铝型材挤压模具优化设计现状和趋势
铝合金挤出成型工艺
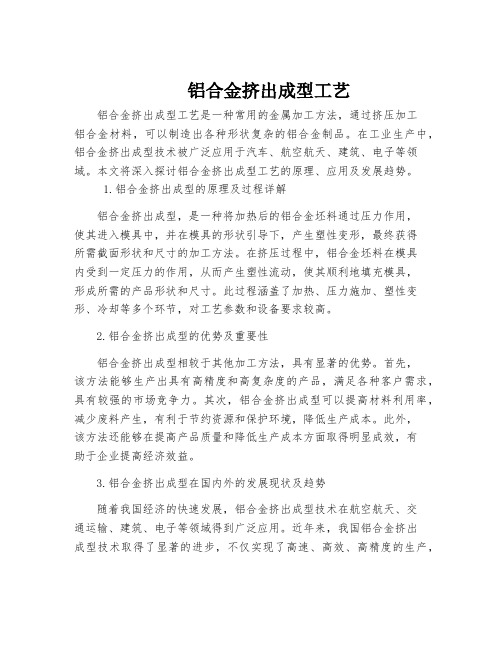
铝合金挤出成型工艺铝合金挤出成型工艺是一种常用的金属加工方法,通过挤压加工铝合金材料,可以制造出各种形状复杂的铝合金制品。
在工业生产中,铝合金挤出成型技术被广泛应用于汽车、航空航天、建筑、电子等领域。
本文将深入探讨铝合金挤出成型工艺的原理、应用及发展趋势。
1.铝合金挤出成型的原理及过程详解铝合金挤出成型,是一种将加热后的铝合金坯料通过压力作用,使其进入模具中,并在模具的形状引导下,产生塑性变形,最终获得所需截面形状和尺寸的加工方法。
在挤压过程中,铝合金坯料在模具内受到一定压力的作用,从而产生塑性流动,使其顺利地填充模具,形成所需的产品形状和尺寸。
此过程涵盖了加热、压力施加、塑性变形、冷却等多个环节,对工艺参数和设备要求较高。
2.铝合金挤出成型的优势及重要性铝合金挤出成型相较于其他加工方法,具有显著的优势。
首先,该方法能够生产出具有高精度和高复杂度的产品,满足各种客户需求,具有较强的市场竞争力。
其次,铝合金挤出成型可以提高材料利用率,减少废料产生,有利于节约资源和保护环境,降低生产成本。
此外,该方法还能够在提高产品质量和降低生产成本方面取得明显成效,有助于企业提高经济效益。
3.铝合金挤出成型在国内外的发展现状及趋势随着我国经济的快速发展,铝合金挤出成型技术在航空航天、交通运输、建筑、电子等领域得到广泛应用。
近年来,我国铝合金挤出成型技术取得了显著的进步,不仅实现了高速、高效、高精度的生产,还大幅提高了材料利用率。
在国际市场上,铝合金挤出成型技术也备受关注,各国纷纷加大研发力度,以期在激烈的市场竞争中占得先机。
4.铝合金挤出成型技术的发展方向及挑战未来,铝合金挤出成型技术的发展方向将主要包括以下几个方面:提高生产效率,降低能耗;提高产品精度,实现精细化生产;研发新型模具材料,提高模具寿命;发展绿色制造,减少废弃物产生。
然而,在技术发展过程中,铝合金挤出成型面临着一系列挑战,如设备研发、工艺优化、环保要求等。
铝型材挤压模具设计课件

铝型材挤压模具设计课件一、铝型材挤压工艺概述二、铝型材挤压模具结构三、铝型材挤压模具设计原则1.尺寸精度:铝型材挤压模具设计时要保证挤压后的铝型材尺寸精度。
模具的内芯设计需考虑材料的收缩率和强度,确保挤压后的铝型材尺寸准确。
2.结构合理:铝型材挤压模具设计时应尽量减小模具的重量和尺寸,提高模具的使用寿命。
同时,要增加模具的刚度和强度,确保在挤压过程中不会变形或断裂。
3.表面质量:铝型材挤压模具的表面光洁度直接影响到挤压后的铝型材表面质量。
因此,在设计模具壳和模具翼时应注意表面的光洁度,减少表面缺陷。
4.降低生产成本:铝型材挤压模具的设计应考虑降低生产成本。
例如,可以采用可更换模具芯片的设计来替换整个模具,从而降低维修和更换模具的成本。
四、铝型材挤压模具制造工艺1.材料选择:铝型材挤压模具一般选用高硬度、高强度的工具钢,如优质合金工具钢或高速工具钢等。
2.预先加工:将选定的工具钢进行粗加工,包括锻造、切割、拉伸等工艺,将模具的初始形状制作出来。
3.精密加工:通过数控加工等精密加工技术,对模具进行精细加工,包括车削、铣削、镗削、磨削等工艺,保证模具的尺寸精度和表面质量。
4.表面处理:对模具进行表面处理,如热处理、氮化等工艺,提高模具的硬度和耐磨性。
