金属半固态成型技术发展详解
金属半固态成形

金属半固态成形一、引言金属半固态成形是一种新兴的金属成形技术,它是在半固态状态下对金属进行成形加工,具有高效、高精度、高质量等优点。
近年来,随着科技的不断进步和人们对产品质量的要求越来越高,金属半固态成形技术得到了广泛的应用和研究。
二、什么是金属半固态成形1.定义金属半固态成形是指在合适温度下,将金属材料加工到一定程度时,使其呈现出部分晶粒熔化和部分晶粒未熔化的状态。
这种状态被称为半固态状态。
在这个状态下进行成型加工可以得到具有优异性能的零件。
2.特点(1)高效:相比传统的铸造和锻造工艺,金属半固态成形具有更快的生产速度。
(2)高精度:由于采用了先进的数控技术和模具制造技术,使得加工精度更高。
(3)高质量:由于采用了先进的材料处理方法和模具制造技术,使得产品质量更高。
三、金属半固态成形的工艺流程1.原材料制备:将金属材料经过特殊处理,使其呈现出半固态状态。
2.模具设计:根据产品的形状和尺寸,设计出合适的模具。
3.加热处理:将金属材料加热到合适的温度,使其呈现出半固态状态。
4.成型加工:将半固态金属材料放入模具中进行成型加工。
5.冷却处理:将成型后的零件进行冷却处理,使其达到稳定状态。
6.后续加工:根据需要对零件进行后续加工和表面处理。
四、金属半固态成形的应用领域1.航空航天领域:由于航空航天领域对于零件质量和性能要求非常高,因此金属半固态成形技术在该领域得到了广泛应用。
例如飞机发动机叶片、涡轮叶片等高精度零部件都可以采用该技术进行生产。
2.汽车制造业:汽车制造业是金属半固态成形技术的另一个重要应用领域。
例如汽车发动机缸体、曲轴等高精度零部件都可以采用该技术进行生产。
3.医疗器械领域:金属半固态成形技术在医疗器械领域的应用也越来越广泛。
例如人工关节、牙科种植体等高精度零部件都可以采用该技术进行生产。
五、金属半固态成形的未来发展趋势1.智能化:随着科技的不断进步,金属半固态成形技术将更加智能化,通过计算机控制和自动化设备,使得生产效率更高、产品质量更稳定。
半固态成形分析

5.易于生产复合材料与新型合金。
金属半固态成形工艺可改善复合材料中非金属材料的漂浮、 偏析以及与基体金属不浸润的技术难题,为复合材料的制备与成 形提供了有利条件。控制固态合金黏度,可以均一地掺入非金属 材料与密度差大的金属材料,生产金属基复合材料与新成分合金。 利用半固态合金的高黏性,在搅拌剪切的过程中加入密度差大的 金属或非金属材料,可以生产其他工艺所不能生产的复合材料。 在生产粒子强化、纤维强化的复合材料方面,半固态成形有着独 特的优越性。半固态成形对复合材料的成形起到很大的推动作用。
关键区别在于?
半固态成形的基本工艺路线
半固态金属浆料具有流变与触变性能,因此有两条线 路,流变成形和触变成形。
流变成形
半固态浆料直接在压力作用下流变成形。
优缺点: 短流程
节能、节材
储存运输困难
触变成形
半固态浆料铸造成锭坯,根据产品尺寸需要下料, 经过二次加热(也叫重熔加热)后,在半固态温 度下压力加工成形,成为触变成形。
• 美国已利用半固态成形生产出许多电器连接元件。半固态 成形电器连接元件与传统的机械加工相比,也具形的特殊成形机理决定了成形产品的良好的内 部组织与整体性能。由于在半固态材料的制备过程中,对合金施 加剪切搅拌作用,可以消除多种缺陷。与传统铸造成形相比,半 固态金属浆料中包含有类球形的固相颗粒,减少了凝固收缩,并 提高了补缩能力,从而减轻或者消除了缩松倾向。同时,半固态 铸造时有一个平滑的液态充模界面,减轻了气体包裹与气泡的产 生,也减轻了成分偏析,提高了材料的致密度、强度以及材料性 能的均匀性。实践证明,半固态铸件内部组织致密,内部气孔、 偏析等缺陷少,组织细小,力学性能提高,或者力学性能相当, 但塑性大大提高。
