2020年压力容器及管道制造安装焊接规范
容器焊接规范

钢制压力容器焊接规程JB/T 4709—2000关于发布《钢制压力容器焊接工艺评定》等四项行业标准的通知国机管[2000]401号各有关单位:根据国家质量技术监督局规定的压力容器行业标准审批程序,现发布《钢制压力容器焊接工艺评定》等四项行业标准,编号与名称如下:强制性标准:JB 4708—2000 钢制压力容器焊接工艺评定(代替JB 4708—1992)JB 4710—2000 钢制塔式容器(代替JB 4710—1992)JB 4744—2000 钢制压力容器产品焊接试板的力学性能检验(代替GB 150—1998附录E)推荐性标准:JB/T 4709—2000 钢制压力容器焊接规程(代替JB/T 4709—1992)以上标准于2000年10月1日起实施,其出版发行工作责成全国压力容器标准化技术委员会按期组织完成。
2000年8月15日前言本标准对JB/T 4709—1992进行修订。
本标准依据JB/T 4709—1992实施以来所取得的经验,参照近期国际同类标准进行了下列变动:1 增加附录A“不锈钢复合钢焊接规程”和附录B“焊接工艺规程推荐表格”。
2 第3章增加了如下内容:①焊材选用并应通过焊接工艺评定要求;②从GB/T 5118选用焊条的规定;③表1和表3增加了一些钢号;④增加了表2。
3 第5章增加了表4,表5增加了一些钢号。
4 第8章增加了焊后热处理厚度的规定。
表6中增加了一些钢号,调整了焊后热处理温度;增加了表7。
本标准从实施之日起,代替JB/T 4709—1992。
本标准的附录A是标准的附录。
本标准的附录B是提示的附录。
本标准由全国压力容器标准化技术委员会提出,由全国压力容器标准化技术委员会制造分委员会归口。
本标准负责起草单位:合肥通用机械研究所、锦西化工机械厂和大连石油化工设计院。
本标准主要起草人:戈兆文、龙红、严国华。
参加本标准编制的工作单位及人员有:中国石化集团公司咨询公司:寿比南、杨国义。
压力容器制造焊接相关技术标准及要求

压力容器制造焊接相关技术标准及要求川化集团有限责任公司化工设备厂《钢制化工容器制造技术要求》摘录5. 焊接和切割5. 1切割5. 1. 1采用火焰切割下料时,应清除熔渣及有害杂质,并采用砂轮或其它工具将坡口加工平整。
当切割材料为标准规定的抗拉强度(T b>540MPa的高强度钢或铬钼合金钢时,火焰切割表面应采用打磨或机械加工的方法清除热影响区和淬硬区,并进行磁粉或渗透探伤。
不锈钢的碳弧气刨表面应采用砂轮打磨,清除渗碳层。
5. 1. 2火焰切割时的预热与否,一般应符合钢材焊接时的预热要求。
受压元件气割的开孔边缘或剪切下料的端部如未经焊接者(如安放式接管的开孔边缘或内伸式接管的端部),应采用打磨等方法去除3mm以上。
5. 2焊缝位置5. 2. 1壳体上的开孔应尽量不安排在焊缝及邻近区域,但符合下列情况之一者,允许在上述区域开孔:1. 符合GB150开孔补强要求的开孔可在焊缝区域开孔。
2. 符合GB150规定的允许不另行补强的开孔,可在环焊缝区域开孔。
但此时应以开孔中心为圆心,对直径为3倍开孔直径长度的圆所包括的焊缝进行100%射线或超声波探伤,并符合要求。
凡因开孔而可予去除的焊缝可不受探伤质量的影响。