5.装配调试:将各个组成部分进行装配,并进行调试,保证模具的合理性和可靠性。
五、铝型材挤压模具的维护与保养1.清洁:定期对铝型材挤压模具进行清洁,除去铝屑和污垢,保持模具的清洁度。
2.润滑:对铝型材挤压模具的摩擦部位进行润滑,减少磨损和摩擦力,并延长模具的使用寿命。
3.定期检查:定期对铝型材挤压模具进行检查,发现问题及时修理,确保模具的正常使用。
4.储存:将不使用的铝型材挤压模具储存到干燥、防尘的环境中,避免受潮和污染。
六、铝型材挤压模具的发展趋势1.高精度:随着制造业对产品精度要求的提高,铝型材挤压模具的精度也将不断提高。
2.高效率:铝型材挤压模具的开发将更加注重提高生产效率和降低能耗。
铝合金挤压制品薄壁模具的设计与优化

铝合金挤压制品薄壁模具的设计与优化第一章介绍铝合金材料在现代工业生产中得到越来越广泛的应用,其中挤压制品是一种重要的工件类型。
薄壁模具是制作铝合金挤压制品的重要工具,其设计和制作质量直接影响制品质量。
本文将探讨铝合金挤压制品薄壁模具的设计和优化问题。
第二章铝合金挤压制品薄壁模具设计的基本原则铝合金挤压制品薄壁模具的设计应遵循以下基本原则:1.结构合理,便于制品的挤压工艺操作。
2.模具的强度和刚性要保证足够的耐用性。
3.模具壁厚要求尽可能的薄,以便使得铝合金挤压制品能够达到更高的质量要求。
4.模具的表面要求光滑度高,以保证挤压制品得到更好的表面质量。
第三章铝合金挤压制品薄壁模具的设计流程铝合金挤压制品薄壁模具的设计流程主要包括以下步骤:1.确定制品的挤压工艺要求。
2.根据铝合金挤压制品的要求和挤压机的参数进行模具设计。
3.进行模具设计计算,并得出模具壁厚、孔隙率、模具支撑点等参数。
4.进行模具制作和安装。
5.进行模具的实验和调试以确定铝合金挤压制品的生产效果。
第四章铝合金挤压制品薄壁模具的优化方法模具优化的目的是使得铝合金挤压制品的制作更加可靠、经济、高效、环保。
以下是针对铝合金挤压制品薄壁模具的优化方法:1.优化挤压工艺。
通过优化挤压工艺参数如挤压比、挤压速度等,减少变形和裂纹的产生,从而降低模具的应力和变形量。
2.优化模具设计。
采用合理的模具设计,以提高模具的强度和刚性、降低模具的应力和变形量,从而能够达到提高模具使用寿命和挤压制品的质量的目的。
3.优化模具材料。
选择合适的模具材料,以达到提高模具强度和刚性、降低模具应力和变形量的目的。
4.加强模具管理。
建立模具管理制度,及时对模具进行检测和维修,在使用过程中防止意外损坏,提高模具的使用寿命和性能。
第五章结论本文从铝合金挤压制品薄壁模具的设计流程、优化方法等方面进行了探讨,可以得出以下结论:1.铝合金挤压制品薄壁模具的设计应遵循基本原则,使得挤压制品质量更加稳定和可靠。
铝合金药筒挤压成形工艺优化

铝合金药筒挤压成形工艺优化『铝合金药筒挤压成形工艺优化』1. 引言铝合金药筒是一种常见的医疗包装材料,由于其良好的气密性、抗氧化性和成本效益,目前已经成为制药行业广泛采用的材料。
而铝合金药筒的生产工艺中,挤压成形是一种常用的工艺方法。
本文将针对铝合金药筒挤压成形工艺进行优化探讨。
2. 挤压成形工艺概述挤压成形是一种通过挤出机将铝合金材料挤压成所需截面形状的工艺方法。
其具体流程为:将铝合金棒材加热到一定温度后,放入挤出机中,通过挤出机内的螺杆,将铝合金挤压成所需的形状。
此工艺方法可高效地生产各种规格和形状的铝合金制品。