1.1 金属半固态成形(SSM)的定义
半固态金属成形技术的发展与应用

半固态金属成形技术的发展与应用70年代初美国麻省理工学院的M.Flemigs和D.Spencer发现,处于固-液相区间的合金经过连续搅拌后呈现出低的表观粘度,此时在结晶过程中形成的树枝晶被粒状晶代替。
这种浆料很容易变形,只要加很小的力就可以充填复杂的型腔,从而开发出一种新的金属成形方法—半固态金属成形。
半固态金属成形可以分为流变成形和触变成形两种。
前者是利用半固态金属的流变性能,将经过强烈搅拌的金属浆料加压成形。
后者则利用金属的触变性能,将凝固的搅拌金属浆料加热至半固态再加压成形。
半固态金属成形具有能消除气孔、缩孔,提高零件的机械性能及模具寿命,减少凝固收缩,提高零件尺寸精度等优点。
半固态金属易于搬运和输送,为连续高效的自动化生产创造了条件。
在节省能源、保护环境方面也较传统的铸造方法更为优越。
目前美国、西欧已将半固态加工成形技术应用于生产。
美国军方把用流变铸造法制造复合材料坦克零件列为五年工艺研制规划之一。
在川崎制铁等18家大型公司的资助下,日本从1988~1994年成立了专门研究机构,对半固态金属的性能、制造与加工技术进行了全面的研究,目前已着手工业化生产。
我国对半固态金属成形技术的研究基本上还处于实验室阶段,离工业性生产尚有一定距离。
1半固态金属的流变特性半固态金属的流变特性是指在外力作用下半固态金属的流动、变形性能。
研究半固态金属的流变特性对半固态金属的制备和成形技术具有重要的指导意义。
当金属液中固体金属颗粒的组分大于0.05~0.1时,其流变行为即呈现非牛顿体型。
在更高的固体组分(0.5~0.6)时,浆料呈非线性粘塑性,具有宾汉(Binghan)流体的特性。
虽然合金成份、半固态金属的制造条件、固体相的形状与大小等因素对半固态金属的流变性能都有影响,但固相组分的数量对流变性能的影响最大。
通常用半固态金属的表观粘度作为其流变性的指标。
通过在一定剪切变形速度及冷却条件下的搅拌试验,测定了在不同固体组分下的铝、铜、铁半固态金属的表观粘度,见图1,并采用悬浊液的粘度公式对表观粘度与固相率的关系进行回归分析,得到如公式(1)所示的半固态金属表观粘度表示式[1]:图1固相率与表观粘度间的关系(曲线为回归结果)(1)式中:ηa—半固态金属表观粘度,Pa.s,ηLa—金属液表观粘度(Pa.s),ρm—合金密度(kg.m-3),C—凝固速度,s-1,—剪切变形速度,s-1,f s—固相率。
浅谈金属半固态成形技术

江苏理工学院JIANGSU UNIVERSITY OF TECHNOLOGY材料先进制备与成形加工技术课程论文学院名称:材料工程学院专业:机械工程2013年04 月浅谈金属半固态成形技术摘要本文综述了半固态成形技术,介绍了半固态成形技术的定义及其成形工艺,研究现状及发展应用,半固态浆料的制备方式及浆料的特点,最后对半固态技术进行了展望。
关键词半固态成形触变成形流变成形1.半固态成形技术定义金属半固态加工就是在金属凝固过程中,对其施以剧烈的搅拌作用,充分破碎树枝状的初生固相,得到一种液态金属母液中均匀地悬浮着一定球状初生固相的固-液混合浆料(固相组分一般为50%左右),即流变浆料,利用这种流变浆料直接进行成形加工的方法称之为半固态金属的流变成形;如果将流变浆料凝固成锭,接需要将此金属锭切成一定大小,然后重新加热(即坯料的二次加热)至金属的半固态温度区,这时的金属锭一般称为半固态金属坯料。
利用金属的半固态坯料进行成形加工,这种方法称之为触变成形。
半固态金属的上述两种成形方法合称为金属的半固态成形技术。
如下图一所示。
图一半固态成形技术2、半固态加工的成形工艺目前,金属半固态成形的工艺路线主要有两种:一种是触变成形,把制浆与成形结合在一起;另一种是流变成形,将制坯和成形结合在一起。
