硅太阳电池开发路线图
晶体硅太阳能电池结构及原理通用课件

行业政策与市场趋势的挑战与机遇
环保政策
随着全球对环境保护意识的增强,各国政府出台了一 系列的环保政策,对晶体硅太阳能电池的生产和应用 提出了更高的要求,但同时也为环保型、高效能的晶 体硅太阳能电池提供了市场机遇。
市场竞争
晶体硅太阳能电池市场竞争激烈,各国企业都在加大 研发和生产力度,提高产品质量和降低成本,以争取 更大市场份额,企业需要保持技术创新和市场敏锐度, 才能立于不败之地。
分类
太阳能电池主要分为硅基太阳能电池、 薄膜太阳能电池、染料敏化太阳能电 池等几大类,其中晶体硅太阳能电池 是硅基太阳能电池的一种。
晶体硅太阳能电池的应用与优势
应用
晶体硅太阳能电池广泛应用于光伏电站、太阳能热水器、太阳能灯具、太阳能 船、太阳能车等方面。
优势
晶体硅太阳能电池具有稳定性好、寿命长、转换效率高等优点,同时,由于其 在制造过程中技术成熟、成本逐渐降低,因此大规模应用较为广泛。
太阳能光伏电站案例分析
光伏电站类型
根据电站规模和应用场景,太阳能光伏电站可分为集中式光伏电站和分布式光伏电站。集中式光伏电 站通常建设在荒漠、戈壁等土地资源丰富地区,而分布式光伏电站则主要建设在建筑屋顶、墙面等闲 置空间。
案例分析
以某大型集中式光伏电站为例,介绍晶体硅太阳能电池在其中的应用,包括电池组件选型、电站布局 设计、发电效率分析等方面。
太阳能交通工具概述
简要介绍太阳能汽车、太阳能船舶、太阳能 飞机等太阳能交通工具的发展现状及趋势。
晶体硅太阳能电池在太阳 能交通工具中的应用
阐述晶体硅太阳能电池在太阳能交通工具中 的关键技术,如高效能量存储系统、轻量化 设计等,并分析其在提高交通工具续航里程、 降低能耗等方面的作用。同时,探讨晶体硅 太阳能电池在未来太阳能交通工具领域的潜
硅太阳能电池-制造工艺
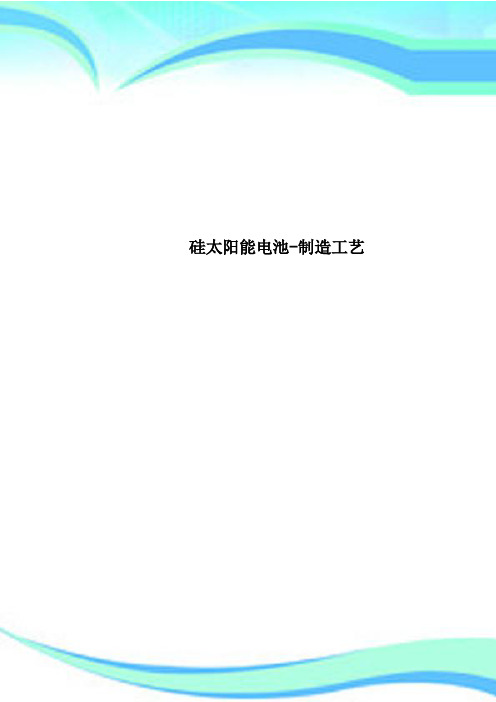
硅太阳能电池-制造工艺————————————————————————————————作者:————————————————————————————————日期:PV的意思:它是英文单词Photovoltaic的简写,中文意思是“光生伏特”(简称“光伏”)。
在物理学中,光生伏特效应(简称为光伏效应),是指光照使不均匀半导体或半导体与金属组合的不同部位之间产生电位差的现象硅太阳能电池制造工艺流程图1、硅片切割,材料准备:工业制作硅电池所用的单晶硅材料,一般采用坩锅直拉法制的太阳级单晶硅棒,原始的形状为圆柱形,然后切割成方形硅片(或多晶方形硅片),硅片的边长一般为10~15cm,厚度约200~350um,电阻率约1Ω.cm的p型(掺硼)。
2、去除损伤层:硅片在切割过程会产生大量的表面缺陷,这就会产生两个问题,首先表面的质量较差,另外这些表面缺陷会在电池制造过程中导致碎片增多。
因此要将切割损伤层去除,一般采用碱或酸腐蚀,腐蚀的厚度约10um。
3、制绒:制绒,就是把相对光滑的原材料硅片的表面通过酸或碱腐蚀,使其凸凹不平,变得粗糙,形成漫反射,减少直射到硅片表面的太阳能的损失。
对于单晶硅来说一般采用NaOH加醇的方法腐蚀,利用单晶硅的各向异性腐蚀,在表面形成无数的金字塔结构,碱液的温度约80度,浓度约1~2%,腐蚀时间约15分钟。
对于多晶来说,一般采用酸法腐蚀。
4、扩散制结:扩散的目的在于形成PN结。
普遍采用磷做n型掺杂。
