半固态成形分析
半固态加工技术概要

固态成形
– 特征:以固态充型 – 优点:高可靠性 – 高性能 – 缺点:流程长 – 柔度低 – 成本高 – 趋势:快速、精确、低耗 – 向液态成形延伸
2018/10/29
–挤压铸造 –压铸 –铸轧一体化
–液态模锻 –液芯轧制 –精密锻造 –等温锻造 –超塑性加工
4
1 半固态成形技术的产生
——加工技术新体系
2018/10/29
26
6 本课题组的主要成果
Fe-Cr-C系合金白口铁半固态成形
半固态
普通
2018/10/29
27
6 本课题组的主要成果
高锰钢半固态成形
半固态
普通铸造
28
2018/10/29
6 本课题组的主要成果
——理论成果
半固态连铸过程稳定性理论 粒状晶形成理论 半固态连铸工艺设计准则
机 械 力
喷 射 沉 积 法 剪 切 冷 却 轧 制 法 悬 浮 剂
添 加 剂
孕 育 变 质 剂
物 理 场 作 用
预 变 形
应 变 诱 发 熔 体 激 活 法
温 度 控 制
强 化 对 流
电 脉 冲 法
超 声 波 法
液 相 线 法
循 环 等 温 法
缓 慢 冷 却 法
紊 流 效 应 法
机 械 搅 拌 法
2018/10/29
18
4 半固态成形技术现状
——以铝代铁
原为铸铁,单重3公斤,现改用半固态铝合金,单重 1.4公斤,减重114%
2018/10/29
19
4 半固态成形技术现状
——以铝代钢
原为精铸碳钢,现为 A356 - T6 铝合金 .完全满足要求 , 且减重50%,成本显著降低
第9章半固态成形技术 PPT

2、半固态金属的组织特性、形成机理与力学行为
(1) 非枝晶的形成与演化
图7 Al-20Cu合金未搅拌和机械搅拌(流变铸造)状态的凝固组织
液体金属在凝固过程中搅拌且激冷,其结晶造成固体颗粒的初始形貌 呈树枝状,然后在剪切力作用下,枝晶会破碎,形成小的球形晶,图7 未常规铸造和半固态铸造的组织对比,可见利用流变铸造方法生产的半 固态金属具有独特的非枝晶、近似球形的显微结构。球形组织的形成过 程?
(2) 半固态金属的力学行为
下表为用不同加工方法获得的A356铝合金的力学性能,从表中可以看出, 半固态金属加工技术的优越性。如触变成形并在T6状态下的性能较金属型 铸造所获得的合金有更好的力学性能,并与锻件的性能相近。
注:SSM为半固态加工;PM为金属型铸造;CDF为闭模锻造
几种铸造方法铸件性能比较
图2 半固态金属的内部结构: (a) 高固相分数, (b) 低固相分数
半固态金属的金属学和力学 主要有以下几个特点:
• 由于固液共存,在两者界面不断 发生熔化、凝固,产生活跃的扩 散现象,因此,溶质元素的局部 浓度不断变化;
• 由于晶粒间或固相粒子间夹有液 相成分,固相粒子间几乎没有结 合力,因此,其宏观流动变形抗 力很低;
根据所研究的材料,可分为有色金属及其合 金的低熔点材料半固态加工和钢铁材料等料半固态成形研究
铝、镁、铅、铜 研究重点在成形工艺的开发
铝合金半固态加工技术(触变成形)已经成熟并进入 规模生产,主要应用于汽车、电器、航空航天领域。
②高熔点黑色金属的半固态成形研究
图8 球形微粒固态金属加工两种方法(流变成形和触变成形)的工艺流程图
半固态浆料搅动时的组织演变受很多因素影响,半固态浆料的 温度、固相分数和剪切速率是三个基本因素。
3~4半固态成型

半固态铸造生产线及自动化
半固态流变成形生产线 该系统由铝合金熔化炉、挤压铸造机、转盘式制 浆机、自动浇注装置、坩埚自动清扫、喷涂料装置等 组成。其工艺过程为:浇注机械手3将铝液从熔化炉2 中浇入制浆机4的金属容器中冷却;同时浆料搬运机 械手5从制浆机的感应加热工位抓取小坩埚,搬运至 挤压铸造机并浇人压射室中成形;随后继续旋转将空 坩埚返回送至回转式清扫装置上的空工位,并从另一 个工位抓去一个清扫过的小坩埚旋转放置到制浆机上; 制浆机和清扫机同时旋转一个角度,进入下一个循环。