3. 符合GB150规定的允许不另行补强的开孔,当壳体板厚小于等于40mm时,开孔边缘距主焊缝的边缘应大于等于13mm。
但若按5.2.1条第一款对主焊缝进行射线或超声波探伤并符合要求者,可不受此限。
5. 2. 2外部附件与壳体的连接焊缝,如与壳体主焊缝交叉时,应在附件上开一槽口,以使连接焊缝跨越主焊缝。
槽口的宽度应足以使连接焊缝与主焊缝边缘的距离在1.5倍壳体壁厚以上。
5. 3焊接准备5. 3. 1焊接坡口及其两侧至少15mm内的母材表面应消除铁锈、油污、氧化皮及其它杂质。
铸钢件应去除铸态表面以显露金属光泽。
5. 3. 2气割坡口的表面质量至少应符合下表的要求。
5. 3. 3坡口上的分层缺陷应予以清除,清除深度为分层深度或10mm (取小者), 并予以补焊。
2020年压力容器及管道制造安装焊接规范

(情绪管理)压力容器及管道制造、安装焊接规范适用范围:本标准适用于压力容器(塔、换热器、贮槽、吸附器等)及管道的焊接(包括压力容器及管道的部件、管件等)。
本规范要求不仅适用于本厂产品制造,也适用于现场安装。
一、要求:容器、管道制造及安装中除必须遵循本标准规定的基本要求外,仍必须遵循有关国标、部标、产品图样的技术要求、用户于合同中提出的技术要求及其有关技术文件的规定等。
二、图样:1、各类压力容器图样和技术文件应符合《压力容器图样和技术文件要求的暂行规定》外,于总图上必须注明:1)容器的类别、名称、容积、(几何容积)设计温度、设计压力介质、主要受压元件的材质、焊缝系数和腐蚀裕度等;2)制造和安装所依据的技术标准代号和标准名称;3)耐压试验、气密试验和检验要求;4)特殊技术要求,如钢板探伤、焊后热处理及容器安装使用说明等;5)每条焊缝(不受力构件或容器外支座等的焊缝采用标注焊接符号者除外)均编焊缝号码。
2、管道图样上必须载明:1)各条焊缝按GB324-80《焊缝代号》规定,标注焊接符合;2)管道设计压力设计温度、介质、材质、焊缝系数等;3)检验要求。
压力容器焊接工艺由专职焊接工程师负责制订,且监督实施。
现场安装的焊接技术要求,壹般应由本厂提出,且委派专门人员或由安装单位指定专人负责指导、监督、执行、检查。
如遇重大技术问题,由用户、安装单位及本厂共同协商解决。
三、对容器、管道结构上的要求:容器管道的结构设计除必须符合壹机部、石油部、化工部颁发的《钢制石油化工压力容器设计规定》及有关标准的规定外,焊缝设计应考虑制造时便于焊接,且应考虑便于无损探伤,且使气密性试验时便于观察、检漏。
1、固定的全位置焊缝打底层以及仅能进行单面焊的铝容器、管道的环焊缝应采用嵌入环式的不锈垫板焊。
2、不等厚度焊件的对接焊,较厚壹侧的板材应作14°削薄。
铝焊件厚壁的过滤应带有壹段(至少为25mm)的园颈,于其余应符合JB741-80《钢制焊接压力容器技术条件》和JB1580-75《铝制焊接容器技术条件》的有关规定。
压力钢管制造安装及验收规范

压力钢管制造安装及验收规范随着工业工程的发展,压力容器的应用越来越广泛。
而在压力容器中,压力钢管是一种常见的结构元件,它承受着高压力的工作环境,因此压力钢管制造、安装及验收规范显得尤为重要。
一、压力钢管制造规范1. 材料选择:在压力钢管制造中,材料的选择十分重要。
