05 防错控制程序
CX05纠正及预防措施程序_商业项目程序文件

1.0 目的为避免不合格的再次发生,防止潜在不合格或不符合的发生,使质量环境职业健康安全管理体系不断完善和持续改进,特建立本程序。
2.0适用范围适用于对不合格或不符合和潜在不合格的纠正、预防措施的制定、实施与验证活动。
3.0职责3.2.1责任部门经理组织本部门纠正/预防措施的制定、实施和检查。
3.2.2安全品质部负责验证纠正/预防措施的可行性、实施情况与效果,保存相关验证记录;协助总经理组织重要或跨部门纠正/预防措施的制定、实施和检查。
3.2.3总经理负责审批《纠正及预防措施报告》,监督和协调措施的实施,组织重大纠正/预防措施的制定和实施。
4.0程序要点及实施4.1纠正、预防措施的制定4.1.1下列情况之一时,应制定纠正措施:(1)设备、设施由于维护检修不及时或未达到适用要求而影响服务质量48小时及以上时;(2)发生治安、刑事案件、突发环境、安全事故时;(3)检查/审核发现严重不合格时;(4)顾客的投诉符合严重不合格条件时;(5)对不合格进行了评审时;(6)环境、职业健康安全行为严重违反法规时。
4.1.2下列情况之一时,应制定预防措施:(1)当服务质量发生周期性、系统性波动,如不采取措施有可能导致不合格发生时;(2)内部质量审核、管理评审指出的潜在不合格的问题;(3)质量体系运行不畅发生“有事无人管理”或“工作推托、扯皮”时;(4)对顾客的意见、建议、抱怨、期望进行分析,需采取措施以满足顾客的需要和期望时;(5)新增重要环境因素及危险源时。
4.2制定纠正/预防措施的基本要求4.2.1必须分析实际和潜在的原因。
4.2.1.1纠正:对于已发现的不合格采取措施改正,以消除不合格现象。
4.2.1.2纠正措施:对于已发现的不合格分析原因,采取措施,以消除产生不合格原因,防止不合格的再次发生,纠正措施应与所遇到的问题的影响相适应。
4.2.1.3预防措施:对于潜在的不合格应制定预防措施,以消除产生潜在不合格的原因,防止不合格发生,所采取的预防措施应与潜在问题的影响程度相适应。
防错控制程序

对防错的要求和方法进行管理,消灭失误,实现零缺陷生产。
2 范围适用于新产品设计开发阶段的防错考虑、现有制造过程的防错控制、策划和实施纠正/ 预防措施的防错。
3 术语防错:又叫防呆,是防止人为做错事的一种方法,是一种采用后,可以消灭错误,或将错误发生几率减至最低的科学方法,他能在缺陷产生前发现错误或缺陷产生时能及时发现与分离处错误。
防错的思路体现在以下五个方面:消除:消除可能的失误,通过产品和制造过程的重新设计,加入防错方法,是防错设计原则中的最好方法。
替代:用更可靠的过程代替目前的过程以减低失误,如运用机器人技术或自动化生产。
简化:使作业更容易完成,通过合并生产步骤,实施工程改善。
检测:在缺陷流入下工序前对其进行检测并剔除。
减少:将失误影响降至最低,采用保险丝进行过载保护等。
挑战件:又叫边界样件或防错样件,是指通过防错装置时能证明不符合操作或者能被探测出的不合格产品,专门用于检测生产线的防错装置。
临时替代方案:也称备用方案、屏蔽( By-pass ),是指防错装置失效后,在保证质量的前提下,为保证正常生产而采取的临时替代措施,如100%的人工检测;使用其他替代性的检验工具等。
4 职责4.1 技术部负责在产品和过程的设计和开发阶段(包括设计变更)组织多方论证小组进行防错设计。
4.2 质量部负责制造现场的防错装置首次验证和挑战件的定期校准。
