含孔复合材料层合板拉伸强度研究_李明
复合材料拉伸强度实验报告

复合材料拉伸强度实验报告引言在现代工程应用中,复合材料广泛应用于各种领域,如航空航天、汽车制造和建筑材料等。
复合材料具有轻质、高强度和优异的特性,成为替代传统材料的理想选择。
复合材料的性能评价是保证其可靠性和安全性的重要方面之一。
其中拉伸强度是评价复合材料性能的关键参数之一,本实验旨在通过拉伸实验来研究复合材料的拉伸强度。
实验目的本实验的目的是通过拉伸实验测量复合材料的拉伸强度,并分析影响拉伸强度的因素。
实验原理1.拉伸强度:复合材料的拉伸强度是指材料在拉伸载荷作用下抵抗破坏的能力。
拉伸强度越高,材料的抗拉性能越好。
拉伸强度可以通过测量材料在拉伸实验中的抗拉应力和断裂断口面积来计算。
2.实验装置:本实验使用万能试验机进行拉伸实验。
该试验机能够施加垂直于试样轴向的拉伸载荷,并测量试样的应变和应力。
3.试样制备:在本实验中,采用常见的矩形试样制备方法制备复合材料试样。
4.实验步骤:–制备复合材料试样;–安装试样到万能试验机;–施加拉伸载荷;–记录试样的应变和应力;–停止加载直到试样破裂;–计算拉伸强度。
实验过程1.试样制备:–准备复合材料板材;–使用切割工具切割板材为一定尺寸的矩形试样。
2.试样安装:–将试样固定在万能试验机的夹具上;–确保试样均匀受力,避免应力集中。
3.施加拉伸载荷:–控制万能试验机施加的拉伸速度;–开始施加拉伸载荷,记录载荷和试样的应变。
4.记录数据:–在拉伸过程中,定期记录应变和应力;–在试样破裂之前停止加载。
5.数据处理:–根据记录的应变和应力数据计算平均拉伸强度;–将强度数据进行分析和比较。
实验结果和讨论1.实验数据:–在实验中记录了多组试验数据;–每组数据包括载荷和应变。
2.结果分析:–对每组数据计算平均拉伸强度;–比较不同组数据的拉伸强度。
3.影响因素:–分析试样尺寸对拉伸强度的影响;–讨论复合材料成分和制备工艺对拉伸强度的影响。
4.结果讨论:–分析实验结果,探讨拉伸强度与试样尺寸、复合材料成分和制备工艺之间的关系;–讨论实验结果与理论模型之间的一致性。
T700复合材料层合板拉-拉疲劳性能

表 1 试 验 件 尺 寸 表
T b e 1 g o ty o p cme s a l e me r fs e i n
能 方 面的研 究 , 目前仍 然还 较 为缺 乏 。 本 研 究 对 T0/ 3 8复 合 材 料 试 件 进 行 了 拉一 70 96
拉 疲劳 试验 , 对试 件 刚度 衰 减 和 疲 劳损 伤 扩 展 进 行 1 2 试 件 设备 与 方案 .
第3 2卷 第 3期
21 0 2年 6月
航
空
材
料
学
报
V0. 2. No 13 .3
J OUR NAL OF AE RONAU CAL MA ER AL TI T I S
J n 2 1 ue 02
T0 7 0复 合 材 料 层 合 板 拉 . 疲 劳 性 能 拉
王 军 , 程 小 全 , 张 纪 奎 , 郦 正 能
了层合板疲 劳累积损 伤模 型 , 并从平均应力准 则概 念 出发 , 立 了含孔层 合板 的疲劳 累积损伤模 型 。将试 验数 据 建 运用最d -乘法拟合后代 入疲 劳损伤模型 , x 得到 T 0/ 3 8光滑板 及含孔 板疲 劳寿命 的具体计 算公式 , 7096 应用 公式 预测 了在不 同应力水平下 的层 合板疲劳寿命 , 与试 验结 果的吻合 良好 。 关键词 : 70 复合材料层合 板 , T0 , 拉伸疲劳寿命
材料 拉一 拉疲 劳 试 验 方 法 ¨ 标 准 。试 验 环 境 条 件 ) 为 自然 干 态 ( 常态 ) 环境 温度 为 ( 3± ) 。 , 2 3℃ 对 三 组 试 件分 别 先 进 行静 载 拉 伸试 验 , 到每 得
作者简介 : 王军 ( 主要从 事 复合 材
复合材料层合板的力学行为与优化设计

复合材料层合板的力学行为与优化设计复合材料层合板是由两个或多个不同材料的层按照一定方式堆叠而成的结构材料。
它具有优异的力学性能和设计灵活性,在航空航天、汽车制造、建筑工程等领域得到广泛应用。
本文将从力学行为和优化设计两个方面对复合材料层合板进行探讨。
首先,复合材料层合板的力学行为是理解和研究该材料的基础。
复合材料层合板的力学性能受到多种因素的影响,包括材料的性质、层间粘结强度、层间厚度比、层间角度等。
