基于模型推理的铸造模具设计研究与应用
模型铸造的特点及应用

模型铸造的特点及应用模型铸造是一种常见的金属制造工艺,其特点包括形状复杂的产品能够快速地进行大规模和精密的生产。
模型铸造的过程中,金属液体被倾倒到特制的模子中,并在凝固后形成所需的零件或产品。
模型铸造在工业界中有广泛的应用,包括汽车制造、航空航天、机械制造等领域。
下面我们将具体讨论模型铸造的特点以及其在不同行业中的应用。
模型铸造的特点主要包括以下几个方面:1. 形状复杂的产品能够快速、精密地生产。
通过制作精密的模具,模型铸造可以生产具有复杂形状的产品,这些产品往往难以通过其他金属加工工艺生产。
模型铸造能够保证产品的精准度和表面光洁度。
2. 生产周期短。
相比较其他金属加工工艺,模型铸造的生产周期通常较短,可以快速地满足客户的需求,并且可以进行大规模的生产。
3. 生产成本相对较低。
模型铸造的生产成本相对较低,因为一次模具可以进行多次生产,而且可以在不同尺寸和形状的产品上使用同一个模具。
4. 适用于多种金属。
模型铸造适用于多种金属,包括铁、铝、锌、铜等,可以满足客户对于不同金属产品的需求。
模型铸造在不同行业中有广泛的应用,具体应用如下:1. 汽车制造。
模型铸造在汽车制造中扮演着重要角色,汽车零部件如汽缸盖、曲轴箱、离合器壳等都可以通过模型铸造来生产。
汽车制造行业对产品的精密度和生产周期要求非常高,模型铸造正是满足了这些需求。
2. 航空航天。
航空航天行业对产品质量和性能要求极高,模型铸造可以生产出高精度和高强度的零部件,如发动机零部件、机身零部件等。
3. 机械制造。
模型铸造在机械制造行业中也有着重要的应用,能够生产出形状复杂且精密的零部件,如齿轮、轴承、机床零件等。
4. 军工和船舶制造。
军工和船舶制造也是模型铸造的重要应用领域。
在这些领域,产品的耐久性和稳定性要求很高,模型铸造可以满足这些需求。
除了上述行业,模型铸造还在电子、化工、建筑等多个领域有着广泛的应用。
总的来说,模型铸造具有形状复杂的产品能够快速、精密地生产、生产周期短、生产成本相对较低、适用于多种金属等特点,因此在诸多行业中有着非常广泛的应用。
基于事例的推理(CBR)及其在注塑模具分型面设计中的应用

颈问题 , 逐渐引起 人工 智能领域研究者的关注。本文对 C R从 基本理论 、 B 关键技术进 行 了综述 , 并结合 注 塑模 具分 型面的设计方法进行了实践应用介绍 。 关键词 : 基于事例 的推理 综述 实践应 用
C s— ae ao ig C R)n s iz gi e s nn ae B sdRe snn ( B a dI l i t i ig t Uti n n h De g
下 面从 理 论 层 面 、技 术 层 面 和 应 用 层 面 , 对
决问题的方法和问题事例一 同被系统记录并存储 起来 ,以备将来之用——系统 的学习能力不断提
高, 知识 和经验也 不断增 加 。 因此 , 个完整的 C R系统一般包括 厂个循环过 — B l 。
程 , m d 和 Paa归纳 为 4 : e eeR ueR v e A ot l z R R t v 、 e s、 ei i r s
类所面对的知识和信息成指数增长 ,这使传统的
基 于 规 则 的推 理 ( ue-ae esnn ,简 称 R l-bsd R aoi - g
基于混合推理的涡轮叶片精铸模具智能设计

mo i e rtiv I e ut Th x e i e tt ns o h t h p r a hi hs p p r a x e t o df t e r a s l yh e r 。 ee p r na i h ws t a e a po c nt i a e ห้องสมุดไป่ตู้ e p c m o t c t
A src- A h b i ra o ig mo e w s po td i wh h C R ( a eb s d ra o i ) wa b t t y r e s nn d l a rmpe n a d i B c c s — a e e s nn g s a pi o c pu l e ina dR R (ueb s dra o ig a p l dt ealdd sg f r p l dt c n e ta d sg n B e o rl—a e e s nn )w sa pi d ti e inat e o e e
