4H曲轴工艺流程
曲轴加工工艺流程

曲轴加工工艺流程曲轴是内燃机的重要零部件之一,它承受着发动机高速旋转时的巨大转矩,因此曲轴的加工工艺流程显得尤为重要。
下面将详细介绍曲轴加工的工艺流程。
首先,曲轴的加工从原材料的准备开始。
通常情况下,曲轴的原材料是优质的合金钢,这种材料具有较高的强度和硬度,能够满足曲轴在高速旋转时的要求。
在原材料准备阶段,需要对原材料进行质量检测,确保原材料符合加工要求。
接下来是曲轴的粗加工。
粗加工包括车削、铣削、钻削等工艺,通过这些工艺可以初步将原材料加工成曲轴的初步形状。
在粗加工过程中,需要严格控制加工尺寸和表面粗糙度,以确保后续加工的顺利进行。
然后是曲轴的热处理工艺。
热处理是提高曲轴强度和硬度的重要工艺环节,通过淬火、回火等热处理工艺,可以使曲轴具有良好的力学性能和耐磨性能。
接着是曲轴的精密加工。
精密加工是曲轴加工工艺流程中的关键环节,包括磨削、抛光等工艺。
通过精密加工,可以使曲轴的尺寸精度达到要求,并且提高曲轴的表面质量,减小表面粗糙度,提高曲轴的耐磨性能。
最后是曲轴的检测和组装。
在曲轴加工完成后,需要进行严格的检测,包括尺寸检测、硬度检测、表面质量检测等,确保曲轴的质量达到要求。
随后进行曲轴的组装,将曲轴与连杆、曲轴箱等零部件进行组装,组装完成后进行整体质量检测,确保曲轴的装配质量。
综上所述,曲轴的加工工艺流程包括原材料准备、粗加工、热处理、精密加工、检测和组装等环节,每个环节都至关重要,需要严格控制加工工艺,确保曲轴的质量和性能达到要求。
曲轴作为内燃机的关键零部件,其加工质量直接影响到发动机的性能和可靠性,因此曲轴加工工艺流程的重要性不言而喻。
曲轴加工工艺流程简述
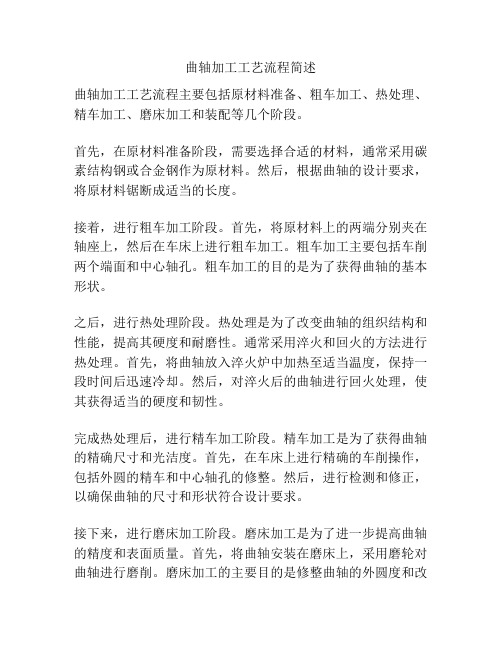
曲轴加工工艺流程简述曲轴加工工艺流程主要包括原材料准备、粗车加工、热处理、精车加工、磨床加工和装配等几个阶段。
首先,在原材料准备阶段,需要选择合适的材料,通常采用碳素结构钢或合金钢作为原材料。
然后,根据曲轴的设计要求,将原材料锯断成适当的长度。
接着,进行粗车加工阶段。
首先,将原材料上的两端分别夹在轴座上,然后在车床上进行粗车加工。
粗车加工主要包括车削两个端面和中心轴孔。
粗车加工的目的是为了获得曲轴的基本形状。
之后,进行热处理阶段。
热处理是为了改变曲轴的组织结构和性能,提高其硬度和耐磨性。
通常采用淬火和回火的方法进行热处理。
首先,将曲轴放入淬火炉中加热至适当温度,保持一段时间后迅速冷却。
然后,对淬火后的曲轴进行回火处理,使其获得适当的硬度和韧性。
完成热处理后,进行精车加工阶段。
精车加工是为了获得曲轴的精确尺寸和光洁度。
首先,在车床上进行精确的车削操作,包括外圆的精车和中心轴孔的修整。
然后,进行检测和修正,以确保曲轴的尺寸和形状符合设计要求。
