石油和天然气勘探中英文对照外文翻译文献
Characterization of Radar Backscatter翻译
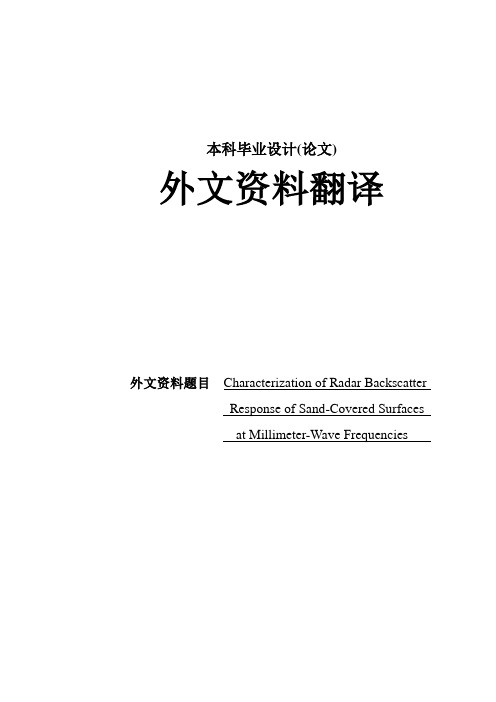
本科毕业设计(论文)外文资料翻译外文资料题目Characterization of Radar BackscatterResponse of Sand-Covered Surfacesat Millimeter-Wave Frequencies摘要摘要由于干沙的介电常数低和沙表面比较粗糙,沙漠的雷达成像会遭受不足的雷达回波低频微波信号。
然而,操作在毫米波段频率,用以矫正这一缺陷的重要雷达回波产生的表面和体积散射。
由于这样的事实,即砂表面粗糙度大,信号穿透到干砂,这是一个空气和砂颗粒尺寸与波长的一小部分的均匀混合物,产生相当大的体积散射。
本文探讨在干砂表面的面积和体积的散射,以奇特的砂表面的物理性能,发现在沙地沙丘覆盖的地区。
提出了一种非相干模型,描述了角依赖体积散射从干砂在存在一维起涟漪的空气/砂表面。
一组室内实验进行平滑和一维起涟漪的砂表面在ka波段证实,大量散射是毫米波频率,该模型正确地捕捉观察角关系当一维表面波纹出现。
关键词:毫米波(MMW)测量雷达体积散射摘要摘要目录i目录一、引言 (1)二、干砂的物理性质的表征 (5)三、干沙丘表面的造型雷达后向散射响应 (9)四、实验表征 (17)五、结论 (23)附录 (25)参考文献 (29)ii目录一、引言1一、引言世界各地的石油和天然气领域的探索,包括地区的特点是干旱或沙漠地区地震试验中经常使用的。
在这些地区,干沙层往往覆盖底层的基岩,并且其厚度变化从一个区域到下一个区域。
在沙层厚度的基石是低的沙区的地震试验通常是成功的。
如果砂层高于基岩的厚度是先验已知的,那么这些测试的成本可以显著降低。
双频干涉合成孔径雷达(SAR)测量(InSAR)已被提议作为一种映射沙层以上的基岩大面积的沙漠和干旱地区的厚度[1][2]的手段。
双频干涉合成孔径雷达的提议包含两个系统:高频和低频InSAR系统,两者都安装在一个平台上。
高频InSAR 技术被用于确定空气/砂界面的高度,而低频InSAR技术被用于确定的砂/基岩界面的高度。
石油专业外文翻译(SPE 121762),英文原文可根据spe号在百度文库收索即可。
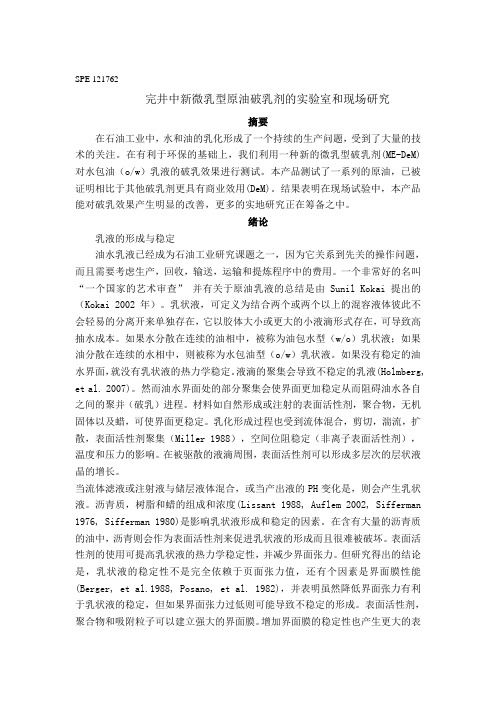
SPE 121762完井中新微乳型原油破乳剂的实验室和现场研究摘要在石油工业中,水和油的乳化形成了一个持续的生产问题,受到了大量的技术的关注。
在有利于环保的基础上,我们利用一种新的微乳型破乳剂(ME-DeM)对水包油(o/w)乳液的破乳效果进行测试。
本产品测试了一系列的原油,已被证明相比于其他破乳剂更具有商业效用(DeM)。
结果表明在现场试验中,本产品能对破乳效果产生明显的改善,更多的实地研究正在筹备之中。
绪论乳液的形成与稳定油水乳液已经成为石油工业研究课题之一,因为它关系到先关的操作问题,而且需要考虑生产,回收,输送,运输和提炼程序中的费用。
一个非常好的名叫“一个国家的艺术审查” 并有关于原油乳液的总结是由Sunil Kokai提出的(Kokai 2002年)。
乳状液,可定义为结合两个或两个以上的混容液体彼此不会轻易的分离开来单独存在,它以胶体大小或更大的小液滴形式存在,可导致高抽水成本。
如果水分散在连续的油相中,被称为油包水型(w/o)乳状液;如果油分散在连续的水相中,则被称为水包油型(o/w)乳状液。
如果没有稳定的油水界面,就没有乳状液的热力学稳定。
液滴的聚集会导致不稳定的乳液(Holmberg, et al. 2007)。
然而油水界面处的部分聚集会使界面更加稳定从而阻碍油水各自之间的聚并(破乳)进程。
材料如自然形成或注射的表面活性剂,聚合物,无机固体以及蜡,可使界面更稳定。
乳化形成过程也受到流体混合,剪切,湍流,扩散,表面活性剂聚集(Miller 1988),空间位阻稳定(非离子表面活性剂),温度和压力的影响。
在被驱散的液滴周围,表面活性剂可以形成多层次的层状液晶的增长。
当流体滤液或注射液与储层液体混合,或当产出液的PH变化是,则会产生乳状液。
沥青质,树脂和蜡的组成和浓度(Lissant 1988, Auflem 2002, Sifferman 1976, Sifferman 1980)是影响乳状液形成和稳定的因素。
油气田开发名词英汉对照
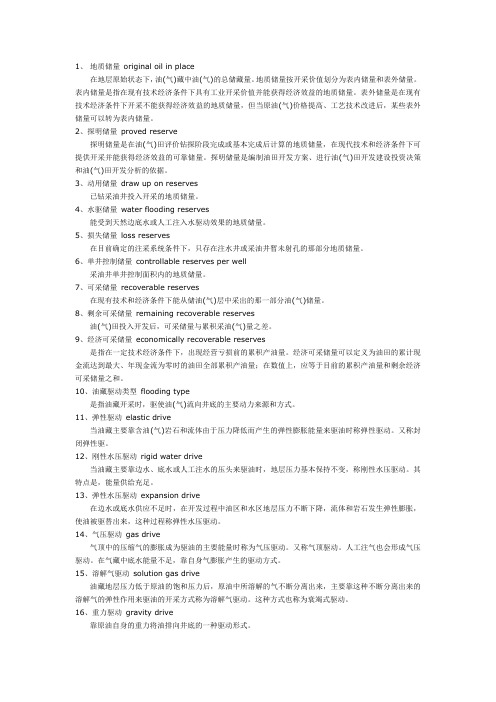
1、地质储量original oil in place在地层原始状态下,油(气)藏中油(气)的总储藏量。
地质储量按开采价值划分为表内储量和表外储量。
表内储量是指在现有技术经济条件下具有工业开采价值并能获得经济效益的地质储量。
表外储量是在现有技术经济条件下开采不能获得经济效益的地质储量,但当原油(气)价格提高、工艺技术改进后,某些表外储量可以转为表内储量。
2、探明储量proved reserve探明储量是在油(气)田评价钻探阶段完成或基本完成后计算的地质储量,在现代技术和经济条件下可提供开采并能获得经济效益的可靠储量。
探明储量是编制油田开发方案、进行油(气)田开发建设投资决策和油(气)田开发分析的依据。
3、动用储量draw up on reserves已钻采油井投入开采的地质储量。
4、水驱储量 water flooding reserves能受到天然边底水或人工注入水驱动效果的地质储量。
5、损失储量loss reserves在目前确定的注采系统条件下,只存在注水井或采油井暂未射孔的那部分地质储量。
6、单井控制储量controllable reserves per well采油井单井控制面积内的地质储量。
7、可采储量recoverable reserves在现有技术和经济条件下能从储油(气)层中采出的那一部分油(气)储量。
8、剩余可采储量remaining recoverable reserves油(气)田投入开发后,可采储量与累积采油(气)量之差。
9、经济可采储量economically recoverable reserves是指在一定技术经济条件下,出现经营亏损前的累积产油量。
经济可采储量可以定义为油田的累计现金流达到最大、年现金流为零时的油田全部累积产油量;在数值上,应等于目前的累积产油量和剩余经济可采储量之和。
10、油藏驱动类型flooding type是指油藏开采时,驱使油(气)流向井底的主要动力来源和方式。
(完整版)油气储运专业英语(英汉互译)
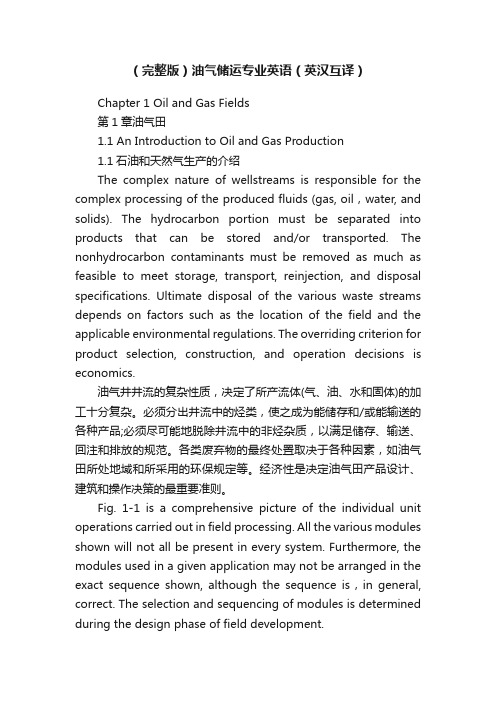
(完整版)油气储运专业英语(英汉互译)Chapter 1 Oil and Gas Fields第1章油气田1.1 An Introduction to Oil and Gas Production1.1石油和天然气生产的介绍The complex nature of wellstreams is responsible for the complex processing of the produced fluids (gas, oil,water, and solids). The hydrocarbon portion must be separated into products that can be stored and/or transported. The nonhydrocarbon contaminants must be removed as much as feasible to meet storage, transport, reinjection, and disposal specifications. Ultimate disposal of the various waste streams depends on factors such as the location of the field and the applicable environmental regulations. The overriding criterion for product selection, construction, and operation decisions is economics.油气井井流的复杂性质,决定了所产流体(气、油、水和固体)的加工十分复杂。
必须分出井流中的烃类,使之成为能储存和/或能输送的各种产品;必须尽可能地脱除井流中的非烃杂质,以满足储存、输送、回注和排放的规范。
石油专业中英文2
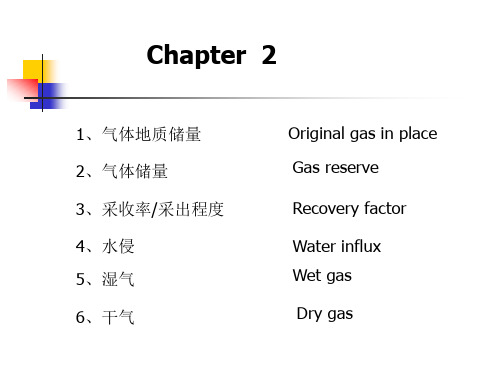
Condensate gas Gas expansion Volumetric method Pore volume(PV) Initial conditions Later conditions
13、净厚度 14、测井 15、岩心分析 16、井底压力 17、试井 18、尖灭
Net thickness Well logs Core analysis Bottomhole pressure Well tests pinchouts
49、三级脱气系统 50、高压分离器 51、储罐 52、气体偏差系数 53、凝析 54、原始露点压力
Three-stage separation system High-pressure separator Stock tank Gas deviation factor condensation Original dewpoint pressure
Water-vapour Water vaporization Gas condensation Rock expansion Condensate saturation Two-phase gas deviation factor
85、单相Z因子 86、两相Z因子 87、汽相 88、水蒸气含量
Single-phase Z factor Two-phase Z factor Vapor phase Water vapor content
55、油气田开发方案 56、占优势的 57、油藏驱动机理 58、物质平衡方程 59、侵入水 60、水驱系统
Field-development strategy predominant Reservoir drive mechanism Material-balance equation Encroaching water Waterdrive system
能源类毕业论文外文及中文翻译

土耳其的能源需求M. Mucuk andD。
Uysal经济学,经济和行政学院,塞尔丘克大学法律系,42075,科尼亚,土耳其摘要:本研究的目的是预测在土耳其使用Box-Jenkins方法论2007 —2015年期间的一次能源需求.由能源和自然资源部规定的期限1970至2006年的年度数据进行的研究中使用。
考虑到单位根检验的结果,能源需求的系列是一阶差分平稳。
位居其后的替代模型可以发现,最合适的模型是能源需求的系列ARIMA(3,1,3)。
根据这个模型,估计结果表明,能源需求也将继续增加的趋势,在预测期内。
据预计,在一次能源需求将在2015年达到119。
472 T OE与相比,应设计用于在土耳其的需求不断增加2006.因此能源政策增加约22%。
介绍经济政策的最终目标是维持社会福利水平的增加。
有必要通过有效地利用资源,以实现在社会福利的增加,以增加产量.出于这个原因,可以看出,已内化到新的增长模式的技术因素是一个快速发展。
在技术的发展也有助于在对能源的需求的增加。
事实上,在与工业革命发生在18世纪末和19世纪初,生产过程中采用新技术,以及无论在国家的基础,并在全球范围内增加能源消耗带来的。
然而,随着工业化在一起因素,例如人口和城市化也起到了作用,显著作为能源消费的增加解释变量.能量需求,这取决于上面提到的因素,表现出动态结构的未来值,是非常重要的在于要今天实施的政策方面,由于所使用在我们的日常生活中的大部分能量资源具有一个不平衡各地区和储量分布中一直在稳步下降。
上面提到的局限性迫使国家在考虑到可持续增长做出预测已经塑造他们的能源政策。
本研究的目的是预测在土耳其通过Box-Jenkins方法的基础上规定的期限1970年至2006年的年度数据对能源的需求期间二零零七年至2015年。
土耳其是不被认为是丰富的化石燃料,诸如石油,天然气和煤炭的国家之列。
出于这个原因,正确的能量需求预测携带在设计在国内实施的策略一个显著值。
热电联产中英文对照外文翻译文献
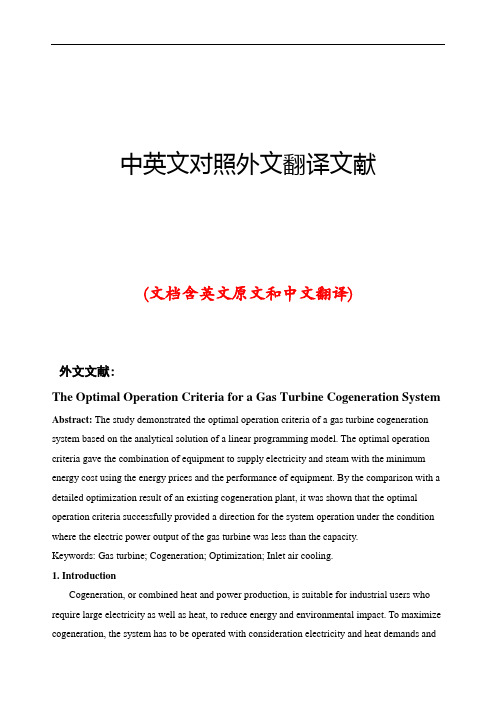