3. 挤压成形工艺的优化提高挤压速度,优化产量铝合金挤压成形工艺中,挤压速度是影响产量和生产效率的重要因素。
通过适当提高挤压速度,不仅可以增加生产效率,提高产量,还能降低生产成本,提升生产效益。
采用优质模具,提高产品质量模具是影响铝合金药筒成形质量的关键因素之一。
采用优质的模具,能够保证产品成形的精度和表面质量,减少次品率,提高产品质量。
控制挤压温度,提高成形良率挤压温度是直接影响铝合金药筒成形良率的重要因素。
合理控制挤压温度,可以有效避免铝合金在成形过程中出现气孔、裂纹等缺陷,提高产品的成形良率。
4. 铝合金药筒挤压成形工艺的发展趋势智能化生产随着工业4.0的发展,智能制造技术在铝合金药筒挤压成形工艺中得到了广泛应用。
智能化生产可以实现设备的远程监控和自动化控制,提高生产效率,降低能耗,减少人工干预,提升产品质量。
绿色环保绿色环保已经成为行业发展的趋势,铝合金药筒挤压成形工艺也不例外。
未来,铝合金药筒挤压成形工艺将更加注重环保要求,采用绿色的生产工艺和环保的材料,实现可持续发展。
5. 个人观点和总结铝合金药筒挤压成形工艺的优化,不仅能够提高生产效率、降低生产成本,还能够提高产品质量,满足市场对产品的需求。
未来,随着智能化生产技术和绿色环保理念的不断发展,铝合金药筒挤压成形工艺将迎来更好的发展机遇。
中国铝挤压产业发展现状及今后的努力方向

中国铝挤压产业发展现状及今后的努力方向中国铝挤压产业发展现状及今后的努力方向2018年1月26日,临朐县铝型材行业协会2017年度年会在山东临朐召开,中国有色金属工业协会党委副书记、中国有色金属加工工业协会(以下简称“加工协会”)理事长范顺科应邀出席会议,并发表重要讲话。
范顺科重点就我国铝挤压产业发展现状及今后的努力方向作了详细介绍,并对临朐县铝型材产业发展提出了建议。
一、我国铝挤压产业现状、特点和存在的问题据初步估计,2017年我国铝挤压材产量为1948万吨,比上年增长5%,占全球铝挤压材总产量的65%以上。
我国不仅是名副其实的铝挤压产业大国,而且正向铝挤压强国迈进,产业整体上呈现以下五方面特点:(一)产能规模全球最大,装备水平世界领先截至目前,我国铝挤压领域已装配45兆牛以上大型挤压机121台,其中,国产最大挤压机225兆牛,为全球独有;进口最大挤压机150兆牛,铝挤压产能超过其他国家的总和。
拥有各种铝材表面处理生产线1000多条。
我国的铝挤压产业不仅产能规模全球最大,而且装备水平世界领先。
(二)挤压材产品种类丰富齐全,在消费中独占鳌头截至目前,型、管、棒等各类铝挤压材,我国都可以生产,而且品种、规格和表面处理方式齐全。
世界有的,中国都有;他国没有的,中国也有。
在铝材消费中,与西方国家铝板带消费占比最大不同,我国由于人口众多,以及受“居者有其屋”传统思维的影响,挤压材在我国铝材消费中独占鳌头,其中主要是建筑型材。
据统计,目前我国在建筑与结构领域中的铝材消费占比高达46%左右,并且这种格局在未来一段时间内仍将保持下去。
(三)标准质量世界领先,产品占领国际市场我国主要铝挤压材的产品标准,在制订过程中广泛参考和采用了欧盟、美国和日本标准,实现了与国际接轨。
其中,GB/T 5237《铝合金建筑型材》和GB/T 8013《铝及铝合金阳极氧化膜与有机聚合物膜》系列国家标准得到了世界上多个国家的认可和采用。
现代铝合金挤压工业的发展概况与特点