半固态铸造成形装备
半固态铸造成形装备主要包括半固态浆料 制备装备、半固态成形装备、辅助装置等。 按流变铸造和触变铸造分类,又有流变铸 造装备和触变铸造装备。 半固态浆料的制备方法主要有机械搅拌、 电磁搅拌、单辊旋转冷却、单/双螺杆法等。 其基本原理都是利用外力将固液共存体中的固 相树枝晶打碎、分散,制成均匀弥散的糊状金 属浆料。最新发展的还有倾斜冷却板法、冷却 控制法、新MIT法等。
半固态铸造成形装备
一步法— 流变铸造 半固态铸造成形是在液态金属凝固的过程中进行强烈 的搅动,使普通铸造凝周易于形成的树枝晶网络骨架被打 碎而形成分散的颗粒状组织形态,从而制得半固态金属液, 然后将其铸成坯料或压成铸件。 根据其工艺流程的不同,半固态铸造可分为流变铸造 二步法— 和触变铸造两大类。 触变铸造 流变铸造是将从液相到固相冷却过程中的金属液进行 强烈搅动,在一定的固相分数下将半固态金属浆料压铸或 挤压成形,又称“一步法”; 触变铸造是先由连续铸造方法制得具有半固态组织的 锭坯,然后切成所需长度,再加热到半固态状,再压铸或 挤压成形,又称“二步法”。
半固态铸造的其他装置
流变铸造采用“一步法”成形,半 固态浆料制备与成形联为一体,装备 较为简单; 触变铸造采用“二步法”成形,除 有半固态浆料制备及坯料成形装备外, 还有下料装置、二次加热装置、坯料 重熔测定控制装置等。
半固态成型技术的发展与应用现状
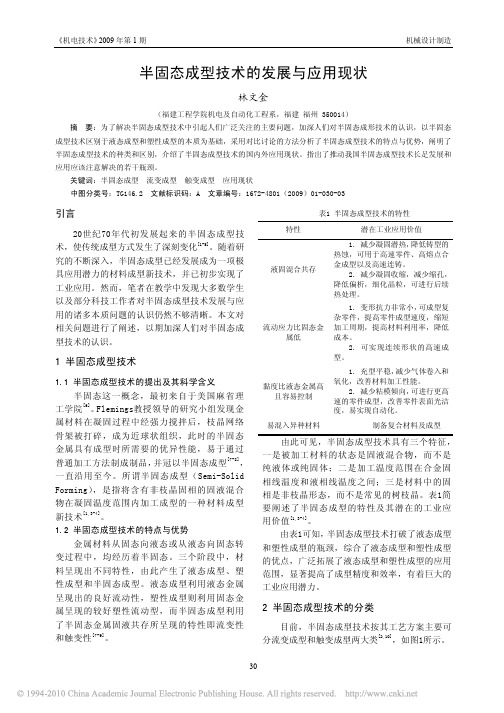
虽然我们在基础理论研究方面已经取得了不少成 果,但仍然要进一步加大基础理论和技术创新的 投入力度,争取走在基础理论的研究前沿。
(3)开发具有自主知识产权的半固态浆料制 备新技术,降低坯料的生产成本,提高生产效率。 半固态金属浆料的价格始终是影响半固态成型技 术发展和普及的关键因素。因此,我们应开发具 有自主知识产权的高效、优质、低成本制备技术。
Honor of Wilfried Kurz, 2004:3-14. [4] X.C. Pang, H.F. Zhang, A. M. Wang, B.Z. Ding, K.Q. Qiu. Journal of Materials Science and Technology[J],
2000, 16:453-460. [5] D. Apelian, A. De Figueredo, M.M. Makhlouf. TMS Annual Meeting: Energy Efficient Manufacturing Processes,
(4)大力开发新型合金的半固态成型工艺, 努力扩展半固态成型技术的应用范围。在引进、 吸收国外先进半固态成型技术的同时,我们应该 从基础理论出发,努力开发新型优质合金的半固 态成型工艺,只有这样,才能掌握半固态成型的 前沿技术,真正成为半固态成型技术的领军者。
(5)国家应该鼓励相关企业参与半固态成型 技术的研究,鼓励相关企业积极引进、吸收国外 先进半固态成型技术。同时采取一定的优惠政策, 鼓励企业进行技术改造,努力为广大科研单位创 造试验平台,争取在最短的时间内将先进研究成 果转化为生产力。
《机电技术》2009 年第 1 期
机械设计制造ຫໍສະໝຸດ 半固态成型技术的发展与应用现状
林文金