中英文对照外文翻译文献(文档含英文原文和中文翻译)外文文献:The Optimal Operation Criteria for a Gas Turbine Cogeneration System Abstract: The study demonstrated the optimal operation criteria of a gas turbine cogeneration system based on the analytical solution of a linear programming model. The optimal operation criteria gave the combination of equipment to supply electricity and steam with the minimum energy cost using the energy prices and the performance of equipment. By the comparison with a detailed optimization result of an existing cogeneration plant, it was shown that the optimal operation criteria successfully provided a direction for the system operation under the condition where the electric power output of the gas turbine was less than the capacity.Keywords: Gas turbine; Cogeneration; Optimization; Inlet air cooling.1. IntroductionCogeneration, or combined heat and power production, is suitable for industrial users who require large electricity as well as heat, to reduce energy and environmental impact. To maximize cogeneration, the system has to be operated with consideration electricity and heat demands andthe performance of equipment. The optimal operation of cogeneration systems is intricate in many cases, however, due to the following reasons. Firstly, a cogeneration system is a complex of multiple devices which are connected each other by multiple energy paths such as electricity, steam, hot water and chilled water. Secondly, the performance characteristics of equipment will be changed by external factors such as weather conditions.For example, the output and the efficiency of gas turbines depend on the inlet air temperature. Lastly,the optimal solution of operation of cogeneration systems will vary with the ratio of heat demand to electricity demand and prices of gas, oil and electricity.Because of these complexities of cogeneration systems, a number of researchers have optimal solutions of cogeneration systems using mathematical programming or other optimization techniques. Optimization work focusing on gas turbine cogeneration systems are as follows. Yokoyama et al. [1] presented optimal sizing and operational planning of a gas turbine cogeneration system using a combination of non-linear programming and mixed-integer linear programming methods. They showed the minimum annual total cost based on the optimization strategies. A similar technique was used by Beihong andWeiding [2] for optimizing the size of cogeneration plant. A numerical example of a gas turbine cogeneration system in a hospital was given and the minimization of annual total cost was illustrated. Kong et al. [3] analyzed a combined cooling, heating and power plant that consisted of a gas turbine, an absorption chiller and a heat recovery boiler. The energy cost of the system was minimized by a linear programming model and it was revealed that the optimal operational strategies depended on the load conditions as well as on the cost ratio of electricity to gas. Manolas et al. [4] applied a genetic algorithm (GA) for the optimization of an industrial cogeneration system, and examined the parameter setting of the GA on the optimization results. They concluded that the GA was successful and robust in finding the optimal operation of a cogeneration system.As well as the system optimization, the performance improvement of equipment brings energy cost reduction benefits. It is known that the electric power output and the efficiency of gas turbines decrease at high ambient temperatures. Some technical reports [5, 6] show that the electric power output of a gas turbine linearly decreases with the rise of the ambient temperature, and it varies about 5 % to 10 % with a temperature change of 10 ◦C. Therefore, cooling of the turbine inlet air enhances electric output and efficiency. Some studies have examined theperformance of the gas turbine with inlet air cooling as well as the effect of various cooling methods [7, 8, 9].The cooling can be provided without additional fuel consumption by evaporative coolers or by waste heat driven absorption chillers. The optimal operation of the system will be more complex, however, especially in the case of waste heat driven absorption chillers because the usage of the waste heat from the gas turbine has to be optimized by taking into consideration the performance of not only the gas turbine and the absorption chiller but also steam turbines, boilers and so on. The heat and electricity demands as well as the prices of electricity and fuels also influence the optimal operation.The purpose of our study is to provide criteria for optimal operation of gas turbine cogeneration systems including turbine inlet air cooling. The criteria give the minimum energy cost of the cogeneration system. The method is based on linear programming and theKuhn-Tucker conditions to examine the optimal solution, which can be applied to a wide range of cogeneration systems.2. The Criteria for the Optimal Operation of Gas Turbine Cogeneration SystemsThe criteria for the optimal operation of gas turbine cogeneration systems were examined from the Kuhn-Tucker conditions of a linear programming model [10]. A simplified gas turbine cogeneration system was modeled and the region where the optimal solution existed was illustrated on a plane of the Lagrange multipliers.2.1. The Gas Turbine Cogeneration System ModelThe gas turbine cogeneration system was expressed as a mathematical programming model. The system consisted of a gas turbine including an inlet air cooler and a heat recovery steam generator (HRSG), a steam turbine, an absorption chiller, a boiler and the electricity grid. Figure 1 shows the energy flow of the system. Electricity, process steam, and cooling for process or for air-conditioning are typical demands in industry, and they can be provided by multiple suppliers. In the analysis, cooling demands other than for inlet air cooling were not taken into account, and therefore, the absorption chiller would work only to provide inlet air cooling of the gas turbine. The electricity was treated as the electric power in kilowatts, and the steam and the chilled water were treated as the heat flow rates in kilowatts so that the energy balance can be expressed in the same units.Figure 1. The energy flow of the simplified gas turbine cogeneration system with the turbineinlet air cooling.The supplied electric power and heat flow rate of the steam should be greater than or equal to the demands, which can be expressed by Eqs. (1-2).