压铸品质缺陷类型及改善方案
压铸件常见缺陷及解决办法

压铸件常见缺陷及解决办法
1、尖角缺陷:表现为在压铸件的边缘和表面出现尖利的角,其
原因是模具的固定不牢,模具合模前没有铂精加光等操作,模具和表
面间的空隙较大,导致铸件连续流和溅射的金属物料的冷凝无法完全
填充到模具内。
解决办法是在压铸件的模具制作中要注意模具的固定,还要在合模前进行铂精加光,使模具缝隙尽量控制在最小。
2、翘曲缺陷:表现为铸件胚体过大或模具设计不当,导致部分
孔表面被填充的金属物料过度凝固后发生变形。
解决办法是提高铸件
的成型质量,在模具设计时应注意做到模具中高低正常,同时要增加
相应的引流装置,降低铸件表面在压铸过程中的温度,减少物料凝固
时间。
3、凹槽缺陷:表现为压铸件内壁或内孔出现浅深不均、粗糙凹槽,一般出现在内壁与模穴孔面间,其原因是模具合模时并未完全排
除空气,另外铸件内孔口位、形喉与内壁模穴间距过大,空气中的熔
融物料的细沙子难以充分清除也会导致此缺陷的产生。
解决办法是采
取真空压铸成型,即采用真空室和真空阀将空气真空,以消除空气;
另外应改变合模方式和模具设计,减少内孔口位与形喉与内壁模穴间距。
常见压铸件缺陷及解决方法
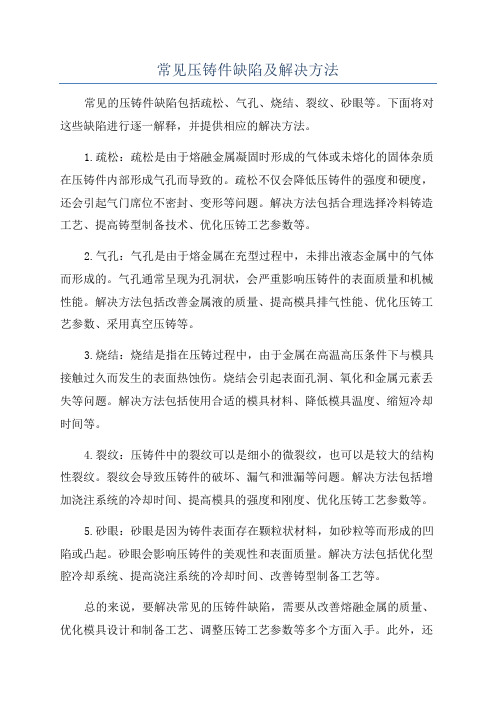
常见压铸件缺陷及解决方法常见的压铸件缺陷包括疏松、气孔、烧结、裂纹、砂眼等。
下面将对这些缺陷进行逐一解释,并提供相应的解决方法。
1.疏松:疏松是由于熔融金属凝固时形成的气体或未熔化的固体杂质在压铸件内部形成气孔而导致的。
疏松不仅会降低压铸件的强度和硬度,还会引起气门席位不密封、变形等问题。
解决方法包括合理选择冷料铸造工艺、提高铸型制备技术、优化压铸工艺参数等。
2.气孔:气孔是由于熔金属在充型过程中,未排出液态金属中的气体而形成的。
气孔通常呈现为孔洞状,会严重影响压铸件的表面质量和机械性能。
解决方法包括改善金属液的质量、提高模具排气性能、优化压铸工艺参数、采用真空压铸等。
3.烧结:烧结是指在压铸过程中,由于金属在高温高压条件下与模具接触过久而发生的表面热蚀伤。
烧结会引起表面孔洞、氧化和金属元素丢失等问题。
解决方法包括使用合适的模具材料、降低模具温度、缩短冷却时间等。
4.裂纹:压铸件中的裂纹可以是细小的微裂纹,也可以是较大的结构性裂纹。
裂纹会导致压铸件的破坏、漏气和泄漏等问题。
解决方法包括增加浇注系统的冷却时间、提高模具的强度和刚度、优化压铸工艺参数等。
5.砂眼:砂眼是因为铸件表面存在颗粒状材料,如砂粒等而形成的凹陷或凸起。
砂眼会影响压铸件的美观性和表面质量。
解决方法包括优化型腔冷却系统、提高浇注系统的冷却时间、改善铸型制备工艺等。
总的来说,要解决常见的压铸件缺陷,需要从改善熔融金属的质量、优化模具设计和制备工艺、调整压铸工艺参数等多个方面入手。
此外,还需要采用适当的检测手段,如金相分析、X射线检测、超声波检测等,对压铸件进行质量检验,及时排除可能存在的缺陷。
压铸件常见缺陷及改善对策

压铸件常见缺陷及改善对策压铸件是常用的金属制造工艺之一,用于制造各种产品,如汽车零件、电子设备外壳等。
然而,压铸件在制造过程中往往会出现一些常见的缺陷,例如气孔、缩松、热裂纹等。
为了提高压铸件的质量,需要采取适当的改善对策。
首先,气孔是压铸件中常见的缺陷之一、这主要是由于金属液中溶解的气体在凝固时无法完全排除,导致气孔形成。
改善对策包括以下几个方面:1.改善炉内冶炼过程:合理调节熔化温度和熔化时间,增加金属液中的液体相和气体相之间的接触时间,有助于气体的溶解和脱除。
