曲轴介绍及其工艺流程修订稿
曲轴的加工工艺流程
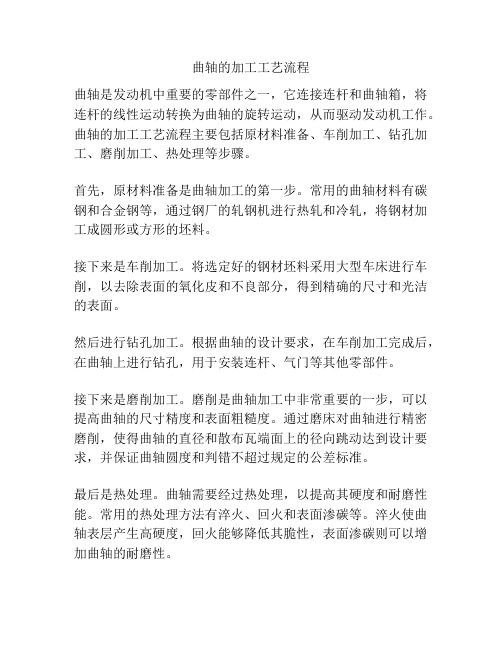
曲轴的加工工艺流程
曲轴是发动机中重要的零部件之一,它连接连杆和曲轴箱,将连杆的线性运动转换为曲轴的旋转运动,从而驱动发动机工作。
曲轴的加工工艺流程主要包括原材料准备、车削加工、钻孔加工、磨削加工、热处理等步骤。
首先,原材料准备是曲轴加工的第一步。
常用的曲轴材料有碳钢和合金钢等,通过钢厂的轧钢机进行热轧和冷轧,将钢材加工成圆形或方形的坯料。
接下来是车削加工。
将选定好的钢材坯料采用大型车床进行车削,以去除表面的氧化皮和不良部分,得到精确的尺寸和光洁的表面。
然后进行钻孔加工。
根据曲轴的设计要求,在车削加工完成后,在曲轴上进行钻孔,用于安装连杆、气门等其他零部件。
接下来是磨削加工。
磨削是曲轴加工中非常重要的一步,可以提高曲轴的尺寸精度和表面粗糙度。
通过磨床对曲轴进行精密磨削,使得曲轴的直径和散布瓦端面上的径向跳动达到设计要求,并保证曲轴圆度和判错不超过规定的公差标准。
最后是热处理。
曲轴需要经过热处理,以提高其硬度和耐磨性能。
常用的热处理方法有淬火、回火和表面渗碳等。
淬火使曲轴表层产生高硬度,回火能够降低其脆性,表面渗碳则可以增加曲轴的耐磨性。
以上就是曲轴的加工工艺流程。
在实际加工过程中,还需要仔细设计工艺路线,选择合适的加工设备和工具,保证每个加工步骤的精度和表面质量,以及严格控制每个加工步骤的尺寸公差,最终确保曲轴的质量和使用性能。
同时,加工过程中需要严格遵守安全操作规程,确保工人的人身安全和设备的正常运行。
曲轴的工艺流程

曲轴的工艺流程
《曲轴的工艺流程》
曲轴是发动机中非常重要的一个零部件,它通过连杆将活塞的上下运动转换为旋转运动,驱动发动机的工作。
在汽车、船舶、飞机等交通工具中都有广泛的应用。
制造曲轴需要经过一系列复杂的工艺流程。
首先,制造曲轴的材料一般采用优质的合金钢。
材料的选择要求耐磨、耐热、抗疲劳等性能,以满足曲轴在高速旋转过程中的工作要求。
接下来是锻造工艺,将选定的合金钢加热至一定温度后进行锻造成型,这个过程需要采用先进的锻造设备和技术。
通过锻造,可以使曲轴的内部组织密实,提高其抗疲劳性能。
然后是粗加工和精密加工。
曲轴经过锻造后,还需要进行车削、铣削、磨削等精密加工工艺,以达到设计要求的尺寸和表面粗糙度。
这个过程需要精密的加工设备和技术,确保曲轴的精度和表面质量。
最后是热处理。
曲轴在经过各种加工后需要进行热处理,通过淬火、回火等热处理工艺,改善曲轴的材料性能,提高其硬度和强度。
除了以上主要的工艺流程外,还需要进行质量检测、表面处理和装配等工序。
只有经过严格的工艺流程和严格的质量控制,
制造出来的曲轴才能保证其工作性能和可靠性。
总的来说,曲轴的制造工艺流程非常复杂,需要经过多道工序和严格的要求。
只有采用先进的工艺设备和技术,严格控制每一个工艺参数,才能制造出高质量的曲轴产品。
曲轴工艺流程