压力钢管所使用的材料应具备良好的耐腐蚀性、高强度、高温性能、良好的可焊接性等特点。
一般来说,高压力容器中使用的主要材料包括碳素钢、合金钢、不锈钢等材料。
2. 制造工艺:压力钢管的制造工艺非常复杂,需要严格遵守相应的制造规范和标准。
制造前必须进行材料的热处理、预处理等步骤。
对于焊接的部分,必须严格控制焊接质量,在制造过程中必须遵循电极消耗量、电弧电压、接头几何形状等方面的标准。
3. 检测和检验:制造完成后,必须进行一系列检测和检验,确保所制造的产品质量符合标准和规范。
常用的检测方法包括X射线检测、磁粉检测、压力试验、热处理试验等。
二、压力钢管安装规范1. 安装前的准备工作:在开始安装压力钢管前,必须准备好相关的工具设备,并确保安装环境符合安全要求。
此外,还需要对压力钢管的防腐、绝缘、保温等相关处理进行检查。
2. 安装流程:安装过程中要严格按照规范和标准进行操作,确保安全可靠。
常见的安装流程包括布置、调整、焊接等过程。
在安装过程中必须防止因设备运转而产生的冲击力和振动对压力管道产生的影响。
3. 安装验收:安装完成后要进行安装验收。
应当严格按照验收标准进行检查。
主要检查内容包括焊缝质量、紧固件是否牢固、管道是否有漏气、管道内壁是否干净、导线是否正确连接、附件是否安装到位等。
三、压力钢管验收规范1. 检测应符合标准,测试设备应具有准确性和精度。
2. 在进行压力测试时,必须对压力钢管及相关附件的饱和液体进行处理。
在液位高度的控制、压力的保持、溢出口的控制等方面,必须按照相关规范要求进行操作。
3. 系统升压测试时,必须按照系统压力试验方案的要求进行操作。
压力容器焊接技术要求
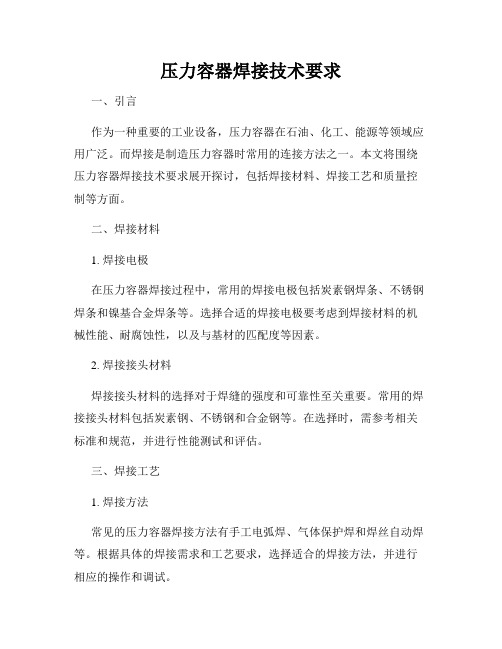
压力容器焊接技术要求一、引言作为一种重要的工业设备,压力容器在石油、化工、能源等领域应用广泛。
而焊接是制造压力容器时常用的连接方法之一。
本文将围绕压力容器焊接技术要求展开探讨,包括焊接材料、焊接工艺和质量控制等方面。
二、焊接材料1. 焊接电极在压力容器焊接过程中,常用的焊接电极包括炭素钢焊条、不锈钢焊条和镍基合金焊条等。
选择合适的焊接电极要考虑到焊接材料的机械性能、耐腐蚀性,以及与基材的匹配度等因素。
2. 焊接接头材料焊接接头材料的选择对于焊缝的强度和可靠性至关重要。
常用的焊接接头材料包括炭素钢、不锈钢和合金钢等。
在选择时,需参考相关标准和规范,并进行性能测试和评估。
三、焊接工艺1. 焊接方法常见的压力容器焊接方法有手工电弧焊、气体保护焊和焊丝自动焊等。
根据具体的焊接需求和工艺要求,选择适合的焊接方法,并进行相应的操作和调试。
2. 焊接参数焊接参数是指焊接过程中需要控制和调节的因素,包括焊接电流、电压、焊接速度和焊接通道等。
合理的焊接参数能够确保焊接质量和焊缝的可靠性。
3. 焊接顺序在进行压力容器焊接时,需要考虑焊接顺序的合理安排。
一般情况下,焊接应从中心部位向四周进行,逐渐将焊接缝填满,并注意热输入的均匀分布,以避免产生过大的焊接变形和内应力。
四、质量控制1. 焊接前的准备工作在进行焊接前,应对焊接部位进行充分的清洁和除锈处理,确保焊接面无杂质和氧化物。
同时,还需进行预热处理,以减少焊接变形和冷裂纹的风险。