2.调节压铸机参数:增加射压和射速,可以改善金属液流动性,减少气体残留的可能性。
3.优化压铸模具结构:设计合理的浇口和废渣口,有利于气体的排除,减少气孔的生成。
其次,缩松是另一个常见的缺陷。
缩松是指压铸件中因内部金属液冷却不均匀而形成的孔洞或松散区域。
改善对策包括以下几个方面:1.控制金属液的冷却速度:通过调整铸型温度、浇注温度和浇注速度等参数,使金属液冷却均匀,减少缩松的可能性。
2.优化浇口和冷却系统:设计合理的浇口和冷却系统,有利于金属液的流动和冷却,减少缩松的生成。
3.采用适当的金属合金:一些合金具有较好的流动性和凝固性,能够减少缩松的产生。
最后,热裂纹是压铸件常见的缺陷之一、这是由于金属在冷却过程中由于内部应力过大而发生裂纹。
改善对策包括以下几个方面:1.控制冷却速率:通过调节冷却速率,使金属在冷却过程中应力得到释放,减少热裂纹的发生。
2.优化模具设计:设计合理的模具结构,减少金属液在冷却过程中的应力集中,可以减少热裂纹的生成。
3.采用合适的退火工艺:通过合适的退火工艺,使金属在冷却过程中应力得到释放,减少热裂纹的发生。
总之,压铸件常见的缺陷包括气孔、缩松和热裂纹等,需要采取一系列的改善对策来提高压铸件的质量。
通过优化工艺参数、改善模具设计和采用合适的金属合金,可以减少这些缺陷的发生,并提高压铸件的品质。
压铸件常见缺陷及解决办法手册 (完整版)
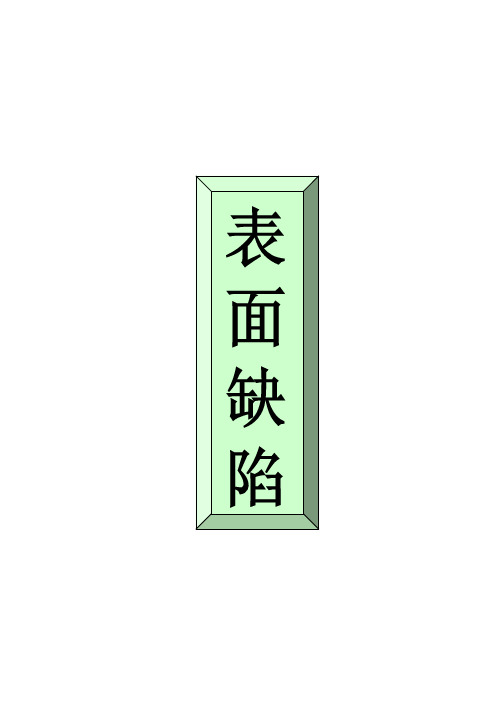
产生原因分析判断及解决办法1、金属液浇注温度低或模具温度低;2、合金成分不符合标准,流动性差;3、金属液分股填充,熔合不良;4、浇口不合理,流程太长;5、填充速度低或排气不良;6、压射比压偏低。
1、产品发黑,伴有流痕。
适当提高浇注温度和模具温度;2、改变合金成分,提高流动性;3、烫模件看铝液流向,金属液碰撞产生冷隔出现一般为涡旋状,伴有流痕。
改进浇注系统,改善内浇口的填充方向。
另外可在铸件边缘开设集渣包以改善填充条件;4、伴有远端压不实。
更改浇口位置和截面积,改善排溢条件,增大溢流量;5、产品发暗,经常伴有表面气泡。
提高压射速度,6、铸件整体压不实。
提高比压(尽量不采用)。
缺陷1 ---- 冷隔缺陷现象:温度较低的金属流互相对接但未熔合而出现的缝隙,呈不规则的线形,有穿透的和不穿透的两种,在外力的作用下有发展的趋势。
其他名称:冷接(对接)缺陷2 ---- 擦伤其他名称:拉伤、拉痕、粘模伤痕缺陷现象:顺着脱模方向,由于金属粘附,模具制造斜度太小而造成铸件表面的拉伤痕迹,严重时成为拉伤面甚至产生裂纹。
产生原因 分析判断及解决办法 1、型芯、型壁的铸造斜度太小或出现倒斜度; 2、型芯、型壁有压痕; 3、合金粘附模具;4、铸件顶出偏斜,或型芯轴线偏斜;5、型壁表面粗糙;6、涂料常喷涂不到;7、铝合金中含铁量低于0.6%; 8、合金浇注温度高或模具温度太高;9、浇注系统不正确, 直接冲击型壁或型芯 ; 10、填充速度太高;11、型腔表面未氮化。
1、产品一般拉出亮痕,不起毛。
修正模具,保证制造斜度; 2、产生拉毛甚至拉裂。
打光压痕、更换型芯或焊补型壁; 3、拉伤起毛。
抛光模具; 4、单边大面积拉伤,顶出时有异声修正模具结构; 5、拉伤为细条状,多条。
打磨抛光表面; 6、模具表面过热,均匀粘铝。
涂料用量薄而均匀,不能漏喷涂料; 7、型腔表面粘附铝合金。
适当增加含铁量至0.6~0.8%;8、型腔表面粘附铝合金,尤其是内浇口附近。
压铸件缺陷产生原因及对应措施