r s a c h e i n p o e s a d d m a n k o e g f iv s me tc s ig m o d d sg i l o e e r h t e d sg r c s n o i n wl d e o n e t n a t n l e i n f d f r e
JA u—o g Z AN i — u , A e — u S aj ING R i n , H G Dn h a W NG W nh , HI s g Hu -e i
( e a oaoyo o tmp rr e ina dItgae n fcui , nsr f d c t n K yL b rtr f ne oayD s n e rtdMa ua tr g Mii yo u ai , C g n n t E o N r w se nP l e h i l i ri , i n7 7 , a n iChn ) o t e tr o tc nc v st X’ 1 0 2 Sh a x, i h y a Un e y a 0 a
砂型铸造模具设计及制造探究

砂型铸造模具设计及制造探究摘要:砂型铸造在现代化社会发展中得到了广泛使用,砂型铸造的使用带来了新的生产方式,极大提升了生产效率。
文章对砂型铸造模具规划和模具生产的问题进行了分析,以实现国内砂型铸造质量得到不断提高,并提升生产效率,确保工业制造的质量。
关键词:砂型铸造;模具设计;模具制造;分析砂型铸造给工业生产效率的提升带来了基础支持,随着高新技术的进步,现代砂型铸造模具的规划与制造过程,融合诸多的新技术,不断提升了砂型铸造母模的规划精确度,提高生产速度,促使工业生产技术的不断进步。
1、砂型铸造砂型铸造是使用相对便宜且容易获得的资源为材料,比如石膏、气管以及木头等资源用作工业生产中进行零件制造所需的模型,让铸造的模型可以适应工业制造中大量生产所需的制造形式,发挥出提升工业生产的制造效率的价值。
砂型铸造模具是实现砂型铸造规程的关键依据,随着工业发展中科学技术的不断提升,砂型铸造模具的规划和制造也随之在改进,给国内工业生产设备的质量提升带来了保障。
2、砂型铸造模型规划2.1绘制平面设计图砂型铸造模型规划的精准性直接影响到砂型铸造模具的后期使用性能,为确保砂型铸造模型的设计精准无误,文章对其主要步骤分类成如下几个部分:绘制砂型铸造模型的平面图纸[1]。
砂型铸造模具的平面设计上要涉及砂型铸造模型规划的主视图、俯视图以及左视图三个部门,提升砂型铸造模型运用的实际规划的立体性特点;另外砂型铸造模型的平面设计上要确定模具规划的长、宽、高以及半径等基本信息,设计师能对砂型铸造模型设计的信息设计变化空间值,然后利用数字模型来验证信息,确保砂型铸造模型设计信息的精准度。
2.2创建砂型铸造模具的数字模型砂型铸造模具规划中的第二环节,是根据砂型铸造模型的平面设计,创建砂型铸造模具规划的运算模型,明确砂型铸造模具平面创作的信息应用的变动精准值,比如砂型铸造模具创作中采用的数字模型中,引入函数运算的形式,确定自变量 X 和因变量 Y,把砂型铸造模具上因变量与自变量的关系展开信息分析,进而有效确定自变变量间存在的函数关系,为确保砂型铸造模具规划应用信息的准确性提供科学、准确的参考依据。
运用Deform有限元分析优化锻造模具设计

软件介绍D eform 是一套基于有限元的工艺仿真系统,用于分析金属成形及其相关工艺的各种成形和热处理工艺。
通过在计算机上模拟整个加工过程,帮助工程师和设计人员设计工具和产品工艺过程,减少昂贵的现场实验成本。
提高模具的设计效率,降低生产的材料成本,缩短产品的研究开发周期。
案例分析以下就通过一个案例阐述在实际设计中如何运用D eform 有限元分析来优化锻造工艺及其锻造模具的设计。
图1产品是水龙头的一个重要零件,材质为铅黄铜(C uZn40Pb2),产品重量419克。
锻造工艺有两种方案:①开式模锻,如图2,②闭式挤压,如图3。
运用Deform 有限元分析优化锻造模具设计刘名水图1水龙头重要零件图2开式模锻图3闭式挤压!!!!!!!!!!!对两种方案分别运用DEFROM 进行模拟分析。
DEFROM 软件操作过程:因DEFROM -3D 本身建立几何模型功能较差,难以建立复杂几何模型,且模具设计是用P roe设计,所以就用P roe 建立几何模型。
上模,下模,以及锻造原材料(铜棒)。