接下来,进行磨床加工阶段。
磨床加工是为了进一步提高曲轴的精度和表面质量。
首先,将曲轴安装在磨床上,采用磨轮对曲轴进行磨削。
磨床加工的主要目的是修整曲轴的外圆度和改善其表面质量。
最后,进行装配阶段。
将其他零部件,如曲柄杆、连杆等组装到曲轴上,使之成为完整的曲轴装配件。
装配完成后,进行必要的检测和调整,确保曲轴的性能和工作可靠性。
以上就是曲轴加工工艺流程的简要描述。
曲轴的加工工艺复杂,需要经过多个步骤的加工和处理,才能获得高精度和高质量的曲轴产品。
曲轴的加工工艺流程
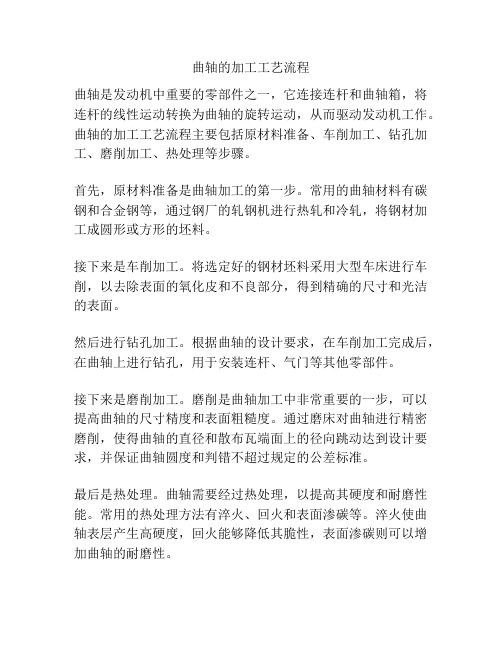
曲轴的加工工艺流程
曲轴是发动机中重要的零部件之一,它连接连杆和曲轴箱,将连杆的线性运动转换为曲轴的旋转运动,从而驱动发动机工作。
曲轴的加工工艺流程主要包括原材料准备、车削加工、钻孔加工、磨削加工、热处理等步骤。
首先,原材料准备是曲轴加工的第一步。
常用的曲轴材料有碳钢和合金钢等,通过钢厂的轧钢机进行热轧和冷轧,将钢材加工成圆形或方形的坯料。
接下来是车削加工。
将选定好的钢材坯料采用大型车床进行车削,以去除表面的氧化皮和不良部分,得到精确的尺寸和光洁的表面。
然后进行钻孔加工。
根据曲轴的设计要求,在车削加工完成后,在曲轴上进行钻孔,用于安装连杆、气门等其他零部件。
接下来是磨削加工。
磨削是曲轴加工中非常重要的一步,可以提高曲轴的尺寸精度和表面粗糙度。
通过磨床对曲轴进行精密磨削,使得曲轴的直径和散布瓦端面上的径向跳动达到设计要求,并保证曲轴圆度和判错不超过规定的公差标准。
最后是热处理。
曲轴需要经过热处理,以提高其硬度和耐磨性能。
常用的热处理方法有淬火、回火和表面渗碳等。
淬火使曲轴表层产生高硬度,回火能够降低其脆性,表面渗碳则可以增加曲轴的耐磨性。
以上就是曲轴的加工工艺流程。
在实际加工过程中,还需要仔细设计工艺路线,选择合适的加工设备和工具,保证每个加工步骤的精度和表面质量,以及严格控制每个加工步骤的尺寸公差,最终确保曲轴的质量和使用性能。
同时,加工过程中需要严格遵守安全操作规程,确保工人的人身安全和设备的正常运行。
曲轴的加工工艺过程

曲轴的加工工艺过程曲轴是发动机上的一个重要的机件,其材料是由碳素结构钢或球墨铸铁制成的,有两个重要部位:主轴颈,连杆颈(还有其他)。
主轴颈被安装在缸体上,连杆颈与连杆大头孔连接,连杆小头孔与汽缸活塞连接,是一个典型的曲柄滑块机构。
曲轴的润滑主要是指与连杆大头轴瓦与曲轴连杆颈的润滑和两头固定点的润滑,曲轴的旋转是发动机的动力源,也是整个机械系统的源动力。
曲轴的工作原理曲轴是发动机中最典型、最重要的零件之一,其功用是将活塞连杆传递来的气体压力转变为转矩,作为动力而输出做功,驱动器他工作机构,并带动内燃机辅助装备工作。