其中,材料的性质是决定层合板力学性能的关键因素。
复合材料层合板通常由纤维增强复合材料和基体材料组成。
纤维增强复合材料具有高强度、高刚度和低密度的特点,而基体材料则具有良好的韧性和耐磨性。
通过选择不同的纤维和基体材料,可以实现对层合板力学性能的调控。
其次,复合材料层合板的优化设计是提高材料性能和降低成本的重要手段。
优化设计的目标是找到最佳的材料组合、层间厚度比和层间角度,以满足特定的工程要求。
优化设计可以通过数值模拟和实验测试相结合的方式进行。
数值模拟可以通过有限元分析等方法,预测不同设计参数对层合板力学性能的影响。
实验测试可以通过拉伸、弯曲、剪切等试验,验证数值模拟结果的准确性。
在优化设计过程中,需要考虑的因素包括强度、刚度、韧性、疲劳寿命和成本等。
强度是指材料抵抗外力破坏的能力,刚度是指材料对应力的响应程度,韧性是指材料在受到外力作用下的变形能力,疲劳寿命是指材料在循环加载下的使用寿命。
通过优化设计,可以在满足这些要求的前提下,尽量降低材料的成本。
在实际应用中,复合材料层合板的优化设计需要综合考虑多个因素。
例如,层间厚度比的选择既要考虑强度和刚度的要求,又要考虑材料的成本和制造工艺的可行性。
层间角度的选择既要考虑层间剪切强度的要求,又要考虑层间粘结强度和制造工艺的限制。
因此,在优化设计中需要综合考虑材料的性能、制造工艺和经济性等多个方面的因素。
总之,复合材料层合板的力学行为与优化设计是研究和应用该材料的重要内容。
薄层合板单面贴补修理拉伸性能研究

1 0.385 0.3
t0n / MPa
24
t
0 s
=
t0t
/ MPa
30
G0n / N·mm-1
0.3
G0s = G0t / N·mm-1
0.9
表 2 ZT7H / QY9611 预浸料材料参数 Table 2 Material property of ZT7H / QY9611 prepreg
FRP / CM 2019. No. 2
84
薄层合板单面贴补修理拉伸性能研究
2019 年 2 月
90 /0]s。补片的厚度和铺层顺序与母板相同。首先 在修理件中心处打直径为 50 mm 的穿透孔来模拟 穿透损伤,然后通过胶黏剂与补片粘接,补片直径分 为 4 种,分别为 60 mm、70 mm、80 mm 和 90 mm,胶 黏剂选用 J299 胶膜。胶黏剂和复合材料的力学性 能参数[13]如表 1 和表 2 所示,具体试验矩阵如表 3 所示。
2试验 2. 1 试验对象
无损试验件及修理件的母板采用复合材料单向 带 ZT7H / QY9611 型预浸料,单层厚度为 0. 125 mm, 板厚为 2 mm,铺层顺序为[45 /90 / - 45 /0 /45 / - 45 /
收稿日期: 2018-05-18 作者简介: 范鎔韬 ( 1995-) ,男,硕士,主要从事复合材料结构设计方面的研究。 通讯作者: 关志东 ( 1964-) ,男,博士后,教授,主要从事飞行器结构设计、飞机结构维修等方面的研究,d5062010@163. com。
2019 年第 2 期
T300AG80复合材料层合板力学性能的测试与分析的开题报告
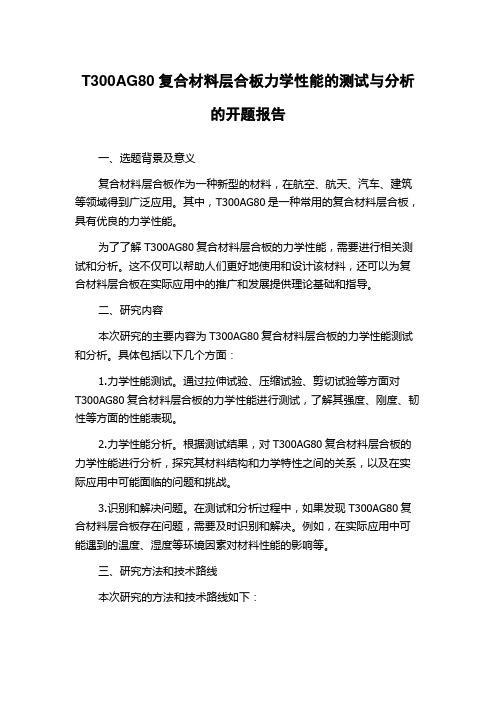
T300AG80复合材料层合板力学性能的测试与分析的开题报告一、选题背景及意义复合材料层合板作为一种新型的材料,在航空、航天、汽车、建筑等领域得到广泛应用。
其中,T300AG80是一种常用的复合材料层合板,具有优良的力学性能。
为了了解T300AG80复合材料层合板的力学性能,需要进行相关测试和分析。
这不仅可以帮助人们更好地使用和设计该材料,还可以为复合材料层合板在实际应用中的推广和发展提供理论基础和指导。
二、研究内容本次研究的主要内容为T300AG80复合材料层合板的力学性能测试和分析。
具体包括以下几个方面:1.力学性能测试。
通过拉伸试验、压缩试验、剪切试验等方面对T300AG80复合材料层合板的力学性能进行测试,了解其强度、刚度、韧性等方面的性能表现。
2.力学性能分析。
根据测试结果,对T300AG80复合材料层合板的力学性能进行分析,探究其材料结构和力学特性之间的关系,以及在实际应用中可能面临的问题和挑战。
3.识别和解决问题。
