模内组装-复合注塑成型新前沿
IML的工艺说明
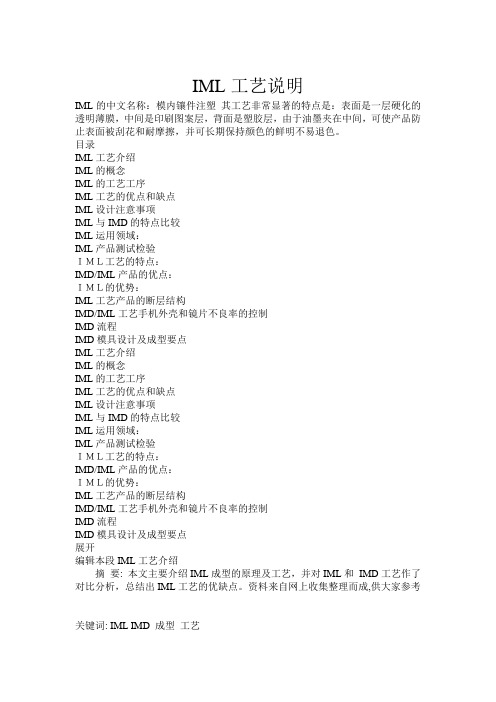
IML工艺说明IML的中文名称:模内镶件注塑其工艺非常显著的特点是:表面是一层硬化的透明薄膜,中间是印刷图案层,背面是塑胶层,由于油墨夹在中间,可使产品防止表面被刮花和耐摩擦,并可长期保持颜色的鲜明不易退色。
目录IML工艺介绍IML的概念IML的工艺工序IML工艺的优点和缺点IML设计注意事项IML与IMD的特点比较IML运用领域:IML产品测试检验IML工艺的特点:IMD/IML产品的优点:IML的优势:IML工艺产品的断层结构IMD/IML工艺手机外壳和镜片不良率的控制IMD流程IMD模具设计及成型要点IML工艺介绍IML的概念IML的工艺工序IML工艺的优点和缺点IML设计注意事项IML与IMD的特点比较IML运用领域:IML产品测试检验IML工艺的特点:IMD/IML产品的优点:IML的优势:IML工艺产品的断层结构IMD/IML工艺手机外壳和镜片不良率的控制IMD流程IMD模具设计及成型要点展开编辑本段IML工艺介绍摘要: 本文主要介绍IML成型的原理及工艺,并对IML和IMD工艺作了对比分析,总结出IML工艺的优缺点。
资料来自网上收集整理而成,供大家参考关键词: IML IMD 成型工艺编辑本段IML的概念IMD(In-Mold Decoration)是一种在注塑模具内放置Film薄膜来装饰塑胶外观表面的新技术。
目前IMD有两种制造方法,一种是把印刷好的Film薄膜制作成循环滚筒卷状带,安装到注塑机和注塑模具内,象标签Label贴到前模面上全自动地循环带移动式的生产出来;即人称之为IMD(在模具内转印注塑)。
另一种是把Film薄膜印刷好经过成型机Forming成型,再经过剪切后放置到注塑模具内生产出来的。
即称之为IML(在模具内贴膜注塑)。
此Film一般可分为三层:基材(一般是PET)、油墨层(INK)、胶合材料(多为一种特殊的粘合胶)。
当注塑完成后,通过粘合胶作用使Film和塑胶紧密结合融为一体,由于本身正表面覆耐磨保护膜的PET在最外层,有耐磨和耐刮伤的作用,其表面硬度可达到3H,而且会越摸越亮。
膜内注塑

膜内注塑本文由规成鑫提供(IMD)概况IMD模内注塑模内镶件注塑成型装饰技术即IMD(In-Mold Decoration),IMD是目前国际风行的表面装饰技术。
主要用于家电产品的装饰及功能控制面板、汽车仪表盘、空调面板、手机外壳/镜片、洗衣机、冰箱等应用非常广泛。
IMD定义IMD就是将已印刷成型好的装饰片材放入注塑模内,然后将树胶注射在成型片材的背面,使树脂与片材接合成一体固化成型的技术。
IMD是在注射成型的同时进行镶件加饰的技术,产品是和装饰承印材覆合成为一体,对立体状的成形品全体可进行加饰印刷,使产品达到装饰性与功能性于一身的效果IMD行情:1.世界4大油墨厂家进攻IMD产业,开发专业IMD油墨,并且不断在大陆展览.2.世界4大薄膜厂家进攻IMD产业,三菱以前2条流水线,现增加到4条.3.国际大企业进攻IMD产业,富士康以前一个部门现在增加2各部门生产.4.一些印刷行业巨头投入IMD全制程.产品的比较IMD与IML,IMR及传统产品的比较传统注塑产品:1,需要有喷漆或电镀等二次加工的过程(增加成本和造成污染)2,油墨等在产品的表面,时间一长的话就会被磨花或刮伤(降低产品的整体质量和外观效果)3,注塑成型后进行后续工作,造成良率下降等IMD模内装饰工艺产品:1,降低成本与时工要。