由于固态扩散需要很高的温度,因此在扩散前硅片表面的洁净非常重要,要求硅片在制绒后要进行清洗,即用酸来中和硅片表面的碱残留和金属杂质。
5、边缘刻蚀、清洗:扩散过程中,在硅片的周边表面也形成了扩散层。
周边扩散层使电池的上下电极形成短路环,必须将它除去。
周边上存在任何微小的局部短路都会使电池并联电阻下降,以至成为废品。
目前,工业化生产用等离子干法腐蚀,在辉光放电条件下通过氟和氧交替对硅作用,去除含有扩散层的周边。
【光伏技术】高效晶体硅太阳能电池_3

【光伏技术】高效晶体硅太阳能电池
HIT 电池是异质结( hetero-junction with intrinsic thin-layer , HIT) 太阳能电池的简称。
1997年,日本三洋公司推出了一种商业化的高效电池设计和制造方法,电池制作过程大致如下:利用PECVD在表面织构化后的N型CZ-Si片的正面沉积很薄的本征α-Si:H层和p 型α-Si:H层,然后在硅片的背面沉积薄的本征α-Si:H层和n型α-Si:H层;利用溅射技术在电池的两面沉积透明氧化物导电薄膜(TCO),用丝网印刷的方法在TCO上制作Ag电极。
值得注意的是所有的制作过程都是在低于200 ℃的条件下进行,这对保证电池的优异性能和节省能耗具有重要的意义。
图3:三洋公司HIT电池h=23%。
单晶硅太阳能电池详细工艺
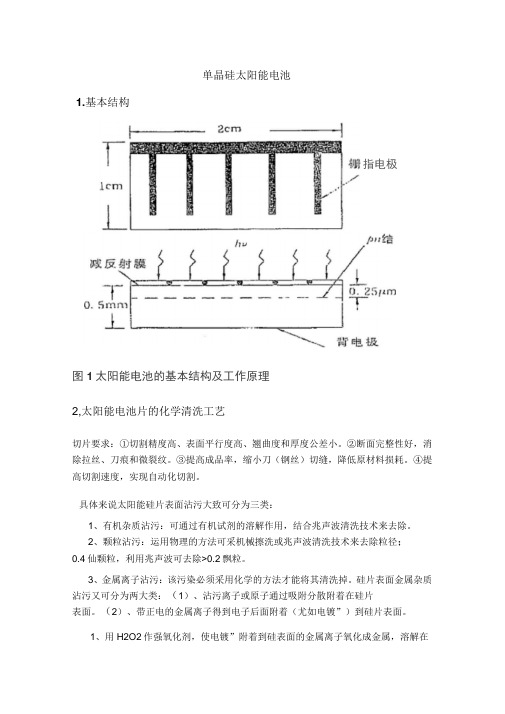
单晶硅太阳能电池1.基本结构指电极图1太阳能电池的基本结构及工作原理2,太阳能电池片的化学清洗工艺切片要求:①切割精度高、表面平行度高、翘曲度和厚度公差小。
②断面完整性好,消除拉丝、刀痕和微裂纹。
③提高成品率,缩小刀(钢丝)切缝,降低原材料损耗。
④提高切割速度,实现自动化切割。
具体来说太阳能硅片表面沾污大致可分为三类:1、有机杂质沾污:可通过有机试剂的溶解作用,结合兆声波清洗技术来去除。
2、颗粒沾污:运用物理的方法可采机械擦洗或兆声波清洗技术来去除粒径;0.4仙颗粒,利用兆声波可去除>0.2飘粒。
3、金属离子沾污:该污染必须采用化学的方法才能将其清洗掉。
硅片表面金属杂质沾污又可分为两大类:(1)、沾污离子或原子通过吸附分散附着在硅片表面。
(2)、带正电的金属离子得到电子后面附着(尤如电镀”)到硅片表面。
1、用H2O2作强氧化剂,使电镀”附着到硅表面的金属离子氧化成金属,溶解在清洗液中或吸附在硅片表面。
2、用无害的小直径强正离子(如H+),一般用HCL作为H+的来源,替代吸附在硅片表面的金属离子,使其溶解于清洗液中,从而清除金属离子。
3、用大量去离子水进行超声波清洗,以排除溶液中的金属离子。
由于SC-1是H2O2和NH40H的碱性溶液,通过H2O2的强氧化和NH4OH的溶解作用,使有机物沾污变成水溶性化合物,随去离子水的冲洗而被排除;同时溶液具有强氧化性和络合性,能氧化Cr、Cu、Zn、Ag、Ni、Co、Ca、Fe、Mg等,使其变成高价离子,然后进一步与碱作用,生成可溶性络合物而随去离子水的冲洗而被去除。
因此用SC-1液清洗抛光片既能去除有机沾污,亦能去除某些金属沾污。
在使用SC-1液时结合使用兆声波来清洗可获得更好的清洗效果。
另外SC-2是H2O2和HCL的酸性溶液,具有极强的氧化性和络合性,能与氧化以前的金属作用生成盐随去离子水冲洗而被去除。
被氧化的金属离子与CL-作用生成的可溶性络合物亦随去离子水冲洗而被去除。
硅太阳能电池工艺流程

背电场
前电极的印刷 在太阳电池正面丝网印刷银浆,形成负
