复合材料层合板的厚度方向性能和层间性能_张汝光[1]
复合材料性能试验方法选择和结果评价

复合材料性能试验方法选择和结果评价张汝光(上海玻璃钢研究院 200126)摘要:由于复合材料性能的多样性和性能机理的复杂性,其试验方法也同样多样、复杂。
应该根据试验目的和考虑材料的性能机理,正确选择试验方法或制订试验方案,以确保试验结果的可靠性。
对试验方法和试验结果都要作科学的评价。
关键词:复合材料性能试验 多样性 复杂性 可靠性1 概 述要用好材料,首先就要认识材料。
认识材料的最重要途径就是通过材料的性能试验。
由于复合材料本身就是个结构,在进行复合材料产品设计时,不能简单地选择材料,而是要同时设计复合材料。
因此认识材料就不单单是了解材料的性能数值范围,而还要了解复合材料的性能机理。
复合材料性能试验变得更加重要。
复合材料的性能试验一般有三种不同的目的。
一是揭示复合材料的材料性能机理;二是取得用于产品设计的材料性能参数;三是取得供材料质量评定用的材料性能参数。
试验目的的不同,对试验方法的要求,就有各自不同的侧重点,自然就会有不同的试验方法或方案。
复合材料细观不均匀结构的本质,使其性能不但具有各向异性的特点,在许多情况下,还具有各种耦合效应。
这就使得复合材料的性能试验相对于常规材料,要多样、复杂,同时也具有更多的影响材料性能的因素。
在制订试验方案或选择试验方法时,这些方面都应该加以考虑,做认真、细致的分析。
对试验方法和试验结果都要作科学的评价。
2复合材料性能试验的目的制订试验方案或选择试验方法,首先要根据自己的试验目的。
即使是对同一个性能,目的不同,对试验方案或方法也会有不同的考虑和选择。
2.1为揭示材料性能机理的性能试验揭示材料性能机理,就是揭示在一定条件下材料作出响应的全过程及其原因,揭示各种因素是如何影响这一过程。
显然,以揭示材料性能机理为目的的材料性能试验,要强调的是试验所得到的性能规律首先必须是定性上准确。
因此,在考虑试验方法时,首先要确保这一点。
例如,当我们要揭示某一因素对某一性能的影响规律时,在试验条件中要特别注意严格排除其他影响因素同时发生变化,否则试验结果就无法说明是哪一因素的影响规律,测试数据再准确也毫无用处。
叶片结构设计(简)
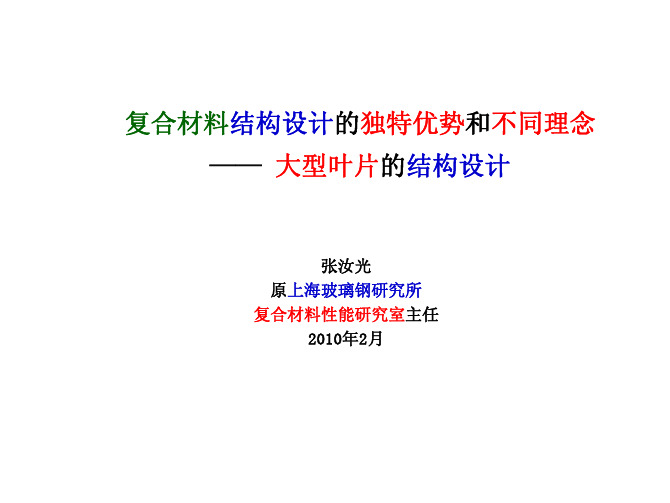
“随意摆布”的工艺;“一张白纸”的性能;“自由灵活”的结构设计
不同制品
“度身剪裁” “一一对应”
最合理结构、最合适材料和最有效工艺
复合材料需要有丰富创意灵感的工程师; 复合材料同时为他提供施展才华的大舞台 !
● “度身剪裁”、“一一对应”的结构设计, 更需要有创新
对应不同的制品:采用不同的材料,不同结构,不同工艺。 实现最优化设计 !