2.1 触变成形触变成形的工艺路线是将半固态合金浆料铸造成锭坯,根据产品尺寸需要进行下料,经二次加热后,在半固态温度下进行压力加工成形。
由于半固态坯料的加热、输送工艺较为方便,并易于实现自动化操作,因而触变成形工艺在得到了广泛应用。
如半固态金属触变压铸、触变锻造、触变挤压工艺目前都已成熟,并进入实际应用。
随着触变成形工艺的推广和应用,生产实践中发现触变成形工艺也存在一些不足,如成本高,坯料损耗过多,坯料重熔时固相率难以精确控制。
工艺图如图二所示。
2.2 流变成形流变成形是将制备的半固态合金熔体直接转移到成形设备进行成形的工艺方法。
半固态成形发展概况及研究进展

半固态成形利用金属材料在固液共存状态下所特有的流变特性进行成形的技术。
首先要制造含有一定体积比例的非枝晶固相的固液混合浆料,成形方法有流变成形和触变成形两种。
优点:1、在工艺方面:成型温度低,延长模具寿命(热冲击小);节省能源;改善生产条件和环境。
2、在产品方面:铸件质量提高(减少气孔和凝固收缩);减少加工余量;零件的尺寸和精度能达到近终形;扩大压铸合金的范围并可以发展金属复合材料。
所谓半固态加工是指金属在凝固过程中,对其施以剧烈的搅拌作用或扰动作用,得到一种液态金属母液,其中均匀悬浮着一定量的球状初生固相或退化的枝晶固相的固2液混合浆料(也称流变浆料) ,对这种浆料进行的加工成型的方法。
半固态成型包括半固态流变成型和半固态触变成型两类,前者是将制备好的半固态浆料直接用于成型,如压铸成型(称为半固态流变压铸成型) ;后者是对制备好的半固态坯料进行重新加热使其达到半熔融状态,然后进行成型,如挤压成型(称为半固态触变挤压)[1]。
1半固态金属成形的发展及现状(半固态成形铝合金材料研究)半固态金属(SSM)成形技术自DavidSpencer于1971年首次提出至今,已有30多年历史【2-5】。
综观整个历史过程,其发展可以分为实验研究、应用研究和工程化应用三个阶段。
从20世纪70年代初开始,实验研究工作大约延续了15年。
这一阶段的研究主要集中在探索具有流变性和触变性的有色金属合金半固态试样的组织特征与制备方法上。
主要成果包括:①揭示了流变性和触变性坯料的组织特征;②提出了枝晶组织向非枝晶组织转变的物理模型:③研究了搅拌速度、强度以及温度等工艺参数对非枝晶化过程的影响规律:④初步探讨了半固态微观组织与流变性能的关系;⑤测试了半固态合金流变性能,并建立了相关的数学模型。
上世纪80年代中期是半固态成形技术应用研究的迅速发展阶段,并且从早期的有色金属合金扩展到高熔点合金以及复合材料的半固态成形。
这期间,开发与研制了包括电磁搅拌在内的多种半固态制坯技术与连铸设备;利用计算机模拟技术揭示了半固态合金充型过程;深入细致研究了成形工艺对产品组织性能影响的规律。
金属材料成型_6.2_半固态成形技术路线
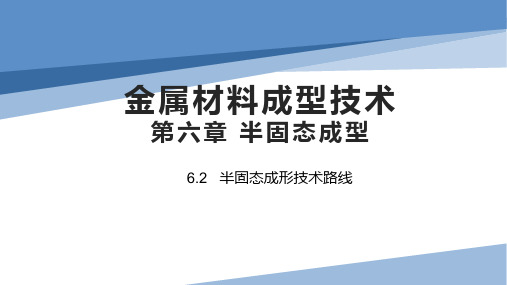
图6-8 半固态成形技术的两种工艺路线
对于流变成形,由于把浆料制备和加工成形相承接,具有生产效率高 、整体流程短的特点,近年来发展十分迅速,不过浆料的保存和输送难度 大,设备自动化控制复杂,成本相对高。对于触变成形,浆料的制备和最 终成形可分开进行,成形厂方甚至可以不参与熔炼制浆,只需提供二次 加热,工业污染小,而且半固态坯料输送方便,易于实现自动化,因而在 国外较早得到了广泛应用,不过这种方式的缺点是坯料经过冷却和再加热 的过程,能源消耗有所增加。
图6-9 机械搅拌制备半固态浆料
b、电磁搅拌法