电极 正面电极有主栅线和副栅线组成
副栅线 主栅线
The End
硅太阳能电池工艺流程
本课件PPT仅供大家学习使用 学习完请自行删除,谢谢! 本课件PPT仅供大家学习使用 学习完请自行删除,谢谢! 本课件PPT仅供大家学习使用 学习完请自行删除,谢谢! 本课件PPT仅供大家学习使用 学习完请自行删除,谢谢!
制备工艺流程
硅片清洗与制绒
硅片清洗与去损
去除表面损失和沾污
N型硅
P型硅
N型硅
减反射膜
沉积深蓝色减反膜SiNx:H膜。
折射率
玻璃~1.5 硅~3.4 介质~2.2
减反射
钝化作用
SiNx Al2O3
最常用
SiNx/SiOx
表面等离子体
为什么要钝化
少子寿命较低的情况下, 寿命提高对电池效率的影响比较明显
少子寿命较高时,表面复合对效 率影响更加重要
随着电池片的减薄,绝大多数硅片体寿命已经大于硅片厚度,提高 少子寿命对电池性能的提高已经比较有限; 同时,随着硅片厚度减薄,表面复合所占比重越来越大,表面钝化 显得更加重要。
酸制绒
酸制绒是各向同性腐蚀
使用HNO3和HF的混合液
单晶和多晶硅都适用 需要表面有缺陷和损伤 可以与H2O, H3PO4,
H2SO4等混合使用
As-cut Alkali
Acidic
RIE(反应离子刻蚀)制绒
一般使用CF4等离子体轰击表面 优点
低温,环境影响小 易单面制绒 硅片应力小 缺点 成本 当 λ < 500 nm时,QE降低
磷扩散
扩散方法
硅太阳能电池工艺[1]
![硅太阳能电池工艺[1]](https://img.taocdn.com/s3/m/ee0eb455551810a6f52486c5.png)
硅太阳能电池工艺[1]
•等离子体刻蚀反应
首先,母体分子CF4在高能量的电子的碰撞 作用下分解成多种中性基团或离子。
PPT文档演模板
其次,这些活性粒子由于扩散或者在电场作 用下到达SiO2表面,并在表面上发生化学反 应。
生产过程中,CF4中掺入O2,这样有利于提 高Si和SiO2的刻蚀速率。
丝网印刷与烧结
PPT文档演模板
硅太阳能电池工艺[1]
PPT文档演模板
•电池片丝网印刷的三步 骤
❖ 背电极印刷及烘干 浆料:Ag /Al浆 如Ferro 3398
❖ 背电场印刷及烘干 浆料:Al浆 如Analog pase-12
❖ 正面电极印刷 浆料:Ag浆 如Dupont PV147
硅太阳能电池工艺[1]
硅太阳能电池工艺[1]
•扩散层薄层电阻及其测量
在太阳电池扩散工艺中,扩散层薄层电 阻(方块电阻)是反映扩散层质量是否 符合设计要求的重要工艺指标之一。
方块电阻也是标志进入半导体中的杂质 总量的一个重要参数。
PPT文档演模板
硅太阳能电池工艺[1]
•方块电阻的定义
PPT文档演模板
考虑一块长为l、宽 为a、厚为t的薄层 如右图。如果该薄 层材料的电阻率为ρ, 则该整个薄层的电 阻为
PPT文档演模板
硅太阳能电池工艺[1]
•等离子体刻蚀原理
PPT文档演模板
等离子体刻蚀是采用高频辉光放电反应,使 反应气体激活成活性粒子,如原子或游离基, 这些活性粒子扩散到需刻蚀的部位,在那里 与被刻蚀材料进行反应,形成挥发性生成物 而被去除。它的优势在于快速的刻蚀速率同 时可获得良好的物理形貌 。(这是各向同性 反应)
本公司目前采用的是第一种方法。
太阳能电池制造工艺---工艺流程以及工序简介ppt课件

2.高温扩散(液态扩散) 3.去磷硅玻璃(去PSG) 4.沉积减反射膜(PECVD)