IMD制程中只需要开一套模具,不像其他老替代制程需开多套模具,降低系统成本与库存成本。
2,制程简化。
有一次注塑成型的工法,将成型与装饰同时达成,降低成本与工时,可稳定生产。
3,产品的稳定性和耐久性。
由于油墨是在片材和注塑料之间,立体成型增加了设计的自由度,图文、色彩在塑料夹层中,耐磨损及抗腐蚀,且色彩亮丽,印刷图案随时变更而无须更换模具。
4, 3D复杂形状设计和多样化风格。
图案,颜色,字体,LOGO是丝印或网印印刷载频面的片材上,成型为3D形状,可以依客户需求创造金属电镀或天然材质特殊式样。
一些效果是电镀喷漆所达不到的。
IMD注塑工艺

IMD注塑技术工艺IMD的中文名称:是指模内装饰镶嵌注塑技术注塑表面装饰技术,即IMD(In-Mold Decoration),IMD----模内装饰镶嵌注塑技术,是一门较新的面板加工工艺,从20世纪90年代初开始,由双层胶片层间黏结结构,发展到注塑成型多元结构的三维成型技术,现在已成为当前的一项热门的铭牌工艺,它已一改平面板的刻板模式,发展到山薄膜与印刷图文、标识的油墨及树脂注塑结合成三位一体面板的新模式。
IMD----也就是将印刷好的薄膜成型后,镶嵌在注塑模腔内然后合模注塑。
注塑树脂在薄膜的背面与油墨层相结合,面板图文、标识置于薄膜与注塑成型的树脂之间,图文、标识不会因磨擦或时间关系而磨损。
它以注塑成型为依托,其形状、尺寸可保持稳定,更便于装配,故IMD技术常被应用于汽车、通讯、电子、电器、仪表、仪器的面板上,集装饰性与功能性于一身。
一、IMD产品特性※精美的装饰图文、标识内藏,不受摩擦或化学腐蚀而消失。
※图文、标识及颜色设计可随时改变,而无需更换模具。
※三维立体形状产品的,印刷精度准确,误差+0.05mm。
※能提供图文、标识背透光性及高透光性的视窗效果。
※功能按键凸泡均匀、手感好,寿命可达100万次以上。
※三维变化,可增加设计者对产品设计的自由度。
※复合成型加工达到无缝效果。
二、IMD/IML的应用领域※家电业:电饭煲、洗衣机、微波炉、空调器、电冰箱等的控制装饰面板;※电子业:Mp3、Mp4、计算器、VCD、DVD、电子记事本、数码相机等装饰面壳、彩壳及标牌;※汽车业:仪表盘、空调面板、内饰性、车灯外壳、标志等;※电脑业:键盘、鼠标、面壳;※通讯业:手机按键、手机镜业、手机彩壳、小灵通及固定电话面板、视窗镜片;※其它业:医疗器械、化妆品盒、装饰盒、玩具、运动和娱乐休闲用品等等。
三、IMD工艺的发展前景目前,IMD模内装饰镶嵌注塑技术被广泛应用于通讯、家电、电子、汽车、仪表、仪器、医疗器、玩具、化妆品等行业,是一种崭新的塑胶装饰工艺技术。
注塑模具成型工艺国内外研究现状及发展趋势

注塑模具成型工艺国内外研究现状及发展趋势一、介绍注塑模具是一种用于塑料制品生产的关键工具,具有至关重要的作用。
注塑模具成型工艺则是指利用注塑机将熔融状态的塑料料料塑料注入到模具中,在一定的温度和压力下使其固化、冷却并获得所需形状的过程。
随着塑料制品行业的快速发展,注塑模具成型工艺也得到了广泛的运用。
为了更好地了解和掌握注塑模具成型工艺的国内外研究现状及发展趋势,本文将进行深入的探讨。
二、国内注塑模具成型工艺的研究现状目前,国内在注塑模具成型工艺的研究方面取得了一定的成果。
以下是对一些主要研究方向的总结和回顾。
