项目2 手工编程-铣平面
数控编程与加工项目2_数控铣削平面

班级第周周(月日)第至节
班级第周周(月日)第至节
班级第周周(月日)第至节
项目名称
项目二数控铣削平面
项目课时
4
模块名称
1用G00_G01编程端铣刀数控铣削平面
模块课时
2
能力目标
终极目标:会用端铣刀数控铣削平面
促成目标:
1、会建立工件坐标系,并用G53-G59/G92调用零点偏置值
2、会根据加工工艺确定刀具路径,制定编程方案
3、会用G00、G01功能用端铣刀铣平面、会用立铣刀铣开口成型槽
4、会计算基点坐标,并用G90~G91、G20~G21表述编辑单位
知识要点
1、确定工件坐标系原点的三原则,G53-G59/G92与工件坐标系的关系
2、绝对与增量尺寸编程G90~G91
3、公、英制转换G20~G21与相关编辑单位和数据设定
在四周Ra3.2,底面Ra1.6、大小100×80×30的锻铝毛坯上:
1、用Ф60的直角端铣刀粗、精台阶平面、台阶侧面各一次,精加工余量0.3;2、用Ф18的高速钢直柄普通立铣刀铣槽一次;先加工面,后加工槽。
两个工步用G00、G01合编一条数控铣削程序。
二、主题讲解(完成工作化任务必备知识、方法、步骤讲解,技能训练演示等)
4、快速定位G00
5、直线插补G01
6、基点坐标计算
工作任务
用G00、G01编程,数控铣削XM-01平面
教学条件
与环境
多媒体教室、数控仿真室、数控实训中心
拓展内容
FANUC系统数控铣床对刀
选用端铣刀、立铣刀规格形状
参考材料
刀具产品样本,网络及图书馆资源等
教学心得
教学设计方案
一、任务呈现(描述工作化任务及具体要求、教学时间安排)
平面零件加工任务一数控铣平行面铣削

市技师学院(高级技工学校)教案任务载体对如图所示的零件进行工艺编制、编程与操作加工准备教学设备:数控铣/立式加工中心共5台;计算机5台,材料:45钢65×65×25板料5快;(塑料代替)工量具:φ16立铣刀5把,φ10钻头5把(配相应刀柄),百分表5个,磁性表座5个,25-50外径千分尺5把;,游标卡尺5把。
教学课件与相关教学资料.教学实施工作过程工作任务教学组织学时资讯分析零件信息、特殊加工要求,理解加工技术要求;了解工具基本条件与技术参数信息,工艺与程序编制规则、标准;其它信息。
公布项目任务,教师协调下的学生自愿分组,明确分工;提出资讯建议,提供获取资讯的方法与途径信息。
1 计划拟定工艺过程,确定工艺装备,零件的装夹方式,辅具的选用,毛坯设计等。
听取学生的决策意见,提出可行性方面的质疑,提供指导意见,帮助形成工艺方案结论。
22.平面铣削常用刀具类型图2-1-2 可转位硬质合金面铣刀图2-1-3 可转位硬质合金 R面铣刀图2-1-4 立铣刀3.刀具直径的确定平面铣削时刀具直径可根据以下方法来确定。
(1)最佳铣刀直径应根据工件宽度来选择,D≈(1.3~1.5)WOC(切削宽度)(2)如果机床功率有限或工件太宽,应根据两次进给或依据机床功率来选择铣刀直径,当铣刀直径不够大时,选择适当的铣削加工位置也可获得良好的效果,此时,WOC=0.75D,一般情况下,在机床功率满足加工要求的前提下,可根据工件尺寸,主要是工件宽度来选择铣刀直径,同时也要考虑刀具加工位置和刀齿与工件接触类型等。
进行大平面铣削时铣刀直径应比切削宽度大 20%~50%。