用P roe 建好几何模型后,把上模,下模,原材料分别导成.stl 文件。
打开DEFROM -3D 中的DEFROM -F3模块,建立模拟文件,首先进行前处理。
导入之前建立的几何模型(.stl 文件),为了简化计算,不考虑热量在原材料与模具之间的传递,原材料进行网格划分,设定锻造参数:锻造温度700℃,模具温度150℃,摩擦系数0.3,上模移动速度400mm/sec ,上模移动距离等,原材料选择DE -FROM-3D 软件自带材料库里的DI N -CuZn40Pb2。
其中最重要的是注意原材料的网格划分,网格划分越粗,即网格数量越少,模拟计算就越不准确。
相反,网格划分越细,即网格数量越多,模拟计算就越准确,但计算量就越大。
需根据计算机硬件条件及分析需求,合理划分网格数。
前处理设定好,检测数据OK 后,生成待模拟计算数据。
然后进行模拟计算。
铸造技术的研究与应用

铸造技术的研究与应用铸造技术是一种广泛应用于制造业的工艺技术。
通过将金属或非金属材料加热到熔融状态,然后借助于模具或模板,将该材料注入模型中进行冷却,从而形成所需的零件、零件。
随着现代制造业的不断发展,铸造技术也在不断进步和改进。
本文将探讨铸造技术的研究与应用。
一、铸造技术的历史与发展铸造技术早在古代就已经出现,最早的铸造技术可以追溯到公元前6000年至公元前5000年的新石器时期。
那时,人们已经学会了用石制成的容器来融化铅、铜、锡等金属,并利用石、砂等材料制造模具,将熔化的金属倒入模具中,待其凝固冷却后拆模得到所需的器物。
随着时间的推移,铸造技术不断发展,出现了多种不同的铸造方法和技术。
近年来,随着科学技术的进步,铸造技术得到了进一步的发展。
例如,3D打印技术可以在数字模型的帮助下制造复杂的图形和结构,在铸造零件的制造中提供了新的可能性。
此外,计算机模拟技术和材料科学技术的不断发展,也为铸造技术的优化提供了强大的支持。
二、铸造技术的研究与发展现状铸造技术的研究和发展一直是制造业领域的热点问题。
如今,国内外学者和企业都在致力于铸造技术的研究与发展。
1、新型材料的研究随着科学技术的发展,越来越多的新型材料得到应用,这些材料需要相应的铸造技术支持。
例如,近年来,由于环保和节能的要求,钼基、镍基等高温合金及其复合材料逐渐得到广泛应用,同时需要相应的铸造技术发展以适应这些新材料的应用。
2、铸造技术的自动化与智能化人工智能、机器学习、大数据等技术日益成熟,这些技术为铸造技术的自动化和智能化提供了技术支持。
例如,利用自动化技术,可以大大提高铸造生产的效率和准确性,降低生产成本。
3、环保问题的解决在现代制造业中,环保问题已经成为不可忽视的重要问题。
铸造过程中,除了释放大量废气、废液等问题,还存在金属材料的浪费问题。
因此,为了解决这些问题,研究人员正在探索新的铸造技术,例如基于粉末冶金的铸造技术,以减少对环境的影响。
CAE仿真技术在先进铸造工艺优化中的应用
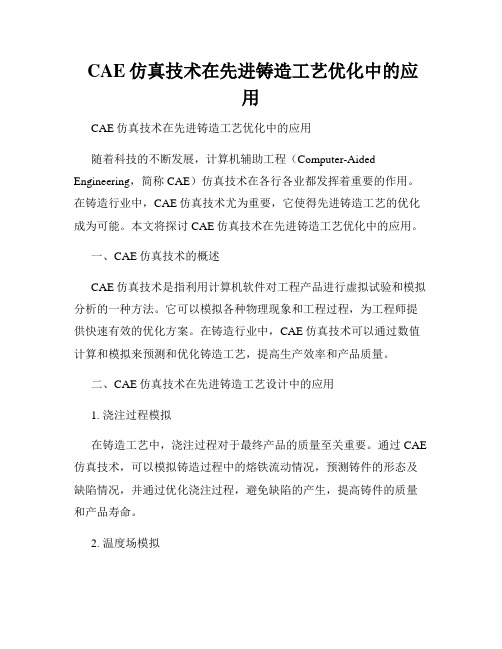
CAE仿真技术在先进铸造工艺优化中的应用CAE仿真技术在先进铸造工艺优化中的应用随着科技的不断发展,计算机辅助工程(Computer-Aided Engineering,简称CAE)仿真技术在各行各业都发挥着重要的作用。
在铸造行业中,CAE仿真技术尤为重要,它使得先进铸造工艺的优化成为可能。
本文将探讨CAE仿真技术在先进铸造工艺优化中的应用。
一、CAE仿真技术的概述CAE仿真技术是指利用计算机软件对工程产品进行虚拟试验和模拟分析的一种方法。
它可以模拟各种物理现象和工程过程,为工程师提供快速有效的优化方案。
在铸造行业中,CAE仿真技术可以通过数值计算和模拟来预测和优化铸造工艺,提高生产效率和产品质量。
二、CAE仿真技术在先进铸造工艺设计中的应用1. 浇注过程模拟在铸造工艺中,浇注过程对于最终产品的质量至关重要。
通过CAE 仿真技术,可以模拟铸造过程中的熔铁流动情况,预测铸件的形态及缺陷情况,并通过优化浇注过程,避免缺陷的产生,提高铸件的质量和产品寿命。
2. 温度场模拟在铸造过程中,铸件温度分布的均匀性直接影响到其力学性能。
通过CAE仿真技术,可以预测铸件在浇注后的温度场分布,根据这些数据进行优化设计,改善铸件的力学性能和耐用性。
3. 废品率优化在传统的铸造生产中,由于工艺参数的不准确性或操作失误,很容易产生大量的废品。
