苯乙烯乳液聚合
四种聚合方法生产的聚苯乙烯的用途
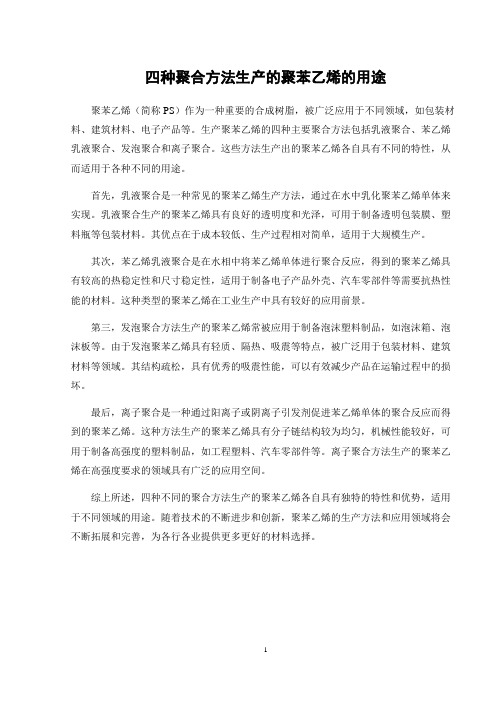
四种聚合方法生产的聚苯乙烯的用途聚苯乙烯(简称PS)作为一种重要的合成树脂,被广泛应用于不同领域,如包装材料、建筑材料、电子产品等。
生产聚苯乙烯的四种主要聚合方法包括乳液聚合、苯乙烯乳液聚合、发泡聚合和离子聚合。
这些方法生产出的聚苯乙烯各自具有不同的特性,从而适用于各种不同的用途。
首先,乳液聚合是一种常见的聚苯乙烯生产方法,通过在水中乳化聚苯乙烯单体来实现。
乳液聚合生产的聚苯乙烯具有良好的透明度和光泽,可用于制备透明包装膜、塑料瓶等包装材料。
其优点在于成本较低、生产过程相对简单,适用于大规模生产。
其次,苯乙烯乳液聚合是在水相中将苯乙烯单体进行聚合反应,得到的聚苯乙烯具有较高的热稳定性和尺寸稳定性,适用于制备电子产品外壳、汽车零部件等需要抗热性能的材料。
这种类型的聚苯乙烯在工业生产中具有较好的应用前景。
第三,发泡聚合方法生产的聚苯乙烯常被应用于制备泡沫塑料制品,如泡沫箱、泡沫板等。
由于发泡聚苯乙烯具有轻质、隔热、吸震等特点,被广泛用于包装材料、建筑材料等领域。
其结构疏松,具有优秀的吸震性能,可以有效减少产品在运输过程中的损坏。
最后,离子聚合是一种通过阳离子或阴离子引发剂促进苯乙烯单体的聚合反应而得到的聚苯乙烯。
这种方法生产的聚苯乙烯具有分子链结构较为均匀,机械性能较好,可用于制备高强度的塑料制品,如工程塑料、汽车零部件等。
离子聚合方法生产的聚苯乙烯在高强度要求的领域具有广泛的应用空间。
综上所述,四种不同的聚合方法生产的聚苯乙烯各自具有独特的特性和优势,适用于不同领域的用途。
随着技术的不断进步和创新,聚苯乙烯的生产方法和应用领域将会不断拓展和完善,为各行各业提供更多更好的材料选择。
1。
苯乙烯的乳液聚合实验报告
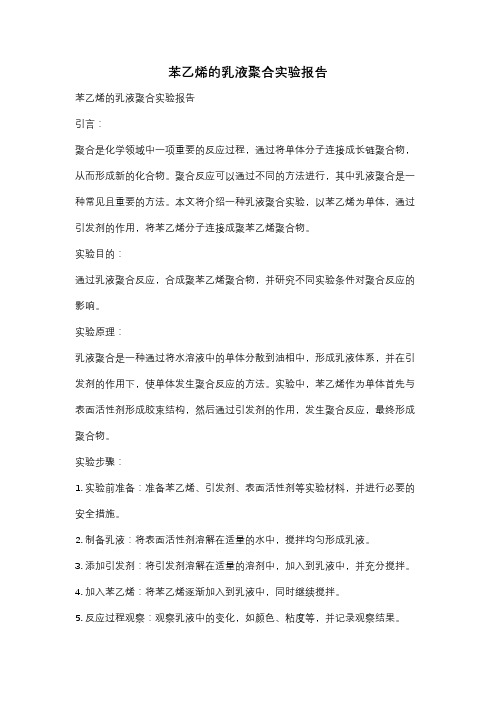
苯乙烯的乳液聚合实验报告苯乙烯的乳液聚合实验报告引言:聚合是化学领域中一项重要的反应过程,通过将单体分子连接成长链聚合物,从而形成新的化合物。
聚合反应可以通过不同的方法进行,其中乳液聚合是一种常见且重要的方法。
本文将介绍一种乳液聚合实验,以苯乙烯为单体,通过引发剂的作用,将苯乙烯分子连接成聚苯乙烯聚合物。
实验目的:通过乳液聚合反应,合成聚苯乙烯聚合物,并研究不同实验条件对聚合反应的影响。
实验原理:乳液聚合是一种通过将水溶液中的单体分散到油相中,形成乳液体系,并在引发剂的作用下,使单体发生聚合反应的方法。
实验中,苯乙烯作为单体首先与表面活性剂形成胶束结构,然后通过引发剂的作用,发生聚合反应,最终形成聚合物。
实验步骤:1. 实验前准备:准备苯乙烯、引发剂、表面活性剂等实验材料,并进行必要的安全措施。
2. 制备乳液:将表面活性剂溶解在适量的水中,搅拌均匀形成乳液。
3. 添加引发剂:将引发剂溶解在适量的溶剂中,加入到乳液中,并充分搅拌。
4. 加入苯乙烯:将苯乙烯逐渐加入到乳液中,同时继续搅拌。
5. 反应过程观察:观察乳液中的变化,如颜色、粘度等,并记录观察结果。
6. 反应终止:根据需要,可以通过加热或加入适量的酸等方法终止聚合反应。
7. 分离聚合物:将聚合物从乳液中分离出来,并进行后续处理。
实验结果:在本次实验中,观察到乳液聚合反应发生了以下变化:1. 颜色变化:乳液由无色逐渐变为浑浊的白色乳状液体。