5.丝网印刷背电极 6.烘 干
7.丝网印刷背电场
8
2)、工序简介
目前硅太阳能电池制造工序主要有:
制绒清洗工序 扩散工序 PECVD工序 丝网印刷工序 烧结工序 Laser刻蚀工序 测试分选工序
扩散的目的:制造太阳能电池的PN结。
PN结是太阳能电池的“心脏” 。 制造PN结,实质上就是想办法使受主杂质在半导体晶体内的一个
区域中占优势(P型),而使施主杂质在半导体内的另外一个区域 中占优势(N型),这样就在一块完整的半导体晶体中实现了P型 和N型半导体的接触。
5POCl 3 600 C以上 3PCl 5 P2O5
17
ser刻蚀工序
Laser刻蚀的目的、作用: 用激光切出绝缘沟道,可以使电池短路,减少电流泄漏。
硅片经Laser刻蚀后的示意图
18
7. 测试分选工序
主要是测量电池片的短路电流(JSC)、开路电压(VOC)、 填充因子(FF),经计算得出电池的光电转换效率(η) 。
根据电池的光电转换效率(η)对电池片进行分类。
2
单晶硅太阳电池
3
多晶硅太阳电池
4
非晶硅太阳电池
5
2. 硅太阳电池的制造工艺流程
下面我们就硅太阳电池的制造工艺流程以及各工序进行简 单的介绍。
晶体硅太阳能电池制造的常规工艺流程主要包括:硅片清 洗、绒面制备、扩散制结、(等离子周边刻蚀)、去 PSG(磷硅玻璃) 、PECVD 减反射膜制备、电极(背面电极、 铝背场和正电极) 印刷及烘干、烧结、Laser和分选测试等。 同时,在各工序之间还有检测项目,主要有抽样检测制绒效 果、抽样 测方块电阻、抽样测氮化硅减反射膜厚度和折射 率等项目。
光伏产业技术路线图

光伏材料产业技术路线图编制研究一、光伏产业发展现状和愿景由于全球气候变暖、生态环境恶化、常规能源短缺等问题,发展可再生能源得到各国政府的重视和支持。
在技术进步的推动和各国政府的激励政策驱动下,太阳能光伏发电产业和市场得以迅速发展。
欧洲光伏工业协会(EPI-A)预测,随着光伏排放量将分别减少0.15系统安装量的快速增加,在2010、2020和2030年,全球CO2亿吨、1.92亿吨、10.81亿吨。
根据欧洲JRC的预测,到2030年可再生能源在总能源结构中占比达到30%以上,太阳能光伏发电在世界总电力供应中达到10%以上;2040年可再生能源占总能耗50%以上,太阳能光伏发电将占总电力的20%以上,经济规模将达到100万亿以上;到21世纪末可再生能源在能源结构中占到80%以上,太阳能发电占到60%以上。
可见光伏产业将是一个长期的朝阳产业。
1.1发展现状全球光伏市场在过去几十年的平均年增长率达到40%,光伏发电累计安装容量已经从1992年的0.1GW增长到2008年的14GW,2008年度全球光伏发电新增安装量达到6GW。
四个国家的光伏发电累计安装容量超过了1GW:德国(5.3 GW)、西班牙(3.4 GW)、日本(2.1 GW)、美国(1.2 GW)。
这些国家的光伏发电累计安装容量占全球累计安装总量的80%。
从制造业来看,中国、欧盟各国、日本、中国台湾地区和美国仍然是世界光伏组件的主要生产地,2008年和2009年,上述地区产量占世界光伏组件总产量的91.5%和95.3%。
其中中国排在第一位,分别占世界生产总量的32.9%和37.4%;欧盟、日本、台湾地区和美国排在第二、三、四、五位。
2008 年,中国光伏发电新装容量为45MW,占全球需求的比重不到1%,远远落后于欧美日等光伏市场大国。