通过CAE仿真技术,可以对铸造工艺进行优化,降低废品率,提供合理的工艺参数和操作指导,从而降低原材料和能源的消耗,提高生产效率。
4. 疲劳寿命预测在一些应用领域中,如航空航天、汽车制造等,对于铸件的疲劳寿命要求较高。
通过CAE仿真技术,可以在铸造工艺设计阶段预测铸件的疲劳寿命,避免在产品研发后才发现问题,从而提前进行优化设计,节省时间和成本。
三、CAE仿真技术的优势与挑战CAE仿真技术在先进铸造工艺优化中具有以下优势:1. 节省时间和成本:相比传统的试验方法,CAE仿真技术可以在虚拟环境下进行快速准确的优化设计,避免了实际试验中的时间和成本消耗。
基于实例推理的模具设计技术研究

基 于实例 推理 的模 具 设 计 技 术研 究
戚 占龙 许建新 田锡天
( 西北 工业 大学 C P A P与 制造 工程软 件研 究 所 , 西安 7 0 7 ) 10 2
E ma le p 3 1 6 .o - i :a p 0 @1 3c r n
计 经 验 不 能 有效 的利 用 。
理 技 术 的 基础 。 计 实 例 的表 示 方 法 直接 关 系 到 推 理 的效 率 和 设
准 确 度 。 确 和 完 整地 表 达 设 计 实 例 是进 行 基 于 实 例 的模 具 设 准
计 的 重要 步骤 。本 文 应 用 状 态 空 间法 进 行 冲模 实例 表 示 。 在 冲模 设 计 中设 计 实 例 由部 件 、 组件 、 件 等 装 配 单元 组 。 零 零 件 是 构成 冲模 设 计 实 例 的最 小 单 元 。其 中 工 作 零 件 为 凸模 、 凹模 以及 凸 凹模 。 冲模 设 计 主要 是 对 凸 、 凹模 零 件 的刃 口尺 寸
文 章 编 号 10 — 3 1 (0 6 2 — o 3 0 文 献 标 识 码 A 0 2 8 3 一 2 0 )0 o 8 — 3 中图 分 类 号 T 1 P8
Ca e Ba e a o i g i o d De i n s - s d Re s n n n M l sg
Ab t a t s r c :Ol l r d c e in i h lf l i e n . a o a l ra ii g a d r u ig p e iu e in e p r n e d mo d p o u t d sg s ep u n n w o e Re s n b y o g n zn n e sn r vo s d sg x e e c i c n r d c h i f mod p o u t d s d i r v f ce c f mod p o u t d sg . hs p p r p e e t a C s - a e u e t e l e o l r d c e i a mp o e e i in y o l rd c e i T i a e r s n s a e f n g n n B sd a e Re s n n meh d o mod rd c d sg . tt s a e ao ig t o fr l p o u t e i S a e- p c me o i n h t d s s d o x r s d s c s . e e r s u e t e p s e i e n g a eT n a e t h n ih o lo t m y e o t e a tae y b s d n i l r y he r i e c b d, d h e c s i t e c e a e eg b r ag r h a t p f r r v l sr tg a e o smi i t o y s i e i at d s r e a t a e n h a b s i n s C l b t e e . i t o a e n a p i d s c e su l o mo d p o u t d sg f a kn f p n h a e r r v d T s me d h b e p l u c s f l t l rd c e i o i d o u c . l e i h h s e y n
- 1、下载文档前请自行甄别文档内容的完整性,平台不提供额外的编辑、内容补充、找答案等附加服务。
- 2、"仅部分预览"的文档,不可在线预览部分如存在完整性等问题,可反馈申请退款(可完整预览的文档不适用该条件!)。
- 3、如文档侵犯您的权益,请联系客服反馈,我们会尽快为您处理(人工客服工作时间:9:00-18:30)。