4.切削用量的选择(推荐表)1)铣削深度 ap(背吃刀量)、2)铣削速度 Vc3)进给速度 F二、程序指令准备1、辅助功能指令(M指令)2、准备功能指令(G指令)二). 绝对坐标编程方式G90指令增量坐标编程方式G91指令指令格式 G90G91指令功能设定坐标输入方式指令说明 1. G90指令建立绝对坐标编程方式,移动指令目标点的坐标值X、Y、Z表示刀具离开工件坐标系原点的距离;2. G91指令建立增量坐标编程方式,移动指令目点的坐标值X、Y、Z 表示刀具离开当前点的坐标增量。
数控机床 模块三:数控铣床编程与操作加工 项目2:平面图形加工

(三).空运行及仿真
打开程序,选择MEM(自动)工作方式,打开机床锁住开关, 按空运行键,再按循环启动键,观察程序运行情况;若按图形显 示键再按循环启动键,可进行轨迹仿真,观察加工轨迹。空运行 结束后,使空运行及机床锁住功能复位,机床重新回参考点。
(四).零件单段运行加工
零件单段工作模式是数按控车下床上循零件环加工启过程动按钮后,刀具在执行完程序 中的一段程序后停止。通过单段加工模式可以一段一段地执行程 序,便于仔细检查数控程序。FANUC系统操作步骤如下:
则运动时间长,效率低 3.圆弧插补指令 (1)指令功能:使刀具按给定进给速度沿圆弧方向进行切削加工。 (2)指令代码:顺时针圆弧插补指令代码:G02(或G2)逆时针圆弧
插补指令代码:G03(或G3)顺时针、逆时针方向判别:从不在圆弧 平面的坐标轴正方向往负方向看,顺时针用G02,逆时针用G03。
沈阳理工大学应用技术学院
可选大些;但刀具直径小,进给量应选择小一些;深2mm,一次下刀 至目标尺寸,具体如下:主轴转速:1200r/min;进给速度:垂直加 工30mm/min;表面加工50mm/min (7)编程原点:工件上表面中心
沈阳理工大学应用技术学院
2.工艺方案: 不分粗、精加工,一次垂直下刀至要求的深度尺寸。加工路线考虑路径 最短原则即可,对于不连续图形,刀具应注意设置抬刀工艺。其参考加 工路线如下:刀具空间移动至P1上方→下刀→顺时针圆弧加工至P2点→ 直线加工至P3点→逆时针圆弧加工至P4点→抬刀→刀具空间移动至P7点 上方→下刀→直线加工至P8点→顺时针圆弧加工至P9点→抬刀→刀具空 间移动至P5点上方→下刀→直线加工至P6点→抬刀→刀具空间移动至 P5′点上方→下刀→直线加工至P6′点→ 抬刀结束加工。
数控铣手工编程

工件
刀具
刀具半径补偿(G41、G42、G40)
左刀补:沿着刀具前进方向刀具在工 件轮廓左侧的补偿
右刀补:沿着刀具前进方向刀具在工 件轮廓右侧的补偿
刀具半径补偿(G41、G42、G40)
指令格式:
刀具半径补偿的建立:
XY
XZ
D
YZ
刀具补偿号
刀具补偿起刀时必须为G00或G01 左、右刀补的设置
刀具半径补偿(G41、G42、G40)
螺旋线进给G02/G03
说明 1.X, Y, Z 中由G17/G18/G19 平面选定的两个坐标为螺旋线投影圆弧的终点 意义同圆弧进给第3 坐标是与选定平面相垂直的轴终点其余参数的意义同圆弧进 给。 2.该指令对另一个不在圆弧平面上的坐标轴施加运动指令对于任何小于360 的 圆弧可附加任一数值的单轴指令。
G90 时为中间点在工件坐标系中的坐标。 G91 时为中间点相对于起点的位移量。
G28 指令首先使所有的编程轴都快速定位到中间点,然后再从中间 点返回到参考点。
一般G28 指令用于刀具自动更换或者消除机械误差,在执行该指 令之前应取消刀具半径补偿和刀具长度补偿。
自动返回参考点G28
利用G28从当前点直接回参考点:
该指令使刀具以F指定的进给速度插补加
工出任意斜率的直线, 指令格式如下: G01 X__ Y __ Z __ F __ ;