截止到2008 年末,中国光伏累计装机容量为145MW,相当于14万KW,相对于8 亿KW 的总电力装机容量而言,几乎可以忽略不计。
- 1、下载文档前请自行甄别文档内容的完整性,平台不提供额外的编辑、内容补充、找答案等附加服务。
- 2、"仅部分预览"的文档,不可在线预览部分如存在完整性等问题,可反馈申请退款(可完整预览的文档不适用该条件!)。
- 3、如文档侵犯您的权益,请联系客服反馈,我们会尽快为您处理(人工客服工作时间:9:00-18:30)。
硅太阳电池开发路线图出自:Els Parton,Guy Beaucarne,IMEC光伏产业增长强劲,过去十年的年平均增长率达40%。
预期未来十年这一增长率将保持在25-40%。
其结果会使全世界减少对化石燃料的依赖,减少与发电相关的CO的排放。
2基于晶体硅的太阳电池现在主宰光伏市场,其市场占有率超过90%。
当前多晶硅光伏组件的成本中,约50%与硅片有关。
主要均匀分布在材料成本、晶体生长和硅片制作三方面。
必须认识到,光伏组件所用硅片价格取决于多晶硅料的成本和可供资源。
现今,光伏产业面临多晶硅料的短缺,硅片价格上涨。
由此很明显,减少太阳电池中昂贵的电子级硅的消耗就能降低太阳电池的成本。
达到这一点有多种不同的途径:用薄硅片,以100-150μm厚的硅片替代常用的220μm厚的硅片;或者在低成本衬底上应用薄膜晶体硅(厚度小于20μm)。
比利时IMEC研究所以其对PV技术的洞察,比较了薄硅片太阳电池和薄膜太阳电池二者的路径,确定了发展路线图(图1)。
体硅太阳电池“体硅”太阳电池是基于自支撑的硅片,厚度为180-240μm。
大多数大型商用太阳电池工厂现在采用多晶硅片。
硅片通常是p-型掺杂的。
N型杂质扩散在硅片上面,这样就在表面下几百纳米处形成p-n结。
然后,在太阳电池的正面加防反射镀层(ARC,大都是氮化硅),增加耦合进入太阳电池的光数量。
ARC层还有表面钝化作用,它可以防止载流子在太阳池表面的复合。
为了进一步减少反射损失,在做其它工艺步骤前常常将太阳电池的表面制绒,为光线进入电池结合提供多重机会。
接着实现金属接触。
在背面制作全面积金属接触,通常是丝网印刷金属浆料(铝)。
在正面,用金属浆料(银),以丝网印刷网状金属接触。
金属接触要进行短时间退火,将其烧结并使正面接触侵蚀穿过ARC层。
最后,各太阳电池用细金属带互相连接,组装成组件或“太阳电池板”。
硅片越来越薄时,上述的传统太阳电池工艺遇到了一些问题。
其中之一是与在整个背面加铝合金有关。
合金工艺及硅与铝之间的热失配引起应力场扩展,使得硅片明显弯曲。
这在硅片处理和组件制造中会产生很多问题。
另一问题是背面的载流子复合。
背面区域高掺杂铝(称为“铝背场BSF”),只能提供中等的表面钝化。
对于很薄的电池片,背面的复合现象非常重要,会引起短路电流密度和开路电压二者的损失。
i-PERC太阳电池概念为了规避薄硅片制造中的这些问题,IMEC开发了i-PERC工艺。
PERC (passivated emitter and rear cells,钝化发射极和背表面电池)概念是为实验室型高效太阳电池提出的。
“i”代表“工业的”,其意是指,与PERC不同,这一工艺是基于工业应用技术。
i-PERC工艺与标准工艺不同,因为不再把铝直接淀积在硅的背面。
而是用低温淀积技术淀积SiO/SiN介质2层,然后用激光打洞,最后是铝丝网印刷,烧结形成穿过孔洞的局部背场(BSF)接触。
这样,大部分硅与铝隔离,减少了背表面复合,从而提高了短路电流和开路电压。