2. 粘度增加:乳液的粘度随着聚合反应的进行逐渐增加。
3. 聚合物形成:在实验结束后,从乳液中分离出了聚苯乙烯聚合物。
实验讨论:通过本次实验,我们成功地合成了聚苯乙烯聚合物,并观察到乳液聚合反应的变化过程。
乳液聚合反应是一种常见的聚合方法,具有以下优点:1. 乳液聚合反应适用于水溶性单体的聚合,可以在水相中进行,无需使用有机溶剂。
2. 乳液聚合反应可以控制聚合反应的速率和产物的分子量,通过调整引发剂的浓度和反应温度等条件,可以得到不同性质的聚合物。
实验五 苯乙烯乳液聚合
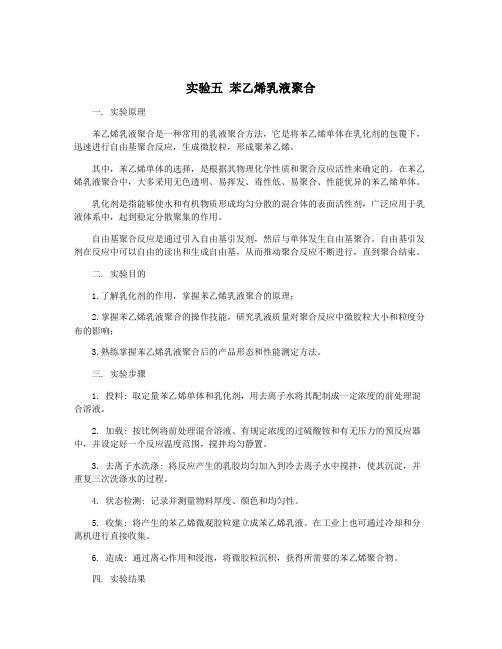
实验五苯乙烯乳液聚合一. 实验原理苯乙烯乳液聚合是一种常用的乳液聚合方法,它是将苯乙烯单体在乳化剂的包覆下,迅速进行自由基聚合反应,生成微胶粒,形成聚苯乙烯。
其中,苯乙烯单体的选择,是根据其物理化学性质和聚合反应活性来确定的。
在苯乙烯乳液聚合中,大多采用无色透明、易挥发、毒性低、易聚合、性能优异的苯乙烯单体。
乳化剂是指能够使水和有机物质形成均匀分散的混合体的表面活性剂,广泛应用于乳液体系中,起到稳定分散聚集的作用。
自由基聚合反应是通过引入自由基引发剂,然后与单体发生自由基聚合。
自由基引发剂在反应中可以自由的读出和生成自由基,从而推动聚合反应不断进行,直到聚合结束。
二. 实验目的1.了解乳化剂的作用,掌握苯乙烯乳液聚合的原理;2.掌握苯乙烯乳液聚合的操作技能,研究乳液质量对聚合反应中微胶粒大小和粒度分布的影响;3.熟练掌握苯乙烯乳液聚合后的产品形态和性能测定方法。
三. 实验步骤1. 投料: 取定量苯乙烯单体和乳化剂,用去离子水将其配制成一定浓度的前处理混合溶液。
2. 加载: 按比例将前处理混合溶液、有规定浓度的过硫酸铵和有无压力的预反应器中,并设定好一个反应温度范围,搅拌均匀静置。
3. 去离子水洗涤: 将反应产生的乳胶均匀加入到冷去离子水中搅拌,使其沉淀,并重复三次洗涤水的过程。
4. 状态检测: 记录并测量物料厚度、颜色和均匀性。
5. 收集: 将产生的苯乙烯微观胶粒建立成苯乙烯乳液。
在工业上也可通过冷却和分离机进行直接收集。
6. 造成: 通过离心作用和浸泡,将微胶粒沉积,获得所需要的苯乙烯聚合物。
四. 实验结果实验操作步骤完成后,观察到形成苯乙烯微胶粒的过程,颜色由无色透明逐渐变为白色,随着前处理混合溶液浓度的减小,胶粒微观大小和粒度分布的变化也逐渐明显。
实验中苯乙烯微观胶粒的大小和粒度分布与处理溶液浓度、乳化剂性质和浸泡时间等有关系。
实验结果表明,浓度适当的前处理混合溶液和表面活性剂,具有很好的乳化作用和稳定微胶粒的能力,能够有效地减小胶粒的尺寸和粒度分布范围。
苯乙烯乳液聚合聚合速率
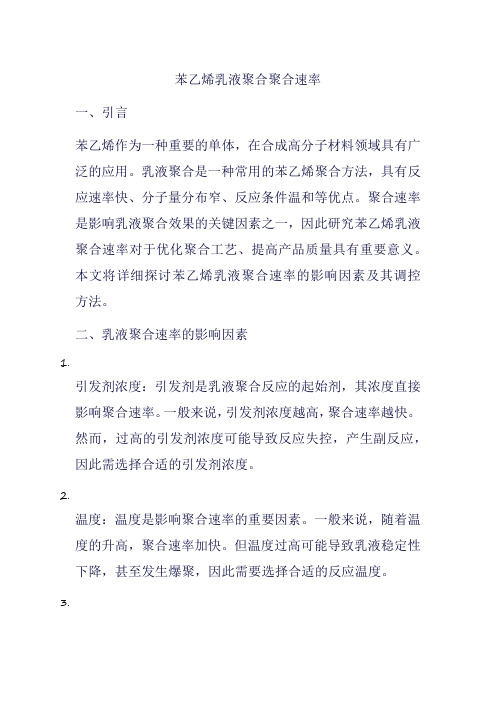
苯乙烯乳液聚合聚合速率一、引言苯乙烯作为一种重要的单体,在合成高分子材料领域具有广泛的应用。
乳液聚合是一种常用的苯乙烯聚合方法,具有反应速率快、分子量分布窄、反应条件温和等优点。
聚合速率是影响乳液聚合效果的关键因素之一,因此研究苯乙烯乳液聚合速率对于优化聚合工艺、提高产品质量具有重要意义。
本文将详细探讨苯乙烯乳液聚合速率的影响因素及其调控方法。
二、乳液聚合速率的影响因素1.引发剂浓度:引发剂是乳液聚合反应的起始剂,其浓度直接影响聚合速率。
一般来说,引发剂浓度越高,聚合速率越快。
然而,过高的引发剂浓度可能导致反应失控,产生副反应,因此需选择合适的引发剂浓度。