1. 材料选择和优化材料选择和优化是注塑模具成型工艺中的重要环节之一。
国内的研究者通过对不同材料的性能和工艺要求进行分析,选取了适合注塑模具成型的材料,并进行了相关优化研究。
一些研究者通过改善材料的热导率和耐腐蚀性能,提高了注塑模具的成型效率和寿命。
2. 设计和制造技术在注塑模具成型工艺的研究中,设计和制造技术起着关键的作用。
国内的研究者通过引进先进的设计和制造技术,提高了注塑模具的精度和可靠性。
采用CAD/CAM技术和快速成型技术,可以加快模具的设计和制造过程,减少错误率和成本,并提高生产效率。
3. 成型工艺参数优化成型工艺参数优化是国内注塑模具成型工艺研究的热点之一。
研究者通过对成型工艺参数(如温度、压力、速度等)的优化调整,实现了产品质量和生产效益的提高。
通过调节注射速度和压力,研究者成功地解决了注塑过程中的热应力和缩水问题,提高了产品的成型精度和表面质量。
4. 模具运行监测和控制模具运行监测和控制是提高注塑模具成型工艺稳定性和生产效率的重要手段。
国内的研究者通过引入传感器和监测技术,实现了对注塑模具运行状态的实时监测和控制。
利用温度传感器和压力传感器,可以监测和控制注塑过程中的温度和压力变化,防止模具因过热或过压而损坏,提高注塑模具的使用寿命。
三、国际注塑模具成型工艺的研究进展国际上,注塑模具成型工艺的研究也取得了一系列进展。
15节-模内覆膜注塑成型IMF
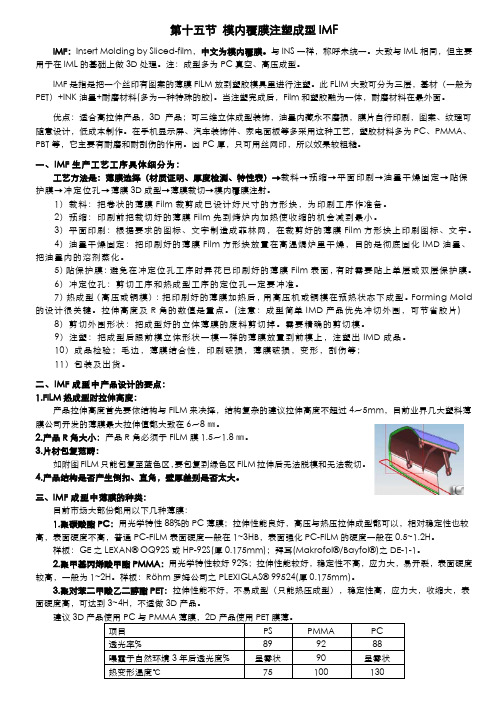
第十五节模内覆膜注塑成型IMFIMF:Insert Molding by Sliced-film,中文为模内覆膜。
与INS一样,称呼未统一。
大致与IML相同,但主要用于在IML的基础上做3D处理。
注:成型多为PC真空、高压成型。
IMF是指是把一个丝印有图案的薄膜FILM放到塑胶模具里进行注塑。
此FLIM大致可分为三层,基材(一般为PET)+INK油墨+耐磨材料(多为一种特殊的胶)。
当注塑完成后,Film和塑胶融为一体,耐磨材料在最外面。
优点:适合高拉伸产品,3D 产品;可三维立体成型装饰,油墨内藏永不磨损,膜片自行印刷,图案、纹理可随意设计,低成本制作。
在手机显示屏、汽车装饰件、家电面板等多采用这种工艺,塑胶材料多为PC、PMMA、PBT等,它主要有耐磨和耐刮伤的作用。
因PC厚,只可用丝网印,所以效果较粗糙。
一、IMF生产工艺工序具体细分为:工艺方法是:薄膜选择(材质证明、厚度检测、特性表)→裁料→预缩→平面印刷→油墨干燥固定→贴保护膜→冲定位孔→薄膜3D成型→薄膜裁切→模内覆膜注射。
1)裁料:把卷状的薄膜Film裁剪成已设计好尺寸的方形块,为印刷工序作准备。
2)预缩:印刷前把裁切好的薄膜Film先到烤炉内加热使收缩的机会减到最小。
3)平面印刷:根据要求的图标、文字制造成菲林网,在裁剪好的薄膜Film方形块上印刷图标、文字。
4)油墨干燥固定:把印刷好的薄膜Film方形块放置在高温焗炉里干燥,目的是彻底固化IMD油墨、把油墨内的溶剂蒸化。
5)贴保护膜:避免在冲定位孔工序时弄花已印刷好的薄膜Film表面,有时需要贴上单层或双层保护膜。
6)冲定位孔:剪切工序和热成型工序的定位孔一定要冲准。
7)热成型(高压或铜模):把印刷好的薄膜加热后,用高压机或铜模在预热状态下成型。
Forming Mold 的设计很关键。
拉伸高度及R角的数值是重点。