4.3 生产部部负责防错装置和挑战件的制作。
4.4? 各车间主管负责本区域防错装置的日常管理4.5 各班组长负责本区域防错装置日常点检。
???5 管理内容5.1 新产品设计开发阶段的防错5.1.1 在新产品设计开发的初期,技术部应依据类似产品的经验(以往产品不合格报告、顾客反馈和投诉、服务中反馈的信息、市场调研的信息、管理评审提供的信息、质量管理体系审核中收集产品存在的问题的信息 )、同类厂家的设立情况等来考虑防错装置的设计。
原则上但不限于以下几方面应考虑设立防错装置。
纠正和预防措施控制程序QGSMQP

5.2.6品管部对从顾客制造厂或代理商退回的产品,组织有关部门进行分析、采取措施和可能工艺更改以防止再发生,顾客要求时必须提供所有记录。
5.2.7对出现不合格采用的纠正措施及其实施控制应能同时消除在其它类似的过程和产品中存在不合格原因。
质量体系程序文件
纠正和预防措施控制程序
QG/SMQP8.6
第A版第0次修改
序号
更改单号
摘录
更改人
更改日期
温州三蒙科技电气有限公司
质量体系程序文件
文件名称:纠正和预防措施控制程序
文件编号:QG/SMQP8.6
版本及修改状态:A/0
编制:赵 峰日期:2004年12月16日
审核:林志刚日期:2004年12月28日
批准:高少华日期:2005年01月01日
受控状态:
分发号:
实施日期:2005年01月01日
温州三蒙科技电气有限公司
3.2纠正措施——为防止已出规的不合格、缺陷或其它不希望发生的情况的再次发生,消除其原因所采取的措施。
3.3预防措施——为防止潜在的不合格、缺陷或其它不希望发生的情况的发生,消除其原因所采取的措施。
4.职责
4.1品管部是纠正/预防措施管理的归口部门,负责纠正/预防措施的跟踪、验证、并组织跨部门的纠正/预防措施的制订工作。
质量体系程序文件
纠正和预防措施控制程序
QG/SMQP8.6P1/3
第A版第0次修改
1.目的
对消除实际存在或潜在不合格原因和持续地改进质量而采取的措施,以求消除并防止不合格的再发生,确保体系运行的有效性和产品质量的稳定提高。
防错法及实施步骤ppt课件

技术可行性评估
评估各项防错措施在技术 上的可行性,包括所需技 术、设备、人员等是否具 备。
经济合理性分析
比较不同防错方案的成本 和效益,选择性价比最高 的方案。
确定最终方案并编制实施计划
综合评估与选择
综合考虑技术可行性、经济合理性、 实施难度等因素,选择最优的防错方 案。
防错法及实施步骤ppt课件
目录
CONTENTS
• 防错法基本概念与原理 • 防错法设计原则与方法 • 实施步骤一:确定防错目标与需求 • 实施步骤二:制定防错方案与计划
01 防错法基本概念与原理
CHAPTER
防错法定义及作用
防错法(Poka-Yoke)定义
是一种在作业过程中采用自动作用、报警、标识、分类等手段,使作业人员不特 别注意也不会失误,或失误导致后果发生前能够被有效纠正的方法。
沟通与协调
与相关部门和人员进行充分沟通和协 调,确保各方对方案和实施计划达成 共识。
编制详细实施计划
包括实施步骤、时间节点、责任人、 所需资源等,确保方案能够顺利落地 。
谢谢
THANKS
CHAPTER
收集相关资料并进行分析
01
02
03
收集历史错误数据
包括错误类型、发生频率 、影响程度等。
分析错误原因
运用统计工具和方法,如 因果图、故障树等,深入 剖析错误产生的根本原因 。
识别关键风险点