2. 焊接过程中的质量控制焊接过程中,要进行严格的质量控制,包括焊缝的准备、热输入的控制、焊接参数的实时监测和焊接表面的保护等。
同时,焊接人员应熟悉焊接工艺规范,确保焊接过程的连续性和稳定性。
3. 焊后处理和检测焊接完成后,需进行焊后热处理和检测工作。
热处理能够恢复焊接材料的力学性能,并减少残余应力;而焊缝检测则能够评估焊接质量和焊缝的可靠性,常用的方法包括无损检测和金相检测等。
五、总结压力容器焊接技术要求是确保制造出安全可靠的压力容器的基础。
压力容器焊接标准
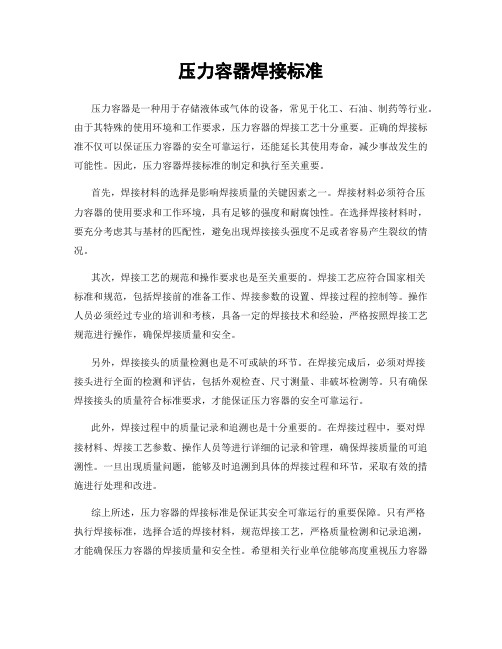
压力容器焊接标准压力容器是一种用于存储液体或气体的设备,常见于化工、石油、制药等行业。
由于其特殊的使用环境和工作要求,压力容器的焊接工艺十分重要。
正确的焊接标准不仅可以保证压力容器的安全可靠运行,还能延长其使用寿命,减少事故发生的可能性。
因此,压力容器焊接标准的制定和执行至关重要。
首先,焊接材料的选择是影响焊接质量的关键因素之一。
焊接材料必须符合压力容器的使用要求和工作环境,具有足够的强度和耐腐蚀性。
在选择焊接材料时,要充分考虑其与基材的匹配性,避免出现焊接接头强度不足或者容易产生裂纹的情况。
其次,焊接工艺的规范和操作要求也是至关重要的。
焊接工艺应符合国家相关标准和规范,包括焊接前的准备工作、焊接参数的设置、焊接过程的控制等。
操作人员必须经过专业的培训和考核,具备一定的焊接技术和经验,严格按照焊接工艺规范进行操作,确保焊接质量和安全。
另外,焊接接头的质量检测也是不可或缺的环节。
在焊接完成后,必须对焊接接头进行全面的检测和评估,包括外观检查、尺寸测量、非破坏检测等。
只有确保焊接接头的质量符合标准要求,才能保证压力容器的安全可靠运行。
此外,焊接过程中的质量记录和追溯也是十分重要的。
在焊接过程中,要对焊接材料、焊接工艺参数、操作人员等进行详细的记录和管理,确保焊接质量的可追溯性。
一旦出现质量问题,能够及时追溯到具体的焊接过程和环节,采取有效的措施进行处理和改进。
综上所述,压力容器的焊接标准是保证其安全可靠运行的重要保障。
只有严格执行焊接标准,选择合适的焊接材料,规范焊接工艺,严格质量检测和记录追溯,才能确保压力容器的焊接质量和安全性。
希望相关行业单位能够高度重视压力容器焊接标准,加强管理和监督,确保压力容器的安全运行,为生产和人员安全提供有力保障。
2020年压力容器的标准

(情绪管理)压力容器的标准1.3压力容器规范标准目的:确保压力容器于设计寿命内安全运行内容:材料、设计、制造、检验等性质:法规,必须遵守特点:定期补充、修改,用新规范1.3.1国外主要规范标准简介:美国A S M E规范、日本压力容器标准、欧盟压力容器标准1、美国A S M E规范目前A S M E规范共有十二卷包括锅炉、压力容器、核动力装置、焊接、材料、无损检测等内容。
A S M E规范每三年出版壹个新的版本,每年有俩次增补。
于形式上,A S M E规范分为4个层次:规范(C o d e)、规范案例(C o d e C a s e)、条款解释(I n t e r p r e t a t i o n)、规范增补(A d d e n d a)A S M E规范中和压力容器设计有关的主要是第Ⅷ篇《压力容器》、第Ⅶ篇《移动式容器建造和连续使用规则》和第Ⅹ篇《玻璃纤维增强塑料压力容器》。