现代铝合金挤压工业的发展概况与特点一、发展概况:1.历史背景:现代铝合金挤压工业起源于20世纪初,随着铝合金在工业领域的广泛应用,尤其是航空、汽车和建筑等领域的需求增加,挤压工业得到快速发展。
2.技术进步:随着科学技术的不断进步,挤压设备和技术得到了显著改进。
现代挤压设备具备更高的挤压速度和更高的压机能力,可以实现先进的挤压成型操作。
3.发展地区:目前,世界上挤压工业的主要发展地区包括欧洲、北美洲、亚洲和大洋洲等。
其中,欧洲的挤压工业发展最为成熟,占据全球市场份额的一大部分。
4.市场需求:随着现代工业的不断发展,对轻质材料、高强度材料和可塑性材料的需求不断增加,促使铝合金挤压工业的发展。
同时,环保节能是现代工业发展的重要方向,铝合金挤压产品具有优异的环保特性,满足了市场需求。
5.应用范围:现代铝合金挤压工业的应用范围广泛,包括航空航天、汽车、电子、建筑、交通工具、家电和包装等领域。
挤压产品主要包括型材、壳体、散热器、边框、电子外壳等。
二、特点:1.节能环保:铝合金挤压工艺相对于其他成型工艺(如铸造和锻造),对能源的消耗较少,同时挤压过程中产生的废料也相对较少,具有较好的节能和环保特点。
2.材料优势:铝合金具有优良的机械性能、导热性能和耐腐蚀性能,挤压工艺可以很好地保留和提升这些优势,满足各行各业对于材料性能的需求。
3.成型精度高:挤压工艺可以实现高精度、高稳定性的形状成型,使得铝合金挤压产品具备较高的尺寸精度和表面质量。
4.批量生产能力强:挤压工艺可以实现大规模生产,同时挤压设备的自动化程度较高,生产效率相对较高。
这使得铝合金挤压产品适用于大批量和连续生产。
5.设计灵活性强:挤压工艺可以实现复杂形状产品的生产,同时也可以根据客户的需求进行个性化设计和定制生产,具有较高的设计灵活性。
三、发展趋势:1.高性能材料:随着科技进步和工业需求的不断提高,铝合金挤压工业将不断发展高性能、多功能的铝合金材料。
2024年汽车用挤压铝材市场前景分析

2024年汽车用挤压铝材市场前景分析1. 引言随着全球汽车行业的持续发展,汽车材料的需求也越来越大。
挤压铝材作为一种轻质高强度的材料,在汽车制造中起着重要的作用。
本文将对汽车用挤压铝材市场的前景进行分析。
2. 汽车用挤压铝材的优势挤压铝材具有以下优势,使其在汽车制造中得到广泛应用:•轻质高强度:挤压铝材相比传统钢材更轻,但却具有更高的强度和刚性,能够减轻汽车的整体重量,提高燃油效率。
•良好的成形性:挤压铝材可以通过挤压工艺制造出各种复杂形状的零部件,满足汽车设计的需求。
•耐腐蚀性:挤压铝材具有良好的耐腐蚀性,能够在恶劣的环境中保持其性能和外观。
•可回收利用:挤压铝材是可回收利用的材料,符合可持续发展的理念。
3. 汽车用挤压铝材市场现状目前,汽车用挤压铝材市场呈现以下趋势:•高端汽车市场需求增长:随着人们生活水平的提高,对于高端汽车的需求不断增加。
高端汽车制造商倾向于使用更轻、更强的材料,以提高汽车性能和燃油效率。
•节能环保政策的推动:全球范围内的节能环保政策对于汽车制造行业提出了更高的要求。
挤压铝材作为一种节能环保的材料,符合政策要求,有助于应对碳排放和节能减排的挑战。
•新能源汽车的快速发展:随着新能源汽车市场的迅猛发展,挤压铝材在电动汽车的制造中扮演着重要的角色。
电池箱、车身结构等组成部分往往采用挤压铝材,以减轻整车重量,延长续航里程。
4. 汽车用挤压铝材市场前景基于以上的市场现状,可以预见汽车用挤压铝材市场具备良好的前景:•挤压铝材的需求将持续增长:随着汽车制造技术的进步,对于更轻、更强的材料的需求将越来越大。