确定哪些环节或步骤最容 易出错,以及出错后可能 带来的后果。
提出可行性方案并进行比较
针对性防错措施
03 实施步骤一:确定防错目标与需求
CHAPTER
纠正措施控制程序c05 rev2.2

1. 目的本糾正措施規程的目的是確保SGW客戶的投訴及SGW環境,質量,3C,Ethics与WEEE&RoHS體系(以下統稱為綜合管理体系)內的不合格點得到處理。
2. 範圍本規程適用於SGW接收的所有客戶投訴及SGW綜合管理体系的反饋。
3. 規程提要規程主要可概括為:3.1 記錄客戶的所有投訴,接收SGW綜合管理体系的反饋。
3.2 分析投訴的原因並推薦糾正措施。
3.3 執行和記錄糾正措施。
3.4 驗証糾正措施,回復客戶(必要時)。
3.5 管理評審已執行的糾正措施。
4.輸入有關資料4.1 客戶的投訴。
4.2 生產或物料控制報告。
4.3 改善行動要求(CAR)。
4.4 SGW綜合管理体系的反饋。
5. 輸出結果5.1 已完成的糾正措施。
6. 職責6.1 QMQM負責審閱顧客的投訴、SGW綜合管理体系的不合格點及向管理層匯報。
QM負責識別顧客的投訴,指定QE工程師分析綜合管理体系不符合點的原因,界定相應的糾正措施及記錄跟進行動。
7. 技能要求7.1 QM7.1.1 熟悉SGW處理投訴的規程和糾正預防措施。
7.1.2 熟悉SGW環境,質量,3C,Ethics与WEEE&RoHS糾正措施的要求。
8. 流程圖本規程之操作任務順序及流程由下頁流程圖說明。
有關主程序內的執行要點及指引及補充資料詳見第9節工作指引。
9. 工作指引05-01 接收並記錄綜合管理体系投訴QMQM接收客戶投訴後,記錄於客戶投訴目錄中幷准備客戶投訴報告。
(STGW/05/F1)05-02 監察執行SGW綜合管理体系的反饋QMQM負責不斷監管SGW綜合管理体系執行過程,接收員工對體系的反饋,幷須確保體系得以順利運行。
QD負責監察生產中發生的問題,建議改善方法,跟進有關的執行情況,使環境和產品品質得到有效控制。
05-03 召開糾正措施會議相關人員有關部門按需要召開會議,跟進所收到的投訴、改善行動要求(CAR)及SGW綜合管理体系的反饋等。
防错管理程序(含表格)

防错管理程序(IATF16949-2016/ISO9001-2015)1.0目的本文件规定了防错装置设计和使用的关键要求。
2.0范围适用于本公司所有的工厂和项目。
3.0定义防错定义:错误是不可避免的;所谓防错是指一种传感器或者装置,它能在缺陷产生前发现错误;防错的目的在于使操作者从错误中解脱出来, 集中精力于增值的操作;最好的防错是简单,便宜和可靠的, 同时不给操作者增加额外的工作负担。
4.0作业内容4.1 开发过程1)在项目获取阶段:应根据类似产品的经验和本标准,在初始BP 中考虑到防错装置的预算。
2)在设计和设计验证阶段:防错是DFMEA 和PFMEA 的关键输出(防错的设计原则请参考附件)。
所有在设计和设计验证阶段输出的防错应整合到控制计划中;并在批量生产阶段被严格执行同时对其可靠性进行确认。
应不断审视和更新PFMEA,以使得检验工作的负荷降低到最合理的水平。
例如:尽量避免人工检验,最好的做法是每个工位人工检验项目为3 个。
防错也可能是在批量生产阶段开发的!为预防问题重复发生,防错是最好的解决方法,在应用防错后我们需要更新控制计划和PFMEA,并将其经验进行总结和横向展开。
