Moldflow_MPI在注射模具优化设计中的应用
Moldflow在注塑成型模拟分析中的应用
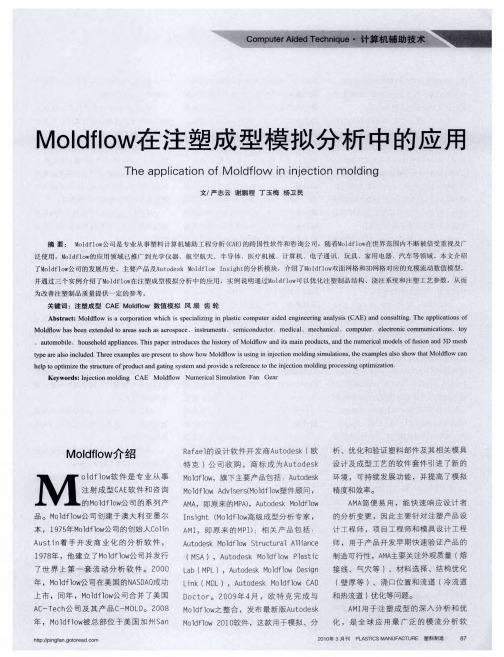
( MS A )
La b Li
n c
Au t
,
o
de
o
s
k
Mo l d f l o w
Pla s t i c
制造 可 行性
A MA 主 要 关 注 外 观 质 量 (
、
熔
( MP L )
Au t
,
d e s k Mo l d f l o w
o
De s i g n CAD
接线
、
气穴等 )
、
材料选 择
m e
d ic
m a
l
、
m e c
ha
ic
,
l
、
p
u te r
、
le
c tr o n
c o m m u n
ic a t i o
an
n s
、
to y
a u to m o
b ile ls
o
ho
c
u s e
h o ld
.
p p lia
e
n c e s
.
T h is p a p e
r
in tr o d u
s
o
s
ho
th a t M o
o w
c a n
h e lp t o
K
p t im
o r
e
tru
c
tu
r e
o
f pr o du
d g m in g
M
o
s
y
te m
d pr o
ic
a
v
a
fe
n
r e n c e
MoldFlow软件在特殊注塑成型中的应用

MoldFlow软件在特殊注塑成型中的应用MoldFlow软件在特殊注塑成型中的应用作者:文劲松麻向军来源:PT现代塑料一前言MPI3.1除了能对传统的注塑成型进行模拟分析外,还能对一些特殊的注塑成型过程进行模拟分析,如共注塑成型(Co-injection Molding)、压注成型(Injection-Compression Molding)、反应注塑成型(Reaction Injection Molding)、微芯片封装(Microchip Encapsulation)、气体辅助注塑成型(Gas-Assisted Injection Molding),其中,气体辅助注塑成型将有专门的文章进行介绍,下面讨论其它的注塑成型模拟分析。
二共注塑成型模拟分析共注塑成型是指用两个或两个以上注塑单元的注塑成型机,将不同的品种或不同色泽的塑料,同时或先后注入模具内的成型方法,可生产多种色彩或多种塑料的复合制品。
MPI/Co-Injection可以模拟先后注射成型过程。
一般用于共注塑的注塑机有两个料筒和一个公用的喷嘴。
制品表面的塑料首先注射,由于喷泉效应,塑料熔体喷射到模腔壁,模壁的温度远低于熔体的凝固温度,熔体迅速凝固,形成绝缘层,新的熔体沿着模壁流动,直到覆盖整个模腔表面。
随后注射制品内部的塑料,最后再次注射表面塑料。
在共注塑过程中,有两个很难控制的工艺参数:1)两种塑料的最优混合比例。
理论上,制品内部塑料最大可占到制品体积的百分之六十七,但实际上很难到达,尤其是复杂制品,工程上内部塑料可达到制品体积的百分之三十。
2)两种塑料注射转换的时间控制点。
由于模具设计不合理或者两种塑料比例不合适,有可能使内部塑料露出表面,尤其是最后填充的地方。
MPI/Co-Injection根据两种注射塑料的特性,预测它们在模腔中的分布,并给出两种塑料的最佳混合比例以及注射时间控制点,分析结果包括:1)两种塑料在填充过程中,模腔中任一点在任一时间的体积百分比。
MoldFlow软件在注射模设计教学中的应用

打开 “ 文件 ” 菜单 , 选择 “ 导入 ” 命令 , 在弹 出的对