1.降低浇注温度,减少收缩量 2.提高压射比压及增压压力,提高致密 性 3.修改内浇口,使压力更好传递,有利 于液态金属补缩作用 4.改变铸件结构,消除金属积聚部位, 壁厚尽可能均匀 5.加快厚大部位冷却 6.加厚料柄,增加补缩的效果
3
夹杂
1.炉料不洁净,回炉料太多 混入压铸件内的金属或非金属 2.合金液未精炼 杂质,加工后可看到形状不规 3.用勺取液浇注时带入熔渣 则,大小、颜色、亮度不同的 4.石墨坩埚或涂料中含有石墨脱落混 点或孔洞 入金属液中 5.保温温度高,持续时间长 1.铝合金中杂质锌、铁超过规定范围 铸件基体金属晶粒过于粗大或 2.合金液过热或保温时间过长,导致 极小,使铸件易断裂或磁碎 晶粒粗大 3.激烈过冷,使晶粒过细 1.压力不足,基体组织致密度差 2. 内部缺陷引起,如气孔、缩孔、渣 压铸件经耐压试验,产生漏气 孔、裂纹、缩松、冷隔、花纹 、渗水 3.浇注和排气系统设计不良 4.压铸冲头磨损,压射不稳定 机械加工过程或加工后外观检 查或金相检查:铸件上有硬度 高于金属基体的细小质点或块 状物使刀具磨损严重,加工后 常常显示出不同的亮度 一、非金属硬点: 1.混入了合金液表面的氧化物 2.合金与炉衬的反应物 3.金属料混入异物 4.夹杂物
铸件缺陷产生原因及应对措施
一、表面缺陷
序号 缺陷名称 特征
沿开模方向铸件表面呈现条状 的拉伤痕迹,有一定深度,严 重时为一面状伤痕;另一种是 金属液与模具产生焊合、粘附 而拉伤,以致铸件表面多肉或 缺肉
产生原因
1.型腔表面有损伤 2.出模方向斜度太小或倒斜 3. 顶出时偏斜 4.浇注温度过高或过低、模温过高 导 致合金液产生粘附 5.脱模剂使用效果不好 6. 铝合金成分铁含量低于 7.冷却时间过长或过短 1.合金液在压室充满度过低,易产生 卷气,压射速度过高 2. 模具排气不良 3. 熔液未除气,熔炼温度过高 4.模温过高,金属凝固时间不够,强 度不够,而过早开模顶出铸件,受压 气体膨胀起来 5.脱模剂太多 6.内浇口开设不良,充填方向不顺
压铸件的常见缺陷和解决的对策

压铸件的常见缺陷和解决的对策
波纹(流痕): 原因:第一层熔汤在表面急遽冷却,第二层熔 汤流过未能将第一层熔解,却又有足够的融 合,造成组织不同. 改善方法: 改善充填模式. 缩短充填时间.
压铸件的常见缺陷和解决的对策
毛边: 原因:锁模力不足. 模具合模不良. 模具强度不足. 熔汤温度太高. 压射力太高。 缩陷: 原因:缩孔发生在压件表面下面. 改善方法: 同改善缩孔的方法. 局部冷却. 加热另一边.
压铸件的常见缺陷和解决的对策
改善方法:
积碳: 检查壁厚是否太薄(设计或制造),较薄的区域应直接充填.
压铸件的 常见缺陷和解决的对策
检改查善流 方道法转: 弯原是否因圆滑:离,截面型积是剂否渐或减. 其它杂质积附在模具上. 适毛原当边因的 ::锁慢模速力.改减不足善小. 方离法型:剂喷洒量. 升高模温. 压铸件的常见缺陷和解决的对策
压铸件的常见缺陷和解决的对策
冷纹(水纹): 原因:熔汤前端的温度太低,相迭时有痕迹. 改善方法: 检查壁厚是否太薄(设计或制造),较薄的区域应直接充填. 检查形状是否不易充填;距离太远、封闭区域(如鳍片 、凸 起) 、被阻挡区域、圆角太小等均不易充填.并注意是否有 肋点或冷点. 缩短充填时间.缩短充填时间的方法:… 改变充填模式. 提高模温的方法:… 提高熔汤温度. 检查合金成分. 加大排气道可能有用. 加真空装置可能有用.
压铸机周边转销13528684580
精品课件!
精品课件!
