
对于低粘度的LSR来讲,若是通过传统注入口注入物料,例如潜伏式阀门或是锥形阀门,那么喂料直径要略小些。
(注入口直径通常在0.2-0.5mm之间。
)
脱模
除非是较特殊的配方,一般固化LSR容易粘在金属表面上,这给脱模带来了一定的困难。
虽然如此,目前LSR橡胶的热撕裂强度还是能够满足脱模要求的,在脱模后基本没有损失。
应用最为普遍的脱模技术设备,包括分馏柱塔板,推顶销和空气推顶。
其他应用较多的方法包括滚筒扫除机,排除塔,和机器人操作。
使用推顶系统时,必须使推顶系统保持在相近的公差范围内。
如果推顶销和套管之间清除过度,或是元件磨损时间过长,都会引起部件毛边的出现。
反锥形或蘑菇形推顶器的接触压比较大,可增进系统的密闭性,因而功效很强。
模具材料
一般情况下,护圈板都是采用非合金加工钢(no. 1.1730, DIN code C45W)来制造的。
由于模板要暴露在170℃-210℃的高温下,所以应该采用预回火的钢材(no.
1.2312, DIN code 40 CrMnMoS 8 6)制造,以提高抗冲压性能。
具有空腔的模板最好采用耐温性好的弹性热钢为材料。
针对像抗油品级这类高填充LSR材料,推荐使用更强硬的材料,例如镀铬钢和粉末金属都在这一应用上有了较大的发展(钢no.1.2379, DIN code X 155 CrVMo 12 I)。
在为研磨性物料制作模具时,要注意使用特别的插件或者其他可替换加工工具,这样元件磨损后可以单独替换,而不必更换整个模具。
模具空腔表面的优劣对部件的品质有重要的影响,简单讲,铸好的部件会将模具空腔的原貌准确的复制下来。
抛光钢对于透明部件显得十分重要。
表面经过处理的钛/镍钢具有很高的抗磨损能力,而PTFE/镍更加容易脱膜。
LSR材料在某种程度上具有研磨特性,因而最好不要选择铝质材料。
在经济条件允许的情况下,选用最好的金属材料,以便得到更好的相容性,同时便于由粗产品加工为最终产品。
温度控制
LSR成型工艺中,典型的加热方式是电加热,通常采用电热丝加热器、加热管或者加热盘。
LSR的一次型固化过程中,模具内温度的均匀分配是非常重要的。
在大型模具中,最经济的加热方法是“油温控制法”。
用绝缘板包裹模具,也有助于减少热损失。
如果表面温度下降过快,会使物料的固化速度降低,不断抑制部件的释放,影响部件的品质。
加热器与分模线之间保留一段距离,可以大大避免模板的弯曲与变形,但是会使铸好的部件出现毛边。
如果模具是为冷流道系统设计的,那么在冷热界面上必须有适合的隔离,这是必不可少的。
像3.7165(Ti Al 6V4)这样的钛合金,相比其他钢材料来说,其热导性能差,因此是冷热隔
离的良好材料。
对于整体模具加热体系,应该在模具与模板之间放置绝缘层,把热损失降低到最小。
模拟设计
LSR分流道系统中,LSR将均匀填充所有的模具空腔,在这样的一个体系中,LSR分流道规划的平衡显得十分重要。
采用电脑物流动力学模拟软件来设计分流道阀门和通风口,可以帮助模具的改进,避免反复试错法的高消耗。
其实验结果可以用填充研究来论证,但是,正确的模拟要求工程师对所注塑的LSR配方的机械反应性能了如指掌。
利用有限元分析法进行部件设计的实验,可忽略高应力区。
小结
予以恰当的设计和规划,LSR材料的注射成型是一项经济收益好,操作相对简洁的生产工艺。
充分理解注射成型与流程设计的原则,制造者即可在避免出现问题的同时,进行高效生产,相信LSR出色的空腔填充性能和快速硫化特性,必将带来高品质、高产出的工业效应。
来源:[]机电之家·机电行业电子商务平台!。