Int J Adv Manuf Technol (2002) 20:284–295Ownership and Copyright2002 Springer-Verlag London LimitedApplication of Case-Based Reasoning in Die-Casting Die Design 基于模型推理的铸造模具设计研究与应用K. S. Lee and C. Luo机械工程部,新加坡,英国东南部州新月国立大学, 新加坡本文所涉及的研究是基于模型推理(CBR)的铸造模具设计的一项研究。
不同于传统的铸造模具设计的CAD系统,这一个系统以知识和经验为基础, 修正了一些早先的理论,得到一种新的系统。
在解决问题的基础上,这个系统可以用积累的知识去解决新的问题,所以该系统能从经验知识中进行自我学习。
其工作包括:1.为铸造模具的设计发展提供以模型推理为基础的环境, 所以系统自己能够从先前的经验知识中进行自我学习,从而变得更有效率。
2.为有效率地重复使用早先的设计资源,需要发展有效的模型表现和改编方法学。
本文把重心集中在铸造模具的设计上。
然而,这种基于特定的程序特征和代码程序设计结构对其他的设计过程 (例如固定设计和注塑模具设计) 也是能够适应的。
关键词: 基于模型推理; 铸造模具; 参数化设计1. 引言铸造模具设计是一个反复设计的过程,需要积累经验知识和具有解决问题的能力。
当使用传统的CAD系统 (比如Pro-Engineer和Unigraphics)进行设计工作的时候,只能提供很少的帮助,利用传统的设计经验和资源是非常耗时的工作。
此外,模具的设计质量非常依赖于设计者的技术, 因为生产一种模具时,它需要材料知识,机器知识和操作的经验。
然而,在铸造模具设计中应用计算机辅助设计 (CAD) 技术,在很短的时间内已经发展的很广泛了。
伴随着铸造模具设计的智能化 (人工智能) 技术的发展,一些工人已经尝试在一个专家系统中储存设计知识和经验[1,2]. 然而,专家系统的发展由于以下原因受到限制: (1). 铸造模具设计的知识和经验是太复杂而无法使用简单的规则去表达。
(2). 它不能够在一个专家系统容易地表达。
(3). 它难以组织和认识特征。
近几年来, 基于模型推理的技术(CBR)[3]已经发展起来。
该技术不只有结果,也有设计观念和意图, 像是什么样的模型, 根据什么样的条件和如何获得这样一个结果。
一个CBR系统使用以前解决问题的方法来配合解决一个新的问题。
因为设计一个计算机辅助工程软件和应用一些修改似乎对人类是更明智和更直觉的,所以这是比运用一个模拟人的思想的专家系统更好的方法。
各种不同计算机辅助工程软件已经应用于很多的工作,比如注塑模具设计[4], 建筑设计[5,6], 固定物设计[7]和程序设计[8].我们打算构造CBR 设计环境应用于铸造模具设计。
为了取的以模型推理为基础用处达到最大程度,系统一定不能设计成一个单机系统,作为用于支持设计的所有阶段的统一的完整结构,应该开发和设计相关的不同数据资源去解决设计问题。
我们开发铸造模具设计的底部环境,是为了要了解它能如何被设计成为使用以推理为基础的计算机辅助工程软件。
这不仅仅是一个CBR系统,而且还有系统的设计环境。
CBR方法是一个应用于全部设计过程的一个具有支持性再可用性的设计方法。
它自身可以很容易的植入传统的设计规则和设计制度。
索引把重心集中在铸造模具设计并非模具的形状,所以软件知识库能有效率地而且正确地被搜寻,而且索引代码能容易地被定义而且延长。
最近的参数设计技术为计算机辅助工程软件所表现和改编采用, 使系统能实时运行改编。
2. 铸造模具设计的原则从产品设计的观点,铸造模具设计被描述为做出设计决定的一个解决问题程序, 评估他们的可应用性和做出那些必须的修改。
大体上,铸造模具设计者过去一直把设计问题分解为一系列的附属功能。
每个附属的功能可能根据一定被运行的功能,更进一步被分解的更简单的附属功能。
铸造模具的主要功能将熔化的金属铸造成一种完成的产品。
它通过一些具体的功能来表现, 形状和大小直接决定模具产品, 像是型腔和型芯等。
铸造模具也必须完成一系列的中级附属的功能 , 像是熔化的金属的流动,冷却和产品的成型。
通常这些中级的附属功能的结构和这些部件的形状不依赖于模具产品, 但是更重要的是,他们在不同的铸造模具的结构和形状通常是相似的。