(1)(2)where, xe and xs represent the electric power demand and the heat flow rate of the steam demand. The electric power supply from the grid, the gas turbine and the steam turbine are denoted by xG, xGT and xST, respectively. xB denotes the heat flow rate of steam from the boiler, and xAC denotes the heat flow rate of chilled water from the absorption chiller. The ratio of the heat flow rate of steam from the HRSG to the electric power from the gas turbine is denominated the steam to electricity ratio, and denoted by ρGT. Then, ρGTxGT represents the heat flow rate o f steam from the gas turbine cogeneration. The steam consumption ratios of the steam turbine and the absorption chiller are given as ωST and ωAC, respectively. The former is equivalent to the inverse of the efficiency based on the steam input, and the latter is equivalent to the inverse of the coefficient of performance.The inlet air cooling of the gas turbine enhances the maximum output from the gas turbine. By introducing the capacity of the gas turbine, XGT, the effect of the inlet air cooling was expressed by Eq. (3).(3).It was assumed that the increment of the gas turbine capacity was proportional to the heatflow rate of chilled water supplied to the gas turbine. The proportional constant is denoted byαGT.In addition to the enhancement of the gas turbine capacity, the inlet air cooling improves the electric efficiency of the gas turbine. Provided that the improvement is proportional to the heat flow rate of chilled water to the gas turbine, the fuel consumption of the gas turbine can be expressed as ωGTxGT¡βGTxAC, whereωGT is the fuel consumption ratio without the inlet air cooling and βGT is the improvement factor of the fuel consumption by the inlet air cooling. As the objective of the optimization is the minimization of the energy cost during a certain time period, Δt, the energy cost should be expressed as a function of xG, xGT, xST, xB and xAC. By defining the unit energy prices of the electricity, gas and oil as Pe, Pg and Po, respectively, the energy cost, C, can be given as:(4)where, ωB is the fuel consumpti on ratio of the boiler, which is equivalent to the inverse of the thermal efficiency.All the parameters that represent the characteristics of equipment, such as ωGT, ωST, ωAC, ωB, ρGT, αGT and βGT, were assumed to be constant so that the system could be m odeled by the linear programming. Therefore, the part load characteristics of equipment were linearly approximated.2.2. The Mathematical Formulation and the Optimal Solution From Eqs. (1–4), the optimization problem is formed as follows:(5)(6)(7)(8)where, x = (xG, xGT, xST, xB, xAC). Using the Lagrange multipliers, λ = (λ1, λ2, λ3), theobjectivefunction can be expressed by the Lagrangian, L(x,λ).(9)According to the Kuhn-Tucker conditions, x and λ satisfy the following conditions at the optimal solution.(10)(11)(12)(13)The following inequalities are derived from Eq. (10).(14)(15)(16)(17)(18)Equation (11) means that xi > 0 if the derived expression concerning the supplier i satisfies the equali ty, otherwise, xi = 0. For example, xG has a positive value if λ1 equals PeΔt. If λ1 is less than PeΔt, then xG equals zero.With regard to the constraint g3(x), it is possible to classify the gas turbine operation into two conditions.The first one is the case where the electric power from the gas turbine is less than the capacity,which means xG < XGT + αGTxAC. The second one is the case where the electric power from the gas turbine is at the maximum, which means xGT = XGT + αGTxAC. We denominate the former and the latter conditions the operational conditions I and II, respectively. Due to Eq. (12) of the Kuhn-Tucker condition, λ3 = 0 on the operational condition I, and λ3 > 0 on the operational condition II.2.3. The Optimal Solution where the Electric Power from the Gas Turbine is less than theCapacityOn the operational condition I where xG < XGT + αGTxAC, Eqs. (14–18) can be drawn on the λ1-λ2 plane because λ3 equals zero. The region surrounded by the inequalities gives the feasible solutions, and the output of the supplier i has a positive value, i.e. xi > 0, when the solution exists on the line which represents the supplier i.Figure 2 illustrates eight cases of the feasible solution region appeared on the λ1-λ2 plane. The possible optimal solutions ar e marked as the operation modes “a” to “g”. The mode a appears in the case A, where the grid electricity and the boiler are chosen at the optimal operation. In the mode b,the boiler and the steam turbine satisfy the electric power demand and the heat flow rate of the steam demand. After the case C, the electric power from the gas turbine is positive at the optimal operation.In the case C, the optimal operation is the gas turbine only (mode c), the combination of the gas turbine and the boiler (mode d) or the combination of the gas turbine and the grid electricity (mode e). In this case, the optimal operation will be chosen by the ratio of the heat flow rate of the steam demand to the electric power demand, which will be discussed later. When the line which represents the boiler does not cross the gas turbine line in the first quadrant, which is the case C’, only the modes c and e appear as the possible optimal solutions. The modes f and g appear in the cases D and E, respectively. The suppliersThe cases A through E will occur depending on the performance parameters of the suppliers and the unit energy prices. The conditions of each case can be obtained from the graphical analysis. For example, the case A occurs if λ1 at the intersection of G and B is smaller than that at the intersection of GT and B, and is smaller than that at the intersection of ST and B. In addition, the line B has to be located above the line AC so that the feasible solution region exists. Then, the following conditions can be derived.