● 手糊成型工艺 ( Hand layup processes ) ● 喷射成型工艺 ( Spayup processes ) ● 模压成型工艺 ( Compression molding ) ● 缠绕成型工艺 ( Filament winding ) ● 拉挤成型工艺 ( Pultrusion )( 缠绕拉挤成型工艺 ) ● 卷管成型工艺 ( Tube rolling ) ● 自动铺放成型工艺 ( Automated fiber placement & Automated
无论是 ,材料性能、结构或构件形式和制造工艺 都可以“度身剪裁”做到“一一对应” 。
可以为制品优化设计:最好的结构、材料和工艺
● 复合材料“ 自由灵活 ”的结构设计
很大的设计自由度,广阔的创意空间。
可以对制品“度身剪裁”
a. 更自由优化设计制品外形; b. 更灵活优化设计结构和结构件形式; c. 更自由优化设计各种性能材料; d. 更灵活处理连接形式; e. 更容易进行结构整体设计。
▲ 材料设计创意(例)
◆ 具有突变刚度的复合材料 ◆ 负泊松比复合材料; ◆ 零热膨胀系数复合材料 ; ◆ 弯-扭耦合;
……….. 等等。
L 不发生热胀冷缩
◆ 突变刚度原理:
碳纤维, 以正弦曲线排列铺设, 增强橡胶。
胶接碳纤维复合材料层合板拉伸性能及有限元模拟_张明星
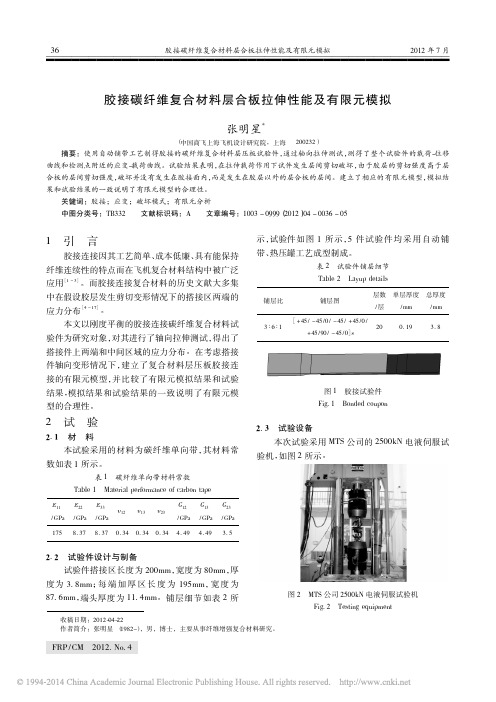
胶接碳纤维复合材料层合板拉伸性能及有限元模拟张明星*(中国商飞上海飞机设计研究院,上海200232)摘要:使用自动铺带工艺制得胶接的碳纤维复合材料层压板试验件,通过轴向拉伸测试,测得了整个试验件的载荷-位移曲线和检测点附近的应变-载荷曲线。
试验结果表明,在拉伸载荷作用下试件发生层间剪切破坏,由于胶层的剪切强度高于层合板的层间剪切强度,破坏并没有发生在胶接面内,而是发生在胶层以外的层合板的层间。
建立了相应的有限元模型,模拟结果和试验结果的一致说明了有限元模型的合理性。
关键词:胶接;应变;破坏模式;有限元分析中图分类号:TB332文献标识码:A文章编号:1003-0999(2012)04-0036-05收稿日期:2012-04-22作者简介:张明星(1982-),男,博士,主要从事纤维增强复合材料研究。
1引言胶接连接因其工艺简单、成本低廉、具有能保持纤维连续性的特点而在飞机复合材料结构中被广泛应用[1 3]。
而胶接连接复合材料的历史文献大多集中在假设胶层发生剪切变形情况下的搭接区两端的应力分布[4 17]。
本文以刚度平衡的胶接连接碳纤维复合材料试验件为研究对象,对其进行了轴向拉伸测试,得出了搭接件上两端和中间区域的应力分布。
在考虑搭接件轴向变形情况下,建立了复合材料层压板胶接连接的有限元模型,并比较了有限元模拟结果和试验结果,模拟结果和试验结果的一致说明了有限元模型的合理性。
2试验#."材料本试验采用的材料为碳纤维单向带,其材料常数如表1所示。
表1碳纤维单向带材料常数Table 1Material performance of carbon tapeE 11/GPa E 22/GPa E 33/GPa υ12υ13υ23G 12/GPa G 13/GPa G 23/GPa 1758.378.370.340.340.344.494.493.5#.#试验件设计与制备试验件搭接区长度为200mm ,宽度为80mm ,厚度为3.8mm ;每端加厚区长度为195mm ,宽度为87.6mm ,端头厚度为11.4mm 。