3)每个防错装置都应制定详细和清晰的作业指导书;作业指导书应包括:1) 防错装置的编号(与控制计划对应);2) 工作原理;3) 检查方法;4) 检查频次;以及5) 出现失效情况下的备用方案。
4)S 特性对于S 特性:仅允许采用控制系统的防错方法,而不允许采用报警系统的防错方法(参见附件)。
备用方案应包括:(i) 100% 人工检验,和(ii) 视觉标识(最好的方法是在下个工位上有视觉标识的证据);同时(iii) 应保持应用备用方案时的相关记录。
5)线末测试用于在线末探测缺陷的装置不属于防错(例如:排气系统的漏气检测装置),因为此时错误已经转变产生为缺陷。
尽管如此,本文件后面规定的强制性规则对于这些装置仍然是必须的。
4.2 批量生产阶段:检查防错和备用方案1)检查防错装置的通用做法是使用标准样件(或者红兔子)来证明不符合的操作或者不合格的产品能够被探测到。
JYYH-PS-05-预防纠正措施控制程序

文档密级:一般文档状态:[ ] 草案 [√]正式发布 [ ]正在修订受控状态:[√] 受控 [ ]非受控预防措施控制程序Corrective and Preventive Action目录1.适用 (1)2.目的 (1)3.职责 (1)4.相关文件 (1)5.程序 (1)5.1. 预防措施控制程序 (1)5.2. 纠正措施控制程序 (3)6.记录 (4)1.适用本程序适用于对本公司为消除管理体系潜在不符合原因所采取的预防措施的控制,为消除与信息安全管理体系要求不符合的原因,防止其再次发生,持续改进和信息安全管理体系的有效性而采取的纠正措施。
2.目的为对潜在的或已经明确的不符合进行分析、采取措施,并予以消除,以逐步改进和完善管理体系,特制定本程序。
3.职责本公司过程改进委员会为公司管理体系纠正预防措施的归口管理部门,负责组织相关部门进行相关数据的收集及分析,确定不符合原因,评价纠正预防措施的需求,组织相关部门制定纠正预防措施,并由过程改进委员会负责跟踪验证。
4.相关文件《信息安全管理体系手册》《内部审核控制程序》《信息安全事件管理制度》5.程序5.1.预防措施控制程序1、预防措施信息来源有:•公司内外安全事件记录、事故报告、薄弱点报告;•日常管理检查及技术检查中指出的不符合;•信息安全监控记录;•内、外部审核报告及管理评审报告中的不符合项;•相关方的建议或抱怨;•风险评估报告;•服务报告•其他有价值的信息等。
2、过程改进委员会每半年组织相关部门利用本文所规定的信息来源,结合《管理评审报告》分析确定潜在不符合及其原因,评价防止不符合发生的措施的需求。
采取预防措施应与潜在问题的影响程度相适应,对于以下情况的潜在不符合应采取预防措施:•可能造成信息安全事故;•可能影响服务等级或造成服务中断;•可能影响顾客满意程度、造成顾客抱怨与投诉;•可能影响本公司的企业形象与经济利益;•可能造成生产经营业务中断。
对于各部门日常发现报告的重大安全隐患(安全薄弱点),过程改进委员会应组织有关部门进行原因分析,采取预防措施。
防错控制程序完整版
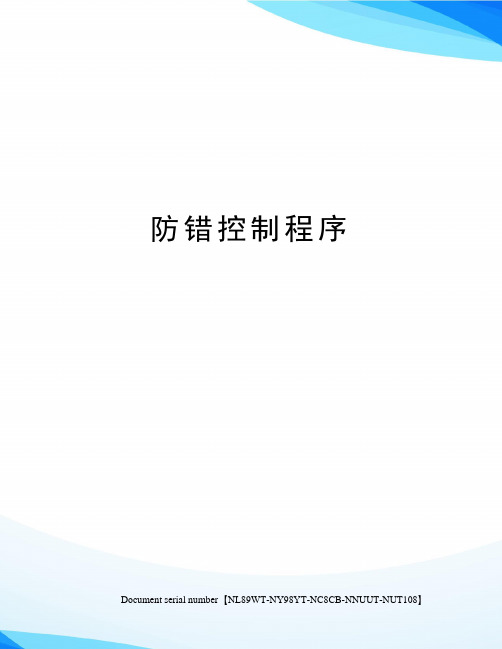
防错控制程序Document serial number【NL89WT-NY98YT-NC8CB-NNUUT-NUT108】1目的对防错的要求和方法进行管理,消灭失误,实现零缺陷生产。
2 范围适用于新产品设计开发阶段的防错考虑、现有制造过程的防错控制、策划和实施纠正/预防措施的防错。
3 术语防错:又叫防呆,是防止人为做错事的一种方法,是一种采用后,可以消灭错误,或将错误发生几率减至最低的科学方法,他能在缺陷产生前发现错误或缺陷产生时能及时发现与分离处错误。