工程( C A E ) 软件 , 作为世界上第一套塑料注射成型流 话 框 中选 定 要 导 入 的对 象 文 件 , 确认导人 , 导 人 后 的 动分析 软件 的发行 者 , 一直主导塑料成型 C A E 软件市 模 型 如 图 1 所示 , 通 过 Mo l d F l o w的 多项 视 图及 动 态 视
Ke y w o r d s : Mo l d F l o w ; i n j e c t i o n mo l d d e s i g n ; t e a o l d F l o w 具有强大的数值计算 、 可视化前后处理
可对塑件的整个成型过程进行 注 射 模 设 计 课 程 是 针 对 材 料 成 型 及 控 制 工 程 专 和用户项 目管理功能 ,
a n d a n i ma t i o n b y t h e a p p l i c a t i o n o f t h e mo l d l f o w s o f t w a r e , wh i c h c a n ma k e t h e t h e o r y t e a c h i n g mo r e v i v i d , s t i mu l a t e s t u d e n t s l e a r n i n g i n t e r e s t , g r e a t l y i mp r o v e t h e q u a l i t y o f c l a s s r o o m t e a c h i n g .
p l a s t i c mo u l d a s a n e x a mp l e , t h e w h o l e i n j e c t i o n mo l d i n g p r o c e s s w a s s h o w n i n t h e f o r m o f c l o u d
MoldFlow在连接器注射模设计中的应用
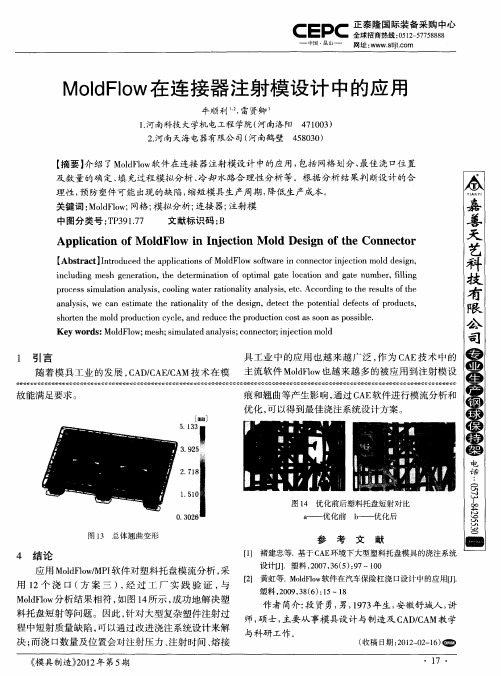
[】 褚建 忠等 . 于 C E环境下大型塑料托盘模具 的浇注系统 1 基 A 设计I】 J.塑料 ,0 7 3 ( )9 ~10 2 0 ,6 5 :7 0 [] 黄虹等 . lFo 2 Mod l w软件在 汽车保 险杠浇 口设计 中的应用[
塑料 ,0 9 3 ( ) 1 1 2 0 ,8 6 :5 8
i c u i g me h g n r to , h e e mi a in o p i lg t o ai n a d g t u e , l n n l d n s e e a in t e d t r n t f o t o ma ae l c t n ae n mb r f l g o i i p o e ssmu a i n a a y i, o l g wae a i n l y a a y i, t . c r i gt er s l f h r c s i l t n l ss c o i t rr t a i n l ss e c Ac o d n t e u t o e o n o t o h s t a ay i , a si t h ai n l y o e d sg ,d t c h o e t ld f cs o r d c s n l s s we c n e t mae t e r t ai ft e i n e e tt e p t n i e e t fp o u t, o t h a
【 摘要】 绍 了M lF w 介 o l 软件在连接 器注射模设计 中的应 用, do 包括 网格划分 、 最佳浇 口位置
及数量的确定、 填充过程模拟分析 、 冷却 水路合 理性分析等 。根据分析 结果判断设计 的合 理 性 , 防 塑件 可 能 出现 的缺 陷 , 短模 具 生 产 周期 , 预 缩 降低 生产 成 本 。