曲轴工艺流程曲轴是内燃机的重要部件,其工艺流程直接影响着曲轴的质量和性能。
下面将从原材料选材、加工工艺、热处理工艺以及检测工艺等方面,介绍曲轴的工艺流程。
首先,原材料选材。
曲轴的主要原材料为钢铁,通常采用优质碳素结构钢或合金结构钢。
在选材时,需要考虑钢材的化学成分、机械性能、热处理性能等因素,以确保曲轴具有足够的强度和韧性。
其次,加工工艺。
曲轴的加工工艺主要包括锻造、粗加工、精加工和平衡加工等环节。
在锻造过程中,通过热加工使原材料形成所需的曲轴形状,并提高其内部组织的致密性和均匀性。
粗加工和精加工则是通过车、铣、刨、磨等机械加工方法,将锻造好的曲轴进行尺寸精度和表面粗糙度的加工,以满足设计要求。
平衡加工则是为了保证曲轴在高速旋转时的平衡性能,通常采用钻孔、切削等方法进行。
接下来是热处理工艺。
曲轴经过加工后需要进行热处理,以改善其组织结构和性能。
热处理工艺主要包括调质、表面强化和表面渗碳等。
调质是通过加热和淬火等方法,使曲轴获得适当的硬度和强度。
表面强化则是通过表面喷丸、镀层等方法,提高曲轴的表面硬度和耐磨性。
表面渗碳则是将碳元素渗入曲轴表面,形成一层高碳含量的渗层,以提高曲轴的表面硬度和疲劳强度。
最后是检测工艺。
曲轴在完成加工和热处理后,需要进行严格的检测,以确保其质量符合要求。
检测工艺主要包括尺寸检测、力学性能检测、表面质量检测和非破坏检测等。
尺寸检测是通过测量仪器对曲轴的尺寸进行检测,以确保其尺寸精度符合设计要求。
力学性能检测则是通过拉伸、冲击等试验,检测曲轴的强度、韧性等力学性能。
表面质量检测主要是检测曲轴表面的硬度、粗糙度等指标。
非破坏检测则是采用超声波、磁粉、射线等方法,对曲轴进行内部缺陷的检测。
综上所述,曲轴的工艺流程包括原材料选材、加工工艺、热处理工艺和检测工艺等环节。
每个环节都对曲轴的质量和性能起着至关重要的作用,只有严格控制每个环节,才能保证曲轴具有优良的性能和可靠的质量。
曲轴加工工艺流程
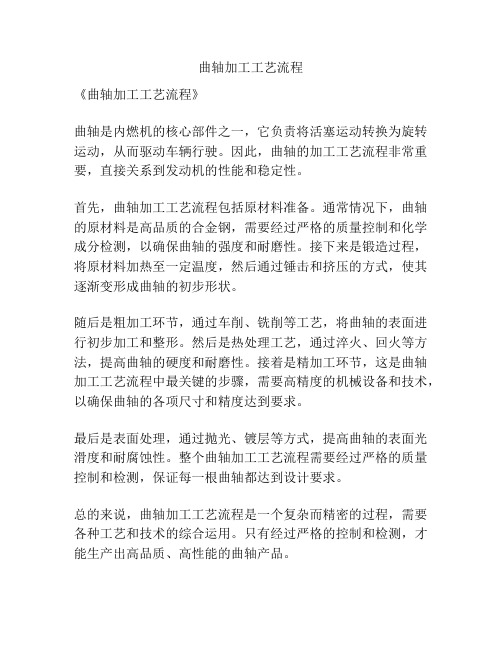
曲轴加工工艺流程
《曲轴加工工艺流程》
曲轴是内燃机的核心部件之一,它负责将活塞运动转换为旋转运动,从而驱动车辆行驶。
因此,曲轴的加工工艺流程非常重要,直接关系到发动机的性能和稳定性。
首先,曲轴加工工艺流程包括原材料准备。
通常情况下,曲轴的原材料是高品质的合金钢,需要经过严格的质量控制和化学成分检测,以确保曲轴的强度和耐磨性。
接下来是锻造过程,将原材料加热至一定温度,然后通过锤击和挤压的方式,使其逐渐变形成曲轴的初步形状。
随后是粗加工环节,通过车削、铣削等工艺,将曲轴的表面进行初步加工和整形。
然后是热处理工艺,通过淬火、回火等方法,提高曲轴的硬度和耐磨性。
接着是精加工环节,这是曲轴加工工艺流程中最关键的步骤,需要高精度的机械设备和技术,以确保曲轴的各项尺寸和精度达到要求。
最后是表面处理,通过抛光、镀层等方式,提高曲轴的表面光滑度和耐腐蚀性。
整个曲轴加工工艺流程需要经过严格的质量控制和检测,保证每一根曲轴都达到设计要求。