防错的思路体现在以下五个方面:消除:消除可能的失误,通过产品和制造过程的重新设计,加入防错方法,是防错设计原则中的最好方法。
替代:用更可靠的过程代替目前的过程以减低失误,如运用机器人技术或自动化生产。
简化:使作业更容易完成,通过合并生产步骤,实施工程改善。
检测:在缺陷流入下工序前对其进行检测并剔除。
减少:将失误影响降至最低,采用保险丝进行过载保护等。
挑战件:又叫边界样件或防错样件,是指通过防错装置时能证明不符合操作或者能被探测出的不合格产品,专门用于检测生产线的防错装置。
临时替代方案:也称备用方案、屏蔽(By-pass),是指防错装置失效后,在保证质量的前提下,为保证正常生产而采取的临时替代措施,如100%的人工检测;使用其他替代性的检验工具等。
4 职责技术部负责在产品和过程的设计和开发阶段(包括设计变更)组织多方论证小组进行防错设计。
质量部负责制造现场的防错装置首次验证和挑战件的定期校准。
生产部部负责防错装置和挑战件的制作。
各车间主管负责本区域防错装置的日常管理各班组长负责本区域防错装置日常点检。
5 管理内容新产品设计开发阶段的防错在新产品设计开发的初期,技术部应依据类似产品的经验(以往产品不合格报告、顾客反馈和投诉、服务中反馈的信息、市场调研的信息、管理评审提供的信息、质量管理体系审核中收集产品存在的问题的信息)、同类厂家的设立情况等来考虑防错装置的设计。
- 1、下载文档前请自行甄别文档内容的完整性,平台不提供额外的编辑、内容补充、找答案等附加服务。
- 2、"仅部分预览"的文档,不可在线预览部分如存在完整性等问题,可反馈申请退款(可完整预览的文档不适用该条件!)。
- 3、如文档侵犯您的权益,请联系客服反馈,我们会尽快为您处理(人工客服工作时间:9:00-18:30)。
1 目的
对防错的要求和方法进行管理,消灭失误,实现零缺陷生产。
2 范围
适用于新产品设计开发阶段的防错考虑、现有制造过程的防错控制、策划和实施纠正/预防措施的防错。
3 术语
防错:又叫防呆,是防止人为做错事的一种方法,是一种采用后,可以消灭错误,或将错误发生几率减至最低的科学方法,他能在缺陷产生前发现错误或缺陷产生时能及时发现与分离处错误。
防错的思路体现在以下五个方面:
●消除:消除可能的失误,通过产品和制造过程的重新设计,加入防错方
法,是防错设计原则中的最好方法。
●替代:用更可靠的过程代替目前的过程以减低失误,如运用机器人技术
或自动化生产。
●简化:使作业更容易完成,通过合并生产步骤,实施工程改善。
●检测:在缺陷流入下工序前对其进行检测并剔除。
●减少:将失误影响降至最低,采用保险丝进行过载保护等。
挑战件:又叫边界样件或防错样件,是指通过防错装置时能证明不符合操作或者能被探测出的不合格产品,专门用于检测生产线的防错装置。
临时替代方案:也称备用方案、屏蔽(By-pass),是指防错装置失效后,在保证质量的前提下,为保证正常生产而采取的临时替代措施,如100%的人工检测;使用其他替代性的检验工具等。
4 职责
4.1 技术部负责在产品和过程的设计和开发阶段(包括设计变更)组织多方论证小组进行防错设计。
4.2 质量部负责制造现场的防错装置首次验证和挑战件的定期校准。
4.3 生产部部负责防错装置和挑战件的制作。
4.4?各车间主管负责本区域防错装置的日常管理
4.5 各班组长负责本区域防错装置日常点检。
???