MoldFlow在注塑成型中的应用

MoldFlow在注塑成型中的应用作者:广西大学机械工程学院汤宏群苏广才摘要:利用MoldFlow对星型注塑件不同浇口位置进行流动模拟分析,预测可能存在的气泡位置和熔接痕位置,确定最佳浇口位置和数目。
以此为例说明MoldFlow在注塑成型中应用的好处。
关键词:MoldFlow;模拟分析;最佳浇口位置中传统的注射模设计主要依靠设计人员的直觉和经验,模具设计加工完后往往需要经过反复地调试与修正才能正式投入生产,发现问题后,不仅要重新调整工艺参数,甚至要修改塑料制品和模具,这种生产方式降低了新产品的开发速度。
而利用Moldflow软件在模具加工之前,在计算机上对整个注塑成形进行模拟分析,可以进行填充、保压、冷却、翘曲、纤维取向、结构应力、收缩以及气辅成形等分析,找出可能出现的缺陷,提高一次试模的成功率,降低生产成本,缩短生产周期。
本文主要介绍使用MOLD-FLOW模拟分析软件对星型注塑件不同浇口位置进行流动模拟分析,预测可能存在的气泡位置和预测熔接痕的位置,确定最佳浇口位置和数目。
为模具设计人员进行模具设计提供依据。
1模拟分析过程1.1分析模型的建立图图1为该零件的三维实体模型,由实体模型建立的该注塑件的有限元分析模型如图2所示,在分析中采用中性面网格,有限元分析模型数据为:面单元数-1547,节点数-821。
1.2浇口位置的确定及流动分析本文分别采用一个浇口和两个浇口进行分析比较:方案1一个浇口居中(如图3所示),方案2两个浇口居左右两侧(如图4所示),塑件所用材料为DUPONT,相关参数为:塑料熔融温度-215.00℃;模具温度-90.00℃。
2. 流动模拟分析结果比较2. 1不同浇口位置产生的气泡在塑料熔体注射充填过程中,模腔内除了原有空气外,还有塑料含有的水分在注射温度下蒸发而成的水蒸气,塑料局部过热分解产生的低分子挥发性气体等。
这些气体若不能通过排气系统顺利排出模腔,将会影响制品成型以及脱模后的质量。
Moldflow在注塑成型工艺优化中的应用

2.Moldflow 充模流动数学模型
Moldflow 提供三种网格类型对制品模型进行网格划分: (1)Midplane(中性面网格) 针对薄壳件产品分析,需抽取中间面; (2)Fusion(双面网格)针对薄壳件产品分析,将需 要数天抽取中间面的时间缩短为几分钟,是应用最广泛的网格类型。 (3)3D(实体三维网 格) ,可适用于所有类型产品,包括薄壳或厚壁件。 中性面网格和双面网格充模流动数学模型采用非牛顿流体在非等温下的广义 Hele-Shaw 流动的控制方程为[4]: 连续性方程
D1 是剪切变稀行为开始的剪应力,D2 为对应低压下的玻璃化转
D3 为压力影响系数,表征粘度对压力的依赖性,在高速高压成型分析中,比如超 A1 、 A2 为模型常数; T 为一个参考温度,通常被认
薄成型,必须考虑粘度的压力依赖性。
为是材料的玻璃化转变温度。 Cross-WLF 模型考虑的是剪切粘度, 不考虑拉压粘度。 在浇口直径变化较剧烈的情况下 往往会有较明显的拉压粘度效应, 造成更大的压力损失, 此时需要考虑 Juncture loss 的 Bagley 修正系数 C1 和 C2 (采用 3D 求解器考虑 Extension viscosity 模型系数 A 和 B) 。 如 Moldflow 未提供修正系数,可在 Moldflow 帮助中查找经验数据进行修正。如果分析时不考虑拉压粘 度影响,分析的注射压力则偏低,锁模力可能会偏大。
能量方程
(6)
(7)
(8)
C p