(福建工程学院机电及自动化工程系,福建 福州 350014) 摘 要:为了解决半固态成型技术中引起人们广泛关注的主要问题,加深人们对半固态成形技术的认识,以半固态 成型技术区别于液态成型和塑性成型的本质为基础,采用对比讨论的方法分析了半固态成型技术的特点与优势,阐明了 半固态成型技术的种类和区别,介绍了半固态成型技术的国内外应用现状。指出了推动我国半固态成型技术长足发展和 应用应该注意解决的若干瓶颈。 关键词:半固态成型 流变成型 触变成型 应用现状 中图分类号:TG146.2 文献标识码:A 文章编号:1672-4801(2009)01-030-03
半固态成型介绍
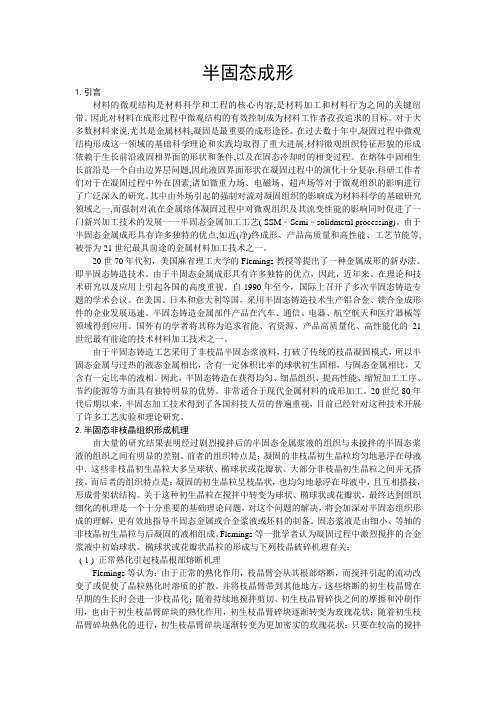
半固态成形1.引言材料的微观结构是材料科学和工程的核心内容,是材料加工和材料行为之间的关键纽带。
因此对材料在成形过程中微观结构的有效控制成为材料工作者孜孜追求的目标。
对于大多数材料来说,尤其是金属材料,凝固是最重要的成形途径。
在过去数十年中,凝固过程中微观结构形成这一领域的基础科学理论和实践均取得了重大进展.材料微观组织特征形貌的形成依赖于生长前沿液固相界面的形状和条件,以及在固态冷却时的相变过程。
在熔体中固相生长前沿是一个自由边界层问题,因此液固界面形状在凝固过程中的演化十分复杂.科研工作者们对于在凝固过程中外在因素,诸如微重力场、电磁场、超声场等对于微观组织的影响进行了广泛深入的研究。
其中由外场引起的强制对流对凝固组织的影响成为材料科学的基础研究领域之一,而强制对流在金属熔体凝固过程中对微观组织及其流变性能的影响同时促进了一门新兴加工技术的发展一一半固态金属加工工艺( SSM﹣Semi﹣solidmetal processing)。
由于半固态金属成形具有许多独特的优点,如近(净)终成形、产品高质量和高性能、工艺节能等,被誉为21世纪最具前途的金属材料加工技术之一。
20世70年代初,美国麻省理工大学的Flemings教授等提出了一种金属成形的新办法。
即半固态铸造技术。
由于半固态金属成形具有许多独特的优点,因此,近年来。
在理论和技术研究以及应用上引起各国的高度重视。
自1990年至今,国际上召开了多次半固态铸造专题的学术会议。
在美国、日本和意大利等国,采用半固态铸造技术生产铝合金、镁合金成形件的企业发展迅速。
半固态铸造金属部件产品在汽车、通信、电器、航空航天和医疗器械等领域得到应用。
国外有的学者将其称为追求省能、省资源、产品高质量化、高性能化的21世纪最有前途的技术材料加工技术之一。
由于半固态铸造工艺采用了非枝晶半固态浆液料,打破了传统的枝晶凝固模式,所以半固态金属与过热的液态金属相比,含有一定体积比率的球状初生固相,与固态金属相比,又含有一定比率的液相。
半固态注射成形

7半固态注射成形7.1概述世界各国科研工作者在研究新的半固态金属成形工艺时,将塑料的注射成形原理,应用于半固态金属加工过程,形成半固态注射成形工艺。
注射成形工艺将半固态金属浆料的制备、输送和成形过程融为一体,是一种一步成形生产最终产品的新工艺,它较好地解决半固态成形过程中金属浆料的保存输送、成形控制困难等难题,为半固态金属成形技术的应用开辟新的前景,因此有的学者将注射成形技术看作是镁合金结构件生产的最好方法。
半固态注射成形技术首先由美国的DOW Chemical Co.公司于1988年开发成功。
1990年后,在密执安的Ann Arbor成立了独立的Thixomat Inc.,从事该项技术的商业性开发。
第二代设备于1991年10月投入使用。
而后英国的Z.Fan等人又发明了双螺旋注射成形机,扩大了注射成形设备的种类和应用范围,为半固态注射成形技术的应用开辟了更为广泛的前景。
7.2注射成形工艺路线及特点7.2.1注射成形工艺路线目前,镁合金在注射成形工艺中应用较多,其成形工艺过程可分为两种方式:一是直接把熔化的金属液而不是处理后的半固态浆液冷却至适宜的温度,并辅以一定的工艺条件压射进入型腔后成形;另一种工艺是将小块枝状晶合金送入螺旋推进系统,合金被加热推进、压射进入模具型腔后成形。