(19)(20)(21)Equation (19) means that the gas cost to produce a certain quantity of electricity and steam with the gas turbine is higher than the total of the electricity and oil costs to purchase the same quantity of electricity from the grid and to produce the same quantity of steam with the boiler.Equation (20) means that the electricity cost to purchase a certain quantity of electricity is cheaper than the oil cost to produce the same quantity of electricity using the boiler and the steam turbine. Equation (21) indicates that the reduction of the gas cost by a certain quantity of the inlet air cooling should be smaller than the oil cost to provide the same quantity of cooling using the boiler and the absorption chiller. Otherwise, the optimal solution does not exist because the reduction of the gas cost is unlimited by the inlet air cooling using the absorption chiller driven by the boiler.Figure 2. The possible cases of the optimal solution on the operational condition ISimilar ly, the following conditions can be derived for the other cases. The condition given as Eq. (21) has to be applied to all the cases below.Case B:(22)(23)Equation (22) compares the production cost of the electricity and the steam between the gas and the oil. The gas cost to produce a certain quantity of electricity and steam by the gas turbine is higher than the oil cost to produce the same quantity of electricity and steam by thecombination of the boiler and the steam turbine. Equation (23) is the opposite of Eq. (20), which means that the oil cost to produce a certain quantity of electricity by the boiler and the steam turbine is cheaper than the purchase price of electricity.Case C:(24)(25)(26)(27)Equation (24) is the opposite case of Eq. (19). Equation (25) compares the boiler and the gas turbine regarding the steam production, which is related to the mode d. In the case C, the oil cos t for the boiler is cheaper than the gas cost for the gas turbine to produce a certain quantity of steam. If the gas cost is cheaper, mode d is not a candidate for the optimal sol ution, as illustrated in the case C’. Equations (26) and (27) evaluate the effectiveness of the steam turbine and the inlet air cooling by the absorption chiller,resp ectively. The grid electricity is superior to the steam turbine and to the inlet air cooling in this case.Case D:In addition to Eq. (25),(28)(29)(30)Similarly to the case C’, the case D’ occurs if the inequality sign of Eq. (25) is reversed. Equation (28) is the opposite case of Eq. (22), which is the comparison of the electricity production between gas and oil. Equation (29) is the opposite case of Eq. (26), which is the comparison of the steam turbine and grid electricity. The gas cost to produce a certain quantity of electricity by the combination of the gas turbine and the steam turbine is cheaper than the purchase cost of the same quantity of electricity from the grid. Equation (30) gives the condition where the steam turbine is more advantageous than the inlet air cooling by the absorption chiller. The left hand side of Eq. (30) represents an additional steam required for a certain quantity of electricity production by the inlet air cooling. Therefore, Eq. (30) insists that the steam required for a certain quantity of electricity production by the steam turbine is smaller than that requiredfor the same quantity of electricity production by the inlet air cooling in this case, and it is independent of energy prices.Case E:In addition to Eq.(25),(31)(32)The case E’ occurs if Eq. (25) is reversed. Equations (31) and (32) are the opposite cases of Eqs. (27)and (30), which give the conditions where the inlet air cooling is more advantageous compared with the alternative technologies. In this case, Eq. (28) is always satisfied because of Eqs. (21) and (32).The conditions discussed above can be arranged using the relative electricity price, Pe/Pg and the relative oil price, Po/Pg. The optimal cases to be chosen are graphically shown in Figure 3 on the Po/Pg-Pe/Pg plane. When Eq. (30) is valid, Figure 3 (a) should be applied. The inlet air cooling is not an optimal option in any case. When Eq. (32) is valid, the cases E and E’ appear on the plane and the steam turbine is never chosen, as depicted in Figure 3 (b). It is noteworthy that if the inlet air cooling cannot improve the gas turbine efficiency, i.e. βGT = 0, the inlet air cooling is never the optimal solution.As the cases C, D and E include three operation modes, another criterion for the selection of the optimal operation mode is necessary in those cases. The additional criterion is related with the steam to electricity ratio, and can be derived from the consideration below.In the c ases C, D and E, λ1 and λ2 have positive values. Therefore, two of the constraints given as Eqs. (6) and (7) take the equality conditions due to the Kuhn-Tucker condition Eq. (12). Then, the two equations can be solved simultaneously for two variables which have positive values at each mode.For the mode d, the simultaneous equations can be solved under xGT, xB > 0 and xG, xST, xAC = 0.Then, one can obtain xGT = xe and xB = xs ¡ ρGTxe. Because xB has a positive value, the following condition has to be satisfied for the mode d to be selected.(33)At the mode e, one can obtain xG = xe ¡ xs/ρGT and xGT = xs/ρGT, and the following condition can be drawn out of the former expression because xG is greater than zero at this mode.