T T T T T T T ) (k ) (k ) 2 C p (u v w ) (k t x y z x x y y z z
(9)
其中 为熔体密度, x 、 y 、 z 为三维坐标, u 、 v 、 w 分别表示 x 、 y 、 z 方向的速 度, P 为压力, T 为温度,
Moldflow/IMoLD技术在注塑模设计中的应用

Moldflow/IMoLD技术在注塑模设计中的应用0 引言传统塑料模具设计往往是由设计人员凭经验与直觉设计模具,待模具制造、装配完毕通过试模后,才能发现问题。
运用Moldflow/IMOLD技术进行塑料模具设计,可以避免设计中的盲目性。
通过计算机的模拟,有目的地修正设计方案和工艺条件,克服因为经验少而造成的不良后果,缩短产品开发周期,提高生产效率。
1 Moldflow软件简介Moldflow是一款具有强大功能的专业注塑成型CAE软件,目前被广泛应用予注塑成型领域中的模拟分析。
Motdflow软件包括三部分:(1)Moldflow Plastics Advisers(产品优化顾问,简称MPA):塑料产品设计人员在设计完产品后,运用MPA软件模拟分析,在很短的时间内,就可以得到优化的产品设计方案,并确认产品表面质量。
(2)Moldflow Plastics Insight(注塑成型模拟分析,简称MPI):对塑料产品和模具进行深入分析的软件包,它可以在计算机上对整个注塑过程进行模拟分析,包括填充、保压、冷却、翘曲、纤维取向、结构应力和收缩,以及气体辅助成型分析等,使模具设计人员在设计阶段就找出未来产品可能出现的缺陷,提高一次试模的成功率。
(3)Moldflow Plastics Xpert(注塑成型过程控制专家,简称MPX):集软硬件为一体的注塑成型品质控制专家,可以直接与注塑机控制器相连,可进行工艺优化和质量监控,自动化注塑周期、降低废品率及监控整个生产过程。
2 IMOLD软件简介IMOLD是SolidWorks环境下进行注塑模三维设计的插件。
IMOLD主要的功能模块有:(1)数据准备:在模具设计前分析产品的造型,以便为后续设计提供合乎要求的三维模型。
(2)项目管理:对模具设计项目进行文档管理,可以输入特别的塑料原料及收缩率,并可以根据加工条件选择X、Y、Z3个不同方向的收缩率来设计模具。
(3)型芯、型腔设计:用于设计出型腔、型芯、侧面型芯。
Moldflow Plastics Insight (MPI)

基于Moldflow Plastics Insight (MPI) 的CAE模流分析结果,可以在模具设计、制造之前对塑胶产品设计、模具设计和注塑成型工艺设定方案进行验证和优化,避免潜在的问题;同时对不能生产合格产品的模具进优化获得高质量产品,以达到降低成本之目的。
1.注射压力注塑压力是指注塑机螺杆在注塑过程中施加于料筒中溶胶上单位面积的力。
注塑压力在一定程度上决定充模速率,并影响产品的质量。
改变注塑压力可改变溶胶的流动性,从而改变产品密度、收缩率、结合线强度。
但是注塑压力过高,容易使产品内应力增加。
2.注塑时间注塑时间是指完成一次注塑所需的时间,它包含充模时间和保压时间。
在生产过程中,一般充模时间不超过10秒钟。
3.锁模力锁模力是指注塑机的锁模系统对模具所能施加的最大锁紧力。
在注塑充填和保压阶段,型腔压力会产生使模具分开的膨胀力,锁模力用以克服这种膨胀力,保证在注塑成型过程中模具不被射压撑开而产生溢料。
4.冷却时间冷却时间主要取决于塑料产品的壁厚、模具的温度、塑料的热性能和结晶性能。
冷却时间一般约为20~120s,冷却时间较短时很难达到理想的冷却效果。
冷却时间较长时,则会增加成型周期,有时还会造成产品脱模困难。
冷却时间的长短一般为不影响产品脱模时不引起变形为原则。