总的来说,曲轴加工工艺流程是一个复杂而精密的过程,需要各种工艺和技术的综合运用。
只有经过严格的控制和检测,才能生产出高品质、高性能的曲轴产品。
曲轴工艺技术报告

曲轴工艺技术报告曲轴工艺技术报告一、引言曲轴是内燃机的关键零部件之一,其工艺技术的优劣直接影响整个内燃机的性能和寿命。
本报告旨在介绍曲轴的工艺技术,并分析其在内燃机领域的应用。
二、曲轴的制造工艺1. 材料选择:曲轴通常由高强度合金钢制成,具有较高的耐磨性和耐腐蚀性。
常用的材料有40Cr、35CrMo等。
2. 热处理:热处理是曲轴工艺技术中的关键步骤,其目的是提高曲轴的硬度和强度。
常用的热处理方法有淬火、回火等。
3. 粗车:粗车是将预制材料进行毛坯成形的过程。
粗车过程中需要注意保证曲轴的圆度和平行度,以确保其后续加工准确度。
4. 精车:精车是将粗车过程中遗留的余量进行去除的工序。
精车过程需要控制加工精度,保证曲轴的几何尺寸和表面质量。
5. 平衡:曲轴是旋转部件,因此必须进行平衡处理。
平衡通过在曲轴上加装铅块或进行动平衡测试来完成,以减少振动和噪音。
三、曲轴工艺技术在内燃机中的应用曲轴是内燃机的核心部件之一,其工艺技术的优劣直接影响内燃机的性能和寿命。
以下将介绍曲轴工艺技术在内燃机中的应用。
1. 优化设计:通过优化曲轴的设计,可以使得内燃机的重量和运动惯量减小,进而提高内燃机的动力性能和燃油经济性。
2. 确保可靠性:通过精确的加工和严格的检测,可以保证曲轴的尺寸和形状的准确度,从而确保内燃机的运转平稳可靠。
3. 提高燃烧效率:通过改变曲轴的几何形状和重量分布,可以改变内燃机的气门正时,从而达到提高燃烧效率的目的。
4. 降低振动和噪音:通过平衡处理,可以减少曲轴的不平衡质量,降低内燃机的振动和噪音,提高其舒适性和使用寿命。
四、结论曲轴工艺技术是内燃机制造中不可或缺的一部分,它直接影响着内燃机的性能和寿命。
通过优化设计、精确加工和严格质量检测,可以提高曲轴的可靠性和工作效率。
曲轴工艺技术的不断发展,将为内燃机的进一步提高提供更多可能。
五、参考文献1. 李明. 内燃机曲轴的制造工艺[J]. 科技信息, 2020(15): 134-136.2. 张辉, 钟宝玉. 曲轴精加工技术的研究进展[J]. 计量与测试技术与装备, 2019, 7(4): 53-57.3. 赵斌. 曲轴磨削加工技术研究[J]. 特种加工技术, 2020, 46(12): 78-80.以上所述,是关于曲轴工艺技术的一份报告。
曲轴生产工艺流程
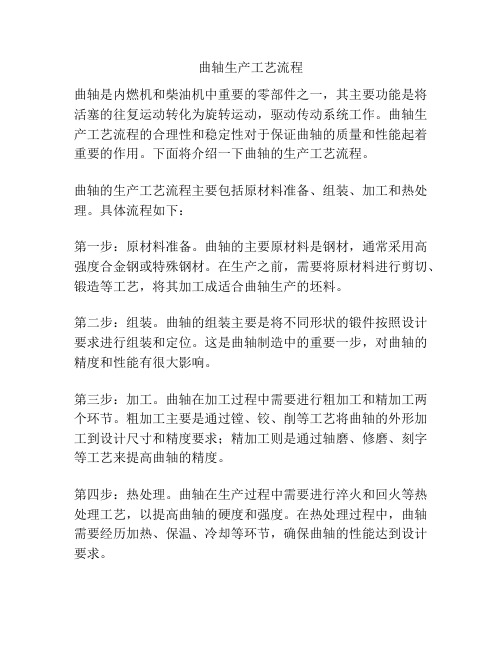
曲轴生产工艺流程
曲轴是内燃机和柴油机中重要的零部件之一,其主要功能是将活塞的往复运动转化为旋转运动,驱动传动系统工作。
曲轴生产工艺流程的合理性和稳定性对于保证曲轴的质量和性能起着重要的作用。
下面将介绍一下曲轴的生产工艺流程。
曲轴的生产工艺流程主要包括原材料准备、组装、加工和热处理。
具体流程如下:
第一步:原材料准备。
