挤出成型工艺参数包括温度
挤出成型工艺介绍工艺
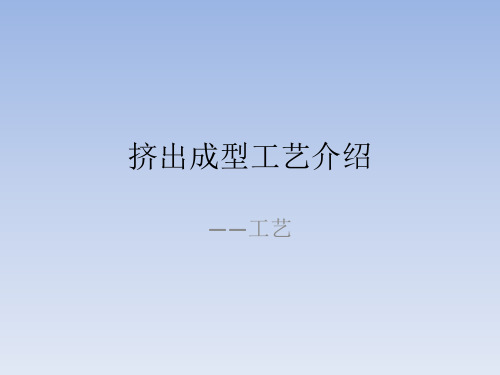
二、片材工艺流程及装置 挤出板、片材生产工艺流程如下:
二、片材工艺流程及装置
单螺杆挤出机,挤出物料多数为粒料,物料配置主要指着色、改性母粒 的混合或共混改性造粒。
双螺杆挤出机,挤出物料多数为粉料,物料配置主要指润性物料或非润 性物料的混合。
片材所用挤出机一般是排气式单螺杆挤出机或双螺杆挤出机。排气式单 螺杆挤出机的螺杆直径为90——200mm。长径比为20——28。
在普通单级螺杆挤出机生产中,挤出速度是决定挤出产量和质量的重要 工艺参数。
在一定操作条件下,挤出速度提高,物料塑化质量降低,其最大挤出速 率取决于挤出机的塑化能力。因此大截面积制品的挤出速率应低于小截面积制品。 对与多级螺杆挤出机或一些特殊设计的挤出机,挤出速率对物料塑化质量影响不 大,可实现高速挤出成形。
挤出成型工艺介绍
——工艺
目录
一、工艺参数设定原则 二、片材工艺流程及装置 三、工艺控制 四、常见缺陷
一、工艺参数设定原则
1、机身温度 对与普通的单组份热塑性塑料固体原料的挤出成形,挤出机机身温度设
定原则为: ①机身设定的最高温度略高于塑料的黏流温度(或熔点); ②机身设定的最低温度应至少低于塑料软化点10; ③单螺杆挤出机机身设定的最高温度与最低温度的差值不大于80; ④机身温度字加料端到熔料出口逐渐升高或与螺杆计量段对应区温度相近; ⑤在满足熔化物料的前提下,机身温度应尽可能低。
②三辊压光机温度直接影响板、片材的表面质量和冷却定型,温度一般 控制在材料的玻璃化温度附近。
三、工艺控制
三、工艺控制
2、螺杆冷却 用单螺杆挤出机生产板、片材时,对于与螺杆表面摩擦因数较大的物料
或较易熔融并使固体输送段很短的物料,应采用螺杆冷却方法以提高固体输送速 率。 3、牵引速度
peek挤出造粒参数

peek挤出造粒参数
PEEK的挤出造粒参数主要包括以下几点:
1. 温度控制:根据原料和产品的不同,温度设置在230°C\~370°C之间。
2. 螺杆转速:螺杆转速通常在100\~150rpm之间,但具体转速应视产品
要求和设备性能而定。
3. 模头温度:模头温度对产品的成型质量和外观影响较大,一般设置在270°C\~300°C之间。
4. 牵引速度:牵引速度决定了产品的厚度和生产效率,通常在
20\~50m/min之间。
5. 收卷张力:收卷张力决定了产品的致密度和平整度,通常在2\~8kg之间。
6. 添加剂使用:根据需要,可以添加一定比例的增强剂、阻燃剂、抗菌剂等添加剂。
7. 冷却时间:冷却时间对产品的性能和生产效率有影响,一般冷却时间在
10\~30秒之间。
8. 切割长度:根据需要,可以设定不同的切割长度,切割长度一般在
10\~30mm之间。
9. 供料速度:供料速度决定了挤出机的生产效率,供料速度在
30\~120r/min之间。
10. 设备配置:根据生产需要,可以选择不同配置的挤出机、切粒机、干燥机等设备。
请注意,这些参数不是固定的,具体需要根据设备性能、产品要求以及生产环境等因素进行调整。
同时,还需要注意安全操作规程,确保生产过程中的安全。
高分子材料成型加工中的挤出成型工艺参数优化
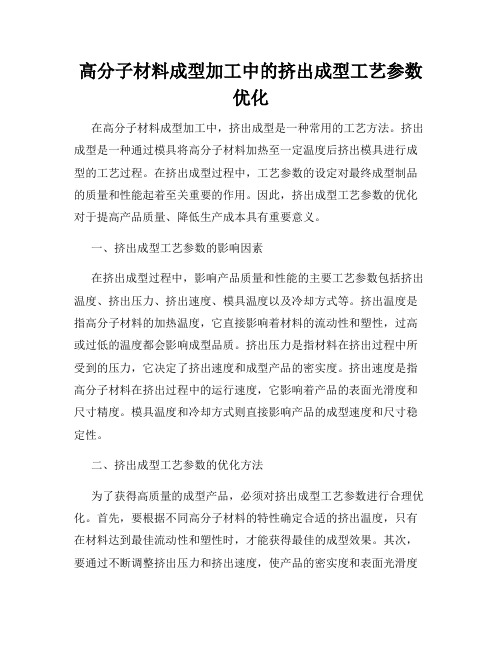