其中, X、 Y、 Z为直线的终点坐标, 可以是绝对坐标, 也可以是增量坐标, 不移动的坐标轴可以省略; F为刀具移 动的速度, 单位为mm/min。
直线插补(G01)
直线插补编程实例:
圆弧半径 圆弧终点的坐标值
圆弧插补G02/G03
圆弧的终点位置与圆心
平面铣方孔的编程方法

平面铣方孔的编程方法
平面铣方孔的编程方法可以按照以下步骤进行:
1. 确定刀具尺寸和材料厚度:根据方孔尺寸和材料厚度选择合适的铣刀。
2. 确定切削参数:根据材料的硬度和特性,确定合适的切削速度、进给速度和切削深度。
3. 绘制刀具路径:根据方孔的尺寸和位置,在CAD软件或CAM软件中绘制刀具路径。
4. 选择初始点:选择合适的初始点,使刀具可以从该点进入材料并开始切削。
5. 编写G代码:根据刀具路径和切削参数,编写相应的G代码。
这包括刀具路径的曲线插补、进刀和退刀等指令。
6. 设置刀具补偿:根据刀具的半径或直径,设置相应的刀具补偿。
这可以通过G41(左补偿)或G42(右补偿)指令来实现。
7. 进行测试和修正:在实际加工中,首先进行试切,然后根据切削情况进行必要的修正,如调整切削参数或刀具路径。
8. 进行加工:在调试完毕后,进行正式的加工。
需要注意的是,编程过程中应当确保刀具路径的合理性和切削过程的稳定性,同时确保刀具和工件的安全。
数控编程第三单元平面铣

3、切削速度Vc
铣削的切削速度Vc与刀具的耐用度、每齿进给量、背吃刀量、侧吃刀量 以及铣刀的齿数成反比,而与铣刀的直径成正比。 铣削加工的切削速度Vc可参考有关切削用量手册中的经验公式计算选取。 主轴转速n(r/min)主要根据允许的切削速度Vc(m/min)选取
n= 1000Vc
式中:Vc—切削速度,由刀具D的耐用度决定;
背吃刀量或侧吃刀量的选取主要由加工余量和对表面的质量的要求决定。
(1)当工件表面粗糙度要求为Ra=12.5~25um时,如果圆周铣削加工余 量小于5mm,端面铣削加工余量小于6mm,粗铣 一次进给就可以达到要 求 。但是在余量较大,工艺系统刚性较差或机床动力不足时,可分为两 面三刀次进给完成。
(2)当工件表面粗糙度要求为Ra=3.2~25um时, 应分为粗铣和半精铣 两步进行,粗铣时背吃刀量或侧吃刀量选取同前。粗铣后留0.5~1.0mm 余量,在半精铣时切除。
启建动立主工轴件,坐转标速系, 2主5快0轴r速/m到进i达n给安到全下高刀度, 开快位冷速置却接近工件
N50 G01 Z0.5 F100; 下到Z0.5面
N60 X-120 F300; 粗加工上表面
N70 Z0 ;
N90 G00 Z50 M09; N100 M05;
1、机用虎钳 2、三爪卡盘 3、角铁 和V形铁 4、组合夹具 5、专用夹具 6、直接装卡
六、工艺路线确定与工艺文件
工艺路线的确定步骤: 1、分析零件图样 2、工艺分析:加工方案、装夹方案、工艺工序、加工路线、 刀具参数等
工艺文件包括: 1、工序卡 2、刀具卡 3、走刀路线图 4、加工程序单
工序划分:刀具集中、粗精加工、按加工部位
N40 G00 Z5; 接近工件
数控手工编程 铣床篇

本 指
令
系中的坐标值。
数控铣床的编程基础
四 、 数 控 铣 床 编 程 的 基 本 指 令
数控铣床的编程基础
注意:
四 、
数
① G92指令通过设定刀具起点相对于工
控 铣
床
件坐标原点的位置建立坐标系。
编
程
② 刀具不产生运动。
的 基
本
指
令
数控铣床的编程基础
2.选择工件坐标系G54~G59