曲轴加工工艺虽然曲轴的品种较多,结构上一些细节有所不同,但加工工艺过程大致相同。
主要工艺介绍(1)曲轴主轴颈及连杆颈外铣加工在进行曲轴零件加工时,由于圆盘铣刀本身结构的影响,刀刃与工件始终是断续接触,有冲击。
因此,机床整个切削系统中控制了间隙环节,降低了加工过程中因运动间隙产生的振动,从而提高了加工精度和刀具的的使用寿命。
(2)曲轴主轴颈及连杆颈磨削跟踪磨削法是以主轴颈中心线为回转中心,一次装夹依次完成曲轴连杆颈的磨削加工(也可用于主轴颈磨削),磨削连杆轴颈的实现方式是通过CNC控制砂轮的进给和工件回转运动两轴联动,来完成曲轴加工进给。
跟踪磨削法采用一次装夹、在一台数控磨床上依次完成曲轴主轴颈和连杆颈的磨削加工,能有效地减少设备费用,降低加工成本,提高加工精度和生产效率。
(3)曲轴主轴颈、连杆颈圆角滚压机床应用滚压机床是为了提高曲轴的疲劳强度。
据统计资料表明,球墨铸铁曲轴经圆角滚压后的曲轴寿命可提高120%~230%;锻钢曲轴经圆角滚压后寿命可提高70%~130%。
滚压的旋转动力来源于曲轴的旋转,带动滚压头中的滚轮转动,而滚轮的压力是由油缸实施的。
发动机主要受力零件曲轴其疲劳破坏最常见的是金属疲劳破坏,即弯曲疲劳破坏和扭转疲劳破坏,前者的发生概率大于后者。
弯曲疲劳裂纹首先产生在连杆轴颈(曲柄销)或主轴颈圆角处,然后向曲柄臂发展。
曲轴生产工艺流程
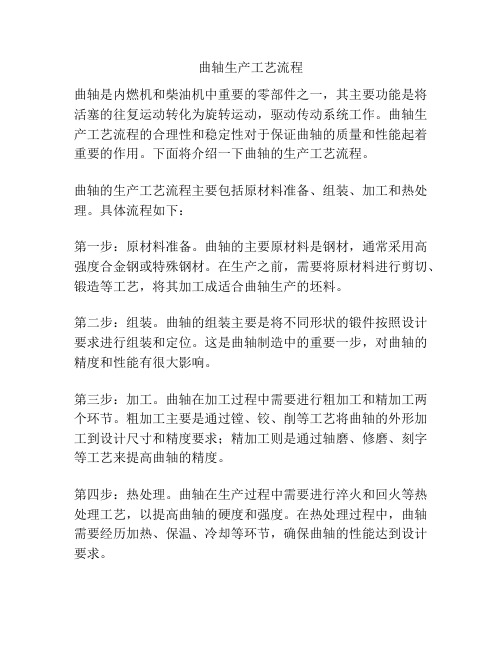
曲轴生产工艺流程
曲轴是内燃机和柴油机中重要的零部件之一,其主要功能是将活塞的往复运动转化为旋转运动,驱动传动系统工作。
曲轴生产工艺流程的合理性和稳定性对于保证曲轴的质量和性能起着重要的作用。
下面将介绍一下曲轴的生产工艺流程。
曲轴的生产工艺流程主要包括原材料准备、组装、加工和热处理。
具体流程如下:
第一步:原材料准备。
曲轴的主要原材料是钢材,通常采用高强度合金钢或特殊钢材。
在生产之前,需要将原材料进行剪切、锻造等工艺,将其加工成适合曲轴生产的坯料。
第二步:组装。
曲轴的组装主要是将不同形状的锻件按照设计要求进行组装和定位。
这是曲轴制造中的重要一步,对曲轴的精度和性能有很大影响。
第三步:加工。
曲轴在加工过程中需要进行粗加工和精加工两个环节。
粗加工主要是通过镗、铰、削等工艺将曲轴的外形加工到设计尺寸和精度要求;精加工则是通过轴磨、修磨、刻字等工艺来提高曲轴的精度。
第四步:热处理。
曲轴在生产过程中需要进行淬火和回火等热处理工艺,以提高曲轴的硬度和强度。
在热处理过程中,曲轴需要经历加热、保温、冷却等环节,确保曲轴的性能达到设计要求。
第五步:检测和质量控制。
曲轴生产完成后需要进行各项质量检测,确保曲轴的尺寸、硬度、表面质量等符合标准要求。
如果出现不合格品,需要及时进行返修或淘汰处理。