高分子材料成型加工中的挤出成型工艺参数优化在高分子材料成型加工中,挤出成型是一种常用的工艺方法。
挤出成型是一种通过模具将高分子材料加热至一定温度后挤出模具进行成型的工艺过程。
在挤出成型过程中,工艺参数的设定对最终成型制品的质量和性能起着至关重要的作用。
因此,挤出成型工艺参数的优化对于提高产品质量、降低生产成本具有重要意义。
一、挤出成型工艺参数的影响因素在挤出成型过程中,影响产品质量和性能的主要工艺参数包括挤出温度、挤出压力、挤出速度、模具温度以及冷却方式等。
挤出温度是指高分子材料的加热温度,它直接影响着材料的流动性和塑性,过高或过低的温度都会影响成型品质。
挤出压力是指材料在挤出过程中所受到的压力,它决定了挤出速度和成型产品的密实度。
挤出速度是指高分子材料在挤出过程中的运行速度,它影响着产品的表面光滑度和尺寸精度。
模具温度和冷却方式则直接影响产品的成型速度和尺寸稳定性。
二、挤出成型工艺参数的优化方法为了获得高质量的成型产品,必须对挤出成型工艺参数进行合理优化。
首先,要根据不同高分子材料的特性确定合适的挤出温度,只有在材料达到最佳流动性和塑性时,才能获得最佳的成型效果。
其次,要通过不断调整挤出压力和挤出速度,使产品的密实度和表面光滑度达到最佳状态。
同时,要合理控制模具温度和采用适当的冷却方式,保证产品的尺寸稳定性和成型速度。
三、挤出成型工艺参数优化的意义挤出成型工艺参数的优化不仅能够提高产品的质量和性能,还能够降低生产成本,提高生产效率。
合理设定工艺参数可以减少废品率,降低维护成本,增加生产线的稳定性和可靠性。
此外,优化工艺参数还可以提高产品的竞争力,满足市场需求,促进企业的可持续发展。
综上所述,挤出成型工艺参数的优化对于高分子材料成型加工具有重要的意义。
合理设定挤出温度、挤出压力、挤出速度、模具温度和冷却方式等工艺参数,可以获得更高质量的成型产品,降低生产成本,提高生产效率,促进企业的可持续发展。
挤出成型工艺参数包括
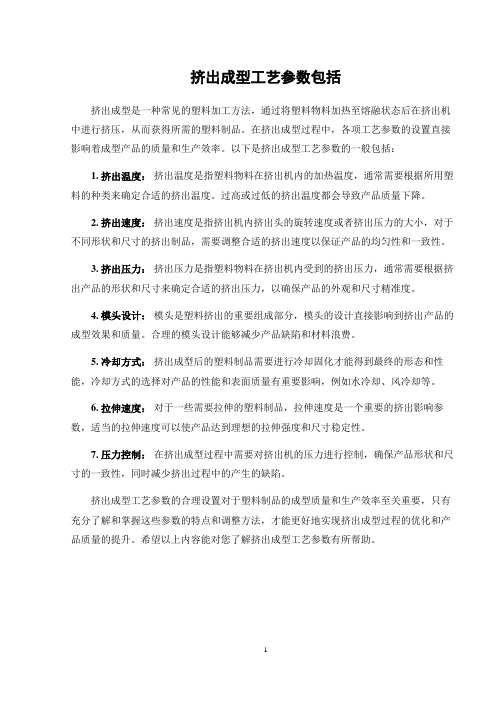
挤出成型工艺参数包括挤出成型是一种常见的塑料加工方法,通过将塑料物料加热至熔融状态后在挤出机中进行挤压,从而获得所需的塑料制品。
在挤出成型过程中,各项工艺参数的设置直接影响着成型产品的质量和生产效率。
以下是挤出成型工艺参数的一般包括:1. 挤出温度:挤出温度是指塑料物料在挤出机内的加热温度,通常需要根据所用塑料的种类来确定合适的挤出温度。
过高或过低的挤出温度都会导致产品质量下降。
2. 挤出速度:挤出速度是指挤出机内挤出头的旋转速度或者挤出压力的大小,对于不同形状和尺寸的挤出制品,需要调整合适的挤出速度以保证产品的均匀性和一致性。
3. 挤出压力:挤出压力是指塑料物料在挤出机内受到的挤出压力,通常需要根据挤出产品的形状和尺寸来确定合适的挤出压力,以确保产品的外观和尺寸精准度。
4. 模头设计:模头是塑料挤出的重要组成部分,模头的设计直接影响到挤出产品的成型效果和质量。
合理的模头设计能够减少产品缺陷和材料浪费。
5. 冷却方式:挤出成型后的塑料制品需要进行冷却固化才能得到最终的形态和性能,冷却方式的选择对产品的性能和表面质量有重要影响,例如水冷却、风冷却等。
6. 拉伸速度:对于一些需要拉伸的塑料制品,拉伸速度是一个重要的挤出影响参数,适当的拉伸速度可以使产品达到理想的拉伸强度和尺寸稳定性。
7. 压力控制:在挤出成型过程中需要对挤出机的压力进行控制,确保产品形状和尺寸的一致性,同时减少挤出过程中的产生的缺陷。