四 、
G54——选择1号加工坐标系
数控铣床的编程基础
二 、 数 控 铣 床 的 加 工 对 象
数控铣床的编程基础
三、数控铣床的加工工艺
(一)零件图工艺分析 (二)数控铣削夹具与刀具的选择 (三)切削用量的选择
数控铣床的编程基础
(一)零件图工艺分析
三
1.零件图分析
、 数
(1)尺寸标注方法分析
控 铣
床
的
加
工
工
艺
数控铣床的编程基础
2.顺铣
二
铣刀与工件接触部分的旋转方向与工件进 给方向相同。
、 相 关
知
识
项目一 平面凸轮廓类零件的编程与加工
3.两种铣削方式适用的场合:
二
一般来说,数控加工应尽可能采用顺铣。
、 相
关
对于铝镁合金、钛合金和耐热合金等材料
知 识
来说,建议采用顺铣加工。
如果零件毛坯为黑色金属锻件或铸件,表 皮硬而且余量一般较大,这时采用逆铣。
四
、
编程格式:G00 X_ Y_ Z_
数
控
说明:G00的运动
铣 床
轨迹不一定为一条
编 程
数控铣床编程与操作模块二平面图形加工课件
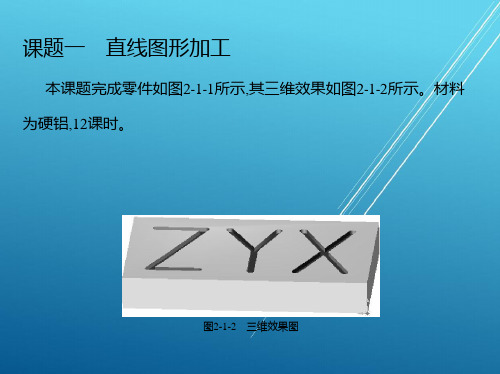
表2-2-2 法那克系统与西门子系统圆弧插补指令
其中,X、Y为圆弧终点坐标;R、CR为圆弧半径;F为圆弧插补 进给速度。
如图2-2-5所示,加工圆弧起点在A点,终点为B点。
图 2-2-5
2) 格式二:终点坐标+圆心坐标。
法那克系统与西门子系统指令格式相同,格式为: G17 G02(G03)X Y I J F
四、零件单段运行加工
零件单段工作模式是按下数控启动按钮后,刀具在执行完程序 中的一段程序后停止。通过单段加工模式可以逐段地执行程序,便于 仔细检查数控程序。
五、零件加工及评分标准(表2-1-7)
表2-1-7 数控铣床课题评分表
【思考与练习】
1.如何编写完整加工一个零件的数控程序? 2.常用数控程序功能字有哪几大类?各有何功能? 3.G00、G01指令格式如何?使用时二者有何区别? 4.编写加工图2-1-8所示图形的程序(图形深1mm)。
转速为1500r/min。
(5)刀具功能字 地址:T。 功能:表示指定加工时所选用的刀具号。例如,T6表示选6号刀。
(6)辅助功能字 地址:M从M00~M99(或M999),前置的“0”可省略不写,如M02与 M2、M03与M3可以互用。
功能:表示数控机床辅助装置的接通和断开,一般由PLC(可编程序 控制器)控制,FANUC(法那克)0i系统和SINUMERIK(西门子)802S/ C系统常用辅助指令含义见表2-1-1。
X、Y、Z轴均采用试切法对刀,并把操作得到的零偏值 输入到G54等偏置寄存器中。 三、空运行
法那克系统:把基础坐标系中Z轴值变为“+50”,选择MEM( 自动加工)工作模式,打开程序,按下空运行按钮,按循环启动按钮,观察 加工轨迹。空运行结束后使空运行按钮复位。
- 1、下载文档前请自行甄别文档内容的完整性,平台不提供额外的编辑、内容补充、找答案等附加服务。
- 2、"仅部分预览"的文档,不可在线预览部分如存在完整性等问题,可反馈申请退款(可完整预览的文档不适用该条件!)。
- 3、如文档侵犯您的权益,请联系客服反馈,我们会尽快为您处理(人工客服工作时间:9:00-18:30)。
内容:刀具路径的规划知识 :往复式刀路,环形刀路等
上一项目中,通过简单案例的介绍,业已清楚,程序编写的步骤以及框架。
接下来,要在这一基础上继续深入,槽的加工已实现它的编程,那么如果是平面呢?能否更进一步,在槽的基础上编写它的程序?