(34)Similar considerations can be applied to the cases D and E. Consequently, Eq. (33) is the condition for the mode d to be selected, while Eq. (34) is the condition for the modes e, f or g to be selected. Furthermore, it is obvious that the mode c has to be chosen if the steam to electricity ratio of the gas turbine is equal to the ratio of the heat flow rate of the steam demand to the electric power demand, i.e. ρGT = xs/xe.Equations (33) and (34) mean that when the steam to electricity ratio of the gas turbine is smaller than the ratio of the heat flow rate of the steam demand to the electric power demand, the gas turbine should be operated to meet the electric power demand. Then, the boiler should balance the heat flow rate of the steam supply with the demand. On the other hand, if the steam to electricity ratio of the gas turbine is larger than the ratio of the heat flow rate of the steam demand to the electric power demand,the gas turbine has to be operated to meet the heat flow rate of the steam demand. Then, the insufficient electric power supply from the gas turbine has to be compensated by either the grid (mode e), the steam turbine (mode f), or the inlet air cooling (mode g). There is no need of any auxiliary equipment to supply additional electric power or steam if the steam to electricity ratio of the gas turbine matches the demands.Figure 3. The optimal operation cases expressed on the relative oil price-relative electricity price plane (the operational condition I).2.4. The Optimal Solution where the Electric Power from the Gas Turbine is at the MaximumIn the operational condition II, the third constraint, Eq. (8), takes the equality condition and λ3 would have a positive value. Then, Eqs. (11) and (18) yields:(35)It is reasonable to assume that ρGT ¡ !AC ®GT > 0 and ωGT ¡ ¯GT ®GT > 0 in the case ofgas turbine cogeneration systems because of relatively low electric efficiency (¼ 25 %) and a high heat to electricity ratio (ρGT > 1.4). Then, the optimal solution cases c an be defined by a similar consideration to the operational condition I, and the newly appeared cases are illustrated in Figure 4. The cases F and G can occur in the operational condition II in addition to the cases A and B of the operational condition I. Similarly to the cases C’ and D’ of the operational condition I, the cases F’ and G’ can be defined where the mode h is excluded from the cases F and G, respectively.Figure 4. The optimal solution cases on the operational condition II.In the operational condition II, the conditions of the cases A and B are slightly different from those in the operational condition I, as given below.Case A:(36)(37)Case B:(38)(39)The conditions for the cases F and G are obtained as follows.Case F:(40)(41)(42)Case G:In addition to Eq. (41),(43)(44)The case s F’ and G’ occur whenthe inequality sign of Eq. (41) is reversed. Equations (36), (38),(40), (41), (42), (43) and (44) correspond to Eqs. (19), (22), (24), (25), (26), (28) and (29), respectively.In these equations, ωGT ¡ ¯GT®GTis substituted for ωGT, an d ρGT ¡ !AC®GTis substituted for ρGT.The optimal cases of the operational condition II are illustrated on the Po/Pg-Pe/Pg plane as shown in Figure 5. Unlike the operational condition I, there is no lower limit of the relative oil price for the optimal solution to exist. The line separating the cases F and G is determined by the multiple parameters.Basically, a larger ρGT or a smaller ωST lowers the line, which causes a higher possibility for the case G to be selected.Figure 5. The optimal operation cases expressed on the relative oil price-relative electricity price plane (the operational condition II).To find the optimal mode out of three operation modes included in the cases F or G, another strategy is necessary. The additional conditions can be found by a similar examination on the variables to that done for the cases C, D and E. In the operational condition II, three variables can be analytically solved by the constraints given as Eqs. (6), (7) and (8) taking equality conditions.In the mode g, only two variables, ωGT andωAC are positive and the other variables are equal to zero.Therefore, the analytical solutions of those in the operational condition II can be obtained from equations derived from Eqs. (6) and (7) as xGT = xe and xAC = (ρGTxe ¡xs)/ωA C. Then the third constraint gives the equality condition concerning xs/xe and XGT/xe as follows:(45)where, XGT/xe represents the ratio of the gas turbine capacity to the electricity demand, and XGT/xe ·1.For mode h, the condition where this mode should be selected is derived from the analytical solution of xB with xB > 0 as follows:(46)For the mode i, xG > 0 and xAC > 0 give the following two conditions.(47)(48)For the mode j, xST > 0 and xAC > 0 give the following conditions.(49)(50)The conditions given as Eqs. (45–50) are graphically shown in Figure 6. In the cases F and G,the operational condition II cannot be applied to the region of xsxe< ρGTXGT xeand xsxe<(ωST+ρGT)XGTxe¡ωST,respectively, because xAC becomes negative in this region. The optimal operation should be found under the operational condition I in this region.3. Comparison of the Optimal Operation Criteria with a Detailed Optimization ResultTo examine the applicability of the method explained in the previous section to a practical cogeneration system, the combination of the suppliers selected by the optimal operation criteria was compared with the results of a detailed optimization of an existing plant.3.1. An Example of an Existing Energy Center of a FactoryAn energy center of an existing factory is depicted in Figure 7. The factory is located in Aichi Prefecture, Japan, and produces car-related parts. The energy center produces electricity by a combined cycle of a gas turbine and a steam turbine. The gas turbine can be fueled with either gas or kerosene, and it is equipped with an inlet air cooler. The electric power distribution system of the factory is also linked to the electricity grid so that the electricity can be purchased