曲轴的主要原材料是钢材,通常采用高强度合金钢或特殊钢材。
在生产之前,需要将原材料进行剪切、锻造等工艺,将其加工成适合曲轴生产的坯料。
第二步:组装。
曲轴的组装主要是将不同形状的锻件按照设计要求进行组装和定位。
这是曲轴制造中的重要一步,对曲轴的精度和性能有很大影响。
第三步:加工。
曲轴在加工过程中需要进行粗加工和精加工两个环节。
粗加工主要是通过镗、铰、削等工艺将曲轴的外形加工到设计尺寸和精度要求;精加工则是通过轴磨、修磨、刻字等工艺来提高曲轴的精度。
第四步:热处理。
曲轴在生产过程中需要进行淬火和回火等热处理工艺,以提高曲轴的硬度和强度。
在热处理过程中,曲轴需要经历加热、保温、冷却等环节,确保曲轴的性能达到设计要求。
第五步:检测和质量控制。
曲轴生产完成后需要进行各项质量检测,确保曲轴的尺寸、硬度、表面质量等符合标准要求。
如果出现不合格品,需要及时进行返修或淘汰处理。
以上就是曲轴生产工艺流程的简要介绍。
在实际生产中,每个步骤都需要严格控制和把握,确保曲轴的质量和性能。
随着科技的发展和生产技术的提高,曲轴生产工艺也在不断的创新和改进,以适应不同类型发动机的需求和要求。
曲轴加工工艺流程简述
曲轴加工工艺流程简述曲轴加工工艺流程是通过多道工序将原材料加工成形成曲轴的过程。
其主要工艺流程包括以下几个步骤:第一步,材料准备。
选择合适的原材料,一般为低碳合金钢或铸铁材料。
对原材料进行切割,将其切成合适的长度,然后进行表面处理,去除可能存在的铁锈或脏物,以保证后续工序的顺利进行。
第二步,粗车粗磨。
使用车床进行粗车粗磨,首先进行车磨一体加工,即在车床上使用刀具对原材料进行粗加工,使其形状初步接近设计要求。
然后进行粗磨,使用砂轮或砂带对曲轴进行磨削,去除车削过程中产生的毛刺和毛毡。
第三步,精车精磨。
经过粗车粗磨后,曲轴形状已经基本接近设计要求,但还存在一些误差和粗糙度。
因此,需要进行精车精磨,使用车床和磨床对曲轴进行精加工,使其形状更加精确,表面更加光滑。
第四步,热处理。
经过精车精磨后,曲轴已经获得一定的硬度和强度,但仍需要通过热处理进一步提高其性能。
通常采用淬火、回火等热处理工艺,对曲轴进行热处理,使其获得所需的硬度和韧性。
第五步,平衡。
在加工过程中,曲轴往往会出现一定的不平衡。
为了保证曲轴在运行时具有良好的平衡性能,需要对曲轴进行动态平衡调整。
通常采用切削平衡、钻孔平衡或添加平衡铁等方法,使曲轴在高速旋转时不产生明显的振动和不平衡力。
第六步,表面处理。
曲轴作为发动机等设备的核心部件,其表面需要进行一定的处理,以提高其耐磨性和防腐性。
常见的表面处理方法包括镀铬、喷涂等。
镀铬可以提高曲轴表面的硬度和耐磨性,喷涂可以形成一层保护膜,防止曲轴被腐蚀和氧化。
第七步,终检和包装。
经过以上工艺流程后,曲轴已经完成了加工过程,但为了确保其质量,需要进行终检。
终检包括对曲轴进行尺寸测量、外观检查、性能测试等各项检验。
通过终检合格后,将曲轴进行包装,以便运输和存储。