压铸件的常见缺陷和解决的对策
变色,氧化。 脱模剂的质量。 喷涂过量、。 材质缺陷:硬点,氧花物。
改善方法:合适的合金原料,保持材料的清洁。 材质缺陷:硬点,氧花物。
改善方法:合适的合金原料,保持材料的清洁。
压铸件铸造缺陷不良改善对策

压铸件铸造缺陷不良改善对策缺陷名称特征产生原因防止方法拉伤沿开模方向铸件表面呈现条状的拉伤痕迹,有一定深度,严重时为一面状伤痕。
另一种是金属液与模具产生焊合、粘附而拉伤,以致铸件表面多肉或缺肉。
1、型腔表面有损伤、出模方向斜度太小或倒斜 23、顶出时偏斜4、浇注温度过高或过低,模温过高导致合金液产生粘附5、脱模剂使用效果不好6、铝合金成分含铁量低于0.6%7、冷却时间过长或过短1、修理模具表面损伤处,修正斜度,600细油石顺磨提高光洁度2、调整或更换顶杆,使顶出力平衡3、更换离型剂4、调整合金含铁量5、控制合适的浇注温度,控制模具温度6、修改内浇口,避免直冲型芯型壁或对型芯表面进行特殊处理气泡铸件表面有米粒大小的隆起表皮下形成的空洞 1、合金液在压室充满度过低,易产生卷气,压射速度过高2、模具排气不良3、溶液未除气,熔炼温度过高4、模温过高,金属凝固时间不够,强度不够,而过早开模顶出铸件,受压气体膨胀起来5、脱模剂太多6、内浇口开设不良,充填方向不顺 1、提高金属液充满度 2、降低第一阶段压射速度,改变低速与高速压射切换点3、降低模温4、增设排气槽、溢流槽、充分排气5、调整熔炼工艺,进行除气处理6、留模时间延长7、减少脱模剂用量裂纹 1. 铸件表面有呈直线状或波浪形的纹路,狭小而长,在外力作用下有发展趋势2. 冷裂,开裂处金属没有被氧化3. 热裂,开裂处金属已经被氧化 1. 合金中含铁量过高或硅含量过低 2. 合金中有害杂质的含量过高,降低了合金的可塑性3. 铝硅合金:铝硅铜合金含锌或含铜量过高;铝镁合金中含镁量过多4. 模具:特别是型芯温度太低5. 铸件壁存有剧烈变之处,收缩受阻,尖角位形成应力6. 留模时间过长,应力大7. 顶出时受力不均匀 1. 正确控制合金成分,在某种情况下可在合金中加纯铝锭以降低合金中含镁量;或在合金中加铝硅中间合金以提高硅含量 2. 改变铸件结构,加大圆角,加大出模斜度,减少壁厚差3. 变更或增加顶出位置,使顶出受力均匀4. 缩短开模及抽芯时间5. 提高模温,保持模温稳定变形 1. 铸件几何形状与图纸不符2. 整体变形或局部变形 1. 铸件结构设计不良,引起不均匀收缩 2. 开模过早,铸件刚性不够3. 顶杆设置不当,顶出时受力不均匀4. 切除浇口方法不当5. 由于模具表面粗糙造成举报阻力大而引起顶出时变形 1. 改进铸件结构 2. 调整开模时间3. 合理设置顶杆位置及数量4. 选择合适的切除浇口方法5. 加强模具型腔表面抛光,减少托模阻力流痕、花纹 1. 铸件表面上有与金属液流动方向一致的条纹,有明显可见的与金属体颜色不一样的无方向性的纹路,无发展趋势 1. 首先进入型腔的金属液形成一个极薄的而又不完全的金属层后,被后来的金属液所弥补而留下的痕迹 2. 模温过低,模温不均匀3. 内浇道截面积过小及位置不当产生喷溅4. 作用于金属液的压力不足5. 花纹:涂料用量过多 1. 提高金属液温度2. 提高模温3. 调整内浇道截面积或位置4. 调整充填速度及压力5. 选用合适的涂料及调整用量冷隔 1. 铸件表面有明显的、不规则的、下陷线性纹路(有穿透与不穿透两种)形状细小而狭长,有的交接边缘光滑,在外力作用下有发展的可能 1. 两股金属流相互对接,但未完全熔合而又无夹杂存在其间,两股金属流结合力很薄弱 2. 浇注温度或压铸模温度偏低3. 选择合金不当,流动性差4. 浇道位置不对或流路过长5. 充填速度低6. 压射比压低 1. 适当提高浇注温度和模具温度 2. 提高压射比压,缩短充填时间3. 提高压射速度,同时加大内浇口截面积4. 改善排气、充填条件5. 正确选用合金,提高合金流动性变色、斑点 1. 铸件表面呈现出不同的颜色及斑点 1. 不合适的脱模剂2. 脱模剂用量过多,局部堆积3. 含有石墨的润滑剂中的石墨落入铸件表层4. 模温过低,金属液温度过低导致不规则的凝固引起 1. 更换优质脱模剂 2. 严格喷涂量及喷涂操作3. 