复合材料层合板
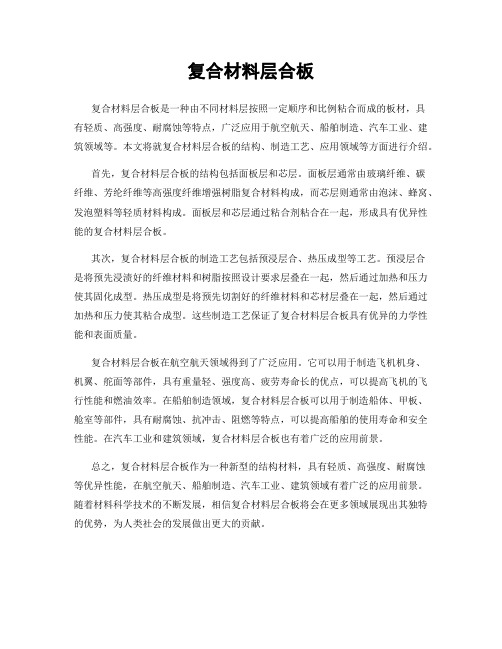
复合材料层合板
复合材料层合板是一种由不同材料层按照一定顺序和比例粘合而成的板材,具
有轻质、高强度、耐腐蚀等特点,广泛应用于航空航天、船舶制造、汽车工业、建筑领域等。
本文将就复合材料层合板的结构、制造工艺、应用领域等方面进行介绍。
首先,复合材料层合板的结构包括面板层和芯层。
面板层通常由玻璃纤维、碳
纤维、芳纶纤维等高强度纤维增强树脂复合材料构成,而芯层则通常由泡沫、蜂窝、发泡塑料等轻质材料构成。
面板层和芯层通过粘合剂粘合在一起,形成具有优异性能的复合材料层合板。
其次,复合材料层合板的制造工艺包括预浸层合、热压成型等工艺。
预浸层合
是将预先浸渍好的纤维材料和树脂按照设计要求层叠在一起,然后通过加热和压力使其固化成型。
热压成型是将预先切割好的纤维材料和芯材层叠在一起,然后通过加热和压力使其粘合成型。
这些制造工艺保证了复合材料层合板具有优异的力学性能和表面质量。
复合材料层合板在航空航天领域得到了广泛应用。
它可以用于制造飞机机身、
机翼、舵面等部件,具有重量轻、强度高、疲劳寿命长的优点,可以提高飞机的飞行性能和燃油效率。
在船舶制造领域,复合材料层合板可以用于制造船体、甲板、舱室等部件,具有耐腐蚀、抗冲击、阻燃等特点,可以提高船舶的使用寿命和安全性能。
在汽车工业和建筑领域,复合材料层合板也有着广泛的应用前景。
总之,复合材料层合板作为一种新型的结构材料,具有轻质、高强度、耐腐蚀
等优异性能,在航空航天、船舶制造、汽车工业、建筑领域有着广泛的应用前景。
随着材料科学技术的不断发展,相信复合材料层合板将会在更多领域展现出其独特的优势,为人类社会的发展做出更大的贡献。
复合材料力学-第四章层合板的宏观力学行为
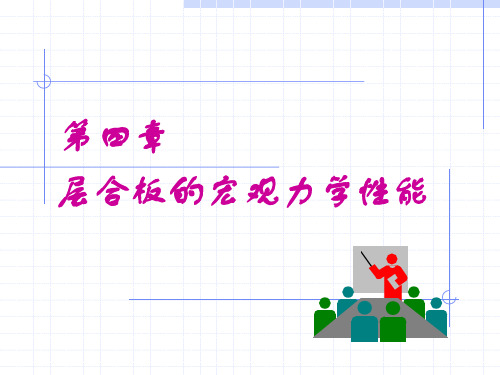
Q 12 t 3 12
D 22
Q 22 t 3 12
D 16 D 26 0
A 66 Q 66 t
D 66
Q 66 t 3 12
合力仅仅与层合板中面内的应变有关,合力矩仅与中面的曲率有关
Nx Ny
A A1121
A12 A22
0 0
00yx
Nx
y
0
0
A660x
y
Mx My
D D11
1 2
引言
有不同物理性质和几何尺寸单层组成的层合板 具有最一般的各向异性性质 层合板不一定有确定的主方向 另一方面,这种层合板在厚度方向具有客观的 非均匀性和力学性质的不连续性 对层合板的力学分析就变得更为复杂 已知单层的性质,主要关注沿厚度方向的应力 和应变的变化
引言
单层板的应力-应变性能
1 2
Q Q1211
Bij 0
相当于特殊正交各向异性单层板
正规对称正交铺层层合板 厚度和材料性能相同 材料主方向与层和板轴交替成0和90角
对称层合板
Q11Q11co4s2(Q122Q66)sin2co2sQ22sin4 Q12(Q11Q224Q66)sin2co2sQ12(co4ssin4) Q22Q11sin42(Q122Q66)sin2co2sQ22co4s Q16(Q11Q122Q66)sinco3s(Q12Q222Q66)sin3cos Q26(Q11Q122Q66)sin3cos(Q12Q222Q66)sinco3s Q66(Q11Q222Q122Q66)sin2co2sQ66(co4ssin4)
经典层合理论
z,w
x,u
u0
y,v
A
B
A
zc C x
复合材料织物层合板层间剪切性能研究