第Ⅷ篇分为3个册:第1册《压力容器》第2册《压力容器——另壹规则》第3册《高压容器另壹规则》简称A S M EⅧ-1、A S M EⅧ-2和A S M EⅧ-3A S M EⅧ-1A S M EⅧ-1为常规设计标准,适用压力小于等于20M P a;它以弹性失效设计准则为依据,根据经验确定材料的许用应力,且对零部件尺寸作出壹些具体规定。
由于它具有较强的经验性,故许用应力较低。
A S M EⅧ-1不包括疲劳设计,但包括静载下进入高温蠕变范围的容器设计。
A S M EⅧ-2A S M EⅧ-2为分析设计标准,它要求对压力容器各区域的应力进行详细地分析,且根据应力对容器失效的危害程度进行应力分类,再按不同的安全准则分别予以限制。
跟A S M EⅧ-1相比,A S M EⅧ-2对结构的规定更细,对材料、设计、制造、检验和验收的要求更高,允许采用较高的许用应力,所设计出的容器壁厚较薄。
A S M EⅧ-2包括了疲劳设计,但设计温度限制于蠕变温度以内。
压力容器焊接规程
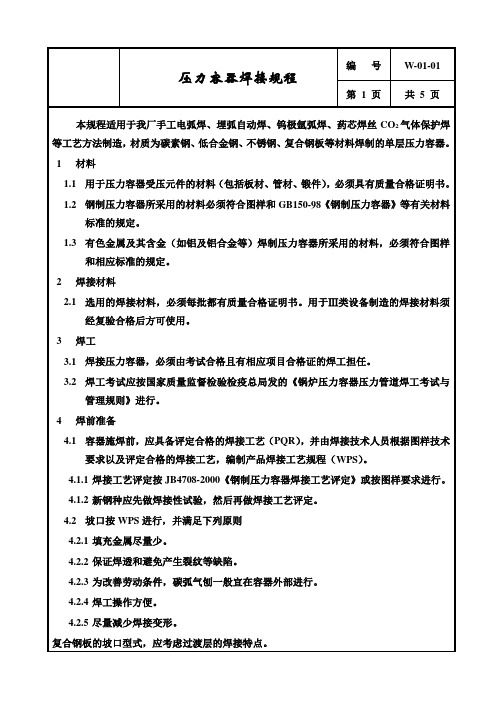
4.6装配点固焊
4.6.1装配点固焊一般应使用与焊接时相同牌号的焊条,并应相同。预热范围:点固焊道的周围,距点固焊道周边3倍工件厚度且不小于100mm的范围内。测温部位:位于距点固焊道周边50mm处。
7返修
7.1焊缝返修会降低产品质量,因此焊工在施焊过程中,应精心操作,尽量提高一次合格率,避免返修。
7.2焊缝返修按《焊缝返修工艺守则》进行。
7.3焊缝同一部位的返修次数不宜超过两次。
7.4对经过两次返修仍不合格的焊缝,需经质保工程师批准才能再返修。
7.5对于裂纹缺陷,应进行质量分析,找出原因,制订相应技术措施或交底后方可返修。
4.6.3点固焊道有裂纹时,必须清除重焊。
4.7严禁在非焊接部位引弧,如发生打弧,须将弧坑按施焊工艺条件补焊、磨平。
4.8当焊接工艺要求焊前预热时,按本规程第6条进行焊前预热。
4.9电源的接地线应与工件可靠的连接,保证导电良好防止打弧现象。
4.10为了防止焊接裂纹和减少内应力,装配时要避免强行组装。
6.5.3后热应在焊后立即进行。
6.5.4工艺文件的后热标注:
应注为a℃×bh,其中a表示后热温度
b表示保温时间,h代表小时
例:某工件,要求焊后200℃,保温1小时30分,注为200℃×1.5h。
压力容器焊接规程
编号
W-01-01
第4页
共5页
6.6产品的焊后热处理必须WPS要求或产品热处理方案(技术措施)进行。产品焊接试板必须与产品同炉热处理。
4.2坡口按WPS进行,并满足下列原则
- 1、下载文档前请自行甄别文档内容的完整性,平台不提供额外的编辑、内容补充、找答案等附加服务。
- 2、"仅部分预览"的文档,不可在线预览部分如存在完整性等问题,可反馈申请退款(可完整预览的文档不适用该条件!)。
- 3、如文档侵犯您的权益,请联系客服反馈,我们会尽快为您处理(人工客服工作时间:9:00-18:30)。
(情绪管理)压力容器及管道制造、安装焊接规范适用范围:本标准适用于压力容器(塔、换热器、贮槽、吸附器等)及管道的焊接(包括压力容器及管道的部件、管件等)。