in case the electric power supply from the energy center is insufficient.The steam is produced from the gas turbine and boilers. The high, medium or low pressure steam is consumed in the manufacturing process as well as for the driving force of the steam turbine and absorption chillers. The absorption chillers supply chilled water for the process, air conditioning and the inlet air cooling. One of the absorption chiller can utilize hot water recovered from the low temperature waste gas of the gas turbine to enhance the heat recovery efficiency of the system.Figure 6. The selection of the optimal operation mode in the cases of F and G.3.2. The Performance Characteristics of the EquipmentThe part load characteristics of the equipment were linearly approximated so that the system could be modeled by the linear programming. The approximation lines were derived from the characteristics of the existing machines used in the energy center.The electricity and the steam generation characteristics of the gas turbine and the HRSG are shown in Figure 8, for example. The electric capacity of the gas turbine increases with lower inlet air temperatures. The quantity of generated steam is also augmented with lower inlet air temperatures.In practice, it is known that the inlet air cooling is beneficial when the purchase of the grid electricity will exceed the power contract without the augmentation of the gas turbine capacity. Furthermore, the inlet air cooling is effective when the outdoor air temperature is higher than 11 ◦C. A part of the operation of the actual gas turbine system is based on the above judgement of the operator, which is also included in the detailed optimization model.3.3. The Detailed Optimization of the Energy CenterThe optimization of the system shown in Figure 7 was performed by a software tool developed for this system. The optimization method used in the tool is the linear programming method combined with the listed start-stop patterns of equipment and with the judgement whether the inlet air cooling is on oroff. The methodology used in the tool is fully described in the reference [11].Figure 7. An energy center of a factory.Figure 8. The performance characteristics of the gas turbine and the HRSG.The Detailed Optimization MethodThe energy flow in the energy center was modeled by the linear programming. The outputs of equipment were the variables to be optimized, whose values could be varied within the lower and upper limits. To make the optimization model realistic, it is necessary to take the start-stop patterns of the equipment into account. The start-stop patterns were generated according to thepossible operation conditions of the actual energy center, and 20 patterns were chosen for the enumeration. The optimal solution was searched by the combination of the enumeration of the start-stop patterns and the linear programming method. The list of the start-stop patterns of the gas turbine and the steam turbine is given in Figure 9.The demands given in the detailed optimization are shown in Figure 10 as the ratios of the heat flow rate of the steam demand to the electric power demand on a summer day with a large electric power demand and on a winter day with a small steam demand. On the summer day, the ratio of the heat flow rate of the steam demand to the electric power demand is at a low level throughout a day. While, it is high on the winter day, and during the hours 2 to 6, the ratio exceeds 1.4 that is the steam to electricity ratio of the gas turbine.Figure 9. The start-stop patterns of the gas turbine and the steam turbine.The Plant Operation Obtained by the Detailed OptimizationThe accumulated graphs shown in Figures 11 through 14 illustrate the electric power supply and the heat flow rate of the steam supply from equipment on the summer and winter days. On the summer day, the gas turbine and the steam turbine worked at the maximum load and the electric power demand was met by the purchase from the grid for most of the day except the hours 2 to 6, at which the electric power demand was small. The inlet air cooling of the gas turbine was used only at the hours 10 and 14, at which the peak of the electric power demand existed. The steam was mainly supplied by the gas turbine, and the boiler was used only if the total heat flow rate of the steam demands by the process, the steam turbine, and the absorption。
主要石油系统中英对照表概要
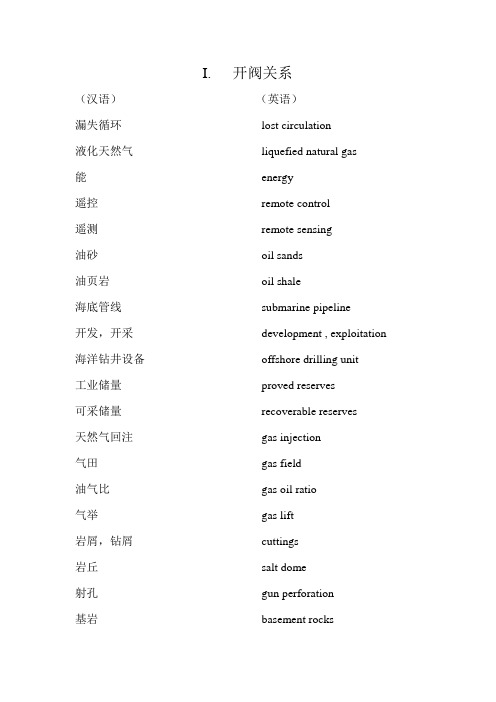
I.开阀关系(汉语)(英语)漏失循环lost circulation液化天然气liquefied natural gas能energy遥控remote control遥测remote sensing油砂oil sands油页岩oil shale海底管线submarine pipeline开发,开采development , exploitation 海洋钻井设备offshore drilling unit工业储量proved reserves可采储量recoverable reserves天然气回注gas injection气田gas field油气比gas oil ratio气举gas lift岩屑,钻屑cuttings岩丘salt dome射孔gun perforation基岩basement rocks凝灰岩tuff记录剖面record section白云岩dolomite钻井drilling钻井泥浆drilling mud采油树X ’ mas tree轻质原油light crude定向钻井directional drilling 套管casing页岩shale地质储量original oil in place 测井logging衰退率decline rate原油crude oil岩心core孔隙率porosity固定平面fixed platform舌进coning生油岩source rock采收率recovery factor砂岩sandstone供应船supply boat三次开采tertiary recovery酸处理acid treatment完井completion时间剖面time section资源resources地震勘探seismic prospecting自喷井flowing well自升式钻井装置jack-up type drilling rig重质原油heavy crude重力勘探gravitational prospecting工业的生产commercial production起始日产量initial daily production渗透率permeability深度剖面depth section注水water flooding , water injection 直井眼straight hole探明储备probable reserves伴生气associated gas抽汲swabbing灰岩limestone分离器separator半沉没的钻井semisubmersible basin固井cementing水泥cement泵站pump station沉积盆地sedimentary basin陆棚continental shelf烃,碳氢化合物hydrocarbon勘探exploration碳酸岩carbonate rocks断层fault地球化学勘探geochemical prospecting 地下构造图subsurface structural map 地槽geosyncline地质图geolgic map油管tubing阻流器choke储层reservoir低硫原油low sulphur crude泥浆mudstone泥浆路井mud logging绞车drawworks二次开采secondary recovery背斜构造anticlinal structure重晶石baritePVT试验PVT analysis生产层障害formation damage不整和unconformity地球物理勘探geophysical prospecting 压裂fracturing井喷blowout防喷器blowout preventer钻杆drill pipe兑深度total depth储量reserves井架derrick有效厚度net pay thickness生产层评价formation evaluation油田oil field预测储备possible reserves钻机rig累计产量cummulativeII.