2.温度:温度是影响聚合速率的重要因素。
一般来说,随着温度的升高,聚合速率加快。
但温度过高可能导致乳液稳定性下降,甚至发生爆聚,因此需要选择合适的反应温度。
3.搅拌速度:搅拌速度影响乳液中单体和引发剂的分布,进而影响聚合速率。
适当的搅拌速度有利于提高聚合速率和乳液稳定性。
4.乳化剂类型和浓度:乳化剂是影响乳液稳定性的关键因素,同时也对聚合速率产生影响。
不同类型的乳化剂和浓度会对聚合速率产生不同的影响,因此需选择合适的乳化剂类型和浓度。
三、苯乙烯乳液聚合速率的调控方法1.优化引发剂浓度:通过调整引发剂的浓度,可以控制聚合速率。
在实际操作中,可以根据产品需求和反应条件,选择合适的引发剂浓度,以达到最佳的聚合效果。
2.控制反应温度:选择合适的反应温度,既可以保证乳液稳定性,又可以提高聚合速率。
在实际操作中,可以通过调整加热或冷却设备,精确控制反应温度。
3.调整搅拌速度:适当的搅拌速度可以提高乳液中单体和引发剂的分散效果,增加反应接触面积,从而提高聚合速率。
在实际操作中,可以根据乳液的性质和反应需求,调整搅拌速度。
4.选择合适的乳化剂和浓度:乳化剂的选择和浓度对乳液稳定性和聚合速率都有重要影响。
在实际操作中,可以根据乳液的稳定性和聚合速率的需求,选择合适的乳化剂和浓度。
ABS专题1 乳液聚合和本体聚合的差异

ABS专题1 乳液聚合和本体聚合的差异一、工艺路线1、乳液聚合工艺乳液聚合法是在乳液中的细小微粒进行聚合。
在聚合过程中,必须使用皂类添加剂,使反应可以在乳液中进行,而这些添加剂部分会残留在最终产品中,成为杂质,导致颜色变黄。
这些杂质对热十分敏感,所以最终产品在经过挤出或者注塑过程后会变得更黄,变黄的程度视牌号不同而各异。
乳液聚合的优点在于产品的灵活性比较大,产品可以有不同的热性能、流动性能和冲击性能组合。
2、本体连续聚合工艺本体聚合工艺使用苯乙烯作为溶剂,它在生产过程中会被完全回收并且循环利用,很少残留在最终产品中。
本体聚合工艺通常使用3-4个连续反应釜以线性排列连续生产。
由于本体聚合工艺不需要乳化剂,因此,生产的ABS树脂具有天然的白色。
同时因为本体聚合工艺的过程是连续的,所以树脂的质量非常的一致和稳定,在正常的挤出和注塑条件下,其颜色可以保持稳定。
二、加工技术1、乳液法的ABS这边就不做介绍了,各位一定都很熟悉的,主要介绍一下本体ABS的加工优点2、本体ABS的在下游加工上的优势A、增加下游产品的设计灵活性由于本体工艺可以生产出较低光泽度的ABS,可以直接注塑制成有低光泽度要求的制品B、适合色母染色本体ABS树脂的底色纯净而且很浅,使其染色效果十分出色。
C、降低色粉成本由于其出色的底色可以减少色粉的使用量,而且色粉用量的减少意味着密度的减少,并最终降低制品的成本。
此外,由于减少了色粉的使用量,降低了色粉对冲击性能的影响。
D、提高成品率本体ABS树脂的纯净度能减少银纹的产生。
E、更宽的加工范围由于本体ABS有较佳的热稳定性和加工稳定性,减少了树脂因为加工条件的变动而变黄给你改一改:ABS专题1:乳液聚合和本体聚合的(工艺与产品应用)差异一、工艺路线1、乳液聚合工艺。
苯乙烯的乳液聚合
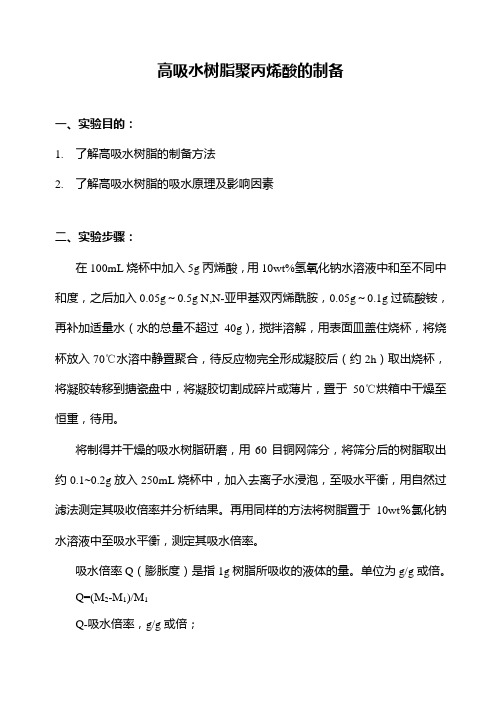