(注意:成型简单IMD产品优先冲切外围,可节省胶片) 8)剪切外围形状:把成型好的立体薄膜的废料剪切掉。
IMD注塑工艺

IMD注塑技术工艺IMD的中文名称:是指模内装饰镶嵌注塑技术注塑表面装饰技术,即IMD(In-Mold Decoration),IMD----模内装饰镶嵌注塑技术,是一门较新的面板加工工艺,从20世纪90年代初开始,由双层胶片层间黏结结构,发展到注塑成型多元结构的三维成型技术,现在已成为当前的一项热门的铭牌工艺,它已一改平面板的刻板模式,发展到山薄膜与印刷图文、标识的油墨及树脂注塑结合成三位一体面板的新模式。
IMD----也就是将印刷好的薄膜成型后,镶嵌在注塑模腔内然后合模注塑。
注塑树脂在薄膜的背面与油墨层相结合,面板图文、标识置于薄膜与注塑成型的树脂之间,图文、标识不会因磨擦或时间关系而磨损。
它以注塑成型为依托,其形状、尺寸可保持稳定,更便于装配,故IMD技术常被应用于汽车、通讯、电子、电器、仪表、仪器的面板上,集装饰性与功能性于一身。
一、IMD产品特性※精美的装饰图文、标识内藏,不受摩擦或化学腐蚀而消失。
※图文、标识及颜色设计可随时改变,而无需更换模具。
※三维立体形状产品的,印刷精度准确,误差+0.05mm。
※能提供图文、标识背透光性及高透光性的视窗效果。
※功能按键凸泡均匀、手感好,寿命可达100万次以上。
※三维变化,可增加设计者对产品设计的自由度。
※复合成型加工达到无缝效果。
二、IMD/IML的应用领域※家电业:电饭煲、洗衣机、微波炉、空调器、电冰箱等的控制装饰面板;※电子业:Mp3、Mp4、计算器、VCD、DVD、电子记事本、数码相机等装饰面壳、彩壳及标牌;※汽车业:仪表盘、空调面板、内饰性、车灯外壳、标志等;※电脑业:键盘、鼠标、面壳;※通讯业:手机按键、手机镜业、手机彩壳、小灵通及固定电话面板、视窗镜片;※其它业:医疗器械、化妆品盒、装饰盒、玩具、运动和娱乐休闲用品等等。
三、IMD工艺的发展前景目前,IMD模内装饰镶嵌注塑技术被广泛应用于通讯、家电、电子、汽车、仪表、仪器、医疗器、玩具、化妆品等行业,是一种崭新的塑胶装饰工艺技术。
什么是IMD
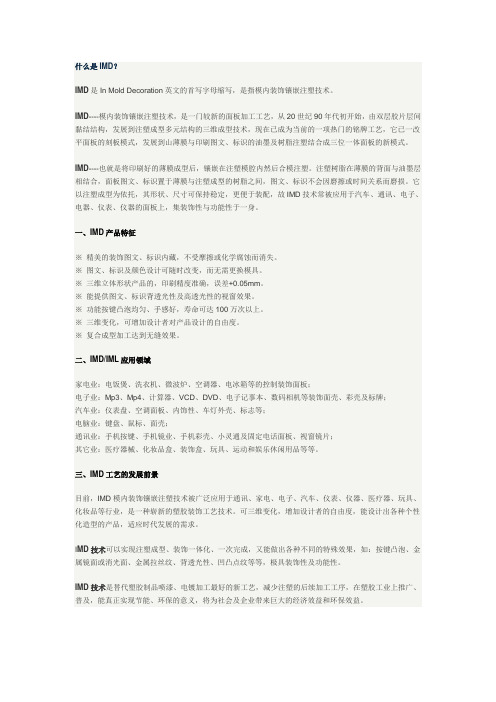
什么是IMD?IMD是In Mold Decoration英文的首写字母缩写,是指模内装饰镶嵌注塑技术。
IMD----模内装饰镶嵌注塑技术,是一门较新的面板加工工艺,从20世纪90年代初开始,由双层胶片层间黏结结构,发展到注塑成型多元结构的三维成型技术,现在已成为当前的一项热门的铭牌工艺,它已一改平面板的刻板模式,发展到山薄膜与印刷图文、标识的油墨及树脂注塑结合成三位一体面板的新模式。
IMD----也就是将印刷好的薄膜成型后,镶嵌在注塑模腔内然后合模注塑。
注塑树脂在薄膜的背面与油墨层相结合,面板图文、标识置于薄膜与注塑成型的树脂之间,图文、标识不会因磨擦或时间关系而磨损。
它以注塑成型为依托,其形状、尺寸可保持稳定,更便于装配,故IMD技术常被应用于汽车、通讯、电子、电器、仪表、仪器的面板上,集装饰性与功能性于一身。
一、IMD产品特征※精美的装饰图文、标识内藏,不受摩擦或化学腐蚀而消失。
※图文、标识及颜色设计可随时改变,而无需更换模具。
※三维立体形状产品的,印刷精度准确,误差+0.05mm。
※能提供图文、标识背透光性及高透光性的视窗效果。
※功能按键凸泡均匀、手感好,寿命可达100万次以上。