以上就是曲轴生产工艺流程的简要介绍。
在实际生产中,每个步骤都需要严格控制和把握,确保曲轴的质量和性能。
随着科技的发展和生产技术的提高,曲轴生产工艺也在不断的创新和改进,以适应不同类型发动机的需求和要求。
曲轴加工工艺流程简述
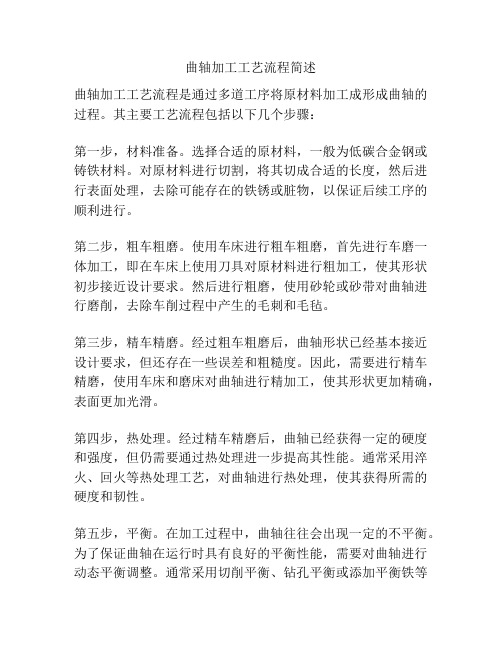
曲轴加工工艺流程简述曲轴加工工艺流程是通过多道工序将原材料加工成形成曲轴的过程。
其主要工艺流程包括以下几个步骤:第一步,材料准备。
选择合适的原材料,一般为低碳合金钢或铸铁材料。
对原材料进行切割,将其切成合适的长度,然后进行表面处理,去除可能存在的铁锈或脏物,以保证后续工序的顺利进行。
第二步,粗车粗磨。
使用车床进行粗车粗磨,首先进行车磨一体加工,即在车床上使用刀具对原材料进行粗加工,使其形状初步接近设计要求。
然后进行粗磨,使用砂轮或砂带对曲轴进行磨削,去除车削过程中产生的毛刺和毛毡。
第三步,精车精磨。
经过粗车粗磨后,曲轴形状已经基本接近设计要求,但还存在一些误差和粗糙度。
因此,需要进行精车精磨,使用车床和磨床对曲轴进行精加工,使其形状更加精确,表面更加光滑。
第四步,热处理。
经过精车精磨后,曲轴已经获得一定的硬度和强度,但仍需要通过热处理进一步提高其性能。
通常采用淬火、回火等热处理工艺,对曲轴进行热处理,使其获得所需的硬度和韧性。
第五步,平衡。
在加工过程中,曲轴往往会出现一定的不平衡。
为了保证曲轴在运行时具有良好的平衡性能,需要对曲轴进行动态平衡调整。
通常采用切削平衡、钻孔平衡或添加平衡铁等方法,使曲轴在高速旋转时不产生明显的振动和不平衡力。
第六步,表面处理。
曲轴作为发动机等设备的核心部件,其表面需要进行一定的处理,以提高其耐磨性和防腐性。
常见的表面处理方法包括镀铬、喷涂等。
镀铬可以提高曲轴表面的硬度和耐磨性,喷涂可以形成一层保护膜,防止曲轴被腐蚀和氧化。
第七步,终检和包装。
经过以上工艺流程后,曲轴已经完成了加工过程,但为了确保其质量,需要进行终检。
终检包括对曲轴进行尺寸测量、外观检查、性能测试等各项检验。
通过终检合格后,将曲轴进行包装,以便运输和存储。
以上就是曲轴加工工艺流程的简单描述。
当然,实际的加工过程还会因具体的工艺要求、设备和加工对象的不同而有所差异。
曲轴生产工艺流程介绍
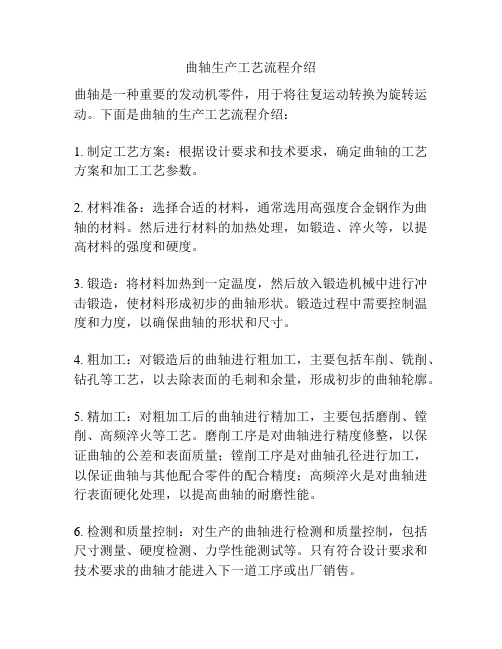
曲轴生产工艺流程介绍
曲轴是一种重要的发动机零件,用于将往复运动转换为旋转运动。
下面是曲轴的生产工艺流程介绍:
1. 制定工艺方案:根据设计要求和技术要求,确定曲轴的工艺方案和加工工艺参数。
2. 材料准备:选择合适的材料,通常选用高强度合金钢作为曲轴的材料。
然后进行材料的加热处理,如锻造、淬火等,以提高材料的强度和硬度。