高吸水树脂聚丙烯酸的制备一、实验目的:1.了解高吸水树脂的制备方法2.了解高吸水树脂的吸水原理及影响因素二、实验步骤:在100mL烧杯中加入5g丙烯酸,用10wt%氢氧化钠水溶液中和至不同中和度,之后加入0.05g~0.5g N,N-亚甲基双丙烯酰胺,0.05g~0.1g过硫酸铵,再补加适量水(水的总量不超过40g),搅拌溶解,用表面皿盖住烧杯,将烧杯放入70℃水溶中静臵聚合,待反应物完全形成凝胶后(约2h)取出烧杯,将凝胶转移到搪瓷盘中,将凝胶切割成碎片或薄片,臵于50℃烘箱中干燥至恒重,待用。
将制得并干燥的吸水树脂研磨,用60目铜网筛分,将筛分后的树脂取出约0.1~0.2g放入250mL烧杯中,加入去离子水浸泡,至吸水平衡,用自然过滤法测定其吸收倍率并分析结果。
再用同样的方法将树脂臵于10wt%氯化钠水溶液中至吸水平衡,测定其吸水倍率。
吸水倍率Q(膨胀度)是指1g树脂所吸收的液体的量。
单位为g/g或倍。
Q=(M2-M1)/M1Q-吸水倍率,g/g或倍;M1-树脂(干态)质量,g;M2-树脂吸水饱和后的质量,g。
三、注意事项1.本实验为研究型实验,中和度、交联度和引发剂用量都为可选条件,同组的同学共享实验结果,并分析讨论不同配方对吸水倍率的影响因素。
2. 在中和过程中,氢氧化钠水溶液应滴加到丙烯酸中,使其缓慢放热。
中和度用摩尔比计算。
3. 在聚合过程中不可搅动溶液,聚合之后应用去离子水洗涤。
四、思考题:1. 高吸水性树脂一般具备什么样的结构?2. 高吸水性树脂的溶胀原理是什么?3. 影响高吸水性树脂吸水倍率的因素有哪些?五、高吸水性树脂的应用简介:高吸水性树脂是20世纪60年代发展起来的新型功能性高分子材料,它能吸收相当于自身质量数百倍甚至上千倍的液体,同时具有较高的保液能力,特殊的结构设计还可以使树脂具有对外界刺激的应答性响应,因此其用途极为广泛。
目前的产品主要用于医药卫生、农林园艺、建筑材料、食品和人工智能材料等方面。
实验5
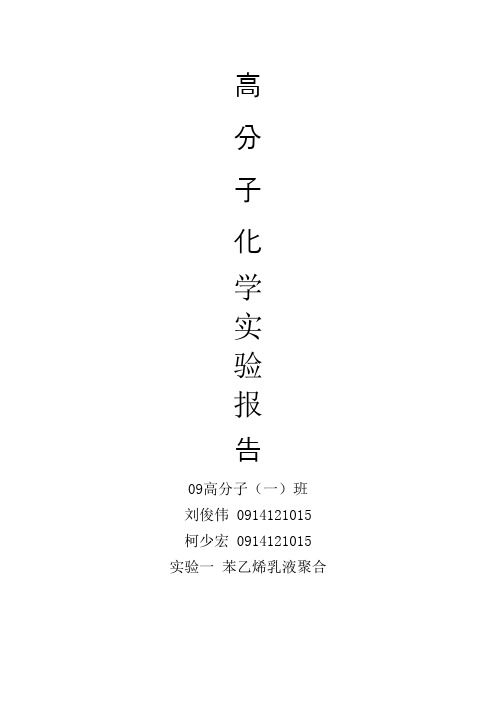
加入10 mL K2S2O8 溶液及10 mL 苯乙烯单体,迅速升温至88 ~90 ℃,并维持此温度1.5 h, 而后停止反应。 将乳液倒入150 mL 烧杯中,加NaCl,迅速搅拌使乳液凝聚。用布氏漏斗吸滤最后把产 物抽干,放于 50~60 ℃烘箱中干燥,称重、计算转化率并测定相对分子质量。
五、实验现象及分析
和悬浮聚合散热情况类似,但也有区别。对悬浮聚合来说,聚合反应发生在水相中的单体珠 中,单体珠滴的直径约在50 一2000um 范围之内,而在乳液聚合体系中,乳胶粒直径一般 在0.05—1um 之间。若把悬浮聚合中的一个单体珠滴比作一个10m 直径的大球,那么乳胶 粒仅象一个绿豆粒那么大。所以从乳胶粒内部内外传热比从悬浮聚合的珠滴内部向外传热要 容易得多。故在乳液聚合体系的乳胶粒中的温度分布要比在悬浮聚合体系的珠滴中的温度分 布均匀很多。 在烯类单体的自由基本体、溶液及悬浮聚合中,当引发剂浓度一定时,要想提高反应速 率,就得提高反应温度。而反应温度的提高,又加速引发剂的分解,使自由基总浓度增大。 因为链终止速率与自由基浓度平方成正比,故自由基总浓度增大链终止速率显著增大,这样 就会引起聚合物平均分子量减小;反过来,要想提高聚合物平均分子量,就必须降低反应温 度,这又会造成反应速率降低。就是说,要想提高分子量,必须降低反应速率;而要想提高 反应速率,就必须牺牲分子量的提高,故二者是矛盾的。但是乳液聚合可以将二者统一起来, 即既有高的反应速率,又可得到高分子量的聚合物。这是因为乳液聚合是按照和其他聚合方 法不同的机理进行的。