同温 度 变化 周期 条件 下 , 分 别 使 用 热 压罐 和 热 补 仪进 行 层 合 板 固化 所 得 到 的 复 合 材 料 层 合 板 的层 间 剪 切 性 能 基 于 A S . r M D 5 3 7 9试 验 标 准 , 开 展 了相 关试 验 , 结 果表 明 : 采 用 热 压罐 进 行 固化 所得 到 的 层 合板 , 其 层 间剪 切 强 度及 刚度 都要 优 于 采 用热 补
1 77 。 C
、
图 3层 间剪切 性 能试 验 装 置
、
1
●
●
衢。
3
' l
2
/ \
d
/ \
图 4 应 变 片 位 置
1 3 数 据 处理 试验 可 以得 到 试件 的载 荷一 位 移 曲线 和 应 变一 时『 H 】 曲线 , 进 一 步 图 I 固 化 过 程 的 温 度 变 化 周 期 处理n J . 以得 到相 应 的 切应 力 一 切应 变 [ H I 线。 槲 下 列 公式 , r 1 『 】 得 到 将 化 完 成 后 的 J 介 饭按 2所示 进 仃 没计 『 J 『 I 得 到标 准 的 试f f : l f ; . I 极 限 剪切 强 度 干 ¨ } J J 卡 } l 量。 试验 什 。 试 验 件 的 姚格 为 7 6 x 2 0 x 2 , 每 种 类 准 备叫块 试件 加 强 片 ( 1 ) 剪 切 应 力与 鲍 切强 J 芟由 如 公式 汁算 : 分 圳 常 温 下 【 古 1 化2 4 h , 6 O c 【 : 卜田化 2 h , 8 2 : 下『 占 1 化l h 、 7_ 尸/ A ( I ) l 2 试验 过 3为层 『 H J } J J 试验装置 , 央 具 两 头 紧 紧 火住 试件 , j i : 试 什 S = P“ / A ( 2 ) v 缺I 1 截 上沿 裁 倚 向产 生 纯 剪 力 存 V, 缺 I I 连 线 上 放置 应 式 } 1 _ 变 片测 切 作 , 1 F, 试仆 v 截 面剪 心 变的 变 化 , 应 变 片 位 T . : 剪切 应 力 ; P . : 戟倚 ; A : v 缺r ] 横 截 { ; s “ : 极 限 剪 切强 度 ; 见『 幺 ] 4 P u : 最 大载 倚 。 试验 过 程 } 1 , 将 试验 什 火 持 到位 后 , 刘 f 、 变 片执 行平 衡 、 清 零 操 ( 2 ) 剪应 变 作, 载简和位移清岑 后 . 行始进仃试验 ; 按 l a r m / a r i n的 速 度 施 加 载 ( 3) 简. , f 至 发 破 坏 试验过 程 【 { J 采 集载 简 、 化移 、 应 变等 数 据 , 记 录试 2 =l s 。 l + l I + I l + J 验 什 的破 坏 模式
复合材料铺层表示方法

复合材料铺层表示方法一、材料类型表示复合材料铺层时,首先需要明确使用的材料类型。
不同的复合材料具有不同的性能,因此选择合适的材料是至关重要的。
常见的复合材料类型包括玻璃纤维、碳纤维、芳纶纤维等,它们可以单独使用或以不同的组合方式使用。
二、铺层厚度铺层厚度是复合材料层合板的重要参数,它决定了材料的承载能力和刚度。
铺层厚度可以用单层厚度或总厚度来表示。
在表示铺层厚度时,应注明各层材料的厚度,以便于理解和分析。
三、铺层方向铺层方向是指纤维在复合材料中的排列方向。
对于层合板,铺层方向决定了其主要性能的取向。
通常情况下,应选择与受力方向一致的铺层方向以提高材料的承载能力。