电磁搅拌法是目前半固态成形工业生产上最成熟最广泛被应用的制浆 方法,它是在感应线圈中通入一定相位的交变交流,从而产生变换旋转的 磁场,而金属液中便有感应电流产生,洛伦兹力就驱使金属熔体产生剧烈 运动,使非枝晶凝固模式取代传统的枝晶凝固趋势,从而获得含有球形固 相的半固态浆料。如图6-10所示,按熔体被搅拌力驱动的流动方式,一般 分为垂直式、水平式、螺旋式。电磁搅拌采用无接触式地对合金熔体进行 搅动,对合金污染极大降低,且通过调节电流、磁场强度和频率等参数就 能实现搅拌效果的控制,可以连续高效地制备坯料,适用于工业化的生产 应用。但由于电磁搅拌的集肤效应,通常认为,直径大于150mm的铸坯 不宜采用电磁搅拌法。
c、注射成型法
注射成型法是将低熔点金属颗粒进行加热至半固态成型,尺寸为几毫米的合金 粒子在料筒中边被加热边被螺旋体剪切推进,通过螺旋强制对流的搅拌作用,得 到细小均匀球状晶的半固态浆料组织,然后以高速(注塑十倍速度)注入模腔里 。这种方法非常适于相对较活泼的镁合金材料,在整个浆料制备和成型工艺中可 以不使用保护气体和防氧化剂,不需要配备熔化炉,而且不会产生浮渣、炉渣等 ,兼顾安全性和环保。
半固态加工技术的发展及其研究现状
技术瓶颈与挑战
流变行为复杂
半固态加工过程中,材料的流变行为受多种因素影响,如温度、 应变速率等,导致加工过程难以控制。
界面问题
在半固态加工过程中,由于固液两相的存在,界面问题成为一大挑 战,如固液界面稳定性、颗粒分散等。
设备与工艺匹配
半固态加工需要特殊的设备和工艺,如何实现设备和工艺的匹配, 提高加工效率是亟待解决的问题。
未来发展前景与展望
拓展应用领域
随着半固态加工技术的不断成熟, 其应用领域将进一步拓展,如航 空航天、汽车、新能源等领域。
绿ቤተ መጻሕፍቲ ባይዱ可持续发展
半固态加工技术具有节能减排的潜 力,未来将在绿色可持续发展领域 发挥重要作用。
智能化与自动化
随着智能制造技术的发展,半固态 加工将实现智能化与自动化,提高 加工效率和产品质量。
01
02
03
汽车工业
研究半固态加工技术在汽 车零部件制造中的应用, 提高零部件的性能和轻量 化水平。
航空航天工业
探索半固态加工技术在航 空航天领域的应用,满足 高性能、轻质材料的需求。
电子产品
研究半固态加工技术在电 子产品外壳、连接器等制 造中的应用,实现产品的 小型化、轻薄化。
04 半固态加工技术的挑战与 前景
输标02入题
应用领域:航空航天业
01
03
优势特点:半固态加工技术能够控制零件的内部结构 和微观组织,提高零件的疲劳寿命和可靠性,满足航
空航天器的高性能要求。
04
技术应用:半固态加工技术用于制造航空航天器的关 键零部件,如发动机叶片、机翼结构件等。
成功应用的案例三
案例名称
医疗器械制造
应用领域
医疗器械制造业
四、半固态金属加工技术
(b) 连续式
图4-5 半固态机械搅拌装置示意图
几种机械搅拌装置示意图 (a)棒式 (b)螺旋式 (c)底浇式 (d)倾转式
2、电磁搅拌法
电磁搅拌法是利用感应线圈产生的平行于或者垂直于 铸形方向的强磁场对处于液-固相线之间的金属液形成强 烈的搅拌作用,产生剧烈的流动,使金属凝固析出的枝晶 充分破碎并球化,进行半固态浆料或坯料的制备。
剪切速率对表观粘度的影响
(3)冷却速度对表观粘度的影响
不同冷却速度下ηa—fs曲线
(4)合金成分对表观粘度的影响
不同合金成分的ηa—fs曲线
3、流变性与组织的关系
半固态金属材料的性质(如表观粘度)必然受到材料内 部微观组织状态的影响。
部分凝固合金的内部组织状态由它的固相组织状态决定。
固相的数量、大小、形状和分布等参数决定了表观粘度的高 低。
(1) 固相分数
固相分数越高,部分凝固合金液相量越少,流动性 越差。表观粘度随固相分数增加而上升。 (2) 搅拌强度对半固态组织的影响
电磁搅拌用磁感应强度描述搅拌强度,电磁搅拌造 成“晶粒倍增”。
不同搅拌强度下Al-6.6%Si合金组织
在电磁搅拌作用下,铝液的湍流对流不断将热脉冲带到液 固界面,加速枝晶臂的熔化,枝晶臂被分离后,随湍流带到 稍微过冷的液体中,形成新的晶体,造成晶粒倍增。 搅拌强度越大,晶粒倍增现象越明显,晶粒越细小。