它被估计超过 90% 的模具设计是以不同的设计为基础的[9]. 这意谓,当一个新的设计问题发生的时候,它通常是由修正现有的设计来解决这个问题,而不是从新设计解决问题。
从精密成度到高难度表现汽车部见,这是难以表示其特色和进行分类的,所以模具铸件以各种尺寸的大小和不同结构的类型生产。
模具产品的形状可能在特定的情况是复杂的和不同的,但是其结构和模具的成份总是相似的, 特别是产品的独立的成份。
因此,重复使用早先的设计方案是有重要价值的。
根据一定被实现的功能,铸造模具设计可以较进一步的分解,铸造模具设计能被区分为下列的设计组件[10]:浇注系统浇注系统是由变化的流道和连接零件不同部分表面的腔组成,它们的作用是让熔化的金属进入型腔。
它由注道,流道,浇口和溢流槽组成。
功能部件功能部件在铸造模具中包括型腔和芯模托板,插件、滑动器。
它们组成了型腔的内部结构和内外倒拔模系统。
脱模系统因为存在收缩现象,在打开铸造模具时产品容易黏住模具。
脱模系统根据不同的类型可以包括以下产品:脱模顶杆,脱模板,脱模环,扁顶杆,二级脱模系统。
冷却系统在冷却介质(水、油)流过冷却管道的帮助下,使模具保持在一个能使熔化金属凝固和安全脱模的温度。
标准件这些标准件包含所有的必需的模座、模块和正向流道衬套、分流道、合模销、脱模导引销、脱模板复位销等等。
3.系统的实现方式以基于事例推理的铸造模具设计(CBR)是在微软数据支持下的Window/NT窗口下运用C++来实现的一个CAD窗口系统,Solidworks,是用来开发参数化设计的环境。
然而,通过其他的CAD工具提供的使用者接口来实现这一系统也是可能的。
例如Unigraphics , SolidEdge 和 AutoCAD。
铸造模具的设计流程在图5所示:图表5.基于模型推理的铸造模具设计流程表(1). 模型的准备在产品模型从模型库中或其他地方取得后,系统的数值需要被设定。
它们包括:材料的选择,收缩率的设定,型体的设计,型腔的布置。
(2). 模型的取回关于索引,设计者需要在产品的外型和其模具的其他重要特征做出一系列的选择。
基于这些选择,设计问题将被自动的编入索引并通过索引代码显示出来。
相似的设计通过索引代码被取回。
取回的过程是通过搜索模型代码中的前两位数字来实现的。
所有前两位数字相同的方式来实现的。
所有前两位数字相同的模型由于它们是相同的而被归为一组,在这一组中通过后面的数字再进行搜寻,直到最相似的模型被取回。
这是设计者必须选择最合适的模型存于模型组中。
由于从这种选择中不会只得到一种结果,就必须以较低的要求在运行一次。
这意味着设计者从早先的选择中选取一个特征,以它作为一个较低的水平从模型库中取回一个相似的模型。
(3). 模型改编系统首先修正取回来的模型,看是否可以满意的解决问题。
如果是,新的解决方案就成功了:如果不是,系统将会从模型库中重新搜索再取回一个新的包含合适的替代模型。
这个过程将会持续到一个满意的结果产生。
(4). 模型的存储当这个系统遇到新的问题,并通过改变以前的,偶像而解决这个问题时,系统自身能够学习和积累这些经验。
新的模型和替代模型被存储在改编库中。
4. 结论CBR作为一种解决问题的方法学,已经在很多难以获得知识的领域发展起来。
在研究过程中,我们增强了这种方法的作用,使它成为了一种专门应用于铸造模具设计的单一应用系统。
这是和SolidWorks API一同完成的。
这一个系统的主要能力是: (1).模型的取回和特征描述是基于产品几何学和模具结构实现的。
这意味着在模型库中搜寻和取出相似的设计是可行的和有效的。
(2).模型的描述和修改是基于参数化设计,工作台驱动设计和结构汇编实现的。
因此系统能够记录和存储设计者的意图和经验。
(3).通过构建模型库,先前的经验可以被存储,并且系统还可以通过新的模型达到自我学习的目的。
原型系统通过帮助设计者提高效率和积累先前的设计资源而得到发展。
由以上的表述,早期的设计经验被积累和存储,由此可以缩短设计周期和简化设计过程。
模型修改的困难是是否能够取回一个相似的模型,并且取回的相似模型是否建立在索引规则的基础上。
在真正的铸造模具设计中增加的特征必须要考虑,包括产品几何学,模具的结构,材料和铸造机器。
在提到的索引中,仅仅学派几何学和模具结构被考虑了。
所以取回的仅仅是原型,必须得到进一步的修改和定义。