以上就是曲轴加工工艺流程的简单描述。
当然,实际的加工过程还会因具体的工艺要求、设备和加工对象的不同而有所差异。
曲轴工艺流程
曲轴工艺流程
《曲轴工艺流程》
曲轴是发动机中的重要部件,它通过连杆与活塞相连,将活塞运动转换成旋转运动,从而驱动发动机运转。
曲轴的制造工艺流程十分复杂,需要经过多道工序和精密加工才能完成。
下面将介绍曲轴的工艺流程。
首先,曲轴的制造通常采用大型机床进行加工,因此首先需要将原材料进行切割和锻造。
锻造后的原材料需要进行精密加工,以确保曲轴的几何尺寸和表面粗糙度符合设计要求。
接下来就是车削和磨削工序,这一步是最为关键的,需要高精度的加工,以达到曲轴的精密度要求。
在车削和磨削过程中,需要对曲轴进行多次的定位和检测,确保每个工序的加工精度达标。
随后,曲轴需要进行动平衡加工,以确保曲轴在运转时不会产生过大的振动,这对发动机的工作效率和寿命至关重要。
动平衡加工需要在专门的设备上进行,对曲轴的各个部位进行精密加工和加重减重,调整使其达到动平衡状态。
最后,曲轴的表面需要进行表面处理,以提高其耐磨性和耐腐蚀性能。
整个曲轴的制造工艺流程需要经过多道工序,每一道工序都需要非常严格的质量控制和精密加工。
只有这样才能保证曲轴的性能和可靠性达到设计要求。
曲轴作为发动机的关键部件,其制造工艺也在不断的进行技术革新,以满足对曲轴更高性能和更高可靠性的要求。
曲轴加工方法
曲轴加工方法一、曲轴的概述曲轴是内燃机中的重要零件之一,它承受着往复运动的连杆和活塞的动力,并将其转化为旋转运动。
曲轴的加工方法直接影响着其质量和寿命。
二、传统曲轴加工方法1. 曲轴加工工艺流程•材料准备•粗加工•精加工•热处理•精磨•组装2. 曲轴粗加工方法曲轴的粗加工包括车削和摇床加工,主要用于加工曲轴的外形和主要轴颈。
3. 曲轴精加工方法精加工是曲轴加工工艺中的关键环节,包括如下几个步骤: - 精磨轴颈:通过磨削去除粗加工时留下的余量,获得更为精确的尺寸和光洁的表面; - 激光熔覆:采用激光技术对曲轴进行表面强化处理,提高其耐磨性和抗疲劳性能; - 平衡加工:通过调整轴颈上的质量来消除曲轴的不平衡,提高其运转平稳性; - 镀铬:在轴颈表面电镀一层铬,增加其硬度和耐磨性。
4. 曲轴热处理方法曲轴通常采用淬火和回火的热处理方法,以提高其强度和硬度。
在淬火过程中,曲轴被迅速冷却,使其表层形成硬脆的组织,然后通过回火来减轻内应力,增加韧性。
5. 曲轴精磨方法曲轴的精磨是对其表面进行加工处理,以提高其光洁度和尺寸精度。
常用的曲轴精磨方法包括外圆磨削、曲轴轴颈磨削等。
三、现代曲轴加工方法1. 数控加工技术在曲轴加工中的应用数控加工技术在曲轴加工中得到了广泛应用,它可以实现曲轴的高效、精确加工。
数控加工中常用的方法包括数控车削、数控磨削等。
2. 先进的加工设备和工艺现代曲轴加工中,广泛采用高速和超精密磨床、石英化处理机床等先进设备,以及先进的加工工艺,如砂带磨削、电火花加工等,从而提高加工效率和加工质量。