(3)随着固相分数的降低,呈现黏性流体特性,在微小外力作用下
即可很容易变形流动; (4)当固相分数在极限值(约75%)以下时,浆料可以进行搅拌, 并可很容易混入异种材料的粉末、纤维等;
图4-2 半固态金属和强化粒子(纤维)的搅拌混合
(5)由于固相粒子间几乎无结合力, 在特定部位虽然容易分离,但由
半固态加工技术最新进展
半固态加工技术的最新发展及应用摘要:金属半固态加工技术是21世纪前沿性金属加工技术,具有高效、节能、近终型生产和成型件性能高等许多优点。
本文着重概述了半固态金属制浆(坯)工艺的研究新进展,并展示了半固态成形技术在高合金化铝合金控制凝固与成型方面的应用与进展。
关键词:半固态加工;均匀凝固;发展趋势;应用1金属半固态加工技术简介20世纪70年代初,美国麻省理工学院(MIT)的Flemings等研究者们提出了一种金属成型新方法,即半固态加工技术(Semi-Solid Metalor SemiSolid Forming,简称SSM或SSF)。
所谓半固态加工是指金属在凝固过程中,对其施以剧烈的搅拌作用或扰动作用,得到一种液态金属母液,其中均匀悬浮着一定量的球状初生固相或退化的枝晶固相的固-液混合浆料(也称流变浆料),对这种浆料进行的加工成型的方法。
半固态成型包括半固态流变成型和半固态触变成型两类,前者是将制备好的半固态浆料直接用于成型,如压铸成型(称为半固态流变压铸成型);后者是对制备好的半固态坯料进行重新加热使其达到半熔融状态,然后进行成型,如挤压成型(称为半固态触变挤压)[1]。
半固态成型方法打破了传统的枝晶凝固模式,开辟了强制均匀凝固的先河,与以往的金属成型方法相比,半固态金属成型在获得均匀细晶组织、提高力学性能、缩短加工工序、节约能源及成型件性能等方面具有明显的优势。
制浆的目的是为了控制凝固过程中的晶体形核与长大形态,以获得细小均匀的显微组织,从而提高材料的综合性能。
但是目前大多数的制浆方法在实际应用方面都还存在不同程度上的局限性,制约了这项技术的工业化推广应用。
因此,近年来半固态浆料制备方法仍在不断的努力探索,推进着半固态加工技术的向前发展。
目前已有包括中国在内的二十多个国家和地区开展了半固态成型研究。
研究对象主要集中在铝合金和镁合金材料的成型。
铝合金半固态成型方法主要有流变压铸、触变压铸、触变锻造等;而镁合金半固态成型的成熟技术目前主要有半固态触变注射成型技术[2]。
半固态金属成形技术
二、半固态成形技术的发展简史
起源和发展
半固态加工起源于美国。20世纪70年代初,麻省理工学院 Spencer和Flemings等人发现凝固过程中的金属材料经强力搅 拌,会生成近球状晶或球状晶组织。 30多年的发展历程中,SSM技术在制坯、重熔加热、零件成 形、组织与力学性能、加工环节数值模拟以及合金流变学研究 等许多方面取得重大进展。目前,这项技术已广泛应用于汽车 工业领域,在航空、航天以及国防工业领域也正处于应用的起 步阶段,具有广阔的前景。 半固态金属加工技术是近多年来才诞生和发展起来的现代 冶金加工新技术。它虽然诞生晚, 但发展很快, 只用十几年的 时间就从试验室过渡到试生产, 又很快实现了产业化和商品化。 被世人称为新一代的合金成形工艺。
三、半固态金属加工的优缺点
优点:
(1) 由于在半固态, 合金具有独特的触变 行为, 可成型复杂的薄壁的零部件
(2)加工件的精度高, 几乎是近净成形, 尺 寸公差接近机加精度 (3)成形件表现平整光滑, 内部组织致密, 缺陷少, 晶粒细小, 力学性能高,可达锻 件性能
(4)节省原材料、能源, 生产同样的零部件, 它与普通铸造相比, 节能约35% (5)成品率高, 几乎达100%
半固态金属成形
一、概念