挤压铝材作为满足这些需求的理想选择,市场前景广阔。
•新能源汽车的发展将推动市场增长:新能源汽车市场将持续快速发展,需要大量的挤压铝材作为轻量化材料。
随着电动汽车的普及,挤压铝材市场有望得到进一步的扩大。
•技术创新将促进市场发展:随着科技的不断进步,挤压铝材的制造工艺和技术将不断完善,降低生产成本,提高产品性能,进一步推动市场发展。
国内挤压现状及发展现状
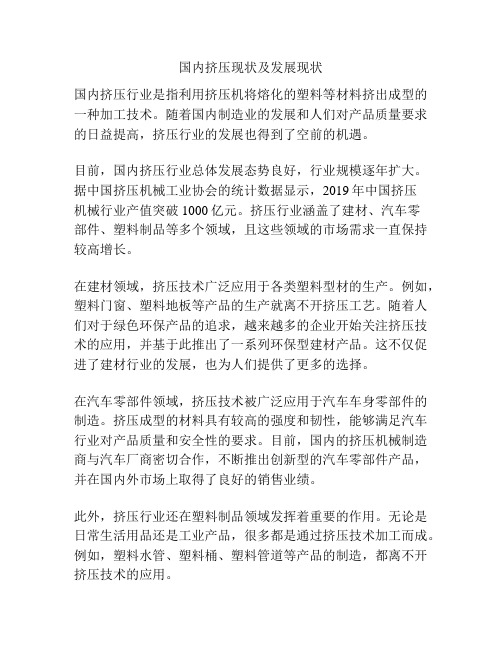
国内挤压现状及发展现状国内挤压行业是指利用挤压机将熔化的塑料等材料挤出成型的一种加工技术。
随着国内制造业的发展和人们对产品质量要求的日益提高,挤压行业的发展也得到了空前的机遇。
目前,国内挤压行业总体发展态势良好,行业规模逐年扩大。
据中国挤压机械工业协会的统计数据显示,2019年中国挤压机械行业产值突破1000亿元。
挤压行业涵盖了建材、汽车零部件、塑料制品等多个领域,且这些领域的市场需求一直保持较高增长。
在建材领域,挤压技术广泛应用于各类塑料型材的生产。
例如,塑料门窗、塑料地板等产品的生产就离不开挤压工艺。
随着人们对于绿色环保产品的追求,越来越多的企业开始关注挤压技术的应用,并基于此推出了一系列环保型建材产品。
这不仅促进了建材行业的发展,也为人们提供了更多的选择。
在汽车零部件领域,挤压技术被广泛应用于汽车车身零部件的制造。
挤压成型的材料具有较高的强度和韧性,能够满足汽车行业对产品质量和安全性的要求。
目前,国内的挤压机械制造商与汽车厂商密切合作,不断推出创新型的汽车零部件产品,并在国内外市场上取得了良好的销售业绩。
此外,挤压行业还在塑料制品领域发挥着重要的作用。
无论是日常生活用品还是工业产品,很多都是通过挤压技术加工而成。
例如,塑料水管、塑料桶、塑料管道等产品的制造,都离不开挤压技术的应用。
尽管国内挤压行业取得了较好的发展成绩,但仍面临一些挑战和问题。
首先是技术水平和设备制造方面存在差距,与国际先进水平相比还有一定的差距。
其次是市场竞争压力大,特别是一些小型企业面临着生存困境。
面对这些问题,国内挤压行业需要加强技术研发和创新能力,提高产品质量和技术水平。
同时,政府应该积极推动挤压行业的转型升级,加大对相关企业的技术支持和政策扶持力度。
此外,加强行业协会的组织和管理,促进企业之间的合作和交流,也是推动行业发展的重要因素。
总之,国内挤压行业在挤压技术的引领下,在建材、汽车零部件、塑料制品等领域取得了良好的发展成绩。
- 1、下载文档前请自行甄别文档内容的完整性,平台不提供额外的编辑、内容补充、找答案等附加服务。
- 2、"仅部分预览"的文档,不可在线预览部分如存在完整性等问题,可反馈申请退款(可完整预览的文档不适用该条件!)。
- 3、如文档侵犯您的权益,请联系客服反馈,我们会尽快为您处理(人工客服工作时间:9:00-18:30)。
铝型材挤压模具优化设计现状和趋势郑军,傅建,李冬(四川工业学院材料工程与科学系,四川成都 610039)
[摘要] 简要叙述了铝型材挤压模具设计现状和趋势,说明了数值模拟在铝型材挤压模具设计优化中的意义,并针对国内外对此所做的工作,提出了一些看法。[关键词] 铝型材;挤压模具;优化设计;数值模拟中图分类号:TG379 文献标识码:B 文章编号:1000-8446(2002)06-0057-03