在测试和分析过程中,如果发现T300AG80复合材料层合板存在问题,需要及时识别和解决。
例如,在实际应用中可能遇到的温度、湿度等环境因素对材料性能的影响等。
三、研究方法和技术路线本次研究的方法和技术路线如下:1.材料准备。
首先需要准备T300AG80复合材料层合板的试片,按照中国国家标准GB/T 1447-2005《复合材料力学性能试验方法》的要求进行制备。
2.力学性能测试。
采用测试设备对T300AG80复合材料层合板的拉伸强度、压缩强度、剪切强度等力学性能进行测试。
测试中需严格按照标准测试操作要求进行。
3.力学性能分析。
通过对测试数据和理论分析的比对,探究T300AG80复合材料层合板的力学特性和材料结构之间的关系。
4.识别和解决问题。
如果在测试和分析过程中发现T300AG80复合材料层合板存在问题,需要采取相应的技术手段和措施解决。
四、预期研究结果通过本次研究,预计可以得出以下预期研究结果:1.分析T300AG80复合材料层合板的力学性能表现,包括其强度、刚度、韧性等方面。
含孔洞复合材料结构的拉伸性能仿真

第1期纤维复合材料㊀No.1㊀1002024年3月FIBER ㊀COMPOSITES ㊀Mar.2024含孔洞复合材料结构的拉伸性能仿真陈英函,刘甲秋,于柏峰,刘㊀佳,郝晨伟(哈尔滨玻璃钢研究院有限公司,哈尔滨150028)摘㊀要㊀本文针对含中心孔洞和含多孔复合材料结构模型,利用Fibersim 进行铺层设计并检验铺层角度是否偏差,对于含中心孔洞复合材料结构采用分区域铺覆的设计方法进行探究,发现可以达到在制造中节省材料成本的作用㊂将两种结构进行仿真失效计算同时与不开孔状态的复合材料结构进行比较,得出失效比值㊂关键词㊀Fibersim;有限元仿真;复合材料;铺层设计Simulation of Tensile Properties of CompositeStructures Containing HolesCHEN Yinghan,LIU Jiaqiu,YU Baifeng,LIU Jia,HAO Chenwei(Harbin FRP Institute Co.,Ltd.,Harbin 150028)ABSTRACT ㊀In this paper,we use Fibersim to design the lay -up for center hole and porous composite structure model,check whether the layup angle is deviated or not,and explore the design method of lay -up by area for center pore compos-ite structures,and find that it can achieve the role of saving the material cost in manufacturing.The two structures were sub-jected to simulated failure calculations while comparing them with the composite structure in the unopened state to derive the failure ratio.KEYWORDS ㊀fibersim;finite element simulation;composite material;lay -up design通讯作者:陈英函,硕士,助理工程师㊂研究方向为复合材料结构设计与仿真㊂E -mail:1374057740@1㊀引言航空航天领域中许多构件由碳纤维复合材料制成[1],其中由碳纤维复合材料制成的开孔板在复杂的服役环境下会引起应力集中进而产生损伤,这类损伤会导致构件的服役寿命减退和降低承载能力[2-3]㊂因此,研究人员对含孔复合材料构件进行了进一步的研究[4]㊂碳纤维复合材料开孔对力学性能影响较大[5-6],因此对于复合材料开孔性能的研究极为重要,Khashaba [7]等通过实验研究发现随着碳纤维复合材料开孔尺寸的增加,复合材料的抗压强度和刚度都会减小㊂卿光辉[8]等基于增强应变理论建立了非协调广义混合模型计算含孔复合材料层合板的应力集中系数,所得模型计算结果好,精度高并具有适用性㊂王振兴[9]等基于复合材料S -N 曲线分析对比了在开孔情况和不开孔情况下的浆叶疲劳寿命,发现开孔情况会产生更大的应力集中,从而影响桨叶的疲劳寿命㊂Fibersim 是一款处理复合材料铺层复杂性问题的专业软件[10],能够模拟复合材料铺层真实角度㊀1期含孔洞复合材料结构的拉伸性能仿真偏差进行改进,本文利用Fibersim 对含中心孔复合材料结构以及含多孔复合材料结构进行铺层的设计及铺层角度的查看校验,分析了两种结构失效的最大载荷并与不开孔状态下的复合材料结构进行比较,得出失效比值㊂2㊀含孔洞复合材料结构基于Fibersim 与仿真软件可以进行数据交互的特点,选取典型的含中心孔以及多孔复合材料结构进行算例的仿真分析,材料属性选取如表1所示㊂表1㊀材料属性纵向弹性模量E 1/MPa 横向弹性模量E 2/MPa 泊松比v 剪切模量G 12/MPa 剪切模量G 23/MPa 密度ρ/g㊃cm 320900094500.27550039001.54㊀㊀失效准则选用Tssi -Wu 应力准则,根据该准则,材料不发生破坏的条件如公式(1)所示㊂F =F 1σ1+F 2σ2+F 11σ21+F 22σ22+F 66τ212+2F 12σ1σ2<1(1)其中,各种强度指标按照以下各式确定,如公式(2)所示㊂F 1=1X t -1X cF 2=1Y t -1Y cF 11=1X t X cF 22=1Y t Y c F 66=1S 2F 12=F ∗12X t X c Y t Y cìîíïïïïïïïïïïïïïïïï(2)其中,F ∗12的值在-1到1之间,一般选取-1/2㊂2.1㊀含中心孔复合材料结构针对含中心孔复合材料结构示意如图1所示,模型尺寸为300mm ˑ300mm,中心含有直径为150mm 的孔洞㊂采用Fibersim 对铺贴面,边界进行提取,并利用点位定义铺层原点和零度方向,其信息如图2所示㊂㊀㊀基于该构型进行复合材料铺层的设计,铺层角度设置为(0/45/-45/90)5s ,复合材料单层厚度为0.05mm,总共铺层数为40层,整体厚度2mm㊂对于每一层的铺层设计,采用纤维影响因子的值为0.3,通过对铺层角度仿真模拟真实铺贴时角度是否偏差,如图3(a)~3(d)所示分别显示为在0ʎ,45ʎ,-45ʎ,90ʎ铺层角度下的角度信息,信息显示图1㊀含中心孔复合材料结构示意图图2㊀含中心孔复合材料结构0ʎ坐标方向图3㊀各角度铺层仿真信息该模型的实际铺层角度与理论铺层角度无偏差㊂101纤维复合材料2024年㊀由于在生产制造中,按图3所示进行预浸料准备时会先利用下料机切出整体模型再去除中心圆形孔洞,这样造成不必要的浪费,基于此对于各个角度进行铺层设计的优化,给出如图4所示建立基于区域划分的铺层设置㊂㊀㊀查看基于分区铺覆下的铺层角度是否有偏差,优化后的各铺层角度信息如图5所示,各个铺层角度均无偏差㊂图4㊀各角度铺层分区信息图图5㊀优化后的各铺层角度信息㊀㊀对图1所示的含中心孔洞复合材料结构,按图5所示节省用料10%以上,并且随着中心开孔直径的增加,节省用料比率越高㊂同时针对此开孔结构利用表1属性进行有限元仿真,网格划分如图6所示㊂对模型采用下端固定约束,在上表面加载拉力作用,查看失效结果,发现当加载力的大小为22437N 时模型出现首层失效,失效时观察不同角度失效系数结果如图7所示,并且发现失效发生在90ʎ铺层的孔洞附近位置㊂图6㊀网格划分示意图图7㊀含中心孔复合材料结构失效结果图㊀㊀将开孔模型与未开孔的模型做失效结果对比,对比结果如表2所示,含中心孔复合材料结构的首201㊀1期含孔洞复合材料结构的拉伸性能仿真层失效载荷是未开孔结构的0.347㊂表2㊀比对结果模型失效载荷失效比值含中心孔复合材料结构22437N 0.347未开孔结构64525N1㊀㊀2.2㊀含多孔复合材料结构针对含多孔复合材料结构示意如图8所示,模型尺寸为200mm ˑ600mm,含有三个直径为100mm 的孔洞,孔间距为200mm㊂图8㊀含多孔复合材料示意图基于该构型按照如含中心复合材料结构铺层进行设计,铺层的零度坐标如图9所示㊂图9㊀含多孔复合材料结构0ʎ坐标方向㊀㊀基于该构型进行复合材料铺层的设计,铺层角度设置为(0/45/-45/90)5s ,复合材料单层厚度为0.05mm,总共铺层数为40层,整体厚度2mm㊂对于每一层的铺层设计,采用纤维影响因子的值为0.3,通过对铺层角度仿真模拟真实铺贴时角度是否偏差,如图10(a)~10(d)所示,分别显示为在0ʎ,45ʎ,-45ʎ,90ʎ铺层角度下的角度信息,信息显示该模型的实际铺层角度与理论铺层角度无偏差,同样可以采用如含中心孔洞复合材料结构相似的分区域铺层设计方法以达到在制造中节省材料的目的㊂图10㊀各角度铺层仿真信息㊀㊀对模型采用下端固定约束,在上表面加载拉力作用,查看失效结果,发现当加载力的大小为54221N 时模型出现首层失效,失效时观察不同角度失效系数结果如图11所示,并且发现失效发生在90ʎ铺层距边线较近的孔洞边缘位置㊂将含多孔复合材料模型与未开孔的模型做失效结果对比,对比结果如表3所示,含中心孔复合材料结构的首层失效载荷是未开孔结构的0.403㊂301纤维复合材料2024年㊀图11㊀含多孔复合材料结构失效结果图表3㊀比对结果模型失效载荷失效比值含多孔复合材料结构54221N0.403未开孔结构134576N13㊀结语(1)利用Fibersim针对含中心孔复合材料进行分区域的铺层设计,节省材料在10%以上㊂㊀㊀(2)将本文含中心孔洞复合材料和含多孔复合材料结构与未开孔结构进行对比,其失效比值分别为0.347和0.403㊂(3)本文采用首层失效进行结果的判断,只能作为单层失效的标准,不能反映结果的最终承载能力㊂参考文献[1]蔡菊生.先进复合材料在航空航天领域的应用[J].合成材料老化与应用,2018,47(6):94-97.[2]MOURE M M,HERRERO C J,GARCíA C S K,et al.Design tool to predict the open-hole failure strength of composite laminates sub-jected to inplane loads[J].Composite Structures,2020,238: 111970.[3]SAYAR H,AZADI M,GHASEMI A,et al.Clustering effect on damage mechanisms in open-hole laminated carbon/epoxy compos-ite under constant tensile loading rate,using acoustic emission[J]. Composite Structures,2018,204:1-11.[4]郭峰,王哲峰,王共冬,等.低温条件下含孔碳纤维复合材料层合板拉伸损伤特性研究[J].复合材料科学与工程,2022(04):56-61.[5]姚辽军,赵美英,周银华.不同孔径复合材料层合板应变集中及失效强度分析[J].机械科学与技术,2011,30(5):761-764.[6]韩小平,郭章新,朱西平,等.含孔复合材料层合板孔边的应力集中[J].复合材料学报,2009,26(1):168-173. [7]KHASHABA U A,KHDAIR A I.Open hole compressive elastic and strength analysis of CFRE composites for aerospace applications [J].Aerospace Science and Technology,2017,60:96-107.[8]卿光辉,王绍波.含孔复合材料层合板的应力集中分析[J].中国民航大学学报,2019,37(05):55-59.[9]汪振兴,陶宪斌,杨建灵,等.直升机复合材料开孔对桨叶疲劳寿命的影响[J].中国科技信息,2020(20):23-25. [10]洪清泉,吕长,王招.Fibersim复合材料设计与工艺技术应用[M].清华大学出版社,2019,1(4):39-42.401。
复合材料拉伸强度实验报告
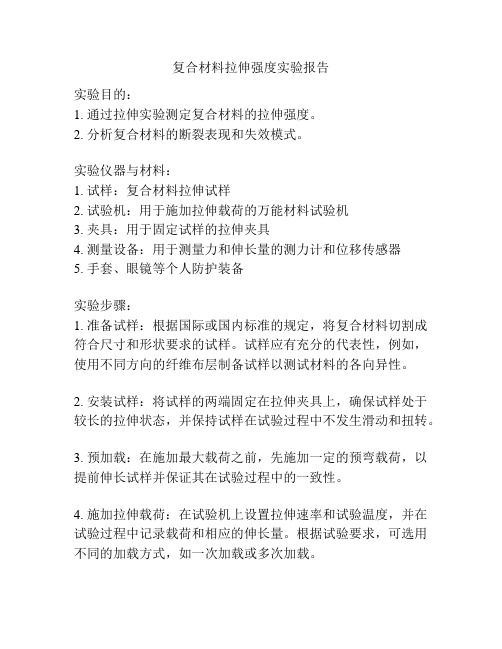
复合材料拉伸强度实验报告实验目的:1. 通过拉伸实验测定复合材料的拉伸强度。
2. 分析复合材料的断裂表现和失效模式。
实验仪器与材料:1. 试样:复合材料拉伸试样2. 试验机:用于施加拉伸载荷的万能材料试验机3. 夹具:用于固定试样的拉伸夹具4. 测量设备:用于测量力和伸长量的测力计和位移传感器5. 手套、眼镜等个人防护装备实验步骤:1. 准备试样:根据国际或国内标准的规定,将复合材料切割成符合尺寸和形状要求的试样。