本规范要求不仅适用于本厂产品制造,也适用于现场安装。
一、要求:容器、管道制造及安装中除必须遵循本标准规定的基本要求外,仍必须遵循有关国标、部标、产品图样的技术要求、用户于合同中提出的技术要求及其有关技术文件的规定等。
二、图样:1、各类压力容器图样和技术文件应符合《压力容器图样和技术文件要求的暂行规定》外,于总图上必须注明:1)容器的类别、名称、容积、(几何容积)设计温度、设计压力介质、主要受压元件的材质、焊缝系数和腐蚀裕度等;2)制造和安装所依据的技术标准代号和标准名称;3)耐压试验、气密试验和检验要求;4)特殊技术要求,如钢板探伤、焊后热处理及容器安装使用说明等;5)每条焊缝(不受力构件或容器外支座等的焊缝采用标注焊接符号者除外)均编焊缝号码。
2、管道图样上必须载明:1)各条焊缝按GB324-80《焊缝代号》规定,标注焊接符合;2)管道设计压力设计温度、介质、材质、焊缝系数等;3)检验要求。
压力容器焊接工艺由专职焊接工程师负责制订,且监督实施。
现场安装的焊接技术要求,壹般应由本厂提出,且委派专门人员或由安装单位指定专人负责指导、监督、执行、检查。
如遇重大技术问题,由用户、安装单位及本厂共同协商解决。
三、对容器、管道结构上的要求:容器管道的结构设计除必须符合壹机部、石油部、化工部颁发的《钢制石油化工压力容器设计规定》及有关标准的规定外,焊缝设计应考虑制造时便于焊接,且应考虑便于无损探伤,且使气密性试验时便于观察、检漏。
1、固定的全位置焊缝打底层以及仅能进行单面焊的铝容器、管道的环焊缝应采用嵌入环式的不锈垫板焊。
2、不等厚度焊件的对接焊,较厚壹侧的板材应作14°削薄。
铝焊件厚壁的过滤应带有壹段(至少为25mm)的园颈,于其余应符合JB741-80《钢制焊接压力容器技术条件》和JB1580-75《铝制焊接容器技术条件》的有关规定。
3、压力容器的单面焊缝不作封底焊时,应设法对焊根部进行外观检查或按规定要求进行无损探伤。
4、避免焊缝集中或形成十字焊缝。
容器俩相邻筒节的纵缝须互相错开,其间距应大于3倍壁厚且不小于100毫米弧长,管道相邻俩节的纵缝应错开大于50毫米弧长。
5、避免焊缝及其附近(小于3倍壁厚的距离内)开孔,如必须开孔者,则应于待开孔中心俩侧各不小于1.5倍开孔直径的范围内进行100%的无损探伤。
6、不得于容器、管道的纵、环焊缝上再焊接其他另件。
若必须焊另件者,和其焊缝距离至少应大于3倍壁厚且不得小于50毫米。
7、容器上的接管、管道支管和主管的相贯焊缝应尽量采用双面焊,且保证焊透或刨(铲)至完好金属。
8、角焊缝和母材应有园滑过滤。
四、对安装单位的要求:安装单位必须配备合格而可靠的焊接设备、无损探伤及材料试验设备(也可委托其他单位进行检验及试验工作)。
配备相应合格的焊接检验人员和焊接技术人员。
若安装单位将焊接工作分包或委托其他单位承担者,则受委托单位变符合规程的规定。
如焊后需热处理,则仍必须配备相应而可靠的热处理设备。
且提供实测温度记录。
同时附测温仪器、设备的计量机关检查鉴定合格证。
于下雨(下雪)、有风或相对湿度>80%的露天作业情况下进行焊接时,须有适当的防护措施。
五、焊接技术人员:安装单位或由本厂派出的焊接技术人员,应对焊接工艺和所焊材料有足够的知识和经验。