StatusandTrendonOptimizingDesignofAluminumProfileExtrusionDieZHENGJun,FUJian,LIDong(SichuanUniversityofScienceandTechnology,Chendu610039,China)Abstract:Thepresentresearchanddevelopmenttrendontheoptimizingdesignofaluminumextrusiondiearediscussed.Thesignificanceofthenumericalsimulationinoptimizingdesignispresented.Thesomeeffortsofoptimizingdesignbasedonnumericalsimulationarepointedout.Keywords:aluminumprofile;extrusiondie;optimizingdesign;numericalsimulation
铝型材挤压,是指将铝合金高温铸坯置于专用模具(机头)内,在挤压机提供的强大压力作用下,按给定的速度,将铝合金从模腔中挤出,从而获得所需形状、尺寸以及具有一定力学性能的铝合金挤压型材。铝型材挤压成形过程非常复杂,除了圆形截面铝型材的挤压属于二维轴对称问题外,一般而言,其它形状的铝型材挤压属于三维流动大变形问题。因此,挤压模具的设计制作质量和其使用寿命就成了挤压过程是否经济可行的关键之一。合理的设计与制造能大大延长模具寿命,对于提高生产效率、降低成本和能耗具有重要意义。目前,我国型材挤压模具设计基本上还停留在传统的依靠工程类比和设计经验的积累上,所设计制作的模具需经反复试模和调整才能保证其成功地投入使用,从而造成企业不时停工待模,影响正常生产;同时也导致挤压产品质量不高,模具使用寿命较短等诸多缺陷。因此,随着铝型材产品不断向大型化、扁宽化、薄壁化、高精化、复杂化和多用途、多功能、多品种、长寿命方向发展,改进传统的模具设计方法已成为当前铝型材工业发展的迫切需求。
1 挤压模具优化设计现状由于要设计出结构合理且经济实用的挤压模具是一件十分复杂而困难的工作,因此,世界各国的挤压工作者对模具设计理论和方法(特别对优化理论和方法)进行了大量的研究工作。随着弹塑性理论和挤压理论的发展,许多新型的实验理论和方法、计算理论和方法已开始用于挤压模具设计制作领域。如工程计算法、金属流动坐标网格法、光弹光塑法、密栅纹云法、滑移线法、上限元理论和有限元理论等被广泛用于模具应变场的确定和各种强度的校核,进而优化其结构和工艺要素。随着计算机技术的发展,挤压模具的CAD/CAM技术在最近20~30年中得到迅速发展,且很大一部分技术集中在模具设计的优化方面。何德林等人[1]利用IDEF0方法开发出能对平面模和分流模进行优化设计的CAD/CAM系统;王孟君等人[2]以AUTOCAD12.0为图形支撑环境,VISUALBASIC4.0为开发工具,开发的CAD系统,可以有效地从事挤压平模的各项计算,从而对设
收稿日期:2002-03-04作者简介:郑军(1974-),女,四川德阳人,在读研究生,助工,主要研究方向:计算机在模具成形中的应用。