控制模温4. 控制金属液温度网状毛翅 1. 压铸件表面上有网状发丝一样凸起或凹陷的痕迹,随压铸次数增加而不断扩大和延伸 1. 压铸模型腔表面龟裂2. 压铸模材质不当或热处理工艺不正确3. 压铸模冷热温差变化大4. 浇注温度过高5. 压铸模预热不足6. 型腔表面粗糙 1. 正确选用压铸模材料及热处理工艺 2. 浇注温度不易过高,尤其是高熔点合金3. 模具预热要充分4. 压铸模要定期或压铸一定次数后退火,消除内应力5. 打磨成型部分表面,减少表面粗糙度6. 合理选择模具冷却方法凹陷 1、铸件平滑表面上出现凹陷部位 1. 铸件壁厚相差太大,凹陷多产生在厚壁处2. 模具局部过热,过热部分凝固慢3. 压射比压低4. 由憋气引起型腔气体排不出,被压缩在型腔表面与金属液界面之间 2. 铸件壁厚设计尽量3. 模具局部领却调整4. 提高压射比压5. 改善型腔排气条件欠铸(缺料) 1、铸件表面有浇不足部位 1、流动性差原因: 1) 合金液吸气、氧化夹杂物,含铁量高,使其质量差而降低流动性 2) 浇注温度低或模温低2、充填条件不良:1) 比压过低2) 卷入气体过多,型腔的背压变高,充型受阻3、操作不良,喷涂料过度,涂料堆积,气体挥发不掉 1、提高合金液质量2、提高浇注温度或模具温度3、提高比压、充填速度4、改善浇注系统金属液的导流方式,在欠铸部位加开溢流槽、排气槽5、检查压铸机能力是否足够毛刺飞边 1. 压铸件在分型面边缘上出现金属薄片 1. 锁模力不够 2. 压射速度过高,形成压力冲击峰过高3. 分型面上杂物未清理干净4. 模具强度不够造成变形5. 镶块、滑块磨损与分型面不平齐 1. 检查合模力和增压情况,调整压铸工艺参数2. 清洁型腔及分型面3. 修理模具4. 最好是采用闭合压射结束时间控制系统,可实现无飞边压铸气孔(内部缺陷) 1. 解剖后外观检测或探伤检查,气孔具有光滑的表面、形状为圆形 1. 合金液导入方向不合理或金属液流动速度太高,产生喷射;过早堵住排气道或正面冲击壁而形成漩涡包住空气,这种气孔多产生排气不良或深腔处2. 由于炉料不干净或熔炼温度过高,使金属液中较多的气体没除净,在凝固时析出没能充分排出。
压铸件常见缺陷和处理
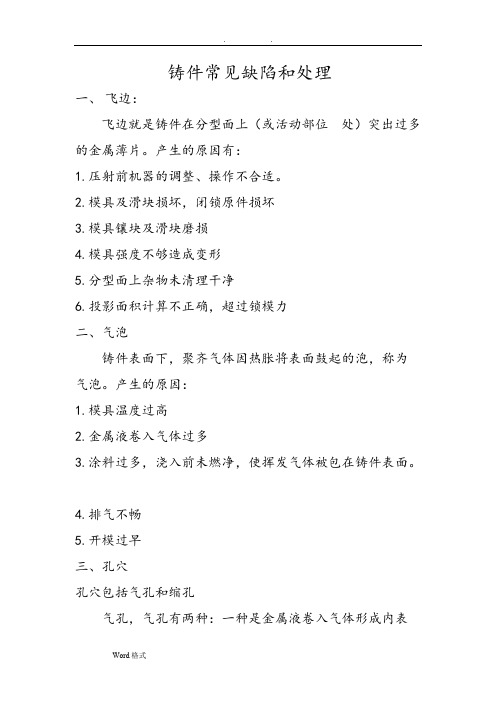
铸件常见缺陷和处理一、飞边:飞边就是铸件在分型面上(或活动部位处)突出过多的金属薄片。
产生的原因有:1.压射前机器的调整、操作不合适。
2.模具及滑块损坏,闭锁原件损坏3.模具镶块及滑块磨损4.模具强度不够造成变形5.分型面上杂物未清理干净6.投影面积计算不正确,超过锁模力二、气泡铸件表面下,聚齐气体因热胀将表面鼓起的泡,称为气泡。
产生的原因:1.模具温度过高2.金属液卷入气体过多3.涂料过多,浇入前未燃净,使挥发气体被包在铸件表面。
4.排气不畅5.开模过早三、孔穴孔穴包括气孔和缩孔气孔,气孔有两种:一种是金属液卷入气体形成内表面光亮和光滑、形状较为规则的孔洞,另一种是合金熔炼不正确或精炼不够,气体溶解于合金中。
压铸时,激冷甚剧,凝固很快,溶于金属中的气体来不及析出,使金属内的气体留在铸件内形成孔洞。
产生的原因有:1.浇口位置选择和导流不当,导致金属液进入型腔产生正面撞击及漩涡。
2.流道形状设计不良,3.压室充满度不够4.内浇口速度太高,形成端流。
5.排气不畅6.模具型腔位置太深7.机械加工于量太大8.涂料过多,在填充前未燃尽9.炉料不干净,精炼不良缩孔,铸件在凝固过程中,由于金属补充不足形成的暗色、形状不规则的孔洞。
产生的原因有:1.合金规范不合适,浇入温度过高2.金属液过热时间太长3.比压太低4.余料柄太薄,最终补压不到作用5.内浇口截面积过小(主要是厚度不够)6.溢流槽位置不对或容量不够7.铸件结构不合理,有热节部位,并且该处无法用溢流槽解决8.铸件的壁厚变化太大四、夹杂夹杂又称为夹物、砂眼、夹渣。
在铸件表面或内部形成不规则的孔穴部分或全部充塞着杂物,产生的原因有:1.炉料不干净2.合金精炼不够,熔渣未除净3.舀取金属液时带入熔渣及金属氧化物4.模具未清里干净5.涂料中石墨太多五、冷豆冷豆也称铁豆,其表现是嵌在铸件表面,未和铸件完全融合的金属颗粒,产生的原因有:1.浇注系统设置不当2.填充速度过快3.金属过早进入型腔六、麻面产生的原因是由于填充时,金属液分散成密集液滴,高速撞击型壁,结果形成具有强烈流向的细小、密集的麻点区域。