5 管理内容
5.1 新产品设计开发阶段的防错
5.1.1 在新产品设计开发的初期,技术部应依据类似产品的经验(以往产品不合格报告、顾客反馈和投诉、服务中反馈的信息、市场调研的信息、管理评审提供的信息、质量管理体系审核中收集产品存在的问题的信息)、同类厂家的设立情况等来考虑防错装置的设计。
原则上但不限于以下几方面应考虑设立防错装置。
?
a)涉及安全、性能方面的;?
b)风险系数和严重度高的;
c)左右件的防错;?
d)关键和重要特殊特性优先考虑防错装置的使用;
5.1.2 在设计和设计验证阶段,防错是PFMEA的关键输出。
5.1.3 所有在设计和设计验证阶段输出的防错应整合到控制计划中,并在批量生产阶段被严格执行,同时对其可靠性进行确认。
?
5.1.4 技术部根据PFMEA的设计输出,以及制造现场防错装置的设立,形成产品和过程《防错装置清单》。
清单内容包括:
a)防错装置的工位和编号(与控制计划对应);
b)防错方法;
c)验证方法;
d)验证频次;
e)临时替代方案(by-pass)。
临时替代方案管理应包括:?
1)100%人工检验;?
2)100%检查过的特性进行可视化标识(在产品标签上说明);?
3)保持应用临时替代方案时的相关记录,以便于追溯;
4)临时替代方案由技术部确定,质量部确认。
临时替代方案下生产的零
件应能确保所生产的不合格零件不流入下道工序;?
5)临时替代方案必须在“防错标识卡”红色的一面简单而清晰的描述;
6)防错装置失效后所采取的措施应在《防错验证检查表》中记录(包括
产品和防错装置的处理措施)。
?
5.2 防错装置的验证和定期审核
5.2.1 在新产品进行首次量产时,质量部应对《控制计划》中的所有防错装置进行一次验证,确保《控制计划》中所有的防错装置都应用到了相应的生产工位上面,同时确保防错装置有效。
?
挑战件来证明不符合的操作或者不合格的产品能够被探测到。
?
5.2.3挑战件必须:?
a)由技术部设计、生产部制作、并会同质量部确认;?
b)正确标识(挑战件上必须标明零件名称和其应用的设备、模具、工装);?
c)与正常生产的零件清晰地区分(用油漆笔标识、张贴标签);?
d)应进行定置定位,并做好防锈工作,存放于防错装置附近的位置,方便
操作者存取,有环境要求的,应按要求予以保存,使用部门做好挑战件
的日常维护。
?
e)质量部应建立《挑战件(NG样件)清单》,对状态、位置、有效期等进行
管理。
f)质量部应定期(至少每年1次)对挑战件进行校验,以确保其满足防错
的要求。
?
5.2.4技术部应依据《防错装置清单》组织制造部、相关车间主管、工/模具管理人员、现场质量控制人员对各工序和工位的防错位置(包含模具、工装、检具等)进行标识,标识卡(见附件1)应包含防错编号、防错功能、临时替代方案内容等信息,并悬挂在防错工位附近。
5.2.5 每个操作者应按《防错验证指导书》的要求,经过防错的培训。
培训包括防错装置的使用和失效后的应急措施。
?