后者是本章需要进行详细讨论的方法。
7.2.2注射成形设备及工艺过程[1-3]图7-1则是注射成形机组的示意图。
注射成形机组,除注射成形主机外,还包括:1-加料机;2-模具温控机;3-脱模剂稀释和传送装置;4-真空机;5-脱模剂喷雾机和产品取出机械手。
图7-1镁合金注射成形辅助设备示意图(1)加料机:通常镁合金原料是装在圆筒内。
加料机将园筒内的镁屑送到成形机的原料漏斗内,也可以将原料集中在一个地方,分别向各台成形机送原料;(2)模具温控机:铝合金压铸成形时金属模具需用水冷却,而镁合金的凝固时间非常短,所以要在金属模具上加热以延长熔融镁合金的流动长度。
铝铅合金的半固态成形工艺研究
ig 教 授 等提 出 了一 种金 属成 形 的新 方法 ,即半 固 ns 固 、 两 相 区 间进 行 , 2 世 纪 金 属成 形 的 关键 技 液 是 1
术之 一l】半 固态 成形 技术 现 主要 用 于铝 、 合金 的 1。 l ' 3 镁 成 形上 。 过程 为 : 合金结 晶的温度 范 围内进行搅 其 在 拌 ,获得 细小 球状 初生 相颗 粒 均布 于 液体 基体 的半
关键词: 固态; 半 铝铅合金; 械搅拌 ; 固相率 中 图分 类号 : G 4 . : T 1 6 21 文献 标识码 : ; A 文章编 号 : 0 — 6 8 2 1 ) 1 4 1 6 9 5 ( 0 0 — 0 0 2 0世纪 7 0年代 初 , 国麻 省 理工 大 学 的 Fe 美 l m—
T iu n0 0 2 Chn ay a 3 0 4, ia)
Ab t c : l w c e ial c n e so c a ig i p o u e O AZ9 i t e s r tYel a o h m c o v rin o t S r d c d n n 1 D n h Ph s h t — o p ae p r n a a e a d a dt e s lt n.whc S S c l d n n- h o e c e ia on e so . h RD e ma g n t n d iv ou i i o ih j O- al o e c r m h m c lc v r in T e X p t r s idia e h tc n e so o t d Iy rwa mo p o s sr c u e h DS a d SE r s l a t n n c t d t a o v r in c a e a e s a e r h u tu t r .T e E n M e ut s
半固态成型镁合金组织与耐腐蚀性能影响
摘要本课题主要针对应用最广泛的AZ91镁合金进行研究,采用半固态重熔加热工艺和金相组织观察的方法,考察铸态树枝晶与挤压后的球形晶两种重熔加热后的组织的变化,探讨用于获得半固态组织的较佳的初始状态,并对两种状态的AZ91镁合金进行浸泡腐蚀试验,研究影响镁合金腐蚀速率的因素,为镁合金的半固态成型奠定基础。
研究结果表明:通过对金相组织分析得出,铸态的试样在560℃开始出现球状晶,挤压态试样就550℃就出现了球状晶。
随保温时间延长或温度的升高,晶粒趋于圆整,由大到小,最后晶粒形态出现了异常,由原来独立球晶变为不规则的粗大球状晶;挤压变形对树枝晶转变成球状晶有促进作用;腐蚀试验结果表明:腐蚀速率随腐蚀时间延长逐渐减小,挤压态的试样耐蚀性低于铸态合金的试样。
这主要与β相的含量、形态、和分布有关。
当β相含量较少时,β相主要充当电偶的阴极;若β相分布不连续会加速α相的腐蚀过程。