※三维变化,可增加设计者对产品设计的自由度。
※复合成型加工达到无缝效果。
二、IMD/IML应用领域家电业:电饭煲、洗衣机、微波炉、空调器、电冰箱等的控制装饰面板;电子业:Mp3、Mp4、计算器、VCD、DVD、电子记事本、数码相机等装饰面壳、彩壳及标牌;汽车业:仪表盘、空调面板、内饰性、车灯外壳、标志等;电脑业:键盘、鼠标、面壳;通讯业:手机按键、手机镜业、手机彩壳、小灵通及固定电话面板、视窗镜片;其它业:医疗器械、化妆品盒、装饰盒、玩具、运动和娱乐休闲用品等等。
三、IMD工艺的发展前景目前,IMD模内装饰镶嵌注塑技术被广泛应用于通讯、家电、电子、汽车、仪表、仪器、医疗器、玩具、化妆品等行业,是一种崭新的塑胶装饰工艺技术。
汽车模内镶件注塑成型( IMD )技术

汽车模内镶件注塑成型(IMD )技术塑料加工商们正在将可成型彩色薄膜视为一个经济、耐用、环境友好的装饰手段,它可使零件在脱模时即已完成装饰。
模内镶件注塑成型(IMD )技术,利用的就是这种可成型薄膜,可替代传统的、在零件脱模后采用的涂漆、印刷、热模锻、镀铬工艺。
该技术的首次成功应用是制成了一些小型的、相对较平的汽车内外饰零部件和手机零件。
今天,IMD技术有了更进一步的发展,可以制成更大的三维零件,例如整个仪表板、汽车保险杠、托板、汽车顶盖,甚至汽车、卡车的发动机罩。
据说,第一个实现商业化的、无需涂漆的水平车身板已经应用在Smart双座敞篷轿车上了。
IMD技术可节省再加工的费用,这对汽车工业极具诱惑力。
GE Plastics的Lexan SLX(一种聚碳酸酯共聚物)车身零件生产经理Venkata-krishnan Umamaheswaran说:“汽车上最贵的就是油漆了,涂漆生产线是汽车装配车间最大的投资,会占据车间一半的地面空间,而且一年内会产生1500多吨VOCs(挥发性有机物)。
”IMD技术的优势还包括:边角料产率低;可在同一地点完成零件的成型和装饰;回收性更好。
IMD技术可获得A级表面,且无流痕,更不会像流痕那样造成“模内驻色”。
但是如果零件本身就有很多孔,必须在脱模后进行装饰,那么IMD技术的经济效益则会大打折扣。
IMD技术的倡导者们宣称:利用最新一代的可成型薄膜制成的车身板,具有与涂漆金属板相媲美的甚至更高的抗划伤性和抗冲击性。
但是,假设汽车制造商们对涂漆生产线仍然施以巨额投资,则IMD在近期内还是无望完全取代涂漆工艺。
不过,工业观察家们相信:在美国,今后即使有投资,也很少会出现建造大型涂漆生产线的情况。
IMD技术首先将一块已经被印刷、涂覆或染色过的塑料薄板经冲切成坯料后,热成型成最终产品的形状。
修正后,把它放入注射腔内,从型腔后面注入一种与其相容的基体材料,最后得到成品。
成品的表面可以是纯色的,也可具有金属外观或木纹效果,还可印有图形符号。
- 1、下载文档前请自行甄别文档内容的完整性,平台不提供额外的编辑、内容补充、找答案等附加服务。
- 2、"仅部分预览"的文档,不可在线预览部分如存在完整性等问题,可反馈申请退款(可完整预览的文档不适用该条件!)。
- 3、如文档侵犯您的权益,请联系客服反馈,我们会尽快为您处理(人工客服工作时间:9:00-18:30)。
模内组装: 复合注塑成型新前沿模内贴标、膜材装饰、多色注塑正逐渐成为大家所熟悉的技术。
因此在模具中完成所有工序,消除二次操作这个方向上的下一个发展阶段会是什么?目前能想到的新目标是模内组装。