精制关系(汉语)(英语)沥青,柏油asphalt闪点flash point机油engine oil辛烷值octane number汽油gasoline粗柴油gas oil减压蒸馏vacuum distillation热解pyrolysis航空汽油aviation gasoline渣油residual oil动力汽油motor gasoline润滑油lubricating oil拔顶车间,常压蒸馏装置topping unit , atmospheric-distillation unit催化剂catalyst初沸点initial boiling point加氢精制hydrotreating氢化裂解hydrocracking稳定塔stabilizer汽提塔stripper炼油厂oil refinery分馏fractionation催化重整catalytic reforming催化裂解catalytic cracking脱蜡dewaxing油槽船tanker油槽汽车tank lorry抽提塔extractor柴油机燃料diesel fuel延迟焦化delayed coking电脱盐electric desalting柴油kerosene石脑油,粗汽油naphtha铂重整platforming反应塔reactor酮苯脱蜡B-K dewaxing裂化气cracked gas裂化汽油cracked gasoline馏出油distillate流化床催化裂变fluid catalytic cracking 倾点,流点,流动点pour point馏分fraction蜡wax渣油催化裂变RECC(Residual FCC)III.石油化学关系(汉语)(英语)丙烯酰胺acrylamide丙烯酯acrylic ester丙烯腈纤维acrylic fiber丙烯腈acrylonitrile己二酸adipic acid乙炔acetylene乙醛acetaldehyde丙酮acetone苯胺aniline烷基苯alkylbenzene氨ammonia异丁烷isobutane异丁烯isobutylene异戊二烯isoprene异丙醇isopropyl alcohol单轴延伸monoaxial stretching 乙丙橡胶EPR膨胀造型inflation modeling 丁苯橡胶SBR乙醇ethanol乙烷ethane乙苯,苯乙烷ethylbenzene乙烯ethylzene环氧乙烷ethylzene oxide乙二醇ethylzene glycol丁腈橡胶NBR环氧树脂epoxy resin甲撑双MDI氯乙烯vinyl chloride氯化chlorination辛醇octanol辛烷octane挤压模型extrusion modeling 邻二甲苯ortho-xylene烯族olefinic化学药品chemicals气gas已内酰胺caprolactam二甲苯xylene枯烯,异丙基苯cumene共聚copolymerization 甘油,丙三醇glycerine氯丁橡胶chloroprene rubber合成橡胶synthetic rubber合成树脂synthetic resin合成纤维synthetic fiber醋酸,乙酸acetic acid醋酸乙酯ethyl acetate醋酸乙烯酯vinyl acetate氧化oxidation氧oxygen环乙烷cyclohexane脂族aliphatic对酞酸二甲酯dimethyl terephthalate 注模injection modeling聚合polymerization硅橡胶silicone rubber聚硅酮树脂silicone resin氢hydrogen氢化hydrogenation水合hydration苯乙烯styrene磺化sulfonation单体monomer氮nitrogen甲苯二异氰酸脂TDI(Tolvene Diisocyanate) 癸烷decane对酞酸terephthalic acid甲苯toluene尼龙nylon环烷族naphthenic二氯乙烯EDC双轴延伸biaxial stretching尿素urea热塑塑料thermoplastics热固树脂thermosettings壬烷nonane正链烷属烃normal paraffin对二甲苯para-xylene卤化halogenation顺丁橡胶BR双酚A bisphenol A乙烯龙vinylon苯酚phenol酚醛树脂phenolic resin吹模blow modeling丁二烯butadiene丁醇butanol丁烷butane丁基橡胶butyl rubber丁烯butylene不饱和聚醋树脂unsaturated polyester resin 塑料plastics丙烷propane丙烯propylene环氧化丙烯propylene oxide丙二醇propylene glycol已二胺hexamethylene diamine已烷hexane庚烷heptane苯benzene季戊四醇pentaerythritol戊烷pentane芳族aromatic芳烃抽提aromatic extraction异戊橡胶polyisoprene聚酯纤维polyester fiber聚乙烯polyethyrene聚氯乙烯polyvinyl chloride聚苯乙烯polystyrene聚乙烯醇polyvinyl alcohol聚丙烯polypropylene高聚物polymer甲醛水formalin酞酐phthalic anhydride马来酐maleic anhydride间二甲苯meta-xylene甲醇methanol甲烷methane甲基乙基甲酮methyl ethyl ketone甲基丙烯酸甲酯methyl methacrylate三聚氰胺melamine氯乙烯单体vinyl chloride monomer。
- 1、下载文档前请自行甄别文档内容的完整性,平台不提供额外的编辑、内容补充、找答案等附加服务。
- 2、"仅部分预览"的文档,不可在线预览部分如存在完整性等问题,可反馈申请退款(可完整预览的文档不适用该条件!)。
- 3、如文档侵犯您的权益,请联系客服反馈,我们会尽快为您处理(人工客服工作时间:9:00-18:30)。
中英文对照外文翻译文献(文档含英文原文和中文翻译)OIL UNDER ICE DETECTION: WHAT IS THE STATE-OF-THE-ART?Abstract. Since the exploration for oil and gas in the Canadian and US arctic commenced in the early 1970s, a need has been identified to develop technology to detect oil under ice. Both electromagnetic and acoustic sensors have been tried, but a practical field instrument has not been identified. Most proposed systems require that the equipment be operated from the ice surface in order to get adequate coupling and, for some systems, the snow must be removed from the ice. For many icesituations, surface access is difficult and poses a severe safety issue. Two recent spills in Alberta used “high technology” ice augers to detect the presence of oil under the ice. Some potential new techniques are discussed and the basic principles of their operation described. Keywords: arctic, oil spill response, oil in ice, detection1. IntroductionThe detection of oil under continuous ice cover has presented one of the most difficult challenges to the oil-spill technological community for the past two decades and there is still no operationally proven system available. Dickins (2000) under the sponsorship of the US Minerals Management Service conducted an excellent review of the status of oil-under-ice detection and this paper complements this review with a more detailed analysis of some systems. Dickins identified many false start concepts, which will not be discussed in this paper. In order to determine the design of a suitable oil-under-ice detector, the various situations under which oil may be found under a continuous ice sheet need to be considered.The oil must come from a sub-surface release since any surface release would either be on the ice surface or in a lead or other opening in the ice. Potential sources of sub-surface oil are a leak in a pipeline, the leakage from a submerged tank or vessel or a natural seep. Oil when trapped under ice does not spread rapidly or cover a large area due to naturalroughness of the ice-water interface (Rosenegger, 1975). The situation is analogous to oil spilled on land, rather than the more dynamic situation of oil on water. Unlike the oil-on-water situation, the probable location of the source of the oil can be well defined spatially, so the search for the oil is over a relatively small confined area. Depending on the time of year, the ice may just be forming, be in a rapid growth phase, be essentially static or in a break-up situation, so that the oil may be on the surface surrounded by ice floes, at the ice-water interface or in the sheet. In the first and last case, traditional remote sensing techniques can be used to detect the oil. When the oil is at the ice-water interface or incorporated in the ice sheet, new oil-under-ice detection systems are required. The basic mode of detection may be different for the two situations.2. Existing