关键字:AZ91镁合金半固态重熔加热耐腐蚀性ABSTRACTThe main subject of the study for the most widely used AZ91 magnesium alloy,with Semi-solid remelting heating process and microstructure observation,inspected changes in the organizations investigated cast dendrites and squeeze both spherical crystal remelting heated and explored better initial state for semi-solid structure.AZ91 magnesium alloy of two states for immersion corrosion was tested,studying factors affecting the corrosion rate of magnesium alloys,which laid the foundation for the semi-solid forming of magnesium alloy.The results showed that, spherical crystal was found in the cast of the specimen at 560 ℃while extruded samples at 550 ℃ by analysis of the microstructure.With the holding time or temperature increases, the grain tended rounded, descending,and the last grain morphology appeared abnormal, irregular coarse spherical crystal from the original independent Spherulite ;The organization from dendrite into spherical crystal was promoted by compressional deformation.The corrosion test results showed that: the corrosion rate gradually decreased with the etching time extending, while the specimen corrosion resistance of squeezed state was lower than the cast alloy specimens.This mainly depended on the content of the β phase, morphology and distribution.When β phase content was small, the β phase mainly acte d as a galvanic cathode;The β phase discontinuous distribution would accelerate the corrosion process of the α-phase.Key words: AZ91Magnesium alloy semi-solid remelting heating corrosion resistance目录第一章绪论 (1)1.1课题来源及意义 (1)1.2镁及其合金发展与应用 (1)1.3半固态加工的概念与发展 (3)1.3.1半固态加工的概念 (3)1.3.2半固态加工的发展 (3)1.4半固态金属浆料或坯料的制备 (5)1.4.1机械搅拌法 (5)1.4.2电磁搅拌法 (5)1.4.3应变诱发熔化激活法 (6)1.4.4半固态等温热处理法 (6)1.4.5注射成形 (6)1.5镁合金表面防腐处理 (6)1.6课题的主要内容 (10)第二章试验材料、设备及试验过程 (11)2.1试验材料 (11)2.2试验设备 (11)2.3试验过程 (14)2.3.1等温热处理试验 (14)2.3.2 金相试样制备 (14)2.3.3 金相显微组织观察 (16)2.3.4 镁合金的耐腐蚀性能实验 (16)第三章试验结果讨论与分析 (18)3.1铸态半固态等温处理显微组织 (18)3.2挤压态半固态等温处理显微组织 (21)3.3耐腐蚀性能分析 (25)第四章结论 (27)谢辞 (28)参考文献 (29)第一章绪论1.1课题来源及意义镁合金作为最轻的工程金属材料,被誉为“21世纪的绿色工程材料”。
半固态成形
如果浆流变浆料凝固成锭,按需要将此金属 锭切成一定大小,然后重新加热(即坯料的二 触变成形 thixoforming 次加热)至金属的半固态温度区(金属锭称为半 固态金属坯料)。利用金属的半固态坯料进行 成形加工的方法为触变成形
金属材料在液态、固态和半固态三个阶段均呈现出明显不同的物理特性,利 用这些特性,产生了凝固加工、塑性加工和半固态加工等多种金属热加工成形 方法。图1表示金属在高温下三态成形加工方法的相互关系
(7) 倾斜冷却板制备法 原理:如图10所示,金属液通过坩埚倾倒在内部具有水冷却装置的冷却 板上,金属液冷却后达到半固态。,流入模具中制备成半固态坯料。
图10 倾斜冷却板制备半固态坯料的工艺及设备图
4、半固态金属触变成形
(1) 触变成形工艺及设备 触变成形(Thixomolding)由美国的Dow公司开发的,1992年由日本引入 并完成成形机的研制开发。图11为Thixomolding工艺的简图,其设备由原 料入料与预热装置、螺旋注射机、加热装置以及压铸机等部分组成。 设备特点: ① 原料进入料斗后边加热边剪切 搅拌,最后形成半固态的状态 再射入模具中; ② 半固态浆料的固相分数可控性 强,成形件质量高、性能稳定 ③ 螺旋机内密闭性好,在成形过 程中不需要严格的保护性气氛 进行保护,仅在投料口处用少 量的Ar气保护即可。
(3) 应变诱导熔化激活法
利用传统连铸方法预先连续铸造出晶粒细小的金属锭坯。
将该金属锭坯在回复再结晶的温度范围内进行大变形量 的热态挤压变形,通过变形破碎铸态组织。 再对热态挤压变形过的坯料加以少量的冷变形,在坯料的 组织中储存部分变形能力。
机械搅拌示意图
按需要将经过变形的金属锭坯切成一定大小,迅速将其加热到固液两相区并 适当保温,即可获得具有触变性的球状半固态坯料。
镁合金半固态压铸成形及其控制技术
镁合金半固态压铸成形及其控制技术发表时间:2020-08-06T08:02:19.822Z 来源:《新型城镇化》2020年3期作者:周贲征[导读] 在众多的合金材料中,镁合金因其重量轻、延展性高、硬度性能良好等优势,被广泛应用在压铸材料中,本文主要分析镁合金半固态压铸成形的方式以及控制技术,希望能够为压铸行业发展提供意见参考。
周贲征广东鸿图南通压铸有限公司摘要:在众多的合金材料中,镁合金因其重量轻、延展性高、硬度性能良好等优势,被广泛应用在压铸材料中,本文主要分析镁合金半固态压铸成形的方式以及控制技术,希望能够为压铸行业发展提供意见参考。
关键词:镁合金;半固态压铸;成形;控制技术在压铸成形材料中,铝合金与镁合金的应用较为广泛,同铝合金相比较,镁合金的强度以及延展性要更高,在压铸成形的材料中,结构相对牢固可靠。