试样应有充分的代表性,例如,使用不同方向的纤维布层制备试样以测试材料的各向异性。
2. 安装试样:将试样的两端固定在拉伸夹具上,确保试样处于较长的拉伸状态,并保持试样在试验过程中不发生滑动和扭转。
3. 预加载:在施加最大载荷之前,先施加一定的预弯载荷,以提前伸长试样并保证其在试验过程中的一致性。
4. 施加拉伸载荷:在试验机上设置拉伸速率和试验温度,并在试验过程中记录载荷和相应的伸长量。
根据试验要求,可选用不同的加载方式,如一次加载或多次加载。
5. 记录试验数据:根据试验机的测量设备,实时记录载荷和伸长量的变化,并制成相应的应力-应变曲线。
6. 分析试验结果:根据实验数据,计算出复合材料的拉伸强度、弹性模量和断裂伸长率等力学性能指标。
分析试验过程中的失效模式和断裂表现,如断裂形态、断口特征等。
安全注意事项:1. 在进行实验前,了解试验材料的性质和使用要求,并遵守相关的安全操作规程。
2. 佩戴个人防护装备,如手套和眼镜,以防止试样断裂时的碎片对人身安全造成伤害。
3. 仔细检查试验设备和夹具的固定情况,确保试样在测试过程中稳定且无滑动。
4. 控制试验机的加载速率,避免过快加载导致试样失稳或突然破坏。
5. 实验结束后,及时清理实验现场,确保实验设备和试样的安全存放。
实验结果与讨论:根据实验数据和分析结果,得出复合材料的拉伸强度、弹性模量和断裂伸长率等力学性能指标。
实验中观察到的断裂表现和失效模式可提供对该复合材料性能的评价和分析依据。
复合材料层合板强度分析实例

25.51
(MPa)
0
显然,外层单层板1,3中 y =25.51MPa,基本接近 x =352.52MPa,远小
x 1,3 82.0697 5.9401
Nx (MPa), h
y 1,3 4.3223 0.4653
Nx (MPa) h
xy 1,3 0
代入校验公式,计算出
Nx 45.53(MPa) h 1,3
将其代入第二步(6)的结果中,得 为
2
x
y xy
1,3
2
352.52
0.1508%
NORTHWESTERN POLYTECHNICAL UNIVERSITY
第三步,第一次刚度降低后层合板性能的确定 当 Nx 36.17MPa时,外层1,3单层板未发生破坏,其单层板刚度举证保持不变
h
内层板2在该层板层内横向(层内x轴方向)破坏,但纵向仍然有刚度:
0
0
0
0
0
0
(2)由n层复合材料单层板构成的复合材料层合板自然坐标系内力、内力矩-应 变、曲率关系(见教材P167)可计算层合板拉伸刚度矩阵A
24.42 4.58 0
A
n
Qk (zk
zk
1)
h
4.58
48.78
0
(GPa)
k 1
0 0 8.62
0.0417 0.0039 0
A1
1 h
0.0039 0
Nx
203.49MPa
h 1,3
(2)内层2单层板,仿照上步中的方法,可得:
N x 36.17MPa h2
NORTHWESTERN POLYTECHNICAL UNIVERSITY
- 1、下载文档前请自行甄别文档内容的完整性,平台不提供额外的编辑、内容补充、找答案等附加服务。
- 2、"仅部分预览"的文档,不可在线预览部分如存在完整性等问题,可反馈申请退款(可完整预览的文档不适用该条件!)。
- 3、如文档侵犯您的权益,请联系客服反馈,我们会尽快为您处理(人工客服工作时间:9:00-18:30)。
(b)不同孔形状的试件 图 2 两种类型的试件
2 含孔复合材料层合板数值模拟
含孔复合材料层合板的强度在理论上预测 较为复杂,尤 其 是 当 孔 的 形 状 为 不 规 则 的 几 何 构型时就更为困难. 并且碳纤维增强复合材料 价格比较 昂 贵,如 果 通 过 实 验 手 段 确 定 不 同 直 径和不同形状的含孔层合板的强度需要花费大 量的人力、物 力 和 财 力. 因 此,采 用 数 值 手 段 来 预测层合板的强度不失为一种经济且快捷的方 法. 本文采用商业软件 ABAQUS - Standard 来预 测层合 板 的 强 度,通 过 其 子 程 序 USDFLD 建 立 了一个逐渐失效模型( Progressive Failure Model, PFM) 来模拟层合板的失效. 一个逐渐失效模型 一般包括 以 下 四 个 部 分: 应 力 计 算、失 效 准 则、 退化准则和单元消去.