挤出成型工艺参数的合理设置对于塑料制品的成型质量和生产效率至关重要,只有充分了解和掌握这些参数的特点和调整方法,才能更好地实现挤出成型过程的优化和产品质量的提升。
希望以上内容能对您了解挤出成型工艺参数有所帮助。
1。
挤出成型工艺参数包括温度

均化段
机头及口模段
丙烯酸类聚合物
室温
100~170
~200
175~210
≤
醋酸纤维素
室温
110~130
~150
175~190
<
聚酰胺(PA)
室温~90
140~180
~270
180~270
<
聚乙烯(PE)
室温
90~140
~180
160~200
<
硬聚氯乙烯(HPVC)
挤出成型工艺参数包括温度
挤出成型工艺参数包括温度、压力、挤出速率和牵引速度等。
1.
温度
温度是挤出成型得以顺利进行的重要条件之一。从粉状或粒状的固态物料开始,高温制品从机头中挤出,经历了一个复杂的温度变化过程。严格来讲,挤出成型温度应指塑料熔体的温度,但该温度却在很大程度上取决于料筒和螺杆的温度,一小部分来自在料筒中混合时产生的摩擦热,所以经常用料筒温度近似表示成型温度。由于料筒和塑料温度在螺杆各段是有差异的,为了使塑料在料筒中输送、熔融、均化和挤出的过程顺利进行,以便高效率地生产高质量制件,关键问题是控制好料筒各段温度,料筒温度的调节是靠挤出机的加热冷却系统和温度控制系统来实现的。机头温度必须控制在塑料热分解温度以下,而口模处的温度可比机头温度稍低一些,但应保证塑料熔体具有良好的流动性。此外,成型过程中温度的波动和温差,将使塑件产生残余应力、各点强度不均匀和表面灰暗无光泽等缺陷。产生这种波动和温差的因素很多,如加热、冷却系统不稳定,螺杆转速变化等,但以螺杆设计和选用的好坏影响最大。表9-1是几种塑料挤出成型管材、片材和板材及薄膜等的温度参数。表9-1热塑性塑料挤出成型时的温度参数
室温~60
120~170
塑料成型工艺与模具设计试题及答案
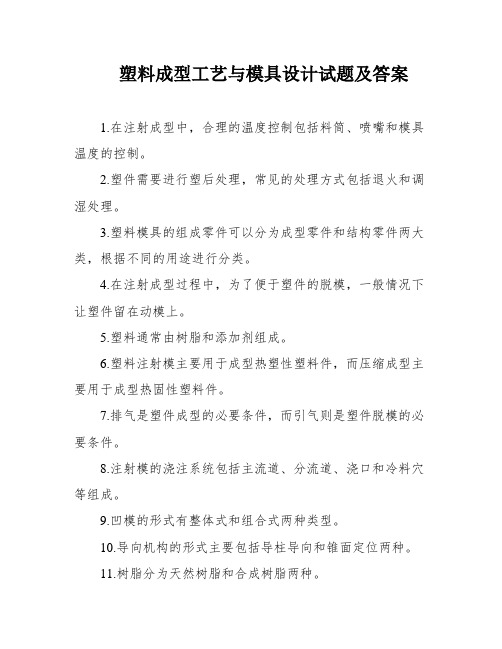
塑料成型工艺与模具设计试题及答案1.在注射成型中,合理的温度控制包括料筒、喷嘴和模具温度的控制。
2.塑件需要进行塑后处理,常见的处理方式包括退火和调湿处理。
3.塑料模具的组成零件可以分为成型零件和结构零件两大类,根据不同的用途进行分类。
4.在注射成型过程中,为了便于塑件的脱模,一般情况下让塑件留在动模上。
5.塑料通常由树脂和添加剂组成。
6.塑料注射模主要用于成型热塑性塑料件,而压缩成型主要用于成型热固性塑料件。
7.排气是塑件成型的必要条件,而引气则是塑件脱模的必要条件。
8.注射模的浇注系统包括主流道、分流道、浇口和冷料穴等组成。
9.凹模的形式有整体式和组合式两种类型。
10.导向机构的形式主要包括导柱导向和锥面定位两种。
11.树脂分为天然树脂和合成树脂两种。
12.注射模塑最主要的工艺条件是“三要素”,即压力、时间和温度。
1.卧式注射机SX-Z-63/50中的50表示锁模力为500kN。
2.注射机料筒温度的分布原则是前高后低。
3.热塑性塑料在常温下呈坚硬固态,属于玻璃态。
4.塑料模失效形式不包括冷却。
5.凹模是成型塑件外表面的成型零件。
6.球头铣刀主要用于加工塑料模具零件中的轮廓。
7.注射模导向机构不包括推杆。
8.主流道一般与注射机的喷嘴轴心线重合。
9.推出机构零件不包括型芯。