新的发展形势下,对于镁合金的需求越来越大,镁合金的应用范围不断扩大,甚至在航空航天以及通讯设备上得到了良好的应用。
为了更好地研究镁合金成形材料,本文便针对镁合金半固态压铸成形技术进行简单分析。
1镁合金半固态压铸成形所采用的方法通常情况下,有三种途径可以实现镁合金半固态压铸成形,即触变压铸、流变压铸以及处变注射三种方法,接下来将依次进行详细分析:1.1镁合金半固态的触变压铸方法该方法是通过对半固态镁合金锭进行二次加热,变为固液后,借助密闭的送料机将其传送给压铸机,再输送到压射料筒中。
整个的压铸工作是靠冲头动作来完成的。
在二次加热前,半固态镁合金锭固相率基本在 48%-58% 之间,粘稠度较高,然二次加热后,固液镁合金锭在处于压射状态下,会受到切变作用,降低粘稠度,这样一来便提高了流动性,有助于压射成形。
1.2镁合金的流变压铸方法有关研究表明,同液态镁合金相比较,半固态镁合金的成形技术更有助于镁合金零件的压铸成型,压铸件的质量也更高。
因此,镁合金的流变压铸方法便是将液态镁合金通过降温或者搅拌的方式,来将其转变为半固态浆料后,输送到压铸机进行压铸工艺。
- 1、下载文档前请自行甄别文档内容的完整性,平台不提供额外的编辑、内容补充、找答案等附加服务。
- 2、"仅部分预览"的文档,不可在线预览部分如存在完整性等问题,可反馈申请退款(可完整预览的文档不适用该条件!)。
- 3、如文档侵犯您的权益,请联系客服反馈,我们会尽快为您处理(人工客服工作时间:9:00-18:30)。
5.易于生产复合材料与新型合金。
金属半固态成形工艺可改善复合材料中非金属材料的漂浮、 偏析以及与基体金属不浸润的技术难题,为复合材料的制备与成 形提供了有利条件。控制固态合金黏度,可以均一地掺入非金属 材料与密度差大的金属材料,生产金属基复合材料与新成分合金。 利用半固态合金的高黏性,在搅拌剪切的过程中加入密度差大的 金属或非金属材料,可以生产其他工艺所不能生产的复合材料。 在生产粒子强化、纤维强化的复合材料方面,半固态成形有着独 特的优越性。半固态成形对复合材料的成形起到很大的推动作用。
关键区别在于?
半固态成形的基本工艺路线
半固态金属浆料具有流变与触变性能,因此有两条线 路,流变成形和触变成形。
流变成形
半固态浆料直接在压力作用下流变成形。
优缺点: 短流程
节能、节材
储存运输困难
触变成形
半固态浆料铸造成锭坯,根据产品尺寸需要下料, 经过二次加热(也叫重熔加热)后,在半固态温 度下压力加工成形,成为触变成形。
• 美国已利用半固态成形生产出许多电器连接元件。半固态 成形电器连接元件与传统的机械加工相比,也具形的特殊成形机理决定了成形产品的良好的内 部组织与整体性能。由于在半固态材料的制备过程中,对合金施 加剪切搅拌作用,可以消除多种缺陷。与传统铸造成形相比,半 固态金属浆料中包含有类球形的固相颗粒,减少了凝固收缩,并 提高了补缩能力,从而减轻或者消除了缩松倾向。同时,半固态 铸造时有一个平滑的液态充模界面,减轻了气体包裹与气泡的产 生,也减轻了成分偏析,提高了材料的致密度、强度以及材料性 能的均匀性。实践证明,半固态铸件内部组织致密,内部气孔、 偏析等缺陷少,组织细小,力学性能提高,或者力学性能相当, 但塑性大大提高。
1.1 金属半固态成形(SSM)的定义
金属半固态成形(Semi-Solid Metal Forming/Processing) 是指利用金属从固态向液态或者从液态向固态两相转变过 程中的半固态区的金属具有良好的流变特性而进行的金属 成形。 金属在凝固过程中,进行剧烈搅拌,或者控制固—液 态温度区间,得到一种液态金属母液中均匀悬浮一定固相 组分的固液混合浆料,这种半固态金属浆料具有流变特性, 即半固态金属浆料具有很好的流动性,易于通过普通加工 方法制成产品,采用这种既非完全液态,又非完全固态的 金属浆料加工成形的方法,也就是半固态金属加工技术。