5.保压保压是由保压压力和保压时间两部分组成。
为什么保压?因为溶胶充满模具型腔后,通常还需要一定的保压时间,通过保压压力对型腔内的溶胶进行压实,补偿溶胶的冷却收缩,从而使生产出来的产品能够获得精确的形状。
生产中,保压压力一般为注塑压力的80%左右,。
足够的保压压力可以减少产品的收缩,并能够稳定产品的外形尺寸,可以弥补因保压不足而使产品出现的短射或收缩较大等缺陷,单保压压力过高时,容易造成脱模后的产品内应力大和脱模困难等问题。
保压时间对塑件最终的成型质量也有较直接的影响,足够的保压时间是使塑件得到良好保压的前提之一,当浇口凝固后,保压过程就没效果,因此保压时间最常应不超过浇口凝固时的时间。
- 1、下载文档前请自行甄别文档内容的完整性,平台不提供额外的编辑、内容补充、找答案等附加服务。
- 2、"仅部分预览"的文档,不可在线预览部分如存在完整性等问题,可反馈申请退款(可完整预览的文档不适用该条件!)。
- 3、如文档侵犯您的权益,请联系客服反馈,我们会尽快为您处理(人工客服工作时间:9:00-18:30)。
10Die and Mould Technology No.5 20050引言高质量的塑料模具与塑料性能、成型工艺和制品设计密切相关。
目前大多数设计人员设计模具时主要是依据自己的经验进行设计。
但由于塑料制品的多样性、复杂性和设计人员经验的局限性,长期以来,工程技术人员很难精确地设计出一套可减少成本、节省时间、提高产品的质量及合格率的最合理工艺方案。
往往是模具设计加工完以后需要不断地试模与修模才能正式投入生产,有些模具由于无法修复而报废。
CAD/CAM在模具设计与制造中运用比较成熟,而要制造出高质量模具,仅仅依靠CAD/CAM是不够的,必须运用CAE技术,在计算机上对整个注塑成型过程进行模拟分析,依据塑料性能,优化成型工艺参数和制品结构。
现以某塑料厂生产的某玩具的一个零件为例,研究Moldflow在模具优化设计中的应用。
1塑料模具设计的关键技术[1 ̄2]1.1浇注系统的设计浇注系统是熔融塑料从注射机喷嘴到型腔的必经通道,它直接关系到成型的难易和制品的质量,是注射模设计中的重要组成部分。
它的作用是使熔融塑料平稳、有序地填充到型腔中去,且把压力充分地传递到各个部位,以获得组织致密、外形清晰、美观的制品。
浇注系统通常分为普通浇注系统和无流道浇注系统两大类。
其中普通浇注系统最为常用。
它由主流道、冷料井、分流道和浇口。
1.2模具温度调节系统的设计在注射成型过程中,模具的温度直接影响到收稿日期:2005-07-29作者简介:黄晨华(1972~),男,讲师。
文章编号:1001-4934(2005)05-0010-03Moldflow/MPI在注射模具优化设计中的应用黄晨华(韶关学院机电系,广东韶关512005)摘要:基于塑料模具设计的关键技术,介绍了Moldflow/MPI CAE解决方案,用实例详述了Moldflow/MPI在注射模具优化设计中的应用。
Moldflow/MPI分析结果与实践中采用的方案相似,说明了Moldflow/MPI在注射模具优化设计中结果的可靠性。
关键词:Moldflow;注射模具;优化设计中图分类号:TP391.72文献标识码:AAbstract: Based on the key technology of plastic injection mold design, the solution of Moldflow/MPI CAE is introduced.The application of Moldflow/MPI in optimizing the design of plasticinjection mold