60X60的平面切除1mm 的量
平面这样形状的加工,该如何同槽联系上呢?槽就是一个平面只不过很小,现在这个要加工的平面很大,那这样的话,可以用一系列的槽组合,那就可以形成这一平面了。
这里用上组合的思维,很容易就能实现平面的编写程序。
到这,对平面的编程,有了大致的方向,但这还不够。
依然需要细化它,这里面槽的组合形式,依然不清楚。
那如何组合这些槽呢?也就是说一系列的刀具路径如何高效而方便的覆盖整个面?这就涉及了刀具路径的规划。
最基础的刀具路径规划就是槽加工所体现的这样的几个动作,定位到起始点;进到安全平面;进到进刀评面;进刀运动;切削运动;退刀运动;退到进刀平面,退到安全平面;退到初始高度。
如果有下一切削位置则,在退到安全平面这移动到下一位置,进行下一切削的动作循环,直到所有位置完成。
进刀平面 切削 起始点 安全平面
安全平面 退刀平面
实际的加工过程,对一定形状的区域的面,只依靠直线形式的刀具路径是不够的。
接下来,介绍几种常见的针对区域面的刀具路径规划形式。
1 往复式刀具路径
2 环形刀具路径
3 两者的结合
它们的形式非常直观,可见下图。
如果有下一切削位置,则在退到安全平面这移动到下一位置,进行下一切削的动作循环,直到所有位置完成。
实际的加工过程,对一定形状的区域的面,只依靠直线形式的刀具路径是不够的。
接下来,介绍几种常见的针对区域面的刀具路径规划形式。
1 往复式刀具路径
2 环形刀具路径
3 两者的结合
它们的形式非常直观,可见下图。
60X60的平面加工
1.看图,定工艺
加工一平面,不分粗加工和精加工,一次到位根据平面大小选取20刀具,采用数控铣床加工
规划刀具路径,
采用往复式的刀具路径规划形式。
确立下刀的位置,结合下图图示确立。
刀具的下刀位置,需要确立两个位置,刀具不能同零件接触,要在零件之外下刀(零件要加工的区域是敞开的),这样刀具的切削边缘,离加工的面的侧边界,留出一定间隙。
这个值取3~5
另外一个位置是刀心落在边界里面,离边界2~3如图所示。
确立了下刀位置,第一切削步的终了位置,可以选在同中心对称的位置。
有了第一个切削步,加上行距值,就能得出第二个切削步。
直到最终把整个面覆盖为止。
如何判断刀具路径覆盖与否?
只要把刀具路径画出来即可。
刀具路径的草绘,可以很好的帮助程序的编写。
这点需要特别注重并掌握。
如图所示,只要判断刀具路径离边缘间距A和刀具半径的大小即可。
A小于刀具半径就覆盖到位。
可以退出刀具。
刀具路径已经规划好了,以平面的中心作为坐标系原点。
那么所有的刀具路径就都是准确的位置,可以准确的进行描述。
那后面的内容就是把图形翻译成
代码了。
规划出的刀具路径如下图所示。
编写程序
按照规划好的刀具路径逐条翻译。
写出如下程序:%G90G54S650M03;
G00X0Y0Z100.0;
G00X-45.0Y27.0Z100.0
G01 X-45.0Y27.0Z30.0F3000
G01 X-45.0Y27.0Z2.0F1000
G01 X-45.0Y27.0Z-1.0F200
G01X45.0Y27.0F600 第一个切削步
G01X45.0Y12.0F600
G01X-45.0Y12.0F600 第一个切削步
G01X-45.0Y-3.0F600
G01X45.0Y-3.0F600 一个切削步
G01X45.0Y-18.0F600
G01X-45.0Y-18.0F600 第一个切削步
G01X-45.0Y-33.0F600
G01X45.0Y-33.0F600 第一个切削步
G01 X-45.0 Y-33.0Z-1.0F200
G01 X-45.0 Y-33.0Z2.0F1000
G01 X-45.0 Y-33.0Z30.0F3000
G00X-45.0Y27.0Z100.0
G00X0Y0Z100.0;
M05M30;
%
请思考能否实现对其它两种刀具规划形式的平面编程?。