3. 锻造:将材料加热到一定温度,然后放入锻造机械中进行冲击锻造,使材料形成初步的曲轴形状。
锻造过程中需要控制温度和力度,以确保曲轴的形状和尺寸。
4. 粗加工:对锻造后的曲轴进行粗加工,主要包括车削、铣削、钻孔等工艺,以去除表面的毛刺和余量,形成初步的曲轴轮廓。
5. 精加工:对粗加工后的曲轴进行精加工,主要包括磨削、镗削、高频淬火等工艺。
磨削工序是对曲轴进行精度修整,以保证曲轴的公差和表面质量;镗削工序是对曲轴孔径进行加工,以保证曲轴与其他配合零件的配合精度;高频淬火是对曲轴进行表面硬化处理,以提高曲轴的耐磨性能。
6. 检测和质量控制:对生产的曲轴进行检测和质量控制,包括尺寸测量、硬度检测、力学性能测试等。
只有符合设计要求和技术要求的曲轴才能进入下一道工序或出厂销售。
7. 表面处理:对曲轴进行表面处理,主要包括除锈、防腐涂层、涂油等工艺,以延长曲轴的使用寿命和提高其外观质量。
8. 组装和测试:将曲轴与其他发动机零件进行组装,然后进行测试。
测试包括静态测试和动态测试,以确保曲轴的正常运转和安全性能。
以上是曲轴的生产工艺流程介绍,不同厂家和不同型号的曲轴可能会有所差异。
曲轴加工工艺流程
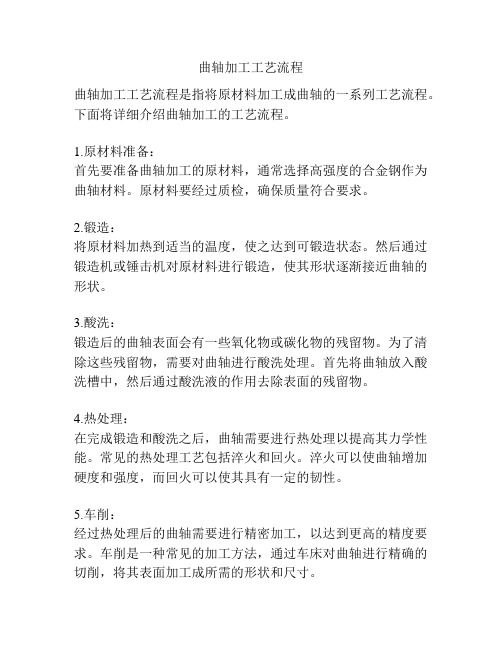
曲轴加工工艺流程曲轴加工工艺流程是指将原材料加工成曲轴的一系列工艺流程。
下面将详细介绍曲轴加工的工艺流程。
1.原材料准备:首先要准备曲轴加工的原材料,通常选择高强度的合金钢作为曲轴材料。
原材料要经过质检,确保质量符合要求。
2.锻造:将原材料加热到适当的温度,使之达到可锻造状态。
然后通过锻造机或锤击机对原材料进行锻造,使其形状逐渐接近曲轴的形状。
3.酸洗:锻造后的曲轴表面会有一些氧化物或碳化物的残留物。
为了清除这些残留物,需要对曲轴进行酸洗处理。
首先将曲轴放入酸洗槽中,然后通过酸洗液的作用去除表面的残留物。
4.热处理:在完成锻造和酸洗之后,曲轴需要进行热处理以提高其力学性能。
常见的热处理工艺包括淬火和回火。
淬火可以使曲轴增加硬度和强度,而回火可以使其具有一定的韧性。
5.车削:经过热处理后的曲轴需要进行精密加工,以达到更高的精度要求。
车削是一种常见的加工方法,通过车床对曲轴进行精确的切削,将其表面加工成所需的形状和尺寸。
6.磨削:车削后的曲轴可能会有一些表面粗糙度或尺寸偏差,为了消除这些缺陷,需要进行磨削。
磨削可以提高曲轴的表面光洁度和精度,使得曲轴的轴向承载能力更好。
7.平衡:曲轴是发动机中的重要部件,对发动机的运行平衡性有很大影响。
为了保证曲轴的平衡性,需要进行平衡加工。
通常采用动平衡方法对曲轴进行平衡处理,确保曲轴在高速旋转时能够保持平衡。
8.油孔加工:曲轴中有一些特定的油孔需要进行加工,以便实现曲轴的润滑和散热功能。
这些油孔可以通过钻孔和铰孔等加工方法进行加工。