在乳液聚合体系中,引发剂溶于水相,且在水相中分解成自由基。自 由基由水相扩散到胶束中或乳胶粒中,在其中引发聚合。聚合反应就发生在一个个被此孤立 的乳胶粒中。假如由水相向某一乳胶粒中扩散进束一个自由基,那么就在这个乳胶检中进行 链引发链增长,形成一个大分子链。当第二个自由基由水相扩散进入这个乳胶粒中以后,就 和这个乳胶牧中原来的那个自由基链发生碰撞而终止。就是说,在第二个自由基扩散进来以 前,在这个乳胶粒中链增长反应一直在进行。在本体聚合体系中,任意两个自由基都有相互 碰撞而彼终止的可能性。而在乳液聚合体系中,一个个自由基链被封闭在彼此孤立的乳胶粒 中,由于乳胶粒表面带电而产生乳胶粒间的静电斥力作用,使乳胶粒不能碰撞到一起面聚并, 就是说,不同乳胶粒中的自由基链之间碰撞到一起而进行终止的几率等于零。也就是说,不 同乳胶粒中的自由基链不能相互终止,只能和由水相扩散进来的韧始自由基发生链终止反 应。 故在乳液聚合中自由基链的平均寿命比用其他聚合方法时要长,自由基有充分的时间增长到 很高的分子量。另外,在乳液聚合体系中有着巨大数量的乳胶粒,其中封闭着巨大数量的自 由基进行链增长反应,自由基的总浓度比其他聚合过程要大。故乳液聚合反应比其他聚合过 程的反应速率要高。聚合速率大.同时分子量高,这是乳液聚合的一个重要的特点。高的反 应速率会使生产成本降低,而高的分子量则是生产高弹性的合成橡胶所必需的。 另外,大多数乳液聚合过程都以水作介质,避免了采用昂贵的溶剂以及回收溶剂的麻烦, 同时减少了引起火灾和污染的可能性。再者,在某些可以直接利用合成乳液的情况下,如水 乳浦、粘合剂、皮革、纸张、织物处理剂以及乳液泡沫橡胶等,采用乳液聚合法尤为必要。 另一方面,乳液聚合也有其自身的缺点。例如在需要固体聚合物的情况下,需经凝聚、洗豫、 脱水、干燥等一系列后处理工序,才能将聚合物从乳液中分离出来,这就增加了成本,再者, 尽管经过了后处理,但产品中的乳化剂也很难完全除净,这就使产物的电性能、耐水性等下 降。还有一个缺点就是乳液聚合的多变性,若严格按照某特定的配方相条件*生产可顺利地 进行i 但如果想使产品适合某种特殊需要,而将配方或条件加以调整,常常会出问题,要么 生产不正常,要么产品不合格。乳液聚合和溶液聚合、悬浮聚合一样,与本体聚合相比有一 个共同的缺点,那就是,由于加入了介质或溶剂而减少了反应器的有效利用空间。例如对于 典型的工业乳液聚合反应过程来说,单体约占总体积的40%一50%,在这种情况下,反应 器的有效体积为单体本身所占体积的两倍到两倍半.故设备利用率低。尽管乳液聚合过程有 上述这些缺点,但是它的可贵而难得的优点,仍决定了它具有很大的工业意义:丁苯橡胶、 丁隋橡胶、氯丁橡胶、聚丙烯酸酯、聚氯乙烯、聚醋酸乙烯配、聚四氟乙烯等均可用乳液聚 合法进行大规模工业生产。
苯乙烯乳液聚合实验心得
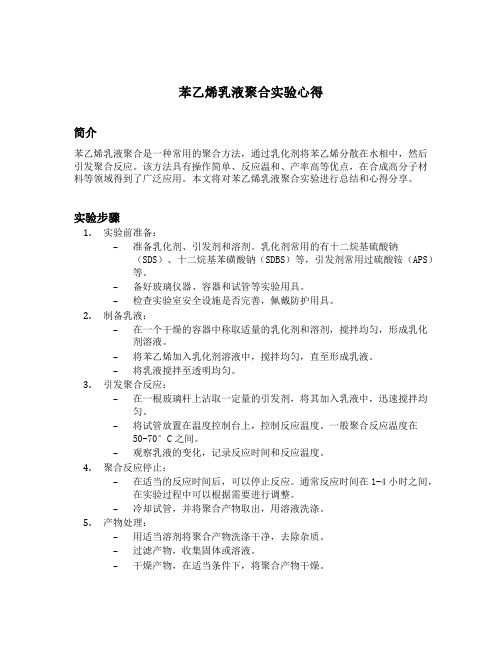
苯乙烯乳液聚合实验心得简介苯乙烯乳液聚合是一种常用的聚合方法,通过乳化剂将苯乙烯分散在水相中,然后引发聚合反应。
该方法具有操作简单、反应温和、产率高等优点,在合成高分子材料等领域得到了广泛应用。
本文将对苯乙烯乳液聚合实验进行总结和心得分享。
实验步骤1.实验前准备:–准备乳化剂、引发剂和溶剂。
乳化剂常用的有十二烷基硫酸钠(SDS)、十二烷基苯磺酸钠(SDBS)等,引发剂常用过硫酸铵(APS)等。
–备好玻璃仪器、容器和试管等实验用具。