10.压缩模具中凸模的结构形式多数是整体式的,以便于加工制造。
11.天然树脂包括松香。
12.塑料模具结构零件不包括成型作用。
13.稳定剂不包括树脂。
角,可以避免模具损坏和塑件表面不光滑的问题(3分)。
此外,圆角的设计还可以避免塑件在使用过程中刮伤人体或其他物品(1分)。
2.请简述多型腔模具的优缺点。
(10分)答:多型腔模具的优点是可以同时生产多个相同或不同的塑件,提高生产效率,降低成本(3分);可以灵活调整模具的生产能力,适应不同的市场需求(2分);同时还可以减少模具的占地面积和存储空间(2分)。
缺点是制造成本较高(1分);需要更高的精度和稳定性(1分);同时需要更多的注塑机和操作人员(1分);还有可能出现一个腔位出现问题,影响整个生产线的正常运行(2分)。
tpv 挤出工艺温度

tpv 挤出工艺温度TPV是一种热塑性弹性体,其挤出工艺温度是指在TPV挤出过程中所需的温度范围。
挤出工艺温度的控制对于生产高质量的TPV制品至关重要。
下面我将详细介绍TPV挤出工艺温度的相关知识。
一、TPV挤出工艺温度的基本概念在TPV挤出过程中,挤出工艺温度指的是挤出机的加热区域温度设置,通常包括进料区、加热区和机筒。
1.进料区温度进料区温度是指TPV原料进入挤出机前的温度,通常要求在60°C 至80°C之间。
进料区温度的控制能够使TPV原料在进入挤出机前获得最佳的流动性能和可挤出性。
2.加热区温度加热区温度是指TPV挤出机的加热区域温度,用于将TPV原料加热至合适的挤出温度。
加热区温度的设置应根据具体的TPV材料种类和厂家的建议进行。
一般来说,加热区温度的范围为160°C至200°C,具体取决于TPV挤出的要求和工艺。
3.机筒温度机筒温度是指挤出机筒体的温度,一般要求在180°C至220°C之间。
机筒温度的设置对于保持TPV原料在挤出过程中的稳定性和流动性能至关重要。
二、TPV挤出工艺温度的影响因素1. TPV材料的种类和成分不同种类和成分的TPV材料对应不同的挤出工艺温度要求。
例如,硅氧烷基TPV通常需要较低的挤出温度,而苯乙烯-乙烯-丁二烯橡胶改性TPV通常需要较高的挤出温度。
因此,生产厂家需要根据具体的TPV材料确定适宜的挤出工艺温度。
2. TPV挤出机的设定和控制系统挤出机的设定和控制系统影响着挤出工艺温度的控制精度和稳定性。
先进的挤出机设备和精确的温度控制系统能够更好地满足不同TPV 材料的挤出温度要求。
三、TPV挤出工艺温度的优化控制方法为了获得高质量的TPV制品,需要对挤出工艺温度进行优化控制。
以下是几种常用的优化控制方法:1.温度曲线设置在挤出过程中,可以设置合适的温度曲线来实现更精确的温度控制。
根据TPV材料的特性,将加热区温度、机筒温度等进行合理的调整和控制,以保持TPV原料在整个挤出过程中的温度稳定。
挤出成型工艺参数有哪些

挤出成型工艺参数有哪些
挤出成型是一种常见的塑料加工工艺,通过加热和压力使塑料颗粒在挤出机中经过螺杆挤出,最终成型为所需的产品。
在挤出成型过程中,需要根据不同的塑料材料和成型要求来调整一系列工艺参数,以确保最终产品的质量和性能。
首先,挤出成型工艺参数中最重要的是挤出温度。
挤出温度是指挤出机不同部位的温度设置,通常包括料筒温度、模头温度和模具温度。
不同类型的塑料材料需要在不同的温度下进行挤出,过高或过低的温度都会影响挤出成型的效果,甚至导致产品质量问题。