- 1、下载文档前请自行甄别文档内容的完整性,平台不提供额外的编辑、内容补充、找答案等附加服务。
- 2、"仅部分预览"的文档,不可在线预览部分如存在完整性等问题,可反馈申请退款(可完整预览的文档不适用该条件!)。
- 3、如文档侵犯您的权益,请联系客服反馈,我们会尽快为您处理(人工客服工作时间:9:00-18:30)。
1.尺寸、形状不符合要求2.表7-1尺寸形状设计原则的缺陷缺陷种类产生原因防止方法缺陷种类求铸件尺寸公差不合要求压铸模设计尺寸错误铸件的收缩和压铸模材料的热膨胀计算不正确压铸模座孔磨损或活动部件导向装置的加工不准确。
由于铸件在压铸模中滞留时问不恒定而引起收缩波动更改模具设计尺寸根据铸件测量后所得到的实际收缩值来修改压铸模通过时间继电器设定铸件在压铸模中的滞留时间为定值垂直分型面的尺寸不正确铸件增厚并在分型面上存在飞边。
由于流体冲击和合模压力不够造成动模放松增大台模压力(更换压铸机)。
为了降低流体冲击.在充型将结束时降低压射速度由活动型芯和镶嵌块完成的尺寸不正确由于缺乏刚性固定,活动型芯和镶嵌块出现错位规定通过扣榫来固定活动部件。
更换已磨损的型芯由活块完成的尺寸不正确在活块壁上存在毛刺。
由于活块的匀错动。
偏移和饿斜造成的壁厚不均匀在压铸模中固定活块不正确。
活块预热不够正确组装带活块的压铸模。
修正倾斜和加工处理配合位置。
在加热状态下安放活块在不同压铸半模中完成的铸件轮廓不正确由于导柱或衬套的磨损造成压俦半模错动更换已磨损的导柱或衬套缺陷种类产生原因防止方法铸造孔洞尺寸不正确型芯损坏·型芯压偏或倾斜。
型芯制备不正确更换型芯铸造螺纹尺寸不正确不均匀的拧出螺纹型苍螺纹型芯损坏。
制备用于从铸件中拧出螺纹型芯的夹具更换螺纹型芯多肉或带肉压俦模热处理不当,产生掉块压铸模龟裂而掉块在滑块分型面处清理不干净合模时压坏成型表面机械损伤按工艺规程进行热处理严格执行操作规程,必须把分型面清理干净参看。
龟裂”防止措施欠铸及轮廓不清晰内浇道宽度不够或压铸模排气不良合金流动性差、浇注温度低或压铸模温度低压射速度低、压射比压不足填。
压铸模腔边角尺寸不合理、不易充填改进内浇道改善排气条件适当提高压铸模温度和浇注温度提高压射比压和压射速度压铸模制造尺寸要准确变形铸件结构不合理.各部收缩不均匀留改进铸件结构、使壁厚均匀不要堆叠存放特别是大面薄的铸件模时间太短顶出过程铸件偏斜铸件刚性不够\堆放不合理或去除浇道方法不当时效或退火时不要堆叠人炉必要时可以进行整形飞翅压射前机器的调整、操作不合适压铸模及滑块损坏.闭锁元件失效镶块及滑块磨损压铸模强度不够造成变形分型面上杂物未清理干净力投影面积计算不正确。
超过了销模力检查合模力及增压情况调整增压机构机构使压射增压峰值降低检查压铸模强度和闭锁元件检查压铸模损坏情况并修理清理分型面防止有杂物2.材料性能不符合要求,见表7-2表7-2材料性能方面的缺陷化学成分不符合要求配料不准确原材料及同炉料未加分析即投人使用个别元素烧损炉料经化验分析后才能配用炉料要严格管理,新旧料要按一定比例使用严格控制熔炼工艺熔炼工具要喷刷涂料力学性能不符合要求化学成分有错误铸件内部有气孔、缩孔、渣孔等对试样处理方法不对(如切取、制备)零件结构不合理配料、熔化要严格控制成分及杂质含量、严格遵守熔工艺、在生产中要定期进行工艺性实验严格控制合金温度尽量消除形成氧化手的各种因素3.铸件表面缺陷缺陷种类产生原因防止方法机械拉伤压铸模设计和制造不正确,如型芯和成型部分无斜度或负斜度型芯或型壁上压伤影响出模铸件有偏斜拉伤在固定部位时要检修压铸模,修正斜度,打光压痕拉伤无固定部位时在接伤相应位置的压铸模上增加涂料检查涂料合金成分,如铝合金中含铁太少,不大于0.6%调整顶杆、使顶出力平衡粘模拉伤合金浇注温度高模具温度太高涂料使用不足或不正确模具某些部位表面粗糙浇系统不正确使合金正面冲击型璧或型芯模具标准材料使用降低浇注温度.模具温度控制在工艺范围内.消除型腔粗糙的表面消除型腔粗糙的表面检查涂料品种或用量是否当调整内浇道防金属液正面冲击,校对合金成分、不当或热处理工艺不正确,硬度不足铝合金古铁量太少(<0.6%)YZCuZn4OPb含锌低或有偏析填充速度太高使铝合金含Fe量在要求范围内检模具材料及热处理工艺和硬度是否合理当降低填充速度.碰伤使用,搬运不当运转,装卸不当注意制品使用搬运和包装从压铸机上取件要小心流痕及花纹流痕:首先进入型腔的金属液形成一个极薄的而又不完全的金属层后、被后来的金属液所弥补而留下的痕迹。