Tensile strength of composite laminated plate containing a hole
LI Ming1,2 , WU Lin-zhi1 , MA Li1 , GUAN Zheng-xi2
( 1. Center for Composite Materials,Harbin Institute of Technology,Harbin 150001,China,lmrocket@ 163. com; 2. No. 201 Faculty,the Second Artillery Engineering College,Xi’an 710025,China)
孔的边缘,使得孔的边缘光滑无毛刺. ( 7) 在试件 的端部粘接上加强片. 1. 2 实验方案
在本文中,研究了两种因素对层合板强度的 影响,一是孔的直径,二是孔的形状. 因此本文设 计了两种类型的试件. 对于圆形孔试件,孔的直径 分别为 0mm ( 完好试件) 、5mm、10mm 和 15mm. 另外又设计了方形孔和菱形孔试件,其中方形孔 和菱形孔的边长皆为 5mm. 两种类型的试件如图 2 所示. 根据国标 GB / T 1447 - 2005,试件的尺寸 取为 250mm × 25mm × 1. 68mm. 为了保证实验的 可靠 性,每 种 尺 寸 的 试 件 各 取 5 个. 采 用 Instron5569 试验机,以 5mm / min 的速度施加载荷, 载荷和位移都用试验机自带的力传感器和位移传 感器测量.
G23 ( GPa) XT ( GPa) XC ( GPa) YT = ZT ( MPa) YC = ZC ( MPa) S12 = S13 ( MPa) S23 ( MPa)
注: T = 拉伸,C = 压缩.
数值 128 8. 7 0. 32 0. 3 4. 0 4. 0 2. 093 0. 87 50 198 104 86
复合材料层合结构的强度预测及失效分析是
基金项目: 国家“973”基金( 2006CB601206) ; 国家自然科学基金 ( 90816024,10872059) 资助项目.
设计复合材料结构时所必需解决的关键问题,是 安全、经济地应用复合材料的前提. 因此,它在复 合材料研究领域中很早受到重视并得到了较为广 泛的研究. 由于影响其强度的因素很多,失效形式 具有多样性,如纤维断裂、基体开裂、基体纤维剪 切破坏、分层等,使得强度预测变得比较复杂. 另 外,传统的设计、试验错误、再设计的方法将耗费 大量的时间和费用. 因此,运用有限元软件模拟复 合材料层合结构的失效过程并预测最终失效强度 具有重要的应用价值,而对于含孔复合材料层合 板的强度预测更是当前国际上复合材料领域的研 究热点. Chang 等[6]首先提出用于分析含孔单向 层合板在拉伸载荷作用下极限强度的逐渐损伤模 型,并对不同铺层顺序层合板的损伤扩展和破坏 情况 进 行 了 研 究. 程 小 全 等[7] 采 用 有 限 元 软 件
·2·
哈尔滨工业大学学报
第 43 卷
ANSYS 对含孔的平面编织层合板在压缩载荷下 进行了仿真,并对其强度进行了预测.
本文对工程中常用到的含孔复合材料层合板 的失效规律进行了研究,并分析了孔的直径和形 状对层合板强度的影响,可以为复合材料结构设 计提供一定的依据,具有重要的工程实际意义.
图 1 鹰狮 JAS ห้องสมุดไป่ตู้9 的典型翼梁
拉伸分层 ( σ33 > 0)
ed = ( σ33 / ZT) 2 + ( σ13 / S13) 2 + ( σ23 / S23) 2≥1
压缩分层 ( σ33 < 0)
ed = ( σ33 / ZC) 2 + ( σ13 / S13) 2 + ( σ23 / S23) 2≥1
注: em 为基体损伤指标,ef 为纤维损伤指标,es 为基 - 纤剪切损伤指标,ed 为分层指标.