不同的铺层方向可以通过角度表示,如0°、90°、±45°等。
四、铺层比例铺层比例是指各层材料在层合板中所占的比例。
通过调整不同材料的铺层比例,可以获得所需的性能组合。
例如,通过增加某一方向的铺层数量可以提高该方向的承载能力。
五、铺层顺序铺层顺序是指层合板中各层的叠加顺序。
合理的铺层顺序可以有效地提高材料的性能,并降低缺陷的可能性。
通常,应遵循先铺设承载力较小的材料,再铺设承载力较大的材料的顺序。
六、连接方式复合材料的连接方式包括机械连接和胶接等。
机械连接是指通过螺钉、铆钉等将各层材料连接在一起,而胶接则是使用胶粘剂将各层材料粘合在一起。
不同的连接方式对材料的性能有一定的影响,应根据实际需求选择合适的连接方式。
七、表面处理对于某些复合材料,需要进行表面处理以提高其粘附力和耐腐蚀性。
常见的表面处理方法包括打磨、喷砂、涂装等。
在进行表面处理时,应选择合适的处理方式并注意保护纤维不受损伤。
八、其他特殊要求在复合材料的表示方法中,可能还需要考虑其他特殊要求,如热处理、防腐处理、防火处理等。
这些特殊要求应根据具体需求和相关标准进行确定和实施。
复合材料层合板结构的力学行为分析
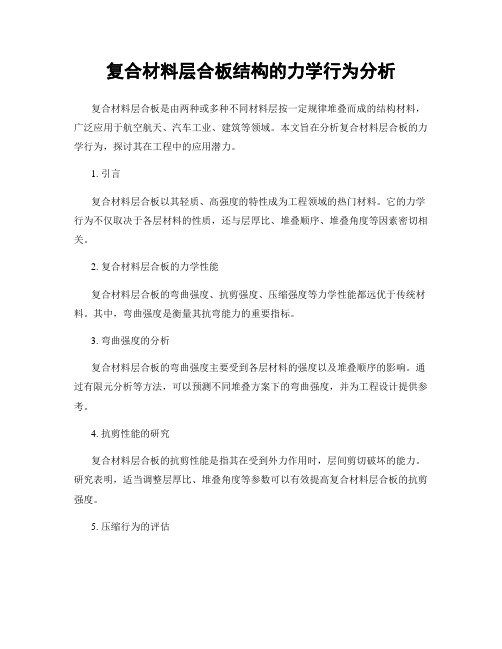
复合材料层合板结构的力学行为分析复合材料层合板是由两种或多种不同材料层按一定规律堆叠而成的结构材料,广泛应用于航空航天、汽车工业、建筑等领域。
本文旨在分析复合材料层合板的力学行为,探讨其在工程中的应用潜力。
1. 引言复合材料层合板以其轻质、高强度的特性成为工程领域的热门材料。
它的力学行为不仅取决于各层材料的性质,还与层厚比、堆叠顺序、堆叠角度等因素密切相关。
2. 复合材料层合板的力学性能复合材料层合板的弯曲强度、抗剪强度、压缩强度等力学性能都远优于传统材料。
其中,弯曲强度是衡量其抗弯能力的重要指标。
3. 弯曲强度的分析复合材料层合板的弯曲强度主要受到各层材料的强度以及堆叠顺序的影响。
通过有限元分析等方法,可以预测不同堆叠方案下的弯曲强度,并为工程设计提供参考。
4. 抗剪性能的研究复合材料层合板的抗剪性能是指其在受到外力作用时,层间剪切破坏的能力。
研究表明,适当调整层厚比、堆叠角度等参数可以有效提高复合材料层合板的抗剪强度。
5. 压缩行为的评估复合材料层合板的压缩行为直接影响其在承受压力时的稳定性。
通过实验和数值模拟,可以研究不同层厚比、纤维束填充方式等因素对压缩性能的影响,并为结构设计提供参考。
6. 破坏机理的分析了解复合材料层合板的破坏机理对于优化设计至关重要。
常见的破坏模式包括层间剥离、纤维断裂、层间剪切破坏等。
深入研究这些破坏机理可以为材料改进和结构设计提供指导。
7. 工程应用潜力复合材料层合板由于其优异的力学性能和轻质化特点,在航空航天、汽车工业、建筑等领域具有广泛的应用潜力。
例如,利用层合板设计轻量化飞机翼等结构,可以提高飞机的燃油效率。
8. 结论复合材料层合板是一种具有优良力学性能的结构材料。
通过深入研究其力学行为,可以为工程设计和材料改进提供指导。
未来,随着技术的不断发展,复合材料层合板的应用前景将更加广阔。
通过以上分析可见,复合材料层合板在工程领域具有重要价值。
对其力学行为的深入理解有助于优化设计,提高结构性能。
- 1、下载文档前请自行甄别文档内容的完整性,平台不提供额外的编辑、内容补充、找答案等附加服务。
- 2、"仅部分预览"的文档,不可在线预览部分如存在完整性等问题,可反馈申请退款(可完整预览的文档不适用该条件!)。