通过不相容材料的扣合、焊接和共同成型,避免二次操作的需要推动着复合注塑成型朝着利用设备组装不同组件的方向前进。
在加工厂商、模具厂商以及机器设备制造商之间讨论这一主题,很快就会发现对“模内组装”(或IMA)这一术语,他们有迥然不同的定义。
本文目的就是要从多枪成型或硬/软重叠注塑的一般领域对此进行辨别。
虽然模内组装通常需要多枪注塑,但是这一概念的本质是将模具内各个单独的部分变成一个整体,否则的话这些部分将在模具外部通过扣合、焊接或者粘合剂粘合进行组装。
Ferromatik Milacron欧洲公司的美国分公司总经理Bob Hare表示:“如果在成型加工过程中需要下一步的工序,(最简单的方法),你就不得不考虑使用模内组装。
”图1,模内组装应用实例1、Innatech公司的PBT、ABS和PP材料的通风窗。
2、MGS公司制造的PC、PP和TPV材料的医用阀件。
3、Gram科技公司的PP和PE材料的翻盖果汁包装盖。
4、Ferromatik Milacron公司的PP 园盖分配器。
5、Gram科技公司的具有PP、PE滑动中心的转换阀6、来自Ferromatik Milacron公司用于个人护理产品的PP上推式瓶盖模内织物或地毯复合看上去似乎符合这一定义。
但这可以被考虑当作是嵌入成型的一种形式――一种已经为大家所熟悉的技术,但不再本文讨论的范围内。
这一点可以从下面讨论的例子中得到验证,模内组装不仅仅只是重叠模塑或者嵌入物成型,但是它们的任一种或者都可以归类为模内组装的一种。
一、复合注塑组装成型的优势与其它的模内加工与增值处理一样,模内组装的优点是经济性,部分因素是和质量有关。
加工厂商兼模具制造厂商Electroform的总裁Wade Clark表示:“这种方式能够提供更加稳定的产品,不会产生采用二次操作会出现的变形或收缩问题,特别是针对有两个或多个需要配对的注塑件。
”恩格尔公司的加工技术部经理Joachim Kragl补充说:“你可以用一台机器以及一副较小的模具以较低的成本加工出组装产品的一个单件,但是如果你考虑到单件组装成配件以及组装线本身所涉及的所有费用,那么利用模内加工出配件来说节约的费用是惊人的。
你所担忧的只不过是一台机器和一个工艺,如果我有一个三元产品要组装,那将需要三个自动化生产线,这样就增加了生产中断的可能性。
”其它优势还有节约省去了运输、料斗、夹具、超声焊接机等,也消除了因错误处理、未对准、加工异常或污染所导致的废件可能来源。
模具和机器制造商普遍认为模内组装还具有如下优势:1、从模具中生产出最终注塑件避免了半成品的存货;2、模内组装可避免使用单独的压机或模具,减少了人力和场地空间的需要;3、模内组装确保了待组装的注塑件正确的搭配或结合,对装饰性注塑件来说它具有很大优势;4、相对于分别成型每一个注塑零件,然后组装在一起所花的时间来说,模内组装能够降低生产各个组装件所花费的总时间;5、那些用常规方法生产会受到成本限制或技术几乎不能实现的制品,在模内组装中可以生产出来。
模内组装通常要求较高的注塑件产量,因为在同样的空化条件下,它的模具成本会比标准的模具高出30%到70%。
一般认为约为25万产品的工作量比较适合模内组装生产。
他们还认为模内组装在欧洲的发展速度要比北美的要快,主要用于汽车及消费类商品,少量用于医用注塑件。
模内组装的关键点更多地是建立在模具上而不是成型加工上。