–检查实验室安全设施是否完善,佩戴防护用具。
2.制备乳液:–在一个干燥的容器中称取适量的乳化剂和溶剂,搅拌均匀,形成乳化剂溶液。
–将苯乙烯加入乳化剂溶液中,搅拌均匀,直至形成乳液。
–将乳液搅拌至透明均匀。
3.引发聚合反应:–在一根玻璃杆上沾取一定量的引发剂,将其加入乳液中,迅速搅拌均匀。
–将试管放置在温度控制台上,控制反应温度。
一般聚合反应温度在50-70°C之间。
–观察乳液的变化,记录反应时间和反应温度。
4.聚合反应停止:–在适当的反应时间后,可以停止反应。
通常反应时间在1-4小时之间,在实验过程中可以根据需要进行调整。
–冷却试管,并将聚合产物取出,用溶液洗涤。
5.产物处理:–用适当溶剂将聚合产物洗涤干净,去除杂质。
–过滤产物,收集固体或溶液。
–干燥产物,在适当条件下,将聚合产物干燥。
实验心得1.实验前的认真准备对于实验的顺利进行非常重要。
仔细选择和准备乳化剂、引发剂和溶剂,以及实验用具,可以降低实验中的误差,提高反应的效果。
2.在制备乳液的过程中,搅拌的时间和强度对于乳液的均匀性和稳定性有重要影响。
搅拌不足会导致乳液不均匀,搅拌过度则可能引起乳液的稳定性下降。
3.引发剂的选择和使用量的控制会影响聚合反应的速率和效果。
过多的引发剂可能引起过快的聚合反应,反应过程失控;而过少的引发剂则可能导致聚合反应缓慢甚至无法进行。
4.反应温度的控制对于聚合反应的进行至关重要。
- 1、下载文档前请自行甄别文档内容的完整性,平台不提供额外的编辑、内容补充、找答案等附加服务。
- 2、"仅部分预览"的文档,不可在线预览部分如存在完整性等问题,可反馈申请退款(可完整预览的文档不适用该条件!)。
- 3、如文档侵犯您的权益,请联系客服反馈,我们会尽快为您处理(人工客服工作时间:9:00-18:30)。
实验四苯乙烯的乳液聚合及其共聚胶乳的合成
化工系毕啸天2010011811
一、实验目的
1.通过制备苯乙烯胶乳,了解乳液聚合的特点,各组份的作用。
2.掌握“理想乳液聚合体系”反应特点,以及用电解质凝聚胶乳和净化聚合物的方法。
3.掌握乳液聚合的制备工艺,了解合成共聚乳液方法和乳液稳定性的测定方法。
二、实验原理
乳液聚合是指在搅拌下,非水溶性或低水溶性单体借助乳化剂作用分散成乳状液进行的聚合反应。
乳液聚合与悬浮聚合是单体、水、乳化剂和水溶性引发剂。
乳液聚合得到的粒径一般在在10m
μ以下。
乳化剂浓度很低时,以单分子状态溶解于水中。
随着浓度增加到CMC值后,开始形成胶束。
在聚合过程中,胶束内有增溶的单体,引发与增长基本都在胶束中发生。
体系中最终有多少单体-聚合物颗粒主要取决于乳化剂和引发剂的种类和用量。
当温度、单体浓度、引发剂浓度、乳化剂种类一定时,在一定范围内,乳化剂用量越多、反应速度越快,产物相对分子质量越大。
乳化剂的另一作用是减少分散相与分散介质间的界面张力,使单体与单体-聚合物颗粒分散在介质中形成稳定的乳浊液。
乳液聚合的优点是:(1)聚合速度快、产物相对分子质量高。
(2)由于使用水作介质,易于散热、温度容易控制、费用也低。
(3)由于聚合形成稳定的乳液体系粘度不大,故可直接用于涂料、粘合剂、织物浸渍等。
如需要将聚合物分离,除使用高速离心外,亦可将胶乳冷冻,或加入电解质将聚合物凝聚,然后进行分离,经净化干燥后,可得固体状产品。
它的缺点是:聚合物中常带有未洗净的乳化剂和电解质等杂质,从而影响成品的透明度、热稳定性、电性能等。