模温过低,内浇道截面积过小及位置不当产生喷溅作用于金属液上的压力不足花纹:涂料用量过多提高模温调整内浇道截而积或位置调整内浇道速度及压力适当的选用涂料及调整用量网状毛翅压铸模型腔表面龟裂压铸模材质不当或热处理工艺不正压铸模冷热温差变化太大浇注温度过高压铸模预热不足型腔表面粗糙压铸模壁薄或有尖角正确选用压铸模材料及热处理工艺浇注温度不宜过高尤其是高熔点合金模具预热要充分压铸模要定期或压铸一定次数后退火、打磨成型部分表面冷隔两股金属泷相互对接.但未完全熔合而又无央杂存在其间,两股金属结合力很薄弱浇注温度或压铸模温度偏低选择合金不当.流动性差浇道位置不对或流路过长填充速度低压射比压低适当提高浇注温度提高压射比压缩短填充时间提高压射速度同时加大内浇口截面积改善排气、填充条件一正确选用合金,提高合金流动性缩陷(凹陷)1.由收缩引起压铸件设计不当壁厚差太大合金收缩性大,浇道位置不当压射比压低,压铸模局部温度过高2.由压铸模损伤引起压铸模损伤压铸模龟裂3.由憋气引起填充铸噩时.局部气体未排出、被壁厚应均匀厚薄过渡要缓和,选用收缩性小的合金正确选择合金液导人位置及增加内浇道截面积增加压射压力适当降低浇注温度及压铸模温度对局部高温要局部冷却检修压铸模消除凸起部分改善排溢条件减少涂料用量压缩在形腔表面.与金属液界面之间印痕I.由顶出元件引起:顶杆端面被磨损、顶杆调整不齐压铸模型腔拼接部分和其他活动部分配合不好2.由拼接或活动部分引起:镶拼部分松动、活动部分松动或磨损铸件的侧壁表面。
由动、定模互相穿插的镶件所形成工作前要检查、修好压铸模顶杆长短要调整到适当位置紧固镶块或其他活动部分设计时消除尖角,配合间隙调整适合改善铸件结构使压铸模消除穿插的镶嵌形式、改进压铸模结构表面起泡过早开模顶压铸件模温过高.金属凝固时间不够,强度不够,受压气泡膨胀起来调整压铸工艺参数适当延长留模时间降低缺陷区域模具温度冷豆压铸件表面嵌有冷豆.未和铸件完全融合的金属颗粒(通常在欠铸处)浇注系统设置不当填充速度快金属液过早流人型腔改进浇注系统避免金属直冲型芯、型壁增大内浇道截面积改进操作。
调整机器粘附物痕迹在压铸模型腔表面上有金属或非金属残留物浇注时先带进杂质附在型腔表面上在压铸前对型腔压室及浇注系统要清理干加净。
去除金属或非金属粘附物对浇注的合金也要清理干净选择合适的涂料涂布要充分分层(夹皮及剥落)模具刚性不够在金属液填充过程中、模板产生抖动压射冲头与压室配合不好.在压射中前进速度不平稳浇注系统设计不当加强模具刚度,紧固模具部件,使之稳定调整压射冲头与压室,使之配合好合理设计内浇道磨擦烧蚀压铸件表面在某些位置上产生粗糙1.由压铸模引起的内浇道的位置方向和形状不当设计方案不合理2.由铸造条件引起的内浇道处金属液冲刷剧烈部位的冷却不够改善内浇道的位置及方向的不当之处改善冷却条件.特别是改善金属液冲刷剧烈部位对烧蚀部分增加涂料调整合金液的流速、使其不产生气穴消除模具上的合金粘附物冲蚀压铸件局部位置有麻点或凸纹1.内浇道位置设置不当2.冷却条件不好内浇道的厚度要恰当修改内浇道的位置、方向和设置方法对被冲蚀部位要加强冷却4.铸件内部缺陷缺陷种类产生原因防止方法气孔压室、浇道和型腔内的空气进入到金属中铸件中存在增厚部分润滑剂过多减少压室套简的直径。
增大排气槽的截面。
在形成气孔的位置设置溢流槽。
增加续时间使铸件壁厚变得较均匀.或在铸件增厚部位加活块减少润滑剂的量针孔炉料不干净或熔炼温度长过高、精炼后保持时问过在散流充型时空气和润属滑剂的气体产物进入金熔化金属中气体析出使用干燥清洁炉料、控制熔炼温度及时间。
增大排气槽的截面。
沿铸件周围设置溢流槽。
增大内浇道截面并转向连续流充型.而在散流充型时增大金属流的速度.减小压室套筒的直径、减小内浇道截面或增大压射速度在分配炉中改普合金的脱气。