- 3、如文档侵犯您的权益,请联系客服反馈,我们会尽快为您处理(人工客服工作时间:9:00-18:30)。
· 2 ·玻璃钢 2006年第4期复合材料层合板的厚度方向性能 和层间性能 张 汝 光(上海玻璃钢研究院,上海 201404)摘 要 复合材料层合板厚度方向性能和层间性能有着完全不同物理的概念,不能混用,以免发生差错。
用三点弯曲外伸梁法,测定一般层合板厚度方向的剪切性能,理论上可行,但在实际测试中会产生较大误差,很难保证数据的准确性。
关键词:层合板; 厚度方向; 层间; 三点弯曲试验 1两个不同的物理概念复合材料层合板厚度方向的性能和层间性能有着完全不同的物理概念,应该加于区别,不能混用,以免发生差错。
虽然厚度方向在单向拉伸、压缩或剪切应力作用下,层间界面相受到同样的拉伸、压缩或剪切应力,但其应变完全不同(见图1、图2和图3),破坏强度也3σ 13τ3图2 层合板厚度-3方向的受力和表观变形 图3 层合板层间界面相的受力和变形· 3 ·层间性能顾名思义,是层合板两层之间界面相的性能,反映单纯界面相对外界作用的响应;而厚度方向的性能,则反映整个层板材料在3方向的表观性能,它包括各层及其界面相对外界作用的综合响应。
在复合材料层板的受力分析中,需要区分这两个不同的概念,以免发生差错。
如,在分析层合板厚度方向的应变时,需要用厚度方向的表观模量;在分析由于相邻层性能的不匹配造成的层间应力时(如:拉伸、压缩时,由于两相邻层泊松比不同或温度变化时,由于两相邻层热膨胀系数不同,而产生的层间剪切应力;或拉伸、压缩时,由于两相邻层模量的不同,而产生的层间正应力等等),需要用层间的界面相模量。
而厚度方向的模量往往要比层间界面相的模量大2至5倍。
又如在分析单向板的拉伸和压缩不同的损伤扩展、破坏模式和强度时,界面相的性能起非常重要的作用,而它完全不同于层合板厚度方向的性能,不能用后者来取代。
1.1 厚度方向和层间的弹性模量由上图可以清楚看出,受简单拉伸(或压缩)和剪切时,虽然复合材料层合板的层间应力和厚度方向的应力相等,其应变完全不同。
材料的弹性模量等于产生单位应变所需要的作用应力,应力相等,而应变不等,自然它们的弹性模量也不相等。
即int E (层间拉伸模量) ≠ 3E (厚度方向拉伸模量)int G (层间剪切模量) ≠ 13G (厚度方向剪切模量)1.2 厚度方向和层间的强度厚度方向的作用应力达到最大时,材料发生破坏,此时的应力是复合材料层合板厚度方向的强度。
其破坏可以是发生在界面相上,也可以是发生在某一层内。
只有当破坏发生在界面相时,厚度方向的强度才等于层间强度。
如,若层合板中含有泡沫层(如泡沫夹层板),破坏往往就发生在泡沫层内,厚度方向的强度等于泡沫材料的强度,而不是层间强度。
对大多数的层合板,破坏常常发生在层间,因此可认为是层间强度。
但这不是绝对的,所有还是分开为好,以避免发生差错。
2 层合板厚度方向性能和层间性能的测试由于通过对厚度方向施加单向力,就可实现对层间界面相施加同样的单向力,层间性能的测试往往就可以相同于对厚度方向的测试,只是在对数据分析处理时,要注意加于区别。
如:2.1 层合板厚度方向性能的测试厚度方向的弹性模量:333/εσ∆∆=E131313/γτ∆∆=G厚度方向的强度:· 4 ·max 3)(σ=Zmax 1313)(τ=S式中,Z 、13S 分别为厚度方向的拉伸(或压缩)强度和剪切强度。
2.2 层合板层间性能的测试层间的弹性模量:一般不能通过层合板的测试取得(很难测量界面相的变形量)。