参考文献[1]. B. T. Cheok, K. Y. Foong, A. Y. C. Nee and C. H. Teng, “Some aspects of a knowledgebased approach for automating progressive metal stamping die design”, Computers inIndustry, 24, pp. 81–96, 1994.[2]. Z. C. Lin and H. Chang, “An investigation of expert systems for die design”, Journal ofIntelligent Manufacturing, 5, pp. 177–192, 1994.[3]. A. Voss, “Case reusing systems –survey, framework and guidelines”, KnowledgeEngineering Review, 12(1), pp. 59–89, 1997.[4]. C. K. Kwong, G. F. Smith and W. S. Lau, “Application of case based reasoning ininjection molding”, Journal of Mat erials Processing Technology, 63, pp. 463–467, 1997.[5]. K. Hua and B. Faltings, “Exploring case-based design –CADRE”, Artificial Intelligencein Engineering Design, Analysis and Manufacturing, 7, pp. 135–144, 1993.[6]. I. Smith, C. Lottaz and B. Faltin gs, “Spatial composition using cases: IDIOM”,Proceedings of First International Conference on Case-Based Reasoning”, pp. 88–97,Springer, Berlin, 1995.[7]. S. H. Sun and J. L. Chen, “A fixture design system using case based Reasoning”,Engineering Applications of Artificial Intelligence, 9(5), pp. 533–540, 1996.[8]. B. Humm, Ch. Schulz, M. Radtke and G. Warnecke, “A system for case-based processplanning”, Computers in Industry, 17, pp. 169–180, 1991.[9]. J. L. Encarnacao, R. Lindner and E. G. Schlechtendahl, Computer-Aided Design, Springer,1990.[10]. E. A. Herman, “Die casting dies: designing”, Rosemont, Ill.: North American DieCasting Association, 1992.[11]. I. Watson, “Case-based reasoning is a methodology not a technology”,Knowledge-Based Systems, 12, pp. 303–308, 1999.[12]. N. C. Suresh and J. M. Kay, Group Technology and Cellular Manufacturing, Kluwer,1998.[13]. T. C. Chang, Richard A. Wysk and H. P. Wang, Computer-Aided Manufacturing,Prentice-Hall, 1998.[14]. I. Watson, Applying Case-Based Reasoning: Techniques for Enterprise Systems, MorganKaufmann, 1997.。