TechnologyThe signal associated with the detection of oil under ice may be due to dielectric or acoustic impedance difference between the oil and the ice, or by a change in the surface roughness of the oil-ice interface. The rougher the interface, the more the probing signal is scattered and hence the weaker the signal returned to the receiver. This is the basis, for example, of the detection of oil-on-water using radar. The interface roughness has been directly measured using a mould system deployed by divers (Goodman et al., 1987) and found to be rough at spatial scales of meters and roughness values of several. The oil released under ice fills theroughness features and generates a smooth inter the water, which can be detected using either acoustic or electromagnetic sensors.2.1. MECHANICAL SYSTEMSThe only proven and widely used technology is to drill a hole in the ice using an ice auger, a chain saw or similar mechanical system. While this is time consuming and is a single point measurement, it works. In order to increase the productivity of such units, they can be mounted on a small snow vehicle to increase their coverage, but consideration must be given to the additional safety concerns of using such equipmenton ice sheets of unknown thickness. Using hand-held systems, ice thicknesses greater than about a meter and a half are difficult.Some experiments (Dickins et al., 2005) have been conducted on the detection of the vapour from the oil that would permeate through the ice and be trapped on the surface. While this system worked well in the laboratory environment, it would be very difficult to implement in a typical cold weather environment. This system is very time consuming to install and the time for each measurement took several minutes. There is some evidence from field experiments that very little evaporation occurs under an ice sheet, so the presence of vapours in the laboratory experiment may well be an arte fact of the experimental situation .The electromagnetic band extends from long-wavelength radio waves to X-rays, and includes the visible band and radar. Various parts of theelectromagnetic spectrum had been tried for the detection of oil under ice, including low-frequency systems at about 100 kHz, various forms of radar from 100 to 1,000 MHz, and the visible band either directly or by detecting the fluorescence of the oil. While there is some variation of the dielectric constant with frequency, the values of Table 1 are typical. It is easy for electromagnetic radiation to be transmitted from the air to either the ice or the oil.The reflection at the oil-ice interface will be weak, but easily detected provided the sensor has an adequate dynamic range. There will be a strong reflection at the interface with the water. As with any sensing package, the spatial resolution depends on the wavelength (and pulse length for pulsed systems).There are a number of low-frequency electromagnetic systems, which use induction to detect surface and sub-surface anomalies .These systems typically operate at frequencies below 100 kHz (wavelengths of greater than 3,000 m). At these large wavelengths the spatial resolution is poor and while such systems have been proven useful for sea-ice thickness measurements, it is unlikely that this group of sensors would detect oil either in ice or at the ice-water interface (Kovacs et al., 1995)Ground penetrating radar (GPR) systems are routinely used to determine sub-surface structures and operate at frequencies between 300 and 1,000 MHz . In order to achieve good spatial resolution, most GPR systems usea high bandwidth antenna (low Q) and produce a short chirp signal (Moorcroft and Tunaley, 1985). Most of the currently available GPR systems are surface based and require good coupling between the unit antennae and the ice. Since such systems are routinely commercially available, they are very attractive to be used as an oil-under-ice detector. There have been a number of experiments, both in test basins and in the field to test the ability of these systems to uniquely detect oil-under-ice. The main problem is both signal strength and dynamic range, since, depending on the value of the dielectric constant of the oil, the reflected signal difference between oil and ice is 0.5–7% as opposed to the nearly 100% at the ice-water interface. Thus, the receiver must be sensitive to small variations in signal strength to see the oil-ice interface, while not being overloaded by the return from the water. Older systems lacked this. dynamic range and the ice-oil signal was masked by the water return. The electronics used by more recent designs have a better dynamic range, and Dickins et al. (2005) have recently used such a system to evaluate an oil-under-ice detection in a test basin using urea ice, and subsequently (Brandvik et al., 2006) in an experiment in the Norwegian Arctic. The test basin experiments used extensive signal analysis in order to identify the presence of oil under ice, which obscures what properties of the interface are actually being detected. The use of urea ice, whose electrical properties are different from natural ice, further complicates theinterpretation. The field data from 2006 is still being analyzed.For more than a decade, radio-echoing sounding systems operating in the same frequency band as the GPS have been used to measure glacier ice thickness from an airborne platform (Figure 7). These systems have a much narrower bandwidth and beam width than a typical GPS system, but offer the potential to remotely detect oil under ice. Since these systems have a much lower spatial resolution than the GPS, a larger area of oil-under-ice would be required for a reasonable test of the units’ capability. No such field studies have been undertaken.石油冰下检测:什么是最先进的?摘要:在二十世纪七十年代早期,石油和天然气勘探在加拿大和美国的北极开始需要被确认开发技术来检测油冰下。