i-PERC背面结构也改善了光线的束缚,因为在1000nm 以上红外波长处,它比Al-BSF有更多的反射。
在1100nm处,Al-BSF的背反射率为64%,而i-PERC背反射率是91%。
这体现了净增长0.9mA/cm2,或总效率提高4%。
此外,对i-PERC太阳电池来说,完全消除了弯曲问题(即使硅片薄至80μm),因为由铝合金工艺引起的应力只是局部的。
i-PERL太阳电池概念PERL(passivated emitter, rear locally diffused,钝化发射极,背面局部扩散)概念是为实验室型小面积高效率太阳电池提出的。
它与PERC概念有关,但特别之处是在背面局部区域有硼掺杂。
由于在扩散区缺少少数载流子,背接触表面处的复合速率就进一步降低。
文献中已经证明,实验室条件下用PERL概念制作的小面积晶硅太阳电池能达到一个太阳的效率接近25%,采用对体硅寿命谱和表面钝化所做的实际假定时,这一性能距可能达到的最大效率(26%)已不远。
IMEC挑战的是开发大面积PERL电池的工艺流程,以及工业上可应用的技术,这些技术目前只是常用在先进的微电子或封装场合。
I2-BC太阳电池概念把正面的金属栅格去掉有很多优点:(1)可产生更多有效的半导体面积,因而有可能增加电池效率;(2)有可能大大降低组件装配成本,因为全部外部接触均在单一表面上;(3)从建造结构的观点看来提供了增值,因为汇流条和焊线串接存在引起的视觉不适被组件背面替代。
当前背接触太阳能电池的研究活动一方面是组件制造,另一方面是开发背接触太阳电池的新概念,重点是便于转换到生产中的工艺技术的使用。
超薄体硅太阳电池(U-电池概念)将来的薄硅片太阳能电池可能薄至40μm。
达到这一点的主要挑战是怎样生产如此薄的硅片。
用传统的线切割技术,硅片的厚度不大可能比100μm低很多,且kerf损失(切割过程中的Si损耗)将是严重的。
但是,这种超薄硅片(更进一步为箔硅片)能用lift-off技术实现。
IMEC近来提出了一种生产厚50μm晶硅片的全新方法。
这种lift-off工艺,只需要用丝网印刷机和网带炉,不需要离子注入或多孔层。
在厚衬底上淀积与衬底热膨胀系数不匹配的一层薄膜(例如金属层)。
冷却时,收缩差异引起了大应力场,它通过平行于表面的方向开始产生并传播的裂开得到释放(图2)。
薄膜硅太阳电池减少太阳电池所用硅数量的另一重要途径是,把有源层厚度减少到20μm或更少。
这些晶体硅可用低成本载体(低成本硅或非硅衬底)支撑。
Epi-电池概念外延薄膜太阳电池是用在低成本高掺杂硅片上生长高质量的薄硅有源层(20μm)实现的,这种硅片来自金属级硅或硅废料。
用化学气相淀积法淀积外延层。
这种epi-电池法的优点是,其太阳电池生产工艺与通常的“体”硅太阳电池非常类似。
因而,与其它薄膜电池概念比较,在现有的生产线中实施这一方法相对来说容易。
此法构成了体硅太阳电池和薄膜太阳电池(在非硅衬底上)间的桥梁。
外延薄膜硅太阳电池工业竞争力的主要不足是,与通常的体硅太阳电池相比,其效率中等,约为11-12%。
这些电池的开路电压和填充因子能达到类似于体硅太阳电池的水平,但由于光学有源层薄(20μm,体硅为200μm),光由外延层进入衬底时就消失在低质量衬底中,导致总量达7mA/cm2的短路电流损失。
IMEC开发旨在提高外延薄膜太阳电池效率的技术。
例如,解决了等离子制绒技术将太阳电池有源层表面制绒,减少反射率并增加表面的光散射。