半固态金属成形技术(Semi-Solid Metal processing,SSM),它是利用在固-液态区间 获得一种液态金属母液中均匀地悬浮着一定固 相组分(50%-60%)合金的混合浆料进行加工 成形的方法。 半固态成形是利用金属材料从固态向液态, 或从液态向固态的转换过程中具有半固态的特 性所实现的成形。
影响因素对结构影响的具体分析
1、板长固定,不同板角下的组织形貌
20度
5度
7.5度
- 1、下载文档前请自行甄别文档内容的完整性,平台不提供额外的编辑、内容补充、找答案等附加服务。
- 2、"仅部分预览"的文档,不可在线预览部分如存在完整性等问题,可反馈申请退款(可完整预览的文档不适用该条件!)。
- 3、如文档侵犯您的权益,请联系客服反馈,我们会尽快为您处理(人工客服工作时间:9:00-18:30)。
4 金属半固态加工4.1概述4.1.1半固态加工的概念与特点4.1.1.1半固态加工的概念传统的金属成形主要分为两类:一类是金属的液态成形,如铸造、液态模锻、液态轧制、连铸等;另一类是金属的固态成形,如轧制、拉拔、挤压、锻造、冲压等。
在20世纪70年代美国麻省理工学院的Flemimgs教授等提出了一种金属成形的新方法,即半固态加工技术。
金属半固态加工就是在金属凝固过程中,对其施以剧烈的搅拌作用,充分破碎树枝状的初生固相,得到一种液态金属母液中均匀地悬浮着一定球状初生固相的固-液混合浆料(固相组分一般为50%左右),即流变浆料,利用这种流变浆料直接进行成形加工的方法称之为半固态金属的流变成形(rheoforming);如果将流变浆料凝固成锭,接需要将此金属锭切成一定大小,然后重新加热(即坯料的二次加热)至金属的半固态温度区,这时的金属锭一般称为半固态金属坯料。
利用金属的半固态坯料进行成形加工,这种方法称之为触变成形(thixoforming)。
半固态金属的上述两种成形方法合称为金属的半固态成形或半固态加工(semi-solid forming or processing of metals),目前在国际上,通常将半固态加工简称为SSM(semi-solid metallurgy)。
就金属材料而言,半固态是其从液态向固态转变或从固态向液态转变的中间阶段,特别对于结晶温度区间宽的合金,半固态阶段较长。
金属材料在液态、固态和半固态三个阶段均呈现出明显不同的物理特性,利用这些特性,产生了凝固加工、塑性加工和半固态加工等多种金属热加工成形方法。
凝固加工利用液态金属的良好流动性,以完成成形过程中的充填、补缩直至凝固结束。
其发展趋势是采用机械压力替代重力充填,从而改善成形件内部质量和尺寸精度.但从凝固机理角度看,凝固加工要想完全消除成形件内部缺陷是极其困难的,甚至是不可能的。
塑性加工利用固态金属在高温下呈现的良好塑性流动性,以完成成形过程中的形变和组织转变。
与凝固加工相比,采用塑性加工成形的产品质量明显好,但由于固态金属变形抗力高,所需变形力大,设备也很庞大,因此要消耗大量能源,对于复杂零件往往需要多道成形工序才能完成。
因此,塑性加工的发展方向是降低加工能耗和成本、减小变形阻力、提高成形件尺寸精度和表面与内部质量。
由此出现了精密模锻、等温锻造和超塑性加工等现代塑性加工方法。
半固态加工是利用金属从液态向固态转变或从固态向液态转变(即液固共存)过程中所具有的特性进行成形的方法。
这一新的成形加工方法综合了凝固加工和塑性加工的长处。
即加工温度比液态低、变形抗力比固态小,可一次大变形量加工成形形状复杂且精度和性能质量要求较高的零件。
所以,国外有的专家将半固态加工称为21世纪最有前途的材料成形加工方法。
图4-l表示金属在高温下三态成形加工方法的相互关系。
4.1.1.2 半固态金属的特点半固态金属(合金)的内部特征是固液相混合共存,在晶粒边界存在金属液体。
根据固相分数不同,其状态不同,图4-2表示半固态金属的内部结构。