阿博格、恩格尔、克劳斯玛菲和米拉克伦等设备制造商认为模内组装设备与其它多组分成型任务使用的设备没有太多不同之处,但是他们认为有区别的地方是一体化自动操作和安排后续操作步骤的关键技术。
克劳斯玛菲注塑成型业务的总经理Peter Lipp 表示:“只要一台机器具有能确保加工重复性和精度的闭环控制系统,那么它就可以用于模内组装。
”某些情况下,特殊模内组装加工的供应商会和特殊的注塑机制造商展开合作。
叠层的模具设计有一个在垂直轴上旋转的中心模板。
取决于系统,中心模板可以有或者两个或者四个面。
一个实例就是Ferromatik 和Foboha公司(德国模具制造商,模具具有一个或多个四面旋转“立方体”)的合作。
同样提供多面“旋转叠层”模具的丹麦Gram科技公司已经和德玛格塑料集团合做了多个项目。
恩格尔公司采取了一个多面的方法:“我们或者自己制造模具,或者和北美的公司进行合作,”卡尔表示,“因为我们也制造了用于多组分成型的设备,并且拥有我们自己的自动化生产能力,对我们来说模内组装就成了我们重要的专业技术领域。
”二、实现模内组装的多种途径许多加工厂商已经开发出许多实现模内组装的方法。
有些方法使用了具有滑动模板或者旋转模板的单面模具。
其它的方法使用了以传统的线性或更新的旋转板设计的多分型叠层模具。
许多情况下,单面模具使用旋转或者滑动式模板来改变射点之间的型腔配置。
单面和叠层模具都能得到借助一个或者多个旋转中心转位得到更多的功能性,其中每一个能够拥有四个面从而起到不同的功能。
同时许多应用能通过自动设备或者更小的设计在型腔或甚至在机器之间进行注塑件转移。
举例来说,用于单面模具的模内组装方法是来自模具制造商StackTeck新的“传递成型”概念。
销售总经理Jordan Robertson介绍,模具上的处理装置是通过模具运动的机械作用将注塑件从一个型腔传递到另一个型腔。
“机械手的推动力来自处于叠层中心部位的击点位置,”Robertson说,“它使用旋转装置通过夹具运动操作自动设备的。
”通过一台机器到另一台机器的自动转移被应用到Gram公司的一个产品中。
在一台机器中“旋转叠层”成型两个透明聚碳酸酯外壳,从另一单独的设备传递一硅树脂膜片并嵌入到其中一个外壳上。
在旋转叠层的适当位置,两个对立的叠层连接好时,对聚碳酸酯的啮合表面再次加热,让外壳焊接在一起。
恩格尔对这一技术进行了变动,能生产出液体硅橡胶和PBT材料组成的二元结构旋塞过滤器。
该注塑件分别使用具有偏离中央旋转板的无拉杆设备加工成型,在模具中注塑件通过自动装置施加给注塑件的互相作用力形成扣合结构从而产生组装产品。
一个较老的模内组装概念出自JSW公司,它和日本的Sakamoto Tool and Die公司合作开发出模具滑移注射成型(DSI)工艺。
该工艺1991年推出,它通过成型两个分开的半型方法生产中空产品,然后通过滑移模板将它们放在一起,最终两个分型通过重叠模塑密封连接在一起。
根据JSW 公司芝加哥技术中心的总经理Robert Columbus介绍,在亚洲有两套这样的系统在使用。
图2,Gram科技公司旋转重叠加工成型一个螺纹帽和一个带拉签的配合螺纹盖,这两个分开的注塑件组装在一起之前是单独的注塑件三、旋转“立方体”与“叠层”Ferromatik Milacron公司和Foboha公司联合开发出用于高容积、二元模内组装的装配完备的系统。
两家公司在去年的美国国际橡塑展上展出了该系统,演示了模具中进行两种色彩应用的扣合成型。