其次,挤出速度也是一个至关重要的参数。
挤出速度取决于螺杆的旋转速度以及料筒的进料速度,控制好挤出速度可以有效地控制产品的尺寸和表面光洁度。
过快的挤出速度可能导致产生内部应力过大,从而影响产品的外观和力学性能。
除了温度和速度外,压力也是挤出成型中不可忽视的参数之一。
合理的挤出压力可以保证塑料材料充分填充模腔,避免产生气泡和瑕疵,并且有利于产品的密实性和强度。
同时,压力的大小也要根据产品形状和尺寸的不同做出相应的调整,以求达到最佳的成型效果。
此外,挤出成型还需考虑挤出机的螺杆转速、冷却方式、模具结构等参数。
螺杆转速的选择直接影响塑料材料的挤出速度和均匀性,冷却方式则关系到产品的收缩率和外观质量,模具结构的设计要符合产品的形状和尺寸需求,以确保最终产品达到设计要求。
综上所述,挤出成型工艺参数多种多样,需要综合考虑材料特性、产品要求和设备性能等因素,通过合理的调整和控制来实现挤出成型过程中的稳定性和高效性,从而生产出优质的塑料制品。
1。
- 1、下载文档前请自行甄别文档内容的完整性,平台不提供额外的编辑、内容补充、找答案等附加服务。
- 2、"仅部分预览"的文档,不可在线预览部分如存在完整性等问题,可反馈申请退款(可完整预览的文档不适用该条件!)。
- 3、如文档侵犯您的权益,请联系客服反馈,我们会尽快为您处理(人工客服工作时间:9:00-18:30)。
硬聚氯乙烯(HPVC)
室温~60
120~170
~180
170~190
<0.2
软聚氯乙烯及氯乙烯共聚物
室温
80~120
~140
140~190
<0.2
聚苯乙烯(PS)
室温~100
130~170
~220
180~245
<0.1
2.压力
在挤出过程中,由于料流的阻力,螺杆槽深度的变化,以及过滤网、过滤板和口模等产生阻碍,因而沿料筒轴线方向,在塑料内部产生一定的压力。这种压力是塑料变为均匀熔体并得到致密塑件的重要条件之一。
挤出速率在生产过程中也存在波动现象,这将影响塑件的几何形状和尺寸精度。因此,除了正确确定螺杆结构和尺寸参数之外,还应严格控制螺杆转速,严格控制挤出温度,防止因温度改变而引起挤出压力和熔体粘度变化,从而导致挤出速度的波动。
4.牵引速度
挤出成型主要生产连续的塑件,因此必须设置牵引装置。从机头和口模中挤出的塑件,在牵引力作用下将会发生拉伸取向。拉伸取向程度越高,塑件沿取向方向的拉伸强度也越大,但冷却后长度收缩也大。通常,牵引速度可与挤出速度相当。牵引速度与挤出速度的比值称牵引比,其值必须大于1。
由于料筒和塑料温度在螺杆各段是有差异的,为了使塑料在料筒中输送、熔融、均化和挤出的过程顺利进行,以便高效率地生产高质量制件,关键问题是控制好料筒各段温度,料筒温度的调节是靠挤出机的加热冷却系统和温度控制系统来实现的。
机头温度必须控制在塑料热分解温度以下,而口模处的温度可比机头温度稍低一些,但应保证塑料熔体具有良好的流动性。
79.7
25
19.1
26
38.5
26
稳流定型段长度/mm
120
60
60
50
45
87
牵引比
1.04
1.2
1.1
1.02
1.5
0.97
真空定径套内径/mm
96.5
—
25
33
31.7
33
定径套长度/mm
300
—
160
250
—
250
定径套与口模间距/mm
—
—
—
25
20
20
3.挤出速率