9.表面处理:为了保护曲轴表面免受腐蚀和磨损,需要进行表面处理。
最常见的表面处理方法是镀铬,通过将曲轴浸入酸性电解液中,进行电解镀铬,形成一层保护性的铬层。
10.总检和包装:最后,需要对加工好的曲轴进行总检,以确保其质量符合要求。
一旦通过总检,曲轴就可以进行包装,送往下一道工序或交付给客户使用。
以上就是曲轴加工的工艺流程,每个工艺步骤都非常重要,只有完整地经历了这些步骤,才能得到质量上乘的曲轴产品。
- 1、下载文档前请自行甄别文档内容的完整性,平台不提供额外的编辑、内容补充、找答案等附加服务。
- 2、"仅部分预览"的文档,不可在线预览部分如存在完整性等问题,可反馈申请退款(可完整预览的文档不适用该条件!)。
- 3、如文档侵犯您的权益,请联系客服反馈,我们会尽快为您处理(人工客服工作时间:9:00-18:30)。
BSC-02T
215 精磨连接法兰轴颈 220 探伤 230 动平衡 240 去除重孔、边缘毛刺 250 曲轴抛光 255 清洗所有油孔 260 清洗曲轴油孔及外表 265 吹风并清除白斑 270 加热压装油泵齿轮
加热装配设备
280 终检 290 防锈 300 包装
锻件 设备型号 CK1463/SSCK6 3 CK1463 RJ-GAKL-C GPM240F2-3 SUC8149d RX-065 DM-3 NCL2001-270 HSQZH100 BH5S H197 3SPL-A Z5140B BSC-02T-M SSCK50 QS40 SUC8114 G1/2B(M565) KA500/1000 BJ-GAKL QS40 GZ-108 H-175 CJW-4000E BRK-0164 TFK1300 F08279
装正时销孔,加热压装正时齿轮和 专用热装压机 法兰 精车止推面及后油封倒角 精抛光油孔口 加工定位销孔和两端孔系 精磨所有主轴颈 数控车床 风动砂轮机 两端孔专机 主轴颈磨床 连杆颈磨床 打标机 风动砂轮机
190 精磨所有连杆颈 195 打标记 200 抛光油孔口 210
精磨齿轮,前油封,皮带轮轴颈及 斜头架磨床 端面 主轴颈磨床 探伤机 动平衡机 抛光机 清洗机
零件号 工序号
10BF11-05020/05021 工序名称 05J 毛坯检查
毛坯种类 设备名称
15 粗车1,4,5,主轴颈,粗精车小头端 数控车床 20 粗精车后端头和精车1,4,5主轴颈 25 打流水号 30 内铣所有的连杆颈和2,3主轴颈 40 钻全部油孔机孔口倒角 60 去毛刺 70 中间清洗 80 轴颈和圆角淬火 90 回火并热校直 100 抛丸处理 110 修整中心孔 120 半精磨1,5主轴颈 130 精磨后端头外圆 140 加工正时销孔 150备 油孔钻 清洗机 淬火机 回火炉 抛丸机 卧式加工中心 主轴颈磨床 斜头架磨床 立式钻床