优缺点:
输送方便
易于实现自动化
半固态成形技术的三个关键环节
• 半固态金属材料的制备
• 二次加热 • 半固态成形
1.2 SSM的优缺点
1. 投资小,能耗小。
由于半固态成形方便简捷,省去了熔化输送、浇 注以及附加控制污染的设备,加工设备可小型化,因 此高效社能,并且易于实现自动控制。这不仅减少了 设备投资,而且改善了车间劳动条件。半固态成形时 材料的变形抗力低,可以用较小的力成形较大的零件。 试验证明,半固态轧制的轧制力仅是传统热轧的40%。 半固态铸造铝合金比传统铸造铝合金可以节能35%。
半固态成形的主要缺点:
(1)金属半固态成形技术对金属的合金成分有一定适用范围, 适合于半固态成形的合金需要具有足够大的半固态区间,并且 固相率随温度变化比较缓慢,以便于监控半固态合金的固相率, 从而实现对半固态材料制备与成形过程的控制。因此,液—固相 线区间范围小的金属不适合于进行半固态成形。 例如? 纯金属,共晶合金。
2. 成形性能好,可实现短流程生产。
半固态材料流动性能与变形性能良好,经过强烈搅拌的固相 分数为40% - 60%的半固态金属的表观黏度在0.1-10Pa.s之间,与 黄油(0.1 Pa.s)、甘油(l Pa.s)及蜂蜜( 10 Pa.s)的表观黏度相当,仅 比水或者液态金属的黏度高出2-4个数量级,表现出很好的流动 性。与固态成形相比,半固态金属中存在液相组元,塑性变形机 理不同于固态塑性成形。塑性变形主要是由于晶粒之间的旋转和 相对滑移引起的,液相起到“润滑”作用,金属流动阻力显著降 低,复杂的零件也可用很少的工步成形。由于半固态合金材料具 有特殊的流变性能,易于加工成形,半固态铸造直接可以生产出 精度较高的产品。与传统生产方法相比,半固态成形可实现近终 形生产,提高了生产率、节约了原材料。与常规金属模铸造相比, 半固态成形汽车零件生产率与成材率高的特点尤为突出。
半固态成形的技术核心是使固液混合浆料或者坯料获得非枝 晶组织,固相必须球化或者细化,合金组织一般含有10100um的球形晶、近球形晶或者等轴晶。
有的学者将金属半固态成形分成广义和狭义两个概念。 狭义上的半固体成形是指首先通过外场或者内部物理化学作 用制备半固态金属浆料或者非枝晶坯料,然后将预先制备好 的金属浆料或者非枝晶坯料冷却或者加热到半固态区进行成 形; 广义上的半固体成形是将常规铸造得到的固态金属坯料 直接加热到半固态区所进行的成形,严格意义上应称为半熔 融成型。
半固态成形
一、概述
一切金属材料在进行其它成形(轧制、锻造)之前都要经 历液固相变的凝固过程。 凝固过程研究与凝固技术的进展在冶金过程、材质控制中 发挥着越来越大的作用,同时引发了各种新型材料及其加工工 艺的诞生和发展。 金属成形一直是在固态区或者液态区进行的,而人们对许 多合金的凝固过程中的半固态区,尤其是金属动态凝固过程中 的半固态区并没有给予足够的重视,直至半固态成形技术的发 明。
A356与A&357合金半固态压铸件与永久模铸件力学性能 比较。可见,两种铸件的强度性能指标相当,而半固态 压铸件的塑性指标远远高于永久模铸件。
4.提高成形工具寿命。
半固态合金的温度比全液态合金温压低,而且由于部分凝固 已经释放,部分结品潜热,成形工具的工作温度低,因此,提高 了成形工具的使用寿命,降低了生产成本。 对大部分铝合金而言,半同态铸造温度比传统铸造生产时的 铸造温度至少低70℃,铸模的使用寿命可提高25%.铝合金半固 态铸造温度比传统铸造温度最大可以降低1200 ℃ ,大大减轻了 对模具的热冲击,模具使用寿命得到大幅度提高。