is elaborated with an instance.The results analyzed by Moldflow/MPI is similarto the solution in practice.It proves that the result of application of Moldflow/MPI in optimiz-ing the design of injection mold is reliable.Key words: Moldflow;injection mold;optimizing design模具技术2005.No.511塑件成型的质量和生产效率。
由于各种塑料的性能和成型工艺要求不同,模具的温度也要求不同。
对于任何塑料制品,模温波动较大都是不利的。
过高的模温会使制品在脱模后发生变形,延长冷却时间,使生产率下降。
过低的模温会降低塑料的流动性,难以充满型腔,增加制品的内应力和明显的溶接痕等缺陷。
1.3成型工艺参数的选择为顺利实现制订的塑料注射成型工艺,得到良好的塑料制品,成型工艺参数的选择是关键。
注射成型的主要工艺参数是温度、压力和时间。
注射成型工艺过程需要控制的温度有料筒温度、喷嘴温度和模具温度。
前两种温度主要影响塑料的塑化和流动,后一种温度主要影响塑料的流动和冷却定型。
注射成型过程中的压力包括塑化压力和注射压力。
增加塑化压力可以提高熔体温度和使温度均匀,但会减小塑化速率,延长成型周期,可能导致塑料降解。
在满足塑料制品质量的前提下,塑化压力低一点为好。
注射压力的作用是克服塑料熔体从料筒流向型腔的流动阻力,使熔体具有一定的充模速率并对熔体进行压实。
为了保证塑料制品的质量,对注射速率有一定的要求,而注射速率又主要取决于注射压力,注射压力高则注射速率高。
在满足塑料制品成型的前提下,一般应尽量采用低的注射压力。
完成一次注射成型过程所需的时间称为成型周期。
在整个成型周期中,注射时间和冷却时间是基本组成部分,注射时间和冷却时间的多少对塑料制品的质量有决定性影响。
2Moldflow/MPICAE解决方案[3]MPI是一个进行深入分析的软件包,用于确定最优的制件形状、材料选用、加工参数、制件和模具设计等。
MPI可以进行流动、冷却、翘曲、纤维取向、制件刚度和收缩、以及气辅和热固性材料流动分析等。
2.1填充分析填充分析计算出从注塑开始到模腔被填满整个过程中的流动前沿位置。
该分析用来预测制件、塑料材料以及相关工艺参数设置下的填充行为。
填充分析结果主要用于查看制件的填充行为是否合理,填充是否平衡,能否完成对制件的完全填充等。
用户可以根据动态的填充时间结果查看填充阶段的熔体流动行为,同时借助等高线显示结果,以便更好地判断填充流动行为是否合理。
填充分析的目的是为了获得最佳浇口位置、浇口数目、最佳浇注系统布局。
2.2流动分析流动分析用于预测热塑性高聚物在模具内的流动。
流动分析的目的是为了获得最佳保压阶段设置,从而尽可能地降低由保压引起的制品收缩、翘曲等质量缺陷。
2.3冷却分析冷却分析用来分析模具赔偿损失热传递。
冷却分析主要包含塑件和模具的温度、冷却时间等。
通过冷却分析结果判断制件冷却效果的优劣,根据冷却效果计算出冷却时间的长短,确定成型周期所用时间。
在获得均匀冷却的基础上优化冷却管道布局,尽量缩短冷却时间,从而缩短单个制品的成型周期,提高生产率,降低生产成本。
2.4翘曲分析翘曲分析用于判定采用热塑性材料成型的制件是否会出现翘曲,如果出现翘曲的话,查出导致翘曲产生的原因。
2.5浇口位置分析Moldflow中的优化分析可以根据模型几何以及相关材料参数、工艺参数分析出浇口最佳位置。