Foboha 的美国销售工程师Lisa Mauro介绍了该公司的TwinCube模具四个面都留有印刷、贴标签和退扣功能的位置。
她指出:“我们的设备为了模具的动作使用了附加的运动(如扣合),因此它不依赖成型设备。
”Milacron/Foboha系统的第一个美国用户是在新泽西州Somerset的Stull Technologies公司,它用来生产带有标签嵌件和扣合组件的叠层外套。
营销高级主管Jason Stull认为该系统将在型号为275吨K-Tec的机器和48腔TwinCube可旋转叠层模具中生产二元聚丙烯的“具有圆形上盖的瓶盖”。
图3,Foboha公司的高输出TwinCube模具是去年卖给Stull科技公司,用于生产聚丙烯盖子和座套,它们通过模具扣合在一起形成圆盖式分配系统。
Stull介绍说这种系统将在保持单件价格低至能抵挡国外竞争者的地步,帮助提高其产能到每年数以亿计的瓶盖。
系统运行几乎与类似注塑件的常规生产线相同,但是公司希望在获得更高生产率和更稳定质量的同时,只使用一半的人工并节约30%的占地空间。
(Stull希望加工能力指数为1.3。
)Gram科技公司提供的旋转叠箱模具具有四个在定模板和动模板之间定位的分度中心设置。
每一个中心设置可以拥有四个面和90°的旋转增量。
公司总裁Jes Gram介绍说其最重要的测试项目是用于一种球形容器的生产。
他说:“全球有数十亿这些产品生产,它们一般是通过成型两个半型外壳,然后用焊接工序进行连接。
这种容器一般是能承受焊接工序的厚壁,最后的形状必须正好是球形以便于它能在除臭剂分散器上平稳滚动,并且不会影响毛发。
在模具中通过Gram的设备连接两个半型。
”KTW公司作为一家向个人护理和消费市场提供高度空化的瓶盖和外壳工具的奥地利制造商,正在使用Gram公司的旋转叠层技术生产食用油容器的瓶盖和瓶盖底座。
KTW公司的总经理Claus Ziegler介绍说注塑件是由具有一次性拉签和瓶盖结构的螺纹瓶盖底座。
“你不能使用重叠模塑组装一个瓶盖和带一次性拉签的瓶盖底座。
模内组装是唯一可以成型的方法。
用不同的工具,将需要花费8到9秒的时间成型底座,以及4到5秒时间成型瓶盖。
KTW的工具在8到9秒的时间内,利用16腔试验工具就能成型出整个结构,这种生产模具将达到48或64腔。
”电动成型是用旋转台加工的新要素。
这使用了其去年在芝加哥美国国际橡塑展上展示的正在申请专利的方法。
它一体化了二次注塑成型,模内薄膜装饰,以及成型并将ABS玩具赛车的上部和底部以及四个轮子扣合在一起的模内组装。
专利的单面模具设计使用了成对的旋转台,而无需额外的自动系统。
从展出以来,周期时间已经从22秒优化到15秒。
MGS制造集团既是加工厂商又是工具制造商,已经生产出许多模内组装注塑件,包括一个和安全有关产品的调节带,产品具有扣合结构。
注塑件具有不可移动的锁定螺帽。
工艺替代了四到五个机器以及众多的下游设备。
四、复杂的重叠注塑MGS公司的市场主管John Berg表示:“模内组装最好的特性之一是能够将组件连接在一起形成不会分开的可移动注塑件。
”越来越多的公司已经设计出使用不同且彼此不粘合的材料成型机械互锁的铰链和连接件,所以配件能够运动自如。
这是与将不同材料彼此粘合在一起为目的的典型重叠注塑最大的不同。
这种情况下,整个要点是对着一种材料注射另一种材料,并且不让它们粘和在一起。
模内组装这一方法的最初想法是通常归功于位于德国Selb的模具制造商Fickenscher公司。