通过压铸型冷却来增大合金的凝固速度气泡型腔气体没有排出。
被包在铸件中涂料产生的气体卷入铸件合金内吸有较多气体.凝固时析出留在铸件内改善内浇道、溢流槽、排气道的大小和位置改善填充时间和内浅道处流速提高压射压力在气孔发生处设型芯尽量少用涂料清除合金液中的气体和氧化物炉科要管理好避免被尘土油类污染缩孔铸件中存在大量增厚部分内浇道太小浇注温度过高压射比压低在铸件增厚部位加活块,增强这些部位压铸型的冷却。
增大内浇道截面和补压压力降低浇注温度或更换合金疏松合金过大收缩铸件中存在剧烈过渡合金体积收缩过大保证铸件厚截面向薄截面平稳过渡。
增大补压压力.减小机加工余量。
增大金属配量和补压持续时间加强压铸型冷却。
更换合金夹渣(渣孔)1.混人熔渣金属液表面上的熔渣未清除将熔渣及金属同时浇注到压室2.石墨混入物落有石墨坩埚时边缘有脱涂料中石墨太多仔细去除金属表面的熔渣遵守金属舀取工艺在石墨坩埚边缘装上铁环使用涂料要均匀,用量适当硬点1.非金属硬点:(1)混人了合金液表面的氧化物铸造时不要把台金液表面的氧化物舀人勺内清除铁坩埚勺子等工具上的氧化物使用与铝不产生反应的涂科(2)混人了合金液同耐火砖产生反应的混合物要使用不和铝合金发生反应的耐火砖和灰浆。
例如氧化物铝质砖定期更换炉衬砖(3)混入了合金液与涂料的反应的生成物应该用与铝合金不发生反应的涂料(4)产生了复合化合钧如由Al、Mn、Fe、Sl组成的化合物在铝合金中含有Mn、Fe等元素时应勿使偏析,并保清洁用干燥的去气剂除气、铝合金台镁时要注意补偿(5)游离硅混入物铝硅合金含Si高铝台金在半液态浇注硅游离存在.或者铝硅合金含Si高于11.6%且Cu、Fe台量亦高铝合金含Cu、Fe多时.应使含Si量降到10.5%以下适当的提高浇注温度.以避免使Si析出(6)其他夹杂物金属料不纯.含有其他异物金属料粘附油污工具清理不净加强管理、严防回收料混入异物或异种材料回收料不要粘上油、砂、尘土等物清理净坩埚、熔炼工具上面的铁锈及氧化物2.金属硬点(I)混人了未熔解的硅元素原料熔炼铝硅合金时.不要使用硅元素粉未调整合金成分时、不要直接加人硅元素必须采用中间合金熔炼温度要高。
时间要长使硅充分熔解(2)混合了促进初生硅结晶生长的原料缩小铸造温度波动范围、使之经常保持熔融状态加冷料时要防止合金锭块使合金凝固。
尽量减少促进初品硅易于生长的成分(3)混人了生成金属问化合物结晶物质低减少温度被动范围.不使合金液的温度过高或过低。
控制合金成分杂质含量的同时,注意勿使增加杂质。
对能产生金属间化合物的材料要在高温下熔炼、为防止杂质增加.应一点一点的少量加入3.偏析性硬点由于急冷组织致密化.使容易偏析的成分析出成为硬点合金液浇人压室后、应立即压射填充尽可能不舍有Ca、Mg、Na等易引起急冷效应的合金成分.Ca应控制在0.05%以下5.裂纹缺陷缺陷种类产生原因防止方法锌合金压铸件裂纹锌合金中有害杂质铅、锡、铁和镉的含量超过了规定范围铸件从压铸模中取出的过或过迟型芯的抽出或顶出受力不均铸件的厚薄相接处转变剧烈熔炼温度过高合金材料的配比要注意杂质含量不要超过起点要求调整好开模时间要使推杆受力均匀改变壁厚不均匀性铝合压铸件合金中铁含量过高或硅含量过低合金中铸件坩埚及熔炼工具要涂好涂料正裂纹有害杂质的含量过高.降低了合金的可塑性铝硅合金.铝硅铜合金含锌或含铜量过高:铝镁合金中含镁量过多模具.特别是型芯温度太低铸件壁厚或凸台.过渡有剧烈火变化留模时间过长顶出时受力不均确控制合金成分、在某些情况下:可在合金中加纯铝锭以降低合金中台镁量:或在合金中加铝硅中间合金以提高硅含量提高模具温度改变铸件结构调整抽芯机构或使推杆受力均匀镁合金压铸件裂纹合金中铝硅镀含量高铸件壁厚薄变化剧烈模具温度低合金过热太大顶出和抽芯受力不均匀合金中加纯镁以降低铝硅含量模具温度要控制在要求的范围内改进铸件结构消除厚薄变化较大的截面内合金的熔炼温度控制在工艺规范之调整好型芯和推杼.使之受力均衡铜合金压铸件裂纹黄铜中锌的含量过高(冷裂)或过低(热裂)硅黄铜中硅的含量高压铸模温度过低浇注温渡过高合金欠压开模时间晚,特别是型芯多的铸件保证合金的化学成份合金元素取其下限:硅黄铜在配制时。