57郑军等 铝型材挤压模具优化设计现状和趋势计结果进行优化;闫洪等人[3]将CAE概念引入模具设计过程,指出了优化设计的方向;刘汉武等人[4]提出智能CAD概念,为模具设计智能化提供了一些思路。此外,国内外科研人员运用理论解析、物理模拟和数值模拟等方法,对铝型材挤压的变形过程、应力场和温度场分布及变化、摩擦与润滑等问题进行了大量的分析和实验,并根据其研究成果对挤压模具进行了优化。例如,赵云路和刘静安[5]对各类挤压模具的优化设计进行了系统论述。国内还有部分科研人员用有限元法结合实验方法对挤压模具最佳轮廓前线及模具结构进行了分析和优化。但是,我国由于模具技术底子薄,起步晚,在综合水平上与国外同行业相比仍有一定差距见表1[6]。表1 国内外模具设计的主要差距指标国际先进水平国内目前水平设计理论和方法普遍采用动态热分析有限元和计算机模拟成形过程。基本采用传统方法,开始研究和开发新理论新方法。近几年来,有限元等技术已进入实用阶段。CAD/CAM技术普遍推广应用CAD/CAM技术从二维向三维发展,开发了大量的平面模和组合模及其它结构模具的应用软件,且商品化。已开发出平面模和平面分流模的二维实用软件及导流模应用软件,正向三维推进。但适用性和实用程度不高。2 数值模拟在挤压模具设计中的作用和国内外对此所做的工作铝型材截面形状越复杂,其挤压过程中变形的不均匀性就越显著,加之截面上各部分的金属在挤出模孔时流速不同,故容易造成型材的扭拧、波浪、弯曲及裂纹等缺陷出现,既影响产品质量,也影响模具寿命。对铝型材的挤压过程进行数值模拟(即在计算机上仿真整个挤压成形过程,获得变形体内的应力、应变、温度、流速等物理量分布,以及挤压各阶段的压力、温度、速度等工艺参数变化情况)可以预测实际挤压过程中可能出现的缺陷,尽快优化模具结构设计、调整挤出工艺参数和有针对性指明技术解决方案。数值模拟还可以部分替代模具设计制造过程中费时费事的试模工作,减少材料浪费,降低生产成本,提高产品质量和市场竞争力。以有限元分析为代表的数值模拟方法主要用于铝型材挤压变形的过程模拟和温度场、压力场、速度场模拟,以及摩擦润滑分析等。国内外研究者们对此已做了许多工作。韩国的Hyun_WooShin等[7]在1993年对非轴对称挤压过程进行了有限元分析,他们利用二维刚塑性有限元方法结合厚板理论将三维问题进行了简化,对整个挤压过程进行了准确的数值模拟,同时也减少了计算量。对于变形模拟,于沪平等[8]采用塑性成型模拟软件DEFORM,结合刚粘塑性有限元罚函数法对平面分流模的挤压变形过程进行了二维模拟,得出了挤压过程中铝合金的应力、应变、温度以及流动速度等的分布和变化。刘汉武等[9]利用AN-SYS软件对分流组合模挤压铝型材进行了有限元分析和计算,找出了原模具设计中不易发现的结构缺陷。周飞等[10]采用三维刚-粘塑性有限元方法,对一典型铝型材非等温成形过程进行了数值模拟,分析了铝型材挤压的三个不同成形阶段,给出了成形各阶段的应力、应变和温度场分布情况以及整个成形过程中模具载荷随成形时间的变化情况。对于压力场,闫洪等[11]在2000年利用ANSYS软件作为平台,对壁板型材挤压过程进行了三维有限元模拟和分析,获得了型材挤压过程的位移场、应变场、应力场。对实际型材挤压中工艺参数选择和模具结构尺寸的修正起到了重要指导作用.对于摩擦与润滑的分析,1997年,俄罗斯的VadimL.Berezhnoy等[12]对摩擦辅助在直接和间接挤压成形硬质铝合金中的技术进行了研究。该技术的发展和应用使生产效率和质量都得到了大大提高。美国的PradipK.Saha[13]在1998年对铝型材挤压成形中热动力学和摩擦学进行了研究。他采用热力学数值模拟法构造了3种不同的实验模型,分析了模具工作带和流动金属接触面上的摩擦特性,还对坯料温度和挤压过程中产生的热量对模具工作带所产生的温升的影响、并进行了实际测量验证;研究表明,挤压过程中的摩擦对型材的精度和表面质量有直接影响,模具工作带的磨损过程取决于挤压过程中的热动力学性能,而挤压热动力学性能又与挤压变量有关。上述研究者所做的工作说明,数值模拟技术正在成为铝型材挤压模具设计优化的重要手段之一。