挤出速率(亦称挤出速度)是单位时间内挤出机口模挤出的塑料质量(单位为kg/h)或长度(单位为m/min)。挤出速度的大小表征着挤出生产能力的高低。
影响挤出速度的因素很多,如机头、螺杆和料筒的结构、螺杆转速、加热冷却系统结构和塑料的特性等。理论和实践都证明,挤出速率随螺杆直径、螺旋槽深度、均化段长度和螺杆转速的增大而增大,随螺杆末端熔体压力和螺杆与料筒间隙增大而增大。在挤出机的结构和塑料品种及塑件类型已确定的情况下,挤出速率仅与螺杆转速有关,因此,调整螺杆转速是控制挤出速率的主要措施。
挤出温度/℃
原料中水分控制/%
加料段
压缩段
均化段
机头及口模段
丙烯酸类聚合物
室温
100~170
~200
175~210
≤0.025
醋酸纤维素
室温
110~130
~150
175~190
<0.5
聚酰胺(PA)
室温~90
140~180
~270
180~270
<0.3ห้องสมุดไป่ตู้
聚乙烯(PE)
室温
90~140
~180
160~200
此外,成型过程中温度的波动和温差,将使塑件产生残余应力、各点强度不均匀和表面灰暗无光泽等缺陷。产生这种波动和温差的因素很多,如加热、冷却系统不稳定,螺杆转速变化等,但以螺杆设计和选用的好坏影响最大。
表9-1是几种塑料挤出成型管材、片材和板材及薄膜等的温度参数。
表9-1热塑性塑料挤出成型时的温度参数
塑料名称
?挤出成型工艺参数包括温度、压力、挤出速率和牵引速度等。
1.温度
温度是挤出成型得以顺利进行的重要条件之一。从粉状或粒状的固态物料开始,高温制品从机头中挤出,经历了一个复杂的温度变化过程。严格来讲,挤出成型温度应指塑料熔体的温度,但该温度却在很大程度上取决于料筒和螺杆的温度,一小部分来自在料筒中混合时产生的摩擦热,所以经常用料筒温度近似表示成型温度。
机头温度/℃
160~170
150~160
130~135
175~180
220~240
200~220
口模温度/℃
160~180
170~180
130~140
190~195
200~210
200~210
螺杆转速/(r/min)
12
20
16
10.5
15
10.5
口模内径/mm
90.7
32
24.5
33
44.8
33
芯模外径/mm
25
25.5
管材厚度/mm
5
3
2
3
—
—
机筒温度/℃
后段
80~100
90~100
90~100
160~165
250~260
200~240
中段
140~150
120~130
110~120
170~175
260~270
240~250
前段
160~170
130~140
120~130
175~180
260~280
230~255
增加机头压力可以提高挤出熔体的混合均匀性和稳定性,提高产品致密度,但机头压力过大将影响产量。
和温度一样,压力随时间的变化也会产生周期性波动,这种波动对塑件质量同样有不利影响,螺杆转速的变化,加热、冷却系统的不稳定都是产生压力波动的原因。为了减少压力波动,应合理控制螺杆转速,保证加热和冷却装置的温度控制精度。
表9-2是几种塑料管材的挤出成型工艺参数。
表9-2几种塑料管材的挤出成型工艺参数
塑料
管材工艺参数
硬聚氯乙烯
(HPVC)
软聚氯乙烯
(LPVC)
低密度
聚乙烯
(LDPE)
ABS
聚酰胺-1010
(PA-1010)
聚碳酸酯
(PC)
管材外径/mm
95
31
24
32.5
31.3
32.8
管材内径/mm
85
25
19
25.5