其职责是:执行焊接技术文件(如有关焊接规程、规范、焊接工艺要求等);对焊工进行培训和考核;对焊工给予明确的技术指导;解决制造或安装中的焊接技术问题;参和分析、裁决焊缝返修和焊接质量事故。
焊接技术人员有权制止违反工艺规程(范)和工艺纪律的操作,且对不合格的焊缝提出返修或报废处理意见;有权处理材料代用等问题且对其正确性负责;有权提出和采取必要的技术措施,以保证焊接质量。
焊接技术人员应逐月、逐项记录安装单位及每个焊工的焊工的焊缝壹次合格率(或焊缝返修率)。
安装过程中的焊接技术总是如遇有分歧时,应由用户、安装单位及本厂有关人员共同研究(或试验)协商解决。
六、焊工:制造厂或安装单位的焊工,必须按国家劳动人事部颁发的“锅炉及压力容器焊工考试规则“的要求进行培训、考核,且取得合格证。
对于铝及其合金的氩弧焊工及担任特殊工作(如特殊材料、特殊位置或方法等)的焊工,则应根据具体情况,由焊接技术人员确定考试项目和要求。
本标准附表中的规定系指安装管道焊工手工焊的必考项目和要求。
制造厂有责任委派代表或由安装单位指派焊接技术人员,对安装焊工的手工焊进行考核,经考核合格后,方允许担任安装的焊接工作。
制造玫应参和检查安装焊接质量。
七、焊接工艺评定:于制作及安装容器、管道之前,应对所采用的焊接材料、焊接工艺、规范参数等进行焊接工艺评定,以证实制造或安装单位对这壹焊接方法能否保证质量。
焊接工艺评定应符合国家劳动人事部“压力容器安全监察规程”的规定要求,于执行过程中允许按有关标准制订实施细则。
八、焊接填充金属:应根据线母材成份、机械性能、工艺性能及工件使用条件等合理选择焊接填充金属。
焊条(焊丝)入库时必须具有材质证明,且按有关标准要求进行各项复验。
焊条应按规定温度经烘干使用,且保证干燥贮藏。
焊丝则应于焊前进行去油(锈)、清理(或清洗)随后于干燥条件下存放。
储藏室允许焊工仅领取壹天工作所需的焊条(焊丝),每天工作后所剩余的焊条(焊丝)须于下班前归仍储藏室。
焊接材料的代用时,均须办理代用手续,等焊接技术人中同意(须考虑是否重新进行焊接工艺评定)后方可代用。
九、焊接辅助材料:焊接用保护气体必须具有合格证或成份分析单,且符合气体标准的规定;焊剂(药)等均须具备质量证明书(或合格证),且按规定烘干后使用。
十、坡口加工:管道及容器(指本厂设计、制造的压力容器)的焊接坡口由焊接技术人员根据标准、焊接工艺评定合理选用,且于图样上注明,继而制订焊接工艺卡(管道可不专门制订焊接工艺卡)。
采用火焰或等离子切割加工的焊接坡口,焊前应对坡口进行打磨或机械加工;焊前应清理焊接区的锈污、氧化物、油漆、油污、水份等杂质;焊接检验员应于施焊前检查坡口的加工及清理(洗)质量,对不合要求的坡口等有权提出返工或焊接区的再清理(洗)意见。
十壹、焊前准备:焊接检验人员应检查对接焊缝的对口错边量应符合JB41-80及JB1580-75等有关标准的规定。
应保护焊接区不受恶劣气候(如寒冷、风和雨雪)的影响。
于+5℃以下的环境温度下进行焊接、切割时要采取适当措施(如预热、加热和搭棚遮挡)。
以保证焊接所要求的温度、湿度。
焊前搭地线应夹持可靠,不得将搭铁焊于工件或浮摆于工件上。
采用裸焊丝进行焊接时,焊工应戴手套,手套上不得有油漆、油、水或其他脏物。