58金属成形工艺 METALFORMINGTECHNOLOGYVol.20l.620023 结 语提高铝型材挤压模具设计与制造水平是改善产品质量和增强市场竞争力之关键所在,而数值模拟技术在铝型材挤压模具设计优化中起着十分重要的作用。国内外同行借助数值模拟方法对优化铝型材挤压模具(包括挤压过程和挤压工艺)进行了有益尝试,取得了不少科研和应用成果,这种动向值得注意。尽快把最新的有限元分析技术应用到整个挤压模具设计与制造过程中,让更多的模具工程师掌握这种优化设计方法,以提高我国铝型材挤压行业及其模具制造业的市场竞争力。
[参考文献][1] 何德林,李志刚.铝型材挤压模CAD/CAM系统及其关键技术的研究.轻合金加工技术[J],1997,25(9):25-30.[2] 王孟君,周伟,田辉,等.铝型材挤压平模CAD系统的开发[J].金属成形工艺,1998,16(3):27-31.[3] 闫洪,包忠诩,柳和生.铝型材挤压模CAD/CAM/CAE
研究进展[J].轻合金加工技术,1999,27(10):1-4.[4] 刘武汉,顾迎新,崔建忠.型材挤压模具的智能CAD系统[J].轻合金加工技术,1999,27(4):6-7.[5] 赵云路,刘静安.空心铝型材挤压模具优化设计(连载)[J].轻合金加工技术,1997,25.[6] 谷兰成,陈学同.我国铝型材挤压业的现状及未来[J].山东冶金,1998,20(4):16-20.[7] Hyun-WooShin,Dong-WookimandNaksooKim.Asimpl-ifiedthree-dimensionalfinite-elementanalysisofthenon-ax-isymmetricextrusionprocesses[J].Journalofmaterialspro-cessingtechnology,1993,38:567-587.[8] 于沪平,彭颖红,阮雪榆.平面分流焊合模成形过程的数值模拟[J].锻压技术,1999,24(5):9-11.[9] 刘汉武,丁桦,崔建忠.铝型材挤压分流组合模有限元分析和计算[J].模具工业,1999,(4):9-11.[10] 周飞,彭颖红,阮雪榆.铝型材挤压过程有限元数值模拟[J].中国有色金属学报,1998,8(4):637-642.[11] 闫洪,包忠诩.型材挤压过程三维弹塑性有限元模拟[J].轻合金加工技术,2000,28(11):30-33.[12] VadimL.Berezhnoy.Friction-assisstedextrusionasanalter-nativetotheindirectanddirectextrusionofhardaluminumalloys[J].Lightmetalage,1997,55(3-4):8-13.[13] PradipK.Saha.Thermodynamicsandtribologyinaluminumextrusion[J].Wear,1998,218(2):179-190.