尽管如此,乳液聚合仍是工业生产的重要方法,特别是在合成橡胶工业中应用得最多。
O乳液聚合
+
苯丙乳液
1/54/5
四、实验仪器
三口瓶,球冷,电热锅,恒压漏斗,搅拌棒,量筒,烧杯
六、实验注意事项
1.注意加料顺序,应当先加乳化剂后再投料,使之充分乳化。
此后再开始反应。
2.注意滴加顺序不能太快,否则不易得到较好的结构片段。
3.不要忘记补引发剂。
七、结果与讨论
1.固含量
固含量是乳液或涂料在规定条件下烘干后剩余部分占总量的质量百分数。
其实叫“不挥发份含量”更确切。
高固含量乳液并无明确的定义,一般认为固含量大于60%即为高固含量乳液,它与固含量在50%以下通常的乳液相比,具有生产效率高、运输成本低、干燥快、能耗低等优点。
本实验中,固含量即加入的单体量与总质量之比。
加入的总质量为60g 水,0.18g 乳化剂,0.4g 引发剂,加入引发剂时带入了5g 水。
再根据投料比计算出加入单体质量,即可得到如下理论固含量表。
实验者 配方体积比 (苯乙烯:丙烯酸丁酯)
理论固含量 实测固含量
田雯婷 0:5
21.5% 21.2% 毕啸天 1:4
21.6% 21.4% 刘政阳 2:3
21.6% 23.8% 颜怀宇 3:2
21.6% 20.4% 张亚清 4:1
21.7% 20.6% 梅豪 5:0
21.7% 22.5% 整体来看,我和田田的数据基本与理论相差无几。
剩余的几组相差稍微大一些。
我记得梅豪实验时壁上结块较多,别的人不记得了。
固含量偏小即表示高分子比理论值相对偏少,反应不完全。
我觉得梅豪结块应该会比理论值小啊,可是实际他又大了……不会分析…… 2.成膜现象
实验者 配方体积比 (苯乙烯:丙烯酸丁酯)
成膜现象
田雯婷 0:5 粘手 毕啸天 1:4 略粘手 刘政阳 2:3 360度无死角完美 颜怀宇 3:2 略掉渣,膜基本透明 张亚清 4:1 掉渣,膜不透明 梅豪 5:0 掉渣明显,膜不透明
考虑这个问题先从玻璃化转变温度入手。
聚苯乙烯的侧基是苯环,刚性较强,玻璃化温度100℃。
聚丙烯酸丁酯的侧基是柔性的酯,玻璃化温度-56℃。
根据Fox 方程
gB
B gA
A g
T W T W T +
=
1,可以由以上比例估算出各组实验的理论玻璃化温度。
实验者 配方体积比
(苯乙烯:丙烯酸丁酯)
Fox 理论玻璃化温度/℃
田雯婷
0:5
毕啸天 1:4
-35.9756 刘政阳 2:3
-12.0122 颜怀宇 3:2
17.1793 张亚清 4:1
53.51931 梅豪 5:0
100 理论上讲,张亚清、梅豪组的玻璃化温度应该在50℃以上,这时高分子室温下是玻璃态,基本是刚性的,在室温下完全不会成膜。
所以最终在玻璃板上只形成了一层粉,一摸就掉。
用硬球理论解释,在成膜时水分挥发,刚性较大的硬球不会变形,最终也不会融合。
在玻璃板上并没有形成均相,而是小颗粒。
就像墙上掉粉一样。
刘政阳组的透明而不粘手,刚柔并济恰到好处,就像高质的清漆一样。
高分子形成了均相体系,而且酯的含量适宜,没有粘手感。
我和田田组的粘手,是酯的含量偏大了,这样的产品可以用作粘合剂。
八、参考文献
1.《高分子化学》,唐黎明、庹新林编著,清华大学出版社
2.《高分子化学实验与技术》,杜奕编著,清华大学出版社
九、思考题
1.根据乳液聚合机理和动力学,解释乳液聚合反应速度快和产物分子量高的原因。
对于任何一个乳胶粒,俘获自由基后引发,当再一个自由基进入后,迅速链终止,乳胶粒暂时停止聚合。