第 43 卷 增刊 1 2011 年 3 月
哈尔滨工业大学学报 JOURNAL OF HARBIN INSTITUTE OF TECHNOLOGY
Vol. 43 Sup. 1 Mar. ,2011
含孔复合材料层合板拉伸强度研究
李 明1,2 , 马 力1 , 吴林志1 , 关正西2
( 1. 哈尔滨工业大学 复合材料与结构研究所,哈尔滨 150080,lmrocket@ 163. com; 2. 第二炮兵工程学院 201 教研室,陕西 西安 710025)
摘 要: 对含孔复合材料层合板的破坏模式和拉伸强度进行了研究,考查了孔的直径和形状对层合板强度 的影响. 通过实验研究,测量出含孔层合板的强度. 利用有限元软件 ABAQUS 的子程序 USDFLD 建立了逐渐 损伤失效模型,对层合板的强度进行了数值模拟. 研究结果表明,数值模拟得到的强度值和实验测量的强度 值吻合较好,文中建立的数值模型可以有效地预测含孔层合板的强度. 关键词: 复合材料; 含孔层合板; 拉伸强度; 数值模拟; 子程序 文章编号: 0367 - 6234( 2011) 增刊 1 - 0001 - 05
1. 1 试件制备 本文采用热压法制造复合材料层合板试件,
具体过程如下: ( 1) 用丙酮将两块光滑平整的钢 板 清 洗 干 净,然 后 在 其 表 面 均 匀 地 涂 上 脱 模 剂. ( 2) 将 T700 /3234 预浸料按照( 0 /90 /0) 4 的顺序 层叠于其中一块钢板之上. 在铺设过程中,用压辊 挤出叠层之间的气体. ( 3) 将另一块钢板覆盖于 铺设好的层合板之上,并将这两块钢板放在热压 机中. ( 4) 以 2℃ / min 的升温速度将层合板升温 至 125℃ ,并施加 0. 5MPa 的压力,保温一个小时. ( 5) 自然冷却至室温,取出层合板,切割成需要的 尺寸. ( 6) 使用金刚石尖的钻头钻出圆形孔,使用 铣床铣出方形孔和菱形孔. 并用细纹锉仔细打磨
Abstract: The failure modes and tensile strength of composite laminated plate containing a hole are studied in the present work,and the influences of hole’s diameter and shape on the tensile strength of laminated plate are investigated. The strengths of laminated plates with circle,square and diamond holes are measured experimentally. A progressive failure model ( PFM) is developed with finite element software ABAQUS through the subroutine USDFLD,the failure modes and tensile strength of laminated plates are simulated by this PFM. The results show that the simulated strengths agree well with the measured ones,and the PFM in the present work can effectively predict the tensile strength of laminated plates with holes. Key words: composite; laminated plate with a hole; tensile strength; numerical simulation; subroutine
增刊 1
李 明,等: 含孔复合材料层合板拉伸强度研究
·3·
2. 1 失效准则 对于不同的复合材料,有不同的失效准则. 而
三维 Hashin 准则能清楚地分辨出纤维增强复合 材料层合板不同的失效模式,因此被广泛应用于 层合板的破坏分析中. 本文也采用三维 Hashin 准 则来预测层合板的失效起始. 三维 Hashin 准则如 表 2 所示.
纤维增强复合材料结构由于具有比强度大、比 刚度高、抗腐蚀性能好以及良好的可设计性,近年 来在航空和航天领域被广泛地应用,已成为飞机和 航空发动机结构的重要材料之一[1 -4]. 纤维增强复 合材料的引入很大程度地提高了飞机的整体性,但 由于检查、拆装、维护的需要以及工艺限制,在纤维 增强复合材料结构件中,经常会存在一些孔. 如用 于螺栓连接的螺栓孔,用于检查的通孔,以及装配 孔,等等. 例如在鹰狮 JAS 39 的翼梁上就存在着很 多各种形状的孔[5],如图 1 所示. 而这些孔对复合 材料结构的强度将会产生一定的影响.
2. 2 刚度退化准则 材料性能退化模型可以分为两类: 突然退化
模型( Sudden Degradation Model) 和渐变退化模型 ( Gradual Degradation Model ) . 突 然 退 化 模 型 又 称 瞬间卸载模型( Instantaneous Unloading Model) . 该 模型中材料的性能瞬间退化为零. 由于突然退化 模型的二元特性,即一点的材料特性要么是完好 的,要么是完全退化的,使得该模型比较简单,容 易实现. 因此该类模型在逐渐失效分析被广泛采 用. 与突然退化模型不同,逐渐退化模式中材料的 刚度逐渐变化的. 即使没有失效发生,材料常数按