实际上,层间界面相可以认为是匀质基体,其弹性模量就等于基体的弹性模量,因此可通过基体浇铸体的性能测试来取得。
层间强度:可采用对层合板厚度方向的受力测得,但只有当破坏发生在层间时,才有Z Z ==max 3int )(σ13max 13int )(S S ==τ式中,int Z 、int S 分别为层间界面相的拉伸(或压缩)强度和层间剪切强度。
3 采用三点弯曲外伸法测试厚度方向的剪切模量理论上,我们可以采用三点弯曲外伸法,测定复合材料层合板的厚度方向剪切模量。
但实际应用中,往往因为误差较大而不可行,因此要特别注意。
3.1 三点弯曲外伸法测定厚度方向剪切模量的原理通过三点弯曲试验可测出中点的挠度δ,它包含了纯弯曲挠度和纯剪切挠度,即 j w δ+= (1) 式中w δ、j δ分别为纯弯曲挠度和纯剪切挠度。
从测出的外伸挠度1δ可求出弯曲刚度1216δa Pl D = (2) 式中P 、l 、α分别为荷载、跨距和外伸挠度测点到最近支点的距离。
由弯曲刚度D ,可以求出中点的纯弯曲挠度w δDPl w 483=δ (3) 由(1)、(2)和(3)方程联立,消去D 和w δ,可以推导出中点的纯剪切挠度j δa l j 31δδ−= (4)δδδ· 5 ·中点纯剪切挠度与剪切刚度之间的关系式为6642A PL L j =×=γδ (5) 由(4)和(5)方程联立,消去j δ,可推得由δ、1δ计算剪切刚度公式)3(4166al PL A δδ−= (6) 厚度方向的剪切模量可由剪切刚度66A 求出。
假设剪切应力沿厚度方向分布均匀,有bh A G /6613= (7)式中,b 和h 分别为层板试件的宽度和厚度。
若考虑到剪切应力的不均匀分布,有bh A G /2.16613=,将方程(6)的66A 代入式中,得 bh al PL G )3(42.1113δδ−= (8) 式中的1.2是理论推导得出的系数。
所以理论上用三点弯曲外伸法测试厚度方向的剪切模量上可行的。
3.2 三点弯曲外伸法求厚度方向剪切模量的精度分析我们在采用三点弯曲试验直接测试层板弯曲模量时,实际上是将中点挠度完全当作纯弯曲挠度处理,这正是由于剪切挠度所占的比例非常小,完全可以忽略不计的缘故,求出的弯曲模量仍然是可靠的。
现在要通过中点挠度和纯弯曲挠度(它们相差很小)相减,来求纯剪切挠度(一个可以被忽略的小数),将是毫无意义。
当然,可以扩大剪切挠度所占的比例,问题是能做到什么程度。
下面分析在三点弯曲试验中,纯剪切挠度在总挠度中所占比例:Ebh PL w 334=δ ; Gbh PL j 103=δ j δ:w δ = 26Eh :25GL = G E 56(L h )2 对(1:1)手糊玻璃钢(A = 45%)*:E = 18 GPa, G = 3.6 GPa, 取跨厚比为32时,j δ :w δ =0.59 % (剪切挠度占总挠度的0.59 %);取跨厚比为16时,j δ :w δ = 2.34 %(剪切挠度占总挠度的2.29 %); 取跨厚比为8时,j δ :w δ = 9.38 % (剪切挠度占总挠度的8.58 %)。
对(7:1)模压玻璃钢(A = 22%)*:E = 45 GPa, G =6 GPa, 取跨厚比为32时,j δ :w δ = 0.88 % (剪切挠度占总挠度的0.87 %) ;取跨厚比为16时,j δ :w δ = 3.52 % (剪切挠度占总挠度的3.40 %);· 6 ·取跨厚比为8时,j δ :w δ = 14.1 % (剪切挠度占总挠度的12.4 %)。