聚合和不聚合的过程交替进行直到反应结束,相当于乳胶粒有一半时间在聚合,另一半时间休眠,平均自由基数为0.5。
假定单位体积内的乳胶粒数目为N ,则聚合反应的乳胶粒数为2
N ,单位体积乳胶粒中
发生聚合的乳胶粒数A
N N M 2][=
⋅。
对单个乳胶粒,聚合速率可表示为][M k r p p =。
总聚合速率为A
p p p N
M N k M M k R 2][]][[=
⋅=。
乳液聚合可以分三个阶段,即加速期、匀速期和减速期。
从上式可以判断三个阶段内的速率变化。
在加速期乳胶粒数不断增加;匀速期乳胶粒数保持恒定,乳胶粒内单体浓度不断下降,聚合速率下降。
由此可见,乳液聚合速率取决于乳胶粒数。
典型乳液聚合中N 可达1014个/mL ,即][⋅M 约为10-7mol/mL ,比典型自由基聚合高一个数量级。
同时,聚合物和单体达到溶胀平衡时,单体体积分数为0.5~0.85,相当于乳胶粒内单体浓度为5mol/L ,因此,乳液聚合速率很高。
乳液聚合中乳胶粒内聚合时间较长,碰撞几率较小,自由基寿命很长,因此分子量较大。
2.在乳液聚合中若乳化剂浓度低于CMC 值时,将有什么结果?
在反应的第一个阶段,胶束成核形成乳胶粒,乳胶粒数目不断增加。
随着随着聚合的进行,乳胶粒内的单体不断消耗,液滴内单体溶入水相,不断向乳胶粒扩散补充,以保持乳胶粒内单体浓度的恒定,所以单体液滴起着供应单体仓库的作用,单体液滴不断变小。
随着反应的进行,乳胶粒不断长大。
为了保持体系的稳定性,它需要不断从水相中吸咐更多的乳化剂。
当水相乳化剂浓度小于CMC 值后,未成核的胶束呈现不稳定状态,会重新溶解分散到水相中,导致未成核胶束减少直到消失。
从而体系不再形成新的乳胶粒,乳胶粒数恒定。
如果这题问的是一开始就低于CMC 的话,目测一个核都不会形成。
那体系中的单体都只以液滴形式存在,乳化剂则以溶解的分子存在,两者没什么关系。
引发剂在水相引发后,以极低的概率成功在相界面上引发单体。
总体来说,这样应该不会反应。
3.若在本实验体系中采用油溶性引发剂,实验结果将会如何?
乳液聚合应当让引发剂在水相中分解产生自由基,然后由胶束捕获后引发增长。
如果
用油溶性引发剂,那么引发剂开始会直接溶解在单体中,跟乳液聚合无关。
因为乳液
聚合是交替引发、终止,从而延长了增长时间,使得同时获得高分子量与高速率。
如
果引发剂直接溶解在了单体里,感觉有点像无数的小本体。
4.如果共聚乳液的制备采用批量法结果将如何?
用批量法时需要在最初将原料都投入体系中。
本体系中两种单体分别是苯乙烯和丙烯酸丁酯,二者竞聚率不同,苯乙烯的活性强于丙烯酸丁酯。
因此直接投料可能会让高活性单体大量进入增长链中,而低活性链则几乎不发生反应。
这样制备出的是接近嵌段的结构,并不是我们希望的交替。
5.采用何种手段可以提高乳液稳定性?
(1)控制pH值。
引发剂分解速率、分散剂稳定性均与pH值密切相关。
改变pH应当会对乳化剂的HLB值产生影响,从而改变乳液的稳定程度。
(2)控制单体滴入速度。
随着单体的加入,乳化剂分子要吸附到单体分子上,再捕获自由基成核。
如果单体滴入太快,则胶束成核可能赶不上胶粒加入速度,降低乳液的稳定性。
(3)适当的电解质的浓度。
适当的电解质浓度可以让乳液吸附形成电层而稳定,但是电解质浓度大了之后则会起到破乳作用。
(4)引发剂加入时间。
应当让乳化剂充分溶解,加入单体乳化后再加入引发剂反应。
如果加入引发剂太早,分解过早,不能被胶束捕获成核,则起不到乳液聚合的效果。