用户可以在设置浇口位置之前进行浇口位置分析,依据这个分析结果设置浇口位置,从而避免由于浇口位置设置不当可能引起的制件缺陷。
3设计实例以某塑料厂生产的某玩具的一个零件为例,详述Moldflow/MPI在模具优化设计中的应用。
制品的三维图如图1所示,该制品与其它制品有装配关系,因此对制品的变形要求较严格。
材料为PP。
该厂在生产该制品时进行了大量的试模,最后才找到合适的模具结构和成型工艺参数,现对制品在设计模具时采用Moldflow/MPI进行CAE分析。
3.2制件的填充—冷却—流动—翘曲分析按3.1分析所得结果,开设好浇注系统和冷却水道,设定好成型工艺条件,进行填充-冷却-流动-翘曲分析。
填充顺序和时间如图3所示,总的填充时间为7.989s。
3.1浇口位置分析在用Moldflow/MPI进行CAE分析时,一般是先进行浇口最佳位置分析,因为其它的分析都要求设置浇口位置。
制品的成型工艺条件为:模温60℃、熔体温度为200℃、开模时间5s,注塑保压冷却时间总和为30s,填充控制、速度/压力控制转换为自动设置,保压控制为填充压力与时间关系,采用默认值,浇口最佳位置分析结果如图2所示。
依据分析结果,结合浇口开设的可能性,可以确定模具的浇口位置。
这里考虑一模多腔,采用侧浇口。
制件的冷却方案和温度分布如图4所示,符合要求。
对制件进行流动分析,可以得到成型过程中非常重要的保压曲线,如图5所示,防止过保压。
制件的收缩率为1.476%~9.123%,制件的翘曲变形最小为0.0216mm,最大为0.0780mm,如图6所示。
变形在合理的范围内。
(下转第20页)势。
由于本套模具中受到结构空间的限制,弹簧复位既不能向外引出,又不能内置弹簧复位,所以最终采用了铰接形式的复位机构。
至于铰接片的设计,是在“自行车链条连接片”的结构启发和参照下设计出来的。
摆块的设计没有什么特别之处,只是需要指出的是摆块的旋转轴——心轴的直径为φ10mm,摆块与心轴为间隙配合。
摆块与铰接片是通过φ3mm的轴连接的。
如图7中的件9、件21。
5结束语由于制件的结构复杂,精度和质量要求较高,因此设计采用了复合模具。
经实践证明,本套模具保证了产品质量,提高了生产效率,从而有效地提高了生产效益。
参考文献:[1]王孝培.冲压手册[M].北京:机械工业出版社,2000.[2]梁炳文.钣金冲压工艺与窍门精选[M].北京:机械工业出版社,2001.[3]中国机械工程学会中国模具设计大典编委会.中国模具设计大典[M].江西:江西科学技术出版社,2003.[4]柏祝海,徐鹤翔,高志等.摆块式弯曲模设计[J].模具工业,2005,(2):20~25.在进行CAE分析时,还可以得到其它非常重要的一些结果,如气穴分布图,熔接线分布图等,这些对优化模具结构都非常有帮助,这里由于篇幅限,不再一一介绍。
4结论把用Moldflow/MPI分析的结论与实际生产中通过试模所得的方案相对比,成型工艺参数大体相同,证明了Moldflow/MPI在模具生产中的实用性,它可以大大减少试模次数,从而缩短了生产周期,降低生产成本。
参考文献:[1]党根茂,骆志斌,李集仁.模具设计与制造[M].西安:西安电子科技大学出版社,2001.[2]成都科技大学,北京化工学院,天津轻工业学院.塑料成型模具[M].北京:中国轻工业出版社,1982.[3]单岩,王蓓,王刚.Moldflow模具分析技术基础[M].北京:清华大学出版社,2004.[4]王丽秀,吴崇峰.利用Moldflow对生化试剂板模具进行优化设计[J].工程塑料,2003,(8):52~54.(上接第12页)△▲△▲△▲△▲△▲△▲△▲△▲△▲△▲△▲△▲△▲△▲△▲△▲△▲△▲△▲△▲△▲△▲△▲△▲△▲△▲△▲△▲△▲△。