5.2.6 《防错验证指导书》应采取图文并茂的方式,识别主要要素和顺序,以及位置和代号(区分同类防错装置)。
《防错验证指导书》应展示在现场操作工位,并让操作者易于取到。
错装置因磨损、失效移位,操作者应对本工位的防错装置进行至少每天一次的验证,一般是在首件检查、模具更换和设备维修后。
必要时,应通知质量部安排人员使用挑战件检查防错装置是否有效。
当过程不稳定或过程能力下降或产品报废明显增加时,提高验证频次至每班2次。
5.2.8采用“防错标识卡”检查防错结果。
防错验证合格后方能继续生产,操作者验证后同时应按《防错验证检查表》作好记录,并将“防错标识卡”翻到绿色面。
?
5.2.9 车间主管和质量部过程巡检员应做好防错的日常确认和监督工作,包括防错装置是否有效、操作者是否对防错装置避而不用。
应定期进行审核,审核的频次按下表,并对检查结果进行通报;其中车间/班组的审核按照《防错功能检查表》进行检查,质量部依据《防错审核检查表》进行专项审核。
防错审核也同时列入《LPA分层过程审核检查清单》。
5.3 防错失效的紧急措施
5.3.1 必须确保防错装置在任何时候都是有效的,如果防错失效,应采取以下措施:
5.3.2 A级——发现装置的防错功能失效,必须立即停止生产(操作者有权停止生产), 装置经维修合格后才能恢复生产,并按“作业准备验证和停工后验证规定”的相关要求执行。
5.3.3 B级——发现设备的防错功能失效,可以不停止生产,但必须按临时替代方案进行控制,替代方案的过程应按照“变更控制”的相关要求实施。
5.3.4 操作者将“防错标识卡”翻转到红色的一面。
?
5.3.5 操作者维持现状并立即报告班长,班长通知技术部工艺工程师立即到达现场确认防错失效的事实。
5.3.6 质量部立即确定断点(从检查的最后一个合格样件开始,之后生产的所有零件都必须当作可疑品处理)并对该批次产品进行标识和隔离。
5.3.7 内部的可疑品应确定100%检测的遏制措施。
5.3.8 如可疑品已经流向客户,应立即通知顾客并采取紧急措施,如退换货。
5.3.9 通知设备部紧急抢修防错装置。
?
5.4 防错失效的处置和问题解决
5.4.1操作工和车间/班组日常检查、分层审核检查中发现防错失效的情况由车
间主管填写《防错功能失效-整改计划》,描述:发现日期、失效防错装置、防错编号、失效工位后3个工作日内提交技术部。
5.4.2质量部定期审核发现的防错失效,由质量主管填写《设备防错功能失效-整改计划》。
描述:发现日期、失效工位、失效防错装置、防错编号后3个工作
日内提交技术部。
5.4.3技术部将《防错功能失效-整改计划》汇总后进行原因分析,制定纠正预
防措施后组织相关责任人遵照《纠正/预防措施控制程序》的要求实施整改。
5.5防错的改善活动策划和实施
5.5.1 技术部根据日常制造过程的产品质量统计状况、顾客抱怨、售后索赔、
退换货发生后,为防止问题重复发生,应该优先考虑防错。
5.5.2 制造过程防
错也可在批量生产阶段开发。
多方论证小组依据设备部模具维护保养、周期性
检修情况,采取优先减少的原则对现有制造过程质量控制采用防错管理。
5.5.3 防错也可能是在批量生产阶段开发的。
工艺部门应不断审视和更新PFMEA,以使得检验工作的负荷降低到最合理的水平。
如:尽量避免人工检验,最好的
做法是每个工位人工检验的项目不超过3个。
5.5.5在应用防错后,技术部门需要更新控制计划和PFMEA,并将其经验进行总结和横向开发。
FMEA、控制计划、作业指导书三者应保持一致。
6 相关文件
纠正/预防措施控制程序
7 质量记录
防错装置清单
挑战件(NG样件)清单
防错功能失效-整改计划
防错功能验证表
防错功能检查表。