3. 新材料的应用新材料的应用也在一定程度上改变了曲轴的加工方法。
如钛合金曲轴的加工对设备和工艺都提出了更高的要求,但其具有更好的机械性能和抗腐蚀性能。
四、未来的曲轴加工趋势1. 智能化加工随着人工智能技术的快速发展,曲轴加工将实现更高水平的智能化。
例如,通过自动化控制系统实现曲轴的全自动加工和检测。
2. 高效加工随着制造业的发展和对产品质量要求的提高,曲轴的高效加工将成为一个重要的趋势。
曲轴生产工艺流程介绍
曲轴生产工艺流程介绍
曲轴是一种重要的发动机零件,用于将往复运动转换为旋转运动。
下面是曲轴的生产工艺流程介绍:
1. 制定工艺方案:根据设计要求和技术要求,确定曲轴的工艺方案和加工工艺参数。
2. 材料准备:选择合适的材料,通常选用高强度合金钢作为曲轴的材料。
然后进行材料的加热处理,如锻造、淬火等,以提高材料的强度和硬度。
3. 锻造:将材料加热到一定温度,然后放入锻造机械中进行冲击锻造,使材料形成初步的曲轴形状。
锻造过程中需要控制温度和力度,以确保曲轴的形状和尺寸。
4. 粗加工:对锻造后的曲轴进行粗加工,主要包括车削、铣削、钻孔等工艺,以去除表面的毛刺和余量,形成初步的曲轴轮廓。
5. 精加工:对粗加工后的曲轴进行精加工,主要包括磨削、镗削、高频淬火等工艺。
磨削工序是对曲轴进行精度修整,以保证曲轴的公差和表面质量;镗削工序是对曲轴孔径进行加工,以保证曲轴与其他配合零件的配合精度;高频淬火是对曲轴进行表面硬化处理,以提高曲轴的耐磨性能。
6. 检测和质量控制:对生产的曲轴进行检测和质量控制,包括尺寸测量、硬度检测、力学性能测试等。
只有符合设计要求和技术要求的曲轴才能进入下一道工序或出厂销售。
7. 表面处理:对曲轴进行表面处理,主要包括除锈、防腐涂层、涂油等工艺,以延长曲轴的使用寿命和提高其外观质量。
8. 组装和测试:将曲轴与其他发动机零件进行组装,然后进行测试。
测试包括静态测试和动态测试,以确保曲轴的正常运转和安全性能。
以上是曲轴的生产工艺流程介绍,不同厂家和不同型号的曲轴可能会有所差异。
- 1、下载文档前请自行甄别文档内容的完整性,平台不提供额外的编辑、内容补充、找答案等附加服务。
- 2、"仅部分预览"的文档,不可在线预览部分如存在完整性等问题,可反馈申请退款(可完整预览的文档不适用该条件!)。
- 3、如文档侵犯您的权益,请联系客服反馈,我们会尽快为您处理(人工客服工作时间:9:00-18:30)。
曲轴介绍及其工艺流程 WEIHUA system office room 【WEIHUA 16H-WEIHUA WEIHUA8Q8-
曲轴介绍及其工艺流程
曲轴一般由主轴颈,连杆轴颈、曲柄、平衡块、前端和后端等组成。
一个主轴颈、一个连杆轴颈和一个曲柄组成了一个曲拐,曲轴的曲拐数目等于气缸数(直列式发动机);V型发动机曲轴的曲拐数等于气缸数的一半。
主轴颈是曲轴的支承部分,通过主轴承支承在曲轴箱的主轴承座中。
主轴承的数目不仅与发动机气缸数目有关,还取决于曲轴的支承方式。
曲轴的支承方式一般有两种,一种是全支承曲轴,另一种是非全支承曲轴。