在高固相分数时,液相成分仅限于部分晶界(见图4-2(a));在低固相分数时,固相颗粒游离在液相成分之中(见图4-2(b))。
半周态金属的金属学和力学主要有以下几个特点。
(1) 由于固液共存,在两者界面熔化、凝固不断发生,产生活跃的扩散现象。
因此溶质元素的局部浓度不断变化;(2) 由于晶粒间或固相粒子间夹有液相成分。
固相粒子间几乎没有结合力,因此,其宏观流动变形抗力很低;(3) 随着固相分数的降低,呈现黏性流体特性,在微小外力作用下即可很容易变形流动;(4) 当固相分数在极限值(约75%)以下时,浆料可以进行搅拌,并可很容易混入异种材料的粉末、纤维等,如图4-3所示:(5) 由于固相粒子间几乎无结合力,在特定部位虽然容易分离,但由于液相成分的存在,又可很容易地将分离的部位连接形成一体化,特别是液相成分很活跃,不仅半固态金属间的结合,而且与一般固态金属材料也容易形成很好的结合,如图4-4所示:(6) 即使是含有陶瓷颗粒、纤维等难加工性材料,也可通过半熔融状态在低加工力下进行成形加工;(7) 当施加外力时,液相成分和固相成分存在分别流动的情况。
虽然施加外力的方法和当时的边界约束条件可能不同,但一般来说,存在液相成分先行流动的倾向或可能性,如图4-5所示;(8) 上述现象在固相分数很高或很低或加工速度特别高的情况下都很难发生,主要是在中间固相分数范围或低加工速度情况下显著。
与普通的加工方法相比半固态金属加工具有许多独特的优点:(1)黏度比液态金属高,容易控制:模具夹带的气体少,减少氧化、改善加工性,减少模具粘接,可进行更高速的部件成形,改善表面光洁度,易实现自动化和形成新加工工艺;(2) 流动应力比固态金属低:半固态浆料具有流变性和触变性,变形抗力非常小,可以更高的速度成形部件,而且可进行复杂件成形,缩短加工周期,提高材料利用率,有利于节能节材,并可进行连续形状的高速成形(如挤压),加工成本低;(3) 应用范围广:凡具有固液两相区的合金均可实现半固态加工。
可适用于多种加工工艺,如铸造、轧制、挤压和锻压等,并可进行材料的复合及成形:4.1.2 半固态加工的基本工艺方法半固态加工的基本工艺方法可分为流变成形(rheoforming)和触变成形(thixoforming)两种。
如图4-6所示,经加热熔炼的合金原料液体通过机械搅拌、电磁搅拌或其他复合搅拌,在结晶凝固过程中形成半固态浆料,下面的工艺分两种:其一是将半固态浆料直接压入模具腔进而压铸成形或对半固态浆料进行直接轧制、挤压等加工方式成形,即流变成形;另一种是将半固态浆料制成坯料,经过重新加热至半固态温度,形成半固态坯料再进行成形加工,此即触变成形。
图4-7为半固态流变成形和触变成形工艺流程示意图。
4.1.3半固态加工的研究及发展4.1.3.1 国外研究现状20世纪70年代初期,美国麻省理工学院的M. C. Flemings教授和David Spener博士提出了半固态加工技术,由于该技术采用了非枝晶半同态浆料,打破了传统的枝晶凝固模式,具有许多独特的优点,因此关于半固态金属成形的理论和技术研究引起各国研究者的高度重视,半同态加工的产品及应用也随之得到迅速的发展。
20世纪80年代后期以来,半同态加工技术已得到了各国科技工作者的普遍承认,目前已经针对这种技术开展了年多工艺实验和一些理论研究。
根据所研究的材料,可分为有色金属及其合金的低熔点材料半固态加工和钢铁材料等高熔点黑色金属材料半固态加工。
(1) 有色金属及其合金的低熔点材料半固态成形研究20世纪70年代以来,美国、日本等国针对铝、镁、铅、铜等的合金进行了研究,其重点主要放在成形工艺的开发上。
目前,国外进入工业应用的半固态金属主要是铝、镁合金,这些合金最成功的应用主要集中在汽车领域,如半固态模锻铝合金制动总泵体、挂架、汽缸头、轮毂、压缩机活塞等。