除了由于反射率减少和光斜面耦合进入电池而提高效率外,与平面电池比较,等离子制绒也降低了接触电阻。
等离子制绒产生的效果是:短路电流提高了1.0-1.5mA/cm2,效率提高了0.5-1.0%。
提高外延薄膜硅太阳电池效率的另一改进措施是,在有源层和低成本衬底之间界面处加入多孔硅镜。
此镜减少长波长光进入衬底的透光率。
实际上,反射镜是由电化学刻蚀多孔硅堆(由交替的高-孔隙率和低-孔隙率层构成)制造的。
这些多孔硅层的折射率取决于孔隙率。
孔隙率交替不同的多层作用如同多级布拉格反射镜。
而且,多孔硅保持下层结构的晶体结构,使外延生长能够进行。
在反射镜和丝网印刷接触电极的低成本硅衬底上制作的太阳电池可达到极佳的效率13.9%,接近体晶硅太阳电池的效率。
薄膜多晶硅电池概念另一个极具降低成本潜力的薄膜太阳电池制造途径是薄膜多晶硅技术。
在低成本非硅衬底上淀积很薄一层(仅约5μm)晶体硅。
为了获得缺陷密度相对较低的一层,用铝引发的结晶(AIC)技术制备了纵深比小的晶粒组成的籽晶层,接着外延加厚。
因为要用热CVD生长有源层,选择的衬底必须要耐高温,例如陶瓷衬底和玻璃-陶瓷衬底。
目前在陶瓷衬底上最好的效率为8%,在玻璃-陶瓷衬底上为6.4%,这些是基于籽晶层方法的薄膜多晶硅电池到目前为止全球最好的结果。
薄膜多晶硅太阳电池中器件最重要的部分是发射极。
用非晶硅/多晶硅异质结发射极代替扩散的同质结发射极使得开路电压提升了90mV。
硅以外的太阳电池除了对硅基太阳电池进行大量研究工作外,IMEC还研究地面集聚器所用的光伏堆叠。
该研究的主要目的是开发创新技术,制造效率能达35%的4端高效机械堆叠。
这包括制造薄膜InGaP/GaAs顶层电池和Ge-底层电池。
长期看来,对于一些特殊应用,有机太阳电池会成为硅基太阳电池的良好替代品。
有机太阳电池的有源层一般在100nm到几微米数量级。
材料消耗少以及淀积这些材料的技术(印刷法)适合极高的生产率(比现有的太阳能电池技术大1-2个数量级)可以使成本比现有的太阳电池技术低5-10倍。
有机太阳电池领域最具前景的概念之一是施主/受主异质结。
此时,有源层是由二种不同的共轭有机材料的均质混合物组成,夹在金属电极之间。
结论太阳电池产业正在飞速增长,全球的研究团队正在寻找提高电池效率和/或降低成本的途径。
IMEC已提出太阳电池发展路线图,预计了基于薄硅片的太阳电池向在低成本载体上厚度低达40μm或单片薄膜太阳电池组件的逐步转变。
所有这些将要使太阳电池的成本至少降低为目前的1/3,每瓦硅用量(Si/W)减少一个数量级——现在此值稍稍低于10g/W。
作者简历Els Parton在比利时Katholieke Universiteit Leuven (K.U.Leuven)获得工程学位和生物科学博士学位。
2001年加入IMEC任科学编辑,负责编写和编辑技术文件和出版物。
Guy Beaucarne 1995年在比利时Catholic University of Leuven (KUL)获得机电工程学位。
在IMEC做有关薄膜硅太阳电池的博士研究工作,2000年从KUL获得博士学位。
2001年,他是悉尼University of New South Wales从事第三代光伏课题的研究。
随后加入悉尼Pacific Solar公司,致力于开发在玻璃上的光伏新技术。
2003年2月重返比利时IMEC,现在是太阳电池技术小组的领导人。
他指导IMEC的所有无机太阳电池工作。