曲轴的形状和曲拐相对位置(即曲拐的
布置)取决于气缸数、气缸排列和发动机的发火顺序。
曲轴的作用:它与连杆配合将作用在活塞上的气体压力变为旋转的动力,传给底盘的传动机构。
同时,驱动配气机构和其它辅助装置,如风扇、水泵、发电机等。
工作时,曲轴承受气体压力,惯性力及惯性力矩的作用,受力大而且受力复杂,并且承受交变负荷的冲击作用。
同时,曲轴又是高速旋转件,因此,要求曲轴具有足够的刚度和强度,具有良好的承受冲击载荷的能力。
曲轴加工材料与毛胚:
曲轴毛坯的制造方法有锻造和铸造两种。
曲轴采用的材料有45钢、45Mn2和40Cr等。
锻造钢件毛坯有好的耐磨性,可得到有利的纤维组织,可获得最佳的截面模量和紧密的细晶粒相组织。
曲轴铸件一般是球墨铸铁,球墨铸铁曲轴铸造工艺好,有利于获得较合理的结构形式,在大批量生产中可采用精密铸造,其机械性能以接近一般中碳钢,切削性能好,耐磨性高。
发动机曲轴工艺流程:
1、粗车第四主轴颈
2、粗磨第四主轴颈
3、粗车其余主轴颈、两端面
4、精车1、3、4、6主轴颈及小端面
5、精车2、5、7主轴颈及大端面
6、在后端面打零件号
7、铣削加工6个连杆颈
8、在后端面上铰第一个孔
9、2、7主轴颈上钻直油孔
10、连杆颈上钻斜油孔,油孔倒角去毛刺
11、零件中间清洗
12、表面淬火
13、回火并热校直
14、表面喷丸处理
15、修正两端面中心孔
16、后端面铰第二工艺孔
17、半精磨1、7主轴颈
18、精车第六主轴颈端面
19、精磨6连杆颈
20、精磨2、4、7主轴颈,在精磨3、4主轴颈,在精磨第六主轴颈,最后斜砂轮磨主轴颈,第一齿轮前封油
21、精磨后油封端面
22、精车皮带轮轴颈和端面
23、油孔倒角去毛刺抛光
24、钻前后端面螺纹底孔
25、螺纹倒角攻丝
26、齿轮轴颈上钻铰
27、零件动平衡
28、砂带表面精抛光
29、最终清洗
30、终检
31、防锈包装
加工备注:
1、粗磨第4主轴颈时,用中心孔作为定位。
2、粗磨其它主轴颈时,用第4主轴颈定位,用顶尖顶住两中心孔。
3、精车主轴颈时,应先加工1、2、
4、6主轴颈和前油封主轴颈,然后再加工3、4、7主轴颈及后油封。
5、铣削六个连杆颈时,应卡紧1、7主轴颈和两个中心孔。
第1工艺孔起角度定位作用。
6、钻直油孔时,夹紧1、7主轴颈,用第1工艺孔进行角度定位。
7、钻斜油孔时,使用斜60°的卡具,其定位方式与主轴颈的定位方式相同。
油孔口倒角、去毛刺是防止热加工时产生裂纹。
8、淬火热处理时,应现对主轴颈进行淬火,再对连杆颈进行淬火,每次只能加工一个颈,淬火层要求有3至5mm,硬度需要达到55HRC。
9、回火时,回火温度要在260°~310°之间,回火主要是为了去应力。
10、喷丸处理的“丸”是一种小钢砂,喷丸可以起到清除表面氧化层和防锈的作用。
11、半精磨1、7主轴颈时,用中心孔进行加工定位。
第6主轴颈是轴向定位基准。
12、对所有油封口倒角、抛光是防止装配时拉伤轴瓦。
荧光磁粉表面探伤是探测表面裂纹。