铝合金半固态加工技术(触变成形)已经成熟并进入规模生产,主要应用于汽车、电器、航空航天等领域。
如美国的Alunaxm公司1997年的两座半固态铝合金成形汽车零件生产工厂的生产能力分别达到每年5000万件。
意大利的Strampal SPA和Fiat Auto公司生产的半固态铝合金汽车零件重达7kg,而且形状很复杂;意大利的MM公司(Magneti Marelli)为汽车公司生产半同态铝合金成形的Fuelinjection Rail零件,在2000年达到日产7500件。
瑞士的Bubler公司已经生产出铝合金半固态触变成形的专用SC型压铸机(实时压射控制和单一压射缸)和铝合金半固态坯料的专用二次加热设备。
日本的Speed Star Wheel公司已经利用半固态金属成形技术生产铝合金轮毂(重约5kg)。
与铝合金半固态成形比较,镁合金的半固态成形技术发展较晚,目前成熟的技术只有Thixomolding技术。
1995年,美国的Thixomat公司的子公司—Lindberg公司利用Thixomolding 工艺,为一些汽车公司生产了50余万件的半固态镁合金铸件。
日本的一些公司利用Thixomolding 工艺制造移动通讯手机外壳、微型便携式计算机外壳等。
但Thixomolding工艺必须要求提供合适的镁合金屑,这就使得该技术比较复杂、生产成本比较高。
近年,英国布鲁诺(Brunel)大学研制出低熔点合金双螺旋半固态流变成形机,目前正在向产业化方向发展。
另外,最近资料报道,一些发达国家正在开发镁合金半固态连铸坯料和触变成形技术,这些情况说明镁合金的半固态成形技术仍然处在不断发展之中,将会出现新的技术突破。
十几年来,关于半固态加工实验方面的研究主要集中在浆料的制备和材料的成形两方面,先后开发出了机械搅拌法、单辊旋转法、电磁搅拌法、超声振动法、直流脉冲法等浆料制备方法以及压铸成形、模锻成形、注射成形和连铸成形等材料成形工艺。
理论上的研究主要是围绕与工艺实现和试样组织、性能有关方面。
在此研究成果基础上,近年来又针对浆料固相分数的控制与测定、输送、工艺参数如变形抗力、成形线速度和铸型温度等对试样的表面质量、内部成分和组织分布规律的影响等较高层次的问题开展了较为系统的理论研究,取得了一定的进展。
另外,在纤维和颗粒增强材料、与陶瓷等的复合材料方面也进行了一些研究。
但关于加工过程中凝固模型的建立和理论模拟等方面的高层次研究还并不多见。
(2) 高熔点黑色金属的半固态成形研究到目前为止,国际上共召开了7次半固态加工方面的专题国际学术会议,从研究的材料来看,绝大多数是关于铝合金、镁合金等低熔点材料。
如2000年9月底在意大利召开的第6届半固态加工国际学术会议上,共发表学术论文134篇,但其中关于高熔点钢铁材料半固态加工的研究论文仪6篇。
所涉及的钢铁材料为M2、共析钢、H11钢和不锈钢等。
由此可见钢铁材料半固态加工的有关基础和应用研究任重道远,但一旦取得突破,其前景将十分光明。
但到了2002年9月在日本筑波召开的第七届半固态加工国际学术会议,研究状况有了一些新的发展。
在此次学术交流会议上,共发表论文148篇,其中关于高熔点钢铁材料半固态加工的研究论文13篇,会议专设了一个钢铁材料半固态加工研讨的分会场。
采用半固态加工方法所研究的高熔点材料涉及D2、HS6-2-5高速工具钢、100Cr6钢、60Si2Mn弹簧钢、AIS1304不锈钢、C80工具钢、铸铁等钢铁材料,半固态加工方法涉及触变锻压、挤压、铸造和直接流变轧制及喷铸成形等等。
根据已有的文献和研究结果来看,高熔点黑色金属半固态加工之所以进展缓慢,其中的重要原因在于以下困难:(1) 选择的材料液固线温度区间较小;(2) 高温半固态浆料难以连续稳定地制备;(3) 熔体的温度、固相的比率和分布难以准确控制;(4) 浆料在高温下输送和保温困难;(5) 成形温度高,工具材料的高温性能难以保证等等。