十二、预热:根据材料性质和焊缝截面的不同,确定是否进行焊前预热,预热规范应于焊接工艺卡或其他有关技术文件中予以规定。
焊接时需预热的材料,于定位焊前亦应按工艺要求进行预热。
预热温度均应进行检测,可用测温毛或热电偶温度计测温。
十三、定位焊:应由考核合格的焊工进行定位焊。
定位焊焊缝隙必须无裂纹。
定位焊缝上如有裂纹不得采用焊接方法封盖,而应将焊缝磨光,且采用和打底焊道相同的焊接方法重焊。
定位焊所用的填充材料应和基本焊缝相同。
十四、装配用卡具、定位件等的焊接:对焊后易造成不良影响的材料应避免采用焊接卡具或定位件等。
必要时,最好使用比母材强度低且适于焊接的材料,使用和其相应的填充金属,将其焊接于工件上,如母材焊时需预热,则定位件、卡具等的焊接也须相应进行预热。
于去除定位件前,应先将焊缝磨平;敲去定位件时,不得损伤工件表面,于去除定位后应将残留焊缝磨光。
根据材料及工件的技术要求,必要时需对上述焊接部位进行着色(或磁粉)检验。
十五、焊接:受压部位诸焊缝的焊接均应和相应的焊接工艺评定壹致。
所有对接焊缝不允许产生大于母材负偏差值深度的缺陷且应设法消除上述缺陷。
于多层焊时,每层焊缝表面可见缺陷应仔细清除且修磨后再焊下壹层。
工件表面不得有打弧点,如若发生者,则须补焊或修磨。
焊缝表面应清除焊渣及飞溅,必要时须用砂轮打磨。
角焊缝应按平或凹形表面进行焊接,应避免过高的角焊缝。
角焊缝厚度按图样标注,若未标注数据者,则其厚度近较小壁厚的0.7倍计算。
于焊接中断和结束时,应特别注意保证接头及收弧处无缺陷。
应尽量避免于焊后进行修整,当须进行修整时,修整工作应于热处理前进行。
修整不得使母材强度和焊缝的质量下降。
若对焊缝质量有疑虑时,应取试件进行检查。
十六、焊后热处理焊后热处理应根据材质和壁厚、结构、焊条填充金属的成份、焊接条件、强度特性、无损探伤检验百分比及工件使用条件而定(有时仍应考虑附加条件的要求)。
热处理须按有关规程及材料和焊条(焊丝)制造厂的规定(或推荐)要求制订专门的热处理工艺规范。
不同材质焊接接头须根据产品要求和结构特点进行试验以确定正确的焊后热处理规范。
产品焊后热得处理时,其焊接试样板均须产品同炉进行。
各种热处理规范和参数均须做好记录。
最终热处理后的工件不得再进行焊接,特殊情况确需焊接者,必于经主管技术负责人批准。
十七、焊缝标志:每条焊缝焊毕应清晰地标上施焊焊工的印记(焊工号)及焊缝拍片号。
标记可采用钢印或刻写等。
十八、焊缝的检验:焊接接头的抽验比例、检验方法和评定要求应根据图样及有关标准规定。
有无损探伤要求,且只能进行单面焊的厚壁件焊缝,于完成打底焊层和第2层焊缝后,须进行射线探伤经过外观检查合格后方可进行射线探伤。
用于破坏性试验的焊接试样的热处理状态必须工件最后热处理相壹致。
凡参加安装的焊工,最初焊接的5条焊缝须作100%射线检查,以确定其焊接资格和技能是否符合要求。
安装X公司于管道安装中允许最高焊缝返修率(指返修焊缝长度和拍片焊缝总长度之百分比)为5%,而每壹个焊工允许最高为8%,每拍20张片,求壹次返修率。
如安装X公司焊缝返修率于5~10%之间,或每壹个焊工于8~16%之间,则拍片应加倍,于超过10~16%时,则全部焊缝应100%进行射线检验。
所有焊缝检验结果,包括焊缝返修应作记录,且应列入产品检验方案中。