(注* : 性能数据取自上海玻璃钢研究所编著《玻璃钢结构设计》;认为G G ≈13。
)以厚度为5mm ,跨厚比为8,层间剪切强度假设为max τ= 60Mpa 计算,(1:1)手糊玻璃钢剪切破坏时的最大剪切挠度为 max ,j δ= 0.20mm (max ,w δ= 2.13mm );(7:1)模压玻璃钢剪切破坏时的最大剪切挠度为 max ,j δ= 0.12 mm (max ,w δ= 0.853 mm )。
以上数据提出了两个问题:① 即使跨厚比为8(已经很小),剪切挠度也仅占总挠度的8.58%-12.4 %,由中点总挠度减去纯弯曲挠度(大数相减)求纯剪切挠度(求得小数),将会产生较大误差;② 厚度为5mm ,跨厚比为8时,破坏时的最大剪切挠度max ,j δ 才0.12-0.20 mm, 测试计算时采用的P ∆若为0.25max P ∆(由于剪切性能的非线性,这已经不小),对应的j δ∆就只有0.03-0.05mm ,系统误差的影响将是很大的。
如何解决上述两个问题:要提高剪切挠度在中点挠度中所占的比例,就需要减小跨距(实际层板厚度往往有一定的范围);而要加大j δ∆的取值,又需要加大跨距。
所以,唯一的办法是要加大跨距(以加大j δ∆的取值),而同时又要以更大比例增加层板的厚度(以提高j δ所占的比例),这样才能做到既提高剪切挠度的比例,又增大j δ∆的取值。
如,对(1:1)手糊玻璃钢,跨厚比要近于4.5,剪切挠度的比例才近于总挠度的30 %,这样在j δ∆取值仍然不变(约为0.05mm )条件下,厚度就需要9 mm 。
若同时又要增大j δ∆取值,厚度还有按同样比例增大,这显然是很困难的。
因此,对于一般复合材料层合板,实际上很难用三点弯曲外伸法可靠地测定复合材料层板厚度方向的剪切模量。
4 结 论4.1 复合材料层合板厚度方向性能和层间性能是两个不同的物理概念,不能混用;4.2 用三点弯曲外伸梁法,测定一般层合板的剪切性能,理论上可行,但在实际测试中会产生较大误差,很难保证数据的准确性。
INTERLAMINAR PROPERTIES AND PROPERTIES IN THICKNESS-DIRECTION OFCOMPOSITE LAMINATEZHANG Ru-guang(Shanghai FRP Research Institute, Shanghai 201404, China)AbstractInterlaminar properties and properties in thickness-direction of composite laminate are totally different in concept. So, in order to avoid confusion they can’t be used equally. Three-point flexure test with out-stretch span can theoretically measure the shear modulus in thickness-direction of a laminate, but in practice it is difficult to do accurately.Key words:laminate; thickness-direction; interlaminar; three-point flexure test。